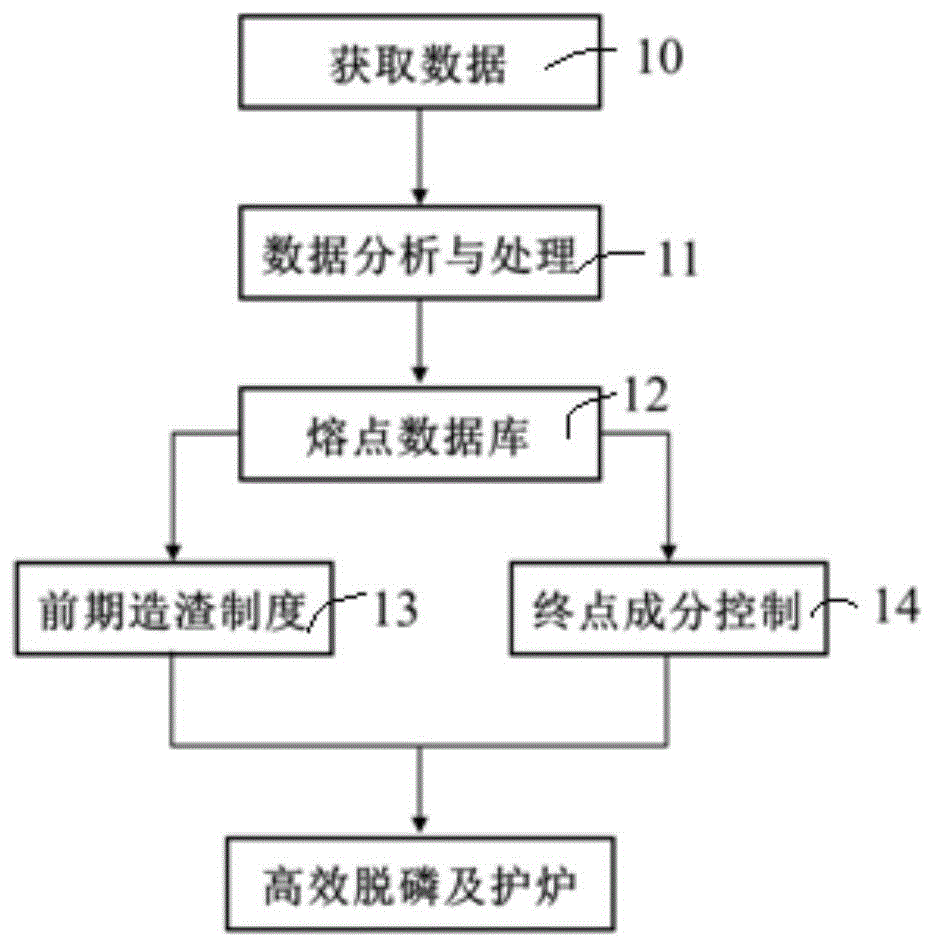
本发明涉及转炉炼钢
技术领域:
,更具体地说,涉及一种转炉渣熔点控制模型的高效脱磷及护炉的方法。
背景技术:
:随着矿石原料品质逐渐下降,高磷铁水出现的比例也大大增加;同时近年来,钢铁产品对磷含量的要求日趋严格。为了满足钢铁品质的要求,国内外各大钢厂对转炉高效脱磷的问题也越来越重视。为了生产低磷钢,现主要的冶炼工艺有:双渣留渣法冶炼、高碱度造渣冶炼、双联转炉工艺;这几种冶炼工艺均不符合当下转炉高效、低成本稳定生产的主流要求。转炉脱磷通过向炉内加入石灰等造渣材料,形成具有适当碱度、高氧化性和良好流动性的炉渣,以满足冶炼终点要求。冶炼前期的低温条件为高效脱磷提供良好的热力学基础,因此前期渣系的选择,造流动性良好(熔点合适)的炉渣是关键;以满足前期渣系的熔点低于最佳脱磷温度(1300℃~1450℃),即在熔池温度为最佳脱磷温度时,炉渣具备良好的脱磷动力学条件。目前转炉的成渣过程包括铁质成渣和钙质成渣两种路径,唐萍等人(钢包铸余渣作为转炉脱磷助熔剂理论及实践[j].钢铁,2016,51(3):84-89.)通过将精炼铸余渣作为转炉脱磷助熔剂的理论研究,得出铸余渣可作为转炉助熔剂使用大大提高脱磷效率。如何利用现有转炉脱磷工序,高效、低成本稳定地达到高效脱磷的目的是目前本领域技术人员亟需解决的技术难题。经检索,中国
专利名称:为:一种转炉单渣生产超低磷钢的方法(cn105132611b),通过调整前期和过程加料,来控制熔池升温速度,延长脱磷时间;以及在前期加入精炼渣,促进化渣,改善炉渣流动性。该方法对前期渣系碱度、氧化镁的控制未进行科学化的说明,同时前期及过程加料未进行量化的精确控制;易造成资源的浪费和人为干扰因素较大。此外,中国
专利名称:为:一种转炉的化渣方法(cn101892342b),该方法在冶炼前期加入高al复合渣,降低炉渣熔点,提高终点脱磷效率。但该方法未考虑到对复合渣的加入量与铁水成分之间的关系进行量化处理,同时对溅渣护炉的影响毫无涉及。中国
专利名称:为:一种转炉高效脱磷的冶炼方法(cn105671248b),该方法虽对预熔渣进行了量化控制,但其采用双渣操作模式,与现快节奏生产模式极为不符,同时该方法也同样不涉及对对前期冶炼渣系的控制。炉渣在钢铁冶炼过程中起着重要的作用,炉渣的熔点对冶炼过程及溅渣效果有着直接的影响。在炼钢生产流程中,转炉炉龄、炉型维护是广大炼钢工作者高度关心的问题。熔点是炉渣的重要性质之一,合理、科学化的控制炉渣熔点与出钢温度之间的关系是高效溅渣护炉的关键;确保在某一出钢温度下,炉渣能化透,流动性良好,溅渣动力学条件良好。定义出钢温度减去炉渣熔点温度为温度差;当正温度差越大,表明在此时炉渣较稀,对炉壁的黏附稳定性较差,炉渣溅干时间较长,护炉效果较差;当出现负温度差时,表明终点渣未化透,流动性较差,溅渣时间延长,但倒渣时炉渣未固化,对炉底及熔池部位冲刷较为严重,护炉效果较差;科学化控制温度差,进而控制好终点炉渣熔点是高效溅渣护炉的关键。