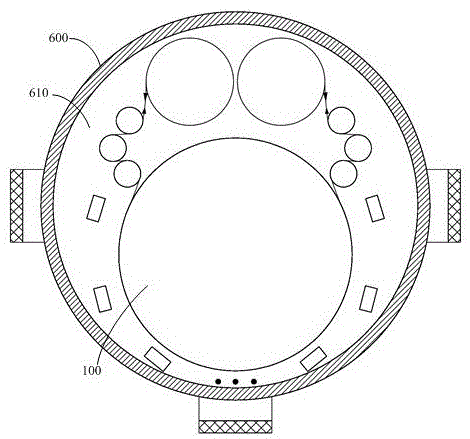
本发明涉及真空镀膜
技术领域:
,特别涉及一种真空镀膜装置。
背景技术:
:真空溅射卷绕镀膜设备可以在真空室内通过磁控溅射技术等方法在卷装导电基材与非导电基材表面制备一层或者多层功能性薄膜的主要设备,可以应用于柔性电路板材料、电磁屏蔽膜材、其他柔性导电材等行业。目前,常用真空磁控溅射镀膜机镀膜质量差,镀膜后的基材厚度厚,不能满足人们的需求。技术实现要素:本发明的主要目的是提供一种真空镀膜装置,旨在提高镀膜质量。为实现上述目的,本发明提出的真空镀膜装置,包括:壳体,所述壳体具有真空腔;第一收放辊和第二收放辊,设置于所述真空腔内,其中一个用于放出未镀膜的基膜,另一个用于收绕已镀膜的基膜;所述第一收放辊的直径为a1;超导主动辊,所述超导主动辊设置于真空腔内,所述超导主动辊用以供待镀基膜缠绕,用于支撑展平待镀基膜;所述超导主动辊的直径为d;靶材,所述靶材沿所述所述超主动辊的边缘排布,所述靶材的尺寸为d;导向辊、张紧辊以及压紧辊,所述导向辊靠近第一收放辊或第二收放辊设置,所述压紧辊靠近所述超导主动辊设置,所述张紧辊位于所述导向辊和所述压紧辊之间;所述压紧辊的直径为l1;所述第一收放辊直径a1与超导主动辊的直径d之间的比值为3/8~11/12;所述靶材的尺寸d与超导主动辊的直径d之间的比值为1/25~1/6;所述压紧辊的直径l1与超导主动辊的直径d之间的比值为1/20~1/5。可选地,所述靶材与真空镀膜装置的主控电路连接,主控电路包括电压调节电路,以调节加载在靶材上的电压。可选地,真空镀膜装置还包括氩气输入装置,所述壳体的侧壁上开设氩气输入口,所述氩气输入装置的出气口与所述氩气输入口连通。可选地,所述第一收放辊和第二位收放辊临近设置于所述超导主动辊的同一侧;所述张紧辊和所述第一收放辊分别位于所述导向辊的相对两侧,所述张紧辊和所述超导主动辊分别位于所述压紧辊的相对两侧。可选地,所述壳体呈圆筒状,所述第一收放辊和第二收放辊位于所述真空腔的上侧;所述靶材的数量为多个,多个所述靶材沿所述超导主动辊的中下部的周向排布。可选地,所述第一收放辊和所述超导主动辊之间具有隔离间隙m,隔离间隙m的尺寸为5~10mm。可选地,真空镀膜装置还包括抽真空装置,抽真空装置与壳体的内部连通,以对壳体的内部进行抽真空。可选地,所述超导主动辊和壳体由石墨烯制成。可选地,所述张紧辊的直径为l2,所述张紧辊的直径l2与超导主动辊的直径d之间的比值为1/20~1/5;所述导向辊的直径为l3,所述导向辊的直径l3与超导主动辊的直径d之间的比值为1/20~1/5。可选地,所述超导主动辊的直径d为600~2000mm;所述压紧辊的直径l1为100~120mm;所述第一收放辊的直径a1为550~750mm;所述靶材的尺寸d为80~100mm。本发明技术方案中,通过为基膜设置简洁的移动估计,避免基膜由于复杂的移动轨迹而褶皱和损坏,有利于提高基膜移动过程的可靠性;通过调整主动辊、第一收放辊、压紧辊的尺寸比例,使得基膜在放出、镀膜、收绕以及贴合超导主动辊的过程中,其都具有大的绕角,使得基膜的过渡非常平缓,增加了基膜在路径上移动的可靠性,如此,提高基膜在高张紧力作用下的安全可靠性;同时,通过设置靶材与超导主动辊之间的比值,使得从靶材上高速释放的粒子可以快速、稳定的附着在基膜上(由于靶材与超导主动辊的尺寸比例非常大,使得高能量的粒子附着在基膜上后,高能量粒子可以快速的与超导主动辊进行能量交换,使得高能量金属粒子可以非常快速、紧密的稳定附着,提高了附着效果),从而提高镀膜层的密度,减小镀膜层的厚度;由于靶材与超导主动辊的尺寸比例非常大,使得基膜和超导主动辊可以实现更高速度、更大能量的金属粒子的能量转换,如此,避免了由于金属粒子能量过高而出现基膜褶皱或者损坏是现象,当增加靶材的激活电压时,在提高镀膜效率,提高靶材利用率的同时,大幅的提高了镀膜的质量。值得说明的是,通过本申请方案实现的镀膜最薄可达1.5微米,相较于传统设备的7.5微米,大幅的减小了厚度,提高了镀膜层的密度和强度,同时提高了镀膜层与基膜之间的剥离强度。