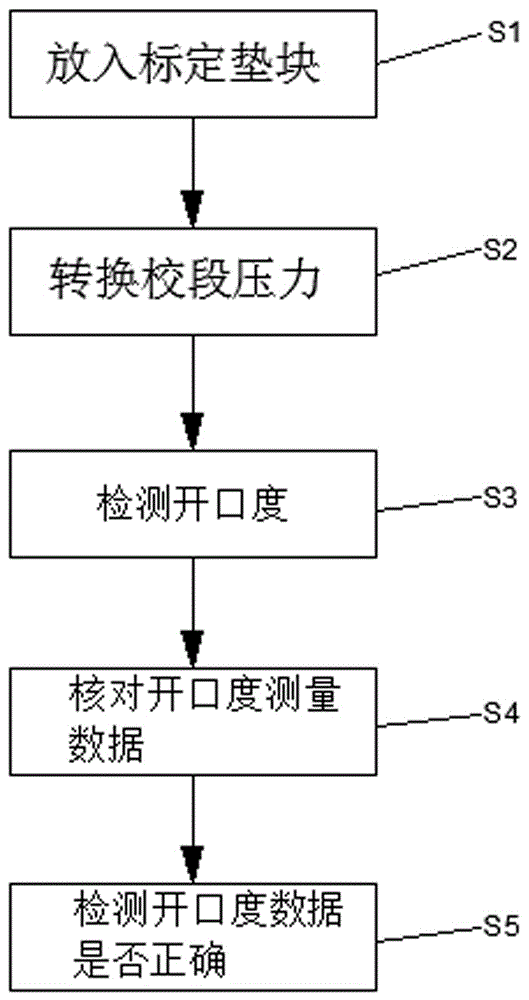
本发明涉及一种轻压下技术领域,更具体地说,它涉及一种板坯连铸扇形段开口度快速标定方法。
背景技术:
轻压下技术始于20世纪70年代末、80年代初,是在70年代收缩辊缝技术的基础上发展而来的,也是近年来推广较快的连铸技术之一。对板坯连铸机来讲,轻压下技术是指凝固末端的轻压下,消除板坯铸坯的中心偏析和中心琉松,提高内部质量。所以说连铸扇形段开口度标定是连铸生产操作中的一个重要环节,随着连铸技术不停的更新和优化,钢铁产品的品种、质量越来越受到用户的关注,提高钢铁产品的质量以及增加生产高附加值的产品比例是每个钢铁生产者追求的目标,扇形段开口度标定更为重要,
采用传统方法标定扇形段时每次需4名职工使用手持辊缝仪反复测量并多次调整,才能将扇形段辊缝值误差控制在0.5mm内,耗时长,效率低。传统扇形段开口度标定方式不仅劳动强度大、工作效率低,而且标定精度不稳定,造成铸坯中间裂纹及三角区裂纹等质量问题频繁发生,铸坯质量波动大,不能适应当前高效高质的连铸机生产要求。
经大量研究表明:扇形段开口度精度,直接影响轻压下的效果,扇形段开口度存在间隙,造成辊缝偏差大,从而无法达到消除板坯铸坯的中心偏析和中心疏松的目的。
技术实现要素:
针对现有技术存在的不足,本发明的目的在于提供一种板坯连铸扇形段开口度快速标定方法,消除了板坯铸坯的中心偏析和中心琉松,进而提高内部质量;具有操作简便、安全可靠、实用高效的特点,降低了工人的劳动强度,提高了板坯铸坯质量。
本发明的上述技术目的是通过以下技术方案得以实现的:一种板坯连铸扇形段开口度快速标定方法,其标定步骤包括:
s1:启动扇形段液压,将扇形段开口度抬至最大,在扇形段上框架和扇形段下框架的出入口框架两端放入标定垫块;
s2:转换校段压力,使用强压把扇形段开口度压到垫块位置;
s3:测量扇形段上口及下口上下两辊扇形段开口度;
s4:核对扇形段开口度测量数据,确认测量数据无误后输入扇形段校准画面进行扇形段开口度校定操作;
s5:校准后马上抬起扇形段,再压下扇形段,检测扇形段开口度校准数据是否正确,如偏差大于0.50mm再用千分尺测量标定。
在其中一个实施例中,在所述步骤s1中用4个支撑垫块卡在扇形段上框架和扇形段下框架的出入口两根辊子两端,距辊边90-110mm。
在其中一个实施例中,在所述步骤s2中调整扇形段液压缸系统压力为校段压力,使用强压压力把扇形段上框架下压紧垫块,使其产生作用力和反作用力,从而消除铰接点间隙,辊子轴承间隙和铰接点扭曲变形间隙。
在其中一个实施例中,在所述步骤s3中用千分尺分别测出扇形段上口及下口上下两辊辊缝值,最后把测量数据输入扇形段开口度标定画面对位移传感器的开口度进行标定,确保辊缝精度≤0.30mm。
在其中一个实施例中,在所述步骤s5中先选择软压下位置控制,将扇形段开口度抬高20mm后,再使用校段压力强压压下,此时看扇形段位置显示就是刚扇形段开口度校定的数据,如数据偏差大,需重新按照以上步骤进行校准。
上述一种板坯连铸扇形段开口度快速标定方法,具有以下有益效果:
(1)提高扇形段标定效率,扇形段开口度标定由原来6小时降至0.5小时,降低了工人的劳动强度;
(2)强化扇形段开口度的检测确认,避免了扇形段标定错误,杜绝各类事故的发生;
(3)提高扇形段开口度精度进而明显改善铸坯低倍质量,减小中心偏析和中心疏松,低倍样合格率从80%提高90%以上。
附图说明
图1为本发明工作步骤图。
具体实施方式
下面结合附图和实施例,对本发明进行详细描述。
参见图1,一种板坯连铸扇形段开口度快速标定方法,其标定步骤包括:
