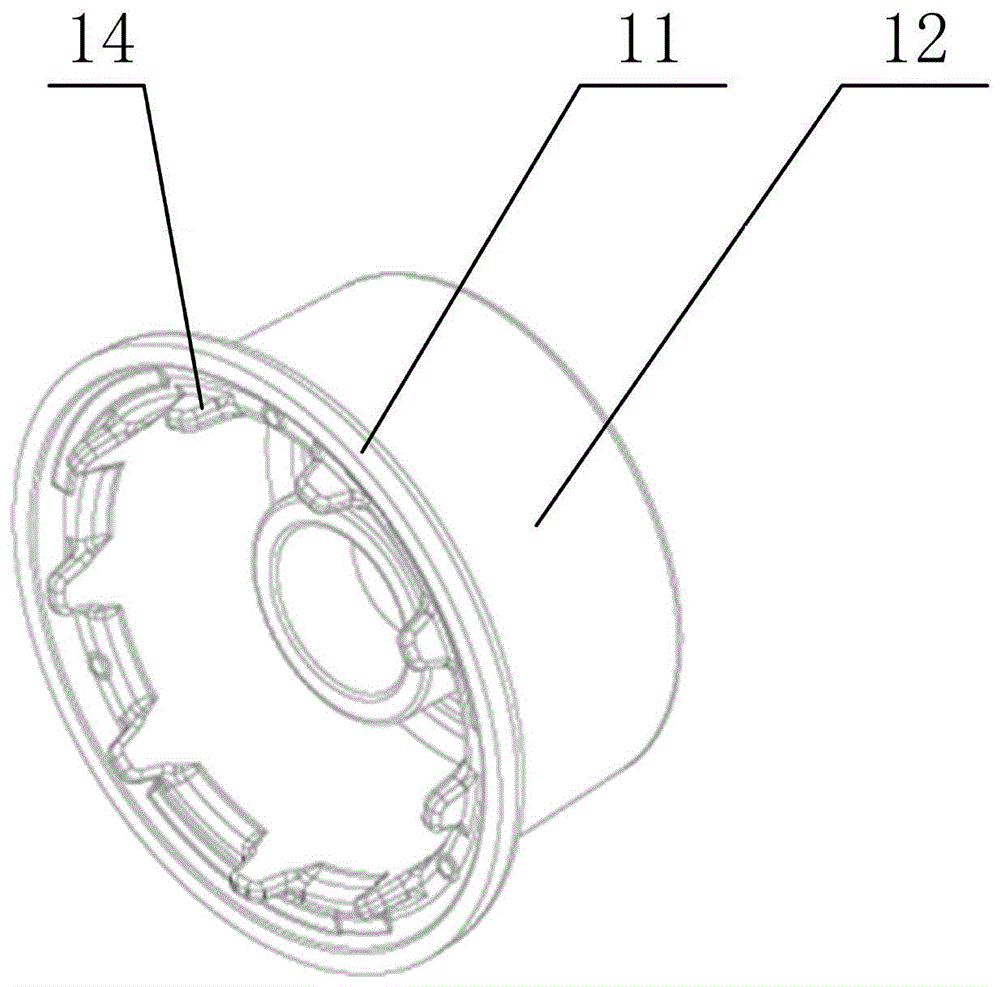
本发明涉及航空精密轮毂模锻件制造
技术领域:
,尤其涉及一种2014铝合金航空精密轮毂模锻件的无锆毛坯。
背景技术:
:大型飞机上具有一个典型规格锻件,为高强2014铝合金航空精密轮毂模锻件中的最大模锻件:半轮(舱内侧)模锻件。该半轮(舱内侧)模锻件为精密模锻件,为圆盘类模锻件,零件最大外轮毂尺寸φ593.3×309.1mmmm,模锻件最大外轮廓尺寸为φ616.5×314.2mm。半轮舱内侧零件如图1和图2所示,图1为本发明实施例提供的2014铝合金航空精密轮毂模锻件的第一侧视结构示意图;图2为本发明实施例提供的2014铝合金航空精密轮毂模锻件的第二侧视结构示意图,是一个比较复杂的大型铝合金锻件,该锻件的最大外形尺寸为φ600mm×310mm,筒形最大深度为240mm,筒壁最小处仅为7.6mm,筒壁最厚处为16mm,是一个典型的深筒薄壁件,其基本体为筒体12,筒体12的上部具有环形的外延部11,外延部11的上方具有内凹部,内凹部与筒体12的内壁交接处具有呈环形排列的9个凸耳14,筒体12的底部具有呈环形的9个椭圆形凹坑13,具体的,该零件在筒形底部较薄,同时存在9个均匀分布的椭圆形凹坑13,形状复杂;对应在零件上侧存在9个凸耳14,该凸耳14高度较高、壁厚薄、斜度小,竖直方向投影面积较小,属于较难成型及易出现缺陷部分。半轮(舱内侧)模锻件本身为精密模锻件,为圆盘类模锻件,型腔深、壁薄、高筋、圆角小、内腔和底部的凸台多、型腔较复杂。半轮(舱内侧)模锻件为有大量非加工面、机加工余量小,表面质量要求高,尺寸精度要求极高;模锻件型腔深,筋高且薄,精密模锻成型难;2014合金容易产生粗晶,组织性能均匀性控制难;轮毂安全性能要求高,综合性能要求极高。因此,轮毂模锻件最大的难点为尺寸控制难度大、组织性能均匀性控制难度大。因此,如何提供一种2014铝合金航空精密轮毂模锻件的无锆毛坯,以提高产品质量,是目前本领域技术人员亟待解决的技术问题。技术实现要素:有鉴于此,本发明的目的在于提供一种2014铝合金航空精密轮毂模锻件的无锆毛坯,以提高产品质量。为了达到上述目的,本发明提供如下技术方案:一种2014铝合金航空精密轮毂模锻件的无锆毛坯,包含0.65%-0.75%si,fe≤0.10%,4.00%-4.40%cu,0.70%-0.90%mn,0.45%-0.55%mg,0.04%-0.07%cr,zn≤0.20%,ti≤0.15%。优选的,上述si为0.70%。优选的,上述fe为0.08%。优选的,上述cu为4.10%。优选的,上述mn为0.80%。优选的,上述mg为0.50%。优选的,上述cr为0.06%。优选的,上述zn为0.04%。优选的,上述ti为0.02%。优选的,上述si为0.72%,所述fe为0.08%,所述cu为4.16%,所述mn为0.80%,所述mg为0.54%,所述cr为0.06%,所述zn为0.04%,所述ti为0.03%。本发明提供的2014铝合金航空精密轮毂模锻件的无锆毛坯,包含0.65%-0.75%si,fe≤0.10%,4.00%-4.40%cu,0.70%-0.90%mn,0.45%-0.55%mg,0.04%-0.07%cr,zn≤0.20%,ti≤0.15%。