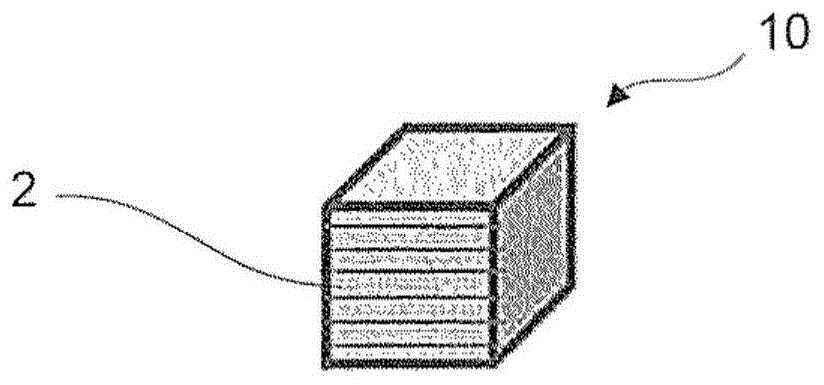
本发明涉及使无定形合金薄带结晶化而成的合金薄带的制造方法。
背景技术:
:无定形合金薄带为软磁性材料,因此无定形合金薄带的层叠体作为铁芯用于马达、变压器等。而且,通过将无定形合金薄带加热而结晶化的纳米晶合金薄带是可兼具高饱和磁通密度和低矫顽力的软磁性材料,因此近年来纳米晶合金薄带的层叠体用作它们的铁芯。为了得到纳米晶合金薄带而使无定形合金薄带结晶化时,由于结晶化反应而放出热,因此有时发生过度的温度上升。其结果,由于发生晶粒的粗化或化合物相的析出,有时软磁特性劣化。为了应对上述问题,能够使用如下方法:将无定形合金薄带在一张张独立的状态下加热而结晶化,从而提高散热性,减少结晶化反应产生的热的放出引起的温度上升的影响,但由于是一张张的热处理,因此生产率低。因此,例如,在日本特开2017-141508中提出了如下方法,其为在将无定形合金薄带的层叠体从层叠方向的两端用板夹持的状态下利用板将层叠体从两端加热以结晶化的方法,其中,通过使两端的板吸收结晶化反应的放出热,从而抑制温度上升。另外,在日本特开2011-165701中记载了如下方法:通过将加热器夹持在邻接的无定形合金薄带间将层叠体加热,从而调整加热时的层叠体内的温度分布。技术实现要素:但是,对于在日本特开2017-141508中提出的方法而言,为了使板从层叠方向的两端吸收多个合金薄带的反应热,将层叠体的厚度(层叠张数)限制为用板能够吸热的厚度,因此在通过对1个层叠体的加热处理从而能够结晶化的合金薄带的数目上有限制,不能以高生产率制造结晶化了的合金薄带。即使应用了日本特开2011-165701中提出的方法也是同样的。本发明的一个方案提供合金薄带的制造方法,其能够以高生产率制造使无定形合金薄带结晶化而成的合金薄带。本发明的一个方案涉及的合金薄带的制造方法包括:准备工序,准备多个无定形合金薄带层叠而成的层叠体,第一热处理工序,将所述层叠体加热至不到所述无定形合金薄带的结晶化开始温度的第一温度范围,和第二热处理工序,在所述第一热处理工序后将所述层叠体的端部加热至所述结晶化开始温度以上的第二温度范围,其中,在所述第一热处理工序后,保持所述层叠体的周围的气氛温度以使得通过在所述第二热处理工序中将所述层叠体的端部加热至所述第二温度范围从而将所述层叠体维持在可结晶化的温度范围,在将所述第一热处理工序中将所述层叠体加热至所述第一温度范围所需的热量设为q1,将所述第二热处理工序中将所述层叠体的端部加热至所述第二温度范围时给予所述层叠体的热量设为q2,将所述层叠体结晶化时放出的热量设为q3,将使所述层叠体的整体成为所述结晶化开始温度所需的热量设为q4的情况下,满足下述式(1)。q1+q2+q3≧q4(1)根据本发明的一个方案,能够以高生产率制造使无定形合金薄带结晶化而成的合金薄带。在上述方案的合金薄带的制造方法中,在所述第二热处理工序中,作为所述端部,可将所述层叠体的层叠方向的端部加热。在上述方案的合金薄带的制造方法中,在所述第二热处理工序中,可在将所述层叠体在所述层叠方向上加压的状态下将所述层叠方向的所述端部加热。在上述方案的合金薄带的制造方法中,在所述第二热处理工序中,作为所述端部,可将所述层叠体的平面方向的端部加热。上述方案的合金薄带的制造方法可进一步包括散热工序,使所述层叠体的与所述端部相反侧的端部与散热用构件接触。附图说明以下参照附图对本发明的例示实施方式的特征、优点以及技术和工业重要性进行说明,其中相同的附图标记表示相同的要素,并且其中:图1a为示出本发明的实施方式涉及的合金薄带的制造方法的一例的概略工序图。图1b为示出本发明的实施方式涉及的合金薄带的制造方法的一例的概略工序图。图1c为示出本发明的实施方式涉及的合金薄带的制造方法的一例的概略工序图。图2为示出图1c中所示的第二热处理工序的示意图。图3a为示出图1c中所示的第二热处理工序引起的结晶化反应的样子的示意图。图3b为示出图1c中所示的第二热处理工序引起的结晶化反应的样子的示意图。图4为示意地示出图1a~图1c中所示的合金薄带的制造方法中层叠体中的各无定形合金薄带的温度分布的坐标图。图5为示出采用差示扫描型热量分析计(dsc)所测定的无定形合金的dsc曲线的坐标图。图6a为示出本发明的实施方式涉及的合金薄带的制造方法的另一例的概略工序图。图6b为示出本发明的实施方式涉及的合金薄带的制造方法的另一例的概略工序图。图6c为示出本发明的实施方式涉及的合金薄带的制造方法的另一例的概略工序图。图7为示出图6c中所示的第二热处理工序的示意图。图8a为示出图6c中所示的第二热处理工序引起的结晶化反应的样子的示意图。图8b为示出图6c中所示的第二热处理工序引起的结晶化反应的样子的示意图。图9为示意地示出图6a~图6c中所示的合金薄带的制造方法中层叠体的各无定形合金薄带中的各部分的温度分布的坐标图。图10a为示出本发明的实施方式涉及的合金薄带的制造方法的另一例的概略工序图。图10b为示出本发明的实施方式涉及的合金薄带的制造方法的另一例的概略工序图。图11为用图像示出实施例1-1中的将上端部加热后经过400秒后的层叠体的计算模型的各位置的温度的图。图12为示出实施例1-1中的层叠体的计算模型的层叠方向的上端部、中央部和下端部的温度变化的坐标图。图13a为示出实施例1-2中的合金薄带的制造方法的实验设备的照片。图13b为示出实施例1-2中的合金薄带的制造方法的实验的示意图。图14a为示出实施例1-2中的层叠体的层叠方向的上端的合金薄带的温度变化的坐标图。图14b为示出实施例1-2中的层叠体的层叠方向的下端的合金薄带的温度变化的坐标图。图15为用图像示出实施例2-1中的将内周侧端部加热后经过20秒后的层叠体的计算模型的各位置的温度的图。图16为示出实施例2-1中的层叠体的计算模型的平面方向的中央部的温度变化的坐标图。图17a为示出实施例2-2中的合金薄带的制造方法的实验的示意图。