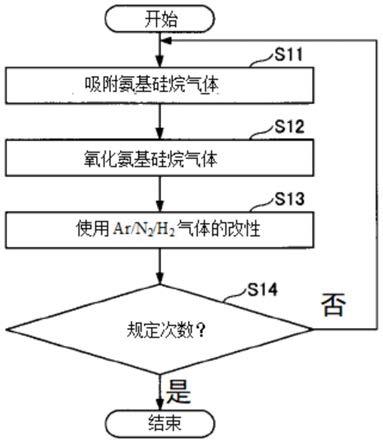
[0001]
本公开涉及一种成膜方法。
背景技术:[0002]
已知有一种成膜方法,所述成膜方法包括:使第一反应气体吸附于基板的步骤;使该第一反应气体与第二反应气体反应而在基板上形成反应产物的步骤;和,向反应产物照射由含氢气体生成的等离子体的步骤(例如,参见专利文献1)。
[0003]
现有技术文献
[0004]
专利文献
[0005]
专利文献1:日本特开2012-255203号公报
技术实现要素:[0006]
发明要解决的问题
[0007]
本公开提供能够将硅氧化膜埋入于凹部而不容易因随后的蚀刻工序出现接缝的技术。
[0008]
用于解决问题的方案
[0009]
基于本公开的一个方式的成膜方法具有如下步骤:使氨基硅烷气体吸附于表面形成有凹部的基板上的步骤;向上述基板供给氧化气体,对吸附于上述基板上的上述氨基硅烷气体进行氧化,从而使硅氧化膜堆积于上述基板上的步骤;和,利用等离子体将包含氮气及氢气的混合气体活化后供给至上述硅氧化膜,从而进行上述硅氧化膜的改性处理的步骤。
[0010]
发明的效果
[0011]
根据本公开,能够将硅氧化膜埋入于凹部而不容易因随后的蚀刻工序出现接缝。
附图说明
[0012]
图1是表示一实施方式的成膜装置的结构例的剖视图。
[0013]
图2是表示图1的成膜装置的真空容器内的结构的立体图。
[0014]
图3是表示图1的成膜装置的真空容器内的结构的俯视图。
[0015]
图4是沿着以能够旋转的方式设于图1的成膜装置的真空容器内的旋转台的同心圆剖切的该真空容器的剖视图。
[0016]
图5是图1的成膜装置的另一剖视图。
[0017]
图6是设于图1的成膜装置的等离子体产生源的剖视图。
[0018]
图7是设于图1的成膜装置的等离子体产生源的另一剖视图。
[0019]
图8是设于图1的成膜装置的等离子体产生源的顶视图。
[0020]
图9是表示一实施方式的成膜方法的流程图。
[0021]
图10是用于说明一实施方式的成膜方法的示意图。
[0022]
图11是一实施方式的成膜方法的机理的说明图(1)。
[0023]
图12是一实施方式的成膜方法的机理的说明图(2)。
[0024]
图13是表示实施例1的实施结果的图。
[0025]
图14是表示实施例2的实施结果的图。
[0026]
附图标记说明
[0027]1ꢀꢀꢀ
真空容器
[0028]2ꢀꢀꢀ
旋转台
[0029]
p1
ꢀꢀ
氨基硅烷气体吸附区域
[0030]
p2
ꢀꢀ
氧化气体供给区域
[0031]
p3
ꢀꢀ
等离子体处理区域
[0032]
d
ꢀꢀꢀ
分离区域
具体实施方式
[0033]
下面,一边参照附图一边对本公开的非限定性的示例的实施方式进行说明。在所附的所有附图中,对相同或对应的构件或部件标注相同或对应的附图标记,并省略重复的说明。
[0034]
(成膜装置)
[0035]
对用于实施一实施方式的成膜方法的合适的成膜装置进行说明。参照图1至图3,成膜装置包括:扁平的真空容器1,其具有大致圆形的平面形状;和旋转台2,其设于真空容器1内,且在真空容器1的中心具有旋转中心。真空容器1具有:容器主体12,其具有有底的圆筒形状;和顶板11,其相对于容器主体12的上表面借助例如o型密封圈等密封构件13(图1)以气密且能装卸的方式配置。
[0036]
旋转台2在中心部固定于圆筒形状的芯部21。芯部21固定于沿着铅垂方向延伸的旋转轴22的上端。旋转轴22贯穿真空容器1的底部14,其下端安装于使旋转轴22(图1)绕铅垂轴旋转的驱动部23。旋转轴22及驱动部23收纳于上表面开口的筒状的壳体20内。壳体20的设于其上表面的凸缘部分气密地安装于真空容器1的底部14的下表面,从而维持壳体20的内部气氛与外部气氛之间的气密状态。
[0037]
如图2和图3所示,在旋转台2的表面,沿着旋转方向(周向)设有用于载置多张(图示的例子中为5张)基板即半导体晶圆(以下称为“晶圆w”)的圆形状的凹部24。需要说明的是,在图3中为了方便仅在一个凹部24示出晶圆w。凹部24具有比晶圆w的直径略大例如4mm的内径以及与晶圆w的厚度大致相等的深度。因而,在将晶圆w收纳于凹部24时,晶圆w的表面与旋转台2的表面(未载置晶圆w的区域)成为相同的高度。在凹部24的底面形成有例如3根升降销贯穿的贯通孔(均未图示),该升降销用于支撑晶圆w的背面而使晶圆w升降。