其性能较好,无论是模锻平行晶粒方向以及垂直晶粒方向的屈服强度、抗拉强度和断后伸长率,还是自由锻的屈服强度、抗拉强度和断后伸长率,或者轧环切向以及轴向的屈服强度、抗拉强度和断后伸长率,均高于现有技术中的ams4133e标准,并且疲劳寿命测试的成绩优异,使用本发明提供的2014铝合金航空精密轮毂模锻件的无锆毛坯,能够极大的提高2014铝合金航空精密轮毂模锻件的产品质量。附图说明为了更清楚地说明本发明实施例或现有技术中的技术方案,下面将对实施例或现有技术描述中所需要使用的附图作简单地介绍,显而易见地,下面描述中的附图是本发明的一些实施例,对于本领域普通技术人员来讲,在不付出创造性劳动的前提下,还可以根据这些附图获得其他的附图。图1为本发明实施例提供的2014铝合金航空精密轮毂模锻件的第一侧视结构示意图;图2为本发明实施例提供的2014铝合金航空精密轮毂模锻件的第二侧视结构示意图;图3为4#合金的宏观偏析数据的示意图;图4为1#合金(标准中间值)的铸态组织的示意图;图5为为5#合金(低cumgsi)的铸态组织的示意图;图6为为铸锭的三级均匀化制度的示意图;图7为1#合金均匀化组织中的粗大相示意图;图8为5#合金均匀化组织中的粗大相示意图;图9为1#(标准中间值)的弥散相扫描示意图;图10为2#(低fe+zr)的弥散相扫描示意图;图11为3#(低femn)的弥散相扫描示意图;图12为5种合金的挤压工艺路线示意图;图13为固溶时效工艺示意图;图14为取样位置示意图;图15为高周疲劳试样的结构示意图。上图1-15中:外延部11、筒体12、椭圆形凹坑13、凸耳14。具体实施方式为使本发明实施例的目的、技术方案和优点更加清楚,下面将结合本发明实施例中的附图,对本发明实施例中的技术方案进行清楚、完整地描述,显然,所描述的实施例是本发明一部分实施例,而不是全部的实施例。基于本发明中的实施例,本领域普通技术人员在没有做出创造性劳动前提下所获得的所有其他实施例,都属于本发明保护的范围。请参考图1-图15,图1为本发明实施例提供的2014铝合金航空精密轮毂模锻件的第一侧视结构示意图;图2为本发明实施例提供的2014铝合金航空精密轮毂模锻件的第二侧视结构示意图;图3为4#合金的宏观偏析数据的示意图;图4为1#合金(标准中间值)的铸态组织的示意图;图5为为5#合金(低cumgsi)的铸态组织的示意图;图6为为铸锭的三级均匀化制度的示意图;图7为1#合金均匀化组织中的粗大相示意图;图8为5#合金均匀化组织中的粗大相示意图;图9为1#(标准中间值)的弥散相扫描示意图;图10为2#(低fe+zr)的弥散相扫描示意图;图11为3#(低femn)的弥散相扫描示意图;图12为5种合金的挤压工艺路线示意图;图13为固溶时效工艺示意图;图14为取样位置示意图;图15为高周疲劳试样的结构示意图。本发明实施例提供的2014铝合金航空精密轮毂模锻件的无锆毛坯,包含0.65%-0.75%si,fe≤0.10%,4.00%-4.40%cu,0.70%-0.90%mn,0.45%-0.55%mg,0.04%-0.07%cr,zn≤0.20%,ti≤0.15%。