图17b为示出实施例2-2中的合金薄带的制造方法的实验的示意图。图18为示出实施例2-2中的层叠体的合金薄带的平面方向的中央部的温度变化的坐标图。图19a为示出合金薄带的制造方法的参考例的概略工序图。图19b为示出合金薄带的制造方法的参考例的概略工序图。图20为示出用根据图19a、图19b中所示的参考例得到的层叠体的各合金薄带测定的矫顽力hc的范围的坐标图。具体实施方式以下对本发明涉及的合金薄带的制造方法的实施方式进行说明。本实施方式涉及的合金薄带的制造方法包括:准备工序,准备多个无定形合金薄带层叠而成的层叠体;第一热处理工序,将所述层叠体加热至不到所述无定形合金薄带的结晶化开始温度的第一温度范围;和第二热处理工序,在所述第一热处理工序后将所述层叠体的端部加热至所述结晶化开始温度以上的第二温度范围,其中,在所述第一热处理工序后,保持所述层叠体的周围的气氛温度以使得通过在所述第二热处理工序中将所述层叠体的端部加热至所述第二温度范围从而将所述层叠体维持在可结晶化的温度范围,在将所述第一热处理工序中将所述层叠体加热至所述第一温度范围所需的热量设为q1,将所述第二热处理工序中将所述层叠体的端部加热至所述第二温度范围时给予所述层叠体的热量设为q2,将所述层叠体结晶化时放出的热量设为q3,将使所述层叠体的整体成为所述结晶化开始温度所需的热量设为q4的情况下,满足下述式(1):q1+q2+q3≧q4(1)。首先,对于本实施方式涉及的合金薄带的制造方法,例示说明。其中,图1a~图1c为示出本实施方式涉及的合金薄带的制造方法的一例的概略工序图。图2为示出图1c中所示的第二热处理工序的示意图。图3a和图3b为示出图1c中所示的第二热处理工序引起的结晶化反应的样子的示意图。图4为示意地示出图1a至图1c中所示的合金薄带的制造方法中的层叠体中的各无定形合金薄带的温度分布的坐标图。图4的坐标图中部分地示出从层叠体的层叠方向的一端起包含一号、二号和三号合金薄带的各合金薄带的中心位置的温度分布。图5为示出采用差示扫描型热量分析计(dsc)所测定的无定形合金的dsc曲线的坐标图。在本例的合金薄带的制造方法中,首先,如图1a中所示那样,准备多个无定形合金薄带2层叠而成的层叠体10(准备工序)。接下来,如图1b中所示那样,将层叠体10移动至第一加热炉20a内,用第一加热炉20a加热至不到无定形合金薄带2的结晶化开始温度的第一温度范围(第一热处理工序)。具体地,例如,如图4的温度分布中所示那样,将层叠体10的整体均热以使层叠体10中的全部的无定形合金薄带2的整体的温度成为第一温度范围内。接下来,如图1c和图2中所示那样,将层叠体10移动至第二加热炉20b内,使从层叠体10的层叠方向的一端起的一号无定形合金薄带2a的表面2as与高温热源30短时间接触。由此,如图4的温度分布中所示那样,在层叠体10中,在将一号无定形合金薄带2a以外的部分维持在不到结晶化开始温度的温度范围的状态下,将一号无定形合金薄带2a的整体加热至结晶化开始温度以上的第二温度范围(第二热处理工序)。另外,其后,使层叠体10中的与一号无定形合金薄带2a在层叠方向上为相反侧的一端的无定形合金薄带2z的表面2zs接触散热用构件40(散热工序)。由此,从该表面2zs散热,从而在层叠体10中的与无定形合金薄带2z的表面2zs接近的部分抑制以结晶化反应产生的放出热为原因的热积存,能够抑制发生晶粒的粗化和化合物相的析出。在本例中,在第一热处理工序后,保持层叠体10的周围的气氛温度以使得通过在第二热处理工序中将一号无定形合金薄带2a的整体加热至第二温度范围从而将层叠体10的整体维持在可结晶化的温度范围。换言之,在第一热处理工序后,以通过在第二热处理工序中将一号无定形合金薄带2a的整体加热至第二温度范围从而将层叠体10的整体维持在可发生层叠体10的整体的结晶化的温度范围的方式保持层叠体10的周围的气氛温度。另外,将第一热处理工序中将层叠体10的整体加热至第一温度范围所需的热量设为q1,将第二热处理工序中将一号无定形合金薄带2a加热至第二温度范围时给予层叠体10的热量设为q2,将层叠体10结晶化时放出的热量设为q3,将使层叠体10的整体成为结晶化开始温度所需的热量设为q4的情况下,满足下述式(1)。q1+q2+q3≧q4(1)根据本例,通过采用第二热处理工序,在层叠体10中,将一号无定形合金薄带2a加热至结晶化开始温度以上的第二温度范围,从而如图3a中所示那样,使一号无定形合金薄带2a结晶化。此时,由图5的dsc曲线可知,一号无定形合金薄带2a放出结晶化反应产生的热。该放出热从结晶化反应后的温度高的一号无定形合金薄带2a移动至温度低的、从一端起的二号无定形合金薄带2b。然后,如上述那样保持层叠体10的周围的气氛温度,并且满足上述式(1),因此二号无定形合金薄带2b主要被该放出热加热,从而如图4的温度分布中所示那样,成为第二温度范围。由此,二号无定形合金薄带2b如图3b中所示那样,在结晶化的同时放出结晶化反应产生的热。同样地,从一端起的三号无定形合金薄带2c主要被二号无定形合金薄带2b的放出热加热,从而如图4的温度分布中所示那样,成为第二温度范围。由此,三号无定形合金薄带2c如图3b中所示那样,在结晶化的同时放出结晶化反应产生的热。这样的结晶化反应和其产生的热的放出如图3b中所示那样反复发生,以致从层叠体10的层叠方向的一端起的一号无定形合金薄带2a传播到另一端的无定形合金薄带2z。因此,仅通过在第一热处理工序中将层叠体10加热到第一温度范围后,在第二热处理工序中将一号无定形合金薄带2a加热到第二温度范围,就能够使层叠体10中的全部的无定形合金薄带2的整体结晶化。此时,对层叠体10的厚度(层叠张数)并无特别限定。其中,图6a~图6c为示出本实施方式涉及的合金薄带的制造方法的另一例的概略工序图。图7为示出图6c中所示的第二热处理工序的示意图。图8a和图8b为示出图6c中所示的第二热处理工序引起的结晶化反应的样子的示意图。