现阶段转炉炼钢领域均为快节奏的生产模式,须杜绝因炉渣未溅干而带来的安全问题的前提下,缩短溅渣时间,达到高效溅渣的目的。为达到这一目的,国内外学者都在积极的进行技术研究与革新,大多数是通过加入改质剂、改善溅渣工艺、控制黏度等等方式,实现这一目的;但对不同冶炼条件下控制炉渣熔点的溅渣护炉工作还未开展研究。那么如何在生产中稳定有效的控制炉渣熔点达到高效化溅渣护炉是亟待解决的技术难题。技术实现要素:1.发明要解决的技术问题针对现有转炉工序中难以实现高效脱磷及溅渣护炉的技术难题,本发明拟提供一种转炉渣熔点控制模型的高效脱磷及护炉的方法,通过对转炉渣熔点的科学化把控,将高效脱磷以及高效护炉进行结合思考,将炉渣熔点通过模型控制,根据不同冶炼计划调控在一个合适的范围;促使炉渣熔点合适,流动性良好,既保证了前期的高效脱磷,又达到了高效护炉的目的。2.技术方案为达到上述目的,本发明提供的技术方案为:本发明的一种转炉渣熔点控制模型的高效脱磷及护炉的方法,按照以下过程进行:采集每一炉的转炉冶炼数据信息,并通过建立的熔点数据库指导出不同阶段的炉渣碱度和炉渣中氧化镁的含量,根据前期造渣制度模块计算出前期造渣材料加入及lf精炼渣加入的量化控制;根据终点成分控制模块计算出造渣材料总加入量的量化控制,以控制转炉炉渣熔点。更进一步地,采集的转炉冶炼数据信息包括转炉铁水成分、铁水温度、金属装入量、钢种终点目标成分与温度、各造渣材料的化学成分。更进一步地,前期造渣制度模块中包括前期总渣量的计算为:其中w1为转炉熔炼前期总渣量,kg;g铁、g废分别为转炉中铁水、废钢装入量,kg;r1为前期炉渣碱度,m1为前期炉渣中氧化镁的质量百分比;[si%]为铁水中硅含量百分比,[p%]为铁水中磷含量百分比;wsio2为留渣和铁水带入的sio2质量,kg。更进一步地,前期造渣制度模块中包括lf精炼渣加入量的计算为:其中,f(a)为精炼渣加入量,kg;[a%]为精炼渣中al2o3含量百分比。更进一步地,前期造渣制度模块中包括前期造渣材料加入量的计算为:其中,f(m3)为转炉中前期轻烧加入量,kg;f(c1)为转炉中前期石灰加入量,kg;wmgo为留渣、铁水中带入的mgo质量,kg;[mgo%]为轻烧中mgo含量百分比;wcao为留渣、铁水和前期轻烧中带入的cao质量,kg;[cao%]为石灰中cao含量百分比;[sio2%]为石灰中sio2含量百分比。更进一步地,终点成分控制模块包括转炉总渣量的计算为:其中,w为转炉总渣量,kg;g铁、g废分别为转炉中铁水、废钢装入量,kg;r2为终点炉渣碱度;m2为终点炉渣中氧化镁含量百分比;[si%]为铁水中硅含量百分比;wsio2为留渣、铁水带入的sio2质量,kg。更进一步地,终点成分控制模块包括总造渣材料加入量的计算为:其中,f(m)、f(c)分别为轻烧、石灰总加入量,kg;wmgo为留渣、铁水中带入的mgo质量,kg;[mgo%]轻烧中mgo含量百分比;w′cao为留渣、铁水和总加入轻烧带入的cao质量,kg;[cao%]为石灰中cao含量百分比;[sio2%]为石灰中sio2含量百分比。