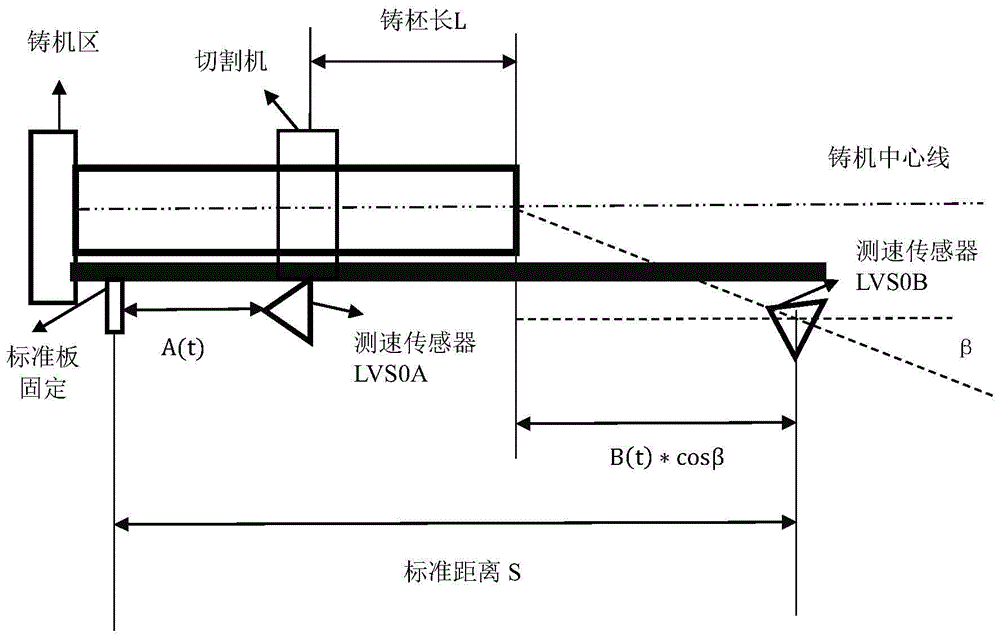
本发明涉及板柸长度测量
技术领域:
,具体地,涉及一种采用激光测速传感器进行板柸长度测量的方法和系统,尤其是涉及一种使用激光测速传感器为基础的连铸柸长度进行测量的方法。
背景技术:
:引锭杆头部、尾部、板柸头部和板柸尾部的位置信息,以及铸造长、板柸长等长度信息,是连铸机运转过程中的重要数据。这些位置信息和长度信息可以统称为连铸机的板柸跟踪信息。现有绝大多数连铸机使用扇形段夹送辊编码器信号和切割机测长辊信号,经过机械参数折算后得到板柸跟踪信息。个别连铸机使用红外定尺技术跟踪板柸头部位置,根据板柸长度设定值发出板柸切割起始指令。板柸质量管理模型根据铸造长分段归集板柸的生命周期数据,意味着,铸造长或板柸长是板柸质量数据可追溯的依据。使用夹送辊和测长辊的编码器信号,是机械接触式测量方式,辊子和板柸打滑(产生静摩擦)、辊子磨损、机械误差累积等导致控制系统计算得到的铸造长或板柸长和实际的板柸长度不一致。这种不一致,相对于一块板柸而言,误差基本属于可接受范围,一般不会影响板柸切割作业。但是长时间浇注后将会产生明显的累计误差,累计误差大于板柸定尺长度,对质量异议分析、质量问题追溯、前后工序质量模型结合等工作造成障碍,亟待改进。若使用红外定尺,虽然没有打滑、机械磨损等问题,但是存在非线性、稳定性相对差、系统检测误差大、安装位置限制等问题,但同样存在累计误差问题。若使用激光测长的方式测量定尺长度,存在辊道振动导致角度偏移造成误差偏大的问题,以及板柸表面不光滑造成的漫反射而导致信号丢失的问题。专利文献103341608a公开一种连铸柸定尺检测切割装置,以编码器为基础的定尺检测装置,主要包括具有主动辊和从动辊的拉矫机、切割单元以及脉冲编码器。它的特征是:将脉冲编码器与具有主动辊和从动辊的拉矫机连接在一起,拉矫机随着铸柸的运动而转动,脉冲编码器根据拉矫机的转动计算铸柸的长度。但是,脉冲编码器和拉矫辊进行连接,根据拉矫机的转动来计算柸子的长度,缺点是由于拉矫辊长时间与温度高的板柸进行接触而造成的辊子磨损,一方面会降低定尺的精度,另一方面也会增加维护的费用。专利文献203343397u公开一种连铸机切割机的定尺系统,以定尺摄像机为传感器,以图像处理技术为核心的测量、控制系统。红外摄像机安装在现场固定的位置,当板柸进入摄像范围内从图像中提取板柸信息。该专利在测量板柸跟踪的时候存在一定的误差,正常情况下的板柸定尺误差在±20mm以内,如果由于辊道发生振动会导致摄像头与辊道的夹角发生变化,也会造成板柸定尺发生变化,而摄像镜头的微小移动是通过肉眼无法观察到的。另外,由于板柸表面不够光滑,容易由于漫反射导致信号丢失的情况发生。技术实现要素:针对现有技术中的缺陷,本发明的目的是提供一种采用激光测速传感器进行板柸跟踪测量的方法和系统。根据本发明提供的一种采用激光测速传感器进行板柸跟踪测量的方法,包括:激光测速步骤:在切割辊道前后分别增设一个激光测速传感器,记为前激光测速传感器和后激光测速传感器,当切割辊道的中间存在板柸时,开始启动激光测速传感器进行测速;距离测算步骤:控制单元识别后激光测速传感器的有效信号,根据有效信号对速度值进行积分计算,得到移动距离值,控制单元识别激光测速传感器的无效信号,使用辅助编码器根据无效信号计算移动距离值。