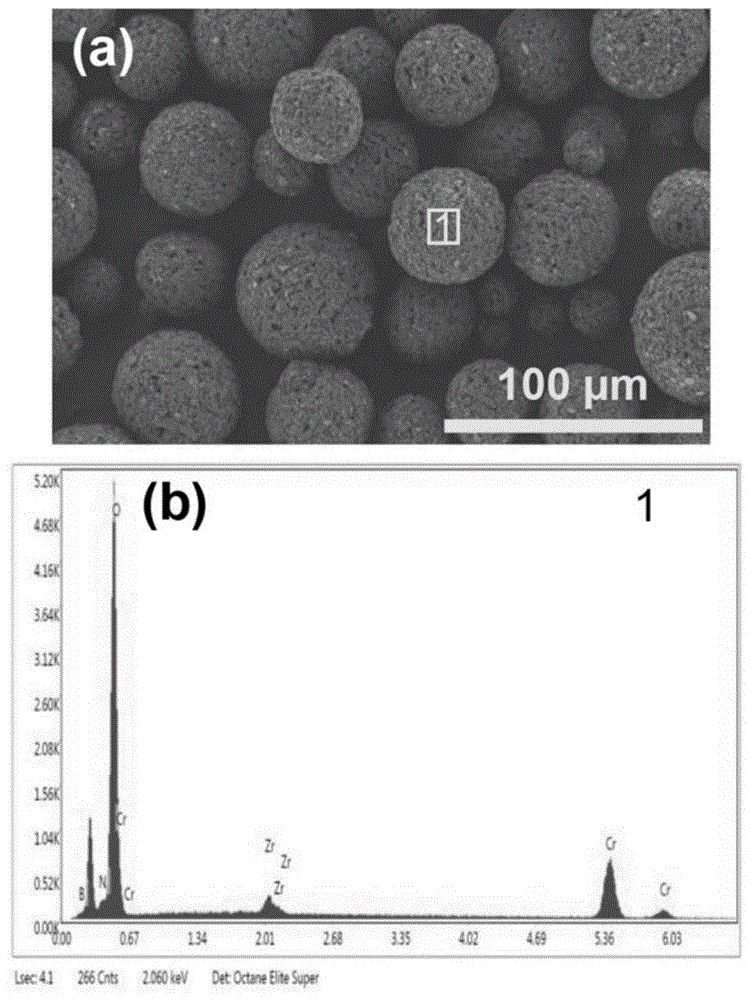
本发明涉及一种氧化铬基减磨涂层及其制备方法,属于耐磨涂层领域。
背景技术:
:近年来随着科学技术的迅猛发展,严苛工作环境的出现对耐磨涂层的要求也逐渐提高,部分无法使用润滑油或者高温下润滑油失效的服役情况下(如内燃机活塞与套筒之间),单相陶瓷涂层很难实现无油自润滑,因此设计一种干摩擦条件下具有优异的耐磨性能及低摩擦系数的减磨涂层显得很有必要。据报道,对比分析等离子喷涂硬质涂层wc-mo、cr3c2-mo、tic-mo及al2o3-tio2在干摩擦条件下的磨损性能时发现,无论是在25℃、425℃还是725℃,以上几种涂层的摩擦系数及磨损率均较高,无法获得实际应用。而cr2o3在某些工况下表现出良好的耐磨性(文献1b.q.wang,r.s.zheng,slidingwearofthermal-sprayedchromiacoatings,wear,1990,138:93-110.)。cr2o3陶瓷涂层作为一种传统的耐磨涂层,以其优异的综合性能,如高熔点、高硬度、优异的耐磨性及高温化学稳定性等在海事、化工及汽车等领域得到了广泛应用。j.h.ouyang等采用在cr2o3涂层中引入自润滑相caf2和ag2o,在从室温到800℃与al2o3球对磨来研究其摩擦学性能,结果显示室温下复合涂层的摩擦系数很高(0.75~0.82),随着温度的逐渐升高,复合涂层的摩擦系数逐渐降低(文献2j.h.ouyang,s.sasaki,effectsofdifferentadditivesonmicrostructureandhigh-temperaturetribologicalpropertiesofplasma-sprayedcr2o3ceramiccoatings,wear,2001,249:56-67.)。中caf2在低温下几乎没有润滑效果。六方氮化硼(h-bn)作为一种固体润滑剂,具有类似石墨一样的层状结晶结构,却不会像石墨那样带来黑色污染,空气中抗氧化温度高达900℃,明显优于石墨(450℃)和mos2(400℃),氮气或惰性气氛下使用温度高达2800℃,并且高温条件下润滑效果更为显著,应用前景广阔。在各种热喷涂技术中,大气等离子体喷涂技术具有等离子体焰流温度高,粉体沉积效率高,可喷涂材料广泛等特点,应用最为广泛,尤其适用于喷涂高熔点涂层材料。技术实现要素:本发明的目的旨在克服现有技术的不足,提供一种具有自润滑减磨特性的氧化铬基复合涂层及其制备方法。一方面,本发明提供了一种氧化铬基减磨涂层,所述氧化铬基减磨涂层的组成包括cr2o3主相、以及分散于所述cr2o3主相中的h-bn第二相,所述h-bn的含量为1~10wt.%,优选为1~7wt.%。本发明提供的氧化铬基复合涂层以cr2o3为主相,以及分散于所述cr2o3主相中具有自润滑性能的h-bn第二相。具有高硬度、良好的化学稳定性及耐磨性能。本案具有自润滑性能的h-bn晶体结构与石墨类似,在摩擦磨损过程中可以在涂层表面起到固体润滑,降低摩擦系数的作用,同时摩擦磨损过程中产生的摩擦热导致涂层表面散点温度升高,bn发生氧化反应生成b2o3,b2o3覆盖在涂层表面,保护涂层免受进一步磨损,从而起到减小摩擦系数和磨损率的作用。