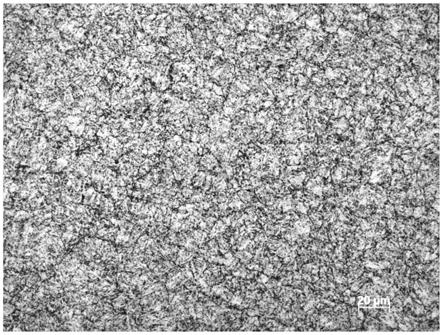
1.本发明涉及一种油套管及其制造方法,尤其涉及一种耐腐蚀的油套管及其制造方法。
背景技术:2.在油气资源中,许多油气田均含有co2、h2s等腐蚀性气体,这些腐蚀性气体严重威胁着油气井管柱的安全。随着石油管行业的发展,近年来已研发出适用于co2、h2s等环境的油套管,比如耐co2腐蚀油套管(3cr/13cr油套管)和抗h2s油套管(抗硫管),其基本可以满足co2、h2s工况油气田的开采开发。然而,需要说明的是,除co2和h2s腐蚀外,很多油气田还面临硫酸盐还原菌腐蚀(srb)、腐生菌(tgb)的风险。
3.随着油田开采时间的延长,油层本身能量将不断地被消耗,这会致使油层压力不断地下降,地下原油大量脱气,粘度增加,油井产量将会大大减少,甚至会停喷停产,从而会造成地下残留大量死油采不出来。在油气资源开采过程中,为了弥补原油采出后所造成的地下亏空,保持或提高油层压力,常常需要对油田进行注水作业,从而实现油田高产稳产,有效提高油藏的采收率。
4.然而,从便捷性和经济性考虑,注水作业中大量使用的水通常来自油田附近河水、湖泊水等。然而,通常来讲,河水、湖泊水以及采出水中含有较高含量的微生物,尤其是硫酸盐还原菌、腐生菌等。
5.硫酸盐还原菌、腐生菌等微生物能够导致油套管严重的腐蚀穿孔失效事故。根据美国1项腐蚀损失调查表明,微生物腐蚀约占所有金属和建筑材料腐蚀破坏的20%;而在生产油井腐蚀方面,77%以上由细菌造成,其特征是腐蚀穿孔。
6.国内外学者已对硫酸盐还原菌腐蚀机理进行了长期研究,目前有阴极去极化机理、浓差电池理论、代谢产物腐蚀理论、沉积物下的酸腐蚀机理、阳极区固定机理等,由于有大量证据分别支持上述的几种腐蚀机理,每种机理都有其合理性,因此还不能断定硫酸盐还原菌在腐蚀过程中的作用是初级作用(即直接影响阴极动力学)还是次级作用(即硫化物的促进作用)。然而生物膜是目前公认的导致发生微生物腐蚀的主要因素之一,即微生物附着于材料表面并形成生物膜,是材料腐蚀过程中的重要步骤。生物膜内是富含不溶性硫化物、低分子有机酸、高分子胞聚糖所组成的复杂混合物,因此生物膜可以与金属表面发生复杂的电化学反应。如果生物膜被抑制或破坏,微生物腐蚀发生的概率将大大减少,因此,控制微生物腐蚀的有效途径之一便是控制生物膜在材料表面的形成和成长。
7.生物膜可以通过以下几种方式影响腐蚀反应的发生:(1)影响电化学腐蚀中的阳极或阴极反应,分泌能够促进阴极还原的酶;(2)改变了腐蚀反应类型,由均匀腐蚀可能转变为局部腐蚀;(3)微生物新陈代谢产生促进或抑制金属腐蚀的化合物;(4)生成生物膜结构,创造了生物膜内的腐蚀环境,改变金属表面状态。生物电化学领域的研究表明,附着在金属表面的生物膜内的细菌,可通过直接电子转移(细胞膜上的电子转运蛋白)或间接电子转移(自身分泌的生物小分子电子转移载体)从金属获得电子,从而导致金属发生微生物腐
蚀。
8.然而,需要注意的是,除了需要面临硫酸盐还原菌、腐生菌等微生物腐蚀穿孔风险外,较多油田注水作业井还含有一定含量的co2腐蚀气体及cl-腐蚀离子。根据现有文献及专利可知,co2和cl-也会引起油套管腐蚀穿孔问题。近年来由于co
2-srb-cl-共存环境导致的油套管破漏事故频发,而单纯抗co2/h2s腐蚀的抗腐蚀油套管不能有效解决co
2-srb-cl-共存环境所导致的穿孔问题。基于此,油气田行业迫切希望能获得一种抗二氧化碳及硫酸盐还原菌腐蚀的油套管产品。