s1:启动扇形段液压,将扇形段开口度抬至最大,在扇形段上框架和扇形段下框架的出入口框架两端放入标定垫块;
s2:转换校段压力,使用强压把扇形段开口度压到垫块位置;
s3:检测扇形段上口及下口上下两辊扇形段开口度,如偏差大于0.50mm再用千分尺测量;
s4:核对扇形段开口度测量数据,确认测量数据无误后输入扇形段校准画面进行扇形段开口度校定操作;
s5:校准后马上检测扇形段开口度校准数据是否正确。
在其中一个实施例中,在所述步骤s1中用4个支撑垫块卡在扇形段上框架和扇形段下框架的出入口两根辊子两端,距辊边90-110mm。
在其中一个实施例中,在所述步骤s2中调整扇形段液压缸系统压力为校段压力,使用强压压力把扇形段上框架下压紧垫块,使其产生作用力和反作用力,从而消除铰接点间隙,辊子轴承间隙和铰接点扭曲变形间隙。
在其中一个实施例中,在所述步骤s3中用千分尺分别测出扇形段上口及下口上下两辊辊缝值,最后把测量数据输入扇形段开口度标定画面对位移传感器的开口度进行标定,确保辊缝精度≤0.30mm。
在其中一个实施例中,在所述步骤s5中先选择软压下位置控制,将扇形段开口度抬高20mm后,再使用校段压力强压压下,此时看扇形段位置显示就是刚扇形段开口度校定的数据,如数据偏差大,需重新按照以上步骤进行校准。
实施例(一)以生产断面厚度270mm为例
1、启动扇形段液压,将扇形段开口度抬至290mm,在扇形段上框架和扇形段下框架的出入口两根辊子两端加标定垫块。
2、在扇形段画面切换扇形段校段压力,同时使用强压把扇形段压到最低位。
3、用千分尺分别测出扇形段第一排及最后一排上下两辊子扇形段开口度。
4、核对扇形段开口度测量数据,确认测量数据无误后输入扇形段校准画面进行扇形段开口度校准操作。
5、校准后,选择软压下位置控制,把扇形段开口度抬到270mm后,再使用校段强压压下,检测校准数据是否正确,此时看扇形段位置显示就是刚扇形段开口度校定的数据,如数据偏差大,需重新校准。
实施例(二)以生产断面厚度200mm为例
1、启动扇形段液压,将扇形段开口度抬至230mm,在扇形段上框架和扇形段下框架的出入口两根辊子两端加标定垫块。
2、等钳工放好标定垫块确认后,主控在扇形段画面切换扇形段校段压力,同时使用强压把扇形段压到最低位。
3、用千分尺分别测出扇形段第一排及最后一排上下两辊子扇形段开口度。
4、核对扇形段开口度测量数据,确认测量数据无误后输入扇形段校准画面进行扇形段开口度校准。
5、校准后,选择软压下位置控制,把扇形段开口度抬到20mm后,再使用校段强压压下,检测校准数据是否正确,此时看扇形段位置显示就是刚扇形段开口度校定的数据,如数据偏差大,需重新校准。
实施例(三)以生产断面厚度220mm为例
1、启动扇形段液压,将扇形段开口度抬至250mm,在扇形段上框架和扇形段下框架的出入口两根辊子两端加标定垫块。
2、等钳工放好垫块确认后,主控在扇形段画面切换扇形段校段压力,同时使用强压把扇形段压到最低位。
3、用千分尺分别测出扇形段第一排及最后一排上下两辊子扇形段开口度。
4、核对扇形段开口度测量数据,确认测量数据无误后输入扇形段校准画面进行扇形段开口度校准。
5、校准后,选择软压下位置控制,把扇形段开口度抬到20mm后,再使用校段强压压下,检测校准数据是否正确,此时看扇形段位置显示就是刚扇形段开口度校定的数据,如数据偏差大,需重新校准。
以上所述实施例仅表达了本发明的几种实施方式,其描述较为具体和详细,但并不能因此而理解为对本发明专利范围的限制。应当指出的是,对于本领域的普通技术人员来说,在不脱离本发明构思的前提下,还可以做出若干变形和改进,这些都属于本发明的保护范围。因此,本发明专利的保护范围应以所附权利要求为准。