其性能较好,无论是模锻平行晶粒方向以及垂直晶粒方向的屈服强度、抗拉强度和断后伸长率,还是自由锻的屈服强度、抗拉强度和断后伸长率,或者轧环切向以及轴向的屈服强度、抗拉强度和断后伸长率,均高于现有技术中的ams4133e标准,并且疲劳寿命测试的成绩优异,使用本发明实施例提供的2014铝合金航空精密轮毂模锻件的无锆毛坯,能够极大的提高2014铝合金航空精密轮毂模锻件的产品质量。具体的,si为0.70%。fe为0.08%。cu为4.10%。mn为0.80%。mg为0.50%。cr为0.06%。zn为0.04%。ti为0.02%。或者,si为0.72%,fe为0.08%,cu为4.16%,mn为0.80%,mg为0.54%,cr为0.06%,zn为0.04%,ti为0.03%。本发明实施例提供的2014铝合金航空精密轮毂模锻件的无锆毛坯,其合金成分设计如下:在ams4133标准成分范围内,按照cu、mg、si、mn、fe、zr在合金中的不同作用,设计了5种2014合金,见表1,表1为五种2014合金的化学成分。成分设计原则:1#合金取2014标准成分的中间值;2#合金降低了fe含量、增加zr元素,研究zr元素的作用;3#合金同时降低fe、mn元素,研究mn元素的作用;4#合金同时增加cu、mg、si含量;5#合金同时降低cu、mg、si含量,对比分析cu、mg、si的作用。对以上5种成分进行熔铸,1#成分2个铸锭,其余成分各1个铸锭,铸锭尺寸φ178×550(37kg)。图3是4#合金的宏观偏析数据的示意图。铸锭半径方向上,距离铸锭心部3/4r处cu、mg元素含量高于其他部位,但没有超出设计成分。表1五种2014合金的化学成分图4所示为1#合金(标准中间值)的铸态组织的示意图;图5所示为5#合金(低cumgsi)的铸态组织的示意图。对5种合金的铸态组织分析表明,①1#、2#、3#、4#、5#合金都含有al2cu、al(femnsi)、al(cumgsi)、mg2si四种粗大相。②2#(低fe+zr)添加zr后,共晶组织明显减少,而块状al2cu相增多。③eds显示,2#(低fe+zr)合金的大部分检测点都含有较高的zr含量,其含量高于1#(标准中间值),认为zr在铸态中主要固溶于铝基体。均热制度确定:在距离圆心3/4r处,取1#标准中间值、4#高cumgsi、5#低cumgsi的铸态组织,进行dsc测试。首先,第一级均匀化采用(55℃/h升温)450℃×5h。第二级均匀化工艺通过dsc初步确定为:500℃,暂定24h。第三级均匀化工艺初步确定为:506℃,暂定18h。根据以上均匀化工艺,对5种合金铸锭进行均匀化,如图6所示,图6为铸锭的三级均匀化制度的示意图。对上述均匀化后的铸锭进行dsc检测,得到以下结论:(1)1#、2#、3#、4#合金铸锭先经过500℃×24h均匀化,再经过506℃×18.5h均匀化后,峰面积没有明显减小,表明第三级均匀化效果不大。因此,需要通过提高第二级均匀化温度,使可溶相在第二级均匀化时尽量回溶。(2)5#合金铸锭500℃×24h+506℃×18.5h均化后,绝大部分al2cu相回溶;残余相回溶吸热峰的起始点推移到520℃,而其峰值527℃接近q相熔点。