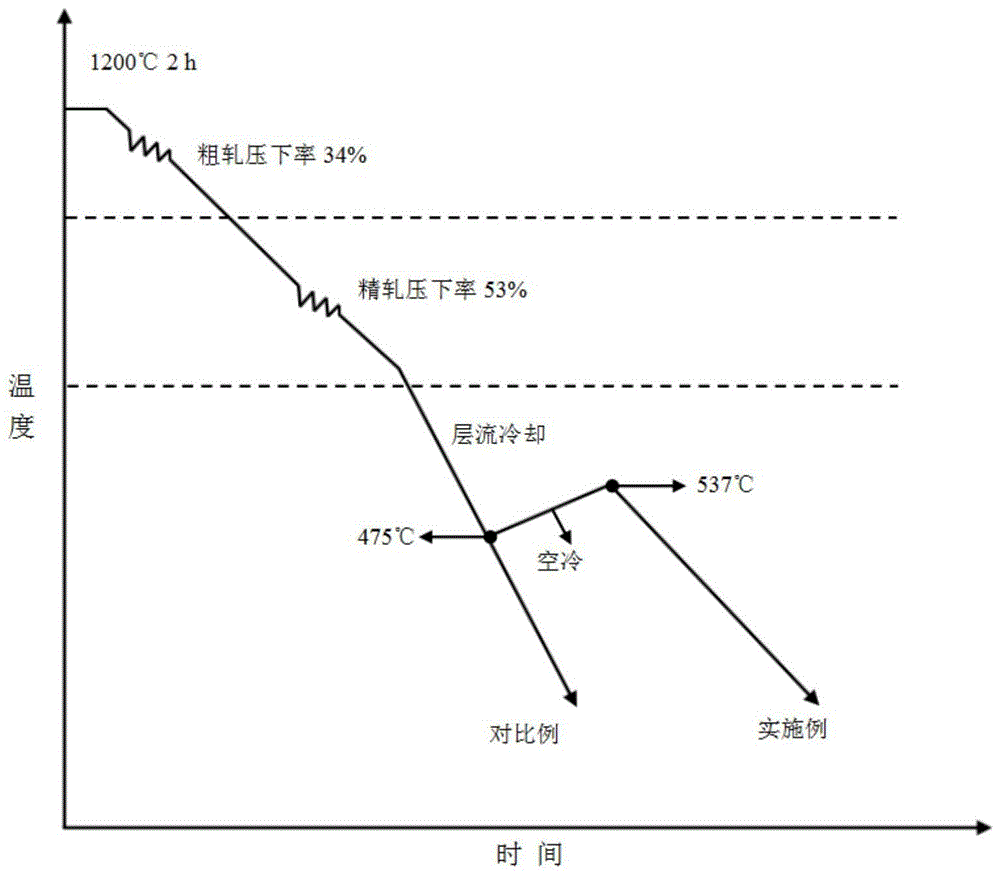
本发明涉及一种tmcp态低压缩比极寒环境用高强度船板钢及其制造方法,属于轧钢工艺
技术领域:
。
背景技术:
:极地具有丰富的资源以及巨大的开发和科学研究价值,但其终年白雪覆盖大地,气温非常低,而极地船舶是极地资源开发过程中所需的基础装备,极地船舶要求使用具有优异低温韧性的极地船舶用船板钢,但现有钢的耐低温性能不佳,成分复杂,亟需开发具有性能优异低温韧性的钢板。针状铁素体是低碳微合金钢中一种具有良好强韧性匹配特性的微观组织,可以在保证钢板强度的同时明显提高钢板韧性,但现有的制备方法容易出现裂纹,且耐低温性能不佳。专利申请的公开号为cn110343937a公开了一种控制夹杂物的极地用钢的冶炼方法,通过zr-ti脱氧高强度低合金钢,引入zr-ti复合氧化物核质点,并在其上形成mns,使其周围出现了贫锰区从而促进针状铁素体的形成。但该方法成本较高且氧化物夹杂与基体的界面有可能会成为裂纹的起裂点。cn109536838a公开了一种针状铁素体型耐低温n80级石油套管用钢及制备方法,但该方法只适用于生产管线钢,不适用生产≥45mm的厚板,而大排水量船只能使用更厚的钢板;并且在宽厚板的生产中,厚度方向上的冷速很难均匀,且心部冷速也无法达到其要求的10~14℃/s。技术实现要素:(一)要解决的技术问题为了解决现有技术的上述问题,本发明的第一目的是提供一种化学成分设计简单,具有优异低温韧性且强韧性匹配良好的极寒环境船舶用钢。本发明第二目的是提供该船板钢的制备方法,即通过合理设计和精确控制控轧控冷参数,不利用非氧化物冶金技术即大幅提高钢板中针状铁素体的含量,来改善厚度方向上的组织均匀性,提高心部的力学性能尤其是低温韧性。(二)技术方案为了达到上述目的,本发明采用的主要技术方案包括:一种tmcp态低压缩比极寒环境用高强度船板钢,其化学成分按重量百分比计包括:c:0.04~0.08%,si:0.15~0.35%,mn:1.00~2.00%,p:≤0.005%,s:≤0.005%,ni:0.35~0.75%,cu:0.14~0.34%,nb:0.15~0.45%,ti:0.005~0.030%,其余为fe及不可避免的杂质。本发明成分的设计理由如下:c元素可通过固溶强化、析出强化等方式提高强度,含量较低时,如低于0.04%,强度水平不容易保证,但含量较高时,如高于0.08%,则损害低温韧性和焊接性,因此,本发明中的c含量优选控制在0.04~0.08%范围内。mn元素是弱碳化物形成元素,可通过固溶强化来提高强度,同时能降低奥氏体转变温度,细化铁素体晶粒。但mn含量过高,如高于2.00%容易损害低温韧性,因此本发明中mn含量优选控制在1.00~2.00%之间。此外在c-mn钢的基础上,通过热、动力学模拟实验,设计复合仅添加ni、cu、nb、ti四种合金元素,发挥细晶强化、析出强化、固溶强化等作用来保证强度级别,研究发现含量在0.15~0.45%nb和0.005~0.030%ti的添加,既可以通过复合析出来提供针状铁素体的形核点,也不过于提高钢板的碳当量而影响其焊接性。所以nb的含量优选在0.15~0.45%,ti的含量优选在0.15~0.45%。