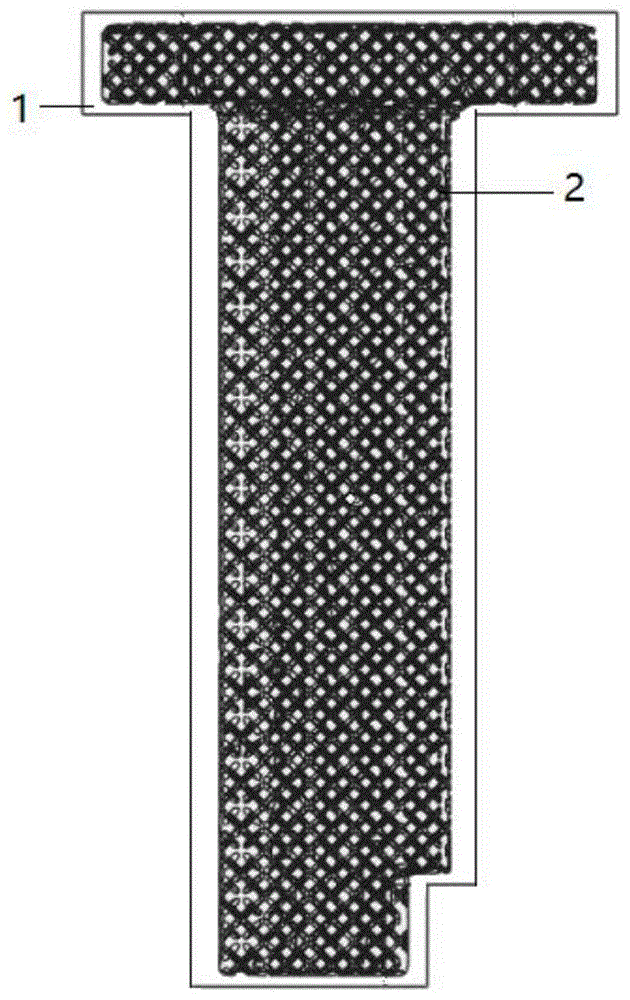
本发明属于高温合金空心叶片加工制造领域,具体涉及一种空心叶片易脱除氧化铝陶瓷型芯及其制备方法。
背景技术:
:航空航天、船舶以及电力等工业用发动机推重比的不断升级对燃气轮机的热效率要求越来越高,提高燃气进口温度是提高燃气轮机热效率的重要途径。随着燃气进口温度的不断提高,单纯通过改善叶片的制备材料来提高叶片的承温能力已无法满足实际使用需求,因此,通过预置陶瓷型芯,生产具有气冷内通道的空心叶片便成为先进燃气轮机制造的关键技术。常用的陶瓷型芯主要有氧化硅基和氧化铝基两种。氧化硅基陶瓷型芯主要用于浇注温度较低的叶片,当使用温度超过1550℃时,普遍存在高温稳定性下降,易于蠕变变形等问题,严重影响叶片的生产合格率和成本。相比之下,氧化铝基陶瓷型芯的化学稳定性更好,使用温度高达1850℃,具有与氧化铝基陶瓷型壳相匹配的膨胀系数,更适于大尺寸定向叶片的生产。但氧化铝难与酸碱脱芯液发生反应,因此陶瓷型芯的脱出很困难,其脱出技术是制约氧化铝基陶瓷型芯使用的一大瓶颈。陶瓷型芯的脱出是通过脱芯液对型芯材料颗粒间连接处的腐蚀破坏来实现的。型芯脱芯性能主要与型芯的孔隙率有关,孔隙率越高,脱芯液越易于渗透进型芯内部与型芯材料发生反应,对脱芯过程越有利。但是孔隙率增大会直接导致型芯强度的降低,强度过低就会在压蜡模阶段或者在浇铸过程中金属液的冲击下断裂。因此,陶瓷型芯的制备成为制约空心叶片生产的一大瓶颈,新型陶瓷型芯制作方法的开发迫在眉睫。【专利102266906a】(一种易脱除陶瓷型芯的制备方法)在陶瓷型芯中添加了一定量的碳纳米管,通过纳米碳管烧结后形成的空间管道来增加脱芯反应速度,使陶瓷型芯快速脱除。但是碳纳米管分散性差,前处理工艺复杂,无法保证其在陶瓷型芯中均匀分布,进而无法保证制备陶瓷型芯的强度和成品合格率。【专利cn105598390a】(一种空心叶片陶瓷铸型及其脱芯方法)在陶瓷浆料中预设多根芯骨棒,芯骨棒由抗腐蚀芯部以及易腐蚀镀层组成,当易腐蚀镀层被腐蚀掉以后,抗腐蚀芯部与陶瓷型芯之间产生空隙,抗腐蚀芯部能够沿此空隙拔出,在陶瓷型芯中形成通孔,增加了陶瓷型芯与脱芯液的接触面积,以进行快速脱芯。所述方法使用的芯骨棒制作过程复杂、成本高,且需要预留孔位进行装配和拆卸,不适合大规模生产。3d打印技术可以在陶瓷型芯内部设计成中空或复杂三维拓扑结构,提高型芯内部空隙率,增大脱芯液与型芯内部的接触面积,脱芯过程中,型芯表层壳体融掉后,脱芯液通过空隙与型芯内部迅速接触,从而大幅降低脱芯时间,提高脱芯效率;陶瓷型芯内部空间点阵的结构类型和相对密度(指实体材料所占据的体积与单胞体积之比)的选择及与陶瓷浆料的特性,坯体成型后的脱脂烧结的技术配合,都是实现陶瓷型芯性能的关键;所谓空间点阵结构是从晶体结构中抽象出来的概念,用于描述结构中各个单元在空间分布周期性的特点,不同的空间点阵结构力学性能不同,对浆料的选择以及后期脱脂烧结的要求也不同;保证陶瓷型芯用材低耗,浇铸时具有稳定的强度,又快速提升脱芯时间,是3d陶瓷型芯打印领域极其有意义的研究。