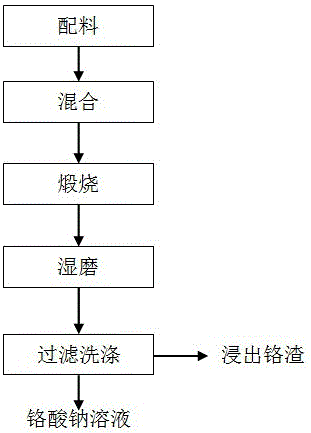
本发明涉及危废处理领域,尤其是废弃物回收领域,具体为一种铁铬合金含铬粉尘资源化利用方法。现有铁铬合金含铬粉尘通常作为炼钢辅料或水泥添加剂等方式进行处理,而本申请提供一种铁铬合金含铬粉尘资源化利用方法,以实现对铬的资源化利用。
背景技术:
:铁铬合金生产企业在炼钢过程中,产生的大量粉尘需经除尘装置处理,并收集其中的粉尘。该粉尘含有约15%~30%的cr2o3和0.1%~0.5%的六价铬,属于《国家危险废物名录2016》中hw21含铬废物,废物代码:315-002-21。铁铬合金含铬粉尘由于粒度极细、结构复杂,且具有一定的毒性,使得其综合利用难度大。针对该类含铬粉尘,传统处置方法是将该含铬粉尘作为炼钢辅料或水泥添加剂进行处置。近年来,随着经济的持续发展,铁铬合金消费量和产量逐年增加,产生的粉尘量也日益增加,造成严重的环境污染和资源浪费。我国作为一个贫铬的国家,97%的铬矿都依赖于进口。而铁铬合金含铬粉尘中的铬含量较高,资源化利用价值较高,且含铬粉尘的量日益增加。为此,研发一种铁铬合金含铬粉尘资源化利用方法,就显得尤为重要。技术实现要素:本发明的发明目的在于:针对铁铬合金生产企业在炼钢过程中,所产生的含铬粉尘,通常作为炼钢辅料或水泥添加剂进行处置,无法实现铬资源化利用的问题,提供一种铁铬合金含铬粉尘资源化利用方法。采用本申请,能实现对于铬的资源化利用,强化有价组元的回收,对于缓解铬资源严重不足,降低对外依存度,减少铁铬合金产生的环境污染,促进可持续发展,具有重要的现实意义。为了实现上述目的,本发明采用如下技术方案:一种铁铬合金含铬粉尘资源化利用方法,包括如下步骤:(1)配料分别按配比称取含铬粉尘、氧化剂、填充剂,备用;氧化剂、填充剂、含铬粉尘的质量百分比为20~25%:20~30%:余量;(2)混合将步骤(1)称取的含铬粉尘、氧化剂、填充剂混合、搅拌均匀,得到生料;(3)煅烧将步骤(2)的生料在高温炉内进行煅烧,高温炉尾气温度控制在500℃~600℃,烧成带温度控制在1000℃~1200℃,煅烧时间2~3h,得到煅烧熟料;煅烧的反应方程式如下:4(fe·cr2o3)+8na2co3+7o2=8na2cro4+2fe2o3+8co2↑;(4)湿磨采用湿法将煅烧熟料粉磨至80~200目;(5)过滤洗涤在碱性条件下,采用真空多级洗涤研磨后的煅烧熟料,再进行固液分离,分别得到铬酸钠溶液、浸出铬渣。所述步骤1中,氧化剂、填充剂、含铬粉尘的质量百分比之和为100%。所述氧化剂为纯碱、碳酸氢钠中的一种或两种。所述高温炉为回转窑。所述步骤5中,滤液中铬酸钠的浓度控制在100~300g/l,分离出的浸出铬渣中总铬含量为3%~5%。所述步骤5中,滤液中铬酸钠的浓度控制在200g/l。所述填充剂为提铬返渣,其用于降低物料的熔盐量,增加物料的疏松度,易于氧化反应。所述含铬粉尘中总铬含量低于30%。综上所述,本申请提供一种铁铬合金含铬粉尘资源化利用方法,其能将铁铬合金生产过程中产生的含铬粉尘进行资源化利用。采用本申请处理含铬粉尘,能够有效回收利用其铬盐,不仅可实现含铬粉尘的资源化利用,还能可降低铬盐生产成本。同时,本申请的工艺流程短,操作方便,能够满足工业化应用的需求,具有较高的应用价值。综上所述,由于采用了上述技术方案,本发明的有益效果是:(1)本申请能对总铬含量低于30%的含铬废物进行资源化利用,回收含铬粉尘中的铬盐,铬回收率可达70%以上,具有较高的应用价值;(2)本申请通过投加填充剂,可降低物料的熔盐量,增加物料的疏松度,易于煅烧时氧化反应的进行;(3)本申请中,把煅烧后的熟料粉磨至粒径为80~200目,便于浸取;采用湿磨增加熟料的比表面积,有利于铬酸钠的浸出,提高浸取率;(4)本申请在碱性条件下进行浸取,可降低锌、镍的浸出,提高铬酸钠的利用效果;(5)本申请采用多级洗涤增加铬酸钠的浓度,有利于拓展铬酸钠的应用范围;(6)本申请得到的铬酸钠溶液铝含量较低,铝含量只有现有无钙焙烧方法的10%;(7)采用本申请处理后分离出的铬渣中总铬含量为3%~5%,而现有无钙焙烧方法制备铬酸钠中,产生的铬渣中总铬含量为8%~9%,表明本申请对铬具有较高的利用率。