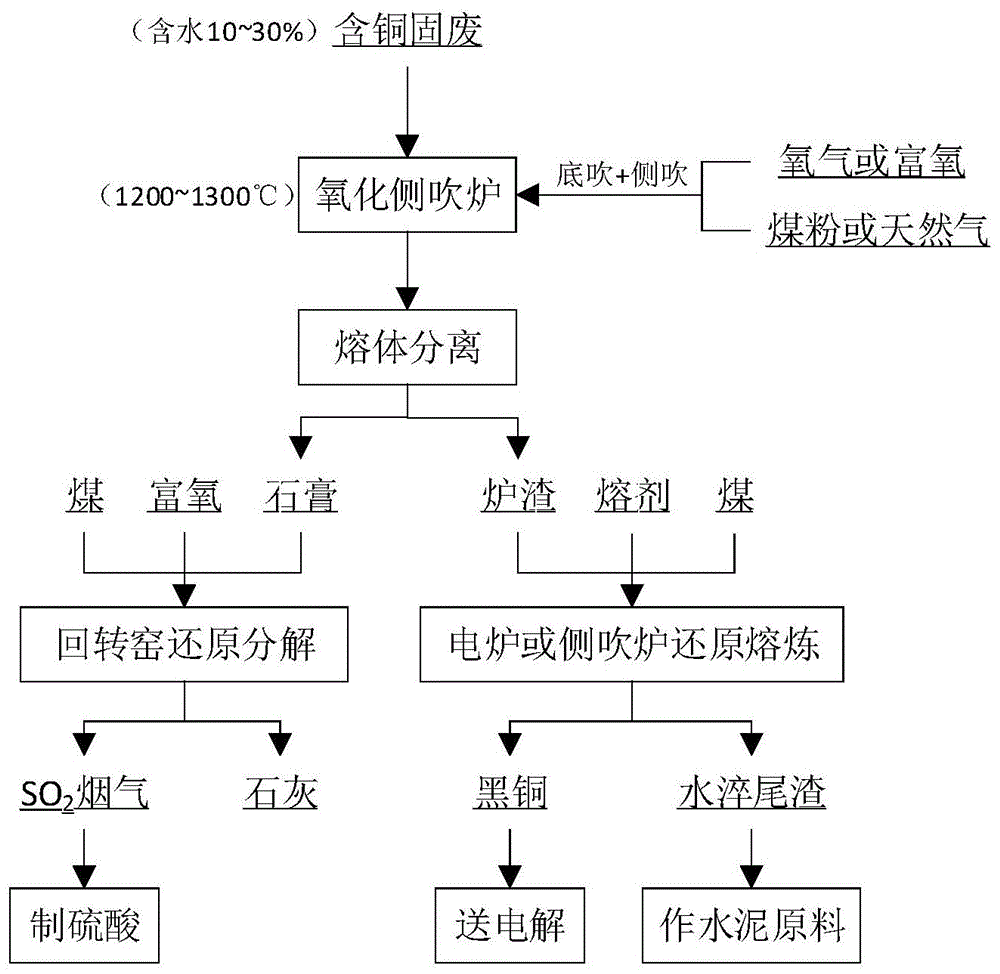
本发明属于固废处理
技术领域:
,具体地涉及一种含铜固废的分离方法。
背景技术:
:电镀行业因使用大量硫酸,在污水处理时以石灰中和沉降,所得的沉淀中除了含有大量的铜氧化物外,还有较多的硫酸钙。污泥经初步烘干后,则主要以cuo和caso4为主,一般将该含铜固废与其他含铜固废、熔剂等混合制块或造球,在侧吹炉或鼓风炉进行还原熔炼,产生黑铜时还有一部分冰铜,易造成熔体分层,分离不彻底,尾渣易夹杂硫化物,产出的黑铜和冰铜需再次分离,黑铜送去电解,冰铜送入吹炼炉,炉渣含铜在0.8%左右,一般作建材原料或堆弃。因此目前的工艺仅能在不影响产品指标的前提下少量掺混该类高钙、高硫的含铜固废,现有处理该类含铜固废的能力非常有限。申请号201611178461.3提出了一种含铜污泥的处理工艺。将含硫低于2%的含铜污泥低温烘干后制砖,与造渣剂和还原焦煤一同加入到富氧侧吹炉中产出次粗铜,含铜0.6%的尾渣经选矿再回收其残余铜,而对含硫高于2%的含铜污泥低温烘干后需进入矿铜冶炼系统中协同处理,其工艺与常规铜冶炼工艺相同。该工艺仅能单独处理硫含量较低的含铜污泥,而大部分含铜污泥中s含量均高于2%,含铜污泥中有机物、卤素等物质的引入会对矿铜冶炼系统带来负面影响,难以大比例掺混含铜污泥,该工艺原料适应性差,处理能力有限。因此,急需开发一种能够处理硫含量高于2%的含铜固废的分离方法,以提高该种含铜固废的处理能力。技术实现要素:本申请是基于发明人对以下事实和问题的发现和认识做出的:现有含铜固废火法处理工艺一般使用鼓风炉和侧吹炉进行还原熔炼。鼓风炉工艺处理含铜固废时,含铜固废与其他低硫原料混合制砖并晾晒脱水,然后进入鼓风炉进行还原熔炼,一般产出黑铜和冰铜,需再次分离将黑铜送电解,冰铜送吹炼,而尾渣含铜约0.8%,需进一步选矿贫化。但该工艺需要较长的预处理流程,如混料、压块、晾干等,鼓风炉顶部有大量挥发性有机物难以处理,所得产品分层需再次分选并送不同流程处理,尾渣含铜高,且利用困难。此外,鼓风炉工艺还存在单体处理能力小、工人劳动强度大、冶炼车间环保条件差等问题。侧吹炉工艺处理含铜污泥时,需将含铜污泥预先脱水至含水10%以下,并将其投入到侧吹熔炼炉内,采用富氧侧浸没燃烧的方式供热和还原,为防止喷枪烧损,喷枪需远离金属和铜锍层,采用不充分燃烧的方式保证体系的还原性,同时也难以将低于喷枪位置的渣、金属、铜锍中的硫化物氧化脱除,尾渣易夹杂铜锍颗粒,仍需缓冷后浮选贫化处理。目前鼓风炉和侧吹炉主要处理的物料中caso4含量较低,由于caso4在还原熔炼过程中的分解和还原会大量吸热且消耗还原剂,同时还需要大量的硅石来调整炉渣碱度,因此导致熔剂、还原剂及能源消耗均较大。对高caso4含量的含铜固废无法采用现有工艺处理,仅能在不影响冶炼指标的条件下少量掺混,导致大量此类含铜固废不能得到很好地利用。本发明旨在至少在一定程度上解决相关技术中的技术问题之一。为此,本发明实施例的目的在于提供一种含铜固废的分离方法,能够处理高钙、高硫、低硅、低铁特性的含铜固废,对原料预处理要求低,避免了深度烘干预处理的高温、高能耗、大烟尘量、有机物挥发量大等问题,具有显著的节能降耗效果,并且对含铜固废具有较大处理能力。