[0038]
图2和图3是用于说明真空容器1内的构造的图,为了方便说明,省略了顶板11的图示。如图2和图3所示,在旋转台2的上方沿着真空容器1的周向(图3的由箭头a所示的旋转台2的旋转方向)互相空开间隔地配置有例如由石英构成的反应气体喷嘴31、32、33和分离气体喷嘴41、42。在图示的例子中,自后述的输送口15向顺时针方向(旋转台2的旋转方向)依次排列有反应气体喷嘴33、分离气体喷嘴41、反应气体喷嘴31、分离气体喷嘴42以及反应气体喷嘴32。这些反应气体喷嘴31、32、33和分离气体喷嘴41、42的基端部即气体导入口31a、
32a、33a、41a、42a(图3)固定于容器主体12的外周壁。而且,反应气体喷嘴31、32、33和分离气体喷嘴41、42以自真空容器1的外周壁向真空容器1内导入并沿着容器主体12的半径方向相对于旋转台2水平地延伸的方式安装。
[0039]
需要说明的是,在反应气体喷嘴33的上方如图3中由虚线简化表示那样设有等离子体产生源80。对等离子体产生源80后述说明。
[0040]
反应气体喷嘴31经由配管和流量控制器等(未图示)连接于氨基硅烷气体的供给源(未图示)。作为氨基硅烷气体,能够利用例如dipas[二异丙基氨基硅烷]、3dmas[三(二甲基氨基)硅烷]气体、btbas[双(叔丁基氨基)硅烷]。
[0041]
反应气体喷嘴32经由配管和流量控制器等(未图示)连接于氧化气体的供给源(未图示)。作为氧化气体,能够利用例如臭氧(o3)气体。
[0042]
反应气体喷嘴33经由未图示的配管和流量控制器等(未图示)连接于改性气体的供给源(未图示)。作为改性气体,能够利用例如氩气(ar)、氮气(n2)、氢气(h2)。
[0043]
分离气体喷嘴41、42均经由配管和流量控制阀等(未图示)连接于分离气体的供给源(未图示)。作为分离气体,能够利用例如ar气体、氮气(n2)。
[0044]
在反应气体喷嘴31、32沿着反应气体喷嘴31、32的长度方向以例如10mm的间隔排列有朝向旋转台2开口的多个喷出孔31h、32h(图4)。反应气体喷嘴31的下方区域成为用于使氨基硅烷气体吸附于晶圆w的氨基硅烷气体吸附区域p1。反应气体喷嘴32的下方区域成为使在氨基硅烷气体吸附区域p1吸附于晶圆w的氨基硅烷气体氧化的氧化气体供给区域p2。需要说明的是,对图4中未示出的反应气体喷嘴33的结构后述说明。
[0045]
参照图2和图3,在真空容器1内设有两个凸状部4。凸状部4与分离气体喷嘴41、42一起构成分离区域d,因此,如后所述,该凸状部4以朝向旋转台2突出的方式安装于顶板11的背面。另外,凸状部4具有顶部被切断成圆弧状的扇型的平面形状,在一实施方式中,以内圆弧与突出部5(后述)连结、外圆弧沿着真空容器1的容器主体12的内周面的方式配置。
[0046]
图4表示自反应气体喷嘴31至反应气体喷嘴32沿着旋转台2的同心圆剖切的真空容器1的剖面。如图4所示,在顶板11的背面安装有凸状部4。因此,在真空容器1内存在:凸状部4的下表面即平坦的较低的顶面(第一顶面44)、和位于第一顶面44的周向两侧的高于第一顶面44的顶面(第二顶面45)。第一顶面44具有顶部被切断成圆弧状的扇型的平面形状。另外,如图所示,在凸状部4的周向中央形成有以沿半径方向延伸的方式形成的槽部43,在槽部43内收纳有分离气体喷嘴42。在另一个凸状部4也同样地形成有槽部43,在槽部43收纳有分离气体喷嘴41。另外,在第二顶面45的下方的空间分别设有反应气体喷嘴31、32。这些反应气体喷嘴31、32自第二顶面45分离开并设于晶圆w的附近。如图4所示,在凸状部4的右侧的第二顶面45的下方的空间481设有反应气体喷嘴31,在左侧的第二顶面45的下方的空间482设有反应气体喷嘴32。
[0047]
另外,在收纳于凸状部4的槽部43的分离气体喷嘴42沿着分离气体喷嘴42的长度方向以例如10mm的间隔排列有朝向旋转台2开口的多个喷出孔42h(参照图4)。另外,在收纳于另一个凸状部4的槽部43的分离气体喷嘴41也同样地沿着分离气体喷嘴41的长度方向以例如10mm的间隔排列有朝向旋转台2开口的多个喷出孔41h。
[0048]
