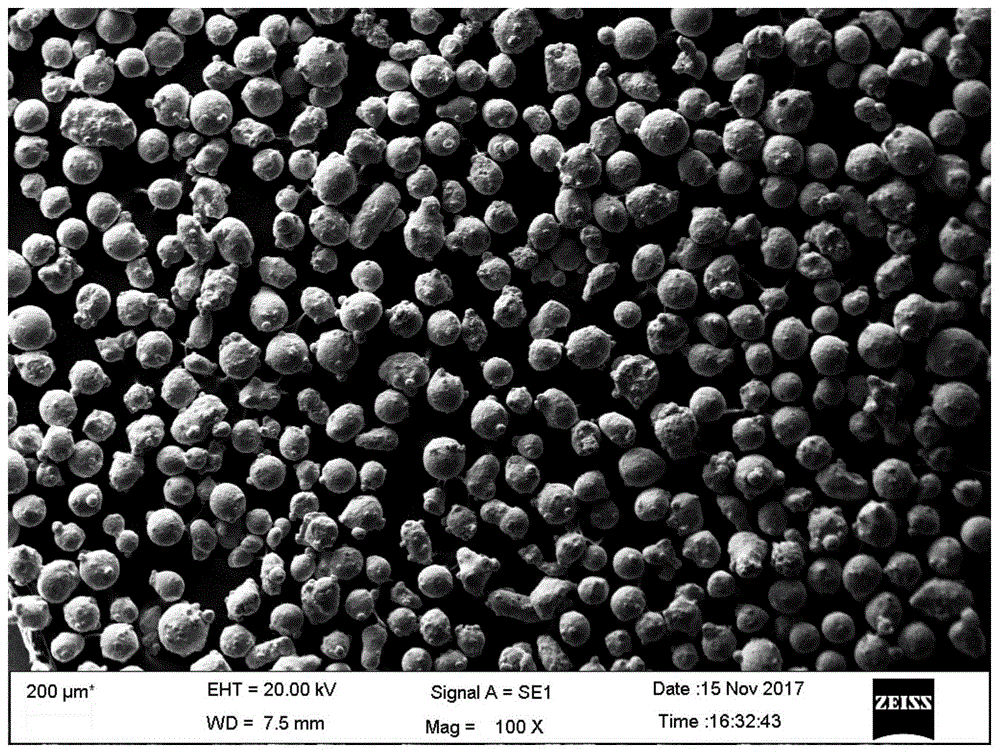
本发明涉及金属粉末研制
技术领域:
,具体而言,涉及一种铁硅铝金属粉末及其制备方法。
背景技术:
:铁硅铝(sendust)磁粉芯是一种改进型的铁硅铝材料,它被设计用代替铁粉芯,磁芯损耗更低,而且能量贮存能力比铁镍钼(mpp)磁粉芯还要高,是开关电源中能量贮存和滤波电感器用磁芯的理想选择。低的磁芯损耗性能可以使sendust铁硅芯比类似尺寸的纯铁粉芯在高频下具有更低的温升,同时它的直流偏磁场性能也比相近磁导率和尺寸的纯铁粉芯要好,耐电流性能好。铁硅铝磁粉芯由铁硅铝粉组成,主要成分为85%铁、9%硅、6%的铝。硫、磷等有害杂质少,含硅量高以保证低损耗高磁感的优良性能。为此炼钢操作要求高,对炼钢用原材料的纯净度要求也高。由于硅钢板在冶金厂生产中工序较多,有很多切头和边角料产生,同时在电器、电机行业使用时大多需要冲制或裁剪,故每年废弃的边角料相当可观,这些边角料大多与价格低廉的杂废一起作为炼钢原料投入转炉或电炉使用。由于大多钢种均采用高氧或者大气环境下进行冶炼,冶炼过程中有益元素硅基本烧损形成熔渣,造成了硅元素的极大浪费。而且高硅含量的熔渣粘度大,容易造成设备挂渣,后期熔渣再次资源化利用困难。鉴于此,特提出本发明。技术实现要素:本发明的目的在于提供一种铁硅铝金属粉末的制备方法,其将硅钢生产中的硅钢废料通过在真空感应熔炼炉内与铁芯、铝铁、高纯硅铁以及工业纯铁进行合理的位置布局,可在高温熔炼和雾化制粉作业过程中有效地避免出现硅钢废料无法融化的问题,从而有效地提高硅钢废料的转化率,以节约废钢资源,提高经济效益。本发明的另一目的在于提供一种铁硅铝金属粉末,其通过上述的制备方法制备得到。因此,其有效地利用硅钢生产中的硅钢废料可有效地提高硅钢生产中边角料的附加值,节约生产成本。本发明是这样实现的:第一方面,实施例提供一种铁硅铝金属粉末的制备方法,包括:将硅钢废料放入真空感应熔炼炉的炉体内的外围以形成废料圈;将铁芯放入炉体内,且置于硅钢废料所形成的废料圈内;在铁芯的下方布置高纯硅铁;在铁芯的上方依次布置铝铁和工业纯铁;对炉体依次进行高温熔炼和雾化制粉作业。在可选的实施方式中,各成分的加入量分别为按照重量百分比计的60~75%的硅钢废料、15~30%铁芯、3~10%高纯硅铁、1~10%铝铁以及10~21%的工业纯铁。在可选的实施方式中,铁芯的材质为q235材质棒材,且其铝含量不能超过3%,直径为5~10mm。在可选的实施方式中,高纯硅铁硅含量为45%以上,碳含量低于1%,杂质元素低于2%,余量为铁。在可选的实施方式中,硅钢废料为硅钢卷通过剪板机剪裁后得到的边角余料与废料;且硅钢废料的长度为20~70mm,宽度为5~10mm。