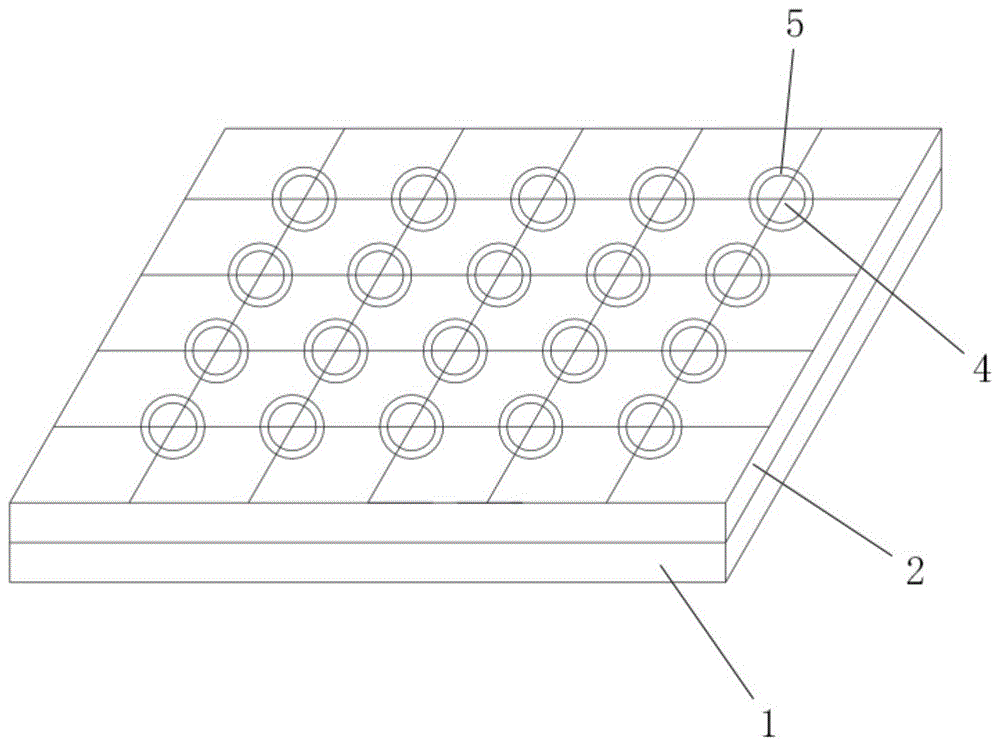
本发明涉及气门导管
技术领域:
,具体涉及一种气门导管材料、气门导管和装置。
背景技术:
:随着涡轮增压、稀薄燃料、缸内直喷发动机的应用与推广,气门导管的工作温度越来越高,普通粉末冶金气门导管在高温下材料容易发生塑性流动,磨损较快,导热性不好。现有技术中的气门导管未针对高温环境进行优化,难以应用在高温发动机上;较为先进的现有技术中会对气门导管进行渗铜处理,但均为单方向渗铜,渗铜不均匀,整体效果差。技术实现要素:为解决上述技术问题,本发明提供一种气门导管材料、气门导管和装置。为解决上述技术问题,本发明采用如下技术方案:一种气门导管的材料,包含有下述质量配比的元素原料:c:0.6-1.5%、cu:10.0-20.0%、mo:1.0-3.0%、s:0.2-1.2%、ni:0.2~1.0%、fe:余量。具体地,包含有下述质量配比的元素原料:c:0.9-1.2%、cu:14.0-16.0%、mo:1.5-2.5%、s:0.4-0.8%、ni:0.4~0.8%、fe:余量。一种气门导管,使用上述气门导管材料制备而成。一种用于生产气门导管的装置,包括下碳板以及悬置在下碳板之上的上碳板,所述下碳板的上表面开设有下安装孔,所述上碳板的下表面开设有与下安装孔在竖直方向上一一对应的上安装孔,所述下安装孔内设置有下铜片且所述上安装孔内设置有上铜片;所述气门导管的下端伸入到下安装孔内并与下铜片接触,且上端伸入到上安装孔内并与上铜片接触。进一步地,还包括底部碳板,所述上安装孔和下安装孔均为通孔,所述下碳板放置在底部碳板之上。进一步地,所述底部碳板、下碳板以及上碳板的各对应边缘在竖直方向上对齐。进一步地,还包括放置在下碳板四个拐角处的碳柱,所述碳柱的顶部与上碳板的下表面顶紧接触。进一步地,所述上铜片的质量与下铜片的质量相同。与现有技术相比,本发明的有益技术效果是:1.在气门导管的两端进行渗铜处理,渗铜均匀,效果比单方向渗铜更好,能够有效填充气门导管金相组织的部分孔隙,所得气门导管的密度、硬度、压溃强度等力学性能显著提高,渗铜后,气门导管金相组织中铁素体减少,马氏体、贝氏体等耐磨相增多,能够提高高温环境下气门导管的耐磨性。附图说明图1为本发明整体的结构示意图;图2为本发明气门导管的结构示意图;图3为上碳板的结构示意图;图4为渗铜前气门导管的金相组织图;图5为渗铜后的金相组织图。具体实施方式下面结合附图对本发明的一种优选实施方式作详细的说明。随着涡轮增压、稀薄燃料、缸内直喷发动机的应用与推广,气门导管的工作温度越来越高,普通粉末冶金气门导管在高温下材料容易发生塑性流动,磨损较快。本发明具体涉及一种气门导管材料、气门导管和装置,能够对气门导管双端渗铜,渗铜效率高,渗铜均匀,能够有效填充气门导管金相组织的部分孔隙;铜具有良好的导热性,使得渗铜后的气门导管能够应用于高温环境中;且各元素相互配合,使得最终产品的金相组织中,耐磨相增多,铁素体减少。