第一顶面44相对于旋转台2形成狭窄的空间即分离空间h。在自分离气体喷嘴42的喷出孔42h供给ar气体时,ar气体穿过分离空间h朝向空间481、482流动。此时,由于分离空
间h的容积小于空间481、482的容积,因此,利用ar气体能够使分离空间h的压力高于空间481、482的压力。即,在空间481、482之间形成压力较高的分离空间h。另外,自分离空间h向空间481、482流出的ar气体作为相对于来自氨基硅烷气体吸附区域p1的氨基硅烷气体和来自氧化气体供给区域p2的氧化气体的逆流而发挥作用。因而,来自氨基硅烷气体吸附区域p1的氨基硅烷气体和来自氧化气体供给区域p2的氧化气体利用分离空间h分离。因而,可抑制氨基硅烷气体与氧化气体在真空容器1内混合并发生反应。
[0049]
考虑成膜时的真空容器1内的压力、旋转台2的转速、分离气体(ar气体)的流量等,将第一顶面44的相对于旋转台2的上表面的高度h1设定为适于使分离空间h的压力高于空间481、482的压力的高度。
[0050]
另一方面,在顶板11的下表面设有突出部5(图2和图3),该突出部5包围使旋转台2固定的芯部21的外周。在一实施方式中,突出部5与凸状部4的靠旋转中心侧的部位连续,突出部5的下表面形成为与第一顶面44相同的高度。
[0051]
之前参照的图1是沿着图3的i-i’线的剖视图,示出设有第二顶面45的区域。另一方面,图5是表示设有第一顶面44的区域的剖视图。如图5所示,在扇型的凸状部4的周缘(真空容器1的外缘侧的部位)以与旋转台2的外端面对置的方式形成有呈l字形弯曲的弯曲部46。弯曲部46与凸状部4同样地,通过抑制反应气体自分离区域d的两侧侵入来抑制氨基硅烷气体与氧化气体的混合。扇型的凸状部4设于顶板11,由于顶板11能够自容器主体12拆下,因此,在弯曲部46的外周面与容器主体12之间略微存在间隙。弯曲部46的内周面与旋转台2的外端面之间的间隙、以及弯曲部46的外周面与容器主体12之间的间隙设定为例如与第一顶面44的相对于旋转台2的上表面的高度相同的尺寸。
[0052]
在分离区域d,容器主体12的内周壁以靠近弯曲部46的外周面的方式形成为垂直面(图5),而在分离区域d以外的部位,容器主体12的内周壁自例如与旋转台2的外端面对置的部位开始持续到底部14地向外方凹陷(图1)。下面,为了方便说明,将具有大致矩形的截面形状的凹陷的部分标记为排气区域e。具体而言,将与氨基硅烷气体吸附区域p1连通的排气区域标记为第一排气区域e1,将与氧化气体供给区域p2连通的区域标记为第二排气区域e2。如图1至图3所示,在这些第一排气区域e1和第二排气区域e2的底部分别形成有第一排气口61和第二排气口62。第一排气口61和第二排气口62如图1所示分别经由排气管63连接于真空排气部即例如真空泵64。需要说明的是,在图1中,示出了压力控制器65。
[0053]
如图1和图5所示,在旋转台2与真空容器1的底部14之间的空间设有作为加热部的加热器单元7,旋转台2上的晶圆w隔着旋转台2被加热至由工艺制程确定的温度(例如400℃)。在旋转台2的周缘附近的下方设有圆环状的罩构件71(图5)。罩构件71对自旋转台2的上方空间至第一排气区域e1和第二排气区域e2的气氛和放置有加热器单元7的气氛进行划分,从而抑制气体向旋转台2的下方区域的侵入。罩构件71包括以自下方面向旋转台2的外缘和比外缘靠外周侧的方式设置的内侧构件71a以及设于内侧构件71a与真空容器1的内周面之间的外侧构件71b。外侧构件71b在分离区域d设于在凸状部4的外缘形成的弯曲部46的下方且靠近弯曲部46地设置。内侧构件71a在旋转台2的外缘下方(以及比外缘略靠外侧的部分的下方)在整周上包围加热器单元7。
[0054]
位于比配置有加热器单元7的空间靠旋转中心侧的部位的底部14以靠近旋转台2的下表面的中心部附近处的芯部21的方式向上方突出而形成突出部12a。突出部12a与芯部
