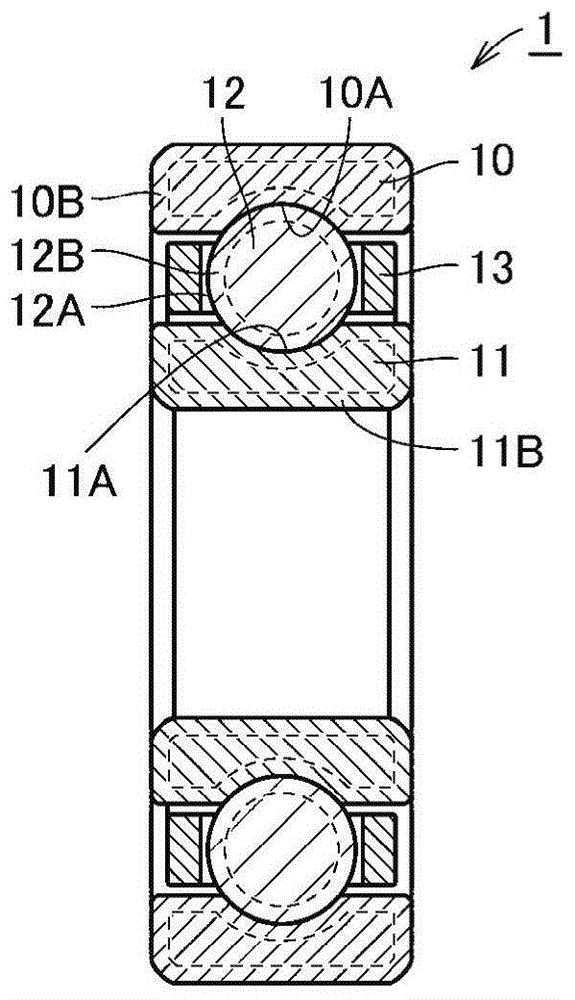
本发明涉及轴承部件、滚动轴承、和轴承部件的制造方法。具体地,本发明涉及:在外来物质容易介入轴承的环境(外来物质介入的环境)下使用的轴承部件;滚动轴承;和轴承部件的制造方法。
背景技术:
:作为轴承部件制造方法,已知如下方法:对由铬钼钢(scm)形成的成形体依次实施碳氮共渗处理、淬火处理、和回火处理。但是,通过上述制造方法制造的轴承部件不具备足以承受在外来物质介入的环境下使用的韧性和耐磨性。当在外来物质介入的环境下使用时,轴承部件会在其表面受到损伤并在早期达到寿命。为解决此问题,一般常规的轴承部件使用包含约大于或等于数%且小于或等于十几%的至少一种选自硅(si)、锰(mn)、铬(cr)、钼(mo)、钒(v)、钛(ti)等可形成碳氮化物的元素的钢材料。通过对钢材料实施预定的热处理,上述添加元素的碳化物和氮化物根据这些元素的含量在轴承部件的滚道面或滚动接触面上析出,因此导致了耐磨性的提高(例如,参见日本专利公开第2-277764号,日本专利公开第3-64431号,日本专利公开第8-49057号,日本专利公开第8-311603号,日本专利公开第11-201168号,日本专利公开第2001-323939号,日本专利公开第2007-232201号,和日本专利公开第2013-11010号)。引用文献列表专利文献专利文献1:日本专利公开第2-277764号专利文献2:日本专利公开第3-64431号专利文献3:日本专利公开第8-49057号专利文献4:日本专利公开第8-311603号专利文献5:日本专利公开第11-201168号专利文献6:日本专利公开第2001-323939号专利文献7:日本专利公开第2007-232201号专利文献8:日本专利公开第2013-11010号技术实现要素:发明所要解决的技术问题但是,上述钢材料由于钢材料以各种比例包含可形成碳氮化物的元素而价格昂贵。本发明的目的在于提供:具备足以承受在外来物质介入的环境下使用的耐磨性、使用上述钢材料且与常规的轴承部件相比以低成本制造的轴承部件;滚动轴承;和轴承部件的制造方法。解决问题的方案本发明的轴承部件由铬钼钢材料构成,其包括滚道面或滚动接触面。由选自碳化物、氮化物、碳氮化物的至少一种构成的化合物颗粒存在于滚道面或滚动接触面。滚道面或滚动接触面中的化合物颗粒的面积率大于或等于3%。滚道面或滚动接触面中的化合物颗粒的平均粒径小于或等于0.3μm。上述轴承部件是由铬钼钢构成的轴承部件且在轴承部件的表面中包括扩散层。扩散层包括多个化合物颗粒和多个马氏体块。化合物颗粒的平均粒径小于或等于0.3μm。扩散层中的化合物颗粒的面积率大于或等于3%。多个马氏体块的最大粒径小于或等于3.8μm。在轴承部件中,多个马氏体块可包括具有小于或等于1.0μm的结晶粒径且组成第一组的马氏体块。属于第一组的马氏体块的总面积除以多个马氏体块的总面积而得的值可大于或等于0.55且小于或等于0.75。在轴承部件中,多个马氏体块可包括属于第二组的马氏体块和属于第三组的马氏体块。属于第三组的马氏体块的结晶粒径的最小值可大于包括在第二组中的马氏体块的结晶粒径的最大值。属于第三组的马氏体块的总面积除以多个马氏体块的总面积而得的值可大于或等于0.5。具有最大结晶粒径且属于第三组的马氏体块以外的属于第三组的马氏体块的总面积除以多个马氏体块的总面积而得的值可小于0.5。属于第三组的马氏体块的平均粒径可大于或等于0.7μm且小于或等于1.4μm。在轴承部件中,多个马氏体块可包括属于第四组的马氏体块和属于第五组的马氏体块。属于第五组的马氏体块的结晶粒径的最小值可大于包括在第四组中的马氏体块的结晶粒径的最大值。属于第五组的马氏体块的总面积除以多个马氏体块的总面积而得的值可大于或等于0.7。具有最大结晶粒径且属于第五组的马氏体块以外的属于第五组的马氏体块的总面积除以多个马氏体块的总面积而得的值可小于0.7。属于第五组的马氏体块的平均粒径可大于或等于0.6μm且小于或等于1.1μm。在轴承部件中,多个马氏体块可包括属于第二组的马氏体块和属于第三组的马氏体块。属于第三组的马氏体块的结晶粒径的最小值可大于包括在第二组中的马氏体块的结晶粒径的最大值。属于第三组的马氏体块的总面积除以多个马氏体块的总面积而得的值可大于或等于0.5。具有最大结晶粒径且属于第三组的马氏体块以外的属于第三组的马氏体块的总面积除以多个马氏体块的总面积而得的值可小于0.5。属于第三组的马氏体块的平均纵横比可大于或等于2.5μm且小于或等于2.8μm。在轴承部件中,多个马氏体块可包括属于第四组的马氏体块和属于第五组的马氏体块。属于第五组的马氏体块的结晶粒径的最小值可大于包括在第四组中的马氏体块的结晶粒径的最大值。属于第五组的马氏体块的总面积除以多个马氏体块的总面积而得的值可大于或等于0.7。具有最大结晶粒径且属于第五组的马氏体块以外的属于第五组的马氏体块的总面积除以多个马氏体块的总面积而得的值可小于0.7。属于第五组的马氏体块的平均纵横比可大于或等于2.4μm且小于或等于2.6μm。在轴承部件中,滚道面或滚动接触面中的原奥氏体晶粒的平均粒径小于或等于8μm。在轴承部件中,扩散层中的原奥氏体晶粒的平均粒径可小于或等于8μm。在轴承部件中,所述化合物颗粒包括(fe,cr)3(c,n)。在轴承部件中,从滚道面或滚动接触面延伸到10μm深度的浅层区域的平均碳浓度大于或等于0.7重量%,浅层区域的平均氮浓度大于或等于0.2重量%。在轴承部件中,铬钼钢可以是jis中规定的scm435。本发明的滚动轴承包括:外环;相对于外环位于内侧的内环;和设于外环和内环之间的多个滚动元件。外环、内环、和滚动元件的至少一个是上述轴承部件。滚动轴承包括:具有设有外环滚道面的内周面、由铬钼钢构成的外环;具有设有内环滚道面的外周面、以使第二滚道面面向第一滚道面的方式设置的由铬钼钢构成的内环;以及可滚动地位于第一滚道面和第二滚道面之间、具有滚动接触面的由铬钼钢构成的滚动元件。扩散层设于外环滚道面、内环滚道面、和滚动接触面的至少一个上。扩散层包括多个化合物颗粒和多个马氏体块。化合物颗粒的平均粒径小于或等于0.3μm。扩散层中的化合物颗粒的面积率大于或等于3%。马氏体块的最大粒径小于或等于3.8μm。本发明的轴承部件的制造方法包括:准备由铬钼钢构成的成形体;通过在包括氨的碳氮共渗气氛下将成形体加热到大于或等于930℃且小于或等于940℃,对成形体进行碳氮共渗;通过将成形体加热到大于或等于850℃且小于930℃的初级淬火温度然后将成形体冷却至小于或等于ms点的温度,对经碳氮共渗的成形体进行初级淬火;通过将成形体加热到大于或等于a1点且小于850℃的次级淬火温度然后将成形体冷却到小于或等于ms点的温度,对经初级淬火的成形体进行次级淬火。在轴承部件的制造方法中,初级淬火温度大于或等于860℃且小于或等于880℃,并且次级淬火温度大于或等于820℃且小于或等于840℃。发明的有益效果根据本发明,可提供:具备足以承受在外来物质介入的环境下使用的韧性和耐磨性、使用上述包含能形成碳氮化物的元素的钢材料且与常规的轴承部件相比以低成本制造的轴承部件;滚动轴承;和轴承部件的制造方法。附图说明图1是示出第一实施方式的滚动轴承和轴承部件的剖面图。图2说明了第一实施方式的轴承部件的制造方法中的热处理方法。图3是示出实施例1的试样1的内环中的碳和氮的浓度分布的图。图4是示出实施例1的试样2的内环中的碳和氮的浓度分布的图。图5示出了实施例1的试样1的内环的表面的电子显微镜图像。图6示出了实施例1的试样1的滚子的表面的电子显微镜图像。图7示出了实施例1的试样2的内环的表面的电子显微镜图像。图8示出了实施例1的试样2的滚子的表面的电子显微镜图像。图9示出了实施例1的试样1的内环的表面的光学显微镜图像。图10示出了实施例1的试样1的滚子的表面的光学显微镜图像。图11示出了实施例1的试样2的内环的表面的光学显微镜图像。图12示出了实施例1的试样2的滚子的表面的光学显微镜图像。