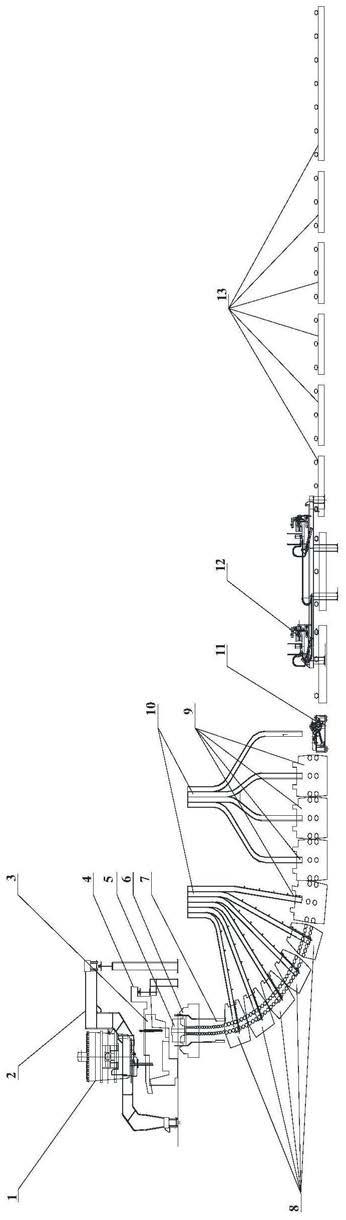
1.本发明涉及钢铁冶金行业连铸设备技术领域,具体涉及一种复合连铸机及其生产方法。
背景技术:2.在特殊钢和型钢生产领域,由于存在钢种多、规格多、批量小的特点,以及需要根据市场需求来灵活生产的客户,同时鉴于场地面积和总投资成本的考虑,会带来相应坯料的供应和选择问题。
3.如果采用多台连铸机来生产不同规格及品种,势必会造成连铸机作业率低、效率低的问题,既增加占地与投资,也增加了运行维护成本。因此根据市场需求和低成本的趋势,越来越多的客户希望一台铸机能兼容更多的断面规格,按市场需求来随时调整生产,而能否设计一种连铸机既能生产多种坯型、又能针对相应坯型采用适合其特点的质量控制技术来生产合格铸坯,成为迫切需要解决的问题。
4.目前国内外钢铁企业,板矩坯复合连铸机很少,在国内仅达涅利和奥钢联各有一台板矩坯连铸机业绩。达涅利的板矩坯连铸机生产板坯及矩坯时中间罐内腔耐材砌筑不同,浇铸板坯时需用耐材堵掉一半中间罐,流场不对称,金属收得率低,生产成本高;同时采用板坯扇形段生产方坯存在二冷冷却不均的问题,容易出现铸坯内部和表面质量问题。普瑞特的板矩坯连铸机在浇铸矩坯时存在脱方严重和中心疏松等质量问题,不能采用大断面方矩坯连铸技术的有效技术手段如二冷均匀冷却、末端电磁搅拌、动态轻压下等,使用效果不好,目前主要生产板坯。两者共同特点是生产矩形坯时需利用板坯的部分扇形段,无法实现常规方矩坯连铸机的二冷设计和喷嘴均匀布置,不能有效采用电磁搅拌、动态轻压下技术等,铸坯质量无法保证。再有传统大包回转台钢包落点固定,无法满足单独浇注板坯或矩形坯时钢包落点对中;如果要兼顾各流可采用加长中间罐的方案,但板坯矩坯流间距较大时会造成中间罐过长,会带来加大起重机吨位及增加厂房投资等影响;同时,针对板坯及矩坯生产时中间罐砌筑方式不同,又会增加中间罐周转数量。
技术实现要素:5.本发明提供了一种复合连铸机及其生产方法,以实现板坯和方矩坯的快速切换生产的目的。
6.本发明解决其技术问题所采用的技术方案是:一种复合连铸机,包括:间隔布置的板坯生产线和矩形坯生产线;中间罐组件,设置在板坯生产线和矩形坯生产线的上方,中间罐组件具有第一水口和位于第一水口两侧的第二水口,第一水口与板坯生产线连接,两个第二水口均与矩形坯生产线连接;浇注组件,能够向中间罐组件内浇注钢水,浇注组件能够在板坯生产线和矩形坯生产线之间移动。
7.进一步地,复合连铸机包括浇注平台,中间罐组件包括中间罐车和中间罐,中间罐车设置在浇注平台上,中间罐设置于中间罐车上,且中间罐能够与板坯生产线和矩形坯生
产线连通。
8.进一步地,第二水口为两个,第一水口和两个第二水口沿同一直线间隔均布,且第一水口位于两个第二水口之间。
9.进一步地,复合连铸机包括等待位、板坯浇注位和矩形坯浇注位,浇注组件至少为两个,至少两个浇注组件能够在等待位与板坯浇注位之间移动或者至少两个浇注组件能够在等待位与矩形坯浇注位之间移动。
10.进一步地,浇注组件包括钢包和钢包浇铸车,钢包设置在钢包浇铸车上,钢包浇铸车能够带动钢包移动。
11.进一步地,钢包浇铸车为半龙门式钢包浇铸车,钢包浇铸车采用变频调速移动方式。
12.进一步地,钢包浇铸车设置有液压驱动的垂直横移组件。
13.进一步地,板坯生产线包括依次设置的板坯结晶器、结晶器液压振动装置、弯曲段、弧形扇形段、矫直及水平扇形段、导轨组、脱引锭装置、第一火切机和第一输出辊道。
