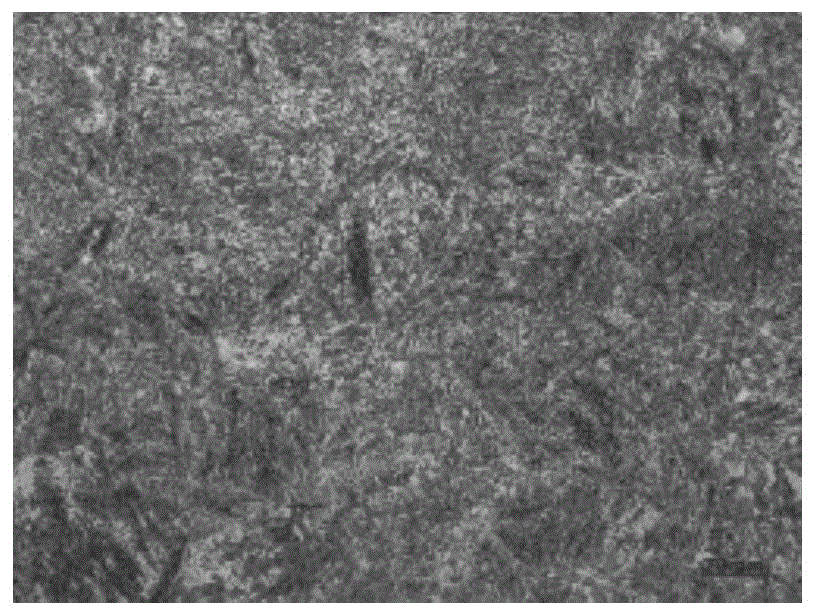
本发明涉及棒材合金钢
技术领域:
,尤其涉及应用于加工滚珠丝杠的钢及其制造方法。
背景技术:
:滚珠丝杠副是传动机械中运用滚珠在丝杠与螺母间的滚动来同时实现动力传递、运动转换功能的常用传动装置之一。其同时兼具高精度、高效率和可逆性等特点,已成为各类数控机床、自动化机械以及加工中心驱动过程中的关键执行部件,被广泛应用于机械、核工业、航空、航天等领域。滚动丝杠副通常是由丝杠、滚珠、螺母及滚珠循环返回装置四个部分组成。滚珠丝杠是精密机械上最常使用的传动元件,其主要功能是将旋转运动转换成线性运动,或将扭矩转换成轴向反复作用力,同时兼具高精度、可逆性和高效率的特点。其工作环境为强冲击、高磨损和超高转速等。其结构特点和工作条件要求零件必须具备高的硬度、耐磨性、接触疲劳强度、良好的韧性、尺寸稳定性、耐腐蚀和冷热加工性能。滚珠丝杠常用材料有高碳铬轴承钢、中碳钢以及渗碳钢等。高碳轴承钢如gcr15、gcr15simn用于滚珠丝杠生产时,整体经过预处理后,在工作部位进行淬火处理,基本可以满足工作部位所需的高强度、高硬度和耐磨性的要求,但这类轴承钢仅仅能勉强满足接触刚度的性能要求,由于滚珠丝杠与轴承有很大差别。例如hrc60的硬化层深度、梯度以及在全行程范围的均匀度很难控制,淬火后弯曲变形难以矫直、轴向伸缩变形难以控制等缺陷,影响最终滚珠丝杠产品质量,甚至导致批量报废,成为制约高精密机械制造业发展的瓶颈。而渗碳轴承钢主要用于需要同时具有表面高接触疲劳强度和心部高韧性的条件。这类钢经过渗碳淬火后表面硬度可以达到60hrc以上,有一定的耐磨性和强度,其使用性能和高碳铬轴承钢相差无几。但由于需要渗碳处理,生产工序复杂且生产成本高昂,不利于推广。而中碳钢经过表面感应加热淬火后,即主要是利用电磁感应原理,以涡流形式将丝杠表面快速加热至淬火温度,而后急剧冷却,形成一定厚度的表面淬硬层,而心部仍保持原有的组织形态。因此,可以满足滚珠丝杠表层具有高硬度、耐磨性而心部则具有高强韧度配合的综合力学性能要求。本发明在已有中碳钢的生产基础上,提出一种新的滚珠丝杠用钢及其生产方法,使加工的滚珠丝杠表面具有高硬度、高强度和耐磨性的同时,心部具有良好的韧性,尺寸稳定性好,满足其使用要求。技术实现要素:本发明的目的是开发一种滚珠丝杠用钢及其制造方法,满足滚珠丝杠用钢材的强度、耐磨性、心部高强韧度以及加工成滚珠丝杠成品后的热处理变形量及尺寸精度要求。本发明的滚珠丝杠用钢为φ20-80mm的棒材,钢材经过调质处理后交货,其硬度满足220-280hbw,显微组织要求为索氏体+贝氏体组织,钢材的奥氏体晶粒度要求≥5级;钢材要求非金属夹杂物按gb/t10561中a法评级,满足a类细系≤1.5;a类粗系≤1.0;b类细系≤1.5;b类粗系≤1.0;c类细系=0;c类粗系=0;d类细系≤1.0;d类粗系≤0.5;ds类≤1.0。采用sep1927水浸高频探伤检测,要求缺陷长度不允许超过5mm。采用astme381对钢材低倍组织评级,要求c≤2.0级、r≤1.5级、s≤2.0级。采用gb/t228对钢材进行拉伸检测,抗拉强度rm≥1150mpa、断后伸长率a≥11%、断面收缩率z≥45%。采用jisg0561法检验末端淬透性,要求j13mm硬度范围57~62hrc。