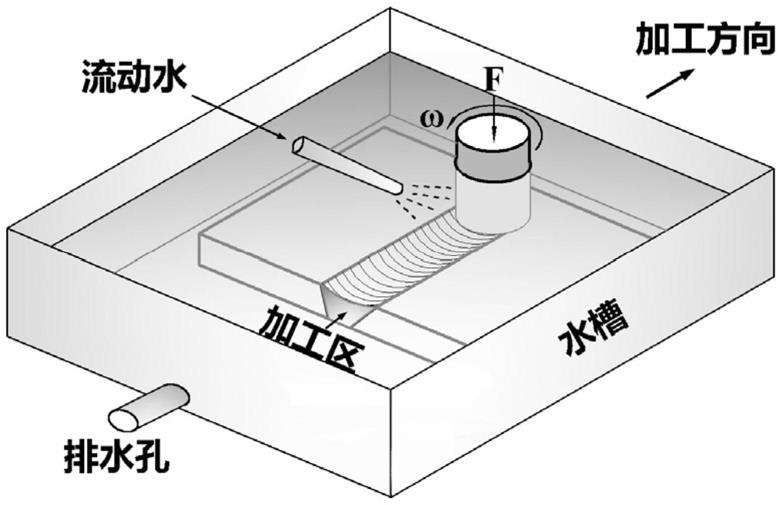
1.本发明涉及高强韧钢铁材料制备技术领域,具体涉及一种同步提升低碳钢强度和塑性的塑性变形加工工艺。
背景技术:2.为了满足轻质高强的应用要求,钢铁材料制备正在向不断提升强度的方向发展,但是提升材料强度的同时常常伴随其塑性的损失,进而降低其后续的可加工性、成形性和服役性能,严重制约高强材料的推广应用。与此同时,节能减排、节约资源和可持续发展目标要求材料不断“素化”,即保证材料强度的同时尽可能降低其合金含量。因此,先进的高强高塑性低碳钢(包括添加少量廉价合金元素的低碳低合金钢)成为国内外材料工作者的研究热点。
3.目前工业中普遍采用细晶强化和多相组织耦合来提升强度和塑性,主要包括先进热机械加工(atmp)和大塑性变形(spd)+退火处理两种工艺。atmp便于批量生产,工业应用背景广,但是塑性变形程度有限,晶粒细化效果一般不及spd+退火工艺;而spd技术虽然具有较高的晶粒细化能力,但是所制备材料的稳定性不高,且样品尺寸受限,不易实现批量化生产。虽然采用上述两种工艺均可制备出具有超细平均晶粒尺度(<1μm)的铁素体、铁素体+碳化物和铁素体+马氏体等双相组织,并且使低碳钢材料的强度提升到1gpa以上;但是这些超细材料的塑性并不够高,单轴静态拉伸过程的总延伸率均在15%以下,严重限制其后续的加工和服役性能。然而,fcc结构的奥氏体相在塑性变形过程中具有相变诱发塑性(trip)效应,有望进一步提升超细晶材料的塑性。但是奥氏体需要碳、锰、铬等合金元素增加其稳定性才能存在于室温下,因此常规制备工艺得到的低碳低合金钢中较难引入奥氏体。
4.搅拌摩擦加工(fsp)是一种基于搅拌摩擦焊(fsw)的新型材料改性工艺,其利用一种由轴肩和搅拌针组成的搅拌工具旋转压入工件产生热塑性变形,并伴随搅拌工具的移动形成加工区,具有晶粒细化效果显著、可大面积加工和加工区组织均匀稳定等特点。近年来,低热输入搅拌摩擦加工技术得到了迅速发展,其通过控制加工参数和附加冷却介质来进一步降低热输入,以实现提升晶粒细化效果和控制相变等目的。不同碳钢的fsw研究表明,通过降低工具转速、提升工具行进速度或施加液态co2冷却可成功将焊核区组织降低至超细晶尺度,同时提升其硬度和强度,(materials science and engineering:a,2006.429:p.50-57;scripta materialia,2007.56:p.637-640;journal of materials processing technology,2016.230:p.62-71)。近年来,有学者通过采用tic陶瓷无针工具和强制水冷工艺(工具转速400转/分钟,行进速度50毫米/分钟)在普通低碳钢搅拌摩擦加工加工区得到了超细铁素体/马氏体双相组织。由于马氏体的存在,加工区组织强度可达母材的两倍以上;但由于马氏体塑性差,且所制备铁素体含量较少等原因,其延伸率损失较为严重,仅为母材的50%(materials science and engineering:a,2013.575:p.30-34)。
5.相较于常规搅拌摩擦加工,低热输入搅拌摩擦加工对搅拌工具的选材和设计要求更高,工具成本高、易损坏和加工区难成形是目前出现的主要问题。在工具选材上,目前较