附图说明为了更清楚地说明本发明实施例或现有技术中的技术方案,下面将对实施例或现有技术描述中所需要使用的附图作简单地介绍,显而易见地,下面描述中的附图仅仅是本发明的一些实施例,对于本领域普通技术人员来讲,在不付出创造性劳动的前提下,还可以根据这些附图示出的结构获得其他的附图。图1为本发明真空镀膜装置一实施例的内部结构示意图;图2为图1中真空腔内部元器件的排布示意图。附图标号说明:标号名称标号名称100超导主动辊210第一收放辊220第二收放辊310导向辊320张紧辊330压紧辊500靶材600壳体610真空腔本发明目的的实现、功能特点及优点将结合实施例,参照附图做进一步说明。具体实施方式下面将结合本发明实施例中的附图,对本发明实施例中的技术方案进行清楚、完整地描述,显然,所描述的实施例仅仅是本发明的一部分实施例,而不是全部的实施例。基于本发明中的实施例,本领域普通技术人员在没有作出创造性劳动前提下所获得的所有其他实施例,都属于本发明保护的范围。需要说明,本发明实施例中所有方向性指示(诸如上、下、左、右、前、后……)仅用于解释在某一特定姿态(如附图所示)下各部件之间的相对位置关系、运动情况等,如果该特定姿态发生改变时,则该方向性指示也相应地随之改变。另外,在本发明中涉及“第一”、“第二”等的描述仅用于描述目的,而不能理解为指示或暗示其相对重要性或者隐含指明所指示的技术特征的数量。由此,限定有“第一”、“第二”的特征可以明示或者隐含地包括至少一个该特征。另外,全文中的“和/或”包括三个方案,以a和/或b为例,包括a技术方案、b技术方案,以及a和b同时满足的技术方案;另外,各个实施例之间的技术方案可以相互结合,但是必须是以本领域普通技术人员能够实现为基础,当技术方案的结合出现相互矛盾或无法实现时应当认为这种技术方案的结合不存在,也不在本发明要求的保护范围之内。本发明主要提出一种真空镀膜装置,主要通过调整主动辊、第一收放辊210、第二收放辊220以及压紧辊330的位置关系,使得基膜具有一个简洁的移动轨迹,从而可以使得提高张紧力的同时,保证基膜的安全可靠性;通过调整主动辊、第一收放辊210、第二收放辊220、压紧辊330以及靶材500的尺寸比例,除了进一步提高基膜在高张紧力作用下的安全可靠性外,使得从靶材500上高速释放的粒子可以快速、稳定的附着在基膜上(由于靶材500与超导主动辊100的尺寸比例非常大,使得高能量的粒子附着在基膜上后,高能量粒子可以快速的与超导主动辊100进行能量交换,使得高能量金属粒子可以非常快速、紧密的稳定附着,提高了附着效果),从而提高镀膜层的密度,减小镀膜层的厚度;由于靶材500与超导主动辊100的尺寸比例非常大,使得基膜和超导主动辊100可以实现更高速度、更大能量的金属粒子的能量转换,如此,避免了由于金属粒子能量过高而出现基膜褶皱或者损坏是现象,当增加靶材500的激活电压时,在提高镀膜效率,提高靶材500利用率的同时,大幅的提高了镀膜的质量。以下将主要描述真空镀膜装置的具体结构。参照图1至图2,在本发明实施例中,该真空镀膜装置1、一种真空镀膜装置,其特征在于,包括:壳体600,所述壳体600具有真空腔610;第一收放辊210和第二收放辊220,设置于所述真空腔610内,其中一个用于放出未镀膜的基膜,另一个用于收绕已镀膜的基膜;所述第一收放辊210的直径为a1;超导主动辊100,所述超导主动辊100设置于真空腔610内,所述超导主动辊100用以供待镀基膜缠绕,用于支撑展平待镀基膜;所述超导主动辊100的直径为d;靶材500,所述靶材500沿所述所述超主动辊的边缘排布,所述靶材500的尺寸为d;导向辊310、张紧辊320以及压紧辊330,所述导向辊310靠近第一收放辊210或第二收放辊220设置,所述压紧辊330靠近所述超导主动辊100设置,所述张紧辊320位于所述导向辊310和所述压紧辊330之间;所述压紧辊330的直径为l1;所述第一收放辊210直径a1与超导主动辊100的直径d之间的比值为3/8~11/12;所述靶材500的尺寸d与超导主动辊100的直径d之间的比值为1/25~1/6;所述压紧辊330的直径l1与超导主动辊100的直径d之间的比值为1/20~1/5。