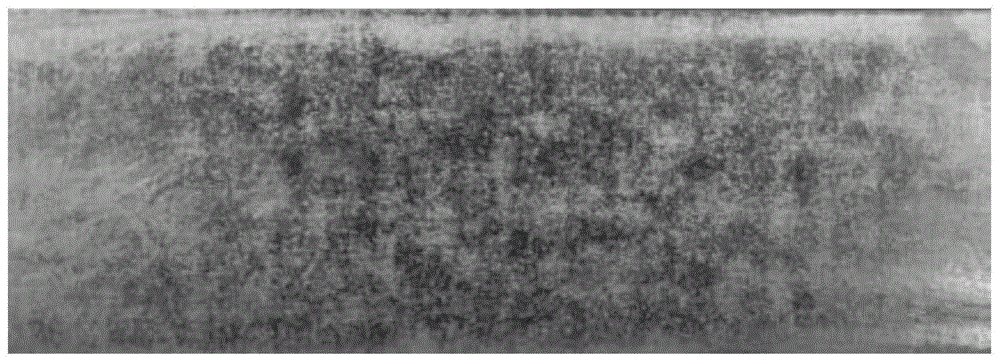
本发明属于汽车车身用铝合金板材
技术领域:
,涉及一种汽车车身外板用6系铝合金板材及其制备方法,尤其涉及一种包边性能优良和冲压后高表面质量的6系铝合金板材及其制备方法。
背景技术:
:随着世界各国汽车保有量的持续增长,燃油消耗及其废气污染在日益加剧,汽车制造商不得不将降低燃料消耗和限制汽车尾气排放列为汽车发展的重要目标之一。车身轻量化是实现这一目标的有效途径,因此,近年来铝合金作为轻质材料在车身上的应用越来越受到青睐。目前汽车车身外板类专利的研究焦点大多集中在提高烤漆硬化性能和冲压成形性上,例如专利公开号为cn100419116c的发明专利《改善6111铝合金汽车板成形性及烤漆硬化性预热处理工艺》和专利公开号为cn1141958a的发明专利《成型性和加热硬化性优良的铝合金板材的制造方法》都是针对成型性和加热硬化性两方面进行了改进。此外相比而言,几大系列铝合金中的6系铝合金,即al-mg-si系合金,具有强度适中、可热处理强化、耐蚀性好的特点,而且该系合金在固溶处理后具有较低屈服强度的状态下供货,使得合金板材具有较好的冲压成形能力,并能在最终的烤漆过程中获得进一步强化。这些特点使得该系合金非常适合应用于汽车车身外板的加工,而且目前已经有几个牌号的合金获得广泛应用,如6016,6111以及6022等。但目前在实际应用中这些合金都或多或少的存在着包边性能差,冲压后表面存在明显罗平线缺陷等问题,影响了6000系汽车板的大规模推广应用。技术实现要素:有鉴于此,本发明为了解决现有工艺制备的6系铝合金板材包边性能和冲压后表面质量达不到生产要求,影响汽车车身外板大规模推广应用的问题,提供一种汽车车身外板用6系铝合金板材及其制备方法。为达到上述目的,本发明提供汽车车身外板用6系铝合金板材,由以下元素组分按照重量百分比配制而成:si:0.55~0.65%、fe:0.10~0.20%、cu:0.10~0.20%、mn:0.05~0.15%、mg:0.65~0.75%、ti:0.01~0.03%、单个杂质≤0.03%,杂质合计≤0.10%,余量为al。进一步,为降低碱性金属的有害影响,杂质中碱金属含量:na≤10ppm,ca≤8ppm,li≤15ppm。一种汽车车身外板用6系铝合金板材的制备方法,包括如下步骤:a、将制备汽车车身外板的铝合金原料按照重量百分比进行配料,将配制好的铝合金原料置于熔炼炉中熔炼为液态铝合金,将熔炼后的铝合金熔体倒入精炼炉中精炼,精炼后的铝合金熔体经除气除杂、在线细化后熔铸为铝合金铸锭;b、将熔铸后的铝合金铸锭切去头尾并铣去铝合金铸锭表面凝壳层;c、将铝合金铸锭在加热炉中进行均匀化热处理,均匀化热处理的工艺为:铝合金铸锭先升温至560℃保温12h,然后降温至530℃保温2~12h出炉;d、将均匀化后铝合金铸锭3min内进入粗轧工序,粗轧道次不多于18次,粗轧完成时间在10min内,粗轧后中间坯厚度50~55mm,然后进行4连式精轧工序,精轧总压下率>80%,最终精轧下线卷坯厚度10mm,卷坯温度为350~370℃,自然冷却至室温;e、冷轧:将热轧后的铝合金板材冷轧至1.0mm,依次经过7.5mm、6.0mm、4.0mm、2.8mm、1.9mm、1.3mm、1.0mm,其中在冷轧至6.0mm时的铝合金板材在380℃的燃气循环加热箱式退火炉退火2h且退火前冷轧压下率为40%,冷轧至2.8mm时的铝合金板材在480℃的气垫式加热炉退火20s且退火前冷轧压下率为53%,退火后冷轧压下率为64%;f、将冷轧后的铝合金板材进行固溶处理,升温速率不小于5℃/s,升温至570℃保温30s后进行水淬,水淬后铝合金板材温度不高于150℃,然后风冷至室温;g、将固溶淬火后铝合金板材立即进行预时效处理,间隔时间不超过30s,使用连续通过式气垫加热炉进行,保证预时效后打卷温度为80~100℃,预时效后铝合金板材转移至20~25℃仓储环境冷却到室温。