图13是示出实施例1的样品1和2的耐磨性测试结果的图。图14是示出实施例1的样品3和4的夏比冲击试验结果的图。图15是示出在实施例1的试样3和4的各滚动轴承的润滑油中引入外来物质时的寿命测试结果的图。图16是第二实施方式的轴承部件的俯视图。图17是图16的沿xvii-xvii的剖面图。图18是图17的区域xviii的放大图。图19是示出第二实施方式的轴承部件的制造方法的流程图。图20是示出第二实施方式的轴承部件的制造方法中的加热模式的图。图21是第二实施方式的滚动轴承100的剖面图。图22是示出试样5中的epma的碳浓度和氮浓度的测定结果的图。图23是示出试样7中的epma的碳浓度和氮浓度的测定结果的图。图24是试样5的表面附近的电子显微镜图像。图25是试样6的表面附近的电子显微镜图像。图26是试样7的表面附近的电子显微镜图像。图27是试样8的表面附近的电子显微镜图像。图28是试样6的表面附近的ebsd图像。图29是试样8的表面附近的ebsd图像。图30是试样5的表面附近的光学显微镜图像。图31是试样7的表面附近的光学显微镜图像。图32是示出试样5和试样7的表面附近中的属于第三组和第五组的马氏体块的平均粒径的图。图33是示出试样6和试样8的表面附近中的属于第三组和第五组的马氏体块的平均粒径的图。图34是示出试样5和试样7的表面附近中的属于第三组和第五组的马氏体块的平均纵横比的图。图35是示出试样6和试样8的表面附近中的属于第三组和第五组的马氏体块的平均纵横比的图。图36是示出试样9和试样10的夏比冲击试验结果的图。图37是进行夏比冲击试验后试样9的缺口侧表面的电子显微镜图像。图38是进行夏比冲击试验后试样10的缺口侧表面的电子显微镜图像。图39是示出试样11和试样12的滚动疲劳测试结果的图。图40是示出试样13和试样14的磨损测试结果的图。实施方式的描述下面参考附图描述本发明的实施方式。应当注意,在下面描述的附图中,相同或相应的部分被赋予相同的附图标记,并且不再重复描述。<第一实施方式的滚动轴承的配置>如图1所示,第一实施方式的滚动轴承1主要包括外环10、内环11、滚珠12、和保持器13。外环10、内环11、和滚珠12均对应于本实施方式的轴承部件。应当注意,滚动轴承1例如是如图1所示的深槽滚珠轴承,但不限于此。滚动轴承1可以是径向滚珠轴承如角接触球轴承,或可以是推力球轴承、径向滚子轴承、或推力滚子轴承。外环10具有环状形状并且在其内周面上具有外环滚道面10a。内环11具有环状形状并且在其外周面上具有内环滚道面11a。内环11位于相对于外环10的内周侧,使得内环滚道面11a面向外环滚道面10a。外环10和内环11均由铬钼钢构成(scm),如scm435。滚珠12位于外环10的内周面。滚珠12例如沿外环10和内环11的圆周方向的环状滚道上以预定的节距通过保持器13并排放置。滚珠12被保持器13所保持,以便可在滚道上滚动。滚珠12具有滚珠滚动接触面12a并在滚珠滚动接触面12a上与外环滚道面10a和内环滚道面11a接触。滚珠12由scm、如scm435构成。保持器13由例如包括合成树脂的材料构成。通过具有这种构造,深槽滚珠轴承1的外环11和内环11可彼此相对转动。<轴承部件的具体配置>从外环10的外环滚道面10a起小于或等于0.5mm深度的表面区域10b的碳浓度高于从外环滚道面10a起大于0.5mm深度的外环10的内部区域的碳浓度。从外环10的外环滚道面10a起小于或等于0.5mm深度的表面区域10b的氮浓度高于外环10的内部区域的氮浓度。由选自碳化物、氮化物、碳氮化物的至少一种构成的化合物颗粒(析出化合物)存在于外环10的外环滚道面10a。外环滚道面10a中的析出化合物的面积率大于或等于3%。外环滚道面10a中的析出化合物的平均粒径小于或等于0.3μm。析出化合物包括铁(fe)和铬(cr)并主要包括(fe,cr)3(c,n)。外环10的表面区域10b具有从外环滚道面10a向10μm深度延伸的外环浅层区域,且外环浅层区域具有大于或等于0.7重量%的平均碳浓度。外环浅层区域的平均氮浓度大于或等于0.2重量%。应当注意浅层区域中的平均碳浓度(或平均氮浓度)通过epma(电子探针微分析)对垂直于滚道面或滚动接触面的深度方向的剖面进行线性分析来计算的。浅层区域中的平均碳浓度(或平均氮浓度)被计算为从滚道面或滚动接触面起到10μm深度的碳浓度(或氮浓度)的平均值。外环10的外环滚道面10a的原奥氏体晶粒的平均粒径小于或等于8μm。从内环11的内环滚道面11a起小于或等于0.5mm深度的表面区域11b的碳浓度高于从内环滚道面11a起大于0.5mm深度的内环11的内部区域的碳浓度。从内环11的内环滚道面11a起小于或等于0.5mm深度的表面区域11b的氮浓度高于内环11的内部区域的氮浓度。由选自碳化物、氮化物、碳氮化物的至少一种构成的析出化合物存在于内环11的内环滚道面11a。内环滚道面11a中的析出化合物的面积率大于或等于3%。内环滚道面11a中的析出化合物的平均粒径小于或等于0.3μm。析出化合物包括铁(fe)和铬(cr)并主要包括(fe,cr)3(c,n)。内环11的表面区域11b具有从内环滚道面11a向10μm深度延伸的内环浅层区域,且内环浅层区域具有大于或等于0.7重量%的平均碳浓度。内环浅层区域的平均氮浓度大于或等于0.2重量%。内环11的内环滚道面11a的原奥氏体晶粒的平均粒径小于或等于8μm。从滚珠12的滚珠滚动接触面12a起小于或等于0.5mm深度的表面区域12b的碳浓度高于从滚珠滚动接触面12a起大于0.5mm深度的滚珠12的内部区域的碳浓度。从滚珠12的滚珠滚动接触面12a起小于或等于0.5mm深度的表面区域12b的氮浓度高于滚珠12的内部区域的氮浓度。由选自碳化物、氮化物、碳氮化物的至少一种构成的析出化合物存在于滚珠12的滚珠滚动接触面12a。滚珠滚动接触面12a中的析出化合物的面积率大于或等于3%。滚珠滚动接触面12a中的析出化合物的平均粒径小于或等于0.3μm。析出化合物包括铁(fe)和铬(cr)并主要包括(fe,cr)3(c,n)。滚珠12的表面区域12b具有从滚珠滚动接触面12a向10μm深度延伸的滚珠浅层区域,且滚珠浅层区域具有大于或等于0.7重量%的平均碳浓度。滚珠浅层区域的平均氮浓度大于或等于0.2重量%。滚珠12的滚珠滚动接触面12a的原奥氏体晶粒的平均粒径小于或等于8μm。从外环10的外环滚道面10a起到外周面的厚度例如大于或等于10mm。从内环11的内环滚道面11a起到内周面的厚度例如大于或等于10mm。滚珠12的直径例如大于或等于10mm。应当注意各个滚道面和滚动接触面中的析出化合物的平均粒径例如可由各个滚道面和滚动接触面的电子显微镜图像计算出。各个滚道面和滚动接触面中的原奥氏体晶粒的平均粒径例如可由各个滚道面和滚动接触面的光学显微镜图像计算出。在本说明书中,术语“平均粒径”是指足够数量(例如,20)颗粒的粒径的算术平均。而且,各个滚道面和滚动接触面中的析出化合物的面积率是指在各个滚道面和滚动接触面中具有预定的表面积的区域中的析出化合物的总表面积与该区域的表面积之比。各个滚道面和滚动接触面中具有预定的表面积的区域是指当使用例如显微镜等观察各个滚道面和滚动接触面时观察视野中的区域。析出化合物的总表面积是从相对于具有观察区域的表面成90°±2°的方向(大致垂直的方向)看观察区域时,所确认到的析出化合物在与该方向上垂直的平面上的投影面积的总和。<轴承部件和滚动轴承的制造方法>在第一实施方式的滚动轴承1的制造方法中,首先形成作为外环10、内环11、和滚珠12的各成形体(工序(s10))。在该工序(s10)中,具有预定的形状的各个成形体通过对scm材料进行机械加工来形成。作为机械加工方法,可以使用任何方法,例如切割或压力加工。接着,如图2所示对成形体进行热处理。图2的水平方向代表热处理工序中的经过时间。这表明越往右侧则经过更多时间。图2的垂直方向表示热处理工序中成形体的加热温度。这表明越往上则温度越高。在热处理工序中,首先,作为加工目标的成形构件被碳氮共渗(工序(s20))。