本发明对滚珠丝杠的化学成分进行了限定:c:0.45~0.60%,si:0.15~0.40%,mn:0.90~1.10%,cr:0.70~1.20%,s≤0.015%,p≤0.025%,ni≤0.25%,mo:0.15~0.40%,cu≤0.30%,al≤0.05%,ca≤0.0010%,ti≤0.003%,o≤0.0010%,n:0.0050~0.0090%,as≤0.04%,sn≤0.03%,sb≤0.005%,pb≤0.002%,余量为fe及不可避免的杂质。本发明的滚珠丝杠用钢的化学成分设计依据如下:1)c含量的确定c是钢中最经济、最基本的强化元素,通过固溶强化和析出强化可明显提高钢的强度,但c过高会对钢的韧性及延性能带来不利影响。本发明c含量的范围确定为0.45~0.60%,本发明涉及钢材属于中碳钢范畴;2)si含量的确定si是钢中的脱氧元素,并以固溶强化形式提高钢的硬度和强度。另外,si减少摩擦发热时的氧化作用和提高钢的冷变形硬化率从而提高材料的耐磨性。但是,si含量较高时钢材的韧性降低,而且si使钢中的过热敏感性、裂纹和脱碳倾向增大。本发明控制si含量为0.15~0.40%。3)mn含量的确定mn作为炼钢过程的脱氧元素,是对钢的强化有效的元素,起固溶强化作用。而且mn能提高钢的淬透性,改善钢的热加工性能。mn能消除s(硫)的影响:mn在钢铁冶炼中可与s形成高熔点的mns,进而消弱和消除s的不良影响。但mn含量高,会降低钢的韧性。本发明的mn含量控制在0.90~1.10%。4)cr含量的确定cr是碳化物形成元素,能够提高钢的淬透性、耐磨性和耐腐蚀性能但cr含量过高,与钢中的碳结合,容易形成大块碳化物,这种难溶碳化物使钢的韧性降低,轴承寿命下降,本发明cr含量的范围确定为0.70~1.20%。5)al含量的确定al作为钢中脱氧元素加入,除为了降低钢水中的溶解氧之外,al与n形成弥散细小的氮化铝夹杂可以细化晶粒。但al含量过多时,钢水熔炼过程中易形成大颗粒al2o3等脆性夹杂,降低钢水纯净度,影响成品的使用寿命。本发明al含量的范围确定为≤0.05%。6)mo含量的确定钼能使钢的晶粒细化,提高淬透性和热强性能,在高温时保持足够的强度和抗蠕变能力。钢中加入钼,能提高机械性能,还可以抑制合金钢由于回火而引起的脆性。但钼是铁素体形成元素,当钼含量较多时就易出现铁素体δ相或其它脆性相而使韧性降低。本发明将mo含量的范围确定为0.15~0.40%7)ca含量的确定ca含量会增加钢中点状氧化物的数量和尺寸,同时由于点状氧化物硬度高,塑性差,在钢变形时其不变形,容易在交界面处形成空隙,使钢的性能变差。本发明ca含量的范围确定为≤0.001%。8)ti含量的确定ti对钢材危害方式是以氮化钛,碳氮化钛夹杂物的形式残留于钢中。这种夹杂物坚硬、呈棱角状,严重影响材料的疲劳寿命,特别是在纯洁度显著提高,其他氧化物夹杂数量很少的情况下,含钛夹杂物的危害尤为突出。本发明ti含量的范围确定为≤0.003%。9)n含量的确定当钢中溶有过饱和的氮,在放置较长一段时间后就会发生氮以氮化物形式的析出,并使钢的硬度、强度提高,塑性下降,发生时效。钢中加入适量的铝,可生成稳定的aln,能够压抑fe4n生成和析出,不仅改善钢的时效性,还可以阻止奥氏体晶粒的长大,起到细化晶粒的作用。但是氮会与钢中的合金元素生成氮化物非金属夹杂,更重要的是降低了合金元素的作用。钢中氮含量高时,钢的强度升高,冲击韧性降低。