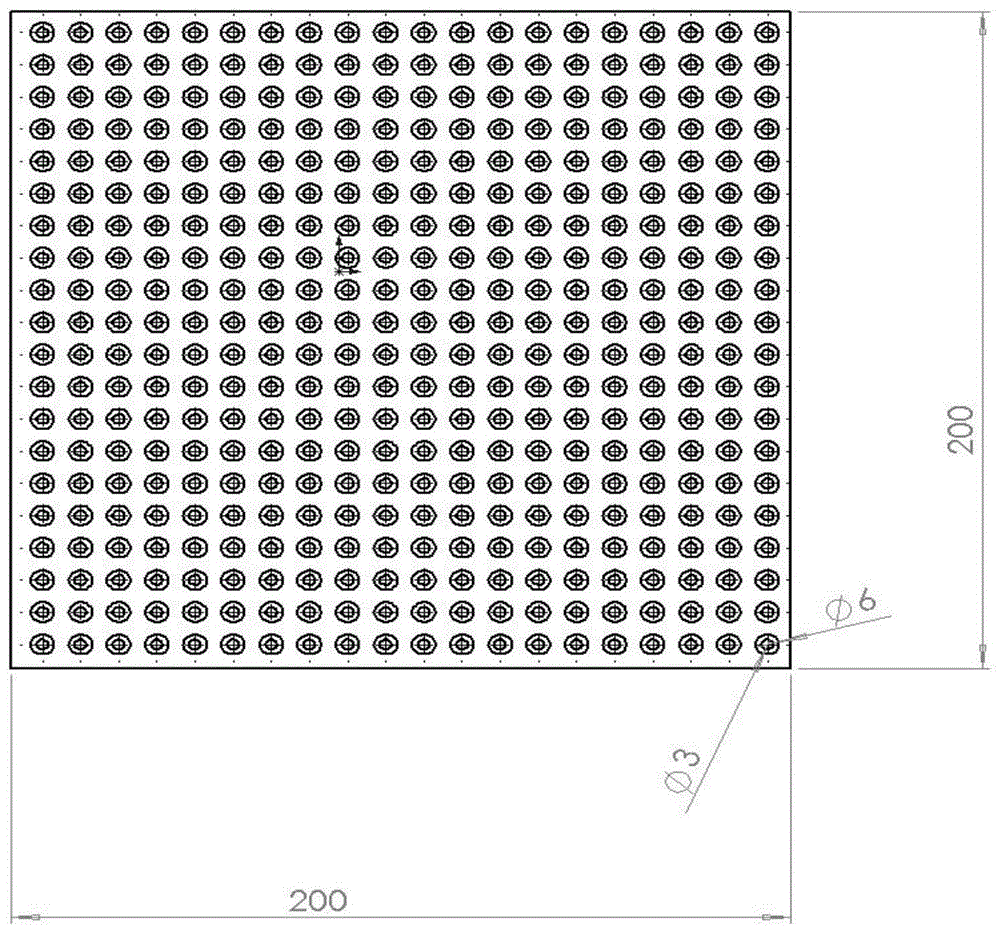
本发明涉及复合材料制造
技术领域:
,尤其涉及一种铝合金-氧化铝复合材料及其制备方法和应用。
背景技术:
:制动盘的性能对于车辆行驶安全有着至关重要的意义,同时也需要兼顾制动盘对轻量化、环保低噪音的要求,传统的铸铁制动盘存在耐磨性较差、质量较大的缺陷,在雨天行车时湿摩擦系数不稳定。近年来,氧化铝增强铝基复合材料成为人们的研究热点。研究人员通过压力铸造、真空铸造、低压铸造等方法制备出了具有双连通结构的氧化铝/金属复合材料。这类双连通结构的金属/氧化铝复合材料采用了3d网络氧化铝骨架作为增强材料。但是3d网络氧化铝骨架的制造效率较低,需要多次挂浆浸渍;烧结成品率较低,烧成骨架有较多闭孔,导致骨架与金属基体结合不牢固;成品骨架硬度过高,造成摩擦副损耗较大。技术实现要素:本发明的目的在于提供一种铝合金-氧化铝复合材料的制备方法,该方法制备的铝合金-氧化铝复合材料中氧化铝骨架与铝合金基体结合牢固,复合材料的摩擦损耗小。为了实现上述发明目的,本发明提供以下技术方案:本发明提供了一种铝合金-氧化铝复合材料的制备方法,包括以下步骤:将干粉与水混合,得到氧化铝浆料;采用模压法或流延法将所述氧化铝浆料进行成型,得到氧化铝坯料;将所述氧化铝坯料进行烧结和钻孔,得到氧化铝骨架;采用浸渗法或压力铸造法将所述氧化铝骨架与铝合金熔液进行复合,得到铝合金-氧化铝复合材料;所述干粉包括以下质量百分含量的组分:氧化铝30~75%,氧化镁14~30%,氧化钛14~30%,分散剂1%,聚乙烯醇1%。优选的,所述干粉与水的质量比为100∶(40~80)。优选的,采用模压法进行所述成型时,成型压力为5mpa,保压时间为5min;采用流延法进行所述成型时,氧化铝浆料的粘度为700~900mpa﹒s,加热温度为90~150℃,加热时间为30~120s。优选的,所述烧结的控温程序为:第一阶段由室温升温至1100~1300℃,升温速率为3~5℃/min;第二阶段在1100~1300℃条件下保温30~60min;第三阶段由1100~1300℃升温至1300~1600℃,升温速率为5℃/min;第四阶段在1300~1600℃条件下保温1h,第五阶段随炉冷却至室温。优选的,所述铝合金熔液的制备过程为将铝合金进行预热处理,得到铝合金熔液;所述预热处理的温度为700~900℃,保温时间为2~2.5h。优选的,采用浸渗法进行所述复合时,浸渗温度为700~800℃,保温时间为1~3h;采用压力铸造法进行所述复合时,铸造压力为1~30mpa,保压时间为5~10min。优选的,所述分散剂为羧甲基纤维素钠或偏六磷酸铵。优选的,采用质量百分含量为30~60%的高岭土替换所述氧化镁和氧化钛。本发明提供了上述技术方案所述制备方法制备得到的铝合金-氧化铝复合材料。本发明提供了上述技术方案所述铝合金-氧化铝复合材料在制动盘中的应用。本发明提供了一种铝合金-氧化铝复合材料的制备方法,将干粉与水混合,得到氧化铝浆料;采用模压法或流延法将所述氧化铝浆料进行成型,得到氧化铝坯料;将所述氧化铝坯料进行烧结和钻孔,得到氧化铝骨架;采用浸渗法或压力铸造法将所述氧化铝骨架与铝合金熔液进行复合,得到铝合金-氧化铝复合材料;所述干粉包括以下质量百分含量的组分:氧化铝75%~30%,氧化镁14~30%,氧化钛14~30%,分散剂1%,聚乙烯醇1%。