技术实现要素:为了解决上述技术问题,本发明提供一种空心叶片易脱除氧化铝陶瓷型芯及其制备方法,所述陶瓷型芯通过壳体和壳体内部的空间点阵结构相结合,实现陶瓷型芯高空隙率的同时,保证陶瓷型芯的抗冲击力;陶瓷浆料的特定组分,实现陶瓷型芯打印稳定,成品坚实耐高温又易脱芯的特性。所述陶瓷型芯抗冲击力强、脱芯时间短、节省陶瓷材料,缩短工艺流程,为氧化铝陶瓷型芯脱出难题提供了一种高效的解决方案。本发明的技术方案为:一种空心叶片易脱除氧化铝陶瓷型芯,由全封闭式壳体和在壳体内部、且生长在壳体上的空间点阵结构构成;所述空间点阵结构拓扑连接、相对密度为20%~50%;所述壳体的厚度为0.4-0.5mm。所述空间点阵结构为菱形十二面体点阵结构、十字点阵结构、y字点阵结构中的一种。所述壳体和空间点阵结构由陶瓷浆料制得,其特征在于,所述陶瓷浆料的制备方式如下:1)将35-45重量份氧化铝、150-170重量份无水乙醇、0.3-0.4重量份有机硅酸酯混合搅拌8-12h,然后过滤、干燥得到表面功能化的级配氧化铝陶瓷粉末;2)将8-12重量份二氧化硅、80-120重量份无水乙醇、0.1-0.3重量份有机硅酸酯混合搅拌8-12h,然后过滤、干燥得到表面功能化的级配二氧化硅陶瓷粉末;3)将80-120重量份的丙烯酸树脂、100-140重量份的丙烯酸丁酯、10-30重量份的苯甲酰甲酸甲酯和5-15重量份的聚二甲基硅氧烷混合制备出光固化树脂预混液;4)将所述级配氧化铝陶瓷粉末、级配二氧化硅陶瓷粉末和所述光固化树脂预混液进行混合搅拌,即得到陶瓷浆料。一种空心叶片易脱除氧化铝陶瓷型芯的制备方法,包括以下步骤:1)制备陶瓷浆料;2)在三维建模软件中创建陶瓷型芯模型,由全封闭式壳体和在壳体内部、且生长在壳体上的空间点阵结构构成;3)设置陶瓷型芯模型的壳体厚度和空间点阵结构相对密度,导出设定好的陶瓷型芯模型;4)将所述陶瓷型芯模型导入用于陶瓷浆料打印的激光3d打印设备中;5)设置激光3d打印设备的激光脉冲宽度、光束焦斑,对打印平台上的陶瓷浆料进行激光扫描,使陶瓷浆料发生聚合交联固化反应,逐层打印直至得到成型坯体;6)用清洗溶液对成型坯体进行清洗;7)将清洗后的坯体依次进行脱脂和烧结,得到陶瓷型芯。所述陶瓷浆料的制备方式如下:1)将35-45重量份氧化铝、150-170重量份无水乙醇、0.3-0.4重量份有机硅酸酯混合搅拌8-12h,然后过滤、干燥得到表面功能化的级配氧化铝陶瓷粉末;2)将8-12重量份二氧化硅、80-120重量份无水乙醇、0.1-0.3重量份有机硅酸酯混合搅拌8-12h,然后过滤、干燥得到表面功能化的级配二氧化硅陶瓷粉末;3)将80-120重量份的丙烯酸树脂、100-140重量份的丙烯酸丁酯、10-30重量份的苯甲酰甲酸甲酯和5-15重量份的聚二甲基硅氧烷混合制备出光固化树脂预混液;4)将所述级配氧化铝陶瓷粉末、级配二氧化硅陶瓷粉末和所述光固化树脂预混液进行混合搅拌,即得到陶瓷浆料。