在该工序(s20)中,上一工序(s10)中准备的成形体在吸热转化气体如r气体中引入氨(nh3)气的气氛中,被加热到大于或等于930℃且小于或等于940℃的碳氮共渗温度t1。碳氮共渗温度t1是大于或等于a1点的温度。加热和保持时间例如大于或等于10小时且小于或等于15小时。该工序(s20)中的气氛例如使用气氛中一氧化碳(co)的量、二氧化碳(co2)的量、和未分解的nh3的量来控制,以使得未分解的氨的量(不分解且存在于气氛中的nh3气体的量)达到大于或等于0.1体积%。因此,包括由此碳氮共渗的成形体的表面的区域的碳浓度和氮浓度变得高于该成形体的其它区域的碳浓度和氮浓度。接着,在热处理工序中,对经碳氮共渗的成形体进行氮扩散处理(工序(s25))。在该工序(s25)中,在之前的工序(s20)中被碳氮共渗的成形体在吸热转化气体如r气体中引入氨(nh3)气的气氛中被加热并保持为碳氮共渗温度t1。加热和保持时间例如大于或等于5小时且小于或等于10小时。与上述碳氮共渗工艺相同,该工序(s25)中的气氛例如使用气氛中一氧化碳(co)的量、二氧化碳(co2)的量、和未分解的nh3的量来控制,以使得未分解的氨的量达到大于或等于0.1体积%。对于下式(1)和(2)所定义的α,氮扩散处理中的α被控制为低于碳氮共渗工艺中的α。pco:一氧化碳的分压(atm)二氧化碳的分压(atm)的平衡常数接着,在热处理工序中,对经碳氮共渗的成形体进行初级淬火(工序(s30))。在该工序(s30)中,在之前的工序(s25)中经过氮扩散处理的成形体在不包括氨气体的气氛中被加热并在以小于碳氮共渗温度t1但足够高于a1点的初级淬火温度t2下保持预定的时间,然后冷却到小于或等于ms点的温度范围。此时,在之前的工序(s25)中被加热到碳氮共渗温度t1的成形体被加热到初级淬火温度t2而没有被冷却到小于a1点的温度。初级淬火温度t2是高于通常的淬火温度850℃的温度,以抑制主要由(fe,cr)3(c,n)构成的析出化合物变得过大。初级淬火温度t2例如大于或等于860℃且小于或等于880℃。初级淬火温度t2例如为870℃。加热和保持时间例如大于或等于0.5小时且小于或等于2小时。冷却例如为油冷却。接着,在热处理工序中,对经过初级淬火的成形体进行次级淬火(工序(s40))。在该工序(s40)中,在之前的工序(s30)中被淬火硬化的成形体被加热并保持为大于或等于a1点且小于初级淬火温度t2的次级淬火温度t3,然后冷却至小于或等于ms点的温度。次级淬火温度t3小于850℃。次级淬火温度t3例如大于或等于820℃且小于或等于840℃。次级淬火温度t3例如为830℃。加热时间例如大于或等于1小时且小于或等于2小时。冷却例如为油冷却。接着,在热处理工序中,进行回火工艺(工序(s50))。在该工序(s50)中,在之前的工序(s40)中被淬火硬化的成形体被加热到小于或等于a1点的回火温度t4,由此进行回火处理。回火温度t4例如大于或等于150℃且小于或等于350℃。回火温度t4例如为180℃。加热和保持时间例如大于或等于0.5小时且小于或等于5小时。通过以上工序,完成热处理工序。接着,对经过热处理工序的成形体进行精加工(工序(s60))。在该工序(s60)中,例如对成形体的表面进行抛光这样的精加工。应当注意精加工的加工量、即相对于成形体的表面的作为机械部件表面的位置的深度例如为250μm。这样,制造作为第一实施方式的轴承部件的外环10、内环11、和滚珠12。接着,组装外环10、内环11、和滚珠12(工序(s70))。在该工序(s70)中,组装分别准备的外环10、内环11、滚珠12、和保持器13。这样,制造如图1所示的深槽滚珠轴承1。<功能和效果>第一实施方式的轴承部件的制造方法包括:准备由铬钼钢构成的成形体(s10);通过在包括氨的碳氮共渗气氛下将成形体加热到大于或等于930℃且小于或等于940℃,对成形体进行碳氮共渗(s20);通过将成形体加热到大于850℃且小于930℃的初级淬火温度然后将成形体冷却至小于或等于ms点的温度,对经碳氮共渗的成形体进行初级淬火(s30);通过将成形体加热到大于或等于a1点且小于850℃的次级淬火温度然后将成形体冷却到小于或等于ms点的温度,对经初级淬火的成形体进行次级淬火(s40)。优选地,在由轴承钢构成的轴承部件的制造方法中,初级淬火温度t2高于通常的初级淬火温度850℃,例如大于或等于860℃且小于或等于880℃。通过如此设置初级淬火温度t2,可抑制由scm材料构成的轴承部件中的上述析出化合物变得过大。优选地,在由轴承钢构成的轴承部件的制造方法中,次级淬火温度t3低于通常的初级淬火温度850℃,例如大于或等于820℃且小于或等于840℃。在次级淬火处理时的成形体中,以固态溶于其基础材料中的碳和氮的浓度下降到低于初级淬火处理时的浓度,使得上述析出化合物不易形成。为了解决该问题,通过将次级淬火温度t3设置在上述数值范围内,可形成大量的微细析出化合物。本发明人确认通过第一实施方式的轴承部件的制造方法得到的外环10、内环11、和滚珠12均具有如下特征(具体参见以下的实施例1)。由碳化物、氮化物、和碳氮化物中的至少一个构成的析出化合物存在于外环滚道面10a、内环滚道面11a、和滚珠滚动接触面12a。外环滚道面10a、内环滚道面11a、和滚珠滚动接触面12a中的析出化合物的面积率大于或等于3%。该值高于由用于渗碳的钢构成、且通过常规的热处理工序制造的常规的轴承部件。而且,析出化合物的平均粒径小于或等于0.3μm。该值小于常规的轴承部件。因此,与常规的轴承部件相比,这样的外环10、内环11、和滚珠12具有更高的耐磨性。即使在外来物质介入的环境下使用,外环滚道面10a、内环滚道面11a、和滚珠滚动接触面12a也不易损坏、具有长寿命。而且,第一实施方式的外环10、内环11、和滚珠12由scm材料构成且因此与使用包含可形成碳氮化物的元素的上述钢材料的常规的轴承部件相比,以更低的成本制造。在上述轴承部件中,原奥氏体晶粒的平均粒径小于或等于8μm。该值小于常规的轴承部件。因此,与常规的轴承部件相比,这样的外环10、内环11、和滚珠12具有更高的韧性。应当注意,在由用于渗碳的钢构成的常规的轴承部件中,为了增加碳化物和氮化物的析出以提高耐磨性,需要更高的可形成碳氮化物的元素含量。但是,随着可形成碳氮化物的元素的含量变高,轴承部件的韧性趋于降低。因此,在常规的轴承部件中,难以兼具足以承受在外来物质介入的环境的韧性和耐磨性。另一方面,在如上所述的外环10、内环11、和滚珠12中,与常规的轴承部件相比,大量上述析出化合物存在于表面区域10b、11b、12b,原奥氏体晶粒微细。因而,同时实现了足以承受在外来物质介入的环境的韧性和耐磨性。因此,即使在外来物质介入的环境下,外环10、内环11、和滚珠12也均具有长寿命。而且,在轴承部件中,析出化合物由包括(fe,cr)3(c,n)的材料构成。在轴承部件中,从外环滚道面10a、内环滚道面11a、和滚珠滚动接触面12a向10μm深度延伸的浅层区域具有大于或等于0.7重量%的平均碳浓度,且具有大于或等于0.2重量%的平均氮浓度。这些值大于或等于常规的轴承部件。这表明与常规的轴承部件相比,在轴承部件中,在浅层区域中大量析出碳化物、氮化物、碳氮化物中的至少2种。<变形例>外环10、内环11、和滚珠12的至少一个可由scm材料构成,碳氮化物可在滚道面和滚动接触面中析出,碳氮化物的面积率可大于或等于3%,且碳氮化物的平均粒径可小于或等于0.3μm。[实施例1]以下描述了为确认本公开的轴承部件和滚动轴承的效果而进行的实验<试样1>试样1是根据第一实施方式的轴承部件的制造方法生产的。具体而言,首先,准备由jis中的scm435构成的成形体并将其成形为滚动轴承的内环的形状。接着,依次对成形体进行碳氮共渗处理、初级淬火处理、次级淬火处理、和回火处理。在碳氮共渗处理中,使用r气体和nh3气体的混合气体,碳氮共渗处理温度设为大于或等于930℃且小于或等于940℃,加热和保持时间设为13小时。