本发明的n含量确定为0.005-0.009%10)o含量的确定氧含量代表了氧化物夹杂总量的多少,氧化物脆性夹杂限制影响成品的使用寿命,大量试验表明,氧含量的降低对提高钢材纯净度特别是降低钢种氧化物脆性夹杂物含量显著有利。本发明氧含量的范围确定为≤0.0010%。11)p、s含量的确定p在钢中会严重引起凝固时的偏析,p溶于铁素体使晶粒扭曲、粗大,且增加冷脆性。本发明p含量的范围确定为≤0.025%。s使钢产生热脆性,降低钢的延展性和韧性,但s能提高钢材的切削性能,本发明s含量的范围确定为≤0.015%。12)as、sn、sb、pb含量的确定as、sn、sb、pb等微量元素,均属低熔点有色金属,在钢材中存在,引起零件表面出现软点,硬度不均,因此将它们视为钢中的有害元素,本发明这些元素含量的范围确定为as≤0.04%,sn≤0.03%,sb≤0.005%,pb≤0.002%。本发明还要提供基于上述化学成分的滚珠丝杠的制造方法,制造流程为电炉或转炉—炉外精炼—vd或rh真空脱气—连铸—连铸坯开方成中间坯(方坯)—中间坯加热轧制成材—精整—调质热处理(高温淬火+回火)—车皮—打件入库。上述生产流程的工艺特点如下:1、采用优质铁水、废钢及原辅料,以降低钢水中有害元素含量。加强精炼过程的脱氧,保证钢中残铝量,利用钢水中的良好的动力学条件,进行集中提前脱氧和vd真空脱气处理,使非金属夹杂物充分上浮并控制较低的气体含量。在真空脱气后进行长时间软吹氩,保证夹杂物充分上浮,同时连铸全程要进行防氧化保护来减少钢中的夹杂物数量。另外选用优质耐材减少外来夹杂对钢水污染的控制技术,强化对生产过程的控制。2、连铸过程采用电磁搅拌及轻压下技术,并采用低过热度浇注,有效改善和降低连铸坯的成分偏析,尤其地,在增加凝固末端电磁搅拌及轻压下等先进设备后,铸坯凝固组织的致密度得到了提高,铸坯中心疏松和缩孔得到了有效控制,而二次枝晶臂间距得到明显改善,中心等轴晶率明显提高,晶粒得到细化,从而显著地改善了铸坯的质量,降低成分偏析。3、本发明的产品将冶炼原料依次经电炉或转炉冶炼、lf精炼、rh或vd真空脱气和连铸,连铸出与钢材成品化学成分相符的规格为390×510及以上的连铸方坯;连铸坯应下坑缓冷,防止连铸坯开裂,缓冷时间不小于48小时,随后将连铸坯送至中性或弱氧化性气氛的加热炉内加热后并开坯成200mm×200mm-300mm×300mm的中间坯,加热温度1150-1250℃,加热时间大于5小时,开坯轧制时开轧温度1000℃-1150℃,終轧温度≥900℃,开坯轧制压缩比大于5,中间坯应下坑缓冷,下坑温度≥500℃,缓冷时间不小于48小时。而后再将中间坯送至加热炉内轧制成目标钢材,具体的轧制工艺为:预热段温度控制在650-900℃,加热段温度控制在1000-1150℃,均热段温度控制在1100-1200℃,为保证坯料充分均匀受热,总加热时间在2小时以上。轧制开轧温度控制在1000℃-1100℃,終轧温度控制在900℃以上,轧制完成后堆冷,再经后续矫直、探伤,制得目标棒材产品。为保证钢材的交货硬度及组织要求,需对上述精整合格的钢材进行调质处理,其中,淬火加热温度为800-1000℃,在炉时间为200-500min,使用淬火环水淬,水温控制在20-30℃,回火加热温度500-700℃,在炉时间400-600min,出炉后空冷或水冷至室温。将调质后的棒材产品再经后续车皮+表面探伤处理,其中,车皮单边车皮量不低于0.5mm,并最终打件入库。