图9为示意地示出图6a~图6c中所示的合金薄带的制造方法中的层叠体的各无定形合金薄带中的各部的温度分布的坐标图。图9的坐标图中部分地示出包含各无定形合金薄带的平面方向的一端至相反侧的端侧依次为一号、二号和三号部分的各部的中心位置的温度分布。在本例的合金薄带的制造方法中,首先,如图6a中所示那样,准备多个无定形合金薄带2层叠而成的层叠体10(准备工序)。接下来,如图6b中所示那样,将层叠体10移动至加热炉20内,用加热炉20加热至不到无定形合金薄带2的结晶化开始温度的第一温度范围(第一热处理工序)。具体地,例如,如图9的温度分布中所示那样,将层叠体10的整体均热以使层叠体10中的全部的无定形合金薄带2的整体的温度成为第一温度范围内。接下来,如图6c和图7中所示那样,将高温热源30移动至加热炉20内,使层叠体10的全部的无定形合金薄带2的平面方向的一个端面2ls与高温热源30短时间接触。由此,如图9的温度分布中所示那样,在全部的无定形合金薄带2中,在将从平面方向的一端起的一号部分即端部2la以外的部分维持在不到结晶化开始温度的温度范围的状态下,将端部2la加热至结晶化开始温度以上的第二温度范围(第二热处理工序)。在本例中,在第一热处理工序后,保持层叠体10的周围的气氛温度以使得通过在第二热处理工序中将全部的无定形合金薄带2的端部2la加热到第二温度范围从而将层叠体10的整体维持在可结晶化的温度范围。换言之,在第一热处理工序后,以通过在第二热处理工序中将全部的无定形合金薄带2的端部2la加热到第二温度范围从而将层叠体10的整体维持在可发生层叠体10的整体的结晶化的温度范围的方式保持层叠体10的周围的气氛温度。另外,将第一热处理工序中将层叠体10的整体加热至第一温度范围所需的热量设为q1,将第二热处理工序中将全部的无定形合金薄带2的端部2la加热至第二温度范围时给予层叠体10的热量设为q2,将层叠体10结晶化时放出的热量设为q3,将使层叠体10的整体成为结晶化开始温度所需的热量设为q4的情况下,满足下述式(1)。q1+q2+q3≧q4(1)根据本例,通过采用第二热处理工序,在全部的无定形合金薄带2中,端部2la加热至结晶化开始温度以上的第二温度范围,从而如图8a中所示那样,使端部2la结晶化。此时,如由上述的图5的dsc曲线可知,端部2la放出结晶化反应产生的热。该放出热在全部的无定形合金薄带2中从结晶化反应后的温度高的端部2la移动至温度低的、从平面方向的一端起的二号部分2lb。然后,如上述那样保持层叠体10的周围的气氛温度,并且满足上述式(1),因此全部的无定形合金薄带2中的二号部分2lb主要被该放出热加热,从而如图9的温度分布中所示那样,成为第二温度范围。由此,全部的无定形合金薄带2中的二号部分2lb如图8b中所示那样,在结晶化的同时放出结晶化反应产生的热。同样地,全部的无定形合金薄带2中的三号部分2lc主要被二号部分2lb的放出热加热,从而如图9的温度分布中所示那样,成为第二温度范围。由此,全部的无定形合金薄带2中的三号部分2lc如图8b中所示那样,在结晶化的同时放出结晶化反应产生的热。这样的结晶化反应和其产生的热的放出如图8b中所示那样反复发生,以致从全部的无定形合金薄带2的平面方向的一个端部2la传播到相反侧的端部2lz。因此,仅通过在第一热处理工序中将层叠体10加热到第一温度范围后,在第二热处理工序中将全部的无定形合金薄带2中的端部2la加热到第二温度范围,就能够使层叠体10中的全部的无定形合金薄带2的整体结晶化。此时,对层叠体10的厚度(层叠张数)并无特别限定。因此,根据本实施方式,如图1a~图1c和图6a~图6c中所示的例子那样,仅通过在第一热处理工序中将多个无定形合金薄带层叠而成的层叠体加热至不到无定形合金薄带的结晶化开始温度的第一温度范围后,在第二热处理工序中将层叠体的端部加热到结晶化开始温度以上的第二温度范围,从而在层叠体中以传播的方式发生结晶化反应,例如能够使对厚度(层叠张数)没有限定的层叠体的整体结晶化。因此,能够以高生产率制造使无定形合金薄带结晶化的合金薄带。接着,对于本实施方式涉及的合金薄带的制造方法,以其条件为中心详细地说明。1.准备工序在准备工序中,准备多个无定形合金薄带层叠而成的层叠体。无定形合金薄带的材质只要为无定形合金,则并无特别限定,例如可列举出fe基无定形合金、ni基无定形合金、co基无定形合金等。其中优选fe基无定形合金等。其中,所谓“fe基无定形合金”,是指以fe作为主成分,含有例如b、si、c、p、cu、nb、zr等杂质的无定形合金。所谓“ni基无定形合金”,是指以ni作为主成分的无定形合金。所谓“co基无定形合金”,是指以co作为主成分的无定形合金。作为fe基无定形合金,例如优选fe的含量为84原子%以上的范围内的无定形合金,其中优选fe的含量更多。这是因为,将无定形合金薄带结晶化而成的合金薄带的磁通密度根据fe的含量而变化。对无定形合金薄带的形状并无特别限定,例如除了单纯的矩形或圆形以外,可列举出马达和变压器等部件中使用的铁芯(定子铁芯、转子铁芯等)中使用的合金薄带的形状等。例如,在材质为fe基无定形合金的情况下,矩形的无定形合金薄带的尺寸(纵×横)例如为100mm×100mm,圆形的无定形合金薄带的直径例如为150mm。对无定形合金薄带的厚度并无特别限定,因无定形合金薄带的材质等而异,在为fe基无定形合金的情况下,例如为10μm以上且100μm以下的范围内,其中优选20μm以上且50μm以下的范围内。对无定形合金薄带的层叠张数并无特别限定,因无定形合金薄带的材质等而异,在为fe基无定形合金的情况下,例如优选500张以上且10000张以下。这是因为,如果过少,则不再能够以高生产率制造纳米晶合金薄带,如果过多,则搬送等变得太费劲,处理变得困难。对层叠体的厚度并无特别限定,因无定形合金薄带的材质等而异,在为fe基无定形合金的情况下,例如优选1mm以上且150mm以下。