本发明采用模压法或流延法制备氧化铝骨架,工艺成熟,且钻孔操作快捷简单,这使得氧化铝骨架成品率达到95%,同时提高了生产效率和良品率;本发明使用的氧化铝材料具有多孔疏松结构,制备的氧化铝骨架质量轻(密度仅为1.1~1.5g/cm3),在烧结完成后的骨架中存在大量的微孔,使得骨架具有非常良好的吸波吸热性能;本发明最终制备的铝合金-氧化铝复合材料的密度仅为2.3~2.5g/cm3,相对于铸钢制动盘制动盘的密度(7.8kg/cm3)明显降低,极大降低了牵引功率的损耗;本发明采用浸渗法或压力铸造法将所述氧化铝骨架与所述铝合金熔液进行复合,可以有效提高生产效率,而且成本较低;进一步的,本发明制备氧化铝骨架时烧结温度为1300~1400℃,传统的碳化硅泡沫骨架在烧结时所需的温度为1600~1700℃,因此本发明制备氧化铝骨架的方法能够减少能耗,降低生产成本;本发明制备的氧化铝骨架的硬度达到hra70,将铝合金-氧化铝复合材料用于带有摩擦副的制动盘时,氧化铝骨架不会因硬度过高而对磨擦副造成严重的损坏,相反这种硬度适中的摩擦面在摩擦过程中掉落一定的粉末,形成自修复的保护膜,提高了制动盘和摩擦副的使用寿命;本发明能够实现较大尺寸(根据工业生产的需求决定,理论上可以达到2m×2m)氧化铝骨架的工业化生产,制备的氧化铝骨架具有良好的二次加工性能,方便切割;本发明将铝合金良好的韧性和氧化铝的耐热耐磨性良好的结合起来制备铝合金-氧化铝复合材料,提高了铝合金的耐磨性,将该铝合金-氧化铝复合材料用于摩擦副时,磨损量<30mg/mj;且该铝合金-氧化铝复合材料具有较好的导热系数,导热系数为75~150w/(m2·k),能够作为高速、吸收高能量的制动材料。附图说明图1为实施例1制备的氧化铝骨架的正视图;图2为实施例1制备的氧化铝骨架的剖面图。具体实施方式本发明提供了一种铝合金-氧化铝复合材料的制备方法,包括以下步骤:将干粉与水混合,得到氧化铝浆料;采用模压法或流延法将所述氧化铝浆料进行成型,得到氧化铝坯料;将所述氧化铝坯料进行烧结和钻孔,得到氧化铝骨架;采用浸渗法或压力铸造法将所述氧化铝骨架与铝合金熔液进行复合,得到铝合金-氧化铝复合材料;所述干粉包括以下质量百分含量的组分:氧化铝75%~30%,氧化镁14~30%,氧化钛14~30%,分散剂1%,聚乙烯醇1%。在本发明中,若无特殊说明,所需制备原料均为本领域技术人员熟知的市售商品。本发明将干粉与水混合,得到氧化铝浆料。在本发明中,所述干粉包括以下质量百分含量的组分:氧化铝75%~30%,氧化镁14~30%,氧化钛14~30%,分散剂1%,聚乙烯醇1%;优选为氧化铝60%~45%,氧化镁20~25%,氧化钛20~25%,分散剂1%,聚乙烯醇1%。在本发明中,所述氧化铝优选来源于铝灰。在本发明中,所述分散剂优选为羧甲基纤维素钠或偏六磷酸铵。在本发明中,所述干粉与水的质量比优选为100∶(40~80),更优选为100∶(45~75),最优选为100∶(50~60)。将干粉与水混合前,本发明优选将所述干粉中氧化铝、氧化镁和氧化钛混合,进行球磨,得到混合粉末。在本发明中,所述球磨的时间优选为3h。完成所述球磨后,所得混合粉末的粒度优选为6~15μm。本发明对所述球磨的具体条件没有特殊的限定,选用本领域技术人员熟知的条件进行球磨即可。本发明通过球磨减小干粉粉末粒度并使得原料组分均匀混合。将干粉与水混合前,本发明优选将所述分散剂和羧甲基纤维素钠溶于水中,得到混合溶液,可以有效避免在混合过程中分散剂分布不均匀。