进一步,步骤a中铝合金原料采用回收铝、工业纯铝、工业纯mg、工业纯zn、中间合金al-si、中间合金al-cu、中间合金al-fe、中间合金al-mn。进一步,步骤a中铝合金原料熔炼温度为700~760℃,融化过程中开启电磁搅拌,精炼温度为720~740℃,使用cl-ar混合气体进行精炼并调整合金成分,成分合格后通过al-ti-b丝细化剂细化后进行扁锭半连续铸造,获得630mm*2150mm*6000mm尺寸的6系铝合金梯形扁锭。进一步,步骤b中铝合金铸锭引头端至少切除200mm,浇口端至少切除100mm,大面单面至少铣10mm,小面斜面至少铣5mm,小面立面至少铣5mm。进一步,步骤c中加热炉为推进式燃气加热炉。进一步,步骤f固溶淬火所使用的加热炉为气垫式加热炉。本发明的有益效果在于:1、包边工艺是将外板零件由冲压产生的下翻边通过折弯压平后,使内外板零件连接在一起的装配工艺。包边性能其实就是弯曲性能,在影响板材包边性能的诸多因素里,金属间化合物的形状、大小和数量起着很关键的作用,形状尖锐的大块金属间化合物往往由于剪切应力大,成为包边过程中的裂纹源,使包边性能大大下降。在6000系铝合金中均匀化热处理后合金中主要存在不可溶的al(femn)si、mg2si和al15mn3si2等金属间化合物,当然合金基体内必然还存在一定数量细小的亚微米或纳米级弥散粒子。为了减少板条状的al15mn3si2和al(femn)si的尺寸和数量,本发明对成分中mg和si元素的比例关系,以及fe和mn的含量进行了严格的限制,另一方面为了有效减少这些金属间化合物在高温热粗轧过程中发生的析出、聚集和长大行为,本发明对热粗轧的轧制道次和工序时间首次进行了严格的限制。本发明最终获得的成品与传统的6016合金相比包边性能有了明显的改善。2、6000系铝合金冲压后表面产生的罗平线缺陷主要是由于沿着轧制方向的再结晶织构和高斯织构的异常排列造成。当具有立方或高斯取向的晶粒沿着轧制方向分布排列并在垂直方向中交替分布时,如果在垂直方向拉伸板材时会出现罗平线。颗粒刺激形核机制(psn机制)认为大于1μm的硬质第二相可以促进再结晶形核时p织构的发展,对于降低再结晶织构和高斯织构的异常排列颇有益处。本发明为了改善成品的织构比例和分布,降低和优化成品中的晶粒取向,创造性地联合采取了三项措施:第一,在保证热轧坯料表面质量的情况下,采用较大的精轧变形率和较高的精轧下线卷坯温度,以期热轧卷坯的再结晶过程更加充分,以使各型织构分布更加均匀;第二,利用颗粒刺激形核原理在冷轧过程中进行第一次中间退火,采用燃气循环加热箱式炉的加热速度慢,保温时间久的特点,促进了合金中弥散析出的亚微米级al(femn)si和mg2si金属间化合物的进一步长大,为后续退火形成p织构做好准备,同时由于箱式退火前合金有40%的冷轧压下率可在退火过程中发生完全再结晶,有效降低了变形织构的剧烈发展。第三,在第二次冷轧中间退火时利用气垫炉加热速度快,保温时间短的特点,一方面退火时能保证再结晶的完全进行,p织构的充分发展,另一方面尽可能降低再结晶晶粒尺寸,以保证最终成品晶粒尺寸不会过大,晶粒的细化能有效提高成品的综合性能。本发明最终获得的成品与传统的6016合金相比,冲压后表面光滑细腻,未有肉眼可见的罗平线缺陷,表面质量得到明显改善。3、针对现有专利对包边性能和冲压后表面质量的研究空白,本专利综合考虑了强度、冲压成形性等方面,针对现在6000系铝合金在车身外板应用中容易出现的包边开裂和成形后出现罗平线的表面质量缺陷等突出问题进行了开发研究。通过优化合金成分,改善原有工艺路线和参数,获得了一种包边性能优良,冲压后铝合金板材表面质量光滑细腻,无肉眼可见罗平线缺陷,可广泛应用于汽车车身引擎盖、车门等部位外板的6000系铝合金材料。