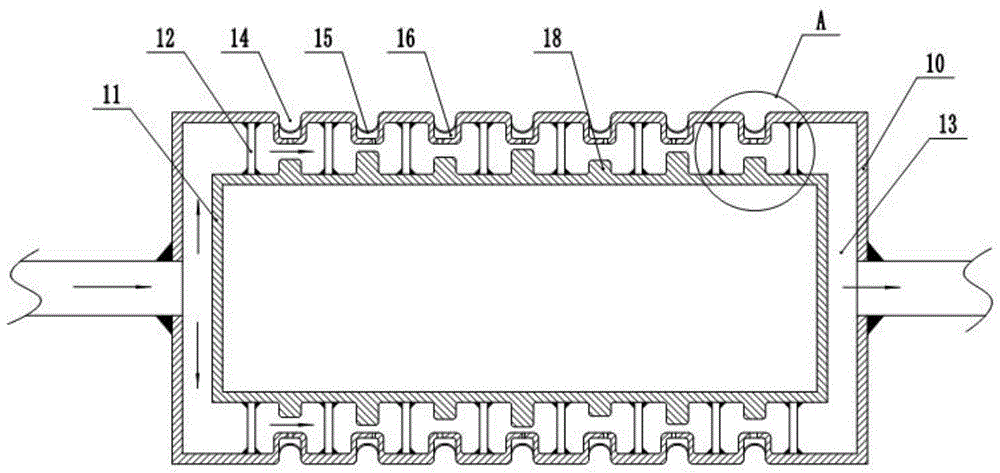
本发明涉及精炼剂制备
技术领域:
,特别涉及一种铝合金用低熔点颗粒精炼剂及其制备方法。
背景技术:
:由于铝合金原料中存在的碱金属以及在熔炼过程中产生的氧化夹渣,对形成的铝合金铸锭都有一定的不良影响,例如铸锭的组织中会产生气孔、夹杂等缺陷,因此为了提高铝合金铸锭的质量,就需要对铝熔体中的碱金属、氧化夹渣等进行充分的去除。精炼剂在铝熔体除杂中起到至关重要的作用,现有的精炼剂通常通过多种无机盐干燥后按照一定比例混合配制而成,这种工艺制备的精炼剂其熔点高,且密度往往与铝熔体的密度接近,使得精炼剂在铝熔体中不能快速的上浮,带走铝熔体内部的夹渣,从而影响铝熔体的精炼效果。技术实现要素:本发明提供了一种铝合金用低熔点颗粒精炼剂及其制备方法,以解决现有的精炼剂因密度与铝熔体密度相近,精炼效果差的问题。为了达到上述目的,本发明的技术方案为:一种铝合金用低熔点颗粒精炼剂,该精炼剂的原料按重量份计包括23~25份的kcl和10~15份的nacl,余量为氟化钠和硫酸钠,该颗粒精炼剂的粒径为0.83~3.15mm,密度为1.20~1.30g/cm3,熔点为480~500℃。本技术方案的技术原理和效果在于:本方案中颗粒精炼剂的熔点低(为480~500℃),使精炼剂在进入铝熔体后能够快速融化,并吸附和包裹渣团,利于铝熔体中渣团的排出,另外本方案中颗粒精炼剂的密度小(为1.20~1.35g/cm3),而铝合金溶体的密度约为2g/cm3,因此本方案中精炼剂的密度要远小于铝熔体的密度,这样精炼剂在应用在铝熔体精炼过程中,进入铝熔体内部的精炼剂能够包裹住渣团快速上浮,排出铝熔体,进而提高铝熔体精炼的效果。进一步,所述颗粒精炼剂中水分含量≤0.5%。有益效果:由于水分存在会对铝熔体有强氧化作用,因此降低水分能够避免铝熔体的烧损。进一步,所述精炼剂为形状不规则颗粒。有益效果:不规则的颗粒能够提高颗粒精炼剂与铝熔体的接触面积,从而提高其除渣的能力。一种铝合金用低熔点颗粒精炼剂的制备方法,包括以下步骤:步骤1:将氯化钠、氯化钾、氟化钠和硫酸钠原料混合后放入熔化炉中进行熔炼,熔炼温度≥700℃;步骤2:将步骤1的熔融料进行保温,保温时间大于70mim,后冷凝至固态;步骤3:对步骤2中冷凝至固态的混合料进行破碎,得粉状料;步骤4:将步骤3得到的粉状料采用挤压造粒机进行造粒,得到粒径为0.83~3.15mm的颗粒精炼剂。有益效果:本方案中通过将nacl、kcl等原料熔融、凝固、破碎后挤压造粒成0.83~3.15mm的颗粒精炼剂,而通过工业生产数据统计显示,采用本方案中的颗粒精炼剂对铝熔体进行精炼后,铝熔体中碱金属的去除率可达70~80%,铝熔体中的氧化夹杂的去除率在70%以上,大大减轻了铝熔体后续的过滤压力。1、将nacl、kcl等原料进行熔融能够形成稳定的二元共晶化合物(nakcl2),该化合物的熔点远低于nacl、kcl等原料,使精炼剂在铝熔体内能够快速溶解,达到精炼的效果。2、本方案中通过将破碎后的粉末料挤压成型为成品颗粒精炼剂,这样的效果在于,由于通过粉末挤压成型的颗粒,其内部具有微小的孔隙,不仅能够降低颗粒精炼剂的密度,同时孔隙的存在使得颗粒能够快速吸收铝熔体内的热量,从而快速融化。对于进入到铝熔体内部的颗粒精炼剂,由于精炼剂内孔隙的存在,使得其表面吸附力大,其对铝熔体中渣团的包裹能力提高,从而提升除渣的效率,更好的实现铝熔体与渣团的分离。而相比于现有技术中将凝固后的物料直接破碎成颗粒状,这样形成的颗粒,其内部没有疏松的气孔,不仅颗粒的密度大,不容易在铝熔体中上浮,同时颗粒表面的吸附力下降,对铝熔体中的渣团的包裹能力降低。