如果过薄,则不再能够以高生产率制造纳米晶合金薄带,如果过厚,则搬送等变得太费劲,处理变得困难。2.第一热处理工序在第一热处理工序中,将上述层叠体加热至不到上述无定形合金薄带的结晶化开始温度的第一温度范围。具体地,例如,将层叠体的整体均热,以使层叠体中的全部的无定形合金薄带的整体的温度成为第一温度范围。本发明中,所谓“结晶化开始温度”,是指将无定形合金薄带加热的情况下其结晶化开始的温度。所谓无定形合金薄带的结晶化,因无定形合金薄带的材质等而异,在为fe基无定形合金的情况下,例如是指使微细的bccfe结晶析出。结晶化开始温度因无定形合金薄带的材质等和加热速度而异,如果加热速度大,则存在结晶化开始温度升高的倾向,在为fe基无定形合金的情况下,例如成为350℃~500℃的范围内。第一温度范围是例如通过在将层叠体维持于第一温度范围的状态下将层叠体的端部加热至结晶化开始温度以上的后述的第二温度范围,从而能够使层叠体的整体结晶化的温度范围。对第一温度范围并无特别限定,因无定形合金薄带的材质等而异,在为fe基无定形合金的情况下,例如优选在结晶化开始温度-100℃以上且不到结晶化开始温度的范围内。这是因为,如果过低,有可能不能通过第二热处理工序使层叠体的整体结晶化。另外因为,如果过高,有可能通过第二热处理工序,在层叠体中发生晶粒的粗化或化合物相的析出,还因为由于合金薄带的材质的不均,有可能通过第一热处理工序在一部分中开始结晶化。3.第二热处理工序在第二热处理工序中,在上述第一热处理工序后将上述层叠体的端部加热至上述结晶化开始温度以上的第二温度范围。具体地,在第一热处理工序后,在将层叠体的该端部以外的部分维持在不到结晶化开始温度的温度范围的状态下,将层叠体的端部加热至结晶化开始温度以上的第二温度范围,在第二温度范围下保持结晶化所需的时间,从而使层叠体的端部的无定形合金结晶化成为纳米晶合金。对第二温度范围并无特别限定,优选为不到化合物相析出开始温度的温度范围。这是因为,能够抑制化合物相的析出。在本发明中,所谓“化合物相析出开始温度”,例如是指图5的dsc曲线中所示的、将结晶化后的无定形合金薄带进一步加热的情况下化合物相的析出开始的温度。另外,所谓“化合物相”,例如是指为fe基无定形合金的情形下的fe-b、fe-p等化合物相这样的、将结晶化后的无定形合金薄带进一步加热的情况下析出、与晶粒粗化的情形相比使软磁特性显著劣化的化合物相。对第二温度范围并无特别限定,因无定形合金薄带的材质等而异,在为fe基无定形合金的情况下,例如优选结晶化开始温度以上且不到结晶化开始温度+100℃的范围内,特别优选结晶化开始温度+20℃以上且不到结晶化开始温度+50℃的范围内。这是因为,如果过低,则有可能不能使层叠体的整体结晶化,如果过高,则有可能在层叠体中发生晶粒的粗化或化合物相的析出。在第二热处理工序中,优选例如如图1a~图1c中所示的例子中从层叠体10的层叠方向的一端起将一号无定形合金薄带2a的整体加热到第二温度范围那样,作为上述端部,将上述层叠体的层叠方向的端部加热。这是因为,能够将层叠体在平面方向上均匀地加热。作为层叠体的层叠方向的端部,例如如图2中所示的一号无定形合金薄带2a的整体那样,可列举出层叠体的层叠方向的端部的平面方向的整体或一部分等,但优选平面方向的整体。应予说明,本发明中,所谓“平面方向”,是指与层叠体的层叠方向垂直的方向。另外,在将层叠体的层叠方向的端部加热至第二温度范围的情况下,优选在将上述层叠体在上述层叠方向上加压的状态下将上述层叠方向的上述端部加热。这是因为,由于层叠方向的合金薄带间的热传导变得良好,因此结晶化反应变得容易在层叠体的层叠方向上传播。这是因为,特别是在制造部件中使用的铁芯的情况下,由于在加压状态下准备层叠体,因此通过在组装的状态下加热能够缩短工序。在第二热处理工序中,优选例如如图6a~图6c中所示的例子中将层叠体10的全部的无定形合金薄带2的平面方向的一个端部2la加热到第二温度范围那样,作为上述端部,将上述层叠体的平面方向的端部加热。这是因为,通过比合金薄带间良好的合金薄带内的热传导,结晶化反应传播,因此结晶化反应变得容易在层叠体中传播。作为层叠体的平面方向的端部,例如可列举出层叠体的全部的无定形合金薄带的平面方向的一个端部等。另外,在第二热处理工序中,作为层叠体的端部,可加热连续的1处端部或分离的多处端部。作为分离的多处端部的组合,例如可列举出层叠方向的一个端部和另一端部的组合、层叠方向的端部和平面方向的端部的组合等。作为将层叠体的端部加热至第二温度范围的方法,只要能够使层叠体的端部的无定形合金结晶化,则并无特别限定,例如可列举出如图1a~图1c和图6a~图6c中所示的例子那样使层叠体的端面与高温热源接触的方法和使用灯的辐射加热等。作为高温热源,例如可列举出由铜等构成的热导率良好的高温板、盐浴等高温的液体、加热器、高频等。使层叠体的端部与高温热源接触的方法只要能够将层叠体的端部加热到第二温度范围、保持结晶化所需的时间,则并无特别限定,例如,能够根据层叠张数、合金薄带的尺寸等适当地设定接触时间、接触面积等,以致在不发生化合物相的析出和晶粒的粗化的情况下使层叠体的整体结晶化。例如,在合金薄带的层叠张数少的情况下,能够将接触时间设定得短,在合金薄带的层叠张数多的情况下,能够将接触时间设定得长。再有,在第二热处理工序中,例如,可通过如图1a~图1c中所示的例子那样使层叠体从进行第一热处理工序的热处理炉内移动至其他腔室的热处理炉内,从而使层叠体与其他腔室内的高温热源接触,也可通过如图6a~图6c中所示的例子那样使高温热源移动至进行了第一热处理工序的热处理炉,从而使层叠体与高温热源接触。4.气氛温度在本实施方式涉及的合金薄带的制造方法中,在上述第一热处理工序后,保持上述层叠体的周围的气氛温度以使得通过在上述第二热处理工序中将上述层叠体的端部加热至上述第二温度范围从而将上述层叠体维持在可结晶化的温度范围(以下有时简称为“可结晶化的温度范围”。)