碳氮共渗处理中的炉内气氛使用气氛中一氧化碳(co)的量、二氧化碳(co2)的量、和nh3的量来控制。co的量设为大于或等于11体积%且小于或等于17体积%,co2的量设为大于或等于0.05体积%且小于或等于0.15体积%,并且nh3的量设为大于或等于0.1体积%且小于或等于0.3体积%。在扩散处理处理中,使用r气体和nh3气体的混合气体,扩散处理温度设为大于或等于930℃且小于或等于940℃,加热和保持时间设为6小时。与碳氮共渗处理相同,扩散处理中的炉内气氛使用气氛中一氧化碳(co)的量、二氧化碳(co2)的量、和nh3的量来控制。co的量设为大于或等于11体积%且小于或等于17体积%,co2的量设为大于或等于0.05体积%且小于或等于0.15体积%,并且nh3的量设为大于或等于0.1体积%且小于或等于0.3体积%。氮扩散处理中的α被控制为低于碳氮共渗处理的α。在初级淬火处理中,初级淬火温度设为870℃且加热和保持时间设为1小时。对于冷却,使用油冷却。在次级淬火处理中,次级淬火温度设为830℃且加热和保持时间设为1.5小时。对于冷却,使用油冷却。在回火处理中,回火温度设为180℃且加热和保持时间设为3小时。对于冷却,使用空气冷却。对经过上述热处理的成形体进行精加工。对于精加工,进行机械抛光。抛光量设为150μm。<试样2>作为比较例,根据常规的轴承部件的制造方法生产试样2。具体而言,首先,准备由jis中的scm435构成的成形体并将其成形为滚动轴承的外环、内环、和滚子的分别的形状。接着,依次对成形体进行碳氮共渗处理,淬火处理、和回火处理。在碳氮共渗处理中,使用r气体和nh3气体的混合气体,碳氮共渗处理温度设为大于或等于930℃且小于或等于940℃,加热和保持时间设为8小时。碳氮共渗处理中的炉内气氛使用气氛中一氧化碳(co)的量、二氧化碳(co2)的量、和nh3的量来控制。co的量设为大于或等于16体积%且小于或等于22体积%,co2的量设为大于或等于0.2体积%且小于或等于0.4体积%,并且nh3的量设为大于或等于0.1体积%且小于或等于0.3体积%。在扩散处理处理中,使用r气体和nh3气体的混合气体,扩散处理温度设为大于或等于930℃且小于或等于940℃,加热和保持时间设为4小时。扩散处理中的炉内气氛使用气氛中一氧化碳(co)的量、二氧化碳(co2)的量、和nh3的量来控制。co的量设为大于或等于16体积%且小于或等于22体积%,co2的量设为大于或等于0.2体积%且小于或等于0.4体积%,并且nh3的量设为大于或等于0.1体积%且小于或等于0.3体积%。氮扩散处理中的α被控制为低于碳氮共渗处理的α。在淬火处理中,淬火温度设为870℃且加热和保持时间设为1小时。对于冷却,使用油冷却。在回火处理中,回火温度设为180℃且加热和保持时间设为3小时。对于冷却,使用空气冷却。对经过上述热处理的成形体进行精加工。对于精加工,进行机械抛光。抛光量设为150μm。<评价>(1)电子探针显微分析仪(epma)分析使用epma来评价试样1和2的内环的表面区域中的碳浓度分布和氮浓度分布。图3示出了试样1的内环的分析结果,而图4示出了试样2的内环的分析结果。图3和图4的横轴代表从其表面起的深度[单位:mm],而图3和图4的纵轴代表碳和氮浓度[单位:重量%]。如图3所示,在作为本公开的实施例的试样1中,在从表面起向0.5mm深度延伸的表面区域中确认到碳浓度和氮浓度中的大量尖峰。因此,确认大量由碳化物、氮化物、和碳氮化物的至少一个构成的析出化合物存在于表面区域,且析出化合物的粗大被抑制。而且,在试样1中,确认到:从表面起向10μm深度延伸的浅层区域的平均碳浓度大于或等于0.7重量%且小于或等于1.2重量%;且浅层区域的平均氮浓度大于或等于0.2重量%且小于或等于0.4重量%。而且,在试样1中,确认渗碳深度和氮化深度约大于或等于1.0mm且小于或等于1.5mm。如图4所示,在作为本公开的比较例的试样2中,在从表面起向0.5mm深度延伸的表面区域中没有确认到碳浓度和氮浓度中的大量尖峰。确认没有大量由碳化物、氮化物、和碳氮化物的至少一个构成的析出化合物存在于试样2的表面区域。而且,在试样2中,确认到:从表面起向10μm深度延伸的浅层区域的平均碳浓度大于或等于0.7重量%且小于或等于0.8重量%;且浅层区域的平均氮浓度大于或等于0.2重量%且小于或等于0.4重量%。而且,在试样2中,确认渗碳深度和氮化深度约大于或等于1.0mm且小于或等于1.5mm。而且,根据epma分析,确认试样1的析出化合物主要是(fe,cr)3(c,n)。鉴于以上结果,确认:试样1具有可比肩试样2的渗碳深度和氮化深度;与试样2相比,大量析出化合物(fe,cr)3(c,n)存在于试样1的表面区域中。(2)电子显微镜观察使用电子显微镜观察试样1和2的内环和滚子的表面。图5示出了试样1的内环的电子显微镜图像,图6示出了试样1的滚子的电子显微镜图像。图7示出了试样2的内环的电子显微镜图像,图8示出了试样2的滚子的电子显微镜图像。如图5和图6所示,确认试样1的表面中存在大量平均粒径大于或等于0.2μm且小于或等于0.3μm的析出化合物。而且,确认图5和图6中的析出化合物的总表面积与视野面积的比例(面积率)大于或等于3%且小于或等于10%。如图7和图8所示,确认试样2的表面中存在少量平均粒径大于或等于0.1μm且小于或等于0.2μm的析出化合物。而且,确认图7和图8中的析出化合物的总表面积与视野面积的比例(面积率)约为1%。鉴于以上结果,确认与试样2相比,试样1中存在大量析出化合物。而且,确认试样1的大量的析出化合物具有微细结构。(3)光学显微镜观察使用光学显微镜观察试样1和2的内环和滚子的表面。图9示出了试样1的内环的光学显微镜图像,图10示出了试样1的滚子的光学显微镜图像。图11示出了试样2的内环的光学显微镜图像,图12示出了试样2的滚子的光学显微镜图像。如图9和图10所示,确认到:试样1的表面中的原奥氏体晶粒的粒径大于或等于1μm且小于或等于10μm;其平均粒径大于或等于4μm且小于或等于8μm。如图11和图12所示,确认到:试样2的表面中的原奥氏体晶粒的粒径大于或等于5μm且小于或等于10μm;其平均粒径大于或等于12μm且小于或等于25μm。鉴于以上结果,确认试样1中的原奥氏体晶粒比试样2微细。还确认试样1中的原奥氏体晶粒的粒径变化小于试样2。(4)磨损测试使用省力型磨损测试机在以下样品中进行磨损测试:用作本发明实施例的样品1,通过与上述试样1相同的方法制备;用作本发明比较例的样品2,通过与上述试样2相同的方法制备。样品1和2均具有平板状的形状。样品1和2具有0.010μm的表面粗糙度ra。测试中的荷重设为50n,样品和对应材料的相对速度设为0.05m/s,测试时间设为60分钟,使用美孚维萝斯油3号(注册商标)(vg2)作为润滑油。根据样品在测试后的磨损量,计算特定磨损量,评价耐磨性。图13示出了样品1和2的特定磨损量[单位:×10-10mm3/n·m]。如图13所示,确认样品1的特定磨损量降低至样品2的特定磨损量的约20%。与本公开的上述实施例的试样1相同,认为样品1具有高耐磨性,因为与样品2相比,样品1的表面区域中存在大量微细析出化合物。(5)夏比冲击试验根据jisz2242,对以下样品进行夏比冲击试验:用作本公开实施例的样品3,通过与上述试样1相同的方法制备;用作本公开比较例的样品4,通过与试样2相同的方法制备。样品3和4中设有u形缺口,其缺口深度为2mm,缺口底部曲率半径为1mm。图14示出了样品3和4的夏比冲击值[单位:j/cm2]。如图14所示,确认样品3的夏比冲击值是样品4的1.5倍或更高,具有高韧性。因此,样品3具有这样的高韧性大概是由于如下原因:与上述试样1相同,样品3的表面区域中存在粒径上变化更小的微细的原奥氏体晶粒。