在可选的实施方式中,对炉体进行高温熔炼的步骤具体包括:依次进行抽真空处理和升温熔炼处理后制得钢水;其中,抽真空处理为将炉体内的真空度抽至20pa,升温熔炼处理是在抽真空之后开始升温,且熔炼曲线为0~30min,温度升到600℃;30~40min,600℃恒温;40~60min,温度升到1200℃;60~65min,1200℃恒温;65~90min,温度升到1600℃;然后继续升温至铁硅铝材料熔点50℃以上。在可选的实施方式中,升温熔炼处理之后还包括将钢水倒入保温中间包内进行保温处理,且保温中间包温度控制为1800~1900℃,保温时间控制在5min以内。在可选的实施方式中,对炉体进行雾化制粉的步骤具体包括:调整好雾化喷嘴压力,并开启雾化制粉装置,在压力作用下,将保温后的钢水在雾化喷嘴3~6mpa的压力作用下喷出,以制成铁硅铝粉末。在可选的实施方式中,在经过雾化喷嘴制成粉末后还包括通过气体分级装置分别将不同粒度的铁硅铝粉末进行收集,并且分别进行真空密封。第二方面,实施例提供一种铁硅铝金属粉末,通过前述实施方式中任一项的铁硅铝金属粉末的制备方法制备得到。本发明的实施例至少具备以下优点或有益效果:本发明的实施例提供了一种铁硅铝金属粉末的制备方法,其包括将硅钢废料放入真空感应熔炼炉的炉体内的外围以形成废料圈;将铁芯放入炉体内,且置于硅钢废料所形成的废料圈内;在铁芯的下方布置高纯硅铁;在铁芯的上方依次布置铝铁和工业纯铁;对炉体依次进行高温熔炼和雾化制粉作业。该方法一方面通过高温处理的方式,可有效地将硅钢废料外层的绝缘涂层进行熔化,以保证硅钢废料在熔炼和雾化制粉作业过程中的成品率,以提高硅钢生产中的硅钢废料的附加值。另一方面该方法将硅钢废料设置于炉体的外圈,将铁芯放入废料圈的中部,然后将高纯硅铁放置于铁芯的下方,将铝铁和工业纯铁设置于铁芯的上方,使得熔炼过程中各成分的接触面积以及作用空间得到有效地保障,使得铁芯可在涡流效应下由于电磁感应而进行有效地导电作业,以进一步地提高硅钢废料的转化率,保证其成品率,节约废钢资源以提高经济效益。本发明的实施例提供的铁硅铝金属粉末,其通过上述的制备方法制备得到。因此,其有效地利用硅钢生产中的硅钢废料进行生产而得到,可有效地提高硅钢生产中边角料的附加值,节约生产成本。附图说明为了更清楚地说明本发明实施例的技术方案,下面将对实施例中所需要使用的附图作简单地介绍,应当理解,以下附图仅显示本发明的某些实施例,因此不应被看作是对范围的限定,对于本领域普通技术人员来讲,在不付出创造性劳动的前提下,还可以根据这些附图获得其他相关的附图。图1为本发明的实施例1提供的fesial粉末微观结构图;图2为本发明的实施例2提供的fesial粉末微观结构图。具体实施方式为使本发明实施例的目的、技术方案和优点更加清楚,下面将对本发明实施例中的技术方案进行清楚、完整地描述。实施例中未注明具体条件者,按照常规条件或制造商建议的条件进行。所用试剂或仪器未注明生产厂商者,均为可以通过市售购买获得的常规产品。以下结合实施例对本发明的特征和性能作进一步的详细描述。