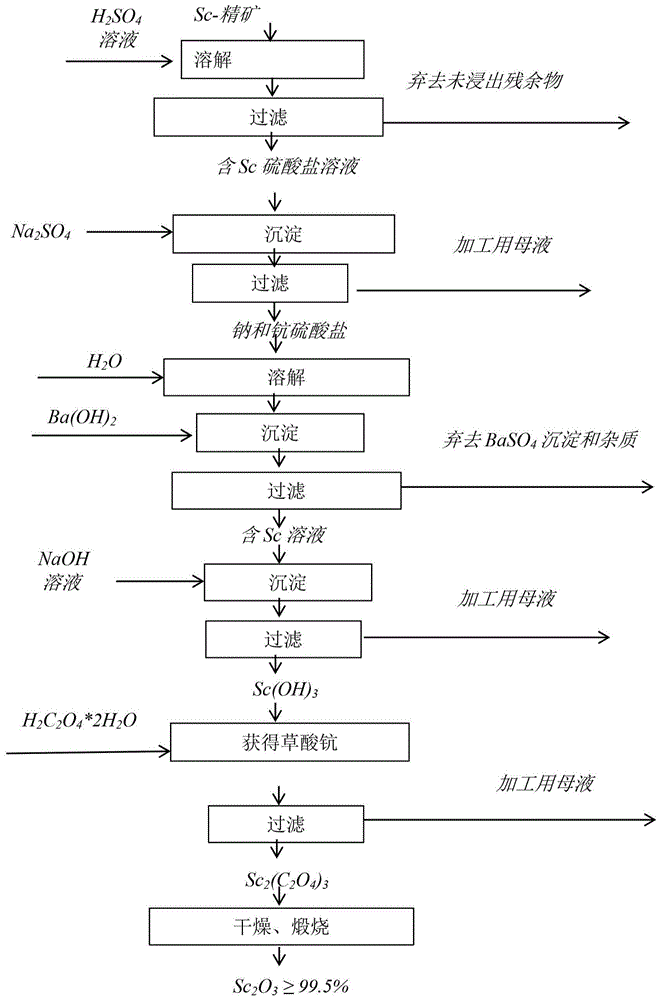
本发明涉及稀有金属冶金领域,具体涉及从含钪精矿生产氧化钪的方法,可用于各种来源的含钪精矿的加工。具体地,在加工钛铁矿精矿、铀矿石以及来自氧化铝生产的赤泥等期间同时获得的含钪精矿。氧化钪具有若干优点:氧化钪的强度在受热时增加,并在1030℃达到最大值。在含铝的合金中,钪提供了额外的强度、锻造性质、超延展性和高耐腐蚀性,因此,它在如航空航天工程、铁路运输制造、造船、石油和天然气生产等工业中的应用将不仅提高其技术和经济性能,而且创造出革命性的产品。存在已知的生产99%氧化钪的方法,该方法包括用nh4f溶液从氟化物含钪精矿中浸出钪,用结晶naf从浸出溶液中将钪以氟钪酸复盐的形式沉淀出,水解na-nh4双氟钪酸盐以生产氟化钪并在700℃的温度在空气流中将scf3转化成sc2o3。该方法允许在用nh4f溶液选择性浸出阶段从ca、mg、al、ti、y、ree、zr、na、u和th杂质中分离钪,以及在沉淀阶段从nh4f溶液中将钪以氟化物盐形式从ti、zr、u、fe和mg杂质中分离(专利ru2040471,1995年07月25日公开)。该方法的缺点在于通过使用昂贵的氟化物处理剂来实施该方法的高昂成本,以及在氟化钪转化为氧化钪期间气态氟化合物进入大气的可能性。专利ru2608033(2017年01月12日公开)描述了一种生产氧化钪的方法,该方法由以下事实构成:在用硝酸浸取含钪原料后获得残余酸度为5g/l-40g/l硝酸的含钪溶液,将该溶液送至具有强酸性阳离子交换剂固定层的柱中进行吸附,用盐水洗涤柱中的钪饱和的树脂,铈(iv)的浓度为1.5g/l至5.0g/l,硝酸的浓度为35g/l至80g/l,速度为3rph至30rph,温度为20℃至50℃,通过电化学方法对其进行氧化,其后进样至装有阳离子交换树脂的柱,将产生的含有从阳离子交换树脂置换的钪和杂质的洗涤液送去纯化除去杂质。洗涤后,用7n硝酸溶液处理阳离子交换树脂以除去残余的钪和杂质,然后将其送去通过真空蒸馏再生硝酸。将中等酸性的含钪洗涤溶液用氨水碱化成中性介质,钪与稀土金属、铁和铝的杂质一起以氢氧化物形式沉淀,将其过滤并在温度85℃溶解在硫酸溶液中,维持10g/l至15g/l硫酸的过度酸性,用氨水调节溶液的酸性至ph3-4,将得到的含钪溶液送去在转化为硫酸盐形式的强碱性阴离子交换树脂上进行吸附,钪和铁(iii)被吸附,而其它杂质保留在溶液中,将其进行氢氧化铈(iv)沉淀,并在石灰处理后复位。接着,用碳酸钠或铵溶液在ph10.1-10.8进行钪的脱附,从洗脱液中沉淀出氢氧化钪,将其过滤后干燥并煅烧得到最终产物——含65.1%钪的氧化钪。该方法的缺点在于多阶段工艺、在技术上使用昂贵的处理试剂和材料如铈盐、离子交换树脂、硝酸再生工艺,这在能量消耗和硬件设计方面相当昂贵。还有一种由贫钪精矿生产氧化钪的方法,该方法包括将含钪精矿溶解在硫酸中,除去酸不溶性沉淀,将滤液中硫酸的浓度提高到540g/dm3至600g/dm3,在氯化铵存在下在50-70℃的温度沉淀钪,然后在搅拌下暴露1-2小时,过滤,用乙醇洗涤沉淀,干燥并煅烧所得沉淀。产物是纯度为99.0%的可市售氧化钪sc2o3。从精矿到氧化物的钪提取率为97%至98%。钪的损失不超过2%至4%(专利ru2478725,2013年04月10日公开)。