多使用的钨基合金和氮化硼陶瓷虽具有足够的强度,但成本高昂;而wc陶瓷虽成本较低,但具有低温脆性问题。在工具设计上,搅拌针的存在使得低热输入过程中材料塑性流动不均匀性更加突出,很容易带来因材料回填不充分造成的孔洞、隧道等缺陷;无针工具仅靠轴肩下压成型,可消除搅拌针带来的缺陷,但其加工层深度受限,很难实现大面积加工制备。在组织控制上,上述塑性加工方法制备的组织均以bcc结构相(铁素体/马氏体/珠光体)为主,而这些相在超细晶尺度范围内的塑性变形能力非常有限,从而导致目前超细低碳钢铁材料高强、低塑性的普遍特点。
6.发明目的
7.本发明的目的在于提供一种同步提升低碳钢强度和塑性的塑性变形加工工艺,通过对现有的搅拌摩擦加工参数和工具进行优化改进,并结合合理的后续热处理工艺调控组织相成分,最终在加工区制备出兼具高强和高塑性的低合金低碳钢铁材料。
8.一种同步提升低碳钢强度和塑性的塑性变形加工工艺,该工艺是对低碳钢母材进行水下搅拌摩擦加工,在加工区得到超细铁素体/马氏体双相组织;再对加工区进行两相区短时低温退火处理与随后的水淬冷却处理,最终在加工区得到兼具高强度和高塑性的低碳钢。
9.所述低碳钢的化学成分以重量百分比计为:c 0.1-0.2%,si 1.0-2.0%,mn 2.5-3.0%,s<0.006%,p<0.007%,al<0.04%,cr<0.013%,余量为fe和其他微量杂质。
10.所用搅拌摩擦加工工具为无针搅拌头,材质为tic基金属陶瓷或ti(c,n)基金属陶瓷,搅拌头自由端形状为半球状凸起结构,半球状凸起结构对应的球体半径为5-10毫米,加工深度为0.5-5毫米。
11.所述搅拌摩擦加工工艺参数为:工具转速200-300转/分钟,行进速度25-200毫米/分钟。
12.所述搅拌摩擦加工过程中采用流动水对加工区进行冷却,如可采用普通水管进行注水对加工区进行冷却,水管出水口直径5-15毫米,水流速2-5升/分钟,出水口水温为15-25℃。
13.为在加工区获得超细晶组织并生成奥氏体相,采用不同于常规热处理工艺的两相区低温短时退火处理,退火温度为710-730℃,保温时间为5-15分钟;为将奥氏体保留至室温,采用低温淬火工艺,淬火处理中冷却水温度为10-20℃,转移速度≤7秒。
14.所述低碳钢母材经搅拌摩擦加工、两相区低温短时退火处理和水淬冷却处理后,所得的加工区组织由铁素体、马氏体、奥氏体和碳化物多相组织组成,多相组织平均晶粒尺寸为0.2μm-1μm。其中马氏体岛平均尺寸为0.5μm-1μm,相比例为20%-40%(体积分数);奥氏体平均晶粒尺寸为0.2μm-1μm,相比例为5%-15%(体积分数);碳化物平均尺寸为0.05μm-0.1μm,相比例为1%-3%(体积分数)。
15.本发明的有益效果是:
16.1、本发明提出了一种同步提升低碳钢强度和塑性的塑性加工工艺,该工艺采用低热输入搅拌摩擦加工工艺,该工艺通过降低工具转速和施加冷却水两种方式协同控制加工过程的热输入,能够得到晶粒显著细化的超细晶铁素体/马氏体两相组织。再通过两相区(710-730℃)短时(10分钟)低温退火处理,并伴随冷却水(15℃)淬火处理,可在加工区中得到铁素体/马氏体/奥氏体/碳化物多相组织。该组织各相平均晶粒尺寸均小于1μm,其中马
氏体岛占比为20%-40%,奥氏体相占比为5%-15%,碳化物相占比为1%-3%(体积分数);通过细晶强化、多相耦合和trip效应,加工区组织的强度和塑性相较母材均有较大提升。