c元素融入fe中起固溶强化作用,提高材料的强度、硬度和耐磨性。本发明中,c的典型但非限制性质量配比为:0.6%、0.8%、1.0%、1.2%或1.5%。cu元素能够填充粉末冶金件中的孔隙,提高产品强度与韧性;能够提高导热性并改善机加工性能。本发明中,cu的典型但非限制性质量配比为:10.0%、11.0%、12.0%、13.0%、14.0%、15.0%、16.0%、17.0%、18.0%、19.0%或20.0%。mo元素一方面能够提高气门导管的强度、硬度和耐磨性;另一方面能够提高气门导管的热稳定性。本发明中,mo的典型但非限制性质量配比为:1.0%、1.5%、2.0%、2.5%或3.0%。s元素能够气门导管机加工性能。本发明中,s的典型但非限制性质量配比为:0.2%、0.4%、0.6%、0.8%、1.0%或1.2%。ni元素能够提高产品的强度、韧性和耐磨性,并能够提高其抗腐蚀能力。本发明中,ni的典型但非限制性质量配比为:0.2%、0.4%、0.6%、0.8%或1.0%。下面结合具体实施例对本发明的技术方案作详细的说明。实施例1实施例1提供的气门导管材料,包含有下述质量配比的元素原料:c:1.1%、cu:15.0%、mo:2.0%、s:0.65%、ni:0.62%、fe:余量。制作步骤如下:(1)按比例对原材料粉末进行称量、混合;(2)在压机上将混合好的粉末进行压制成型,同时压制渗铜用铜片;(3)将导管成型毛坯与渗铜用铜片在烧结炉中进行双端渗铜处理;(4)用液氮对烧结毛坯进行深冷处理;(5)热处理炉中对冷处理后的毛坯进行热处理;(6)无心磨床粗磨外圆;(7)数控车床加工头部与尾部;(8)外圆精磨(9)浸油包装。实施例2实施例2提供的气门导管材料,包含有下述质量配比的元素原料:c:0.6%、cu:10.0%、mo:3.0%、s:1.2%、ni:1.0%、fe:余量。制作步骤如下:(1)按比例对原材料粉末进行称量、混合;(2)在压机上将混合好的粉末进行压制成型,同时压制渗铜用铜片;(3)将导管成型毛坯与渗铜用铜片在烧结炉中进行双端渗铜处理;(4)用液氮对烧结毛坯进行深冷处理;(5)热处理炉中对冷处理后的毛坯进行热处理;(6)无心磨床粗磨外圆;(7)数控车床加工头部与尾部;(8)外圆精磨(9)浸油包装。实施例3实施例3提供的气门导管材料,包含有下述质量配比的元素原料:c:1.5%、cu:20.0%、mo:1.0%、s:0.2%、ni:0.2%、fe:余量。制作步骤如下:(1)按比例对原材料粉末进行称量、混合;(2)在压机上将混合好的粉末进行压制成型,同时压制渗铜用铜片;(3)将导管成型毛坯与渗铜用铜片在烧结炉中进行双端渗铜处理;(4)用液氮对烧结毛坯进行深冷处理;(5)热处理炉中对冷处理后的毛坯进行热处理;(6)无心磨床粗磨外圆;(7)数控车床加工头部与尾部;(8)外圆精磨(9)浸油包装。对比例1对比例1提供的气门导管材料,包含有下述质量配比的元素原料:c:0.5%、cu:22.0%、mo:0.8%、s:0.1%、ni:0.1%、fe:余量。