该方法的缺点是使用高浓度的硫酸溶液,这导致耐腐蚀设备的高成本,需要利用由硫酸钪煅烧产生的气态硫氧化物,以及使用昂贵的乙醇试剂洗涤硫酸钪的沉淀物。根据全部特征和目的,最接近所要求保护的方法是一种由含钪中间产品和精矿生产氧化钪的方法,包括:在80℃至120℃的温度将含钪精矿在浓度为250g/l至400g/l的盐酸溶液中溶解1-4小时,通过用硫酸和/或硫酸钠然后用氯化钡处理纯化钪溶液中的杂质,从钪溶液中分离沉淀,在加入到目标浓度为20g/dm3至100g/dm3的氢氧化钠或碳酸钠中时从溶液中沉淀出氢氧化钪,从溶液中分离出溶解性差的钪化合物的沉淀,用甲酸处理沉淀获得甲酸钪,将其洗涤、干燥并在700℃煅烧。过滤甲酸钪后,将母液送去再生甲酸并返回到氢氧化钪的处理阶段。该方法允许获得纯度高达99.99%的氧化钪,损失为2.5±0.5%(专利ru2257348,2005年7月27日公开)。该已知原型方法的一个显著缺点是由于在含钪精矿的浸出阶段使用盐酸溶液而导致组织该方法的高材料成本,这涉及对昂贵的耐酸设备的需求,以及对建立执行从母液中再生甲酸的工艺的附加技术单元的需求。本发明基于开发从各种来源的含钪精矿生产氧化钪的新方法的任务,其特征在于,通过使用允许最大限度地将钪提取到最终产物(氧化钪)中的一定顺序的技术阶段和模式,简化了工艺,降低了实施该方法的成本,并保持了高品质产物——氧化钪,而且选择性地将其与杂质分离,而不使用高价的处理剂和设备。根据所提出的方法,可以使用在加工钛铁矿精矿、铀矿石、来自氧化铝生产的赤泥以及其它含钪矿物和技术来源的同时获得的含钪精矿作为生产氧化钪的原料。起始精矿中氧化钪的含量应为至少1质量%sc2o3,其提供不小于99.5重量%的高纯度氧化钪。本发明的技术效果是解决了该问题,以更低的成本简化了实施获得高纯度氧化钪的方法的工艺。同时,重要的是不使用高浓度的酸溶液、昂贵的试剂和吸附剂,不实行试剂再生,不提供吸附和吸附剂再生单元,这可以显着地简化技术方案并降低工艺的运行和资金成本。在所提出的由含钪精矿生产氧化钪的方法中解决了该问题同时实现了技术效果,该方法包括以下步骤:将含钪精矿溶解在无机酸中以获得钪溶液;纯化获得的钪溶液以除去杂质;将沉淀从钪溶液中分离;用碱性试剂处理钪溶液;将钪化合物的沉淀从钪溶液中分离。在这种情况下,含钪精矿的溶解在ph为1.5-3.0、优选2.0-3.0的硫酸中进行以获得钪溶液,将该钪溶液与酸不溶性沉淀分离并用硫酸钠处理,同时将硫酸钠和钪的复盐沉淀,将其过滤、用硫酸钠溶液洗涤、溶解在水中并加入氢氧化钡或钡盐以沉淀杂质,滤出杂质沉淀,通过加入氢氧化钠在ph4.8-6.0从钪溶液中沉淀出氢氧化钪,滤出沉淀并用草酸溶液处理以获得草酸钪,将其从溶液中分离、用水洗涤、干燥并煅烧。如果在40℃至60℃的适宜温度用氢氧化钡或氯化钡处理钪溶液,在40℃至100℃的适宜温度沉淀氢氧化钪并保持1-10小时,并且在40℃至100℃的适宜温度用草酸处理氢氧化钪,氢氧化钪的处理用优选浓度为80g/dm3至100g/dm3的草酸进行,草酸钪的煅烧在700℃至900℃的适宜温度进行,则实现最大效率。初始含钪精矿中氧化钪的含量应为至少1质量%sc2o3,这提供了具有至少99.5重量%的高纯化的氧化钪的所提出方法。本发明与原型方法的主要非显而易见的区别是在含钪精矿的溶解阶段使用稀硫酸溶液,这允许降低溶液中杂质的提取度,同时保持溶液中钪的高提取度。