为此,本发明实施例的一个方面提出了一种含铜固废的分离方法,包括如下步骤,a、将含铜固废制粒和烘干预处理,得到含铜固废颗粒;b、将所述含铜固废颗粒投入氧化侧吹炉熔池中,氧化侧吹炉熔池温度为1200-1300℃,所述含铜固废颗粒熔化,形成上层的石膏熔体和下层的含铜熔融炉渣。本发明上述实施例的含铜固废的分离方法具有如下有益效果:将含ca、s较高的含铜固废投入到氧化侧吹炉熔池中熔化,实现上部石膏熔体与下部含铜熔融炉渣的分离,含铜固废直接进入熔池,控制熔池内为氧化性气氛和较低温度(1200-1300℃),抑制了硫酸钙的分解,不仅避免了因硫酸盐分解的大量吸热,还可使污泥中有机物污染物彻底分解,含铜固废中过量的钙和硫以硫酸钙熔体的形式被分离出去,下层的含铜熔融炉渣由于大量的硫酸钙被预先分离出去,含铜炉渣在后续熔炼过程中熔剂及还原使用量将大幅减少,渣量显著降低,下层熔融炉渣再经还原可以获得黑铜产品,cu、ni等有价金属可综合回收且回收率高。在本发明的一些实施例中,所述步骤a中,烘干预处理后所述含铜固废颗粒的含水量低于30%,优选为10-30%。在本发明的一些实施例中,所述步骤b中,所述氧化侧吹炉熔池依次设置投料区、中间过渡区和出料区,所述投料区侧壁下方和底部设置喷枪,所述中间过渡区底部设置喷枪,所述出料区为静置沉降区,石膏熔体和含铜熔融炉渣在所述出料区沉降分离。在本发明的一些实施例中,所述喷枪采用水冷结构保护。在本发明的一些实施例中,所述步骤b中,向所述氧化侧吹炉熔池中喷吹煤粉或天然气,以及体积浓度为85-100%的氧气。在本发明的一些实施例中,所述步骤b中,所述氧化侧吹炉熔池上方为氧化性气氛。在本发明的一些实施例中,所述步骤b中,所述氧化侧吹炉熔池的烟气中o2体积浓度为5-10%。在本发明的一些实施例中,所述步骤b得到的石膏层送入回转窑内还原焙烧分解,得到石灰和so2烟气。在本发明的一些实施例中,所述步骤b中得到的含铜熔融炉渣送入电炉或侧吹炉,经还原熔炼得到黑铜和尾渣。附图说明图1是根据本发明实施例的含铜固废的分离方法的工艺流程图;图2是根据本发明的实施例的氧化侧吹炉的示意图。附图标记:10-氧化侧吹炉;1-熔池;2-喷枪;3-加料口;4-排烟口;5-排石膏口;6-排渣口。具体实施方式下面详细描述本发明的实施例,所述实施例的示例在附图中示出。下面描述的实施例是示例性的,旨在用于解释本发明,而不能理解为对本发明的限制。根据本发明实施例的一种含铜固废的分离方法,包括如下步骤,a、将含铜固废制粒和烘干预处理,得到含铜固废颗粒;b、将所述含铜固废颗粒投入氧化侧吹炉熔池中,氧化侧吹炉熔池温度为1200-1300℃,所述含铜固废颗粒熔化,形成上层的石膏熔体和下层的含铜熔融炉渣。本发明上述实施例的含铜固废的分离方法,将含ca、s较高的含铜固废投入到氧化侧吹炉熔池中熔化,实现上部石膏熔体与下部含铜熔融炉渣的分离,含铜固废直接进入1200-1300℃的熔池,不仅避免了因硫酸盐分解的大量吸热,还可使污泥中有机物污染物彻底分解,含铜固废中过量的钙和硫以硫酸钙熔体的形式被分离出去,下层的含铜熔融炉渣由于大量的硫酸钙被预先分离出去,含铜炉渣在后续熔炼过程中熔剂及还原使用量将大幅减少,渣量显著降低,下层含铜熔融炉渣再经还原可以获得黑铜产品,cu、ni等有价金属可综合回收且回收率高。