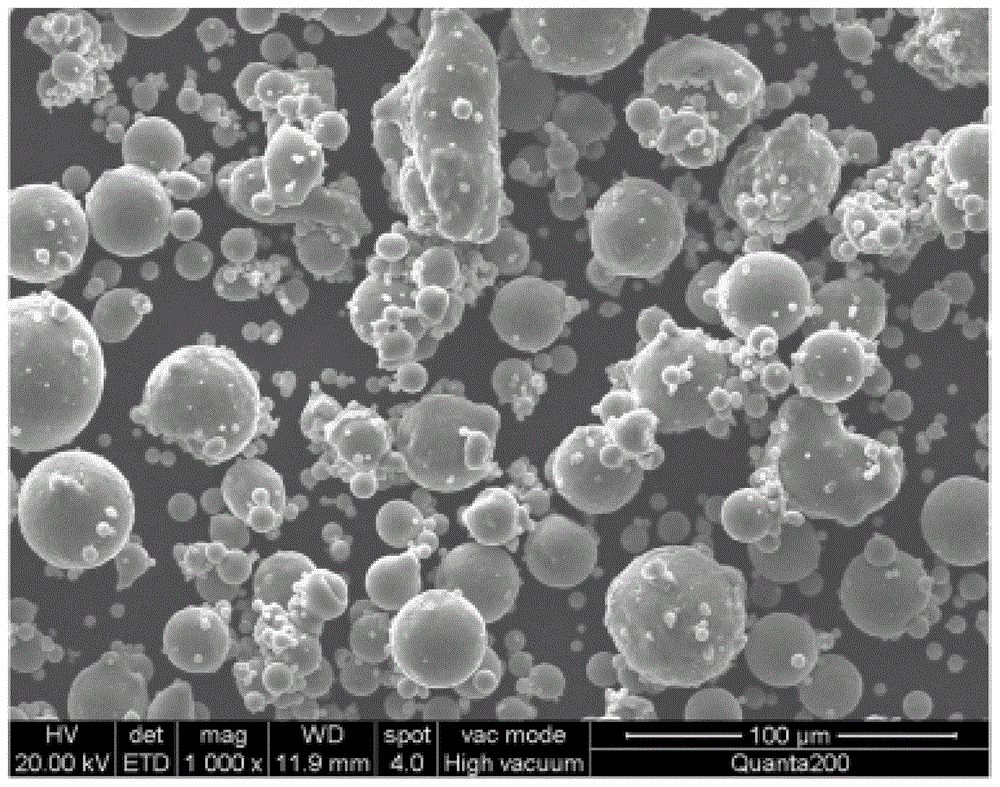
本发明属于增材制造
技术领域:
,具体涉及一种提高铝合金粉体激光吸收率的方法。
背景技术:
:区别与传统的去除型加工方式,3d打印作为增材制造技术,正以其简易的制造工艺、相对较低的生产成本和较短的研发周期,备受人们关注。目前,3d打印技术已经开始从研发阶段逐步向产业化发展,但3d打印用金属粉末的成本及其性能是制约该产业快速发展的关键因素。3d打印用的金属粉末需要满足高纯度、高球形度、细粒径和窄的粒径分布要求。纯度方面,在金属粉末的制备过程中,由于制粉工艺的缺陷,会带入一些杂质,这些杂质的存在会改变所制备零件的特性甚至致使打印无法进行。金属粉末的纯净度会直接影响3d打印的成形质量。通常粉末中的夹杂物会提高颗粒硬度,降低粉末的成形性能,对材料的韧性造成负面影响。高球形度方面,粉末的颗粒形状直接影响粉末的流动性、松装密度,最终对所制备金属零件的性能产生影响。在lens(laserengineerednetshaping,简称lens)成形过程中,粉末颗粒由载粉气流输送进入激光熔池,连续稳定的输送需要流动性良好的粉末,才能保证形成零件的均匀致密。在slm(selectivelasermelting,选择性激光熔化,简称slm)和ebsm(electronbeamselectivemelting,电子束选区熔化,简称ebsm)工艺中,粉末颗粒首先在铺粉机构的作用下铺展成粉末层,粉末良好的流动性对获得均匀平整的粉末层至关重要。球形或者近球形粉末具有良好的流动性,在打印过程中不易堵塞供粉系统,能铺成薄层,进而提高3d打印零件的尺寸精度、表面质量和零件的密度和组织均匀性。粒径分布方面,粉末粒度的大小直接影响铺粉层的厚度,一般来说,铺粉层厚度为50~100μm,要想铺出均匀密实的粉层,铺粉层厚度必须是粉末颗粒直径的两倍以上。理论上粒度小的粉末有利于烧结的顺利进行,但是如果细颗粒过多,易造成铺粉厚度不均匀,在烧结过程中容易出现球化现象。slm技术是利用金属粉末在激光束的热作用下完全熔化、经冷却凝固而成形的一种技术。为了完全熔化金属粉末,要求较高的激光能量密度。在高激光能量密度作用下,金属粉末完全熔化,经散热冷却后可实现与固体金属冶金焊合成形。铝合金材料具有高的比强度,耐腐蚀等特点,在航空航天、汽车工业领域有广泛的应用前景。随着增材制造技术的发展,铝合金材料应用于slm技术也备受关注。由于金属粉末需要在高的激光能量密度作用下完全熔化成形,而铝合金粉体材料激光吸收率低的本征性质制约了其在slm技术中的应用。技术实现要素:本发明旨在至少解决现有技术中存在的技术问题之一。为此,本发明提出一种提高铝合金粉体激光吸收率的方法,该方法可以使铝合金粉体表面因附着有细小的铝合金粒子且表面凹凸不平,从而增加激光在铝合金粉体表面的反射次数,达到提高铝合金粉体激光吸收率的效果。根据本发明第一方面实施例的一种提高铝合金粉体激光吸收率的方法,所述方法是将铝合金粉体进行球形化处理后,再通过超声波进行清洗并干燥,所述铝合金粉体的粒径范围是15~53μm。该粒径范围的铝合金粉体适合用于3d打印。