14.进一步地,矩形坯生产线包括依次设置的矩形坯结晶器、结晶器振动装置、结晶器电磁搅拌、二次冷却段、末端电磁搅拌、拉矫机组、第二火切机和第二输出辊道。
15.本发明还提供了一种复合连铸机的生产方法,包括以下步骤:步骤10、如果生产板坯,将浇注组件移动至板坯浇注位,开启板坯生产线并通过浇注组件和中间罐组件向板坯生产线浇注钢水;步骤20、如果生产矩形坯,将浇注组件移动至矩形坯浇注位,开启矩形坯生产线并浇注组件和中间罐组件向矩形坯生产线浇注钢水。
16.本发明的有益效果是:本发明实施例使间隔布置的板坯生产线和矩形坯生产线共用中间罐组件和浇注组件,当需要进行板坯和矩形坯切换时,只需将浇注组件开到相应浇注位,既保证了浇注组件的水口与中间罐组件的对中浇注,同时改变了传统复合铸机在板坯和矩形坯切换时需要更换结晶器和扇形段的操作模式,解决了同一铸机单独生产板坯和矩坯的难题,实现板坯和方矩坯的快速切换生产。
附图说明
17.构成本技术的一部分的说明书附图用来提供对本发明的进一步理解,本发明的示意性实施例及其说明用于解释本发明,并不构成对本发明的不当限定。在附图中:
18.图1为本发明实施例中板坯生产线的结构示意图;
19.图2为本发明实施例中矩形坯生产线的结构示意图。
20.图中附图标记:1、钢包;2、钢包浇铸车;3、中间罐;4、中间罐车;5、板坯结晶器;6、结晶器液压振动装置;7、弯曲段;8、弧形扇形段;9、矫直及水平扇形段;10、导轨组;11、脱引锭装置;12、第一火切机;13、第一输出辊道;14、矩形坯结晶器;15、结晶器振动装置;16、结晶器电磁搅拌;17、二次冷却段;18、末端电磁搅拌;19、拉矫机组;20、第二火切机;21、第二输出辊道。
具体实施方式
21.需要说明的是,在不冲突的情况下,本技术中的实施例及实施例中的特征可以相互组合。下面将参考附图并结合实施例来详细说明本发明。
22.如图1和图2所示,本发明实施例提供了一种复合连铸机,包括间隔布置的板坯生产线和矩形坯生产线、中间罐组件和浇注组件。中间罐组件设置在板坯生产线和矩形坯生产线的上方,中间罐组件具有第一水口和位于第一水口两侧的第二水口,第一水口与板坯生产线连接,两个第二水口均与矩形坯生产线连接。浇注组件能够向中间罐组件内浇注钢水,浇注组件能够在板坯生产线和矩形坯生产线之间移动。
23.本发明实施例使间隔布置的板坯生产线和矩形坯生产线共用中间罐组件和浇注组件,当需要进行板坯和矩形坯切换时,只需将浇注组件开到相应浇注位,既保证了浇注组件的水口与中间罐组件的对中浇注,同时改变了传统复合铸机在板坯和矩形坯切换时需要更换结晶器和扇形段的操作模式,解决了同一铸机单独生产板坯和矩坯的难题,实现板坯和方矩坯的快速切换生产。
24.复合连铸机包括浇注平台,中间罐组件包括中间罐车4和中间罐3,中间罐车4设置在浇注平台上,中间罐3设置于中间罐车4上,且中间罐3能够与板坯生产线和矩形坯生产线连通。
25.中间罐3是基于中间罐流场仿真和浇铸耦合模拟制作开发的板矩坯兼容中间罐;该中间罐3的横截面呈t形结构。在工作时,通过该中间罐3对板坯生产线和矩形坯生产线进行浇注,方便生产调度,提高作业率,减少了中间罐3的数量、运行成本和项目投资。
26.优选地,第二水口为两个,第一水口和两个第二水口沿同一直线间隔均布,且第一水口位于两个第二水口之间。浇注板坯时使用中间的第一水口,浇注矩形坯时使用两侧的第二水口。通过中间罐3流场数值仿真技术,优化中间罐3的内腔结构和控流装置,改善中间罐3内钢液的流动特性,以减少死区,增加钢液在中间罐3内的停留时间,促进钢液中夹杂物的上浮去除,达到净化钢液的目的。