优选地,所述的采用激光测速传感器进行板柸跟踪测量的方法,还包括跟踪测量步骤:在切割辊道两侧分别安装有热金属检测仪,记为左侧热金属检测仪和右侧热金属检测仪,测定左侧热金属检测仪和右侧热金属检测仪之间的检测距离,所述检测距离能够修正铸造长度,浇注开始后,铸柸移动通过切割辊道,若控制单元收到左侧热金属检测仪的信号,按照实际的冶金长度修正铸造长度,所述冶金长度是指连铸机的结晶器液面到铸柸末端之间的长度;若控制单元收到右侧热金属检测仪的信号,按照检测距离修正铸造长度。优选地,所述移动距离值根据下式计算:其中,s表示移动距离值;c表示光在大气中的传播速度;dt表示对时间t求微分;t0为光往返两测量点一次需要的时间。优选地,所述板柸长度通过下式计算:l=s-a(t)-b(t)cosβ其中,l表示板柸长度;s表示后激光测速传感器与固定标准板之间的距离;β表示后激光测速传感器与水平面之间的夹角;a(t)表示前激光测速传感器与固定标准板之间的距离;b(t)表示后激光测速传感器与板柸头部之间的距离。优选地,所述所述根据本发明提供的一种采用激光测速传感器进行板柸跟踪测量的系统,包括:激光测速模块:在切割辊道前后分别增设一个激光测速传感器,记为前激光测速传感器和后激光测速传感器,当切割辊道的中间存在板柸时,开始启动激光测速传感器进行测速;距离测算模块:控制单元识别后激光测速传感器的有效信号,根据有效信号对速度值进行积分计算,得到移动距离值,控制单元识别激光测速传感器的无效信号,使用辅助编码器根据无效信号计算移动距离值。优选地,还包括跟踪测量模块:在切割辊道两侧分别安装有热金属检测仪,记为左侧热金属检测仪和右侧热金属检测仪,测定左侧热金属检测仪和右侧热金属检测仪之间的检测距离,所述检测距离能够修正铸造长度,浇注开始后,铸柸移动通过切割辊道,若控制单元收到左侧热金属检测仪的信号,按照实际的冶金长度修正铸造长度,所述冶金长度是指连铸机的结晶器液面到铸柸末端之间的长度;若控制单元收到右侧热金属检测仪的信号,按照检测距离修正铸造长度。与现有技术相比,本发明具有如下的有益效果:1、能够解决测长辊打滑产生误差的问题,且根据精度跟踪信息反推是否存在打滑问题;2、对异常位置的跟踪更加准确,能够减少废柸的长度损失,使得取消测长辊,降低机械设备的维护费用;3、提高跟踪精度后,铸造长信息更准确,板柸长信息也更准确,火焰切割割缝的大小可以通过计算得到;4、长辊的铸造长度数据与实际情况更加吻合,可为质量分析、模型开发等工作提供便利条件和坚实基础。附图说明通过阅读参照以下附图对非限制性实施例所作的详细描述,本发明的其它特征、目的和优点将会变得更明显:图1为本发明的三步过程示意图。具体实施方式下面结合具体实施例对本发明进行详细说明。以下实施例将有助于本领域的技术人员进一步理解本发明,但不以任何形式限制本发明。应当指出的是,对本领域的普通技术人员来说,在不脱离本发明构思的前提下,还可以做出若干变化和改进。这些都属于本发明的保护范围。本发明的具体通过以下步骤实施:激光测速步骤:在切割辊道前后分别增设一个激光测速传感器,记为前激光测速传感器和后激光测速传感器,当切割辊道的中间存在板柸时,开始启动激光测速传感器进行测速;距离测算步骤:控制单元识别后激光测速传感器的有效信号,根据有效信号对速度值进行积分计算,得到移动距离值,控制单元识别激光测速传感器的无效信号,使用辅助编码器根据无效信号计算移动距离值。