根据本发明实施例的一种提高铝合金粉体激光吸收率的方法,至少具有如下技术效果:该方法利用等离子体球化过程温度高、冷却速度快的特点,将铝合金粉末送入等离子体炬中快速熔融,并在惰性气氛中迅速冷却,熔融的粉末在表面张力的作用下形成高球形度铝合金粉末。该方法可以使铝合金粉体表面因附着有细小的铝合金粒子且表面凹凸不平,从而增加激光在铝合金粉体表面的反射次数,达到提高铝合金粉体激光吸收率的效果,使铝合金粉体的激光吸收率从未经处理时的16.7%提升到了29.2%,使得本发明实施例方法制备的铝合金粉末在slm成形过程中能更有效的吸收激光能量,最终实现改善打印件的成型性能。此外,铝合金粉体材料的流动性、松装密度和振实密度也得到了显著改善。根据本发明的一些实施例,所述提高铝合金粉体激光吸收率的方法的步骤包括:s1:对所述铝合金粉体进行射频等离子体球化处理;s2:超声清洗步骤s1处理后的粉体材料;s3:对步骤s2处理后的粉体材料进行真空干燥处理。步骤s1中,射频等离子体球化处理的设备为teksphero-40kwsy165等离子体球化系统。射频等离子体球化系统送粉器探头型号为sg792或si792。根据本发明的一些实施例,所述射频等离子体球化处理的功率为30~40kw。根据本发明的一些实施例,所述射频等离子体球化处理的送粉速率为20~40g/min。根据本发明的一些实施例,所述射频等离子体球化处理的鞘气气体流量为50~55slpm。鞘气为氩气。根据本发明的一些实施例,所述射频等离子体球化处理的中心气气体流量为12~15psia。中心气为氩气。根据本发明的一些实施例,所述射频等离子体球化处理的载气气体流量为5~8slpm。载气为氩气。步骤s2中,超声清洗过程中,超声波在颗粒表面的振动产生的作用力是清洗干净的关键,清洗时的溶剂仅作为载体,载体可以为乙醇,也可以为其它不与铝合金发生反应的溶剂。假如只有溶剂,没有超声作用,无法将步骤s1处理后的粉体材料清洗干净。洗涤过程外加超声波清洗,超声波清洗的时间大于30min,重复清洗2~3次。根据本发明的一些实施例,所述清洗剂为无水乙醇。根据本发明的一些实施例,所述真空干燥处理的温度为55~65℃。根据本发明的一些实施例,所述真空干燥处理的时间为1~2h。附图说明图1是处理前alsi10mg合金粉末的微观形貌图。图2是处理后alsi10mg合金粉末的微观形貌图。图3是等离子体球化后得到的alsi10mg粉末超声清洗前的微观形貌图。图4是等离子体球化后得到的alsi10mg粉末超声清洗后的微观形貌图。图5是处理前后的alsi10mg合金粉末drs检测结果示意图。具体实施方式以下是本发明的具体实施例,并结合实施例对本发明的技术方案作进一步的描述,但本发明并不限于这些实施例。实施例1本例提供了一种提高铝合金粉体激光吸收率的方法,该方法是将铝合金粉体进行球形化处理后,再用超声波清洗并干燥,铝合金粉体的粒径范围是15~53μm。实施例2本例提供了一种提高铝合金粉体激光吸收率的方法,步骤包括:s1:对所述铝合金粉体进行射频等离子体球化处理;s2:超声清洗步骤s1处理后的粉体材料;s3:对步骤s2处理后的粉体材料进行真空干燥处理。步骤s1中,射频等离子体球化处理的设备为teksphero-40kwsy165等离子体球化系统。