在本发明中,所述水的温度优选为90℃。得到混合粉末和混合溶液后,本发明优选将所述混合粉末与混合溶液进行搅拌混合,得到氧化铝浆料;所述搅拌混合的时间优选为1~3h,更优选为2h,搅拌速率优选为1000~3000r/min,更优选为1500~2500r/min。作为本发明的另一个方案,本发明优选采用质量百分含量为30~60%的高岭土替换所述氧化镁和氧化钛。当使用高岭土替换氧化镁和氧化钛时,本发明对所述原料的混合顺序不作任何更改,与氧化镁和氧化钛的方案保持一致即可。得到氧化铝浆料后,本发明采用模压法或流延法将所述氧化铝浆料进行成型,得到氧化铝坯料。在本发明中,采用模压法进行所述成型时,成型压力优选为5mpa,保压时间优选为5min。本发明对所述模压成型所用的模具没有特殊的限定,选用本领域技术人员熟知的模具即可。完成所述成型后,本发明优选将所得成型坯料在室温干燥48h后,放入烘干机在120℃条件下烘干12h,得到氧化铝坯料。在本发明中,升温至烘干所需温度的升温速率优选≤3℃/min,本发明通过进一步控制烘干的升温速率来控制水蒸发的速度,避免氧化铝坯料开裂,从而进一步提高氧化铝坯料的强度。在本发明中,采用模压法进行所述成型时,所得氧化铝坯料的厚度优选为5~10mm,更优选为6~8mm;所述氧化铝坯料的形状优选为方形,所述方形的尺寸优选为150×150mm。本发明采用模压法成型,能够有效减少氧化铝坯料在烘干或烧结过程中的开裂倾向。在本发明中,采用流延法进行所述成型时,氧化铝浆料的粘度优选为700~900mpa·s,本发明优选采用红外线灯、热风机或微波烘干机进行辅助加热,所述加热的温度优选为90~150℃,更优选为100~120℃;所述加热的时间优选为30~120s,更优选为50~100s,最优选为60~80s。在本发明中,采用流延法进行所述成型时,所得氧化铝坯料的厚度优选为3~10mm,尺寸优选为200mm×200mm。得到氧化铝坯料后,本发明将所述氧化铝坯料进行烧结和钻孔,得到氧化铝骨架。在本发明中,当所述干粉成分包括氧化镁和氧化钛时,优选先进行烧结,再进行钻孔;当所述干粉成分包括高岭土时,由于加入高岭土的氧化铝坯料硬度较高,在烧结后难以加工成型,本发明优选先进行钻孔,再进行烧结。在本发明中,当采用模压法进行成型时,所述烧结的控温程序优选为:第一阶段由室温升温至1100~1300℃,升温速率3~5℃/min;第二阶段在1100~1300℃条件下保温30~60min;第三阶段由1100~1300℃升温至1300~1600℃,升温速率为5℃/min;第四阶段在1300~1600℃条件下保温1h,第五阶段随炉冷却至室温。本发明优选在电阻炉中进行所述烧结。本发明在第一阶段使用较低的升温速度有利于减小氧化铝坯料的开裂倾向。在本发明中,当采用流延法进行成型时,所述烧结的控温程序优选为:第一阶段用时1h从室温升至100℃,保温1h;第二阶段用时4h从100℃升温至1100℃,保温30min;第三阶段用时1h从1100℃升温至1300℃;第四阶段在1300℃保温1h;第五阶段随炉冷却。当所述干粉成分包括氧化镁和氧化钛时,完成所述烧结后,本发明优选将烧结所得氧化铝片进行钻孔。在本发明中,所述氧化铝片的两面分别称为大孔面和小孔面,所述大孔面为摩擦面,小孔面为结合面;对所述摩擦面进行钻孔的孔径优选为3~10mm,对结合面进行钻孔的孔径优选为2~6mm。