(6)外来物质介入的润滑条件下的滚动疲劳寿命测试对如下锥形滚子轴承进行外来物质介入的润滑条件下的滚动疲劳寿命测试:用作本公开的实施例的试样3的锥形滚子轴承,通过与上述试样1相同的方法和jis30206制备;用作本公开的比较例的试样4的锥形滚子轴承,通过与上述试样2相同的方法和jis30206制备。在该寿命测试中,外环被固定,内环以2000rpm的旋转速度在以下条件下旋转:使用油浴润滑,用涡轮机油vg56作为润滑油;荷重设为17kn;外环温度设为65℃。然后,检查从测试开始到剥落发生的一段时间(寿命)并进行统计分析,以计算l10寿命和l50寿命。l10寿命是累积破损概率为10%时的寿命,l50寿命是累积破损概率为50%时的寿命。图15示出了作为本公开的实施例的试样3和作为比较例的试样4的寿命测试的结果。图15横轴代表寿命[单位:时间],而图15的纵轴代表累积破损概率[单位:%]。如图15所示,在比较例中,l10寿命是38小时且l50寿命是76小时,而在本公开的实施例中,l10寿命是89小时且l50寿命是152小时。确认本公开的实施例的滚动疲劳寿命是比较例的滚动疲劳寿命的两倍或以上。与试样1和样品1、3相同,认为本公开的实施例具有比较例的2倍或以上滚动疲劳寿命是因为与比较例相比,本公开的实施例具有更高的耐磨性和更高的韧性。(第二实施方式的轴承部件)以下描述第二实施方式的轴承部件的配置。图16是第二实施方式的轴承部件的俯视图。图17是图16的沿ii-ii的剖面图。如图16和图17所示,第二实施方式的轴承部件例如是深槽滚珠轴承的内环110。第二实施方式的轴承部件不限于此。第二实施方式的轴承部件例如可以是深槽滚珠轴承的外环,或者可以是深槽滚珠轴承的滚动元件。内环110由铬钼钢构成。用于内环110的铬钼钢例如是属于jis(jisg4053:2008)中规定的scm钢的钢。用于内环110的铬钼钢可以是jis中规定的scm435。内环110具有表面。更具体地,内环110具有内周面110a和外周面110b。内周面110a是安装有轴杆的一侧的表面。外周面110b是构成内环110的滚道面的表面。图18是图17的区域iii的放大图。如图18所示,内环110在其表面(外周面110b)具有扩散层111。扩散层111是氮和碳浓度比内环110的铬钼钢中的氮和碳浓度高的部分。扩散层111例如具有大于或等于1mm且小于或等于1.5mm的深度d。扩散层111包含多个化合物颗粒(析出化合物)和多个马氏体块。化合物颗粒是铁(fe)碳化物、铁氮化物、或铁碳氮化物的晶粒。更具体地,化合物颗粒是化合物的晶粒,其中铬代替部分渗碳体(fe3c)的铁部位,并且氮(n)取代其部分碳(c)部位(即,由(fe,cr)3(c,n)表示的化合物)。扩散层111中的化合物颗粒的平均粒径小于或等于0.3μm。扩散层111中的化合物颗粒的平均粒径优选小于或等于0.25μm。扩散层111中的化合物颗粒的面积率大于或等于3%。扩散层111中的化合物颗粒的面积率优选大于或等于8%。扩散层111中的化合物颗粒的面积率例如小于或等于10%。应当注意,扩散层111中的化合物颗粒的平均粒径和面积率通过如下方法测定。首先,对扩散层111的剖面进行抛光。其次,对抛光的表面进行腐蚀。再次,对腐蚀的抛光表面进行sem(扫描电子显微镜)图像捕获(在下面的描述中,通过sem图像捕获获得的图像将被称为“sem图像”)。应当注意,捕获sem图像以包括足够数量(大于或等于20)的化合物颗粒。第四,进行图像处理以获得sem图像,从而计算sem图像中每个化合物颗粒的面积和化合物颗粒的总面积。在化合物颗粒的等效圆直径与化合物颗粒的面积之间建立以下关系:π×(化合物颗粒的等效圆直径)2/4=化合物颗粒的面积。因此,通过计算通过将sem图像中的每个化合物颗粒的面积除以4/π而获得的值的平方根,计算sem图像中的每个化合物颗粒的等效圆直径。在扩散层111中的化合物颗粒的平均粒径由通过将sem图像中的化合物颗粒的等效圆直径的总和除以sem图像中的化合物颗粒的数量而获得的值表示。扩散层111中的化合物颗粒的面积率由通过将sem图像中的化合物颗粒的总面积除以sem图像的面积而获得的值表示。每个马氏体块是由晶体取向一致的晶体构成的马氏体相的块。马氏体相是通过使具有以固态溶解在其中的碳的铁的奥氏体相淬火而获得的非平衡相。当第一马氏体相的块的晶体取向和与第一马氏体相的块相邻的第二马氏体相的块的晶体取向之间的偏差大于或等于5°时,则第一马氏体相的块和第二马氏体相的块是不同的马氏体块。另一方面,当第一马氏体相的块的晶体取向和与第一马氏体相的块相邻的第二马氏体相的块的晶体取向之间的偏差小于5°时,则第一马氏体相的块和第二马氏体相的块构成一个马氏体块。扩散层111中的马氏体块的最大粒径小于或等于3.8μm。扩散层111中的马氏体块的最大粒径大于或等于3.6μm。包含在扩散层111中的小于或等于1μm的结晶粒径的马氏体块构成第一组。构成第一组的马氏体块的面积率相对于包含在扩散层111中的马氏体块的总面积优选大于或等于0.55且小于或等于0.75。包含在扩散层111中的马氏体块可被分为第二组和第三组。属于第二组的马氏体块的结晶粒径的最大值可小于包括在第三组中的马氏体块的结晶粒径的最小值。属于第三组的马氏体块的总面积除以包含于扩散层111中的马氏体块的总面积而得的值可大于或等于0.5。具有最大结晶粒径且属于第三组的马氏体块以外的属于第三组的马氏体块的总面积除以包含于扩散层111中的马氏体块的总面积而得的值可小于0.5。从不同的角度来看,包括在第二组中的马氏体块和属于第三组的马氏体块按以下方法分类。即,首先,马氏体块从具有最小结晶粒径起依次分配给第一组,并且相对于马氏体块的总面积,依次计算分配给第二组的马氏体块的总面积。第二,当分配给第二组的马氏体块的总面积相对于马氏体块的总面积的比例达到不超过50%的极限时,停止将马氏体块分配给第二组。第三,未分配给第二组的马氏体块被分配给第三组。优选地,包括在第三组中的马氏体块的平均粒径可大于或等于0.7μm且小于或等于1.4μm。优选地,包括在第三组中的马氏体块的平均纵横比可大于或等于2.5且小于或等于2.8。包含在扩散层111中的马氏体块可被分为第四组和第五组。属于第四组的马氏体块的结晶粒径的最大值可小于包括在第五组中的马氏体块的结晶粒径的最小值。属于第五组的马氏体块的总面积除以包含于扩散层111中的马氏体块的总面积而得的值可大于或等于0.7。具有最大结晶粒径且属于第五组的马氏体块以外的属于第五组的马氏体块的总面积除以包含于扩散层111中的马氏体块的总面积而得的值可小于0.7。从不同的角度来看,包括在第四组中的马氏体块和属于第五组的马氏体块按以下方法分类。即,首先,马氏体块从具有最小结晶粒径起依次分配给第四组,并且相对于马氏体块的总面积,依次计算分配给第四组的马氏体块的总面积。第二,当分配给第四组的马氏体块的总面积相对于马氏体块的总面积的比例达到不超过30%的极限时,停止将马氏体块分配给第四组。第三,未分配给第四组的马氏体块被分配给第五组。优选地,包括在第五组中的马氏体块的平均粒径可大于或等于0.7μm且小于或等于1.1μm。优选地,包括在第五组中的马氏体块的平均纵横比可大于或等于2.4且小于或等于2.6。使用ebsd(电子背散射衍射)方法测定扩散层111中马氏体块的结晶粒径和马氏体块的纵横比。首先,基于ebsd方法,捕获扩散层111中的剖面图像(下文中,称为“ebsd图像”)。应当注意,捕获ebsd图像以包括足够数量(大于或等于20)的马氏体块。基于ebsd图像,指定相邻马氏体相的块的晶体取向的偏差。藉此,指定每个马氏体块的边界。其次,根据指定的马氏体块的边界,计算ebsd图像中每个马氏体块的面积和形状。更具体地,通过计算通过将ebsd图像中的每个马氏体块的面积除以4/π而获得的值的平方根,计算ebsd图像中的每个马氏体块的等效圆直径。ebsd图像中马氏体块的等效圆直径的最大值被认为是扩散层111中马氏体块的最大粒径。基于如上所述计算的每个马氏体块的等效圆直径,确定ebsd图像中的马氏体块中的属于第一组的马氏体块。