9.公开号为cn1401809a,公开日为2003年3月12日,名称为“抗二氧化碳腐蚀的低合金钢及油套管”的中国专利文献公开了一种油套管,其化学元素组成为:c 0.01~0.30%,si 0.1~1.0%,mn 0.10~2.0%,cr 0.5~5.0%,mo0.01~1.0%,cu 0.05~2.0%,ni 0.05~1.0%,al 0.005~0.1%;还可含有稀土0.005~0.25%和w 0.01~1.0%中任意的一种或二种;其余为fe和不可避免的杂质组成,其组织为索氏体,其用于制造油气井油套管,抗co2腐蚀性能好、成本低。该油套管虽然抗co2腐蚀性能优异,然而不具有耐srb腐蚀性能。
10.公开号为cn101082112a,公开日为2007年12月5日,名称为“110ksi级抗co2、h2s腐蚀油井管及制造方法”的中国专利文献公开了一种油套管及其制造方法,其化学元素组成为:c 0.20~0.35%,si 0.10~1.0%,mn 0.10~1.0%,cr 1.0~2.5%,mo 0.1~1.0%,ni 0.1~1.0%,nb 0.01~0.1%,cu 0.10~1.0%,al 0.01~0.10%,其余为fe和不可避免的杂质。该110ksi高钢级、经济型油套管钢抗硫性能按照nace0177-96a法标准在加载90%、95%名义屈服强度下经过720小时不开裂,抗co2腐蚀性能比常规产品提高5倍以上,其虽然具备优异的抗co2和h2s腐蚀性能,然而不具有抗co
2-srb腐蚀性能。
11.公开号为cn101096744a,公开日为2008年1月2日,名称为“高钢级高抗二氧化碳、氯离子腐蚀油套管用钢及制造方法”的中国专利文献公开了一种油套管及其制造方法,特别涉及一种110ksi高钢级抗高温(120~150℃)、高抗co2、氯离子腐蚀条件下的油井管用钢及其制造方法,其化学元素组成为:c 0.15~0.25%,si 0.2~0.5%,mn 0.20~1.0%,cr 12.0~14.0%,ni 0.5~1.5%,mo 0.2~1.0%,al 0.01~0.1%,其余为fe和不可避免的杂质元素,杂质元素总量低于0.5%。该发明获得的油套管用钢可适用于高温高压、高含co2、cl-等共存的油田井下强腐蚀环境,但不具备耐srb腐蚀性能。
技术实现要素:12.本发明的目的之一在于提供一种抗二氧化碳及硫酸盐还原菌腐蚀的油套管,该抗二氧化碳及硫酸盐还原菌腐蚀的油套管具有良好的强度以及优异的抗二氧化碳及硫酸盐还原菌腐蚀性能,其可以有效应用于油气田开采等领域,具有良好的推广前景和应用价值。
13.为了实现上述目的,本发明提供了一种抗二氧化碳及硫酸盐还原菌腐蚀的油套管,其除了fe以外还含有质量百分比如下的下述化学元素:
14.c:0.15~0.3%,si:0.1~2.0%,mn:0.25~2.5%,cr:1.5~5.5%,ni:0.5~2.5%,cu:0.3~3.5%,mo:0.08~1.5%,la:0.08~0.2%,ce:0.05~0.15%。
15.进一步地,在本发明所述的抗二氧化碳及硫酸盐还原菌腐蚀的油套管中,其各化学元素质量百分比为:
16.c:0.15~0.3%,si:0.1~2.0%,mn:0.25~2.5%,cr:1.5~5.5%,ni:0.5~2.5%,cu:0.3~3.5%,mo:0.08~1.5%,la:0.08~0.2%,ce:0.05~0.15%,余量为fe和其他不可避免的杂质元素。
17.在本发明所述的抗二氧化碳及硫酸盐还原菌腐蚀的油套管中,各化学元素的设计原理如下所述:
18.c:在本发明所述的抗二氧化碳及硫酸盐还原菌腐蚀的油套管中,c是保证钢管室温强度和淬透性所必需的成分,适量的c元素可以有效保证钢管的强度和淬透性。若钢中c元素含量低于0.15%时,则钢管的淬透性和强度不够;而当钢中c元素含量高于0.3%时,会使钢管的韧性和耐co2腐蚀性能变坏。基于此,在本发明所述的抗二氧化碳及硫酸盐还原菌腐蚀的油套管中控制c的质量百分比在0.15~0.3%之间。
19.si:在本发明所述的抗二氧化碳及硫酸盐还原菌腐蚀的油套管中,si是炼钢过程中重要的脱氧剂,si元素可以有效提高钢管的高温抗氧化和耐酸性能,但若钢中si元素含量过多,则会降低钢管的韧性和塑性。因此,在本发明所述的抗二氧化碳及硫酸盐还原菌腐蚀的油套管中控制si的质量百分比在0.1~2.0%之间。
20.mn:在本发明所述的抗二氧化碳及硫酸盐还原菌腐蚀的油套管中,mn是改善钢的强韧性必需的元素。若钢中mn元素含量低于0.25%时,则mn的作用不够明显;而当钢中mn元素含量高于2.5%时,会导致钢管的耐co2腐蚀性能下降。基于此,在本发明所述的抗二氧化碳及硫酸盐还原菌腐蚀的油套管中控制mn的质量百分比在0.25~2.5%之间。
21.cr:在本发明所述的抗二氧化碳及硫酸盐还原菌腐蚀的油套管中,cr元素能够明显提高钢的强度和抗co2局部腐蚀和均匀腐蚀能力,并具有一定抗微生物作用。但是,需要说明的是,钢中cr元素含量并不是越高越好,这是因为cr元素的碳化物在晶界的偏析容易导致钢种抗腐蚀性能下降。基于此,在本发明所述的抗二氧化碳及硫酸盐还原菌腐蚀的油套管中控制cr的质量百分比在1.5~5.5%之间。
22.ni:在本发明所述的抗二氧化碳及硫酸盐还原菌腐蚀的油套管中,ni元素可以明显改善钝化膜性能,提升钢种的耐腐蚀作用。为了使ni元素在本发明中有效发挥其作用,在本发明所述的抗二氧化碳及硫酸盐还原菌腐蚀的油套管中控制ni的质量百分比在0.5~2.5%之间。
23.cu:在本发明所述的抗二氧化碳及硫酸盐还原菌腐蚀的油套管中,cu元素对微生物具有生物毒性,其能有效提升钢的耐微生物腐蚀性能。cu元素能够有效改善钢的抗大气腐蚀及微生物腐蚀性能。但需要注意的是,过量的cu会使得钢在热加工时易产生裂纹。基于此,在本发明所述的抗二氧化碳及硫酸盐还原菌腐蚀的油套管中控制cu的质量百分比在0.3~3.5%之间。
24.mo:在本发明所述的抗二氧化碳及硫酸盐还原菌腐蚀的油套管中,mo元素可以有效增加钢耐点蚀能力,同时mo元素具有较好的固溶强化效果,有利于提升钢的强度。基于此,在本发明所述的抗二氧化碳及硫酸盐还原菌腐蚀的油套管中控制mo的质量百分比在0.08~1.5%之间。
25.la、ce:在本发明所述的抗二氧化碳及硫酸盐还原菌腐蚀的油套管中,稀土元素la和ce的添加能够有效提高钢种的韧性,大大改善钢的耐腐蚀性能,la和ce有易于提升钢的耐硫酸盐还原菌腐蚀性能。但需要注意的是,钢中也不宜添加过量的稀土元素。因此,在本
发明所述的抗二氧化碳及硫酸盐还原菌腐蚀的油套管中控制la的质量百分比在0.08~0.2%之间,控制ce的质量百分比在0.05~0.15%之间。
26.进一步地,在本发明所述的抗二氧化碳及硫酸盐还原菌腐蚀的油套管中,还满足0.15%≤[la]+[ce]≤0.3%。其中,式中的la和ce均表示相应元素质量百分含量。
[0027]