在本发明中,进行钻孔所用钻头优选为台阶钻头或变径钻头。本发明优选根据铝合金和氧化铝的体积比例来确定钻孔数量,首先规定复合材料的体积,确定氧化铝的体积分数后,根据公式计算钻孔数量,钻孔数量=(复合材料体积-复合材料体积×氧化铝体积分数)/单个孔体积;比如铝合金-氧化铝复合材料中氧化铝体积分数为10~40%,如所需氧化铝占铝合金-氧化铝复合材料的体积分数为10%时,在尺寸为150mm×150mm的氧化铝片上钻孔360个。在本发明中,进行所述钻孔时,钻头加载速率优选为1mm/3s;在钻孔过程中,本发明优选加水润滑以减小氧化铝对钻头的磨损和降低钻孔时的温度,加水量优选为1ml/s。本发明精确设计氧化铝片的钻孔形式制备氧化铝骨架,得到的氧化铝骨架中,一侧表面有直径较大的孔,另一侧表面有直径较小的孔,孔洞较大且分布均匀,且这些孔连通,该氧化铝骨架能够牢固扎入铝合金基体的表面和铝合金复合形成铝合金-氧化铝复合材料,能够提高铝合金和氧化铝骨架的结合能力。本发明通过在氧化铝片上钻孔使其形成氧化铝骨架,由于氧化铝骨架中摩擦面的孔径较大,结合面的孔径较小,因此氧化铝骨架在与铝合金复合时会被这种结构钉扎在铝合金基体上,提高了铝合金-氧化铝复合材料的复合性能;在进行复合时,由于骨架的孔径较为规则,同时孔径较大,骨架厚度较薄,熔融态的铝合金很容易进入这些孔洞和氧化铝复合在一起。同时,本发明的钻孔工艺步骤简单,既可以提高成品率也可以提高生产效率。当所述干粉成分包括高岭土时,按照上述条件,直接对所述氧化铝坯料进行钻孔,然后进行烧结即可。在模压成型和流延成型的过程中,本发明优选将所述钻孔中的孔设计为六边形、三角形、矩形或梯形,根据所需氧化铝体积分数对孔的数量和分布进行排列,即成型时预留孔结构。本发明采用浸渗法或压力铸造法将所述氧化铝骨架与铝合金熔液进行复合,得到铝合金-氧化铝复合材料。本发明优选将铝合金进行预热处理,得到铝合金熔液;本发明优选根据所述复合的方法具体选择对铝合金进行预热处理的方式。在本发明中,采用浸渗法进行所述复合时,优选包括以下步骤:将所述氧化铝骨架进行保温处理,得到保温氧化铝骨架;将所述铝合金进行预热处理,得到铝合金熔液;将所述保温氧化铝骨架浸入铝合金熔液中,进行浸渗,得到铝合金-氧化铝复合材料。在本发明中,所述保温处理的温度优选为600~800℃,所述保温处理的时间优选为1h。在本发明中,所述预热处理的温度优选为700~900℃,所述预热处理的时间优选为2~2.5h。在本发明中,所述浸渗的温度优选为700~800℃,保温时间优选为1~3h;本发明优选在马弗炉中进行所述氧化铝骨架的保温处理和铝合金的预热处理。将所述保温氧化铝骨架浸入铝合金熔液中之前,本发明优选将所述铝合金熔液通过过滤和扒渣除去氧化渣,本发明对所述过滤和扒渣的条件没有特殊的限定,选用本领域技术人员熟知的条件即可。在本发明中,采用压力铸造法进行所述复合时,优选包括以下步骤:将所述氧化铝骨架置于压铸模具中,进行保温处理,得到保温氧化铝骨架;将铝合金熔化,将所得铝合金熔液倒入压铸模具内进行压力铸造,得到铝合金-氧化铝复合材料。在本发明中,所述保温处理的温度优选为600~800℃,时间优选为1h。在本发明中,所述压铸模具优选为钢制模具;所述压铸模具的尺寸优选为:(90~300)×(90~300)mm。在本发明中,所述铝合金的熔化温度优选为700~900℃;在压力铸造过程中,铸造压力优选为1~30mpa,保压时间优选为5~10min。