。换言之,在第一热处理工序后,以通过在第二热处理工序中将层叠体的端部加热至第二温度范围从而将层叠体维持在可发生层叠体的结晶化的温度范围的方式保持层叠体的周围的气氛温度。具体地,在第一热处理工序后,以将层叠体中的合金薄带的非晶质的部分维持在可结晶化的温度范围的方式保持气氛温度。对气氛温度的保持温度并无特别限定,因无定形合金薄带的材质等而异,在为fe基无定形合金的情况下,例如优选第一温度范围的下限-10℃以上且第一温度范围的上限以下的范围内,特别优选第一温度范围的范围内。这是因为,如果过低,有可能在层叠体中不再使结晶化反应发生以致传播;如果过高,有可能在层叠体中发生晶粒的粗化或化合物相的析出;成本升高。5.各热量的关系在本实施方式涉及的合金薄带的制造方法中,在将上述第一热处理工序中将上述层叠体加热至上述第一温度范围所需的热量设为q1,将在上述第二热处理工序中将上述层叠体的端部加热至上述第二温度范围时给予上述层叠体的热量设为q2,将上述层叠体结晶化时放出的热量设为q3,将为了使上述层叠体的整体成为上述结晶化开始温度所需的热量设为q4的情况下,满足下述式(1)。在不满足下述式(1)的情况下,有可能不能使层叠体的整体结晶化。应予说明,q4更具体地为在第一热处理工序中将层叠体用q1加热、在第二热处理工序中将层叠体的端部用q2加热、在第二热处理工序后将层叠体用q3加热的情形的层叠体的温度经历中使层叠体的整体从在第一热处理工序中用q1加热之前的状态成为结晶化开始温度所需的热量。例如在上述情形下,特别是在除了用q1和q2加热以外没有层叠体与外部之间的热移动时的层叠体的温度经历中,q4是使层叠体的整体从在第一热处理工序中用q1加热之前的状态成为结晶化开始温度所需的热量。q1+q2+q3≧q4(1)另外,在满足上述式(1)的情况下,将q1中将层叠体中的各个无定形合金薄带加热至第一温度范围所需的热量设为qa1,将q2中对该无定形合金薄带给予的热量设为qa2,将q3中对该无定形合金薄带给予的热量设为qa3,将q4中使该无定形合金薄带的整体成为结晶化开始温度所需的热量设为qa4的情形下,对于层叠体中的全部的无定形合金薄带,优选满足下述式(1a)。这是因为,能够使全部的无定形合金薄带的整体结晶化。应予说明,qa4更具体地为在第一热处理工序中将层叠体中的各个无定形合金薄带用qa1加热、在第二热处理工序中将该无定形合金薄带用qa2加热、在第二热处理工序后将该无定形合金薄带用qa3加热时的该无定形合金薄带的温度经历中为了使该无定形合金薄带的整体从在第一热处理工序中用qa1加热之前的状态成为结晶化开始温度所需的热量。例如在上述情形下、特别是在除了用qa1、qa2和qa3加热以外无该无定形合金薄带与外部之间的热移动时的该无定形合金薄带的温度经历中,qa4为使该无定形合金薄带的整体从在第一热处理工序中用qa1加热之前的状态成为结晶化开始温度所需的热量。应予说明,在图1a~图1c和图6a~图6c中所示的例子满足下述式(1a)。qa1+qa2+qa3≧qa4(1a)再有,在本实施方式涉及的合金薄带的制造方法中,通常为了使用层叠体结晶化时放出的热量来使层叠体的整体结晶化,从外部给予的热量(q1和q2的合计)不会超过为了使层叠体的整体成为结晶化开始温度所需的热量(q4),满足下述式(2)。q1+q2<q4(2)另外,在本实施方式涉及的合金薄带的制造方法中,在将使层叠体的整体成为化合物相析出开始温度所需的热量设为q5的情况下,优选满足下述式(3)。这是因为,能够抑制化合物相的析出。应予说明,q5更具体地为在第一热处理工序中将层叠体用q1加热、在第二热处理工序中将层叠体的端部用q2加热、在第二热处理工序后将层叠体用q3加热时的层叠体的温度经历中使层叠体的整体从在第一热处理工序中用q1加热之前的状态成为化合物相析出开始温度所需的热量。例如在上述情形下、特别是除了用q1和q2加热以外无层叠体与外部之间的热移动时的层叠体的温度经历中,q5是使层叠体的整体从在第一热处理工序中用q1加热之前的状态成为化合物相析出开始温度所需的热量。q1+q2+q3<q5(3)另外,在满足上述式(3)的情况下,在将q1中将层叠体中的各个无定形合金薄带加热至第一温度范围所需的热量设为qa1,将q2中对该无定形合金薄带给予的热量设为qa2,将q3中对该无定形合金薄带给予的热量设为qa3,将使该无定形合金薄带的整体成为化合物相析出开始温度所需的热量设为qa5的情形下,对于层叠体中的全部的无定形合金薄带,优选满足下述式(3a)。这是因为,能够在全部的无定形合金薄带中抑制化合物相的析出。应予说明,qa5更具体地为在第一热处理工序中将层叠体中的各个无定形合金薄带用qa1加热、在第二热处理工序中将该无定形合金薄带用qa2加热、在第二热处理工序后将该无定形合金薄带用qa3加热时的该无定形合金薄带的温度经历中为了使该无定形合金薄带的整体从在第一热处理工序中用qa1加热之前的状态成为化合物相析出开始温度所需的热量。例如在上述情形下、特别是除了用qa1、qa2和qa3加热以外无该无定形合金薄带与外部之间的热移动时的该无定形合金薄带的温度经历中,qa5是使该无定形合金薄带的整体从在第一热处理工序中用qa1加热之前的状态成为化合物相析出开始温度所需的热量。qa1+qa2+qa3<qa5(3a)6.合金薄带的制造方法在本实施方式涉及的合金薄带的制造方法中,层叠体从加热至第二温度范围的端部开始结晶化,从而制造层叠体中的多个无定形合金薄带结晶化的多个纳米晶合金薄带。其中,所谓“纳米晶合金薄带”,是指通过在基本上没有发生化合物相的析出和晶粒的粗化的情况下使微细的晶粒析出,从而获得所期望的矫顽力等软磁特性的纳米晶合金薄带。纳米晶合金薄带的材质因无定形合金薄带的材质等而异,在为fe基无定形合金的情况下,例如,成为具有fe或fe合金的晶粒(例如,微细的bccfe结晶等)和非晶质相的混相组织的fe基纳米晶合金。