在上述技术方案中,为了得到更好的实施效果,在本发明所述的抗二氧化碳及硫酸盐还原菌腐蚀的油套管中,在控制单一元素含量的同时,通过控制0.15%≤[la]+[ce]≤0.3%,可以有效保证本发明所述的抗二氧化碳及硫酸盐还原菌腐蚀的油套管的优异的抗二氧化碳及硫酸盐还原菌腐蚀性能。
[0028]
进一步地,在本发明所述的抗二氧化碳及硫酸盐还原菌腐蚀的油套管中,在其他不可避免的杂质中,p≤0.015%,并且/或者s≤0.007%。
[0029]
上述技术方案中,在本发明所述的抗二氧化碳及硫酸盐还原菌腐蚀的油套管中,p和s均是钢中不可避免的杂质元素,在钢中p和s元素含量越低越好。p是钢中的有害元素,其会对钢的抗co2腐蚀性能和热加工性能产生不利影响,若钢中p元素含量超过0.015%,则会使钢的抗腐蚀性能无法满足co2环境要求。相应地,s元素同样也是使得钢的热加工性能降低并对冲击韧性产生不良影响的有害元素。若钢中s元素的含量超过0.007%,则不能正常制造钢管。基于此,在本发明所述的抗二氧化碳及硫酸盐还原菌腐蚀的油套管中,控制p的质量百分比为p≤0.015%,控制s的质量百分比为s≤0.007%。
[0030]
在一些优选的实施方式中,为了得到更好的实施效果,油套管中s的质量百分比可以控制为s≤0.005%。
[0031]
进一步地,在本发明所述的抗二氧化碳及硫酸盐还原菌腐蚀的油套管中,其微观组织为回火索氏体。
[0032]
进一步地,在本发明所述的抗二氧化碳及硫酸盐还原菌腐蚀的油套管中,其性能满足下述各项的至少其中之一:其屈服强度为552mpa~758mpa,至少0℃下的全尺寸冲击功≥150j;其在硫酸盐还原菌和二氧化碳环境下的均匀腐蚀速率<0.10mm/a,局部腐蚀速率<0.2mm/a。
[0033]
相应地,本发明的另一目的在于提供一种抗二氧化碳及硫酸盐还原菌腐蚀的油套管的制造方法,采用该制造方法制得的抗二氧化碳及硫酸盐还原菌腐蚀的油套管的屈服强度为552mpa~758mpa,至少0℃下的全尺寸冲击功≥150j;其在硫酸盐还原菌和二氧化碳环境下的均匀腐蚀速率<0.10mm/a,局部腐蚀速率<0.2mm/a,具有优异的抗二氧化碳及硫酸盐还原菌腐蚀特性。
[0034]
为了实现上述目的,本发明提出了上述的抗二氧化碳及硫酸盐还原菌腐蚀的油套管的制造方法,包括步骤:
[0035]
(1)制得管坯;
[0036]
(2)轧制荒管;
[0037]
(3)淬火+回火:将钢管加热到920~1000℃,保温0.5~1.0h,再进行水冷或油冷;然后回火,控制回火温度为620℃~700℃,保温时间为0.8~1.5h。
[0038]
在本发明所述的抗二氧化碳及硫酸盐还原菌腐蚀的油套管的制造方法中,通过对工艺条件尤其是热处理工艺参数的控制,使得采用本发明所述的制造方法所制得的抗二氧化碳及硫酸盐还原菌腐蚀的油套管微观组织为回火索氏体,从而保证本发明的抗二氧化碳
及硫酸盐还原菌腐蚀的油套管具有优异的性能。
[0039]
在上述方案,步骤(3)中,控制回火温度在620℃~700℃之间,可以在保证钢管强度的前提下,尽可能消除内应力,从而获得足够的韧性。
[0040]
进一步地,在本发明所述的制造方法中,在步骤(2)中,将管坯加热到1100~1280℃,保持1~4h后,经穿孔、连轧、张力减径或张力定径制得荒管。
[0041]
进一步地,在本发明所述的制造方法中,在步骤(2)中,控制终轧温度为900℃-1000℃,以使得终轧结束时管子为全奥氏体组织。
[0042]
本发明所述的抗二氧化碳及硫酸盐还原菌腐蚀的油套管及其制造方法相较于现有技术具有如下所述的优点以及有益效果:
[0043]