21之间成为狭窄的空间,而且贯穿底部14的旋转轴22的贯通孔的内周面与旋转轴22之间的间隙变窄,且这些狭窄的空间与壳体20连通。而且,在壳体20设有吹扫气体供给管72,该吹扫气体供给管72用于将作为吹扫气体的ar气体向狭窄的空间内供给并进行吹扫。另外,在真空容器1的底部14,在加热器单元7的下方沿着周向以规定的角度间隔设有用于对加热器单元7的配置空间进行吹扫的多个吹扫气体供给管73(图5中示出一个吹扫气体供给管73)。另外,为了抑制气体向设有加热器单元7的区域的侵入,在加热器单元7与旋转台2之间设有盖构件7a,该盖构件7a在周向上连续地覆盖自外侧构件71b的内周壁(内侧构件71a的上表面)至突出部12a的上端之间的部分。盖构件7a由例如石英形成。
[0055]
另外,在真空容器1的顶板11的中心部连接有分离气体供给管51,构成为向顶板11与芯部21之间的空间52供给作为分离气体的ar气体。供给到空间52的分离气体经由突出部5与旋转台2之间的狭窄的间隙50沿着旋转台2的晶圆载置区域侧的表面朝向周缘喷出。间隙50能够利用分离气体维持为高于空间481、482的压力的压力。因而,利用间隙50,能够抑制向氨基硅烷气体吸附区域p1供给的氨基硅烷气体和向氧化气体供给区域p2供给的氧化气体穿过中心区域c而混合。即,间隙50(或中心区域c)与分离空间h(或分离区域d)同样地发挥功能。
[0056]
进而,如图2和图3所示,在真空容器1的侧壁形成有输送口15,该输送口15用于在外部的输送臂10与旋转台2之间进行晶圆w的交接。输送口15利用未图示的闸阀开闭。在旋转台2的下方且在与晶圆w的交接位置对应的部位设有交接用的升降销及其升降机构(均未图示),其贯穿凹部24并用于将晶圆w自背面抬起。
[0057]
接着,一边参照图6至图8一边对等离子体产生源80进行说明。图6是设于图1的成膜装置的等离子体产生源80的剖视图,表示等离子体产生源80的沿着旋转台2的半径方向的剖面。图7是设于图1的成膜装置的等离子体产生源80的另一剖视图,表示等离子体产生源80的沿着与旋转台2的半径方向正交的方向的剖面。图8是设于图1的成膜装置的等离子体产生源80的顶视图。为了方便图示,在这些附图中简化了一部分的构件。
[0058]
参照图6,等离子体产生源80包括:框架构件81、法拉第遮蔽板82、绝缘板83、天线85。框架构件81由高频透过性的材料制作,具有自上表面凹陷的凹部,并嵌入于形成在顶板11的开口部11a。法拉第遮蔽板82收纳于框架构件81的凹部内,具有上部开口的大致箱状的形状。绝缘板83配置在法拉第遮蔽板82的底面上。天线85支撑于绝缘板83的上方,形成为具有大致八边形的平面形状的线圈状。
[0059]
顶板11的开口部11a具有多个台阶部,在其中的一个台阶部在整周上形成有槽部,在槽部嵌入有例如o型密封圈等密封构件81a。另一方面,框架构件81具有与开口部11a的台阶部对应的多个台阶部。由此,在将框架构件81嵌入于开口部11a时,多个台阶部中的一个台阶部的背面与嵌入于开口部11a的槽部的密封构件81a接触,而维持顶板11与框架构件81之间的气密性。另外,如图6所示,设有沿着嵌入于顶板11的开口部11a的框架构件81的外周的按压构件81c,由此,框架构件81相对于顶板11被向下方按压。因此,更可靠地维持顶板11与框架构件81之间的气密性。
[0060]
框架构件81的下表面与真空容器1内的旋转台2对置,并在该框架构件81的下表面的外周设有在整周上向下方(朝向旋转台2)突起的突起部81b。突起部81b的下表面靠近旋转台2的表面,由突起部81b、旋转台2的表面以及框架构件81的下表面在旋转台2的上方划
分形成等离子体处理区域p3。需要说明的是,突起部81b的下表面与旋转台2的表面之间的间隔可以和分离空间h(图4)中的第一顶面44的相对于旋转台2的上表面的高度h1大致相同。
[0061]
另外,贯穿了突起部81b的反应气体喷嘴33向等离子体处理区域p3延伸。在一实施方式中,如图6所示,在反应气体喷嘴33连接有填充有ar气体的氩气供给源90、填充有n2气的氮气供给源91、填充有h2气的氢气供给源92。自氩气供给源90、氮气供给源91以及氢气供给源92以规定的流量比(混合比)向等离子体处理区域p3供给利用对应的流量控制器93、94、95对流量进行了控制的ar气体、n2气以及h2气。
[0062]
