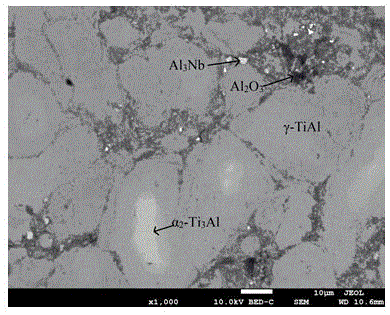
本发明涉及钛铝基复合材料的制备方法,尤其涉及一种粉末冶金钛铝基复合材料及其制备方法,属于高温结构材料加工
技术领域:
。
背景技术:
:目前,随着我国工业的高速发展,对材料的应用方面有着越来越高的要求,而钛铝基合金,作为一种新兴的金属化合物结构材料,拥有着高熔点、低密度、高比强度、高比模量等一系列的特点,除此之外,在高温下仍然能够保持足够高的强度和刚度,并且具有良好的抗蠕变及抗氧化性能等突出特点。这使其成为应用于航空、航天等高温
技术领域:
最具潜力的高温结构材料。钛铝基复合材料大多是通过传统的铸造方法来进行制备的,将钛粉和铝粉熔融之后直接进行合金化处理,而由此得到的铸态组织通常为粗大的树枝晶状,存在缩孔疏松和成分偏析,导致其脆性增大,室温延展性很低从而成形性很差,在使用过程中会影响性能,降低使用寿命,除此之外,传统的铸造方法所花费的成本很高,生产效益低,应用不广泛。因此需要找到一种可以代替铸造的制备方法,在更低的成本下得到性能更优良的钛铝基复合材料。粉末冶金法能够有效减少材料宏观偏析、细化晶粒,避免困难的铸锭开坯而直接进行常规锻造或轧制成型,目前是国内外研究的热点。如专利号cn201210131206.9公开了一种粉末冶金超细晶钛铝基合金板材的制备方法,采用旋转电极雾化法制取预合金,经过成形和烧结,制备得到钛铝基合金板材,但该方法中预合金法使用预合金粉末(一般为雾化法,旋转电极法制备),采用热压烧结、热等静压烧结、放电等离子烧结等强化烧结工艺进行致密化。预合金粉的制备对设备要求高,产量低,生产成本很高。并且预合金粉粒度一般较粗(30~200m),形貌为球形或类球形,比表面积小,烧结性能差,所以必须采用强化烧结工艺才能制备高致密度的合金材料,而这些烧结方法同样对设备要求高,成本高,限制了其应用范围。技术实现要素:针对上述现有技术的不足,本发明的目的在于提供一种粉末冶金钛铝基复合材料及其制备方法,解决现有制备方法存在成本高、工艺复杂、设备要求高和性能不佳等问题。为了解决上述技术问题,本发明采用了如下的技术方案:一种粉末冶金钛铝基复合材料,包括以下重量百分比的元素粉末组分:ti粉30.0~40.0%、tio2粉2.0~8.0%、nb2o5粉1.0~5.0%,余量为al粉。选择该配比能够直接使元素粉末通过高能球磨进行合金化形成γ-tial基体,并且原位合成质量分数约为10%~15%的弥散分布的第二相al2o3颗粒,无需通过外界添加第二相颗粒,也就不会污染复合材料之间的界面,提高复合材料界面的结合强度。生成的第二相al2o3颗粒能够细化tial组织颗粒,同时nb2o5颗粒的添加为复合材料增加了一定的室温延展性。上述粉末冶金钛铝基复合材料的制备方法,包括以下步骤:1)按元素粉末组分进行配料,然后将其放入真空球磨机,再添加钢球和球磨介质后进行高能球磨,使所述元素粉末完成合金化;2)将球磨合金化的粉末经干燥、放电等离子烧结后,即得到所述粉末冶金钛铝基复合材料。本发明采用放电等离子烧结(sps),该烧结方法是利用强脉冲电流作用来促进材料的固化,具有升温速度快,烧结温度低等特点,可有效降低tial合金的烧结温度,并且试样在高温阶段保温时间短,可有效减少由于柯肯达尔效应造成的材料致密度降低。另本发明中nb元素含量较小(不超过5%),其偏析不会对组织性能造成影响。优选的,所述钢球与元素粉末总量的质量比为3~5:1。优选的,所述球磨介质为无水乙醇,所述球磨机转速为250~500r/min。无水乙醇作为球磨介质,可以避免在球磨过程中物料粘结在钢球上,提高球磨效率,并且无水乙醇易挥发,有利于球磨后浆体在低温下而不被氧化干燥。优选的,所述球磨介质与元素粉末总量的质量比为3~5:1,球磨时间为2~6h。