附图说明本发明将通过例子并参照附图的方式说明,其中:图1为本申请的工艺流程图。具体实施方式本说明书中公开的所有特征,或公开的所有方法或过程中的步骤,除了互相排斥的特征和/或步骤以外,均可以以任何方式组合。本说明书中公开的任一特征,除非特别叙述,均可被其他等效或具有类似目的的替代特征加以替换。即,除非特别叙述,每个特征只是一系列等效或类似特征中的一个例子而已。本申请实施例采用的含铬粉尘为某家废钢加工冶炼企业在精炼生产过程产生的烟灰,该含铬粉尘主要成分如表1所示。表1含铬粉尘成分组分含量(%)组分含量(%)总铬(cr2o3)21.06镁(mgo)8.64硅(sio2)1.59钒(v)mg/kg291.30铁(fe2o3)47.88水溶铬0.19铝(al2o3)0.71碱度14.29钙(cao)11.60水份0.18硫酸盐0.23烧失量(loss)-0.79镍(nio)2.11锌(zno)5.31实施例1~5(1)将含铬粉尘、氧化剂、填充剂混合,充分搅拌,得到生料,含铬粉尘、氧化剂、填充剂配比见表2。其中,氧化剂采用碳酸钠,填充剂为提铬返渣。(2)将配好的生料在高温炉内进行煅烧,将尾气温度控制在550℃,烧成带温度控制在1000℃,煅烧时间2h后,获得熟料。(3)采用湿磨将煅烧后的熟料研磨至粒径约为100目。(4)在碱性条件下,采用真空多级洗涤研磨后的熟料,再经固液分离,得到铬酸钠溶液,将滤液中铬酸钠的浓度控制在200g/l左右。表2实施例1~5原料配比及反应参数对制备的铬酸钠溶液进行测定,测定结果如下表3所示。表3实施例1~5含铬粉尘回收利用效果分析从表2、表3可以看出实施例3、4、5中总铬回收率可达70%以上,处理后的铬渣中总铬含量为3%~5%。说明含铬粉尘中填充剂的投加量为20%~30%时效果最佳。实施例6~10(1)将含铬粉尘、氧化剂、填充剂混合,充分搅拌,得到生料,含铬粉尘、氧化剂、填充剂配比见表4。其中,氧化剂采用碳酸氢钠,填充剂采用提铬返渣。(2)将配好的生料在高温炉内进行煅烧,将尾气温度控制在550℃,烧成带温度控制在1000℃,煅烧时间2h后,获得熟料。(3)采用湿磨将煅烧后的熟料研磨至粒径约为100目。(4)在碱性条件下,采用真空多级洗涤研磨后的熟料,再经固液分离,得到铬酸钠溶液,将滤液中铬酸钠的浓度控制在200g/l左右。表4实施例6~10原料配比及反应参数表5实施例6~10含铬粉尘回收利用效果分析从表4、表5可以看出随着氧化剂投加的增加,熟料转化率和总铬回收率均增加,实施例8、9、10中总铬回收率可达70%以上,但随着氧化剂的投加量增加,熟料转化率和总铬回收率增加趋势减缓,说明含铬粉尘中氧化剂投加量为20%~25%时效果最佳。实施例11~15(1)将含铬粉尘、氧化剂、填充剂混合,充分搅拌,得到生料,含铬粉尘、氧化剂、填充剂配比见表6。其中,氧化剂采用碳酸钠,填充剂采用提铬返渣。(2)将配好的生料在高温炉内进行煅烧,烧成带温度控制见表6,煅烧时间2h后,获得熟料。(3)采用湿磨将煅烧后的熟料研磨至粒径约为100目。(4)在碱性条件下,采用真空多级洗涤研磨后的熟料,再经固液分离,得到铬酸钠溶液,将滤液中铬酸钠的浓度控制在200g/l左右。表6实施例11~15原料配比及反应参数表7实施例11~15含铬粉尘回收利用效果分析从表6、表7可以看出实施例12、13、14中总铬回收率可达70%以上,处理后的铬渣中总铬含量为3%~5%。当反应温度到达1300℃时,熟料转化率增加,但总铬回收率成下降趋势,说明含铬粉尘处理烧成带温度为1000℃~1200℃时效果最佳。尽管本发明的实施方案已公布如上,但其并不仅仅限于说明书和实施方式中所列运用,它完全可以被适用于各种适合本发明的领域,对于熟悉本领域的人员而言,可容易地实现另外的修改,因此在不背离权利要求及等同范围所限定的一般概念下,本发明并不限于特定的细节和这里示出与描述的图例。当前第1页12