另外,在反应气体喷嘴33沿着其长度方向以规定间隔(例如10mm)形成有多个喷出孔33h,自喷出孔33h喷出上述的ar气体、n2气以及h2气。如图7所示,喷出孔33h自相对于旋转台2垂直的方向朝向旋转台2的旋转方向的上游侧倾斜。因此,自反应气体喷嘴33供给的混合气体朝向与旋转台2的旋转方向相反的方向喷出,具体而言,朝向突起部81b的下表面与旋转台2的表面之间的间隙喷出。由此,抑制氧化气体、分离气体自沿着旋转台2的旋转方向位于比等离子体产生源80靠上游侧的位置的第二顶面45的下方的空间向等离子体处理区域p3内流入。另外,如上所述,由于沿着框架构件81的下表面的外周形成的突起部81b靠近旋转台2的表面,因此,利用来自反应气体喷嘴33的气体能够容易地将等离子体处理区域p3内的压力维持得较高。由此,也会抑制氧化气体、分离气体向等离子体处理区域p3内流入。
[0063]
法拉第遮蔽板82由金属等导电性材料制作,虽省略图示,但该法拉第遮蔽板82接地。如图8明确地示出那样,在法拉第遮蔽板82的底部形成有多个狭缝82s。各狭缝82s以与具有大致八边形的平面形状的天线85的对应的边大致正交的方式延伸。
[0064]
另外,如图7和图8所示,法拉第遮蔽板82在上端的两个部位具有向外侧弯折的支撑部82a。通过将支撑部82a支撑于框架构件81的上表面,从而将法拉第遮蔽板82支撑于框架构件81内的规定位置。
[0065]
绝缘板83利用例如石英玻璃制作,具有略小于法拉第遮蔽板82的底面的大小,并载置于法拉第遮蔽板82的底面。绝缘板83使法拉第遮蔽板82与天线85之间绝缘,并且使自天线85放射的高频向下方透过。
[0066]
天线85通过以平面形状成为大致八边形的方式将铜制的中空管(管)卷绕例如3层而形成。在管内能够使冷却水循环,由此,防止由向天线85供给的高频导致天线85被加热至高温。另外,在天线85设有竖立设置部85a,在竖立设置部85a安装有支撑部85b。利用支撑部85b将天线85维持在法拉第遮蔽板82内的规定位置。另外,在支撑部85b经由匹配器86连接有高频电源87。高频电源87产生具有例如13.56mhz的频率的高频。
[0067]
根据该等离子体产生源80,在经由匹配器86自高频电源87向天线85供给高频电力时,利用天线85产生电磁场。由于电磁场中的电场分量被法拉第遮蔽板82遮蔽,因而无法向下方传播。另一方面,磁场分量穿过法拉第遮蔽板82的多个狭缝82s向等离子体处理区域p3内传播。利用磁场分量,由自反应气体喷嘴33以规定的流量比(混合比)向等离子体处理区域p3供给的改性气体产生等离子体。利用如此产生的等离子体,能够降低对堆积在晶圆w上的薄膜产生的照射损伤、真空容器1内的各构件的损伤等。
[0068]
另外,如图1所示,在成膜装置上设有用于进行装置整体的动作的控制的控制部100,该控制部100由计算机构成。在控制部100的存储器内存储有在控制部100的控制下使
成膜装置实施后述的成膜方法的程序。程序编入有步骤组以执行后述的成膜方法。程序存储于硬盘、光盘、光磁盘、存储卡、软盘等介质102,利用规定的读取装置被读入到存储部101,并安装于控制部100内。
[0069]
(成膜方法)
[0070]
列举使用上述的成膜装置成膜硅氧化膜(sio2膜)的情况的例子说明一实施方式的成膜方法。图9是表示一实施方式的成膜方法的流程图。图10是用于说明一实施方式的成膜方法的示意图。在一实施方式中,如图10的(a)所示,列举向在表面形成有沟槽t的晶圆w的沟槽t埋入硅氧化膜来成膜的情况的例子进行说明。需要说明的是,沟槽t为形成于晶圆w的表面u的凹部的一个例子,除了沟槽t以外,还可以形成有通孔等。另外,也可以在晶圆w的表面形成硅氮化膜等底膜。
[0071]
首先,打开闸阀,从外部利用输送臂10经由输送口15向旋转台2的凹部24内交接晶圆w。晶圆w的交接是通过在使凹部24停止于面向输送口15的位置时使升降销经由凹部24的底面的贯通孔、自真空容器1的底部侧升降而进行的。使旋转台2间歇地旋转并进行这样的晶圆w的交接,从而在旋转台2的五个凹部24内分别载置晶圆w。
[0072]
接着,关闭闸阀,利用真空泵64对真空容器1内进行排气,直到真空容器1内可达到的真空度为止。然后,自分离气体喷嘴41、42作为分离气体以规定流量喷出ar气体,自分离气体供给管51和吹扫气体供给管72以规定流量喷出ar气体。另外,利用压力控制器65将真空容器1内控制为预先设定的处理压力。接下来,一边使旋转台2向顺时针方向以例如5rpm的转速旋转,一边利用加热器单元7将晶圆w加热至例如400℃。