因此,均匀化制度基本满足5#合金。图7为1#合金均匀化组织中的粗大相。图8为5#合金均匀化组织中的粗大相。5种合金均匀化后,al2cu相都没有完全回溶,未回溶的al2cu和难溶的al(femnsi)依然保留在晶界。尽管5#合金的dsc显示al2cu峰已经消除,但在组织中还残留部分小块al2cu(尺寸约5微米)。分别对1#(标准中间值)、2#(低fe+zr)、3#(低femn)合金进行第一级均匀化析出弥散相的种类、数密度分析。表2为弥散相分析实验方案。表2弥散相分析实验方案选取合金状态目的1#(标准中间值)450℃/5h+505℃/24h水淬分析弥散相种类、数密度2#(低fe+zr)450℃/5h+505℃/24h水淬分析弥散相种类、数密度3#(低femn)450℃/5h+505℃/24h水淬分析弥散相种类、数密度请参考图9、图10和图11,依次是1#(标准中间值)、2#(低fe+zr)、3#(低femn)的弥散相扫描照片。根据上述的弥散相扫描照片,对1#、2#、3#合金中的弥散相进行了种类辨别、数密度计算,结果列于表3。表3为1#、2#、3#实验室均匀化析出弥散相分析结果。表3为1#、2#、3#实验室均匀化析出弥散相分析结果。表31#、2#、3#实验室均匀化析出弥散相分析结果分析均匀化析出弥散相,获得如下结论:(1)1#和3#合金中析出的含mn弥散相种类相同,均为al(mn2si)、al(mn)。2#合金中很少观察到单独存在的al-zr弥散相,原因是第一级均匀化450/5h不是al3zr最佳析出温度。(2)2#合金从室温升至450℃过程中,zr可能首先析出;在450℃保温阶段,al3zr可能成为含al-mn相析出的形核点,使得al-mn相析出相密度偏大、尺寸偏小。(3)3#中mn含量较低,al(mn2si)、al(mn)弥散相数密度明显低于1#、2#,且尺寸偏大。进行试验验证:采用挤压变形能够较好的比较合金性能。对5种合金进行热挤压,选择现有模具(截面尺寸25mm×125mm),确保挤出板带的尺寸能够满足拉伸、疲劳性能测试。挤压工艺路线如图12所示,最后挤压后头段切除0.4m,尾段切除1m,剩余约2m可用。按照ams2772标准推荐制度,采用固溶温度502℃×保温3.5h;时效工艺177℃×8h。切取400mm长的挤压板料,进行固溶时效,其中固溶处理的时效处理为随炉升温。固溶时效工艺如图13所示,取样位置如图14所示。选择挤压板带l-s面进行ebsd组织分析,并与挤压态ebsd对比,分析固溶热处理对组织的影响。5种合金均显示拉长的带状组织,而且再结晶程度均不明显,但有细微差别。详细说明如下:1#、3#、4#合金在3h固溶+时效后,挤压态中的细小再结晶晶粒在3h固溶后没有明显长大。2#、5#合金在5h固溶+时效后,细小再结晶发生轻微长大。综合考虑,5h固溶+时效的强度更高、塑性更好;但固溶时间的增长会导致再结晶份数增加,可能对疲劳寿命不利。表4列出了ebsd再结晶模块统计的5种合金的固溶时效态的再结晶分数。试样的ls面的ebsd照片所含晶粒数量较少,ts面的ebsd照片所含晶粒较多;因此,ts面的再结晶分数统计比较准确。