制作步骤与实施例1相同。对比例2对比例2提供的气门导管材料,包含有下述质量配比的元素原料:c:1.6%、cu:9.0%、mo:3.5%、s:1.5%、ni:1.2%、fe:余量。制作步骤与实施例1相同。对比例3对比例3提供的气门导管材料,包含有下述质量配比的元素原料:c:1.1%、mo:2.0%、s:0.65%、ni:0.62%、fe:余量。制作步骤如下:(1)按比例对原材料粉末进行称量、混合;(2)在压机上将混合好的粉末进行压制成型;(3)将成型毛坯在烧结炉中进行高温烧结;(4)无心磨床粗磨外圆;(5)数控车床加工头部与尾部;(6)外圆精磨(7)浸油包装。即对比例3中的气门导管未进行渗铜处理。对比例4对比例4提供的气门导管材料,包含有下述质量配比的元素原料:c:1.1%、cu:15.0%、mo:2.0%、s:0.65%、ni:0.62%、fe:余量。制作步骤如下:(1)按比例对原材料粉末进行称量、混合;(2)在压机上将混合好的粉末进行压制成型,同时压制渗铜用铜片;(3)将导管毛坯与渗铜用铜片在烧结炉中进行单端渗铜处理;(4)用液氮对烧结毛坯进行深冷处理;(5)热处理炉中对冷处理后的毛坯进行热处理;(6)无心磨床粗磨外圆;(7)数控车床加工头部与尾部;(8)外圆精磨(9)浸油包装。对上述实施例和对比例进行耐磨性试验。试验条件:温度为300℃,转数为1000rpm,试验时间为10小时,试验设备为导管摩擦试验机。试验结果如下:实施例1实施例2实施例3对比例1对比例2对比例3对比例4导管内圆磨损量/mm0.0740.0890.0830.1050.1180.1750.129气门杆磨损量/mm0.0050.0040.0070.0060.0050.0060.004总磨损量/mm0.0790.0930.0900.1110.1230.1810.133密度平均值/(g/cm3)7.4957.2857.5127.5357.3856.7047.245硬度平均值/hrb113.2109.3115.3116.4108.585.3114/87压溃强度平均值/mpa815765825831756622.5689参照对比例3和实施例1,与未进行渗铜的气门导管进行比较,双端渗铜气门导管的耐磨性提升了一倍以上、密度平均值提高了约11.8%、硬度平均值提高了约32.7%、压溃强度平均值提高了约31%。参照对比例4和实施例1,与单端渗铜的气门导管进行比较,双端渗铜气门导管的耐磨性提升了40.6%、密度平均值提高了约3.5%、硬度平均值提高了约12.1%、压溃强度平均值提高了约18.3%。参照对比例1-2以及实施例1-3,当气门导管的材料,包含有下述质量配比的元素原料时:c:0.6-1.5%、cu:10.0-20.0%、mo:1.0-3.0%、s:0.2-1.2%、ni:0.2~1.0%、fe:余量,其耐磨性更好,密度、硬度以及压溃强度更高;可以满足采用了涡轮增压、稀薄燃烧、缸内直喷等技术的高性能发动机的要求。