作为纳米晶合金薄带的晶粒的粒径,只要获得所期望的软磁特性,则并无特别限定,因材质等而异,在为fe基纳米晶合金的情况下,例如优选25nm以下的范围内。这是因为,如果粗化则矫顽力劣化。应予说明,晶粒的粒径能够通过使用了透射电子显微镜(tem)的直接观察来测定。另外,晶粒的粒径能够由纳米晶合金薄带的矫顽力或温度分布推定。作为纳米晶合金薄带的矫顽力,因纳米晶合金薄带的材质等而异,在为fe基纳米晶合金的情况下,例如为20a/m以下,其中优选10a/m以下。这是因为,通过这样降低矫顽力,例如能够有效地降低马达等的铁芯中的损耗。应予说明,由于本实施方式涉及的各热处理工序中的温度范围等条件受到限制,因此纳米晶合金薄带的矫顽力的降低存在限度。本实施方式涉及的合金薄带的制造方法如图1a~图1c中所示的例子那样,优选还包括散热工序,使上述层叠体中的上述端部的相反侧的一端与散热用构件接触。这是因为,通过从层叠体中的相反侧的一端散热,从而在层叠体中的与相反侧的一端接近的部分,抑制以结晶化反应产生的放出热为原因的热积存,能够抑制发生晶粒的粗化和化合物相的析出。再有,作为散热工序,可以是在第二热处理工序中将层叠体的端部加热至第二温度范围之前使相反侧的一端与散热用构件接触的工序,也可以是在第二热处理工序中将层叠体的端部加热至第二温度范围之后使相反侧的一端与散热用构件接触的工序,通常,如图1a~图1c中所示的例子那样,为在第二热处理工序中将层叠体的端部加热至第二温度范围后使相反侧的一端与散热用构件接触的工序。这是因为,能够有效地抑制热积存。作为本实施方式涉及的合金薄带的制造方法,只要能够制造多个纳米晶合金薄带,则并无特别限定,例如,优选如下制造方法:在基本上没有发生化合物相的析出和晶粒的粗化的情况下,使层叠体的整体(具体地,例如层叠体中的全部的无定形合金薄带的整体)结晶化,使纳米晶合金薄带的晶粒成为所期望的粒径。在上述的合金薄带的制造方法中,为了在基本上没有发生化合物相的析出和晶粒的粗化的情况下,使层叠体的整体结晶化,使纳米晶合金薄带的晶粒成为所期望的粒径,不仅是目前为止说明的条件,也能够适当地设定其他的条件。另外,能够独立地适当设定各条件,也能够适当地设定各条件的组合。7.其他方案对于本实施方式涉及的合金薄带的制造方法的其他方案进行说明。图10a和图10b为示出本实施方式涉及的合金薄带的制造方法的其他例子的概略工序图。在本例中,首先,如图10a中所示那样,在准备将多个无定形合金薄带2层叠、制成定子铁芯的形状的层叠体10的准备工序后,使该层叠体10移动到加热炉20内,对该层叠体10进行本实施方式涉及的第一热处理工序和第二热处理工序。这种情况下,在第一热处理工序后,以将层叠体10维持在可结晶化的温度范围的方式保持层叠体10的周围的气氛温度,并且使其满足下述式(1)。q1+q2+q3≧q4(1)接下来,如图10b中所示那样,使层叠体10含浸于树脂并固定。由此制造定子铁芯10′。作为本实施方式涉及的合金薄带的制造方法,可如本例那样在准备工序中准备例如形成了部件中使用的铁芯的形状的层叠体。这是因为,能够以高生产率制造使用了无定形合金薄带结晶化而成的合金薄带的层叠体的铁芯。以下列举实施例和参考例,对本实施方式涉及的合金薄带的制造方法进一步具体地说明。1.在第二热处理工序中将层叠体的层叠方向的端部加热的实施例对在第二热处理工序中将层叠体的层叠方向的端部加热的合金薄带的制造方法的实施例进行说明。实施例1-1实施使用了cae(computeraidedengineering)的上述合金薄带的制造方法的模拟。以下具体地说明。无定形合金薄带的层叠体的计算模型作为本模拟中使用的无定形合金薄带的层叠体的计算模型,制作了具有图11中所示的形状的层叠体的计算模型m10。层叠体的计算模型m10是具有用位于定子铁芯中使用的层叠体的齿部分(与计算模型m10的齿部分m10t对应)的对称面(与计算模型m10的对称面ms对应)分割的形状,将层叠体简化为多个无定形合金薄带一体化而成的产物,并考虑与在层叠方向上邻接的无定形合金薄带之间的热移动而模型化的模型。将层叠体的计算模型m10设想为将由一般的fe基无定形合金构成的无定形合金薄带层叠而成,如下所述设定与无定形合金薄带有关的模拟所需的参数。结晶化开始温度:360℃,化合物相析出开始温度:530℃,热导率(层叠方向):4w/mk,与结晶化相伴的放出热量:90j/g就层叠体的计算模型m10而言,各部的尺寸如下所述设定。层叠方向的厚度t1:150mm,与合金薄带的外周的一部分对应的部分的长度l1:14mm,与合金薄带的内周的一部分对应的部分的长度l2:9mm,径向的宽度w1:40mm,齿部分m10t的径向的长度lt1:35mm,齿部分m10t之间的沟槽的周向的宽度wt1:5mm使用了cae的模拟使用了cae的模拟采用下述条件实施。模拟用软件:sftc公司制造deform本模拟中,首先,将层叠体的计算模型m10的整体均热至不到结晶化开始温度的320℃(第一热处理工序)。其次,使图11中所示的均热至500℃的高温热源的模型m30与层叠体的计算模型m10的层叠方向的上端面m10s接触60秒,将层叠体的计算模型m10的层叠方向的上端部m10a加热至结晶化开始温度以上的温度范围(第二热处理工序)。在本模拟中,在第一热处理工序后,将层叠体的计算模型m10的周围的气氛温度保持于320℃以使得通过在第二热处理工序中将层叠体的计算模型m10的层叠方向的上端部m10a加热至结晶化开始温度以上的温度范围从而将层叠体的计算模型m10的整体维持于可结晶化的温度范围。并且,满足本实施方式涉及的上述式(1)。另外,层叠体的计算模型m10及其周围的气氛之间的热移动也计算在内。解析结果通过本模拟,对在第二热处理工序中将层叠体的计算模型m10的层叠方向的上端部m10a加热到结晶化开始温度以上的温度范围后的层叠体的计算模型m10的各位置的温度变化进行了解析。