本发明的滚珠丝杠用钢具有如下特点:1)本发明钢材经过后续表面淬火处理后加工的滚珠丝杠成品,既能够保证表面具有足够的硬度和耐磨性,同时心部具备一定的韧性,能够显著提高产品的使用寿命。2)本发明钢材由于交货组织为均匀的索氏体+贝氏体,组织均匀度控制好,热处理后产品热处理变形小,尺寸精度高,能够满足高端滚珠丝杠的使用要求。3)本发明钢材通过水浸高频探伤检测内部质量,能够保证高端滚珠丝杠使用疲劳寿命的可靠性。附图说明图1为本发明实施例1的索氏体+贝氏体的晶相组织图;图2为本发明实施例2的索氏体+贝氏体的晶相组织图;图3为本发明实施例3的索氏体+贝氏体的晶相组织图。具体实施方式以下结合实施例对本发明作进一步详细描述。实施例1-3对本发明滚珠丝杠用钢的化学成分和制造方法分别举例。各实施例的化学成分(wt%)参见表1、2表1实施例csimnpscrcunial10.50.250.970.0180.0061.010.010.020.01620.490.250.980.0170.00610.010.020.01530.50.270.990.0150.0050.980.010.020.016表2各实施例钢材的夹杂物见表3表3各实施例钢材的硬度数据见表4表4实施例硬度(hbw)126622633269各实施例钢材的低倍数据见表5表5实施例crs11.01.01.021.01.01.031.01.01.0各实施例钢材的晶粒度数据见表6表6实施例晶粒度(级)172737各实施例钢材的水浸高频探伤数据见表7表7实施例水浸高频探伤检出缺陷长度(mm)102230各实施例钢材的力学性能数据见表8表8各实施例钢材的末端淬透性数据见表9表9实施例j13mm(hrc)159.58259.73359.59各实施例钢材的组织参见图1-3。各实施例的滚珠丝杠用钢的制造流程为电炉或转炉—炉外精炼—vd或rh真空脱气—连铸—连铸坯开方成中间坯—中间坯加热轧制成材—精整—调质热处理—车皮—打件入库。具体的冶炼时,选用优质铁水、废钢及原辅料,选用优质脱氧剂及耐火材料。在电炉/转炉生产过程中,三个实施例的出钢终点c分别控制在0.05-0.25%,终点p要求≤0.020%,连铸过热度控制在15-35℃之内。各实施例的连铸坯进行开坯轧制工艺如下表10所示。表10将中间坯送至加热炉内轧制成目标圆棒,具体的轧制工艺为:设置预热段温度控制在650-900℃,加热段温度控制在1000-1150℃,均热段温度控制在1100-1200℃,为保证坯料充分均匀受热,总加热时间在2小时及以上。轧制开轧温度控制在1000℃-1100℃,終轧温度控制在900℃以上,轧制完成后应缓慢冷却,使钢中aln质点细小、均匀、充分析出,从而细化晶粒并防止钢材出现混晶的情况,轧制完成后堆冷,再经后续矫直、探伤,得到目标棒材产品。将轧制的成品棒材进行调质处理,其中,淬火加热温度为800-1000℃,在炉时间为200-500min,使用淬火环水淬,水温控制在20-30℃,回火加热温度500-700℃,在炉时间400-600min,出炉后空冷或水冷至室温。将调质后的棒材产品再经后续车皮+表面探伤处理,其中,车皮单边车皮厚度不低于0.5mm,并最终打件入库。尽管以上详细地描述了本发明的优选实施例,但是应该清楚地理解,对于本领域的技术人员来说,本发明可以有各种更改和变化。凡在本发明的精神和原则之内所作的任何修改、等同替换、改进等,均应包含在本发明的保护范围之内。当前第1页12