进一步,所述步骤1中熔炼时,加热分步进行,先将混合料以≤3℃/min的速率加热至445~480℃,并保温20min~25min,后再加热至温度≥700℃。有益效果:先将混合料≤3℃/min的速率加热至445~480℃,并保温20min~25min,是由于nacl与kcl为主要原料在融化时,当温度达到445℃以上时,会形成多种二元共晶化合物,而缓慢的加热使这两种化合物能够更充分的形成二元共晶化合物。进一步,加热至≥700℃后,保温50min~65min。有益效果:在≥700℃的温度下保温50min~65min能够使得共晶体系中一些不稳定的二元共晶化合物例如:nakcl3、nakcl4的分解,形成稳定的共晶化合物。进一步,所述步骤2中破碎分多步完成,先采用颚式破碎机将物料破碎成块状,后采用锤式破碎机将块状物料破碎成粉末状。有益效果:分步完成破碎可降低对破碎机的损耗,提高破碎机的使用寿命。进一步,对步骤3中的粉末状料进行筛分处理,得粒状料和粉状料,采用的筛目为200~300目。有益效果:筛分后可以保证粉状料的粒度,将大块的粒状料筛分出去,避免粒状料对后续造粒产成不良的影响。进一步,筛分后粒状料继续回到步骤3中进行破碎,或者进入步骤1中重新熔炼。有益效果:实现对粒状料的回收,减少物料的损失。进一步,所述步骤4中挤压造粒前向粉末状物料中加入了粘接剂。有益效果:粘接剂的使用能够提高粉状料之间的结合强度,使形成的颗粒不易破裂。附图说明图1为本发明实施例1采用的挤压造粒机中造粒辊筒的结构示意图;图2为本发明中图1中a部分的放大示意图。具体实施方式下面通过具体实施方式进一步详细说明:说明书附图中的附图标记包括:外层筒10、内层筒11、加强筋12、通道夹层13、造粒槽14、弹性层15、气腔16、气流孔17、凸起18。一种铝合金用低熔点颗粒精炼剂,该精炼剂的原料按重量份计包括23~25份的kcl和10~15份的nacl,余量为氟化钠和硫酸钠,该颗粒精炼剂的粒径为0.83~3.15mm,密度为1.20~1.30g/cm3,熔点为480~500℃,该颗粒精炼剂中水分含量≤0.5%,该精炼剂颗粒的形状呈不规则状。上述降低铝合金烧损的颗粒精炼剂的制备方法通过实施例1~5进行说明,实施例1~5的工艺参数如下表1所示:表1为一种铝合金用低熔点颗粒精炼剂的制备方法实施例1~5的工艺参数下面以实施例1为例详细说明一种铝合金用低熔点颗粒精炼剂的制备方法,包括以下步骤:步骤1:将氯化钠、氯化钾、氟化钠和硫酸钠原料混合后的混合料放入熔化炉中进行熔炼,第一次加热温度为445℃,加热的速率为3℃/min,并保温20min,后再加热至700℃得熔融料。步骤2:将步骤1中熔融料保温50min后冷凝至固态,采用颚式破碎机将固态料破碎成块状,保证块状料的粒径在15cm以下,后采用锤式破碎机将块状料破碎成粉末状,再采用200筛目的目筛进行过筛,筛分后得粉状料和粒状料。将筛分后的粒状料再次采用锤式破碎机进行破碎,或者将粒状料返回步骤1的熔化炉中重新熔炼。步骤3:将步骤2中过筛后的粉状料加入环氧树脂,加入环氧树脂的质量占粉状料的8%~10%,采用挤压造粒机进行挤压造粒,得到粒径为0.83~3.15mm的颗粒精炼剂。步骤3中采用的挤压造粒机中造粒辊筒的结构如图1所示,包括外层筒10和内层筒11,内层筒11与外层筒10之间固定有加强筋12,外层筒10与内层筒11之间形成有通道夹层13,外层筒10的两端均同轴连接有管道,管道与通道夹层13连通,在外层筒10上均布有多个造粒槽14,造粒槽14内粘接有弹性层15,结合图2所示,弹性层15与造粒槽14之间形成气腔16,在造粒槽14的底部开设有连通气腔16与通道夹层13的气流孔17,在内层筒11的外壁上均布有多个凸起18,且各凸起18均与外层筒10上的造粒槽14位置相对,各凸起18的高度各不相同,因此凸起18与造粒槽14之间通道的间距也不同,同时各造粒槽14上的气流孔17开设的位置也不同,气流孔17的大小也不相同。