所述激光3d打印设备的激光脉冲宽度19~27ns、光束焦斑0.02~0.05mm;逐层打印时的打印层厚0.02~0.1mm。所述脱脂即在惰性气体保护下,将清洗后的成型胚体放入脱脂炉中,通入惰性气体,将温度调至500~600℃,达到最高温度时保温0.5-1.5h;保温后,将炉体冷却至室温。所述烧结过程即室温时,将脱脂后的成型胚体放入烧结炉中,以50~200℃/h的升温速率升到1250~1450℃,保温4~8h,然后将炉体冷却至200℃,得到陶瓷型芯。所述壳体的厚度为0.4-0.5mm;所述空间点阵结构相对密度为20%~50%。所述空间点阵结构为菱形十二面体点阵结构、十字点阵结构、y字点阵结构中的一种。本发明的技术效果为:本发明利用陶瓷浆料激光3d打印技术,制作内部为空间点阵结构的陶瓷型芯,在脱芯过程中,当型芯0.4-0.5mm厚的壳体被溶解后,所述脱芯液能够快速蔓延至型芯内部结构的各个孔隙中,增大脱芯液与型芯的接触面积,大大加快陶瓷型芯与脱芯液的反应速度,快速脱除型芯;所述陶瓷型芯空间点阵结构的相对密度仅为20%~50%,壳体仅为0.4-0.5mm厚,在大幅节省原材料且保证型芯抗冲击力的同时,脱芯时间缩短50%以上。空间点阵结构的类型有多种,而利用激光3d打印技术成型结构复杂的空间点阵结构,不同的空间点阵结构的高比强度和高比刚度不同,不仅能满足型芯力学性能要求,还能促进脱芯过程中型芯与脱芯液之间的热交换和化学反应,实现高强度陶瓷型芯快速脱除。本发明中菱形十二面体点阵结构、十字点阵结构、y字点阵结构的空间点阵结构在由所述陶瓷浆料打印成型并经过脱脂烧结后,得到的陶瓷型芯,除了能快速脱芯,同时能达到所需挠度,抗弯强度高,不易断裂。本发明制作的陶瓷型芯适用于内腔结构复杂的空心叶片制作;使用所述3d打印成型技术可制作的结构复杂、任意形状的陶瓷型芯;使用高流动性低粘度陶瓷浆料,可保证复杂空间点阵结构成型完整,进而保证陶瓷型芯的力学性能;在陶瓷浆料中引入二氧化硅,烧结过程中形成粘结相,可进一步提高抗冲击性能;所述陶瓷型芯强度高、脱芯时间短、节省陶瓷材料,缩短工艺流程,为氧化铝陶瓷型芯脱出难题提供了一种极为高效的解决方案。附图说明图1为本发明实施例剖视图。图2为菱形十二面体点阵结构中菱形十二面体结构示意图。图3为十字点阵结构中十字结构示意图。图4为y字点阵结构中y字结构示意图。其中,壳体1;空间点阵结构2。具体实施方式以下结合具体实施例对本发明作进一步说明。实施例1氧化铝陶瓷浆料采用3d打印成型技术制作的陶瓷型芯具体实施步骤如下:1)取氧化铝40g、无水乙醇200ml和有机硅酸酯0.4g混合搅拌10h。2)过滤、干燥制备出表面功能化的级配氧化铝陶瓷粉末。3)取二氧化硅10g、无水乙醇100ml和有机硅酸酯0.2g混合搅拌10h。