通过ni在铁素体基体中的固溶改善低温冲击韧性,ni的含量高于0.75%时大大提升冶炼成本,低于0.35%不能完全保证强度和韧性,所以ni元素的含量优选0.35~0.75%。通过适量cu元素来提高耐蚀性,cu的含量高于0.34%会降低钢材韧性,低于0.14%则不易保证抗蚀性能,所以cu元素的含量优选0.14~0.34%,并严格控制p、s有害元素的含量。本发明中的化学成分属于低碳微合金钢范畴,合金成分种类较少,成本较低。一种tmcp态低压缩比极寒环境用高强度船板钢的制备方法,其包括如下步骤:s1、冶炼:铁水采用转炉冶炼,并通过lf炉脱硫处理+rh真空处理,控制钢中化学成分按重量百分比在如下范围内:c:0.04~0.08%,si:0.15~0.35%,mn:1.00~2.00%,p:≤0.005%,s:≤0.005%,ni:0.35~0.75%,cu:0.14~0.34%,nb:0.15~0.45%,ti:0.005~0.030%,其余为fe及不可避免的杂质;s2、将获得的铸坯加热、轧制;s3、冷却。在一个优选的实施方案中,在步骤s2中,所述铸坯加热的温度介于1050~1250℃,加热时间为2~4h。在一个优选的实施方案中,在步骤s2中,轧制采用奥氏体再结晶区和奥氏体未再结晶区两阶段轧制,奥氏体再结晶区轧制的温度范围为1000~1250℃,奥氏体未再结晶区轧的制温度范围为780~850℃。在一个优选的实施方案中,在步骤s2中,所述轧制过程中总的压缩比为3.0~3.4:1,其中奥氏体未再结晶区总的压下量要求≥50%。在一个优选的实施方案中,在步骤s2中,所述奥氏体再结晶区轧制的开轧温度1120℃,终轧温度1066℃,奥氏体再结晶区的压下量为34%;奥氏体再结晶区轧制的开轧温度815℃,终轧温度810℃,奥氏体未再结晶区的压下量为53%。在一个优选的实施方案中,在步骤s3中,所述冷却采用三阶段冷却方式,第一阶段为层流冷却速度为7~20℃/s,冷却终止温度为440~520℃,之后在空气中返温至530~590℃,该步骤减小了钢板表面和心部的温度差别,提高了组织均匀性并使钢板在针状铁素体反应区停留时间更长;第二阶段为层流冷却速度为5~10℃/s,冷却至终冷温度350~420℃,第三阶段为空冷至室温,以上温度均指冷却过程中钢板的表面温度。上述方法制备的tmcp态低压缩比极寒环境用高强度船板钢具有优异的性能,其钢板压缩比为3.0~3.4∶1,其一优选的钢板纵向屈服强度为442~455mpa,抗拉强度为583~592mpa,延伸率≥25%,-60℃夏比冲击功≥310j,钢板在厚度截面上的微观组织为粒状贝氏体+针状铁素体+铁素体,其中针状铁素体在1/2厚度位置处的比例≥40%,在1/4厚度位置处的比例≥35%。本发明在轧制过程中,奥氏体再结晶区(即精轧)阶段超过50%的压下量保证了奥氏体晶粒中引入足量的位错,细化相变组织。在ar3点以上完成精轧,随后层流冷通过两相区,此时会在原奥氏体晶界等部位发生部分铁素体相变。当钢板表面温度冷却至440~520℃时停止水冷,此时心部温度高于表面,热传导导致表面温度升高,控制返温至530~590℃。该过程使得钢板表面和心部在针状铁素体相变区停留时间增长,且第一阶段层流冷却形成的部分铁素体钝化原奥氏体晶界,进一步促进了需要晶内形核的针状铁素体相变。此外,空冷阶段的返温过程同时对钢板表面组织中的m/a岛进行回火,提高韧性,稳定强度。