通过将ebsd图像中的马氏体块的总面积除以ebsd图像中的马氏体块中属于第一组的马氏体块的总面积而获得的值被视为通过将扩散层111中的属于第一组的马氏体块的总面积除以扩散层111中的马氏体块的总面积而获得的值。基于如上所述计算的每个马氏体块的等效圆直径,ebsd图像中的马氏体块被分为第二组和第三组(或分为第四组和第五组)。通过将在ebsd图像中分类为第三组(或第五组)的马氏体块的数量除以在ebsd图像中分为第三组(或第五组)的马氏体块的等效圆直径的总和而获得的值被视为在扩散层111中属于第三组(或属于第五组)的马氏体块的平均晶粒尺寸。根据ebsd图像中每个马氏体块的形状,ebsd图像中的每个马氏体块的形状通过最小二乘方法被近似为椭圆形。通过最小二乘方法近似成椭圆是根据s.biggin和d.j.dingley,《应用结晶学杂志(journalofappliedcrystallography)》,(1977)10,376-378中描述的方法进行的。通过将椭圆形状中的长轴尺寸除以短轴尺寸,计算ebsd方法图像中的每个马氏体块的纵横比。通过将在ebsd图像中分类为第三组(或第五组)的马氏体块的纵横比的总和除以在ebsd图像中分类为第三组(或第五组)的马氏体块的数量而获得的值被认为是在扩散层111中属于第三组(或属于第五组)的马氏体块的平均纵横比。多个原奥氏体晶粒包含在扩散层111中。应当注意,每个原奥氏体晶粒是由在保持工序s41和保持工序s51中形成的奥氏体晶粒的晶粒边界(原奥氏体晶界)限定的区域。原奥氏体晶粒的平均粒径优选小于或等于8μm。原奥氏体晶粒的平均粒径更优选小于或等于6μm。应当注意,扩散层111中的原奥氏体晶粒的平均粒径通过如下方法测定。首先,对扩散层111的剖面进行抛光。其次,对抛光的表面进行腐蚀。再次,对腐蚀的抛光表面进行光学显微镜图像捕获(在下面的描述中,通过光学显微镜图像捕获获得的图像将被称为“光学显微镜图像)。”应当注意,捕获光学显微镜图像以包括足够数量(大于或等于20)的原奥氏体晶粒。第四,对得到的光学显微图像进行图像处理,从而计算光学显微镜图像中每个原奥氏体晶粒的面积。因此,通过计算通过将光学显微镜图像中的每个原奥氏体晶粒的面积除以4/π而获得的值的平方根,计算光学显微镜图像中的每个原奥氏体晶粒的等效圆直径。在扩散层111中的原奥氏体晶粒的平均粒径由通过将光学显微镜图像中的原奥氏体晶粒的等效圆直径的总和除以光学显微镜图像中的原奥氏体晶粒的数量而获得的值表示。内环110的表面(外周面110b)与距离内环110的表面相距10μm的位置之间的扩散层111中的平均碳浓度优选大于或等于0.7质量%。内环110的表面(外周面110b)与距离内环110的表面相距10μm的位置之间的扩散层111中的平均碳浓度优选小于或等于1.2质量%。内环110的表面(外周面110b)与距离内环110的表面相距10μm的位置之间的扩散层111中的平均氮浓度优选大于或等于0.2质量%。内环110的表面(外周面110b)与距离内环110的表面相距10μm的位置之间的扩散层111中的平均氮浓度优选小于或等于0.4质量%。内环110的表面(外周面110b)与距离内环110的表面相距10μm的位置之间的扩散层111中的平均碳浓度和平均氮浓度使用epma(电子探针显微分析仪)测定。(第二实施方式的轴承部件的制造方法)以下描述第二实施方式的轴承部件的制造方法。图19是示出第二实施方式的轴承部件的制造方法的流程图。如图19所示,第二实施方式的轴承部件的制造方法包括准备工序s1、碳氮共渗工序s2、扩散工序s3、初级淬火工序s4、次级淬火工序s5、回火工序s6、和后处理工序s7。在准备工序s1中,准备通过碳氮共渗工序s2、扩散工序s3、初级淬火工序s4、次级淬火工序s5、回火工序s6、和后处理工序s7以加工成内环110的处理目标构件。处理目标构件由铬钼钢构成,例如jis中规定的scm钢类型之一。在碳氮共渗工序s2中,对处理目标构件的表面进行碳氮共渗。碳氮共渗工序s2通过将处理目标构件在预定的温度(以下称为“第一保持温度”)的炉子中保持预定的时间(以下称为“第一保持时间”)来进行。对于炉内气氛,例如使用包含吸热转化气体(r气体)和氨(nh3)的气体。第一保持温度例如大于或等于930℃且小于或等于940℃。第一保持时间例如大于或等于10小时且小于或等于15小时。在扩散工序s3中,在碳氮共渗工序s2中经由处理目标构件的表面而被引入的碳和氮被扩散到处理目标构件的内部。扩散工序s3通过将处理目标构件在预定的温度(以下称为“第二保持温度”)的炉子中保持预定的时间(以下称为“第二保持时间”)来进行。对于炉内气氛,例如使用包含吸热转化气体(r气体)和氨(nh3)的气体。第二保持温度例如大于或等于930℃且小于或等于940℃。第二保持时间例如大于或等于5小时且小于或等于10小时。扩散工序s3中,上述式(1)和(2)所定义的α被调整为低于碳氮共渗工序s2。从上述式(1)和(2)显而易见,通过调节气氛中的一氧化碳的量,二氧化碳的量和未分解的氨的量来进行α的调节。应当注意,气氛中的未分解的氨的量优选大于或等于0.1体积%。在初级淬火工序s4中,对处理目标构件进行淬火。初级淬火工序s4包括保持工序s41和冷却工序s42。保持工序s41通过将处理目标构件在预定的温度(以下称为“第三保持温度”)的炉子中保持预定的时间(以下称为“第二保持时间”)来进行。应当注意,在初级淬火工序s4中,炉内气氛中不包含氨。第三保持温度是大于或等于钢的a1转变点、且小于第一保持温度和第二保持温度的温度。第三保持温度例如大于或等于850℃且小于930℃。优选地,第三保持温度大于或等于860℃且小于或等于880℃。第三保持时间例如大于或等于0.5小时且小于或等于2小时。在冷却工序s42中,对处理目标构件进行冷却。冷却工序s42例如通过油冷却进行。在次级淬火工序s5中,对处理目标构件进行淬火。次级淬火工序s5包括保持工序s51和冷却工序s52。保持工序s51通过将处理目标构件在预定的温度(以下称为“第四保持温度”)的炉子中保持预定的时间(以下称为“第四保持时间”)来进行。应当注意,在次级淬火工序s5中,炉内气氛中不包含氨。第四保持温度是大于或等于处理目标构件的钢的a1转变点、且小于第三保持温度的温度。第四保持温度例如大于或等于处理目标构件的钢的a1转变点、且小于或等于850℃。第四保持温度优选大于或等于820℃且小于或等于840℃。第四保持时间例如大于或等于1小时且小于或等于2小时。在冷却工序s52中,对处理目标构件进行冷却。冷却工序s52例如通过油冷却进行。扩散层111中的化合物颗粒主要在保持工序s41和保持工序s51中析出。随着保持温度变高,钢中碳和氮各自的固溶极限增加(随着保持温度变低,钢中碳和氮各自的固溶极限降低)。为了避免保持工序s41中在扩散层111中析出的化合物颗粒变得过大,第三保持温度被设为高于通常的淬火中的保持温度(第三保持温度被设为与通常的淬火相比相对地增加钢中碳和氮的固溶极限)。在保持工序s51中,化合物颗粒已经在保持工序s41中析出。也就是说,在保持工序s51中,基础材料中的碳浓度和氮浓度被降低,与保持工序s41相比,化合物颗粒不易析出。因此,为了促进保持工序s51中通过降低钢中的氮和碳的固溶极限而引起的化合物颗粒的析出,第四保持温度被设为低于第三保持温度。因此,扩散层111中的化合物颗粒的面积率可大于或等于3%。而且,通过将第四保持温度设为低于第三保持温度,可抑制保持工序s41和保持工序s51中析出的化合物颗粒的粗大化,由此扩散层111中的化合物颗粒的平均粒径可小于或等于0.3μm。在保持工序s41和保持工序s51中,通过如上所述析出的大量微细化合物颗粒的钉扎效应,奥氏体晶粒的成长被抑制,由此奥氏体晶粒保持微细。关于马氏体转变,一个奥氏体晶粒中形成多个马氏体块。从另一个角度看,一个马氏体块不会以横跨多个奥氏体晶粒的方式形成。因此,奥氏体晶粒越是微细,则其中包括的马氏体块也越微细。在回火工序s6中,对处理目标构件进行回火。