27.复合连铸机包括等待位、板坯浇注位和矩形坯浇注位,浇注组件至少为两个,至少两个浇注组件能够在等待位与板坯浇注位之间移动或者至少两个浇注组件能够在等待位与矩形坯浇注位之间移动。
28.本发明实施例工作时:一个浇注组件上浇注完毕,直接开到等待位,另一有满包钢水的浇注组件开到对应的浇注位,实现多炉连浇。两台浇注组件独立坐包不影响另一台浇注组件的正常浇钢。
29.本发明实施例中浇注组件包括钢包1和钢包浇铸车2,钢包1设置在钢包浇铸车2上,钢包浇铸车2能够带动钢包1移动。
30.钢包浇铸车2行走采用变频调速,垂直横移组件采用液压缸驱动,钢包浇铸车2整体采用钢结构框架支撑,以支承钢包1进行浇铸作业,整体结构安全可靠。并且钢包浇铸车2为半龙门式钢包浇铸车,能够实现钢包1快速更换,减少中间罐3内钢液面波动。
31.同时,该钢包浇铸车2可开到板坯浇注位和矩形坯浇注位,有效实现了两套连铸设备共用一套平台浇注系统的需求。同时由于板坯和矩形坯设备的独立性,有效缩短了断面的切换和检修时间,即一种坯型生产时不影响另一种坯型的设备更换、检修和生产准备,大大地提高了设备的利用率和浇注系统的作业率。
32.板坯生产线包括依次设置的板坯结晶器5、结晶器液压振动装置6、弯曲段7、弧形扇形段8、矫直及水平扇形段9、导轨组10、脱引锭装置11、第一火切机12和第一输出辊道13。其中,弯曲段7、弧形扇形段8和矫直及水平扇形段9均是带有密排夹持的且配有二次喷淋冷
却段。
33.矩形坯生产线包括依次设置的矩形坯结晶器14、结晶器振动装置15、结晶器电磁搅拌16、二次冷却段17、末端电磁搅拌18、拉矫机组19、第二火切机20和第二输出辊道21。本发明实施例中,为改善矩形坯铸坯质量配置了结晶器电磁搅拌16和末端电磁搅拌18,具备内外左右喷水功能的二次冷却段17,以及为改善铸坯内部质量具备轻压下功能的拉矫机组19。
34.板坯和矩形坯各自采用独立的铸流设备,即从结晶器、二次冷却段到出坯辊道板坯和矩形坯铸流各自独立配置。这样使得板坯和矩形坯,在共用浇铸平台的情况下,可以分别采用适合各自坯型特点铸坯质量控制技术。例如,板坯采用了弧形扇形段8结构,矩形坯采用带四面支撑辊的二次冷却段17,并且设置末端电磁搅拌18,同时保证了铸坯四面的均匀冷却,保证了矩形坯内部质量。
35.本发明实施例可以用于生产的板坯断面为:200
×
(550~850)mm2、260
×
(550~850)mm2、300
×
(550~870)mm2,钢种主要是合金钢。可生产的矩坯断面为:200
×
380mm2,钢种主要是重轨钢。
36.一种复合连铸机的生产方法,包括以下步骤:
37.步骤10、如果生产板坯,将浇注组件移动至板坯浇注位,开启板坯生产线并通过浇注组件和中间罐组件向板坯生产线浇注钢水;
38.步骤20、如果生产矩形坯,将浇注组件移动至矩形坯浇注位,开启矩形坯生产线并浇注组件和中间罐组件向矩形坯生产线浇注钢水。