优选的,球磨介质与元素粉末总量的质量比为3:1,球磨时间为6h。球料比是磨球(球磨介质)的质量和物料(元素粉末总量)的质量之比,如果球料比太小,球磨强度达不到,球磨过程中的冲击磨碎效果达不到要求;若球料比太大,磨球之间、磨球和球磨罐之间的冲击和摩擦增加,会造成无用功损失,这不仅使球磨时的功耗增加,产量降低,而且会加剧球磨罐的磨损,增加金属消耗,消耗的金属也将作为杂质引入物料中,在相同的球磨时间来看,球料比为3:1已经达到要求。球磨时间会影响合金化和颗粒的细化程度,球磨过程中,粉末因摩擦、冲击,新的表面不断地暴露出来,且使粉体发生严重的变形而形成了高密度的位错等缺陷,提高了元素的自由能,最终实现纳米晶化和合金化。球磨时间过长或过短都达不到预期的效果。优选的,所述干燥温度为40~60℃,干燥25~40h。优选的,所述放电等离子烧结是在压力为40mpa的条件下,以80~100℃/min的升温速率升温到1000~1250℃,保温10min~30min,然后以300℃/min降温至室温。烧结压力与烧结体组织的致密度有很大的影响,烧结压力过高会使颗粒产生变形或者破碎,且对设备的要求更高;而烧结压力过低会使压坯密度不够,烧结体的致密化难以完成,导致颗粒之间存在孔隙,烧结块不易成型。因此本发明选择了一个设备能满足且能完成烧结体致密化的烧结压力40mpa。烧结温度过高或保温时间过长都会使晶粒粗大,降低复合材料的力学性能;烧结温度过低或保温时间过短会使烧结过程造成的内应力不能充分释放;而在本发明的烧结条件下能够得到晶粒细小性能优良的复合材料烧结块。sps烧结过程中降温速率为300℃/min,快速的降温可以很好的控制晶粒的长大,提高复合材料的力学性能。相比现有技术,本发明具有如下有益效果:1、本发明以元素粉末为原料,通过高能球磨就能够实现合金元素之间的合金化,制得钛铝基复合材料,本发明制备方法简单易操作,制备工艺流程简单,生产周期短,设备操作简便,原材料廉价易得,大大降低了生产成本,有利于工业化大规模生产,解决了预合金法存在成本高和设备要求高的问题,具有良好的应用前景和经济效益。2、本发明制备得到的钛铝基复合材料中,原位合成弥散分布的第二相al2o3颗粒以网状的方式分布在基体tial晶界上,al2o3作为增强相能细化钛铝合金组织,且原位合成的al2o3颗粒与基体的相容性好,不会污染复合材料之间的界面,使复合材料界面的结合强度得到提高,由此所得到的复合材料组织颗粒细小,可达到纳米级,分布也更加的均匀,所以与普通的钛铝基复合材料相比,本发明所制备的钛铝基复合材料具有更高的抗弯强度、抗压强度、硬度和界面强度,进而提高了其稳定性和耐磨性,实现了在成本低廉的情况下能够得到性能更为优良的钛铝基复合材料,其在高温结构材料领域具有更广泛地应用。附图说明图1为实施例1制备的钛铝基复合材料的显微组织图。具体实施方式下面结合实施例对本发明作进一步的详细说明。一、一种粉末冶金钛铝基复合材料的制备方法实施例1分别将粒度均为300目的24.0gti粉,30.0gal粉,4.8gtio2粉,3.0gnb2o5粉装入真空球磨机中,再加入180g钢球和60g无水乙醇进行高能球磨,转速为250r/min,球磨2h后粉末完成合金化;然后将合金化的粉末在50℃下真空干燥30h,再在压力为40mpa的条件下,将上述干燥后的混合粉末放入sps设备中烧结,以100℃/min的升温速率升温到1000℃,并保温10min后以300℃/min降温至室温,最终得到钛铝基复合材料。再将该复合材料制成试样后,得到预制样。将本实施例得到的钛铝基复合材料在扫描电子显微镜下观察,结果如图1所示。从图中可以看出,烧组织主要以灰色γ-tial相为基体,沿晶界分布的黑色相为al2o3颗粒、灰白部分为α2-ti3al相,在晶界处也分布有少量高亮白的al3nb颗粒。