更进一步地,lf精炼渣的理化指标要求为:氧化钙含量不小于45%、氧化铝含量不小于25%以及粒度控制为15mm~35mm。更进一步地,控制前期炉渣熔点温度不大于1470℃,熔点数据库根据炉渣熔点指导出前期炉渣碱度r1和前期炉渣中氧化镁的含量百分比m1。更进一步地,定义出钢温度减去终点炉渣温度为温度差δt,控制15℃≤δt≤80℃,熔点数据库根据温度差指导出终点炉渣碱度r2和终点炉渣中氧化镁的含量百分比m2。3.有益效果采用本发明提供的技术方案,与现有技术相比,具有如下有益效果:(1)本发明的一种转炉渣熔点控制模型的高效脱磷及护炉的方法,通过合理、科学化的控制炉渣熔点与出钢温度之间的关系,给出不同冶炼时期渣系成分的合理控制以及加料模式的量化控制;促使炉渣熔点合适,流动性良好,既保证了前期的高效脱磷,又达到了缩短溅渣时间、高效护炉的目的。(2)本发明的一种转炉渣熔点控制模型的高效脱磷及护炉的方法,将lf精炼渣回转炉使用,造低熔点的复合渣系,促进前期化渣,达到高效脱磷的目的;又充分考虑高al2o3渣系,对溅渣护炉效果的影响;从而对精炼渣的加入量进行严格控制。通过系统模块的精确计算对精炼渣的加入量进行量化处理,进而减少了因操作的随意性,而带来的后续一系列的影响。附图说明图1是本发明中转炉渣熔点控制模型的结构示意图。示意图中的标号说明:10、数据获取模块;11、数据处理模块;12、熔点数据库模块;13、前期造渣制度模块;14、终点成分控制模块。具体实施方式为进一步了解本发明的内容,结合附图对本发明作详细描述。在本发明的描述中,需要说明的是,术语“中心”、“上”、“下”、“左”、“右”、“竖直”、“水平”、“内”、“外”等指示的方位或位置关系为基于附图所示的方位或位置关系,仅是为了便于描述本发明和简化描述,而不是指示或暗示所指的装置或元件必须具有特定的方位、以特定的方位构造和操作,因此不能理解为对本发明的限制。此外,术语“第一”、“第二”、“第三”仅用于描述目的,而不能理解为指示或暗示相对重要性。下面结合实施例对本发明作进一步的描述。实施例1本实施例的一种转炉渣熔点控制模型的高效脱磷及护炉的方法,其中所述的转炉渣熔点控制模型包括有数据获取模块10、数据处理模块11、熔点数据库模块12、前期造渣制度模块13和终点成分控制模块14,其中数据获取模块10用于采集和输入每一炉冶炼数据并将数据信息传递给数据处理模块11,数据处理模块11对上一级的数据加工得出供下一级模块使用的数据,熔点数据库模块12接收上一级数据并指导选择出合适的冶炼数据区间指导生产,最终通过前期造渣制度模块13和终点成分控制模块14和计算及相互弥补功能,促使炉渣熔点合适,化渣良好,实现高效脱磷和护炉的目的。本实施例的高效脱磷及护炉方法具体按照以下过程进行:采集每一炉的转炉冶炼数据信息,并通过建立的熔点数据库指导出炉渣碱度和炉渣中氧化镁的含量,根据前期造渣制度模块13计算出前期造渣材料加入及lf精炼渣加入的量化控制;根据终点成分控制模块14计算出造渣材料总加入量的量化控制,以控制转炉炉渣熔点。