第三阶段的层流冷却促进心部贝氏体组织转变,避免过多珠光体等硬相的形成。本发明的方法通过合理控轧控冷过程,不利用氧化冶金技术并在较低压缩比条件下即可大幅提高具有较好强韧性的针状铁素体含量,进而提高钢板的低温韧性。(三)有益效果本发明的有益效果是:本发明提供的tmcp态低压缩比极寒环境用高强度船板钢的合金种类较少,成分简单,压缩比较低,并且可利用一般钢厂的现有设备和工艺条件,可提高生产效率并节能减耗。本发明提供的制备方法生产的厚板不利用氧化物冶金技术即可大幅提高钢板中针状铁素体组织的比例,在非氧化物冶金技术生产的厚板中较为少见,不需要如非氧化物冶金技术的有意添加和控制钢水中的夹杂物分布、成分和尺寸,即可获得针状铁素体组织,改善厚度方向上的组织均匀性,提高心部的力学性能尤其是低温韧性,且成本大大降低。本发明制备的tmcp态低压缩比极寒环境用高强度船板钢的屈服强度≥442mpa,1/2处-60℃平均冲击功310j,-80℃平均冲击功202j;1/4处-60℃平均冲击功324j,-80℃平均冲击功335j。在保证eh40级别强度的同时大幅提高低温韧性,-60℃、-80℃的低温冲击功均远超船级社相关要求,且厚度方向上的组织均匀,板型良好。附图说明图1为本发明实施例和对比例工艺图;图2为本发明实施例中1/4t处的组织图;图3为本发明实施例中1/2t处的组织图。具体实施方式为了更好的解释本发明,以便于理解,下面结合附图,通过具体实施方式,对本发明作详细描述。实施例1tmcp态低压缩比极寒环境用高强度船板钢的制备方法,采用如下步骤:冶炼及获得铸坯:铁水采用转炉冶炼,并通过lf炉脱硫处理+rh真空处理进行精炼,其中,控制钢中化学成分组成重量百分比为:c=0.06%,si=0.25%,mn=1.55%,p=0.005%,s=0.002%,ni=0.55%,cu=0.24%,nb=0.03%,ti=0.015%,其余为fe和不可避免杂质;获得铸坯厚度为155mm。轧制工艺:铸坯加热温度为1200℃,保温2h,采用两阶段轧制,第一阶段奥氏体再结晶区即粗轧开轧温度1120℃,终轧温度1066℃,粗轧压下率为34%(即奥氏体再结晶区的压下量),中间坯厚度102mm。第二阶段奥氏体未再结晶区即精轧开轧温度815℃,终轧温度为810℃,最终厚度48mm,精轧压下率(奥氏体未再结晶区的压下量)为53%。钢板最终厚度为48mm,总压缩比约为3.2:1。其中,总压缩比是指铸坯厚度与钢板最终厚度的比值。冷却工艺:精轧结束后,钢板即开始层流冷却,第一阶段冷却速度10℃/s,终冷温度475℃,随后开始在空气中返温,当钢板表面温度上升至537℃后,继续进行层流冷却即第二阶段的冷却速度为5℃/s,终冷温度为400℃,第三阶段为空冷至室温。工艺的温度路径见图1,以上温度均指冷却过程中钢板的表面温度。之后将获得的钢板rd-nd方向的截面研磨、抛光、腐蚀后,按现行gb/t13299-1991标准进行显微组织评定。每个位置随机统计20张500倍金相显微组织照片后获得表1统计结果。表1为实施例1钢板微观组织中的各相比例位置针状铁素体比例/%粒状贝氏体比例/%铁素体比例/%1/238.234.127.21/449.127.523.4通过表1可知,钢板在全厚度方向上具有较为均匀的组织,且针状铁素体均为1/2和1/4处所占比例最高的优势组织。