本发明优选在搅拌或超声处理条件下进行所述复合;所述搅拌的转速优选为3000r/min,所述超声处理的功率优选为100w。本发明采用与超声场辅助铸造技术提高氧化铝骨架与铝合金熔液的润湿性,使得铝合金熔液易于进入氧化铝骨架的孔道和毛细缝隙中,并与氧化铝骨架完成更好的界面结合,同时细化铝合金基体的晶粒,并减少铸造产生的偏析。完成所述复合后,本发明优选将所得材料进行热处理,得到铝合金-氧化铝复合材料。在本发明中,所述热处理的工艺优选采用t6或t651工艺;本发明对所述t6或t651工艺没有特殊的限定,选用本领域技术人员熟知的t6或t651工艺即可。本发明通过热处理进一步提高铝合金-氧化铝复合材料的强度。在本发明中,所述的铝合金-氧化铝复合材料采用的铝合金优选为zlxxx系列、7xxx系列、6xxx系列、5xxx系列或2xxx系列,更优选为zl114、7xxx系列7079、6xxx系列6061、5xxx系列5083或2xxx系列2024。本发明提供了上述技术方案所述制备方法制备得到的铝合金-氧化铝复合材料。在使用氧化镁氧化钛体系作为骨架原料时,烧结出的氧化铝骨架(骨架1)的硬度低于使用高岭土体系的骨架,然而骨架1在实际使用时具有较好的吸波性能和自修复性能,由于其表面存在大量不可见微孔,因此,在高速摩擦后磨屑会嵌入这些孔洞中,可以形成良好的自润滑层,可以作为一种性能优越的摩擦材料使用;而在使用高岭土体系制备氧化铝骨架时,所制备的氧化铝骨架(骨架2)的硬度较高,若作为摩擦材料使用则会对闸片造成较为严重的磨损,然而在使用骨架2作为硬质材料应用于类似盾构机的刀片上,则能大大降低磨损量,提高材料的使用寿命,同时其表面也存在大量微孔,同样可以有效的形成自修复层,可以作为一种性能优越的硬质摩擦材料使用。本发明提供了上述技术方案所述铝合金-氧化铝复合材料在制动盘中的应用。本发明对将所述铝合金-氧化铝复合材料用于制动盘中的方法没有特殊的限定,选用本领域技术人员熟知的方法即可。下面结合实施例对本发明提供的铝合金-氧化铝复合材料及其制备方法和应用进行详细的说明,但是不能把它们理解为对本发明保护范围的限定。实施例1以100g干粉制备氧化铝骨架为例将氧化铝、氧化镁和氧化钛粉末按照质量比75∶14∶14的比例均匀混合,在球磨中磨制3h,得到平均粒径6~10μm的混合粉末;将1g羧甲基纤维素钠和1g聚乙烯醇溶于40ml水中,加热至90℃,进行溶解,得到混合溶液;将所述混合溶液和混合粉末混合,在3000r/min条件下进行搅拌1h,得到氧化铝浆料;将模具喷上氮化硼脱模剂,将所述氧化铝浆料放入模具中加压,压力5mpa,保压时间1min,进行模压成型,得到200mm×200mm方形坯料;将所述方形坯料放入烘箱中进行烘干,控制升温速率为3℃/min,升温至100℃保温1h,得到氧化铝坯料;将所述氧化铝坯料放入电阻炉中,进行烧结,第一阶段从室温升至1100℃,升温速率为6℃/min,第二阶段在1100℃保温30min,第三阶段从1100℃升温至1300℃,用时1h,第四阶段在1300℃保温30min,第五阶段随炉冷却后将烧成的氧化铝片取出,待用;将所述氧化铝片用台阶钻钻孔,钻头加载速率为1mm/3s,按照1ml/s的量加水,钻孔完成后,得到尺寸为150mm×150mm的氧化铝骨架,其中摩擦面孔径为6mm,结合面孔径为3mm,孔数量为360个;将所