本发明提供的氧化铬基减磨涂层在摩擦磨损过程(室温下模拟环境测试)中所述h-bn第二相发生氧化反应生成以b2o3为主要成分的摩擦膜覆盖在涂层表面。较佳地,所述氧化铬基减磨涂层的厚度为100~500μm,优选为200~400μm。另一方面,本发明还提供了一种如上述的氧化铬基减磨涂层的制备方法,选用cr2o3-bn复合粉体作为原料,采用大气等离子喷涂技术在基体表面制备所述氧化铬基减磨涂层;所述大气等离子体喷涂工艺参数为:等离子体气体ar流量30~50slpm;等离子体气体h2流量为5~20slpm;送粉载气ar:2~7slpm;原料的送粉速率:10~25rpm;喷涂距离:100~150mm;喷涂功率为:30~55kw。较佳地,所述cr2o3-bn复合粉体的粒径分布范围为20~100μm。较佳地,所述cr2o3-bn复合粉体为含有cr2o3粉体和h-bn粉体的复合粉体,其制备方法包括:将cr2o3粉体和h-bn粉体,加入溶剂和粘结剂,得到浆料;将所得浆料再经喷雾造粒和干燥后,得到所述含有cr2o3粉体和h-bn粉体的复合粉体。较佳地,所述cr2o3粉体的粒径分布范围为1~8μm;所述h-bn粉体的粒径分布范围为1~8μm。较佳地,所述基体为金属基体、合金基体、石墨基体或碳/碳复合材料基体。又,较佳地,当基体为金属基体或合金基体时,所述基体表面带有nicr过渡层;当基体为石墨基体或碳/碳复合材料基体时,所述基体表面带有sic过渡层。又,较佳地,所述基体的表面经过预处理,所述预处理包括超声清洗和喷砂粗化。本发明中,所述氧化铬基减磨涂层是在纯cr2o3涂层的基础上进一步改性后制备得到,其改善了涂层的摩擦磨损性能。而且,所得涂层中的自润滑相(第二相)能够在摩擦磨损过程中在涂层表面起到润滑、降低摩擦系数的作用,具有良好的减磨耐磨性能。附图说明图1为实施例1中制备的cr2o3-5wt.%bn复合粉体的微观形貌图(a)及eds图(b);图2为实施例1中制备的cr2o3-5wt.%bn复合涂层的表面形貌图;图3为实施例1中制备的cr2o3-5wt.%bn复合涂层的截面形貌图;图4为实施例1中制备的cr2o3-5wt.%bn复合涂层与对比例1制备的纯cr2o3涂层在50n载荷分别与wc-co摩擦副对磨的平均摩擦系数(a)及磨损率(b)对比图;图5为实施例1中制备的cr2o3-5wt.%bn复合涂层与wc-co摩擦副对磨后磨损表面生成的摩擦膜截面形貌(a)和对应的元素分布图(o元素和b元素);图6为实施例2制备的cr2o3-10wt.%bn复合涂层与实施例1中制备的cr2o3-5wt.%bn复合涂层和对比例1中制备的纯cr2o3涂层在50n载荷分别与wc-co摩擦副对磨的平均摩擦系数(a)和磨损率(b)对比图;图7为对比例1中制备的纯cr2o3涂层的表面形貌图(a)和截面形貌图(b)。具体实施方式以下通过下述实施方式进一步说明本发明,应理解,下述实施方式仅用于说明本发明,而非限制本发明。本公开中,氧化铬基减磨涂层(也可称自润滑减磨涂层)以cr2o3为主相,利用cr2o3高硬度,优良的耐磨特性,使得涂层具有良好的耐磨性能;同时以h-bn为第二相(含量占1~10wt.