图11为用图像示出将实施例1-1中的上端部加热后经过400秒后的层叠体的计算模型的各位置的温度的图。另外,图12为示出实施例1-1中的层叠体的计算模型的层叠方向的上端部、中央部和下端部的温度变化的坐标图。如图11中所示那样,在层叠体的计算模型m10中,将层叠方向的上端部m10a加热后,按层叠方向的上端部m10a、中央部m10b和下端部m10c的顺序成为结晶化开始温度以上,将上端部m10a加热后经过400秒后,大部分成为了结晶化开始温度以上。虽然未图示,但将上端部m10a加热后经过450秒后,整体成为了结晶化开始温度以上。再有,为了完成层叠体的各部位的结晶化,需要将层叠体的各部位保持在结晶化开始温度以上的温度一定时间。另外,如图12中所示那样,上端部m10a的温度在上升至结晶化开始温度以上后降低,中央部m10b的温度比上端部m10a慢地上升至结晶化开始温度以上后降低,下端部m10c的温度比中央部m10b慢地上升至结晶化开始温度以上后降低。实施例1-2实施了上述的合金薄带的制造方法的实验。以下具体地说明。无定形合金薄带的层叠体作为本实验中使用的无定形合金薄带的层叠体,制作了具有用于定子铁芯的形状的层叠体。层叠体通过将由fe的含量为84原子%以上的fe基无定形合金构成的无定形合金薄带层叠而制作。合金薄带的厚度和层叠张数以及各部的尺寸如下所述。合金薄带的厚度:0.025mm,合金薄带的形状:尺寸(纵×横)为50mm×50mm的矩形,层叠张数:500张合金薄带的制造方法的实验图13a为示出实施例1-2中的合金薄带的制造方法的实验设备的照片,图13b为示出实施例1-2中的合金薄带的制造方法的实验的示意图。本实验使用图13a中所示的实验设备100,如图13b中示意地示出那样进行。在本实验中,首先,如图13b中所示那样,将层叠体10配置于均热至320℃的下模52的上面,将层叠体10的周围用均热至320℃的防散热用构件54以没有与防散热用构件54接触的方式包围后,在它们之上配置了均热至320℃的上模56。然后,将层叠体10在该状态下保持10分钟。由此,将层叠体10的整体均热至不到结晶化开始温度的温度范围(第一热处理工序)。接下来,如图13b中所示那样,将上模56暂时移除后,采用上模56使均热至470℃的高温热源(高温板)30压靠层叠体10的层叠方向的上端面10s,在用层叠方向的5mpa的压力对层叠体10加压的状态下保持了1分钟。由此,将层叠体10的层叠方向的上端的无定形合金薄带加热至结晶化开始温度以上的温度范围(第二热处理工序)。在本实验中,在第一热处理工序后,利用下模52、防散热用构件54和上模56保持层叠体10的周围的气氛温度以使得通过在第二热处理工序中将层叠体10的层叠方向的上端的无定形合金薄带加热至结晶化开始温度以上的温度范围从而将层叠体10的整体维持在可结晶化的温度范围。而且,满足本实施方式涉及的上述式(1)。实验结果通过本实验,测定了在第二热处理工序中将层叠体10的层叠方向的上端的无定形合金薄带加热后的层叠体10的层叠方向的各位置的合金薄带的温度变化。图14a和图14b为示出实施例1-2中的层叠体的层叠方向的上端的合金薄带和下端的合金薄带的温度变化的坐标图。如图14a中所示那样,层叠体10的层叠方向的上端的合金薄带的温度在成为了结晶化开始温度以上后进一步上升,其后降低。如图14b中所示那样,层叠体10的层叠方向的下端的合金薄带的温度比上端的合金薄带慢地成为了结晶化开始温度以上后进一步上升,其后降低。另外,使用tem,在通过本实验得到的反应后的层叠体的层叠方向的上端和下端的合金薄带中测定晶粒的平均粒径,考察化合物相的析出的有无。将它们的结果示于下述表1中。【表1】如上述表1中所示那样,在反应后的层叠体的层叠方向的上端和下端的合金薄带中,晶粒的平均粒径均成为25nm以下,均无化合物相的析出。2.在第二热处理工序中将层叠体的平面方向的端部加热的实施例对在第二热处理工序中将层叠体的平面方向的端部加热的合金薄带的制造方法的实施例进行说明。实施例2-1实施采用了cae(computeraidedengineering)的上述合金薄带的制造方法的模拟。以下具体地进行说明。无定形合金薄带的层叠体的计算模型作为本模拟中使用的无定形合金薄带的层叠体的计算模型,制作了具有图15中所示的形状的层叠体的计算模型m12。层叠体的计算模型m12是具有用定子铁芯中使用的层叠体中的1张无定形合金薄带的齿部分(与计算模型m12的齿部分m12t对应)和后轭部分(与计算模型m12的后轭部分m12y对应)的对称面(与计算模型m12的对称面ms对应)分割的形状、考虑了与位于这1张无定形合金薄带的层叠方向的两侧的无定形合金薄带之间的热移动而模型化的模型。层叠体的计算模型m12设想为将由一般的fe基无定形合金构成的无定形合金薄带层叠而成的产物,如下所述设定了与无定形合金薄带有关的模拟所需的参数。结晶化开始温度:360℃,化合物相析出开始温度:530℃,热导率:10w/mk,与结晶化相伴的放出热量:90j/g,与邻接于层叠方向的两侧的无定形合金薄带之间的传热系数:50w/(m2k)层叠体的计算模型m12的各部的尺寸如下所述设定。合金薄带的厚度t2:0.025mm,与合金薄带的外周的一部分对应的部分的长度l3:7mm,与合金薄带的内周的一部分对应的部分的长度l4:3mm,径向的宽度w2:35mm,齿部分m12t的径向的长度lt2:20mm,齿部分m12t之间的沟槽的周向的宽度wt2:2mm使用了cae的模拟使用了cae的模拟在与实施例1-1相同的条件下实施。在本模拟中,首先,将层叠体的计算模型m12的整体均热至不到结晶化开始温度的320℃(第一热处理工序)。接下来,使图15中所示的均热至500℃的高温热源的模型m30与层叠体的计算模型m12的平面方向的内周侧端面m12s接触30秒,将层叠体的计算模型m12的平面方向的内周侧端部m12a加热至结晶化开始温度以上的温度范围(第二热处理工序)。