回火工序s6通过将将处理目标构件在预定的温度(以下称为“第五保持温度”)的炉子中保持预定的时间(以下称为“第五保持时间”)后进行冷却来实施。第五保持温度是小于或等于处理目标构件的钢的a1转变点的温度。第五保持温度例如大于或等于150℃且小于或等于350℃。第四保持时间例如为0.5小时至5小时。回火工序s6冷却例如通过空气冷却来进行。图20是示出第二实施方式的轴承部件的制造方法中的加热模式的图。图20示意性地示出第一保持温度~第五保持温度和第一保持时间~第五保持时间的关系。在后处理工序s7中,对处理目标构件进行后处理。在后处理工序s7中,例如进行处理目标构件的清洗、处理目标构件的机械加工如研磨或抛光等。以如上所述的方式,制造第二实施方式的轴承部件。(第二实施方式的滚动轴承的配置)以下描述第二实施方式的滚动轴承100的配置。图21是第二实施方式的滚动轴承100的剖面图。如图21所示,滚动轴承100例如是深槽滚珠轴承。但是,第二实施方式的滚动轴承100不限于此。第二实施方式的滚动轴承100例如可以是锥形滚子轴承。第二实施方式的滚动轴承100具有内环110、外环120、滚动元件130、和保持器140。内环110的配置如上所述。外环120由铬钼钢构成。外圈120中使用例如jis中规定的scm钢。用于外环120的铬钼钢例如是jis中规定的scm435。外环120具有内周面120a和外周面120b。内周面120a构成外环120的滚道面。内环110和外环120以使外周面110b面向内周面120a的方式设置。扩散层121设置在外环120的表面(内周面120a)中。扩散层121具有与扩散层111相同的配置。滚动元件130由铬钼钢构成。滚动元件130使用例如jis中规定的scm钢。用于滚动元件130的铬钼钢例如是jis中规定的scm435。滚动元件130设置为可在外周面110b和内周面120a之间滚动。滚动元件130具有球形。滚动元件130具有表面130a。表面130a构成滚动元件130的滚动接触面。扩散层31设于滚动元件130的表面130a。扩散层31具有与扩散层111相同的配置。应当注意,外周面110b、内周面120a、和表面130a中不需要都设置扩散层。扩散层可设于外周面110b、内周面120a、和表面130a中的至少一个。保持器140例如由树脂材料构成。保持器140具有环状形状。保持器140设于内环110和外环120之间。保持器140设有多个通孔。通孔在从内周面朝向外周面的方向上延伸穿过保持器140。通孔在保持器140的圆周方向上以等间隔设置。滚动元件130设于通孔内。因此,在圆周方向上的相邻滚动元件130之间的空间得以保持。(第二实施方式的轴承部件和第二实施方式的滚动轴承的效果)以下描述第二实施方式的轴承部件和第二实施方式的滚动轴承100的效果。第二实施方式的轴承部件由铬钼钢构成。因此,在第二实施方式的轴承部件中,合金元素的含量相对低,由此抑制钢材料成本的增加和处理成本的增加。由于扩散层111中的化合物颗粒的平均粒径小于或等于0.3μm且扩散层111中的化合物颗粒的面积率大于或等于3%,扩散层111中分散有大量相对微细的化合物颗粒。因此,由于化合物颗粒的钉扎效应,扩散层111中的原奥氏体晶粒变得微细,结果是扩散层111中的马氏体块也变得微细。随着分散大量具有相对高硬度微细的化合物颗粒以及随着马氏体块的结晶粒径变得更微细,扩散层111的硬度和韧性进一步提高。因此,第二实施方式的轴承部件可确保轴承部件的耐磨性和韧性,同时抑制合金元素的含量增加导致的钢材料成本的增加和处理成本的增加。当扩散层111中属于第一组的马氏体块的总面积除以马氏体块的总面积而得的值大于或等于0.55且小于或等于0.75时,扩散层111中具有小于或等于1.0μm的结晶粒径的微细马氏体块的比例变得相对高。因此,在该情况下,可进一步提高轴承部件的耐磨性和韧性。当扩散层111中属于第三组的马氏体块的平均粒径大于或等于0.7μm且小于或等于1.4μm时,扩散层111中微细马氏体块的比例变得相对高。因此,在该情况下,可进一步提高轴承部件的耐磨性和韧性。马氏体块具有越小的纵横比(纵横比越接近1),则马氏体块越不会成为应力集中源。因此,当扩散层111中属于第三组的马氏体块的平均纵横比大于或等于2.5且小于或等于2.8时,则轴承部件的韧性可进一步提高。当扩散层111中属于第五组的马氏体块的平均粒径大于或等于0.6μm且小于或等于1.1μm时,扩散层111中微细马氏体块的比例变得相对高。因此,在该情况下,可进一步提高轴承部件的耐磨性和韧性。当扩散层111中属于第五组的马氏体块的平均纵横比大于或等于2.4且小于或等于2.6时,则轴承部件的韧性可进一步提高。一个奥氏体晶粒产生多个马氏体块,且一个马氏体块不会以跨越多个奥氏体晶粒的方式形成。因此,原奥氏体晶粒的结晶粒径变得越小,则晶粒中形成的马氏体块的结晶粒径变得越小。因此,当扩散层111中原奥氏体晶粒的平均粒径小于或等于8μm时,扩散层111中马氏体块的粒径可更微细,由此可进一步提高轴承部件的耐磨性和韧性。第二实施方式的滚动轴承100中,外周面110b、内周面120a、和表面130a中的至少一个设有与扩散层111的配置相同的扩散层。因此,第二实施方式的滚动轴承100可确保滚动轴承的耐磨性和韧性,同时抑制合金元素的含量增加导致的钢材料成本的增加和处理成本的增加。[实施例2]下面描述用于确认第二实施方式的轴承部件和第二实施方式的滚动轴承100的效果而进行的实验(下文中,称为“本实验”)。<试样>本试验中使用试样5~试样8。用于试样5~试样8的钢是示于表1的scm435。试样5和试样7是锥形滚子轴承的内环,而试样6和试样8是锥形滚子轴承的锥形滚子。[表1]如表2所示,试样5~试样8在第一保持温度大于或等于930℃且小于或等于940℃且第一保持时间为13小时的条件下进行碳氮共渗工序s2。试样5~试样8在第二保持温度大于或等于930℃且小于或等于940℃且第二保持时间为6小时的条件下进行扩散工序s3。应当注意,碳氮共渗工序s2和扩散工序s3中,气氛中一氧化碳的量、二氧化碳的的量、和氨的量分别大于或等于11体积%且小于或等于17体积%、大于或等于0.05体积%且小于或等于0.15体积%、大于或等于0.1体积%且小于或等于0.3体积%。试样5~试样8在第三保持温度为870℃且第三保持时间为1小时的条件下进行初级淬火工序s4。试样5和试样6在第四保持温度为830℃且第四保持温度为1.5小时的条件下进行次级淬火工序s5。而且,试样5~试样8在第五保持温度为180℃且第五保持时间为3小时的条件下进行回火工序s6。作为后处理工序s7,试样5~试样8均以150μm的抛光量被机械抛光。[表2]试样1,试样2试样3,试样4第一保持温度(℃)930~940930~940第一保持时间(h)1313第二保持温度(℃)930~940930~940第二保持时间(h)66第三保持温度(℃)870870第三保持时间(h)11第四保持温度(℃)830-第四保持时间(h)1.5-第五保持温度(℃)180180第五保持时间(h)33<碳浓度和氮浓度的测定>图22是示出试样5中的epma的碳浓度和氮浓度的测定结果的图。图23是示出试样7中的epma的碳和氮浓度的测定结果的图。应当注意,图22和图23中,横轴代表试样5和试样7的从表面起的距离(单位:mm),而纵轴代表碳浓度和氮浓度(单位:质量%浓度)。如图22所示,在试样5的表面附近,碳浓度和氮浓度中确认到大量尖峰。由该结果,实验证实,微细的化合物颗粒如碳化物、氮化物、和碳氮化物在试样5的表面附近析出。而且,在试样5中,表面与距离表面10μm远的位置之间的区域中的平均碳浓度在大于或等于0.7%且小于或等于1.2%的范围内,该区域的平均氮浓度在0.2质量%以上且0.4质量%以下的范围内。另一方面,如图23所示,在试样6的表面附近,碳浓度和氮浓度中没有确认到大量尖峰。由该结果,实验证实,微细的化合物颗粒如碳化物、氮化物、和碳氮化物没有在试样7的表面附近析出。<结构观察>图24是试样5的表面附近的电子显微镜图像。