述氧化铝骨架放入马弗炉中进行保温,保温温度为800℃,保温时间1h,得到保温氧化铝骨架;将铝合金进行预热(铝合金选用zlxxx系列的代表铝合金zl114,化学组成按重量比为镁mg:0.45~0.75,钛ti:0.1~0.2,钛+稀土ti+zr:≤0.20,余量为al),预热温度900℃,保温时间2h,得到铝合金溶液;将所述铝合金熔液除去氧化渣,将所述保温氧化铝骨架放入铝合金熔液中进行浸渗,并在100w条件下使用超声波辅助复合,保温时间1h;将所得材料采用t6热处理工艺进行精加工和打磨,检验,分别包装、入库,得到铝合金-氧化铝复合材料。图1为实施例1制备的氧化铝骨架的正视图;由图可以看出,制备的氧化铝骨架上含有多个均匀的孔结构;图2为实施例1制备的氧化铝骨架的剖面图;由图可以看出,氧化铝骨架的两面孔径大小不同,分别称为大孔面和小孔面,所述大孔面为摩擦面,小孔面为结合面;孔洞较大且分布均匀,且这些孔连通,该氧化铝骨架能够牢固扎入铝合金基体的表面和铝合金复合形成铝合金-氧化铝复合材料。实施例2以100g干粉制备氧化铝骨架为例将氧化铝、高岭土粉末按照69∶29的质量比均匀混合,在球磨中磨制3h,得到平均粒径为10~15μm的混合粉末;将1g羧甲基纤维素钠和1g聚乙烯醇溶于60ml水中,加热至90℃,进行溶解,得到混合溶液;将所述混合溶液和混合粉末混合,在3000r/min条件下进行搅拌2h,得到氧化铝浆料;将模具喷上氮化硼脱模剂,将所述氧化铝浆料放入模具中加压,压力5mpa,保压时间30min,进行模压成型,得到200mm×200mm方形坯料,将所述方形坯料放入烘箱中热风烘干,控制升温速率为3℃/min,升温至100℃保温1h,得到氧化铝坯料;将所述氧化铝坯料用台阶钻钻孔,钻头加载速率为1mm/1s,钻孔完成后,得到尺寸为150mm×150mm的氧化铝骨架,其中摩擦面孔径为6mm,结合面孔径为3mm,孔数量为360个,将所得带孔坯料放入电阻炉中,第一阶段从室温升至1100℃,用时4h,第二阶段在1100℃保温30min,第三阶段从1100℃升温至1300℃,用时1h;第四阶段在1300℃保温1h;第五阶段随炉冷却,得到氧化铝骨架;将所述氧化铝骨架放入马弗炉中保温,保温温度600~800℃,保温时间1h,得到保温氧化铝骨架;选用7079铝合金,化学成分按重量比为(al余量,硅si≤0.30,铁fe≤0.40,铜cu0.40~0.8,锰mn0.10~0.30,镁mg2.9~3.7,铬cr0.10~0.25,锌zn3.8~4.8,钛ti:≤0.10),在温度700~900℃条件下进行预热处理,保温时间2h,得到铝合金熔液;将所述铝合金熔液除去氧化渣,将所述保温氧化铝骨架放入铝合金熔液中进行浸渗处理,并在100w条件下进行超声波辅助复合,保温时间1h,将所得材料采用t651热处理工艺进行精加工和打磨,检验,分别包装、入库,得到铝合金-氧化铝复合材料。