本发明的其他优点、目标和特征在某种程度上将在随后的说明书中进行阐述,并且在某种程度上,基于对下文的考察研究对本领域技术人员而言将是显而易见的,或者可以从本发明的实践中得到教导。本发明的目标和其他优点可以通过下面的说明书来实现和获得。附图说明为了使本发明的目的、技术方案和优点更加清楚,下面将结合附图对本发明作优选的详细描述,其中:图1为对比例所制备铝合金板材的表面形貌图;图2为实施例所制备铝合金板材的表面形貌图。具体实施方式以下通过特定的具体实例说明本发明的实施方式,本领域技术人员可由本说明书所揭露的内容轻易地了解本发明的其他优点与功效。本发明还可以通过另外不同的具体实施方式加以实施或应用,本说明书中的各项细节也可以基于不同观点与应用,在没有背离本发明的精神下进行各种修饰或改变。实施例一种汽车车身外板用6系铝合金板材的制备方法,包括如下步骤:a、将制备汽车车身外板的铝合金原料按照重量百分比进行配料,铝合金原料各元素质量百分数配比如下:元素sifecumnmgti杂质al含量0.600.150.150.100.700.020.03余量杂质中含有碱金属,碱金属中na≤10ppm,ca≤8ppm,li≤15ppm;铝合金原料采用回收铝、工业纯铝、工业纯mg、工业纯zn、中间合金al-si、中间合金al-cu、中间合金al-fe、中间合金al-mn。将配制好的铝合金原料置于熔炼炉中熔炼为液态铝合金,铝合金原料熔炼温度为700~760℃,融化过程中开启电磁搅拌,将熔炼后的铝合金熔体倒入精炼炉中精炼,精炼温度为720~740℃,使用cl-ar混合气体进行精炼并调整合金成分,成分合格后通过al-ti-b丝细化剂细化后进行扁锭半连续铸造,获得630mm*2150mm*6000mm尺寸的6系铝合金梯形扁锭;b、将熔铸后的铝合金铸锭切去头尾并铣去铝合金铸锭表面凝壳层,铝合金铸锭引头端至少切除200mm,浇口端至少切除100mm,大面单面至少铣10mm,小面斜面至少铣5mm,小面立面至少铣5mm;c、将铝合金铸锭在推进式燃气加热炉中进行均匀化热处理,均匀化热处理的工艺为:铝合金铸锭先升温至560℃保温12h,然后降温至530℃保温9h出炉;d、将均匀化后铝合金铸锭3min内进入粗轧工序,粗轧道次不多于18次,粗轧完成时间在10min内,粗轧后中间坯厚度50~55mm,然后进行4连式精轧工序,精轧总压下率>80%,最终精轧下线卷坯厚度10mm,卷坯温度为350~370℃,自然冷却至室温;e、冷轧:将热轧后的铝合金板材冷轧至1.0mm,依次经过7.5mm、6.0mm、4.0mm、2.8mm、1.9mm、1.3mm、1.0mm,其中在冷轧至6.0mm时的铝合金板材在380℃的燃气循环加热箱式退火炉退火2h且退火前冷轧压下率为40%,冷轧至2.8mm时的铝合金板材在480℃的气垫式加热炉退火20s且退火前冷轧压下率为53%,退火后冷轧压下率为64%;f、将冷轧后的铝合金板材在气垫式加热炉进行固溶处理,升温速率不小于5℃/s,升温至570℃保温30s后进行水淬,水淬后铝合金板材温度不高于150℃,然后风冷至室温;g、将固溶淬火后铝合金板材立即进行预时效处理,间隔时间不超过30s,使用连续通过式气垫加热炉进行,保证预时效后打卷温度为80~100℃,预时效后铝合金板材转移至20~25℃仓储环境冷却到室温。对比例一种汽车车身外板用6016铝合金板材的制备方法,包括如下步骤:a、将制备汽车车身外板的铝合金原料按照重量百分比进行配料,铝合金原料各元素质量百分数配比如下:元素sifecumnmgti杂质al含量1.100.200.050.050.450.020.03余量杂质中含有碱金属,碱金属中na≤10ppm,ca≤8ppm,li≤15ppm;铝合金原料采用回收铝、工业纯铝、工业纯mg、工业纯zn、中间合金al-si、中间合金al-cu、中间合金al-fe、中间合金al-mn。