具体通过数据获取模块10采集信息,采集的转炉冶炼数据信息包括转炉铁水成分、铁水温度、金属装入量、钢种终点目标成分与温度、各造渣材料的化学成分。熔点数据库模块12为提前建立的熔点数据库,根据大量现场工业试验和实验室理论计算、热态试验等,拟合出不同组分转炉渣所对应的的炉渣熔点数据库,可以根据该提前建立的熔点数据库指导后续生产。本实施例中前期造渣制度模块13中包括前期总渣量的计算为:其中w1为转炉熔炼前期总渣量,kg;g铁、g废分别为转炉中铁水、废钢装入量,kg;r1为前期炉渣碱度,m1为前期炉渣中氧化镁的质量百分比;[si%]为铁水中硅含量百分比,[p%]为铁水中磷含量百分比;wsio2为留渣和铁水带入的sio2质量,kg。转炉熔炼过程包含前期、中期、终点等多个阶段,此为行业内公知常识,在此不再赘述,本实施例主要对转炉熔炼前期造渣和终点造渣进行精确有效控制。本实施例中控制前期炉渣熔点温度不大于1470℃,以使前期炉渣具备良好的化渣条件和流动性,从而有助于提高脱磷效率;熔点数据库根据该前期炉渣熔点指导出相对应的最佳前期炉渣碱度r1和前期炉渣中氧化镁的含量百分比m1的控制范围。本实施例中还需对精炼渣进行严格的量化控制,以减少因炉渣中al2o3含量高而对溅渣护炉效果产生影响;本实施例炉渣中al2o3含量控制在6%以内,具体地,前期造渣制度模块13中包括lf精炼渣加入量的计算为:其中,f(a)为精炼渣加入量,kg;[a%]为精炼渣中al2o3含量百分比。lf精炼渣的理化指标要求为:氧化钙含量不小于45%、氧化铝含量不小于25%以及粒度控制为15mm~35mm。本实施例中前期造渣制度模块13中包括前期主要造渣材料加入量的计算为:其中,f(m3)为转炉中前期(即第一批)轻烧加入量,kg;f(c1)为转炉中前期(即第一批)石灰加入量,kg;wmgo为留渣、铁水中带入的mgo质量,kg;[mgo%]为轻烧中mgo含量百分比;wcao为留渣、铁水和前期轻烧中带入的cao质量,kg;[cao%]为石灰中cao含量百分比;[sio2%]为石灰中sio2含量百分比。本实施例中终点成分控制模块14通过上一级冶炼成分的精确制导,通过继续运算得出造渣材料总加入量的量化控制,具体地,终点成分控制模块14包括转炉总渣量的计算为:其中,w为转炉总渣量,kg;g铁、g废分别为转炉中铁水、废钢装入量,kg;r2为终点炉渣碱度;m2为终点炉渣中氧化镁含量百分比;[si%]为铁水中硅含量百分比;wsio2为留渣、铁水带入的sio2质量,kg。本实施例中定义出钢温度减去终点炉渣温度(即终点炉渣熔点温度)为温度差δt,控制15℃≤δt≤80℃,以使终点炉渣具备高效脱磷及护炉的性能,熔点数据库根据温度差指导出适宜的终点炉渣碱度r2和终点炉渣中氧化镁的含量百分比m2控制范围。本实施例中终点成分控制模块包括总造渣材料加入量的计算为:其中,f(m)、f(c)分别为轻烧、石灰总加入量,kg;wmgo为留渣、铁水中带入的mgo质量,kg;[mgo%]轻烧中mgo含量百分比;w′cao为留渣、铁水和总加入轻烧带入的cao质量,kg;[cao%]为石灰中cao含量百分比;[sio2%]为石灰中sio2含量百分比。