[0073]
之后,自反应气体喷嘴31供给氨基硅烷气体,自反应气体喷嘴32供给o3气。另外,自反应气体喷嘴33供给ar/n2/h2气,以例如4000w的电力对于等离子体产生源80的天线85供给具有13.56mhz的频率的高频。由此,在等离子体产生源80与旋转台2之间的等离子体处理区域p3生成等离子体。在等离子体中生成有nh活性物种、高能颗粒。
[0074]
利用旋转台2的旋转,晶圆w反复按顺序穿过氨基硅烷气体吸附区域p1、分离区域d、氧化气体供给区域p2、等离子体处理区域p3以及分离区域d。在氨基硅烷气体吸附区域p1,如图10的(a)所示,在晶圆w的表面u、沟槽t的内表面生成sih3基(步骤s11)。穿过了分离区域d之后,在氧化气体供给区域p2,生成于晶圆w的表面u、沟槽t的内表面的sih3基被o3气分子氧化(步骤s12)。由此,如图10的(b)所示,沿着沟槽t的内表面生成羟基(oh基)。
[0075]
接着,在晶圆w到达等离子体产生源80的等离子体处理区域p3时,晶圆w暴露于由ar/n2/h2气体生成的等离子体(步骤s13)。此时,oh基的一部分因等离子体中所含的nh活性物种的碰撞而被氨基(nh2基)取代。等离子体到达晶圆w的表面u、沟槽t的开口附近,但难以到达沟槽t的底部附近。因此,在晶圆w的表面u和沟槽t的开口附近的侧面,相对大量的oh基被nh2基取代。其结果,如图10的(c)所示,oh基以oh基的密度在沟槽t的底部和底部附近的侧面较高且随着去向沟槽t的开口和晶圆w的表面u而密度降低的方式分布。
[0076]
接着,在利用旋转台2的旋转使晶圆w再次到达氨基硅烷气体吸附区域p1时,自反应气体喷嘴31供给的氨基硅烷气体的分子吸附于晶圆w的表面u、沟槽t的内表面。此时,由于氨基硅烷气体的分子容易被oh基吸附而难以被nh2基吸附,因此,如图10的(d)所示,该氨基硅烷气体的分子按照依据oh基分布的分布吸附于晶圆w的表面u、沟槽t的内表面。即,氨基硅烷气体的分子以在沟槽t的底部和底部附近的侧面、密度较高且随着去向沟槽t的开口
而密度降低的方式吸附于沟槽t的内表面。
[0077]
接下来,当晶圆w穿过氧化气体供给区域p2时,吸附于晶圆w的表面u、沟槽t的内表面的氨基硅烷气体被o3气氧化,进一步成膜硅氧化膜。此时,硅氧化膜的膜厚分布反映出吸附于沟槽t的内表面的氨基硅烷气体的密度。即,硅氧化膜在沟槽t的底部和底部附近的侧面较厚且随着去向沟槽t的开口而变薄。而且,因氨基硅烷气体的氧化而生成的oh基吸附于硅氧化膜的表面。
[0078]
接着,在晶圆w再次到达等离子体产生源80的等离子体处理区域p3时,如上所述,oh基以在沟槽t的底部和底部附近的侧面、oh基的密度较高且随着去向沟槽t的开口而密度降低的方式分布。
[0079]
之后,在重复上述的工艺时,硅氧化膜自沟槽t的底部开始逐渐变厚。在硅氧化膜逐渐变得更厚时,沟槽t被硅氧化膜埋入而没有形成空隙,沟槽t的埋入完成。
[0080]
如以上说明那样,根据一实施方式的成膜方法,对于在等离子体处理区域p3中进行的硅氧化膜111的改性处理,利用等离子体将作为改性气体的ar/n2/h2气体活化后供给。由此,能够成膜硅氧化膜而不容易因随后的蚀刻工序出现接缝。需要说明的是,对于通过利用等离子体将作为改性气体的ar/n2/h2气体活化后供给,能够成膜硅氧化膜而不容易因随后的蚀刻工序出现接缝的机理及实施结果后述说明。
[0081]
需要说明的是,在上述的成膜方法中,示出了通过利用等离子体将ar/n2/h2气体活化后供给并进行硅氧化膜的改性处理的情况,但用于改性处理的混合气体只要包含n2气及h2气即可,也可以是另一混合气体。例如,也可以使用包含he气来替代ar气体的he/n2/h2气体、除了ar气体以外还包含he气的ar/he/n2/h2气体。在此情况下,与上述的成膜方法同样地,通过利用等离子体进行活化,生成nh活性物种。
[0082]
(机理)
[0083]
对于通过利用等离子体将作为改性气体的ar/n2/h2气体活化后供给,能够成膜硅氧化膜而不容易因随后的蚀刻工序出现接缝的机理进行说明。
[0084]