实施例3以100g干粉制备氧化铝骨架为例将氧化铝、高岭土粉末按照质量比69∶29均匀混合,球磨3h,得到平均粒径6~10μm的混合粉末;将1g羧甲基纤维素钠和1g聚乙烯醇溶于65ml水中,加热至90℃,进行溶解,得到混合溶液;将所述混合溶液与混合粉末混合,在3000r/min条件下进行搅拌1h,得到氧化铝浆料;将所述氧化铝浆料直接倒入流延机进行成型,将成型氧化铝浆料切割成长宽为200mm×200mm、钻孔完成后,得到尺寸为200mm×200mm的氧化铝骨架,其中摩擦面孔径为6mm,结合面孔径为3mm,孔数量为400个,厚度为3mm的氧化铝坯料;用台阶钻在所述氧化铝坯料上进行钻孔,钻头加载速率为1mm/s;将钻孔所得氧化铝坯料放入电阻炉中,第一阶段使用1h从室温升至100℃,保温1h;第二阶段用4h从100℃升温至1100℃,保温30min;第三阶段使用1h从1100℃升温至1300℃;第四阶段在1300℃保温1h;第五阶段随炉冷却,得到氧化铝骨架;将所述氧化铝骨架放入马弗炉中保温,保温温度600~800℃,保温时间1h;选用6xxx的代表合金6061,化学组成按重量比为(mg0.8~1.2%,si0.4~0.8%,fe0.7%,cu0.15~0.4%,mn0.15%,cr0.04~0.35%,zn0.25%,ti0.15%,al余量),在温度700~900℃条件下进行预热处理,保温时间2h,得到铝合金熔液;将所述铝合金熔液除去氧化渣,将所述保温氧化铝骨架放入铝合金熔液中进行浸渗处理,并使用功率为100w的超声波发生器进行超声波辅助复合,保温时间1h;将所得材料采用t6热处理工艺进行精加工和打磨,检验,分别包装、入库,得到铝合金-氧化铝复合材料。实施例4以100g干粉制备氧化铝骨架为例将氧化铝、高岭土粉末按照69∶29的质量比均匀混合,在球磨中磨制3h,得到平均粒径为10~15μm的混合粉末;将1g羧甲基纤维素钠和1g聚乙烯醇溶于60ml水中,加热至90℃,进行溶解,得到混合溶液;将所述混合溶液和混合粉末混合,在3000r/min条件下进行搅拌2h,得到氧化铝浆料;将模具喷上氮化硼脱模剂,将所述氧化铝浆料放入模具中加压,压力5mpa,保压时间30min,进行模压成型,得到200mm×200mm方形坯料,将所述方形坯料放入烘箱中热风烘干,控制升温速率为3℃/min,升温至100℃保温1h,得到氧化铝坯料;将所述氧化铝坯料使用模具压出异形孔(正方形孔洞),其中摩擦面孔径为6mm,结合面孔径为3mm,孔数量为400个,将所得带孔坯料放入电阻炉中,第一阶段从室温升至1100℃,用时4h,第二阶段在1100℃保温30min,第三阶段从1100℃升温至1300℃,用时1h;第四阶段在1300℃保温1h;第五阶段随炉冷却,得到氧化铝骨架;将所述氧化铝骨架放入马弗炉中保温,保温温度600~800℃,保温时间1h,得到保温氧化铝骨架;选用5xxx代表合金5083铝合金,化学成分按重量比为(铝al余量,硅si≤0.40,铜cu≤0.10,镁mg4.0~4.9,锌zn≤0.25,锰mn0.40~1.0,钛ti≤0.15,铬cr0.05~0.25,铁0.000~0.400),在温度700~900℃条件下进行预热处理,保温时间2h,得到铝合金熔液;将所述铝合金熔液除去氧化渣,将所述保温氧化铝骨架放入铝合金熔液中进行浸渗处理,并在100w条件下进行超声波辅助复合,保温时间1h,将所得材料采用t651热处理工艺进行精加工和打磨,检验,分别包装、入库,得到铝合金-氧化铝复合材料。