在本模拟中,在第一热处理工序后,将层叠体的计算模型m12的周围的气氛温度保持于320℃以使得通过在第二热处理工序中将层叠体的计算模型m12的平面方向的内周侧端部m12a加热至结晶化开始温度以上的温度范围从而将层叠体的计算模型m12的整体维持在可结晶化的温度范围。而且,满足本实施方式涉及的上述式(1)。另外,层叠体的计算模型m12及其周围的气氛之间的热移动也计算在内。解析结果通过本模拟,对第二热处理工序中将层叠体的计算模型m12的平面方向的内周侧端部m12a加热到结晶化开始温度以上的温度范围后的层叠体的计算模型m12的各位置的温度变化进行了解析。图15为用图像示出将实施例2-1中的内周侧端部加热后经过20秒后的层叠体的计算模型的各位置的温度的图。另外,图16为示出实施例2-1中的层叠体的计算模型的平面方向的中央部的温度变化的坐标图。如图15中所示那样,在层叠体的计算模型m12中,将平面方向的内周侧端部m12a加热后,按平面方向的内周侧端部m12a、中央部m12b和外周侧端部m12c的顺序成为结晶化开始温度以上,将内周侧端部m12a加热后经过20秒后大部分成为了结晶化开始温度以上。虽然没有图示,但将内周侧端部m12a加热后经过30秒后,整体成为了结晶化开始温度以上。再有,为了完成层叠体的各部位的结晶化,必须将层叠体的各部位保持在结晶化开始温度以上的温度一定时间。另外,如图16中所示那样,平面方向的中央部m12b的温度在上升到结晶化开始温度以上后降低。另外,由图15和图16中所示的结果,认为平面方向的内周侧端部m12a的温度比中央部m12b先上升到结晶化开始温度以上后降低,平面方向的外周侧端部m12c的温度比中央部m12b慢地上升到结晶化开始温度以上后降低。实施例2-2实施了上述的合金薄带的制造方法的实验。以下具体地说明。无定形合金薄带的层叠体作为本实验中使用的无定形合金薄带的层叠体,制作了具有定子铁芯中使用的形状的层叠体。层叠体通过将由fe的含量为84原子%以上的fe基无定形合金构成的合金薄带层叠而制作。合金薄带的厚度和层叠张数以及各部的尺寸如下所述。合金薄带的厚度:0.025mm,合金薄带的形状:尺寸(纵×横)为50mm×50mm的矩形,层叠张数:500张合金薄带的制造方法的实验图17a和图17b为示出实施例2-2中的合金薄带的制造方法的实验的示意图。本实验中,首先,如图17a中所示那样,将层叠体10配置于均热至320℃的下模52的上面,将层叠体10的周围用均热至320℃的防散热用构件54以没有与防散热用构件54接触的方式包围,然后在它们之上配置了均热至320℃的上模56。然后,将层叠体10在该状态下保持了10分钟。由此,将层叠体10的整体均热至不到结晶化开始温度的温度范围(第一热处理工序)。接下来,如图17b中所示那样,将位于层叠体10的平面方向的一个端面侧的防散热用构件54的一部分暂时去除后,将均热至500℃的高温液体32压靠至层叠体10的平面方向的一个端面,在该状态下保持了1分钟。由此,将层叠体10的平面方向的一个端部加热至结晶化开始温度以上的温度范围(第二热处理工序)。在本实验中,在第一热处理工序后,利用下模52、防散热用构件54和上模56保持层叠体10的周围的气氛温度以使得通过在第二热处理工序中将层叠体10的平面方向的一个端部加热至结晶化开始温度以上的温度范围从而将层叠体10的整体维持于可结晶化的温度范围。而且,满足本实施方式涉及的上述式(1)。实验结果通过本实验,测定了在第二热处理工序中将层叠体10的平面方向的一个端部加热后的层叠体10的合金薄带的平面方向的各位置的温度变化。图18为示出实施例2-2中的层叠体的合金薄带的平面方向的中央部的温度变化的坐标图。如图18中所示那样,层叠体的合金薄带的平面方向的中央部的温度在成为了结晶化开始温度以上后进一步上升,其后降低。另外,使用tem,在通过本实验得到的反应后的层叠体的合金薄带的平面方向的中央部测定晶粒的平均粒径,考察了化合物相的有无。将它们的结果示于下述表2中。【表2】层叠体的合金薄带的平面方向的中央部晶粒的平均粒径[nm]25以下化合物相的析出的有无[-]无如上述表2中所示那样,在反应后的层叠体的合金薄带的平面方向的中央部,晶粒的平均粒径成为25nm以下,无化合物相的析出。3.通过均热处理给予用于结晶化反应的热量的参考例为了本实施方式的参考,对通过均热处理给予层叠体的结晶化所需的热量的合金薄带的制造方法的参考例进行说明。图19a和图19b为示出合金薄带的制造方法的参考例的概略工序图,在图19b中示出图19a中所示的玻璃管的截面。本参考例中,首先,如图19a中所示那样,准备将由fe的含量为84原子%以上的fe基无定形合金构成的3张无定形合金薄带2(形状:尺寸(纵×横)为10mm×30mm的矩形、厚度:0.016mm)层叠而成的层叠体10,用碳板60夹持,放入玻璃管70内。接下来,如图19b中所示那样,在内壁面施涂有au镀层24的加热炉20内配置玻璃管70,采用红外线灯80,利用在au镀层24反射的红外线均匀地将层叠体10加热。具体地,将加热炉20内的温度以20℃/分钟的升温速度加热到结晶化开始温度以上的400℃后,在400℃下保持10分钟,从而均匀地将层叠体10加热。其中,图20为示出用根据图19a、图19b中所示的参考例得到的层叠体的各合金薄带测定的矫顽力hc的范围的坐标图。在图20中将层叠体的合金薄带的矫顽力hc的目标范围一并示出。如图20中所示那样,参考例的矫顽力hc的范围的上限为10000a/m以上,与10a/m以下的目标范围相比,大幅地提高。认为由于发生热积存,从而产生晶粒的粗化,进一步成为高温,甚至产生了析出物。以上对本发明涉及的合金薄带的制造方法的实施方式进行了详述,但本发明并不限定于上述的实施方式,在不脱离专利权利要求书中记载的本发明的构思的范围内能够进行各种设计改变。当前第1页12