在本发明所述的抗二氧化碳及硫酸盐还原菌腐蚀的油套管中,发明人通过研究不同合金元素对低合金钢组织和性能的影响规律,最终采用合理的化学成分设计,配合特定的变形和热处理工艺获得了一定强度的回火索氏体组织,且具有优异抗二氧化碳及硫酸盐还原菌腐蚀性能的油套管。该抗二氧化碳及硫酸盐还原菌腐蚀油套管的屈服强度为552mpa~758mpa,至少0℃下的全尺寸冲击功≥150j;其在硫酸盐还原菌和二氧化碳环境下的均匀腐蚀速率<0.10mm/a,局部腐蚀速率<0.2mm/a,具有良好的强度以及优异的抗二氧化碳及硫酸盐还原菌腐蚀性能。
[0044]
此外,本发明所述的抗二氧化碳及硫酸盐还原菌腐蚀的油套管钢化学成分简单,且经济成本低廉,具有良好的推广前景和应用价值。
附图说明
[0045]
图1为实施例1的抗二氧化碳及硫酸盐还原菌腐蚀的油套管的金相组织图。
具体实施方式
[0046]
下面将结合具体的实施例和说明书附图对本发明所述的抗二氧化碳及硫酸盐还原菌腐蚀的油套管及其制造方法做进一步的解释和说明,然而该解释和说明并不对本发明的技术方案构成不当限定。
[0047]
实施例1-7和对比例1-4
[0048]
实施例1-7的抗二氧化碳及硫酸盐还原菌腐蚀的油套管和对比例1-4的油套管均采用以下步骤制得:
[0049]
(1)按照表1所示的化学成分进行冶炼并制得φ300mm圆管坯;
[0050]
(2)轧制荒管:将管坯加热到1100~1280℃,保持1~4h后,经穿孔、连轧、张力减径或张力定径制得荒管。控制终轧温度为900℃-1000℃,以使得终轧结束时管子为全奥氏体组织;
[0051]
(3)淬火+回火:将钢管加热到920~1000℃,保温0.5~1.0h,再进行水冷或油冷;然后回火,控制回火温度为620℃~700℃,控制回火保温时间为0.8~1.5h。
[0052]
表1列出了实施例1-7的抗二氧化碳及硫酸盐还原菌腐蚀的油套管和对比例1-4的油套管中各化学元素质量百分比。
[0053]
表1.(wt%,余量为fe和其他除了p、s以外的不可避免的杂质)
[0054]
编号csimnpscrnicumolace[la]+[ce]
实施例10.300.10.550.0150.0022.02.23.51.50.200.050.25实施例20.152.01.50.0150.0025.01.02.00.20.080.120.2实施例30.181.00.250.0150.0021.51.80.30.080.130.070.2实施例40.200.82.50.0150.0024.52.03.00.80.150.150.3实施例50.230.52.00.0150.0025.51.50.80.50.090.060.15实施例60.261.81.00.0150.0023.00.51.51.20.180.100.28实施例70.301.51.80.0150.0024.02.52.51.00.100.140.24对比例10.180.82.50.0150.0020.52.01.01.00.150.080.23对比例20.201.51.50.0150.0022.01.50.060.20.180.100.28对比例30.220.80.550.0500.013.02.22.01.00.120.150.27对比例40.450.12.20.0150.0024.51.03.01.50.090.120.21
[0055]
表2列出了实施例1-7的抗二氧化碳及硫酸盐还原菌腐蚀的油套管和对比例1-4的油套管的具体工艺参数。
[0056]
表2.