本实施例通过对转炉冶炼数据的采集,经过一系列的加工处理,计算得出转炉冶炼过程中石灰、轻烧的分批加入量以及lf精炼渣加入的量化控制,以控制转炉炉渣熔点在一个适宜范围内,实现前期的高效脱磷及重点高效护炉的目的。下面将结合具体案例进行说明。本实施例的一种转炉渣熔点控制模型的高效脱磷及护炉的方法,在河北永洋120吨顶底复吹转炉成功试验,通过熔点控制模型,达到高效脱磷护炉的具体过程为:将温度为1390℃的铁水105t兑入转炉,同时加入废钢25t,铁水成分为c:4.84%,si:0.42%,mn:0.25%,p:0.106%。本炉次生产计划要求:出钢温度1620±15℃,终点p≤0.025%。在转炉吹炼之前,获取以上数据;通过熔点数据库指导出前期碱度r1控制1.6~1.9,氧化镁含量百分比m1控制6%~8%;终点碱度r2控制2.7~3.0,氧化镁含量百分比m2控制7%~8%。通过公式:其中,f(a)为精炼渣加入量,kg;[a%]为精炼渣中al2o3含量百分比。经上计算可精确得出精炼渣的合理加入量。基于以上分析,通过系统模型指导造渣材料的加入,具体石灰、轻烧和精炼渣的分批加入如表1所示。通过试验过程取过程渣样和钢样的分析结果如表2所示。表1造渣材料的具体加入量(kg)石灰轻烧精炼渣第一批36002500740第二批11008000总量47003300740表2冶炼过程渣样与钢样的分析实施例2本实施例的一种转炉渣熔点控制模型的高效脱磷及护炉的方法,具体案例如下:在河北永洋120吨顶底复吹转炉成功试验,本实施例通过熔点控制模型,达到高效脱磷及护炉效果的具体过程为:将温度为1400℃的铁水118t兑入转炉,同时加入废钢18t,铁水成分为c:5.0%,si:0.25%,mn:0.23%,p:0.121%。本炉次生产计划要求:出钢温度1650±15℃,终点p≤0.025%。在转炉吹炼之前,获取以上数据;通过熔点数据库指导出前期碱度r1控制1.8~2.0,氧化镁含量百分比m1控制6%~8%;终点碱度r2控制3.0~3.2,氧化镁含量百分比m2控制7%~8%。通过公式:其中,f(a)为精炼渣加入量,kg;[a%]为精炼渣中al2o3含量百分比。经上可精确得出精炼渣的合理加入量。基于以上分析,通过系统模型指导造渣材料的加入,具体石灰、轻烧和精炼渣的分批加入如表3所示。通过试验过程取过程渣样和钢样的分析结果如表4所示。表3造渣材料的具体加入量(kg)石灰轻烧精炼渣第一批210017001040第二批140010000总量350027001040表2冶炼过程渣样与钢样的分析以上示意性的对本发明及其实施方式进行了描述,该描述没有限制性,附图中所示的也只是本发明的实施方式之一,实际的结构并不局限于此。所以,如果本领域的普通技术人员受其启示,在不脱离本发明创造宗旨的情况下,不经创造性的设计出与该技术方案相似的结构方式及实施例,均应属于本发明的保护范围。当前第1页1 2 3