在造粒时,一组侧壁贴合的造粒辊筒形成相对转动,且两个造粒辊筒相邻部位的切线方向朝下,造粒时粉状料与粘接剂混合后从上往下掉落在两个造粒辊筒之间,图1中箭头所指为冷气流动的方向,在造粒过程中,高压冷气体(温度不高于18℃)从造粒辊筒的左端进入通道夹层13中,后沿着通道夹层13从造粒辊筒的右端流出,当冷气流流动至凸起18与造粒槽14之间时,此时由于凸起18与造粒槽14之间的通道的间距缩小,气体流速增大,因此气流压强减小,因此气腔16内的气体经气流孔17进入到通道夹层13中,同时弹性层15向气流孔17处发生形变,弹性层15形变过程中将进入到造粒槽14内的粉状料进行挤压,从而形成颗粒排出。由于各凸起18与造粒槽14之间的通道间距不同,同时气流孔17的大小也不同,因此各凸起18与造粒槽14之间的压强也会不一致,使得各弹性层15产生形变的大小不同,从而形成了不同的形状不规则的颗粒精炼剂。需要注意的是,本申请中通入造粒辊筒内的高压气体流速并不是恒定的,而处于变化的状态,这样弹性层15有机会恢复形变,从而完成造粒。采用这样的造粒辊筒,不仅能够得到形状各异的颗粒精炼剂,另外通入的高压冷气还能对颗粒精炼剂以及造粒辊筒进行降温处理,提高造粒辊筒的使用寿命,同时保证颗粒精炼剂的温度不会过高。实施例2~5与实施例1的工艺相同,区别仅在于工艺参数不同。另设置两组对比例与实施例1~5制得的颗粒精炼剂进行对比实验:对比例1:与实施例1的区别在于,对比例1中没有进行步骤3,仅采用破碎机将固态料破碎至粒径为1~4mm的颗粒。对比例2:与实施例1的区别在于,对比例2制得的颗粒约为2mm的球状颗粒。现将实施例1~5和对比例1~2制得的颗粒精炼剂进行喷粉精炼实验:根据生产需求,将实施例1~5和对比例1~2制得的精炼剂加入到喷粉精炼罐内,在铝液温度为700~750℃时,打开精炼罐,通入惰性气体(惰性气体压力为1.2~1.8kg/cm2),惰性气体把颗粒精炼剂喷入铝熔体中,在弥散性小气泡和颗粒精炼剂的联合作用下,除去铝液中的氧化夹杂、碱金属和氢气等,精炼时间每次15~20分钟。精炼后的铝熔体凝固后,对其铸态组织进行检测,测其中碱金属和氧化夹杂去除率,取平均值。实施例1~5与对比例1~2的实验结果如下表2所示:表2为实施例1~5与对比例1~2制得精炼剂的碱金属和氧化夹杂去除率实施例1实施例2实施例3实施例4实施例5对比例1对比例2碱金属除杂率72%74%70%75%80%55%67%氧化夹杂去除率75%72%72%70%77%56%61%根据上表2可知:1、实施例1~5得到的颗粒精炼剂在铝熔体精炼的工业应用中,铝熔体中碱金属的去除率可达70~80%,铝熔体中的氧化夹杂的去除率在70%以上,大大减轻了铝熔体后续的过滤压力,同时使得铝合金的铸钛组织得到极大的改善,质量得到很大的提升。2、对比例1中由于未采用挤压造粒成型,经检测对比例1制得的颗粒精炼剂密度约为1.77~1.95g/cm3,密度与铝合金溶体的密度接近,不能快速的包裹渣团上浮,使得碱金属和氧化夹杂的去除率均有所下降。3、对比例2中由于将颗粒制成了球状颗粒,其在进入铝溶体内之后,与溶体之间横向或竖向的接触面积减小,因此对渣团的吸附作用有所下降,结合检测结果可见,碱金属和氧化夹杂的去除率均略有下降。以上所述的仅是本发明的实施例,方案中公知的具体结构及特性等常识在此未作过多描述。应当指出,对于本领域的技术人员来说,在不脱离本发明结构的前提下,还可以作出若干变形和改进,这些也应该视为本发明的保护范围,这些都不会影响本发明实施的效果和专利的实用性。本申请要求的保护范围应当以其权利要求的内容为准,说明书中的具体实施方式等记载可以用于解释权利要求的内容。当前第1页12