[0057][0058]
将制得的规格为φ114.3*9.65的实施例1-7的抗二氧化碳及硫酸盐还原菌腐蚀的油套管和对比例1-4的油套管进行各项性能测试,所得的测试结果列于表3中,具体测试方式如下:
[0059]
(1)测试屈服强度:
[0060]
将制成的实施例和对比例的油套管加工成api弧形试样,按api标准检验后取平均数得出各油套管屈服强度的数据。
[0061]
(2)测试全尺寸夏比v型冲击吸收功:
[0062]
在制成的实施例和对比例的油套管上取截面积为10*10*55全尺寸v型冲击试样,按gb/t 229标准检验后取平均数得出各油套全尺寸夏比v型冲击吸收功数据。
[0063]
(3)测试腐蚀速率:
[0064]
在二氧化碳及硫酸盐还原菌共存环境进行腐蚀试验,将试样浸入容器中液体,控制温度为50℃,控制co2分压为1.0mpa,硫酸盐还原菌浓度为40000个/ml,控制试验时间为240h,试验完成后,对比试验前后的试样重量,通过计算便可以得出均匀腐蚀速率。再对点蚀坑进行截面分析计算便可得到局部腐蚀速率。
[0065]
表3列出了实施例1-7的抗二氧化碳及硫酸盐还原菌腐蚀的油套管和对比例1-4的
油套管的性能测试结果。
[0066]
表3.
[0067][0068]
由表3可看出,相较于对比例1-4,本发明各实施例的性能明显更优,各实施例的屈服强度rt
0.5
均在552mpa~758mpa之间,至少0℃下的全尺寸冲击功均≥150j,各实施例在硫酸盐还原菌和二氧化碳环境下的均匀腐蚀速率均<0.10mm/a,局部腐蚀速率均<0.2mm/a。各实施例的抗二氧化碳及硫酸盐还原菌腐蚀的油套管的各项性能十分优异,不仅具有良好的强度,还具有优异的抗二氧化碳及硫酸盐还原菌腐蚀性能。
[0069]
图1为实施例1的抗二氧化碳及硫酸盐还原菌腐蚀的油套管的金相组织图。
[0070]
如图1所示,在实施例1的抗二氧化碳及硫酸盐还原菌腐蚀的油套管中,其微观组织为其微观组织为回火索氏体。
[0071]
综上所述可以看出,本发明通过合理的化学成分设计,配合特定的变形和热处理工艺获得了一定强度的回火索氏体组织、具有优异抗二氧化碳及硫酸盐还原菌腐蚀性能的油套管。该抗二氧化碳及硫酸盐还原菌腐蚀油套管的屈服强度为552mpa~758mpa,至少0℃下的全尺寸冲击功≥150j;其在硫酸盐还原菌和二氧化碳环境下的均匀腐蚀速率<0.10mm/a,局部腐蚀速率<0.2mm/a,具有良好的强度以及优异的抗二氧化碳及硫酸盐还原菌腐蚀性能。
[0072]
此外,本发明所述的抗二氧化碳及硫酸盐还原菌腐蚀的油套管钢化学成分简单,且经济成本低廉,具有良好的推广前景和应用价值。
[0073]
需要说明的是,本发明的保护范围中现有技术部分并不局限于本技术文件所给出的实施例,所有不与本发明的方案相矛盾的现有技术,包括但不局限于在先专利文献、在先公开出版物,在先公开使用等等,都可纳入本发明的保护范围。
[0074]
此外,本案中各技术特征的组合方式并不限本案权利要求中所记载的组合方式或是具体实施例所记载的组合方式,本案记载的所有技术特征可以以任何方式进行自由组合或结合,除非相互之间产生矛盾。
[0075]
还需要注意的是,以上列举的仅为本发明的具体实施例,显然本发明不限于以上实施例,随之有着许多的类似变化。本领域的技术人员如果从本发明公开的内容直接导出
或联想到的所有变形,均应属于本发明的保护范围。