表4为5种合金t6态的再结晶分数。表45种合金t6态的再结晶分数对5种合金的残余相进行分析:以1#合金为例,通过衬度差别区分了不同的相种类:亮白色为al2cu,浅灰色为al(femnsi),深灰色为al(cumgsi)。表5列出了三种残余相的统计数据。表5为所有残余相含量比较。表5所有残余相含量比较(1)首先分析al2cu:1#(4.49cu)、3#(4.48cu)中cu含量中等、5#(4.2cu)合金中cu含量偏低,这与合金中al2cu面积百分数规律一致。2#(4.3cu)中cu含量偏低,但残余al2cu含量偏高。在2#合金的铸态组织中,共晶组织较少,而块状的al2cu较多。由此推测,2#合金中加入了zr,引起al2cu形貌更趋于块状;在后续的均匀化中,块状al2cu的回溶慢于共晶组织,因此在最终的t6态中保留了较多的al2cu相。4#(4,75cu)中cu含量最高,均匀化态dsc和上述相统计都表明al2cu相含量也较高。(2)其次分析al(femnsi):al(femnsi)相含量首先由mn含量决定,如3#(0.12fe、0.62mn)中al(femnsi)相含量最少。al(femnsi)相含量其次由fe含量决定,如1#(0.19fe、0.8mn)、2#(0.15fe、0.8mn)、5#(0.09fe、0.8mn)四者mn含量相同,al(femnsi)含量与fe含量基本成正相关。4#(0.09fe、0.77mn)中femn含量比5#(0.09fe、0.8mn)更低,其al(femnsi)相含量相应的低于5#。(3)最后分析al(cumgsi):由于al(cumgsi)相在sem照片中衬度不明显,统计数据可信度相比于al2cu和al(femnsi)低,但5种合金之间仍然可以互相比较。4#(4.75cu、0.8mg)中cumg含量最高,相应的al(cumgsi)相残余最多。5#(4.2cu、0.68mg)中cumg含量最低,没有发现al(cumgsi)相。可以认为,cu、mg含量与al(cumgsi)相的含量基本成正相关。(4)所有残余相分析:5种合金的残余相面积百分数,分析获得如下结论:通过降低cu含量降低al2cu残余相含量;通过降低fe、mn含量降低al(femnsi)残余相含量;通过降低cu、mg含量降低al(cumgsi)残余相含量。表6为挤压材t6态(3h固溶+时效)室温拉伸性能数据。表7分别为挤压材t6态(5h固溶+时效)室温拉伸性能数据。其中,△σ0.2(l-t)、△σb(l-t)、△δ(l-t)分别是挤压方向和横向的屈服强度之差、抗拉强度之差、断后伸长率之差。表8为时效时间3h和5h固溶对性能的影响。表6t6(502℃×3h+177℃×8h)态室温拉伸性能表7t6(502℃×5h+177℃×8h)态室温拉伸性能表8时效时间3h和5h固溶对性能的影响通过室温拉伸性能分析,得到如下结论:(1)5种合金t6态性能均高于ams4133e标准。5h固溶比3h固溶提高强度5-20mpa,提高延伸率1-4.5%,原因可能是较长时间固溶使残余al2cu相的回溶程度增大,时效强化增强。