39.步骤10具体包括:生产板坯时,钢包1盛接着钢液,通过天车吊运至接受跨,放置在钢包浇铸车2上,钢包浇铸车2载着装有钢液的钢包1直接开至放置在板坯结晶器5上方的中间罐3上。通过中间罐3将钢液分配到各流的板坯结晶器5。待板坯结晶器5内钢液高度合适后,弧形扇形段8和矫直及水平扇形段9开始启动,并伴随弧形扇形段8和矫直及水平扇形段9启动结晶器液压振动装置6同步振动(其结晶器的振动频率和振幅,根据拉速、钢种和断面,可匹配不同的振动方案)。弧形扇形段8和矫直及水平扇形段组9拉出引锭杆和铸坯,期间铸坯经历弯曲段7、弧形扇形段8和矫直及水平扇形段9的喷水冷却。期间引锭杆通过引锭杆存放装置实现回收,以备下一次铸机开浇使用;当引锭杆从矫直及水平扇形段组9拉出完毕后,用脱引锭装置11实现脱引锭。当铸坯长度满足定尺要求后,启动第一火切机12进行切割。当定尺铸坯切割完成后,通过第一输出辊道13将铸坯输出。
40.连续浇铸时,只需将载着浇铸完成的钢包浇铸车2开走,立刻将载着满包钢水的钢包浇铸车2开到板坯浇注位,打开浇铸水口,即可实现多炉连浇。两台钢包浇铸车独立坐包不影响另一台钢包浇铸车的正常浇钢。
41.步骤20具体包括:生产矩坯时,钢包1盛接着钢液,通过天车吊运至接受跨,放置在钢包浇铸车2上,钢包浇铸车2载着装有钢液的钢包1直接开至放置在矩形坯结晶器14上方的中间罐3上。通过中间罐3将钢液分配到各流的矩形坯结晶器14。待矩形坯结晶器14内钢液高度合适后,拉矫机组19开始起步,并伴随拉矫机组19起步结晶器振动装置15同步振动(其结晶器的振动频率和振幅,根据拉速、钢种和断面,可匹配不同的振动方案)。拉矫机组19拉出引锭杆和铸坯,期间铸坯经历结晶器电磁搅拌16,具备内外左右喷水功能的二次冷却段17,以及末端电磁搅拌18实现对矩坯表面和内部铸坯质量的提升。期间引锭杆通过引
锭杆存放装置实现回收,以备下一次铸机开浇使用;当铸坯长度满足定尺要求后,启动第二火切机20进行切割。当定尺铸坯切割完成后,通过第二输出辊道21将铸坯输出。
42.连续浇铸时,只需将载着浇铸完成的钢包浇铸车2开走,立刻将载着满包钢水的钢包浇铸车开到矩形坯浇注位,打开浇铸水口,即可实现多炉连浇。两台钢包浇铸车独立坐包不影响另一台钢包浇铸车的正常浇钢。
43.从以上的描述中,可以看出,本发明上述的实施例实现了如下技术效果:
44.1、板坯和矩形坯共用浇铸平台,即采用横移式浇注系统,实现了板坯和方矩坯的快速切换生产。平台上钢包1、钢包浇铸车2、中间罐3、中间罐车4等设备板坯和矩形坯连铸共用。板坯与矩形坯切换时只需将钢包浇铸车开到相应浇注位,既保证了钢包水口与中间罐的对中浇注,同时改变了传统复合铸机在板坯和矩形坯切换时需要更换结晶器和扇形段的操作模式。
45.2、板坯和矩形坯各自采用独立的铸流设备,即从结晶器、二次冷却段到出坯辊道板坯和矩形坯铸流各自独立配置。这样使得板坯和矩形坯,在共用浇铸平台的情况下,可以分别采用适合各自坯型特点铸坯质量控制技术。例如,板坯采用了弧形扇形段8结构,矩形坯采用带四面支撑辊的二次冷却段17,并且设置末端电磁搅拌18,同时保证了铸坯四面的均匀冷却,保证了矩形坯内部质量。
46.3、钢包浇铸车2可开到板坯浇注位和矩形坯浇注位,有效实现了两套连铸设备共用一套平台浇注系统的需求。同时由于板坯和矩形坯设备的独立性,有效缩短了断面的切换和检修时间,即一种坯型生产时不影响另一种坯型的设备更换、检修和生产准备,大大地提高了设备的利用率和浇注系统的作业率。
47.以上所述,仅为本发明的具体实施例,不能以其限定发明实施的范围,所以其等同组件的置换,或依本发明专利保护范围所作的等同变化与修饰,都应仍属于本专利涵盖的范畴。另外,本发明中的技术特征与技术特征之间、技术特征与技术方案之间、技术方案与技术方案之间均可以自由组合使用。