%),h-bn的自润滑特性可以进一步降低涂层摩擦系数及磨损率,使涂层具有减磨特性,延长了涂层服役寿命。在可选的实施方式中,h-bn含量可为1~7wt.%。若是含量过量,bn可能会在涂层中存在团聚现象,由于bn本身硬度较低,在高载荷条件下,微裂纹易出现在bn富集区并在后续磨损过程中发生涂层剥落现象,导致涂层磨损率增高;同时由于涂层剥落引起涂层表面粗糙度增加,易导致涂层摩擦系数增加。在可选的实施方式中,氧化铬基减磨涂层的厚度可为100~500μm,优选为200~400μm。本公开中,氧化铬基减磨涂层(也可称自润滑减磨涂层)可采用喷雾造粒法制备出cr2o3-bn复合粉体,然后采用大气等离子体喷涂技术在基体表面制备出氧化铬基减磨涂层(即、cr2o3-bn复合涂层)。作为一个示例,通过在氧化铬粉体中引入自润滑相六方氮化硼制备出cr2o3-bn复合粉体,采用等离子喷涂技术将该复合粉体喷涂在预处理过的基体表面而制得cr2o3-bn复合涂层。以下具体说明本发明提供的氧化铬基减磨涂层的制备方法。cr2o3-bn复合粉体的制备。该cr2o3-bn复合粉体由喷雾造粒法制得。称取一定比例的cr2o3粉体和bn粉体,加入溶剂和粘结剂制成浆料。其中溶剂可为水、酒精等。粘结剂可为聚乙烯醇、聚乙烯醇缩丁醛等。粘结剂的加入量可为cr2o3粉体和bn粉体总质量的15~20wt%。然后将浆料和氧化锆球一同放入球磨罐中,在行星式球磨机中球磨一段时间(例如,球磨转速为300r/min,球磨时间为20min)。最后取出浆料,并将其输送进喷雾造粒机中进行喷雾处理和干燥,制成复合粉体。其中,cr2o3粉体和bn粉体的粒径可为1~8μm。喷雾造粒工艺参数可包括:进口温度为200~240℃;出口温度为100~140℃;进料速度为25~35rpm;转子速度为15000~18000rpm。所得cr2o3/h-bn复合粉体的粒径范围可为20~100μm。准备基体。基体可以是带有nicr过渡层的金属或合金、或带有sic过渡层的石墨或碳/碳复合材料。优选,首先对基体进行预处理,包括喷砂粗化、超声清洗和烘干。采用金属或合金作为基体时,通过等离子体喷涂技术在将nicr粉体喷涂在与处理过的金属或合金表面制备nicr过渡层。采用石墨或碳/碳复合材料作为基体时,通过等离子体喷涂技术在预处理过的石墨或碳碳复合材料表面制备si涂层,在(氩气等)惰性气氛保护下,对加有si涂层的石墨或碳/碳复合材料进行高温热处理,形成sic过渡层。或者,可以通过采用si粉、c粉等为原料的包埋法,再在(氩气等)惰性气氛保护下进行反应热处理获得sic涂层。或者,可以通过cvd方法直接沉积sic涂层。氧化铬基减磨涂层的制备。采用大气等离子体喷涂技术在基体表面制备cr2o3-bn复合涂层。例如,采用大气等离子体喷涂技术将复合粉体喷涂在c/c复合材料表面来制备复合涂层。其中,等离子体喷涂工艺参数可包括:等离子体气体ar流量30~50slpm,优选为35~45slpm;等离子体气体h2流量为5~20slpm,优选为7~15slpm;送粉载气ar为2~7slpm;送粉速率:10~25rpm;喷涂距离:100~150mm;喷涂功率为:30~55kw,所述slpm是指标准升/分钟,rpm是指转/分钟。