具体地,本实施例中,壳体600的形式可以有很多,其横截面可以为方形、椭圆形、三角形等,以呈圆形设置为例。本实施例中的真空镀膜装置,仅包括一个超导主动辊100,第一收放辊210、第二收放辊220以及引导基膜走向的导向辊310,提高和调节基膜张紧力的张紧辊320,确保基膜与超导主动辊100贴合度的压紧辊330。基膜自第一收放辊210放出后,依次经过导向辊310、张紧辊320和压紧辊330,然后贴附在超导主动辊100的外表面,再依次经过另外的压紧辊330、张紧辊320和导向辊310,最后收绕在第二收放辊220上。如此,使得基膜的移动路径非常的简洁,避免了复杂路径带来的褶皱和破坏风险,使得基膜可以承受更大的冲击载荷。所述超导主动辊100和壳体600的材质可以有很多,以均由超导石墨烯制成为例,如此,可以非常高效的实现金属粒子的能量转移,从而实现金属粒子的高效附着。其中,靶材500的形状可以有很多,如方形、三角形、椭圆形,圆形等,其尺寸d为最大尺寸;第一收放辊210的直径a1和第二收放辊220的直径a2为收绕有基膜的直径。通过将第一收放辊210直径a1与超导主动辊100的直径d之间的比值为3/8~11/12,使得基膜在放出、镀膜以及收绕的过程中,其都具有大的绕角,使得基膜的过渡非常平缓;将所述压紧辊330的直径l1与超导主动辊100的直径d之间的比值为1/20~1/5,使得基膜在贴合到超导主动辊100上时,具有大的绕角,使得基膜的移动非常平缓,如此,使得基膜移动路径非常简洁的基础上,路径也非常平滑,增加了基膜在移动路径上的可靠性。将所述靶材500的尺寸d与超导主动辊100的直径d之间的比值设置为1/25~1/6,使得每一靶材500所对应的超导主动辊100的面积非常大,也即靶材500相较于超导主动辊100,尺寸小,如此,使得从靶材500上激发的高能量金属粒子的能量,在接触到基膜时,可以非常快的被转换至超导主动辊100,从而使得高能量的金属粒子可以非常快速并稳定的附着在基膜上,从而在提高金属粒子的附着效率的同时,还有利于提高粒子之间的紧密性。关于第一收放辊210、第二收放辊220、超导主动辊100以及导向辊310、张紧辊320和压紧辊330在真空腔610中的排布形式可以有很多,下面举一个例子进行说明。所述第一收放辊210和第二位收放辊临近设置于所述超导主动辊100的同一侧;所述张紧辊320和所述第一收放辊210分别位于所述导向辊310的相对两侧,所述张紧辊320和所述超导主动辊100分别位于所述压紧辊330的相对两侧。所述壳体600呈圆筒状,所述第一收放辊210和第二收放辊220位于所述真空腔610的上侧;所述靶材500的数量为多个,多个所述靶材500沿所述超导主动辊100的中下部的周向排布。具体地,通过将第一收放辊210和第二收放辊220临近设置于超导主动辊100的同一侧,使得基膜可以大面积的缠绕在超导主动辊100的表面,从而增加了可以接收高能金属粒子的面积,有效的提高了空间利用率。通过张紧辊320的位置排布,使得基膜可以被有效的张紧,同时,保证基膜的运动路径简洁,基膜在移动过程中的突变阻力小。值得说明的是,在一些实施例中,为了避免第一收放辊210和第二收放辊220与超导主动辊100之间由于安装等误差发生挤压,在所述第一收放辊210和所述超导主动辊100之间,以及在第二收放辊220与超导主动辊100之间均具有隔离间隙m,隔离间隙m的尺寸为5~10mm。