(2)3#合金mn含量较低,抑制再结晶作用减弱,固溶处理使得立方织构增强,导致挤压方向的强度相对于其他合金偏弱,挤压方向和横向的性能差较小。对挤压板带进行高周疲劳寿命测试,取应力水平300mpa、应力比-1、频率50hz。每种合金l向和t向各3个平行试样,为无缺口光滑试样,本实验采用的高周疲劳试样尺寸如图15所示。表9为5种合金t6态(502℃×5h+177℃×8h)疲劳性能。表95种合金t6态(502℃×5h+177℃×8h)疲劳性能挤压方向(l向)的疲劳寿命(60-130万次)普遍高于横向(t向)疲劳寿命(10-90万次)。5#(低cumgsi)合金在挤压方向寿命最高,但在横向寿命最低。4#(高cumg)合金在挤压方向和横向的寿命差异最小。对疲劳断口进行分析,5种合金的裂纹扩展区相差不大,萌生区差别很大。因此对裂纹源重点观察:(1)断口宏观形貌(2)裂纹启裂位置(3)起裂位置的相成分。2#l-2试样(76万周次)的疲劳断口:观察到mg、o富集区域,没有发现其他粗大相。2#t-1试样(53万周次)的疲劳断口:观察到mg、o富集区域,没有发现其他粗大相。对于2#t-1试样,裂纹很明显萌生于粗大相颗粒。成份面扫显示,粗大相富mg、o,且含有si,而其他元素分布均匀。在粗大相周围,存在富cu粗大相。2#l-2试样(99万周次)的疲劳断口,裂纹源处有mg、o元素富集;同时有少量的fe、mn、si富集点。疲劳寿命分析比较复杂,涉及到粗大相的种类、数量、尺寸、分布、再结晶、基体的力学性能。另外,疲劳数据分散,对分析也带来难度。根据实验数据,对5种合金的疲劳寿命分析如下:疲劳裂纹的萌生:根据2#(含zr)和5#(低cumg)合金的断口分析,裂纹源均产生于富mg、富o处,其周围存在fe、mn、si富集点。表明在mgo处裂纹萌生比在粗大相处更加敏感。本批合金在苏研院熔铸,除气除杂设备条件有限,可能导致合金中mgo偏多。尽管发现裂纹普遍萌生于mgo处,但比较4#(高cumg)和5#(低cumg)合金发现:5#(低cumg)挤压方向疲劳寿命最高,但横向寿命没有明显提高。4#(高cumg)横向疲劳性能最高,但挤压方向寿命没有明显降低。初步认为mgo对疲劳裂纹的萌生时间是一致的,粗大相的影响可能体现在裂纹扩展。通过综合分析,提出成分优化方案:(1)无zr合金:4.1%cu,0.4%mg、0.1%fe,0.7%si,0.8%mn。当炉温可控偏差±5℃,均匀化工艺采用:450℃×5h+505℃×30h。(2)加zr合金:4.1%cu,0.4%mg、0.1%fe,0.7%si,0.6%mn,0.1%zr。当炉温可控偏差±5℃,均匀化工艺采用:400℃×10h+450℃×5h+505℃×30h。如表10所示,表10为实际生产时铸锭成品成分控制表。表102014铸锭成品成分对所公开的实施例的上述说明,使本领域专业技术人员能够实现或使用本发明。对这些实施例的多种修改对本领域的专业技术人员来说将是显而易见的,本文中所定义的一般原理可以在不脱离本发明的精神或范围的情况下,在其它实施例中实现。因此,本发明将不会被限制于本文所示的这些实施例,而是要符合与本文所公开的原理和新颖特点相一致的最宽的范围。当前第1页1 2 3