原位合成的增强相al2o3以网状的方式分布在基体tial晶界上,与普通的钛铝基复合材料相比,具有更好的界面强度、稳定性和高温性能。实施例2分别将粒度均为300目的18.0gti粉,40.0gal粉,1.2gtio2粉,0.6gnb2o5粉装入真空球磨机中,再加入300g钢球和60g无水乙醇进行高能球磨,球磨2h后粉末完成合金化;然后将合金化的粉末在60℃下真空干燥25h,再在压力为40mpa的条件下,将上述干燥后的混合粉末放入sps设备中烧结,以100℃/min的升温速率升温到1000℃,并保温10min后以300℃/min降温至室温,最终得到钛铝基复合材料。再将该复合材料制成试样后,得到预制样。实施例3分别将粒度均为300目23.0gti粉,33.0gal粉,3.5gtio2粉,0.8gnb2o5的粉装入真空球磨机中,再加入420g钢球和60g无水乙醇进行高能球磨,转速为250r/min,球磨2h后粉末完成合金化;然后将合金化的粉末在50℃下真空干燥30h,再在压力为40mpa的条件下,将上述干燥后的混合粉末放入sps设备中烧结,以100℃/min的升温速率升温到1000℃,并保温10min后以300℃/min降温至室温,最终得到钛铝基复合材料。再将该复合材料制成试样后,得到预制样。实施例4分别将粒度均为300目的20.0gti粉,37.0gal粉,2.0gtio2粉,1.0gnb2o5的粉装入真空球磨机中,再加入180g钢球和60g无水乙醇进行高能球磨,转速为250r/min,球磨2h后粉末完成合金化;然后将合金化的粉末在40℃下真空干燥40h,再在压力为40mpa的条件下,将上述干燥后的混合粉末放入sps设备中烧结,以80℃/min的升温速率升温到1250℃,并保温10min后以300℃/min降温至室温,最终得到钛铝基复合材料。再将该复合材料制成试样后,得到预制样。实施例5分别将粒度均为300目的20.0gti粉,36.0gal粉,1.8gtio2粉,0.8gnb2o5粉装入真空球磨机中,再加入180g钢球和60g无水乙醇进行高能球磨,转速为250r/min,球磨6h后粉末完成合金化;然后将合金化的粉末在50℃下真空干燥30h,再在压力为40mpa的条件下,将上述干燥后的混合粉末放入sps设备中烧结,以100℃/min的升温速率升温到1000℃,并保温10min后以300℃/min降温至室温,最终得到钛铝基复合材料。再将该复合材料制成试样后,得到预制样。二、产品检测1、对实施例1~5制备的钛铝粉进行组织特征测定,结果如表1所示。表1预制样颗粒平均尺寸(μm)分布均匀度实施例121.80.58实施例220.50.52实施例319.10.50实施例4220.60实施例520.80.72从表1可以看出,本发明的制备的钛铝基粉末颗粒细小均匀,且部分粉末颗粒尺寸可达到纳米级;且在实施例范围内,球料比越大,得到的钛铝基复合材料的分布均匀度越小,粒径变化范围越大;球磨时间越长,机械合金化粉体的分布均匀度越高。2、对实施例1~5的钛铝基复合材料制得的预制样的机械性能进行测定,结果如表2所示。表2预制样室温压缩性能/mpa硬度hv/mpa实施例11459490.4实施例21463475.1实施例31456487.9实施例41433480.6实施例51449489.7从表2可以看出,在合适的球磨参数下制备的预制样具有较高的室温压缩性和硬度值,进而提高了钛铝合金的硬度和耐磨性,这主要是由于通过原位生长的al2o3作为增强相能细化钛铝合金组织,提高了其机械性能。以上所述仅为本发明的较佳实施例而已,并不以本发明为限制,凡在本发明的精神和原则之内所作的任何修改、等同替换和改进等,均应包含在本发明的保护范围之内。当前第1页12