本发明的实施例提供了一种铁硅铝金属粉末的制备方法,其包括将硅钢废料放入真空感应熔炼炉的炉体内的外围以形成废料圈;将铁芯放入炉体内,且置于硅钢废料所形成的废料圈内;在铁芯的下方布置高纯硅铁;在铁芯的上方依次布置铝铁和工业纯铁;对炉体依次进行高温熔炼和雾化制粉作业。详细地,由于硅钢废料的外表面通常涂有绝缘涂层,绝缘涂层包括有机成分以及无机成分,其中有机成分在通常条件下不易分解,导致涡流被限制在狭小的薄片之间,回路的电阻很大,涡流便大为减小,电流集肤效应与热效应降低,容易出现硅钢小板条无法熔化的现象。因此,在本实施例中,该方法一方面通过高温处理的方式,可有效地将硅钢废料外层的绝缘涂层表面的有机成分进行熔化,以保证硅钢废料在熔炼和雾化制粉作业过程中的成品率,以提高硅钢生产中的硅钢废料的附加值。另一方面,由于现有技术中硅钢废料在制备过程中硅钢废料存在转化率低,成品率较低的技术问题。该方法在保证高温熔炼条件的基础之上,将硅钢废料设置于炉体的外圈,将铁芯放入废料圈的中部,然后将高纯硅铁放置于铁芯的下方,将铝铁和工业纯铁设置于铁芯的上方,使得高温熔炼过程中各成分的接触面积以及作用空间得到有效地保障,使得铁芯可在涡流效应下由于电磁感应而进行有效地导电作业,以进一步地提高硅钢废料的转化率,保证其成品率,节约废钢资源以提高经济效益。需要说明的是,在本发明的实施例中,各成分的加入量分别为按照重量百分比计的60~75%的硅钢废料、15~30%铁芯、3~10%高纯硅铁、1~10%铝铁以及10~21%的工业纯铁。将各成分用量控制在该范围内,使得对应用量的硅钢废料可得到最大程度化的转化,使得其他成分用量得到有效地控制,从而节约制备成本,保证制备后的粉末的成品率。作为优选的方案,可以将高纯硅铁的用量控制在8%、铝铁的用量控制在5%,以进一步地保证各成分的转化率,以节约制备成本。当然,在本发明的其他实施例中,各成分的用量还可以根据需求进行调整,本发明的实施例不做限定。另外,在本发明的实施例中,选用的铁芯的材质为q235材质棒材,且其铝含量不能超过3%,直径为5~10mm。通过铁芯的设置,可有效地作为助熔剂,可进一步地避免硅钢废料无法熔化的现象出现。本发明的实施例选用的高纯硅铁硅含量为45%以上,碳含量低于1%,杂质元素低于2%,余量为铁。选用的硅钢废料通过硅钢生产过程中的硅钢钢卷通过剪板机剪裁后得到;且硅钢废料的长度为20~70mm,宽度为5~10mm。通过控制硅钢废料的尺寸,使得在真空感应熔炼炉的炉体内的硅钢废料与其他成分的接触面积以及作用面积得到扩大,从而有效地保证铁硅铝的成品率。同时,在本发明的实施例中,采用的工业纯铁为工业纯铁棒,要求工业纯铁棒表面使用砂轮打磨,表面光亮呈金属光泽,无锈层。还需要说明的是,在本发明的实施例中,对炉体进行高温熔炼的步骤具体包括:依次进行抽真空处理和升温熔炼处理后制得钢水。