射频等离子体球化系统送粉器探头型号为sg792或si792。射频等离子体球化处理的功率为30~40kw。射频等离子体球化处理的送粉速率为20~40g/min。射频等离子体球化处理的鞘气气体流量为50~55slpm。鞘气为氩气。射频等离子体球化处理的中心气气体流量为12~15psia。中心气为氩气。射频等离子体球化处理的载气气体流量为5~8slpm。载气为氩气。步骤s2中,超声波清洗的时间大于30min,重复清洗2~3次。清洗时所用的溶剂为无水乙醇。步骤s3中,真空干燥处理的温度为55~65℃。真空干燥处理的时间为1~2h。实施例3本例对alsi10mg合金粉末进行了处理,具体为:将粒径范围为15~53μm的气雾化alsi10mg合金粉末进行等离子体球化处理,球化工艺条件为:功率为30kw,压力为15psia,氩气鞘气气体流量为55slpm,氩气中心气气体流量为15psia,氩气载气气体流量为5slpm。等离子体球化后得到的alsi10mg粉末进行超声清洗并干燥,得到粉末成品。用sem观察处理前后的alsi10mg合金粉末的微观形貌,如图1和图2所示,其中图1是原始alsi10mg合金粉末的微观形貌图,图2是处理后alsi10mg合金粉末的微观形貌图。比较图1和图2可以发现,经过处理后,铝合金粉体表面粗糙,凹凸不平,附着有细小的铝合金粒子,从而可以增加激光在铝合金粉体表面的反射次数,提高粉末的激光吸收率。此外,经过等离子体球化处理,粉体的球形度也得到明显改善。图3是等离子体球化后且未清洗前得到的单个alsi10mg粉末的微观形貌图,图4是等离子体球化后并超声清洗后得到的单个alsi10mg粉末微观形貌图。比较图3和图4可以看出,超声波清洗后去除了alsi10mg粉末表面的部分细小的铝合金粒子,有利于提高了粉末的流动性和质量,从而改善3d打印件质量。然而,超声波清洗仅将alsi10mg粉末表面以机械力结合的细小粒子去除,仍有部分粒子熔化凝固在铝合金粉末表面未被去除,清洗后这些未被去除的细小粒子留在alsi10mg粉末表面起到了增加铝合金粉体表面粗糙度的作用,增加了激光在铝合金粉体表面的反射次数、提高了激光吸收率。最终产生的效果是,在粉末表面粗糙度与粉末的流动性和利于3d打印之间取得了平衡。若没有进行超声清洗,alsi10mg粉末表面过多的细小粒子会影响alsi10mg粉末的流动性,不利于3d打印。分别取原始alsi10mg合金粉末和等离子体球化后的alsi10mg合金粉末产品进行drs检测,得到了如图5所示的激光吸收率图。图5中,曲线1为处理前alsi10mg合金粉末的吸收曲线,曲线2为等离子体球化后的alsi10mg合金粉末的吸收曲线,可以看出铝合金粉体的激光吸收率从未经处理时的16.7%提升到了29.2%。分别取原始alsi10mg合金粉末和等离子体球化后的alsi10mg合金粉末产品测试其流动性、松装密度及振实密度,结果如表1所示。表1处理前后alsi10mg合金粉末的流动性、松装密度及振实密度测试结果合金粉末流动性松装密度振实密度原始alsi10mg无流动1.122g/ml1.449g/mlalsi10mg产品101.14s/50g1.756g/ml1.923g/ml当前第1页12