本发明所制备的复合涂层具有优异的减磨耐磨性能,可显著提高纯氧化铬涂层的耐磨性,降低摩擦系数,可应用在化工、海事及冶金等领域延长零件的使用寿命。本发明所涉及的制备方法具有成本低、效率高、工艺简单及可规模化生产等优点。下面进一步例举实施例以详细说明本发明。同样应理解,以下实施例只用于对本发明进行进一步说明,不能理解为对本发明保护范围的限制,本领域的技术人员根据本发明的上述内容作出的一些非本质的改进和调整均属于本发明的保护范围。下述示例具体的工艺参数等也仅是合适范围中的一个示例,即本领域技术人员可以通过本文的说明做合适的范围内选择,而并非要限定于下文示例的具体数值。实施例1:在带有sic过渡层的碳/碳复合材料表面制备cr2o3-bn复合涂层,涂层组成为以cr2o3作为主相,h-bn作为第二相。涂层制备步骤如下:步骤1):称取一定比例的cr2o3粉体和h-bn粉体,所述cr2o3粉体和bn粉体的粒径可为1~8μm,其中第二相h-bn占粉体总质量的5wt.%,将粉体与水和粘结剂搅拌混合配成浆料,将浆料和氧化锆球放入球磨罐中在行星式球磨机中球磨20min,取出浆料输送进喷雾造粒机中进行喷雾干燥得到cr2o3-bn复合原料粉体,备用。喷雾造粒工艺参数参见表1。表1为喷雾造粒制备cr2o3-bn复合粉体工艺参数:进口温度出口温度进料速度转子速度220℃100℃35rpm15000rpm步骤2):将带有sic过渡层的碳/碳复合材料基体用无水乙醇超声清洗3次,每次10min,在100℃烘箱内烘干,备用。步骤3):采用等离子喷涂系统(a-2000,sulzermetcoag,switzerland)将上述复合粉体喷涂在带有sic过渡层的碳/碳复合材料表面,所述涂层厚度为300μm;喷涂工艺参数参见表2。表2为大气等离子体喷涂cr2o3-bn复合涂层工艺参数:等离子体气体ar40slpm喷涂距离110mm等离子体气体h211slpm送粉速率18rpm喷涂功率45kw粉末载气ar3.5slpm*slpm:标准升/分钟。图1为cr2o3-bn复合粉体的表面和截面扫描电子显微镜照片。复合粉体的球形度很好,粉体流动性好,适合等离子体喷涂。图2和图3分别为cr2o3-bn复合涂层的表面和截面扫描电子显微镜照片,可以看出,所得复合涂层的厚度为200μm。涂层表面粒子扁平化度高,熔融状态良好,截面中涂层与基体之间结合紧密。由摩擦磨损仪器系统自带公式计算出摩擦系数,通过仪器显示器直接读取摩擦系数;采用轮廓仪测量磨痕截面积,再通过公式1计算涂层磨损率w:w=2πrs/dn);式中:r—磨损时的回转半径;s—磨痕截面积;d—摩擦行程;n—摩擦试验载荷。试样测量三次,取平均值。采用摩擦磨损仪对cr2o3-bn复合涂层的摩擦磨损性能进行考核,考核条件为:将涂层表面进行抛光处理,然后将样品通过球-盘磨损形式置在50n载荷和0.5m/s速度下与wc-co金属陶瓷摩擦副对磨30min。图4为纯cr2o3涂层与cr2o3-5wt.%bn复合涂层在50n载荷分别与wc-co摩擦副对磨的摩擦系数(a)及磨损率(b)对比图。