详细地,抽真空处理为将炉体内的真空度抽至20pa,升温熔炼处理是在抽真空之后开始升温,且熔炼曲线为0~30min,温度升到600℃;30~40min,600℃恒温;40~60min,温度升到1200℃;60~65min,1200℃恒温;65~90min,温度升到1600℃;然后继续升温至铁硅铝材料熔点50℃以上。在此过程中通过将温度的控制使得硅钢废料表面的绝缘涂层的有机成分得到有效地熔化,从而便于提高铁硅铝金属粉末的制备效率。当然,在本发明的其他实施例中,抽真空处理以及升温熔炼处理的真空参数以及温度参数还可以根据需求进行选择和处理,本发明的实施例不做限定。作为优选的方案,升温熔炼处理之后还包括将钢水倒入保温中间包内进行保温处理,且保温中间包温度控制为1800~1900℃,保温时间控制在5min以内。通过保温处理,使得钢水的温度得到有效地保证,从而便于通过雾化喷雾进行制粉作业。其中,对炉体进行雾化制粉的步骤具体包括调整好雾化喷嘴压力,并开启雾化制粉装置,在压力作用下,将保温后的钢水在雾化喷嘴3~6mpa的压力作用下喷出,以制成铁硅铝粉末。然后,在经过雾化喷嘴制成粉末后还包括通过气体分级装置分别将不同粒度的铁硅铝粉末进行收集,并且分别进行真空密封。需要说明的是,本发明的实施例所采用的雾化喷嘴的优选压力为5mpa,通过对压力的控制使得雾化制粉所喷出的粉末的均匀性得到保障,同时使得粉末中的硅含量得到有效地控制,从而提高成品质量。当然,在本发明的其他实施例中,各参数还可以根据需求进行调整,本发明的实施例不做限定。本发明的实施例还提供一种铁硅铝金属粉末,通过前述实施方式中任一项的铁硅铝金属粉末的制备方法制备得到。因此,其有效地利用硅钢生产生中的硅钢废料进行生产而得到,可有效地提高硅钢生产中边角料的附加值,节约生产成本。下面结合具体实施例对上述的制备过程进行详细地说明。实施例1如图1所示,本实施例提供了一种铁硅铝金属粉末,其通过以下方法制备得到:s1:将35kg的硅钢废料放入真空感应熔炼炉的炉体内的外围以形成废料圈;s2:将9kg的铁芯放入炉体内,且置于硅钢废料所形成的废料圈内;s3:在铁芯的下方布置2kg的高纯硅铁;s4:在铁芯的上方依次布置1kg的铝铁和12kg的工业纯铁;s5:打开真空雾化设备的真空感应熔炼控制装置,先抽真空至真空度为20pa;s6:开始升温熔炼,且熔炼曲线为0~30min,温度升到600℃;30~40min,600℃恒温;40~60min,温度升到1200℃;60~65min,1200℃恒温;65~90min,温度升到1600℃;然后继续升温至铁硅铝材料熔点50℃以上;s7:升温结束后,将钢水倒入保温中间包内,保温中间包温度控制为1800~1900℃;钢水在中间包保温时间为5分钟以内;s8:调整好雾化喷嘴压力,并开启雾化制粉装置,在压力作用下,保温中间包内钢水流出,在雾化喷嘴5mpa的压力作用下,制成粉末。