17.2、本发明采用的低热输入搅拌摩擦加工工艺中,搅拌头材质选用成本低廉、低温韧性和耐磨性均较好的金属陶瓷材料制成,大大降低了生产成本。通过选用改进设计的凸形球状搅拌工具可消除由搅拌针带来的孔洞、隧道等成形缺陷,改善加工区成形性,扩大加工区面积;无棱角设计可大幅降低工具磨损,提升工具寿命,同时可提升加工过程设备的稳定性。
18.3、与现有高强低碳钢铁材料制备方法相比,本发明可明显提升加工区材料的综合力学性能,工艺过程简单易用、生产成本低、效率高,在低碳及低碳低合金钢铁材料制备领域具有广阔的应用前景。
附图说明
19.图1为本发明所采用的低热输入搅拌摩擦加工工艺过程示意图。
20.图2为实施例1中采用低热输入搅拌摩擦加工(加工参数为275转/分钟、50毫米/分钟,冷却介质为室温流动水)并辅以短时低温退火(720℃保温10分钟)和水淬(水温15℃,转移时间3秒)所制备的高强高塑性加工区组织的典型扫描电镜形貌。
21.图3为实施例1中加工区组织x射线衍射(xrd)测试结果,射线源为cu靶,扫描速度为4度/分钟。
22.图4为实施例1中加工区组织和未加工母材的典型拉伸曲线对比图,初始拉伸应变速率均为1
×
10-3
s-1
。
具体实施方式
23.以下结合附图和实施例详述本发明。
24.本发明利用低热输入搅拌摩擦加工技术和短时退火工艺在提升低碳钢铁材料强度的同时大幅提升其塑性,制备出强塑性兼优的低碳钢铁材料。
25.本发明中所采用的低热输入搅拌摩擦加工工艺过程如图1所示。所用搅拌摩擦加工工具为无针搅拌头,工具材质为tic基金属陶瓷或ti(c,n)基金属陶瓷,如文献1中公开的mo含量4wt.%、tin含量6wt,%的ti(c,n)/nicrmoalti金属陶瓷(文献1:王全兆,高性能ti(c,n)/nicrmoalti金属陶瓷制备及与钢的连接研究[d].中国科学院金属研究所.2007.)。搅拌头自由端设计为半球状凸起结构,半球状凸起结构对应的球体半径为5-10毫米,加工深度为0.5-5毫米。搅拌摩擦加工过程在水槽中进行,水槽底面作为加工平台,工件置于加工平台上。采用普通水管输出流动水对加工区进行冷却,水温为15-25℃,水管出水口直径5-15毫米,水流速2-5升/分钟。
[0026]
实施例1
[0027]
使用3毫米厚的普通低碳低合金钢板,其化学成分以重量百分比计为:c 0.16%,si 1.58%,mn 2.75%,s 0.005%,p 0.006%,al 0.039%,cr 0.012%,余量为fe。如图4中的拉伸曲线所示,母材的抗拉强度为744mpa,均匀延伸率为17.5%,总延伸率为31%。采用半径为7毫米的凸球型金属陶瓷搅拌头进行搅拌摩擦加工,工具转速275转/分钟,行进速度50毫米/分钟;加工过程采用流动水对加工区进行冷却,施加流动水所采用的水管出水口
直径8毫米,流速2.2升/分钟,出水口水温为18℃,加工层深度为1.5毫米。加工后对加工区进行两相区低温退火处理,温度为720℃,保温时间为10分钟。随后对退火组织进行淬火,淬火介质为15℃自来水,转移速度为3秒。组织表征显示加工区组织由铁素体/马氏体/多边形奥氏体/碳化物组成(图2),平均晶粒尺寸为0.6μm,马氏体相含量约为30%,碳化物相含量约为1.8%,xrd分析表明奥氏体相含量约为10.6%(图3);由于采用了低热输入搅拌摩擦加工+低温短时退火工艺,加工区组织抗拉强度为1016mpa,相对母材提升36%,均匀延伸率和总延伸率分别为30.3%和39.1%,相对母材分别提升73%和31%(图4)。
[0028]
对比例1