纯cr2o3涂层与wc-co对磨的平均摩擦系数为0.54±0.08,而cr2o3-bn复合涂层与wc-co对磨的平均摩擦系数为0.38±0.01,自润滑相h-bn的引入使涂层的平均摩擦系数降低了约30%。通过图4中(b)中的磨损率对比图也可以看出,随着h-bn的引入,涂层的磨损率也有大大降低,纯cr2o3涂层的磨损率为(34±10)×10-6mm3/nm,复合涂层的磨损率为(5.6±0.9)×10-6mm3/nm,磨损率降低了约83%。显然自润滑相h-bn的引入显著降低了涂层的摩擦系数和磨损率,改善了纯cr2o3涂层的摩擦磨损性能。说明本发明所设计的涂层体系具有良好的减磨耐磨性能。图5为cr2o3-5wt.%bn复合涂层与wc-co摩擦副对磨后磨损表面生成的摩擦膜截面形貌(a)和对应的元素分布图。从图中5中(a)可以看出,复合涂层表面生成了一层致密的摩擦膜,厚度约为1μm-2.56μm,结合摩擦膜对应的元素分布图,可看出摩擦膜主要由b和o元素组成,复合涂层在高载荷条件下与硬度较高的wc-co对磨时,随着磨损过程中摩擦热的增加,摩擦接触区域温度相应升高,bn发生氧化反应生成b2o3(4bn+o2=2b2o3+2n2)。以b2o3为主要成分的摩擦膜均匀的覆盖在涂层表面,保护涂层免遭受进一步磨损,起到同时减小摩擦系数和磨损率的作用。实施例2在带有sic过渡层的碳/碳复合材料表面制备cr2o3-bn复合涂层,涂层组成为以cr2o3作为主相,h-bn作为第二相,具体制备步骤参见实施例1,区别在于h-bn中加入量为10wt%。采用实施例1中相同的条件对本实施例2所得复合涂层的摩擦磨损性能进行考核,具体参数包括:磨损形式为球-盘磨损;摩擦副为wc-co金属陶瓷材料;载荷为50n;速度为0.5m/s;磨损时间为30min。图6为cr2o3-10wt.%bn复合涂层与cr2o3-5wt.%bn复合涂层和纯cr2o3涂层在50n载荷分别与wc-co对磨的平均摩擦系数(a)和磨损率(b)对比图。通过对比发现,虽然10wt.%bn的加入使纯cr2o3涂层与wc-co摩擦副对磨的摩擦系数和磨损率均有明显降低,但是减磨效果不如实施例1中制得的cr2o3-5wt.%bn复合涂层。与cr2o3-5wt.%bn复合涂层相比,较多bn的加入,使cr2o3-5wt.%bn复合涂层的摩擦系数和磨损率呈现增加现象,cr2o3-5wt.%bn复合涂层的摩擦系数从0.38±0.01增至0.41±0.03;磨损率从(5.6±0.9)×10-6mm3/nm增至(9.0±3.8)×10-6mm3/nm。该涂层耐磨性能相比于实施例1中制得的cr2o3-5wt.%bn复合涂层有所减弱,皆由于h-bn中加入量增加所致。对比例1:采用实施例1中相同的等离子喷涂工艺条件在带有sic过渡层的碳/碳复合材料表面制备纯cr2o3涂层。采用实施例1中相同的条件对纯cr2o3涂层的摩擦磨损性能进行考核。图7为纯cr2o3涂层的表面(a)及截面(b)的形貌图,观察发现涂层表面存在较多未熔融及半熔融的颗粒,涂层表面熔融状态不如实施例1中制得的cr2o3-5wt.%bn复合涂层(参见图2)。当前第1页12