首先,对于利用由等离子体产生源80生成的等离子体进行活化的改性气体进行说明。一般而言,在将氨基硅烷气体作为原料气体而成膜硅氧化膜的情况下,oh基成为吸附位点,氨基硅烷气体吸附在oh基上。然而,对于在晶圆w的表面形成有凹部,并向该凹部埋入来进行成膜的情况,为了堵塞凹部的上部的开口而不在内部形成空隙,优选自凹部的底面缓慢地向上方进行成膜的自下而上成膜(v字成膜)。
[0085]
在利用等离子体使作为改性气体的h2气和o2气的混合气体(以下称为“h2/o2气体”。)活化时,能够成膜膜质良好的膜,但在晶圆w的上表面形成作为氨基硅烷气体的吸附位点的oh基。因此,难以进行自下而上成膜。
[0086]
为了进行自下而上成膜,有时使用不包含h2气的改性气体,例如ar气体与o2气的混合气体(以下称为“ar/o2气体”。)、ar气体与n2气的混合气体(以下称为“ar/n2气体”。)。然而,在使用ar/o2气体或ar/n2气体作为改性气体时,在随后的蚀刻工序中对埋入于凹部内的硅氧化膜的一部分进行蚀刻时,有时会在凹部内出现接缝(接头)。
[0087]
于是,在一实施方式中,通过包含利用等离子体使包含n2气与h2气的混合气体(以下称为“n2/h2气体”。)活化并进行供给的改性处理的工序来成膜硅氧化膜,并向形成于晶圆w的表面的凹部内填充(埋入)。如此,在改性处理中使用n2/h2气体时,硅氧化膜的表面的oh
基(参照图11的(a))利用改性处理中供给的nh活性物种而被nh2基取代(参照图11的(b))。另一方面,在改性处理中使用ar/n2气体时,硅氧化膜的表面的oh基(参照图12的(a))在改性处理中被n基取代(参照图12的(b))。
[0088]
在此,由于si-n键的键离解能为302kj/mol,si-nh2键的键离解能为286kj/mol,si-nh2键比si-n键更容易被o3气取代。因此,在向si-nh2键供给o3气时,si-nh2键断裂而相邻的si原子之间经由o原子形成化学键(si-o-si键)(参照图11的(c))。可推测如此一来在膜中不容易出现基于物理键的边界部分,能够抑制在随后的蚀刻工序中出现接缝。
[0089]
另一方面,在改性处理中使用ar/n2气体的情况下,当向si-n键供给o3气时,相邻的si原子间难以经由o原子形成化学键。因此,在膜中,基于键合力比化学键弱的oh基彼此相邻的物理键而出现边界部分(参照图12的(c))。如此一来,由于膜中因物理键而容易出现边界部分,因此,可推测在随后的蚀刻工序中,基于物理键的边界部分比其它部分容易被蚀刻而出现接缝。
[0090]
(实施例)
[0091]
对于实施一实施方式的成膜方法、并进行实施结果的评价的实施例1进行说明。在实施例1中,作为晶圆w,使用表面形成有沟槽的硅晶圆。
[0092]
首先,在上述的成膜装置的旋转台2的凹部24内载置硅晶圆,自分离气体喷嘴41、42喷出作为分离气体的ar气体,自分离气体供给管51和吹扫气体供给管72喷出ar气体。另外,利用压力控制器65将真空容器1内控制在预先设定的处理压力。接着,一边使旋转台2向顺时针方向旋转一边利用加热器单元7将硅晶圆加热至处理温度。
[0093]
之后,自反应气体喷嘴31供给氨基硅烷气体,自反应气体喷嘴32供给氧化气体。另外,自反应气体喷嘴33供给改性气体,对于等离子体产生源80的天线85供给具有13.56mhz的频率的高频。
[0094]
进而,利用旋转台2的旋转,使硅晶圆反复按顺序穿过氨基硅烷气体吸附区域p1、分离区域d、氧化气体供给区域p2、等离子体处理区域p3以及分离区域d,向沟槽内进行硅氧化膜的埋入。需要说明的是,在实施例1中,以使硅氧化膜埋入于沟槽内的一部分的方式调节处理时间。
[0095]
处理条件如下。
[0096]
处理温度:400℃
[0097]
处理压力:240pa
[0098]
氨基硅烷气体:二异丙基氨基硅烷(dipas)气体
[0099]
氧化气体:o3气
[0100]
改性气体:ar/o2气体、ar/n2气体、ar/n2/h2气体
[0101]
高频电力:4000w
[0102]
旋转台2的转速:20rpm
[0103]
接下来,使用扫描型电子显微镜(sem:scanning electron microscope),观察埋入于沟槽内的一部分的硅氧化膜,由此评价硅氧化膜的高度差覆盖性。
[0104]