根据本发明的一些实施例,所述步骤a中,烘干预处理后所述含铜固废颗粒的含水量低于30%,优选为10-30%。本发明实施例的方法无需将含铜固废烘干至10%以下,只要把含铜固废烘干至含水30%以下即可,对原料烘干要求低,避免了深度烘干预处理的高温、高能耗、大烟尘量、有机物挥发量大等问题。根据本发明的一些实施例,所述步骤b中,所述氧化侧吹炉熔池依次设置投料区、中间过渡区和出料区,所述投料区侧壁下方和底部设置喷枪,所述中间过渡区底部设置喷枪,所述出料区为静置沉降区,石膏熔体和含铜熔融炉渣在出料区沉降分离。本发明实施例的方法中,投料区使用侧吹和底吹喷枪,喷枪数量较多,供热强度和熔池搅拌强度大;中间过渡区主要通过底吹喷枪喷吹燃料供热,维持熔池温度,熔池搅动逐渐趋于缓和;出料区为静置沉降区域,不设置喷枪,无喷枪喷吹,主要为促进含铜熔融炉渣与石膏熔体两相的沉降分离。在氧化侧吹炉中间过渡区及出料区附近区域,出现上层石膏熔体和下层含铜熔融炉渣两相分层,炉渣以cu2o-cao-sio2-fe2o3-al2o3-mgo多元渣系为主,石膏以caso4为主。根据本发明的一些实施例,所述喷枪采用水冷结构保护。本发明实施例的方法中,喷枪接触的位置为炉渣,使用水冷结构可以保护喷枪,同时水冷挂渣也能减少热量的散失,有利于延长喷枪寿命。根据本发明的一些实施例,所述步骤b中,向所述氧化侧吹炉熔池中喷吹煤粉或天然气,以及体积浓度为85-100%氧气。本发明实施例的方法中,喷吹高浓度氧气,有利于减少氧化侧吹炉中喷入的煤粉用量,并提高含铜熔融炉渣中cu、ni等有价金属的含量,有利于cu、ni等有价金属的回收。根据本发明的一些实施例,所述步骤b中,所述氧化侧吹炉熔池上方为氧化性气氛,烟气中o2体积浓度为5-10%。本发明实施例中的方法,在喷枪喷吹的过程中控制氧过剩,使熔池上方为氧化性气氛,主要以co2、o2和n2为主,烟气中o2浓度控制在5-10%,使含铜固废在氧化性条件下升温熔化形成熔融石膏层和含铜熔融炉渣层,有利于提高含铜熔融炉渣层中cu、ni等有价金属的含量。在本发明的一些实施例中,所述步骤b得到的上层石膏送入回转窑内还原焙烧分解,得到石灰和so2烟气。本发明实施例中分离出的石膏可在回转窑内还原分解,热态入炉减少了能量消耗,产出的石灰可再次被回收,烟气可制硫酸,实现了钙和硫元素的回收利用。分离出的熔融态石膏,冷却至800-900℃后,可以在电炉或侧吹炉内继续熔炼,向其中加入铁尾矿,通过sio2和fe2o3与cao结合成硅酸钙(cao·sio2)和铁酸钙(cao·fe2o3),促进石膏的分解产生so2。反应如下:2caso4+2sio2=2cao·sio2+2so2+o22caso4+fe2o3=cao·fe2o3+2so2+o2由于此时电极供热或燃料燃烧,可控制炉内气氛为弱氧化性气氛,可以进一步促进硫酸钙的分解。反应如下:caso4+sio2+co=cao·sio2+so2+co22caso4+fe2o3+co=cao·fe2o3+2so2+co2在电炉或侧吹炉内最终形成cao-sio2-feox的低熔点渣系,尾渣水淬后可作为建材原料。根据本发明的一些实施例,所述步骤b中得到的含铜熔融炉渣送入电炉或侧吹炉,经还原熔炼得到黑铜和尾渣。