另外,钪溶液中杂质的纯化是逐步进行的:首先,通过加入过量的结晶硫酸钠作为盐析剂来沉淀出硫酸钠钪复盐(同时锆、钛、铝杂质保留在母液中),然后将硫酸钠钪复盐溶解在水中,并通过加入氢氧化钡或其盐来沉淀残留在溶液中的fe(+3)和其它杂质的沉淀。与原型的另一个区别是在ph4.8-6.0的氢氧化钪沉积阶段,以及将工艺持续时间增加到至多2-12小时,以便将钪与稀土金属和其它金属的杂质进行高质量分离。与原型相反,用草酸溶液将从杂质中提纯的钪以草酸钪的形式沉淀,并送去干燥和煅烧。钪在ph2-3的硫酸溶液中的溶解过程允许实现溶液中钪的最大提取度,而杂质的提取最小。表1显示了ph对在硫酸盐溶液中从含钪精矿的钪提取度的影响的实验数据。ph降至小于2时,出现钪的提取度增加,且溶液中铁和铝杂质的量增加;ph增加到3以上时,观察到溶液中钪的提取度降低。在60℃至90℃进行从含有硫酸钪的溶液中以浓度为200g/dm3至400g/dm3的na2so4剂量沉淀硫酸钠钪复盐的工艺,然后冷却至室温,这是由于在60℃至90℃的温度观察到最大的硫酸钠钪复盐形成速率,并且在室温下钪化合物的溶解度最小而锆、钛和铝杂质具有显著溶解度。表2显示了复盐形成阶段溶液温度对冷却和过滤复盐沉淀后母液中钪浓度的影响。温度降低到低于60℃导致硫酸钠钪复盐的形成速率降低,这在随后冷却溶液和滤出复盐沉淀后导致钪随母液损失。就增加能量消耗而没有增加钪从溶液中提取到复盐沉淀中的效果而言,将温度增加到高于90℃是不切实际的。表2.复盐形成阶段溶液温度对冷却过滤复盐沉淀后母液中钪浓度的影响钪复盐形成阶段的溶液温度,℃5060708090溶液中sc2o3浓度,g/dm32.50.80.70.60.5通过在水中溶解硫酸钪钠复盐并加入结晶氢氧化钡以在溶液中达到1.5g/dm3至4g/dm3的浓度达2-4小时而进行从含钪溶液中沉淀杂质的工艺,其原因在于在将钪保持在溶液中的同时使铁杂质(+3)和其它元素的沉淀程度最大并最少地消耗氢氧化钡。随着沉积时间的减少,观察到溶液中杂质的量增加;随着工艺时间的增加,部分钪被吸附在杂质固体沉淀的表面上。在ph4.8-6.0和40-100℃的温度从在杂质与钡化合物共沉淀后获得的钪溶液中沉淀氢氧化钪,其原因在于在这些条件下rem杂质(稀土金属)保留在溶液中,钪尽可能多地转移到钪的固相。表3显示了研究在氢氧化钪沉积阶段ph对氧化钪终产物中rem含量以及滤出氢氧化钪沉淀后的母液中氧化钪的损失的影响的实验结果(在60℃进行1小时沉积过程)。表3.氢氧化钪沉积阶段ph对氧化钪终产物中稀土金属含量和氢氧化钪沉积阶段的氧化钪损失的影响表4显示了研究氢氧化钪的沉积时间对在ph5.5和60℃过滤氢氧化钪沉淀后母液中氧化钪损失的影响的实验结果。表4.氢氧化钪沉积持续时间对氢氧化钪沉积阶段氧化钪损失的影响通过用浓度为80g/dm3至100g/dm3的草酸在40℃至100℃处理氢氧化钪1-6小时来进行沉淀草酸钪的工艺,其原因在于在这些条件下草酸钪的溶解度最小,而从氢氧化物到草酸盐的转化程度最大且在草酸消耗最优。将草酸钪干燥并在700℃至900℃的温度煅烧1-5小时,在这些条件下,草酸钪完全分解,得到致密的细分散氧化钪沉淀。工艺温度和/或煅烧时间的增加会导致不合理的能量成本,工艺温度和/或煅烧时间的降低会导致产品品质下降。在含钪精矿中伴随钪的杂质组基本上不影响该方法。关键的是精矿中氧化钪的含量必须为至少1质量%。