按国标gb/t228-87中的要求对钢板不同位置进行纵向拉伸试验,按国标gb/t229-1994中的要求进行夏比冲击功的检测,测得结果见表2。表2为实施例1钢板的综合力学性能表2中,reh表示屈服强度,rm表示抗拉强度,a表示延伸率,表中数值均为五次测量后的平均值。通过表2可知,该发明船板钢强度和延伸率均满足各船级社对390mpa级别的要求,但低温冲击韧性远超该级别的各船级社要求,在-80℃仍具有优异的低温冲击韧性。以上方法生产的48mm厚极寒环境用高强度船板钢,对1/2t和1/4t处的进行电镜扫描,其1/4t处的组织图如图2所示,1/2t处的组织图如图3所示,可以看到,在显微镜下钢板1/4t和1/2t处存在的典型的针状铁素体组织,该组织犬牙交错的形态可以有效阻止裂纹扩展,从而大幅提高钢板韧性。因此利用本发明的方法生产的钢板厚度方向上均匀的铁素体+贝氏体+针状铁素体的多相组织屈服强度442~455mpa,抗拉强度583~592mpa,1/2处-60℃平均冲击功310j,-80℃平均冲击功202j;1/4处-60℃平均冲击功324j,-80℃平均冲击功335j,具有优异的低温韧性。对比例对比例中的铸坯组分含量与轧制规程与实施例1中相同,不同之处在于冷却工艺控制冷却阶段采用常规两阶段冷却,流程图见图1。精轧结束后,钢板即开始层流冷却,冷却速度7℃/s,终冷温度为400℃,最后空冷至室温。经检测,对比例钢板微观组织中的各相比例见表3,综合力学性能见表4。表3为对比例中钢板微观组织中的各相比例位置针状铁素体比例/%粒状贝氏体比例/%铁素体比例/%1/27.084.58.51/46.780.612.7通过表3可知,钢板在全厚度方向上具有较为均匀的组织,但明显低于实施例1中的针状铁素体含量,组织主要以粒状贝氏体为主。表4为对比例钢板的综合力学性能通过表4结合表2可知,对比例船板钢强度和延伸率均满足各船级社对390mpa级别的要求,但明显低于实施例中钢板的低温冲击韧性,实施例在-80℃仍具有优异的低温冲击韧性。目前现有技术的氧化物冶金是通过有意的添加和控制钢水中的夹杂物分布、成分和尺寸,从而利用这些夹杂物改善钢材性能的冶金方法。其中,弥散分布的夹杂物可以在奥氏体晶内成为针状铁素体的形核点从而促进针状铁素体组织的形成。针状铁素体组织由于其“犬牙交错”的形态可以有效阻滞裂纹的扩展,从而提高钢材,尤其是焊接热影响区的韧性。虽然氧化物冶金技术可以促进针状铁素体组织的形成,但是势必会增加成本,且氧化物夹杂如果控制不得当还有可能成为裂纹的形核点,反而影响韧性。本发明的实施例1中三阶段冷却工艺明显提高了钢板厚度方向上的组织均匀性,且生产的钢板中针状铁素体的含量明显高于对比例,较高含量的针状铁素体通过其犬牙交错的结构可以有效阻止裂纹扩展,因而大幅提高了钢板的低温韧性。且本发明生产的钢板无需经过氧化物冶金工艺即可获得高比例的针状铁素体组织,节约了成本并且降低了裂纹在氧化物夹杂形核的可能性。以上所述,仅是本发明的较佳实施例而已,并非是对本发明做其它形式的限制,任何本领域技术人员可以利用上述公开的技术内容加以变更或改型为等同变化的等效实施例。但是凡是未脱离本发明技术方案内容,依据本发明的技术实质对以上实施例所作的任何简单修改、等同变化与改型,仍属于本发明技术方案的保护范围。当前第1页12