[0029]
与实施例1不同之处在于,本实施例未采用凸形球状搅拌工具进行加工,而是采用了带有搅拌针的常规工具,具体方法如下:
[0030]
使用与实施例1相同板厚、成分和力学性能的低碳低合金钢板。采用轴肩直径12毫米、搅拌针根部直径和长度分别为5毫米和2毫米的金属陶瓷搅拌头进行搅拌摩擦加工,工具转速275转/分钟,行进速度50毫米/分钟;加工过程采用流动水对加工区进行冷却,施加流动水所采用的水管出水口直径8毫米,流速2.2升/分钟,出水口水温为18℃。由于搅拌工具未采用凸形球状设计,加工过程中搅拌针从根部断裂失效,无法继续进行加工;已加工的区域底部存在大量孔洞和明显隧道,且加工区宽度不足5毫米。
[0031]
对比例2
[0032]
与实施例1不同之处在于,本实施例并未采用水冷工艺对加工区进行辅助冷却,具体方法如下:
[0033]
使用与实施例1相同板厚、成分和力学性能的低碳低合金钢板,工具材质、尺寸和加工参数也与实施例1相同。加工过程中未采用强制水冷,而是使加工区在空气中自然冷却。随后对加工区组织在720℃保温10分钟,并在温度为15℃的自来水中做淬火处理,转移速度为3秒。由于未采用水冷工艺进行强制冷却,最终加工区组织平均晶粒尺寸较大,为6μm左右;奥氏体相含量较低,约为2%;均匀延伸率和总延伸率分别为20.2%和37.8%,相对母材有少量提升,但其抗拉强度仅为710mpa,相对母材并未有所提升。
[0034]
对比例3
[0035]
与实施例1不同之处在于,本实施例并未对加工区组织进行退火处理,具体方法如下:
[0036]
使用与实施例1相同板厚、成分和力学性能的低碳低合金钢板,工具材质、尺寸、加工参数和辅助冷却工艺也与实施例1相同。加工后未对加工区组织进行退火处理。在加工区获得的组织平均晶粒尺寸小于1μm,为铁素体/马氏体双相组织。由于未经后续退火处理调控相成分,加工区未检测到奥氏体相的存在,而马氏体相含量高达90%以上,拉伸测试结果表明加工区组织抗拉强度为1825mpa,为母材的1.4倍,但塑性相对母材大幅降低,均匀延伸率低于3%,总延伸率低于10%。
[0037]
对比例4
[0038]
与实施例1不同之处在于,本实施例采用了较高温度的退火处理,且缩短了退火时间,具体方法如下:
[0039]
使用与实施例1相同板厚、成分和力学性能的低碳低合金钢板,工具材质、尺寸、加工参数和辅助冷却工艺也与实施例1相同。加工后对加工区组织进行两相区中温退火处理,
温度为740℃,保温时间为3分钟。随后对退火组织进行淬火,淬火介质为15℃自来水,转移速度为3秒。由于所采用的退火工艺不合理,在最终的加工区中未检测到马氏体和奥氏体相的存在,而碳化物相含量高达4%以上;力学测试表明加工区组织抗拉强度为1029mpa,相对母材提升33%,但塑性相对母材大幅降低,均匀延伸率低于1%,总延伸率低于15%。
[0040]
实施例2
[0041]
使用4毫米厚的普通低碳低合金钢板,其化学组分以重量百分比计为:c 0.12%,si 1.05%,mn 2.07%,s 0.004%,p 0.003%,al 0.021%,cr 0.007%,余量为fe;其抗拉强度、均匀延伸率和总延伸率分别为857mpa、15%和22%。采用半径为10毫米的凸球型金属陶瓷搅拌头进行搅拌摩擦加工,工具转速220转/分钟,行进速度30毫米/分钟;加工过程采用流动水对加工区进行冷却,水管出水口直径8毫米,流速2.5升/分钟,出水口水温为19℃。加工后对加工区进行两相区低温退火处理,温度为710℃,保温时间为10分钟。随后对退火组织进行淬火,淬火介质为15℃自来水,转移速度为5秒。由于采用了改进的加工工具、较低的加工参数和合理的退火工艺,最终得到的加工区组织平均晶粒尺寸小于1μm,并含有约6%奥氏体相,38%马氏体相;抗拉强度为1200mpa,相对母材提升40%,均匀延伸率和总延伸率分别为21%和31%,相对母材分别提升40%和41%。