4)过滤、干燥制备出表面功能化的级配二氧化硅陶瓷粉末。5)取平均分子量2500的丙烯酸树脂100ml、丙烯酸丁酯120ml、苯甲酰甲酸甲酯20ml和聚二甲基硅氧烷10ml混合制备出光固化树脂预混液。6)将级配氧化铝陶瓷粉末和光固化树脂预混液进行混合搅拌,得到光固化陶瓷浆料。7)在三维建模软件magics中创建陶瓷型芯模型实体。8)选择实体,外壳厚度设置为0.49mm,结构类型参数设置为相对密度30%的菱形十二面体点阵结构(所述结构每个结点的菱形十二面体结构如图2所示,由十二个全等菱形围成了球状结构),然后进行内部结构功能处理。9)点击生成内部结构后导出陶瓷型芯模型。10)将陶瓷型芯模型导入市购的陶瓷浆料激光3d打印设备中(如武汉因泰莱激光科技有限公司生产的专利号为201721184227.1的3d打印机中)。11)设置设备运行参数及加工工艺参数,并根据运行参数进行初始化。12)泵送系统对所述陶瓷浆料进行均匀混合和密封搅拌,并通过泵送系统将搅拌后的陶瓷浆料从储料盒中输送至打印平台。13)控制刮刀相对水平位置倾斜5°进行往返运动,对打印平台上的陶瓷浆料进行刮平,并使多余的陶瓷浆料流入循环回收系统的材料回收盒中。14)激光扫描系统根据设置的激光脉冲宽度20ns和光束焦斑0.04mm,对打印平台上的陶瓷浆料进行激光扫描,使陶瓷浆料发生聚合交联固化反应。15)打印平台升降机构根据设置的加工速度20mm/s、升降台提升速度1mm/s、打印层厚0.06mm和打印速度300层/h,控制打印平台下降。16)重复步骤10-13,直到完成所有分层切片的打印,得到成型坯体。17)打印平台升降机构控制打印平台上升至初始位置,取下成型坯体,并使用清洗溶液对成型坯体进行清洗。18)脱脂,将清洗后的成型胚体放入脱脂炉中,通入惰性气体,将温度调至550℃,达到最高温度时保温1小时左右。保温后,将炉体冷却至室温。整个过程一直在惰性气体的保护气氛,防止制品热氧化。脱脂的目的是:除去成型坯体中的高分子材料,定型胚体。19)烧结,将脱脂后的成型胚体放入高温烧结炉中烧结至1250℃,具体烧结步骤为:室温时,将脱脂后的成型胚体放入烧结炉中,以100℃/h的升温速率升到1250℃,保温4h,然后将炉体冷却至200℃,取出陶瓷型芯。本发明所述“级配氧化铝陶瓷粉末”、“级配二氧化硅陶瓷粉末”中的“级配”,指的颗粒级配,即小尺寸的颗粒填充到大尺寸颗粒的空隙中,本发明氧化铝陶瓷粉末和二氧化硅陶瓷粉末范围是0.1-10微米。所述丙烯酸树脂的分子量为1500-3000。实施例2氧化铝陶瓷浆料采用3d打印成型技术制作的陶瓷型芯具体实施步骤如下:1)取氧化铝35g、无水乙醇200ml和有机硅酸酯0.3g混合搅拌10h。2)过滤、干燥制备出表面功能化的级配氧化铝陶瓷粉末。3)取二氧化硅8g、无水乙醇120ml和有机硅酸酯0.2g混合搅拌10h。4)过滤、干燥制备出表面功能化的级配二氧化硅陶瓷粉末。