本发明实施例的方法中,将得到的熔融炉渣送入电炉或侧吹炉进行还原熔炼时,还原熔炼温度为1300-1400℃,通过加入还原剂和熔剂,可还原出黑铜产品和水淬渣,烟气为还原性,经二次燃烧后经余热锅炉回收余热,再经除尘后排放。下面参考附图1和2描述本发明的具体实施例。下面实施例中使用的含铜固废经制粒和烘干预处理后,呈颗粒状,其成分见表1,以质量百分含量计,其中,物料中含水量为12.5%。表1cutfefeosnicaosio2mgoal2o3cco2h2o16.787.078.765.551.9015.642.921.511.624.7616.512.5其中,硫主要以硫酸盐形式存在;钙主要以碳酸钙和硅酸钙形式存在;铜主要以硫酸铜和氧化铜的形式存在;碳主要以有机碳、游离碳和碳酸盐形式存在。如图2所示,本发明实施例中采用的氧化侧吹炉10的熔池1依次设置投料区i、中间过渡区ii和出料区iii,投料区i侧壁下方和底部设置喷枪2,中间过渡区ii侧壁设置喷枪2,出料区iii为静置沉降区,投料区i上方设置投料口3,出料区iii上方设置排烟口4,出料区iii侧壁中部石膏层处设置排石膏口5,出料区iii侧壁下方设置排渣口6。氧化侧吹炉10中的喷枪2采用水冷结构。实施例1经预处理后的含铜固废颗粒通过氧化侧吹炉10的投料口3直接投入至熔池1的投料区i中,投料区i侧壁和底部的喷枪2向熔池内喷吹煤粉和富氧(氧气的体积浓度为86.96%),熔池温度为1200-1300℃,由于投料区i侧壁和底部均设置喷枪,喷枪数量较多,供热强度和熔池搅拌强度大,含铜固废在熔池1的投料区i中熔融,之后进入中间过渡区ii,中间过渡区ii底部的喷枪2向熔池内喷吹煤粉和富氧,维持熔池温度,熔池搅动逐渐趋于缓和,之后熔体进入出料区iii,出料区iii不设置喷枪,无喷枪喷吹,为静置沉降区,熔体分层,上层为以caso4为主的石膏熔体,下层为以cu2o为主的多种金属氧化物组成的炉渣,石膏熔体和含铜熔融炉渣在出料区iii实现沉降分离。熔池1维持氧化性氛围,排烟口6排出的烟气中o2体积含量为6.5%。经出料区iii沉降分离后,上层石膏熔体通过排石膏口5排出,下层含铜熔融炉渣通过排渣口6排出。处理每吨含铜固废消耗无烟煤60kg,空气33nm3(部分作为无烟煤载气),氧气200nm3,可产出石膏熔体270kg,熔融炉渣400kg,石膏和炉渣主要成分见表2,以质量百分含量计。表2成分cufesnicaosio2上层石膏5.712.2017.320.2639.841.14下层炉渣37.116.001.044.5414.646.79下层的熔融炉渣倒入熔炼电炉内,每吨渣配加无烟煤85kg,硅石110kg,每吨炉渣还原熔炼可得黑铜440kg,尾渣500kg,所得黑铜和尾渣成分见表3,以质量百分含量计。表3成分cufeniscaosio2黑铜82.144.909.872.29--尾渣0.3527.50.02-28.134.2上层石膏在回转窑内进行还原焙烧,每吨石膏可分解得到石灰600kg,其中cao质量含量为63.08%。采用本实施例的方法处理10万吨含铜固废,将消耗0.94万吨无烟煤,0.44万吨硅石,将产出1.76万吨黑铜,2万吨水淬渣,1.62万吨石灰。铜回收率达到86.15%,镍回收率达到91.43%。实施例2与实施例1的方法相同,不同之处在于,喷吹富氧体积浓度为95.79%,烟气中o2体积含量为7.3%。