[0042]
实施例3
[0043]
使用4毫米厚的普通低碳钢板,其化学组分以重量百分比计为:c 0.20%,si 1.34%,mn 2.25%,s 0.004%,p 0.005%,al 0.030%,cr 0.006%,余量为fe;其抗拉强度、均匀延伸率和总延伸率分别为550mpa、20%和34%。采用半径为5毫米的凸球型金属陶瓷搅拌头进行搅拌摩擦加工,搅拌头转速300转/分钟,行进速度100毫米/分钟;加工过程对加工区冷却所采用的水管出水口直径为8毫米,流速为2.5升/分钟。加工后对加工区进行两相区退火处理,温度为720℃,保温时间为15分钟。随后对退火组织进行淬火,淬火所用自来水水温为15℃,转移时间为5秒。微观组织观察表明最终所得加工区组织的平均晶粒尺寸接近1μm,所含奥氏体相体积分数约为8%,马氏体相体积分数约为33%,碳化物相体积分数约为2.1%;拉伸结果表明加工区组织的抗拉强度为930mpa,相对母材提升69%,均匀延伸率和总延伸率分别为35%和44%,相对母材分别提升75%和29%。
[0044]
实施例4
[0045]
使用3毫米厚的普通低碳钢板,其化学组分以重量百分比计为:c 0.11%,si 1.75%,mn 2.05%,s 0.004%,p 0.006%,al 0.020%,cr 0.006%,余量为fe;其抗拉强度、均匀延伸率和总延伸率分别为600mpa、25%和29%。采用半径为7毫米的凸球型金属陶瓷搅拌头进行搅拌摩擦加工,搅拌头转速275转/分钟,行进速度100毫米/分钟;加工过程所采用的冷却水管出水口直径8毫米,流速2.5升/分钟。加工后对加工区进行两相区退火处理,温度为710℃,保温时间为5分钟。随后对退火组织进行淬火,淬火所用自来水水温为15℃,转移时间为5秒。微观组织观察表明最终所得加工区组织的平均晶粒尺寸约为0.7μm,所含奥氏体相体积分数约为14%,马氏体相体积分数约为39%,碳化物相体积分数约为1.7%;拉伸结果表明加工区组织的抗拉强度为1300mpa,相对母材提升117%,均匀延伸率和总延伸率分别为28%和33%,相对母材分别提升12%和14%。
[0046]
对比例4
[0047]
与实施例4不同之处在于,本实施例在搅拌摩擦加工过程中采用了较高的热输入
参数,具体方法如下:
[0048]
使用与实施例4相同板厚、成分和力学性能的普通低碳钢板,工具材质、尺寸和行进速度也与实施例4一致,但工具转速增加到了400转/分钟。加工过程对加工区进行强制冷却,工艺同实施例4。加工后搅拌头表面可发现肉眼可见裂纹,且存在明显的磨损现象。随后对加工区组织进行与实施例4相同的退火和淬火处理。对最终加工区进行组织观察发现其中存在明显的磨损颗粒,平均晶粒尺寸接近1μm;拉伸测试结果表明加工区组织的抗拉强度为900
±
100mpa,虽相对母材有一定程度提升,但由于磨损颗粒的引入使强度波动较为明显;均匀延伸率和总延伸率分别为17%和19%,相对母材均显著降低。