实施例2如图2所示,本实施例提供了一种铁硅铝金属粉末,其通过以下方法制备得到:s1:将36kg的硅钢废料放入真空感应熔炼炉的炉体内的外围以形成废料圈;s2:将9kg的铁芯放入炉体内,且置于硅钢废料所形成的废料圈内;s3:在铁芯的下方布置2kg的高纯硅铁;s4:在铁芯的上方依次布置1.5kg的铝铁和10.5kg的工业纯铁;s5:打开真空雾化设备的真空感应熔炼控制装置,先抽真空至真空度为20pa;s6:开始升温熔炼,且熔炼曲线为0~30min,温度升到600℃;30~40min,600℃恒温;40~60min,温度升到1200℃;60~65min,1200℃恒温;65~90min,温度升到1600℃;然后继续升温至铁硅铝材料熔点50℃以上;s7:升温结束后,将钢水倒入保温中间包内,保温中间包温度控制为1800~1900℃;钢水在中间包保温时间为5分钟以内;s8:调整好雾化喷嘴压力,并开启雾化制粉装置,在压力作用下,保温中间包内钢水流出,在雾化喷嘴5mpa的压力作用下,制成粉末。实验例1将实施例1和2制备得到的铁硅铝金属粉末的成分进行分析,成分如表1和表2。表1.实施例1提供的fesial粉末金属粉末成分表csialpfe0.01%8.5%6%0.015%84%表2.实施例1提供的fesial粉末金属粉末成分表csialpfe0.01%8%6.5%0.015%85%根据表1和表2以及图1和图2的显示结果可知,本发明的实施例所制备得到的铁硅铝金属粉末中的硅含量得到有效地控制。同时,其制备过程中,该方法一方面通过高温处理的方式,可有效地将硅钢废料外层的绝缘涂层进行熔化,以保证硅钢废料在熔炼和雾化制粉作业过程中的成品率,以提高硅钢生产中的硅钢废料的附加值。另一方面该方法将硅钢废料设置于炉体的外圈,将铁芯放入废料圈的中部,然后将高纯硅铁放置于铁芯的下方,将铝铁和工业纯铁设置于铁芯的上方,使得熔炼过程中各成分的接触面积以及作用空间得到有效地保障,使得铁芯可在涡流效应下由于电磁感应而进行有效地导电作业,以进一步地提高硅钢废料的转化率,保证其成品率,节约废钢资源以提高经济效益。综上所述,本发明的实施例提供的铁硅铝金属粉末的制备方法,其将硅钢生产中的硅钢废料通过在真空感应熔炼炉内与铁芯、铝铁、高纯硅铁以及工业纯铁进行合理的位置布局,可在高温熔炼和雾化制粉作业过程中有效地避免出现硅钢废料无法融化的问题,从而有效地提高硅钢废料的转化率,以节约废钢资源,提高经济效益。本发明的实施例提供的铁硅铝金属粉末,其通过上述的制备方法制备得到。因此,其有效地利用硅钢生产生中的硅钢废料进行生产而得到,可有效地提高硅钢生产中边角料的附加值,节约生产成本。以上所述仅为本发明的优选实施例而已,并不用于限制本发明,对于本领域的技术人员来说,本发明可以有各种更改和变化。凡在本发明的精神和原则之内,所作的任何修改、等同替换、改进等,均应包含在本发明的保护范围之内。当前第1页12