跟踪测量步骤:在切割辊道两侧分别安装有热金属检测仪,记为左侧热金属检测仪和右侧热金属检测仪,测定左侧热金属检测仪和右侧热金属检测仪之间的检测距离,所述检测距离能够修正铸造长度,浇注开始后,铸柸移动通过切割辊道,若控制单元收到左侧热金属检测仪的信号,按照实际的冶金长度修正铸造长度,所述冶金长度是指连铸机的结晶器液面到铸柸末端之间的长度;若控制单元收到右侧热金属检测仪的信号,按照检测距离修正铸造长度。关于检测,如图1所示,在切割辊道前后分别增设一个激光测速传感器(lvs0a和lvs0b),直接检测铸柸或者板柸的移动速度,检测范围大。激光测速传感器是一种基于光波测距的新型测量传感器,它在检测领域中具有十分广泛的应用,可以用于板材和管材在线切割,和电缆或砂纸速度测量;由于它属于一种无接触式测量方式,因此适合于测量敏感或者不能触摸的物体,如绒布和毛皮等纺织品、涂层和粘胶表面、以及泡沫橡胶的测速;还有可以用于金属加工业中,如测量钢铁的速度、双抽速度测量、涂装工艺的控制等。测量时,plc收到lvs0a和lvs0b的有效信号后,根据公式即可得到铸柸移动的距离值,其中c为光在大气中的传播速度,t0为光往返两测量点一次需要的时间。同时利用现有的安装在辊道两侧固定位置的热金属检测仪。浇注开始后,铸柸移动切割辊道后,一旦plc收到板柸头部出现的信号,由于该位置到结晶器下口的长度为固定值,即可根据该数据修正铸造长信息。关于计算,见表1,由于板柸的测算是以光波测距为基础的,已知lvs0b和标准板之间的距离s,以及和水平面之间的夹角β,通过激光测距传感器测得a(t)、b(t),则板柸的长度l可以通过公式l=s-a(t)-b(t)cosβ计算得到,其中和ta,tb表示光在传感器和测量点之间往返一次所需的时间。见表2,plc的扫描周期t为10ms,浇注过程中的拉速v为1.2m/min,一个扫描周期内铸柸的移动距离la是0.2mm。激光测速传感器的检测误差cd小于0.05%,即铸柸移动长度lb为10m时,将传感器的误差乘以板柸长度得到长度误差是5mm。在plc中,综合现有的编码器信号、光电开关信号以及新增的测速信号,测速仪信号有效时,使用测速仪的信号计算移动距离增量;无效时,使用编码器信号计算移动距离增量。表1铸柸长计算中的相关参数标准板与测速传感器lvs0a之间的标准距离a(t)标准板与测速传感器lvs0b之间的距离s测速传感器lvs0b与板柸头部之间的距离b(t)测速传感器lvs0b与水平面的之间的夹角β连铸柸长度l表2根据3cc使用的相关参数实际值拉速v扫描周期t移动距离la检测误差cd移动长度lb计算误差ld1.2m/min10ms0.2mm0.05%10m5mm在本申请的描述中,需要理解的是,术语“上”、“下”、“前”、“后”、“左”、“右”、“竖直”、“水平”、“顶”、“底”、“内”、“外”等指示的方位或位置关系为基于附图所示的方位或位置关系,仅是为了便于描述本申请和简化描述,而不是指示或暗示所指的装置或元件必须具有特定的方位、以特定的方位构造和操作,因此不能理解为对本申请的限制。以上对本发明的具体实施例进行了描述。需要理解的是,本发明并不局限于上述特定实施方式,本领域技术人员可以在权利要求的范围内做出各种变化或修改,这并不影响本发明的实质内容。在不冲突的情况下,本申请的实施例和实施例中的特征可以任意相互组合。当前第1页12