图25是试样6的表面附近的电子显微镜图像。如图24和图25所示,在试样5和试样6的表面附近,确认到大量大于或等于0.2μm且小于或等于3.0μm的化合物颗粒析出。而且,在试样5和试样6的表面附近,确认化合物颗粒的平均粒径约为0.25μm。而且,在试样5和试样6的表面附近,确认化合物颗粒的面积率约为8%。图26是试样7的表面附近的电子显微镜图像。图27是试样8的表面附近的电子显微镜图像。如图26和图27所示,在试样7和试样8的表面附近,确认化合物颗粒的面积率约为1%。图28是试样6的表面附近的ebsd图像。如图28所示,在试样6的表面附近,确认马氏体块的最大粒径在大于或等于3.6μm且小于或等于3.8μm的范围内。而且,在试样6的表面附近,确认具有小于或等于2μm的结晶粒径的马氏体块占据了马氏体块面积的90%以上。而且,在试样6的表面附近,确认具有小于或等于1μm的结晶粒径的马氏体块占据了马氏体块面积的55%以上且75%以下。图29是试样8的表面附近的ebsd图像。如图29所示,在试样8的表面附近,确认马氏体块的最大粒径在大于或等于5.1μm且小于或等于7.3μm的范围内。而且,在试样8的表面附近,确认具有小于或等于2μm的结晶粒径的马氏体块占据了马氏体块面积的65%以上且80%以下。而且,在试样8的表面附近,确认具有小于或等于1μm的结晶粒径的马氏体块占据了马氏体块面积的35%以上且45%以下。图30是试样5的表面附近的光学显微镜图像。如图30所示,在试样5的表面附近,确认原奥氏体晶粒的平均粒径在大于或等于4μm且小于或等于8μm的范围内,原奥氏体晶粒的结晶粒径分布在大于或等于1μm且小于或等于10μm的范围内。图31是试样7的表面附近的光学显微镜图像。如图31所示,在试样7的表面附近,确认原奥氏体晶粒的平均粒径在大于或等于12μm且小于或等于25μm的范围内,原奥氏体晶粒的结晶粒径分布在大于或等于5μm且小于或等于100μm的范围内。图32是示出试样5和试样7的表面附近中的属于第三组和第五组的马氏体块的平均粒径的图。应当注意在图32中,纵轴代表平均粒径(单位:μm)。图33是示出试样6和试样8的表面附近中的属于第三组和第五组的马氏体块的平均粒径的图。应当注意在图33中,纵轴代表平均粒径(单位:μm)。如图32所示,在试样5的表面附近,属于第三组的马氏体块的平均粒径约为1.0μm。如图33所示,在试样6的表面附近,属于第三组的马氏体块的平均粒径约为0.9μm。由此,在试样5和试样6中,确认属于第三组的马氏体块的平均粒径在大于或等于0.7μm且小于或等于1.4μm的范围内。如图32所示,在试样5的表面附近,属于第五组的马氏体块的平均粒径约为0.8μm。如图33所示,在试样6的表面附近,属于第五组的马氏体块的平均粒径约为0.7μm。由此,在试样5和试样6中,确认属于第五组的马氏体块的平均粒径在大于或等于0.6μm且小于或等于1.1μm的范围内。另一方面,在试样7和试样8的表面附近,属于第三组的马氏体块的平均粒径分别为约1.7μm和约2.2μm。另一方面,在试样7和试样8的表面附近,属于第五组的马氏体块的平均粒径分别为约1.3μm和约1.5μm。图34是示出试样5和试样7的表面附近中的属于第三组和第五组的马氏体块的平均纵横比的图。应当注意在图34中,纵轴代表平均纵横比。图35是示出试样6和试样8的表面附近中的属于第三组和第五组的马氏体块的平均纵横比的图。应当注意在图35中,纵轴代表纵横比。如图34所示,在试样5的表面附近,属于第三组的马氏体块的平均纵横比约为2.8。如图35所示,在试样6的表面附近,属于第三组的马氏体块的平均纵横比约为2.8。由此,在试样5和试样6中,确认属于第三组的马氏体块的平均纵横比在大于或等于2.5且小于或等于2.8的范围内。如图34所示,在试样5的表面附近,属于第五组的马氏体块的平均纵横比约为2.6。如图35所示,在试样6的表面附近,属于第五组的马氏体块的平均纵横比约为2.6。由此,在试样5和试样6中,确认属于第五组的马氏体块的平均纵横比在大于或等于2.4且小于或等于2.6的范围内。另一方面,在试样7和试样8的表面附近,属于第三组的马氏体块的平均纵横比分别为约3.2和约3.5。另一方面,在试样7和试样8的表面附近,属于第五组的马氏体块的平均纵横比分别为约3.0和约3.1。<夏比冲击试验>对以下试样进行夏比冲击试验:以与如上所述的试样5和试样6相同的方法准备的试样9;以与如上所述的试样7和试样8相同的方法准备的试样10。夏比冲击试验根据jis(jisz2242:2005)进行。在试样9和试样10中,以具有2mm的缺口深度和1mm的缺口底部曲率半径的方式形成u形缺口。图36是示出试样9和试样10的夏比冲击试验结果的图。应当注意在图36中,纵轴代表夏比冲击值(单位:j/cm2)。如图36所示,确认试样9的夏比冲击值是试样10的夏比冲击值的1.5倍或更多。图37示出了夏比冲击试验后试样9的缺口侧表面的电子显微镜图像。图38示出了夏比冲击试验后试样10的缺口侧表面的电子显微镜图像。应当注意在图37和图38中,上侧对应于缺口侧。如图37所示,在试样9的夏比冲击试验之后的破碎表面中,观察到表明韧性断裂的发生的大量凹坑。另一方面,如图38所示,在试样10的夏比冲击试验之后的破碎表面上,确认这样的凹坑减少并且表现出脆性断裂引起的破碎表面。<外来物质介入的润滑条件下的滚动疲劳寿命测试>试样11和试样12在外来物质介入的润滑条件下进行滚动疲劳测试(下文中称为“滚动疲劳测试”)。试样11和试样12是jis30206的锥形滚子轴承。通过以与如上所述的试样5和试样6相同的方法准备用于试样11的内环、外环、和锥形滚子。通过以与如上所述的试样5和试样6相同的方法准备用于试样12的内环、外环、和锥形滚子。滚动疲劳测试中的润滑是使用涡轮机油vg56的油浴润滑。滚动疲劳测试中的荷重设为17kn,且外环温度设为65℃。在滚动疲劳测试中,外环固定,内环以旋转速度2000rpm的速度旋转。在滚动疲劳测试中,评价根据:l10寿命(当从测试开始到剥落发生的一段时间进行统计分析并且累积破损概率为10%的测试时间);l50寿命(当从测试开始到剥落发生的一段时间进行统计分析并且累积破损概率为50%的测试时间)。图39是示出试样11和试样12的滚动疲劳测试结果的图。应当注意在图39中,横轴代表寿命(单位:时间)且纵轴代表累积破损概率(单位:%)。如图39所示,在试样11中,l10寿命为89小时,且l50寿命为152小时。另一方面,在试样12中,l10寿命为38小时,且l50寿命为76小时。因此,确认试样11具有试样12的两倍或更多的滚动疲劳寿命。<磨损测试>对以下试样进行磨损测试:以与如上所述的试样5和试样6相同的方法准备的试样13;以与如上所述的试样7和试样8相同的方法准备的试样14。磨损测试使用省力型磨损测试机进行。试样13和试样14具有平板状的形状,且具有0.010μm的表面粗糙度(算术平均粗糙度)ra。测试中的荷重设为50n,与相对材料的相对速度设为0.05m/s。测试时间设为60分钟,使用美孚维萝斯油3号(注册商标)(vg2)作为润滑油。在磨损测试中,通过从已经通过试验的每个试样的磨损量计算特定磨损量来评估耐磨性。图40是示出试样13和试样14的磨损测试结果的图。图40中,纵轴代表特定磨损量(单位:10×10-10mm3/n·m)。如图40所示,试样13中的特定磨损量是试样14的特定磨损量的约20%。本文公开的实施方式和实施例在任何方面都是说明性的而非限制性的。由权利要求书而非上述的实施方式和实施例限定本发明的范围,并且旨在包括与权利要求书等同的范围和含义的任意修饰。附图标记清单10、120:外环;10a、120a:外环滚道面(内周面);10b、11b、12b:表面区域;11、110:内环;11a、110b:内环滚道面(外周面);12、130:滚珠(滚动元件);12a、130a:滚珠滚动接触面(表面);13、140:保持器;100:滚动轴承;111:扩散层;121:扩散层。当前第1页12