对气门导管进行双端渗铜时,可以借助下述的装置,渗铜效率高,渗铜均匀;铜具有良好的导热性,使得渗铜后的气门导管能够应用于高温环境中;最终产品的金相组织中,耐磨相增多,铁素体减少。如图1-3所示,一种用于生产气门导管的装置,包括下碳板2以及悬置在下碳板之上的上碳板8,所述下碳板的上表面开设有下安装孔5,所述上碳板的下表面开设有与下安装孔在竖直方向上一一对应的上安装孔9,所述下安装孔内设置有下铜片4且所述上安装孔内设置有上铜片10;所述气门导管的下端伸入到下安装孔内并与下铜片接触,且上端伸入到上安装孔内并与上铜片接触。上铜片与气门导管的上端紧密接触,下铜片与气门导管的下端紧密接触,能够提升渗铜的效果。与单端渗铜相比,双端渗铜能够提高渗铜的均匀性;且双端渗铜后,气门导管的两端性能相同,进行机械加工时无需用专门的工艺或设备对气门导管的渗铜端进行判断,能够提高气门导管后续的机加工效率。如图1所示,还包括底部碳板1,所述上安装孔9和下安装孔5均为通孔,所述下碳板2放置在底部碳板之上。如图1和2所示,所述底部碳板1、下碳板2以及上碳板8的各对应边缘在竖直方向上对齐;能够提高装置的稳定性,避免操作过程中各部件彼此脱离。如图2所示,还包括放置在下碳板四个拐角处的碳柱7,所述碳柱的顶部与上碳板8的下表面顶紧接触。如图3所示,所述上铜片10的质量与下铜片4的质量相同;上铜片和下铜片的质量相同,使得气门导管两端的渗铜量相同,气门导管各部位的性能具有一致性。本发明的渗铜流程如下:根据气门导管的外径大小,确定下安装孔、上安装孔的孔径以及各安装孔之间的孔距;准备好粉末冶金成型后的气门导管,并计算所需上铜片和下铜片的质量;将打好孔的下碳板放置到底部碳板上,边缘对齐;将下铜片放置到下安装孔内,将气门导管的下端插入到下安装孔内;在下碳板的四个拐角处各放置一个碳柱,将上碳板搁置在碳柱上,并使得气门导管的上端插入上安装孔内,上碳板、下碳板以及底部碳板的边缘对齐;将上铜片穿过上安装孔放置到气门导管的上表面;将上述组装体放入烧结炉中烧结,完成渗铜。图4为未进行渗铜的气门导管的金相组织,图5为渗铜后的气门导管的金相组织,对比可发现,气门导管中大部分孔隙被铜充填,渗铜后的铁素体减少,马氏体、贝氏体等耐磨相增多。对于本领域技术人员而言,显然本发明不限于上述示范性实施例的细节,而且在不背离本发明的精神或基本特征的情况下,能够以其他的具体形式实现本发明。因此无论从哪一点来看,均应将实施例看作是示范性的,而且是非限制性的,本发明的范围由所附权利要求而不是上述说明限定,因此旨在将落在权利要求的等同要件的含义和范围内的所有变化囊括在本发明内,不应将权利要求中的任何附图标记视为限制所涉及的权利要求。此外,应当理解,虽然本说明书按照实施方式加以描述,但并非每个实施方式仅包含一个独立技术方案,说明书的这种叙述方式仅仅是为了清楚起见,本领域技术人员应当将说明书作为一个整体,各实施例中的技术方案也可以经适当组合,形成本领域技术人员可以理解的其他实施方式。当前第1页12