本实施例中,通过为基膜设置简洁的移动估计,避免基膜由于复杂的移动轨迹而褶皱和损坏,有利于提高基膜移动过程的可靠性;通过调整主动辊、第一收放辊210、压紧辊330的尺寸比例,使得基膜在放出、镀膜、收绕以及贴合超导主动辊100的过程中,其都具有大的绕角,使得基膜的过渡非常平缓,增加了基膜在路径上移动的可靠性,如此,提高基膜在高张紧力作用下的安全可靠性;同时,通过设置靶材500与超导主动辊100之间的比值,使得从靶材500上高速释放的粒子可以快速、稳定的附着在基膜上(由于靶材500与超导主动辊100的尺寸比例非常大,使得高能量的粒子附着在基膜上后,高能量粒子可以快速的与超导主动辊100进行能量交换,使得高能量金属粒子可以非常快速、紧密的稳定附着,提高了附着效果,超导主动辊,能量溅射量大,对超大能量的转换起到稳定作用),从而提高镀膜层的密度,减小镀膜层的厚度;由于靶材500与超导主动辊100的尺寸比例非常大,使得基膜和超导主动辊100可以实现更高速度、更大能量的金属粒子的能量转换,如此,避免了由于金属粒子能量过高而出现基膜褶皱或者损坏的现象,当增加靶材500的激活电压时,在提高镀膜效率,提高靶材500利用率的同时,大幅的提高了镀膜的质量。值得说明的是,通过本申请方案实现的镀膜最薄可达1.5微米,相较于传统设备的7.5微米,大幅的减小了厚度,提高了镀膜层的密度和强度,同时提高了镀膜层与基膜之间的剥离强度。在一些实施例中,为了满足不同需求,得到更多形式的镀膜,所述靶材500与真空镀膜装置的主控电路连接,主控电路包括电压调节电路,以调节加载在靶材500上的电压。通过调节加载靶材500带上的电压,可以调节从靶材500激发的金属粒子的速度和能量,从而调节金属粒子附着在基膜上的情况,从而满足不同工况下,对镀膜的需求,有利于提高真空镀膜装置的适应性。在一些实施例中,为了镀膜质量,真空镀膜装置还包括氩气输入装置,所述壳体600的侧壁上开设氩气输入口,所述氩气输入装置的出气口与所述氩气输入口连通。氩气输入装置将氩气输入到真空腔610中,以使得镀膜过程在充满氩气的工况下进行。真空镀膜装置的真空腔610的形成方式有多种,可以由外部设备辅助形成真空腔610,也可以由其自身携带真空形成设置。以其自身具有真空形成能力为例,真空镀膜装置还包括抽真空装置,抽真空装置与壳体600的内部连通,以对壳体600的内部进行抽真空。通过抽真空装置的设置,使得真空镀膜装置可以自身壳体600的内部进行真空处理,有利于真空腔610的形成。值得说明的是,在一些实施例中,为例进一步确保基膜在移动过程中的所有转弯处,均为大角度弯绕,进一步确保其在移动过程中的安全可靠性,所述张紧辊320的直径为l2,所述张紧辊320的直径l2与超导主动辊100的直径d之间的比值为1/20~1/5;所述导向辊310的直径为l3,所述导向辊310的直径l3与超导主动辊100的直径d之间的比值为1/20~1/5。关于超导主动辊100等零部件的尺寸,可以根据型号的需求进行设置,下面举例进行说明。所述超导主动辊100的直径d为600~2000mm;所述压紧辊330的直径l1为100~120mm;所述第一收放辊210的直径a1为550~750mm;所述靶材500的尺寸d为80~100mm。所述第二收放辊220的直径a2为550~750mm;所述导向辊310的直径l3为100~120mm;所述张紧辊320的直径l2为100~120mm。值得强调的是,在靶材上加载电压,从靶材上喷射出大量的高温金属粒子,高温金属粒子喷射至基材的表面,并附着在基材的表面,其中,高温金属粒子喷射的速度和其所具有的高温能量可以通过调节电压等方式进行调整。金属粒子喷射的速度越快,所含的能量越高,对基材的冲击和影响就越大,而基材所承受的能量有限,使得在更高温度的金属粒子冲击时,由于能量无法转化,致使基材容易损坏,致使现有的真空镀膜工艺无法满足用户的需求。本申请的技术方案中,通过大幅增加超导主动辊对应靶材的面积,使得金属粒子的高温,在接触到基膜的同时,快速的被传递到超导主动辊,实现高温金属粒子和超导主动辊之间的能量转移,从而减小高温对基膜的影响,使得基膜可以承受更高温度和速度的金属粒子,如此,更高温度的金属粒子在基膜上凝结的过程中,可以更好的与在先附着的粒子结合和能量转移,从而使得,真空镀膜的密度得到大幅的增加,有利于提高镀膜质量。以上所述仅为本发明的优选实施例,并非因此限制本发明的专利范围,凡是在本发明的发明构思下,利用本发明说明书及附图内容所作的等效结构变换,或直接/间接运用在其他相关的
技术领域:
均包括在本发明的专利保护范围内。当前第1页12