实施例5以100g干粉制备氧化铝骨架为例将氧化铝、氧化镁和氧化钛粉末按照质量比75∶14∶14的比例均匀混合,在球磨中磨制3h,得到平均粒径6~10μm的混合粉末;将1g羧甲基纤维素钠和1g聚乙烯醇溶于40ml水中,加热至90℃,进行溶解,得到混合溶液;将所述混合溶液和混合粉末混合,在1000~3000r/min条件下进行搅拌1h,得到氧化铝浆料;将模具喷上氮化硼脱模剂,将所述氧化铝浆料放入模具中加压,压力5mpa,保压时间1min,进行模压成型,得到200mm×200mm方形坯料,阴干后待用;将所述方形坯料放入烘箱中进行烘干,控制升温速率为3℃/min,升温至100℃保温1h,得到氧化铝坯料;将所述氧化铝坯料放入电阻炉中,进行烧结,第一阶段从室温升至1100℃,用时3h,第二阶段在1100℃保温30min,第三阶段从1100℃升温至1300℃,用时1h;第四阶段在1300℃保温30min,第五阶段随炉冷却后将所得氧化铝片用台阶钻钻孔,钻头加载速率为1mm/3s,按照1ml/s的量加水,钻孔完成后,得到尺寸为150mm×150mm的氧化铝骨架,其中摩擦面孔径为6mm,结合面孔径为3mm,孔数量为360个;将所述氧化铝骨架固定在钢制模具的铸腔内进行保温,保温温度600~800℃,保温时间1h;选用2xxx代表合金2024铝合金,化学成分按重量比为(铜cu3.8%~4.9%,锰mn0.30%~1.0%,镁mg1.2%~1.8%,铬cr0.10%,锌zn0.25%,铝al余量),将铝合金在700~900℃进行预热处理,保温2h后倒入压力铸造机的保温炉内进行压力铸造,压力为1~30mpa,保压时间为5~10min;将所得材料采用t6热处理工艺进行精加工和打磨,检验,分别包装、入库,得到铝合金-氧化铝复合材料。性能测试将实施例1~5制备的铝合金-氧化铝复合材料进行性能测试:1)对实施例1~5制备的氧化铝骨架和铝合金-氧化铝复合材料进行机械性能测试,具体结果见表1。表1实施例1~5制备的氧化铝骨架和铝合金-氧化铝复合材料的性能数据2)对实施例1~5制备的铝合金-氧化铝复合材料进行摩擦表面粗糙度测定,对铝合金-氧化铝复合材料中的铝合金基体的晶粒尺寸进行测定;具体结果见表2。表2实施例1~5制备的铝合金-氧化铝复合材料的摩擦表面粗糙度案例摩擦表面粗糙度ra晶粒尺寸μm实施例10.8~1.680实施例20.8~1.670实施例30.8~1.670实施例40.8~1.650实施例50.8~1.6703)将实施例1~5制备的铝合金-氧化铝复合材料与粉末冶金铜材料组成摩擦副,按照tj/cl310-2013进行摩擦实验,结果表面,本发明制备的铝合金-氧化铝复合材料摩擦系数大,噪音小,干湿条件下摩擦系数稳定,未产生可见热裂纹;具体数据见表3。表3实施例1~5制备的铝合金-氧化铝复合材料用于摩擦副时的相关性能及用途由以上实施例可知,本发明提供了一种铝合金-氧化铝复合材料的制备方法,本发明采用模压法或流延法制备氧化铝骨架,氧化铝骨架成品率达到95%,同时提高了生产效率和良品率;本发明制备的氧化铝骨架的硬度达到hra70,将铝合金-氧化铝复合材料用于带有摩擦副的制动盘时,氧化铝骨架不会因硬度过高而对磨擦副造成严重的损坏,提高了制动盘和摩擦副的使用寿命;本发明将铝合金良好的韧性和氧化铝的耐热耐磨性良好的结合起来制备铝合金-氧化铝复合材料,提高了铝合金的耐磨性,将该铝合金-氧化铝复合材料用于摩擦副时,磨损量<30mg/mj;且该铝合金-氧化铝复合材料具有较好的导热系数,能够作为高速、吸收高能量的制动材料。以上所述仅是本发明的优选实施方式,应当指出,对于本
技术领域:
的普通技术人员来说,在不脱离本发明原理的前提下,还可以做出若干改进和润饰,这些改进和润饰也应视为本发明的保护范围。当前第1页12