处理每吨含铜固废消耗无烟煤55kg,空气13nm3(部分作为无烟煤载气),氧气180nm3,可产出石膏熔体270kg,熔融炉渣400kg,石膏和炉渣主要成分见表4,以质量百分含量计。表4成分cufesnicaosio2上层石膏4.772.5417.660.2240.610.75下层炉渣38.1815.880.764.5112.767.92下层的熔融炉渣倒入侧吹熔炼炉内,每吨渣配加无烟煤120kg,硅石95kg,每吨炉渣还原熔炼可得黑铜450kg,尾渣480kg,所得黑铜和尾渣成分见表5,以质量百分含量计。表5成分cufeniscaosio2黑铜84.122.979.91.69--尾渣0.4129.10.03-26.135.1上层石膏在回转窑内进行还原焙烧,每吨石膏可分解得到石灰600kg,其中cao含量为64.30%。采用本实施例的方法处理10万吨含铜固废,将消耗1.75万吨无烟煤,0.38万吨硅石,将产出1.8万吨黑铜,1.92万吨水淬渣,1.62万吨石灰。铜回收率达到87.73%,镍回收率达到91.18%。实施例3与实施例1的方法相同,不同之处在于,喷枪喷吹的为氧气,烟气中的o2体积含量为9.76%。处理每吨含铜固废消耗无烟煤50kg,空气3nm3(作为无烟煤载气),氧气160nm3,可产出石膏熔体270kg,熔融炉渣400kg,石膏和炉渣主要成分见表6,以质量百分含量计。表6成分cufesnicaosio2上层石膏4.372.7918.210.2539.610.97下层炉渣38.7214.810.964.8713.988.76下层的熔融炉渣倒入侧吹熔炼炉内,每吨渣配加无烟煤110kg,硅石85kg,每吨炉渣还原熔炼可得黑铜460kg,尾渣480kg,所得黑铜和尾渣成分表7,以质量百分含量计。表7成分cufeniscaosio2黑铜82.63.279.982.08--尾渣0.4727.5-0.0228.834.8上层石膏在回转窑内进行还原焙烧,每吨石膏可分解得到石灰570kg,其中cao含量为63.93%。采用本实施例的方法处理10万吨含铜固废,将消耗0.94万吨无烟煤,0.34万吨硅石,将产出1.82万吨黑铜,1.92万吨水淬渣,1.54万吨石灰。铜回收率89.59%,镍回收率95.60%。本说明书的描述中,术语“含铜固废”是指铜含量大于10%,且硫、钙含量高,硅、铁含量低的含铜固废,例如:cao>10%,s>2%,或,caso4>15%;sio2<5%,fe<10%。在本说明书的描述中,参考术语“一个实施例”、“一些实施例”、“示例”、“具体示例”、或“一些示例”等的描述意指结合该实施例或示例描述的具体特征、结构、材料或者特点包含于本发明的至少一个实施例或示例中。在本说明书中,对上述术语的示意性表述不必须针对的是相同的实施例或示例。而且,描述的具体特征、结构、材料或者特点可以在任一个或多个实施例或示例中以合适的方式结合。此外,在不相互矛盾的情况下,本领域的技术人员可以将本说明书中描述的不同实施例或示例以及不同实施例或示例的特征进行结合和组合。尽管上面已经示出和描述了本发明的实施例,可以理解的是,上述实施例是示例性的,不能理解为对本发明的限制,本领域的普通技术人员在本发明的范围内可以对上述实施例进行变化、修改、替换和变型。当前第1页12