将配制好的铝合金原料置于熔炼炉中熔炼为液态铝合金,铝合金原料熔炼温度为700~760℃,融化过程中开启电磁搅拌,将熔炼后的铝合金熔体倒入精炼炉中精炼,精炼温度为720~740℃,使用cl-ar混合气体进行精炼并调整合金成分,成分合格后通过al-ti-b丝细化剂细化后进行扁锭半连续铸造,获得630mm*2150mm*6000mm尺寸的6系铝合金梯形扁锭;b、将熔铸后的铝合金铸锭切去头尾并铣去铝合金铸锭表面凝壳层,铝合金铸锭引头端至少切除200mm,浇口端至少切除100mm,大面单面至少铣10mm,小面斜面至少铣5mm,小面立面至少铣5mm;c、将铝合金铸锭在推进式燃气加热炉中进行均匀化热处理,均匀化热处理的工艺为:铝合金铸锭先升温至560℃保温6h,然后降温至500℃保温10h出炉;d、将均匀化后铝合金铸锭转入粗轧工序,粗轧道次20±2次,粗轧后中间坯厚度40~45mm,然后进行4连式精轧工序,精轧总压下率>80%,最终精轧下线卷坯厚度6mm,卷坯温度为300~330℃,自然冷却至室温;e、冷轧:将热轧后的铝合金板材冷轧至1.0mm,依次经过4.2mm、3.0mm、1.9mm、1.3mm、1.0mm,其中在冷轧至3.0mm时的铝合金板材在480℃的气垫式加热炉退火20s且退火前冷轧压下率为50%,退火后冷轧压下率为66.7%;f、将冷轧后的铝合金板材在气垫式加热炉进行固溶处理,升温速率不小于5℃/s,升温至560℃保温20s后进行水淬,水淬后铝合金板材温度不高于150℃,然后风冷至室温;g、将固溶淬火后铝合金板材立即进行预时效处理,间隔时间不超过30s,使用连续通过式气垫加热炉进行,保证预时效后打卷温度为80~100℃,预时效后铝合金板材转移至20~25℃仓储环境冷却到室温。根据vda238-100标准进行弯曲试验,首先按照0°和90°制备250mm×70mm的条状样片,按照25mm/min的速度预拉伸10%,然后每个条状样片裁取两个60mm×60mm的小样片,采用3点弯曲试验机进行弯曲试验,采用直径30mm的滚动式支撑辊,跨距为2×板厚,压头半径为0.2mm,以10mm/min预加载30n后,以20mm/min速度进行弯曲,直至最大下压力降低30n时停止试验,测量样片弯曲角度。实施例与对比例所制备铝合金板材包边性能对比试验结果如表1所示,显然弯曲角度越大,材料的弯曲性能更好,在实际包边时更不容易出现开裂,实施例和对比例相比,0°方向大约提高20°左右,90°方向提高15°以上,包边性能有了明显的提高,达到了预期目的。表1图1为对比例所制备铝合金板材的表面形貌图,图2为实施例所制备铝合金板材的表面形貌图。按照gb/t33227-2016标准试验对比结果可见,本发明最终获得的成品与传统的6016合金相比,预拉伸10%模拟冲压后表面光滑细腻,未有肉眼可见的罗平线缺陷,表面质量得到明显改善。按照gb/t228-2002,gb/t5027-2016和gb/t5028-2008标准试验,实施例与对比例力学性能对比结果如表2所示,相比对比例,实施例t4态和t64态的抗拉和屈服强度无明显差异,能够满足车身覆盖件的正常使用,同时实施例t4态的延伸率a80和ag、加工硬化指数n值和塑性应变比r值均有一定提高,说明实施例的成形性能也有了一定的改善,能够更好的拓展6000系铝板材的应用范围。表2最后说明的是,以上实施例仅用以说明本发明的技术方案而非限制,尽管参照较佳实施例对本发明进行了详细说明,本领域的普通技术人员应当理解,可以对本发明的技术方案进行修改或者等同替换,而不脱离本技术方案的宗旨和范围,其均应涵盖在本发明的权利要求范围当中。当前第1页12