5)取平均分子量2000的丙烯酸树脂100ml、丙烯酸丁酯120ml、苯甲酰甲酸甲酯20ml和聚二甲基硅氧烷10ml混合制备出光固化树脂预混液。6)将级配氧化铝陶瓷粉末和光固化树脂预混液进行混合搅拌,得到光固化陶瓷浆料。7)在三维建模软件magics中创建陶瓷型芯模型实体。8)选择实体,外壳厚度设置为0.40mm,结构类型参数设置为相对密度35%的十字点阵结构(所述结构每个结点的十字结构如图3所示,相互垂直的x面和y面上的十字形构成),然后进行内部结构功能处理。9)点击生成内部结构后导出陶瓷型芯模型。10)将陶瓷型芯模型导入市购的陶瓷浆料激光3d打印设备中(如武汉因泰莱激光科技有限公司生产的专利号为201721184227.1的3d打印机中)。11)设置设备运行参数及加工工艺参数,并根据运行参数进行初始化。12)泵送系统对所述陶瓷浆料进行均匀混合和密封搅拌,并通过泵送系统将搅拌后的陶瓷浆料从储料盒中输送至打印平台。13)控制刮刀相对水平位置倾斜5°进行往返运动,对打印平台上的陶瓷浆料进行刮平,并使多余的陶瓷浆料流入循环回收系统的材料回收盒中。14)激光扫描系统根据设置的激光脉冲宽度20ns和光束焦斑0.03mm,对打印平台上的陶瓷浆料进行激光扫描,使陶瓷浆料发生聚合交联固化反应。15)打印平台升降机构根据设置的加工速度30mm/s、升降台提升速度1.5mm/s、打印层厚0.05mm和打印速度200层/h,控制打印平台下降。16)重复步骤10-13,直到完成所有分层切片的打印,得到成型坯体。17)打印平台升降机构控制打印平台上升至初始位置,取下成型坯体,并使用清洗溶液对成型坯体进行清洗。18)脱脂,将清洗后的成型胚体放入脱脂炉中,通入惰性气体,将温度调至600℃,达到最高温度时保温1小时左右。保温后,将炉体冷却至室温。整个过程一直在惰性气体的保护气氛,防止制品热氧化。脱脂的目的是:除去成型坯体中的高分子材料,定型胚体。19)烧结,将脱脂后的成型胚体放入高温烧结炉中烧结至1450℃,具体烧结步骤为:室温时,将脱脂后的成型胚体放入烧结炉中,以100℃/h的升温速率升到1350℃,保温4h,然后将炉体冷却至200℃,取出陶瓷型芯。实施例3氧化铝陶瓷浆料采用3d打印成型技术制作的陶瓷型芯具体实施步骤如下:1)取氧化铝45g、无水乙醇220ml和有机硅酸酯0.3g混合搅拌10h。2)过滤、干燥制备出表面功能化的级配氧化铝陶瓷粉末。3)取二氧化硅12g、无水乙醇120ml和有机硅酸酯0.3g混合搅拌10h。4)过滤、干燥制备出表面功能化的级配二氧化硅陶瓷粉末。5)取平均分子量2500的丙烯酸树脂110ml、丙烯酸丁酯135ml、苯甲酰甲酸甲酯25ml和聚二甲基硅氧烷12ml混合制备出光固化树脂预混液。6)将级配氧化铝陶瓷粉末和光固化树脂预混液进行混合搅拌,得到光固化陶瓷浆料。7)在三维建模软件magics中创建陶瓷型芯模型实体。