图13是表示实施例1的实施结果的图,示出改性气体的种类与高度差覆盖性之间的关系。在图13中,横坐标表示改性气体的种类,纵坐标表示沟槽的高度方向的中央部(以下称为“mid”。)相对于上部(以下称为“top”。)的膜厚的比例[%]。
[0105]
如图13所示,在使用ar/n2/h2气体时,在n2/h2气体的流量比为1:1、1:2、1:3的任一种情况下,mid相对于top的膜厚的比例为250~300%的范围内。另一方面,在使用ar/o2气体时,mid相对于top的膜厚的比例为100~150%的范围内。另外,在使用ar/n2气体时,mid相对于top的膜厚的比例为150~200%的范围内。
[0106]
根据这些结果,可以说通过使用ar/n2/h2气体,与使用ar/o2气体、ar/n2气体的情况相比,可以提高mid相对于top的膜厚的比例。即,通过使用ar/n2/h2气体,与使用ar/o2气体、ar/n2气体的情况相比,能够促进自下而上成膜。
[0107]
接着,对于实施一实施方式的成膜方法并进行实施结果的评价的实施例2进行说明。在实施例2中,与实施例1同样地,使用表面形成有沟槽的硅晶圆作为晶圆w。
[0108]
首先,在上述的成膜装置的旋转台2的凹部24内载置硅晶圆,自分离气体喷嘴41、42喷出作为分离气体的ar气体,自分离气体供给管51和吹扫气体供给管72喷出ar气体。另外,利用压力控制器65将真空容器1内控制在预先设定的处理压力。接着,一边使旋转台2向顺时针方向旋转一边利用加热器单元7将硅晶圆加热至处理温度。
[0109]
之后,自反应气体喷嘴31供给氨基硅烷气体,自反应气体喷嘴32供给氧化气体。另外,自反应气体喷嘴33供给改性气体,对于等离子体产生源80的天线85供给具有13.56mhz的频率的高频。
[0110]
进而,利用旋转台2的旋转,使硅晶圆反复按顺序穿过氨基硅烷气体吸附区域p1、分离区域d、氧化气体供给区域p2、等离子体处理区域p3及分离区域d,向沟槽内进行硅氧化膜的埋入。需要说明的是,在实施例2中,以使硅氧化膜完全埋入于沟槽内的方式调节处理时间。除了处理时间以外,处理条件与实施例1相同。
[0111]
接下来,通过使用有稀氢氟酸(dhf:diluted hydrofluoric acid)的湿式蚀刻法,对硅氧化膜进行蚀刻并去除直至硅晶圆的表面露出为止。
[0112]
接下来,使用扫描型电子显微镜(sem:scanning electron microscope),来确认残留于沟槽内的硅氧化膜上是否出现了接缝。
[0113]
图14是表示实施例2的实施结果的图,是表示埋入于沟槽内的硅氧化膜的蚀刻前后的截面的sem图像。图14的(a)和图14的(b)分别为使用ar/o2气体(o2气体供给量:75sccm)作为改性气体时的蚀刻前后的sem图像。图14的(c)和图14的(d)分别为使用ar/n2气体(n2气体供给量:50sccm)作为改性气体时的蚀刻前后的sem图像。图14的(e)和图14的(f)分别为使用ar/n2/h2气体(n2气体供给量:50sccm、h2气体供给量:100sccm)作为改性气体时的蚀刻前后的sem图像。需要说明的是,在图14的sem图像中,对出现了接缝的部分标记虚拟线(虚线)。
[0114]
首先,对硅氧化膜向沟槽内的埋入特性进行研究。如图14的(a)、图14的(c)和图14的(e)所示,在使用ar/o2气体、ar/n2气体及ar/n2/h2气体作为改性气体时,能够将硅氧化膜埋入于沟槽内而不会出现空隙、接缝等。即,可以说不管使用上述的哪一种气体作为改性气体,都可以获得良好的埋入特性。
[0115]
接着,对由埋入后的蚀刻带来的影响进行研究。如图14的(f)所示,在使用ar/n2/h2气体作为改性气体时,埋入于沟槽内的硅氧化膜上没有出现接缝。另一方面,如图14的(b)所示,在使用ar/o2气体作为改性气体时,埋入于沟槽内的硅氧化膜上出现了较大的接缝。另外,如图14的(d)所示,在使用ar/n2气体作为改性气体时,埋入于沟槽内的硅氧化膜出现
了较小的接缝。即,可以说通过使用ar/n2/h2气体作为改性气体,能够将硅氧化膜埋入于沟槽内而不会因埋入后的蚀刻而出现接缝。
[0116]
应该认为,此次公开的实施方式在所有方面为示例,而并不是限制性的解释。上述的实施方式只要不偏离所附的权利要求书及其主旨,就能够以各种各样的形态进行省略、置换、变更。