通过对由含钪精矿生产氧化钪的研究,由此确定了该方法基本实施的最佳方式,即:a)在硫酸溶液中溶解含钪精矿:-ph1.5-3.0,优选2.0-3.0;-工艺温度10℃-90℃,优选达20℃-60℃;b)沉淀硫酸钠钪复盐:-加入结晶硫酸钠,使na2so4浓度达到200g/dm3-300g/dm3;-该工艺的温度为60℃-90℃,优选70℃-80℃,然后冷却至室温;-将获得的硫酸钠-钪复盐沉淀过滤并用硫酸钠溶液洗涤;c)在水中溶解钪硫酸钠钪复盐:-工艺温度40℃-90℃,优选50℃-70℃;d)在添加钡化合物时沉淀杂质:-添加结晶氢氧化钡以达到在溶液中浓度为1.5g/dm3-4g/dm3,优选2g/dm3-2.5g/dm3;-沉积工艺的持续时间为2-6小时,优选3-4小时;e)沉淀氢氧化钪:-添加氢氧化钠溶液以达到4.8-6.0的ph;-工艺温度40℃-100℃,优选50℃-70℃;-过滤所得的氢氧化钪沉淀并用水洗涤;-沉积工艺的持续时间为2-12小时,优选6-10小时;f)沉淀草酸钪:-用浓度为80g/dm3-150g/dm3、优选95g/dm3-100g/dm3的草酸处理氢氧化钪;-工艺温度40℃-100℃,优选50℃-70℃;-沉积工艺的持续时间为1-6小时,优选2-4小时。g)煅烧草酸钙钪生产氧化钪:-工艺温度为700℃-900℃,优选750℃-850℃。-煅烧工艺的持续时间为1-5小时,优选1-3小时。由含钪精矿生产氧化钪的示意流程图如图1所示,由以下操作组成:-将含钪精矿溶解在硫酸溶液中;-过滤得到含钪硫酸盐溶液和精矿浸出残留物;-通过加入硫酸钠作为盐析剂沉淀硫酸钠钪复盐;-过滤得到硫酸钠钪复盐和加工用母液;-将硫酸钠钪复盐溶解在水中;-通过添加钡化合物从含钪溶液中沉淀杂质;-过滤以获得纯化的含钪溶液和杂质的固体沉淀;-用氢氧化钠溶液沉淀氢氧化钪;-过滤得到氢氧化钪和加工用母液;-通过用草酸处理氢氧化钪获得微溶草酸钪;-干燥并煅烧草酸钪,得到纯度≥99.3%的氧化钪。通过以下实例来证实所提出的方法的实施及其优于原型的优点。实施例取27.7g具有以下化学组成质量的含钪精矿(质量%):sc2o3:32.4;tio2:0.67;zro2:7.8;al2o3:0.28;fe2o3:1.7;水分含量49.3%;在将其溶解在200g的ph3硫酸溶液中2小时。过滤出酸不溶性沉淀,用硫酸钠(na2so4)(使其浓度达到280g/dm3)处理含钪溶液,形成沉淀的硫酸钠钪复盐。将所得沉淀滤出,用浓度为200g/dm3的硫酸钠溶液洗涤并溶解在水中。将0.8g氢氧化钡ba(oh)2加入到所得的含钪溶液中并在ph3.8保持5小时。过滤浆液,得到硫酸钡和杂质的沉淀以及含钪溶液,通过用45%氢氧化钠溶液处理从其中沉淀出氢氧化钪。滤出氢氧化钪的沉淀,用水洗涤并用10%的草酸溶液处理以获得草酸钪,将其从溶液中分离、用水洗涤、干燥并在850℃的温度煅烧2小时。得到sc2o3含量为99.5%的氧化钪。与杂质一起损失的钪总计约2%。因此,通过使用所提出的由含钪精矿生产氧化钪的方法,实现了98%的氧化钪提取度,获得纯度≥99.5质量%的氧化钪,同时简化了工艺并降低了实施该方法的成本,这是由于使用了允许将钪最大程度提取到最终产物(氧化钪)中并选择性地将钪与杂质分离并且不使用消耗性处理试剂和设备的一定顺序的技术阶段和模式。当前第1页12