8)选择实体,外壳厚度设置为0.45mm,结构类型参数设置为相对密度25%的y字点阵结构(所述结构每个结点的y字结构如图4所示,相互垂直的x面和y面上分别为一字型和x形),然后进行内部结构功能处理。9)点击生成内部结构后导出陶瓷型芯模型。10)将陶瓷型芯模型导入市购的陶瓷浆料激光3d打印设备中(如武汉因泰莱激光科技有限公司生产的专利号为201721184227.1的3d打印机中)。11)设置设备运行参数及加工工艺参数,并根据运行参数进行初始化。12)泵送系统对所述陶瓷浆料进行均匀混合和密封搅拌,并通过泵送系统将搅拌后的陶瓷浆料从储料盒中输送至打印平台。13)控制刮刀相对水平位置倾斜10°进行往返运动,对打印平台上的陶瓷浆料进行刮平,并使多余的陶瓷浆料流入循环回收系统的材料回收盒中。14)激光扫描系统根据设置的激光脉冲宽度25ns和光束焦斑0.03mm,对打印平台上的陶瓷浆料进行激光扫描,使陶瓷浆料发生聚合交联固化反应。15)打印平台升降机构根据设置的加工速度20mm/s、升降台提升速度3mm/s、打印层厚0.1mm和打印速度500层/h,控制打印平台下降。16)重复步骤10-13,直到完成所有分层切片的打印,得到成型坯体。17)打印平台升降机构控制打印平台上升至初始位置,取下成型坯体,并使用清洗溶液对成型坯体进行清洗。18)脱脂,将清洗后的成型胚体放入脱脂炉中,通入惰性气体,将温度调至600℃,达到最高温度时保温1小时左右。保温后,将炉体冷却至室温。整个过程一直在惰性气体的保护气氛,防止制品热氧化。脱脂的目的是:除去成型坯体中的高分子材料,定型胚体。19)烧结,将脱脂后的成型胚体放入高温烧结炉中烧结至1450℃,具体烧结步骤为:室温时,将脱脂后的成型胚体放入烧结炉中,以200℃/h的升温速率升到1450℃,保温8h,然后将炉体冷却至200℃,取出陶瓷型芯。结果检测将上述实施例制作的陶瓷型芯进行以下结果检测。1、抗冲击力测试,使用高温挠度和高温抗弯强度表征。2、脱芯测试。检测结果如下:表1实施例陶瓷型芯高温挠度和高温抗弯强度测试结果从表1中可以看出,实施例得到的陶瓷型芯不仅可以满足一定的高温挠度范围,其高温抗弯强度也完全满足实际工业所需,而达到上述性能的陶瓷型芯相对传统陶瓷型芯节约了大量原料。表2实施例陶瓷型芯和传统陶瓷型芯进行脱芯测试结果项目名称脱芯液脱芯效果脱芯时间实施例1koh完全脱除1.8h实施例2koh完全脱除2.1h实施例3koh完全脱除1.6h传统陶瓷型芯koh完全脱除3.9h从表2可以看出,所述实施例陶瓷型芯的脱芯速度相对传统陶瓷型芯提升了一倍以上,降低工艺时间,大幅提升生产效率。当然,以上仅是本发明的具体应用范围,这些实施例仅用于说明本发明而不用于限制本发明的范围。此外应理解,在阅读了本发明讲授的内容之后,本领域技术人员可以对本发明作各种改动或修改,这些等价形式同样落于本申请所附权利要求书所限定的范围。当前第1页1 2 3