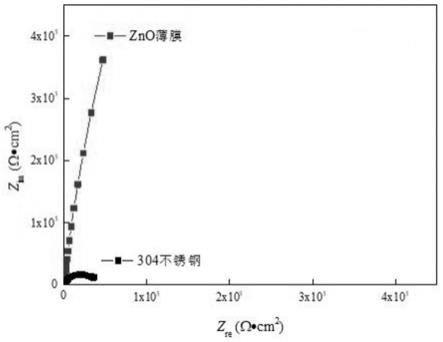
一种阻变型zno耐蚀薄膜及其制备方法
技术领域
1.本发明涉及一种阻变型耐蚀保护薄膜的制备方法,具体来说是一种含氧空位缺陷的zno薄膜,可以通过控制制备条件来改变薄膜的电阻值。
背景技术:2.钢在在服役过程中一般都会处在介质环境中,而钢在介质中发生的最主要的腐蚀形式就是电化学腐蚀。从本质上说,钢的电化学腐蚀原理由铁的阳极溶解fe
→
fe
2+
+2e-与氧去极化o2+2h2o+4e-→
4oh-或氢去极化2h
+
+2e-→
h2过程组成,从而使钢材表面形成大量氧化物,导致钢铁各种性能的下降,造成大量财产损失。钢表面的锈层,包括铁的氧化物fe(oh)2、fe(oh)3、α-feooh、β-feooh、γ-feooh和δ-feooh等。其中α-feooh就是一种很好的保护锈层(m.yamashita,h.miyuki,h.nagano,t.misawa,proceedings of13th international corrosion congress,melbourne,1996,pp.258
–
264.)。但是在自然环境下,钢铁表面形成的锈层结构疏松,耐蚀性不强,不能起到保护的作用。而要想在自然环境下得到致密的保护性锈层,需要数年的时间,显然,在这样的形成时间下,钢铁已经开始失效,意义不大。
3.针对这种情况,在碳钢中加入cu、cr、p、ni、co、si、al、co等合金元素,可以促进锈层中α-feooh的形成与致密化,并在内锈层中形成具有阳离子选择性的α-fe
1-x
cr
x
ooh或fe2cro4等尖晶石型氧化物(钝化膜),从而有效地隔离了腐蚀介质与钢基体的接触、阻止了水和腐蚀性离子(如cl-、so
42-等)的浸入,从而起到了减缓腐蚀的效果(董杰,董俊华,韩恩厚,等.低碳钢在模拟酸与大气条件下的腐蚀演化[j].腐蚀科学与防护技术,2009,21(1):1-4.)。
[0004]
除了改变钢铁自身的元素组成和结构外,常见的保护措施还有改变环境、电化学防护、涂层保护等方法。其中,涂层保护法因为其成本价格低廉,操作简单等特点,目前已经成为使用最为广泛的腐蚀防护方法。涂层防护,主要包括金属涂层、非金属涂层和化学转化膜等。金属涂层,是通过物理方法或化学(电化学)方法等将锌、镉等阳极性涂层及镍、锡等阴极性涂层沉积在材料表面;但存在制备温度高(热浸镀、渗镀、堆焊等)、设备较复杂(等离子喷涂、真空蒸镀等)、脆性大(电镀、化学镀等)、对环境有污染(电镀、化学镀等)等缺点,一定程度上限制了金属涂层在防腐蚀过程中的应有作用。非金属涂层的原理是通过有机高分子和陶瓷等膜层隔绝腐蚀介质从而达到防护的效果。但是这类涂层普遍厚度较高,不够美观。化学转化膜是通过钢铁中铁原子与转化溶液中的物质发生化学反应从而形成一层耐蚀性的膜层,效果最为突出的是cr离子转化膜,但是由于cr元素具有毒性,这种转化膜基本已经被禁止使用。所以寻找一种良好的耐蚀性保护涂层是十分必要的。
[0005]
阻变性薄膜,是一种在外加电场的作用下在高阻态和低阻态之间实现可逆转变的材料。阻变性能的产生,是源于材料内部存在的大量氧空位,这些氧空位在电场的作用下会产生漂移,形成导电细丝使材料向低阻态转变,而导电细丝的断裂又使材料重新回到高阻态,从而实现高阻态和低阻态之间的可逆转变。目前,已发现的具有忆阻特性的材料主要
有:硫化物、有机薄膜、金属氧化物等。氧化锌是直接宽带禁带(3.37ev)半导体,具有较高的电子束缚能(60mev)。早期的氧化锌就在涂料、医药等领域有简单的应用。在被发现荧光特性之后,对纳米尺寸的氧化锌研究更为深入,使其导带、价带的费米能级可调控,从而改变可氧化锌在整个波段的光子利用率。而且氧化锌存在大量空位型缺陷,是天然的n型半导体材料。这些特征使氧化锌在光学器件、光催化、半导体领域都得到了广泛的应用。研究结果表明,由于氧化锌含有大量空位型缺陷(主要是氧空位),并且氧空位会随电压的变化而漂移,消失或产生,因此氧化锌的电阻会随电压的变化而变化。因此,它是一种良好的阻变薄膜材料。当这种电阻膜工作时,环境中的氧阴离子将被吸附在其表面上,然后与膜中的氧空位重新结合,从而减少了氧空位的数量,并且高电阻值电阻状态增加。这是阻变薄膜的环境屏蔽作用。目前,还没有人将这种具有阻变特性的半导体材料用于钢的腐蚀防护。
技术实现要素:[0006]
本发明的目的在于克服现有技术的不足,提供一种阻变型zno耐蚀薄膜及其制备方法,利用薄膜的致密性阻碍腐蚀性离子向基底的扩散,利用薄膜中氧空位结合氧的能力阻碍氧向基底的扩散,从而达到减缓基底腐蚀的作用。并通过改变工艺参数达到调控氧空位浓度(mg掺杂浓度),进而调控薄膜的电阻值。
[0007]
本发明的技术方案是以二水合乙酸锌(zn(ch3coo)2·
2h2o)、四水合乙酸镁(mg(ch3coo)2·
4h2o)、单乙醇胺(c2h7no)和乙二醇甲醚(ch3och2ch2oh)为原料,通过溶胶-凝胶法制备出具有纳米级厚度、耐蚀性良好、电阻值可控的zno薄膜以及mg
x
zn
1-x
o薄膜。
[0008]
本发明的技术目的通过下述技术方案予以实现。
[0009]
一种阻变型zno耐蚀薄膜及其制备方法,按照下述步骤进行:
[0010]
步骤1,将二水合乙酸锌或者二水合乙酸锌和四水合乙酸镁的混合物均匀分散在乙二醇甲醚中,加入与二水合乙酸锌同摩尔量的乙醇胺,均匀分散后在室温20—25摄氏度下进行陈化,以得到溶胶
[0011]
在步骤1中,使用磁力搅拌器进行搅拌,以分散均匀,搅拌速度为每分钟100—200转,搅拌时间为6—12小时,陈化时间为24小时以上,优选24—30小时。
[0012]
在步骤1中,使用二水合乙酸锌制备溶胶时,乙酸锌浓度为0.1-1mol/l。即称取2.195-21.95g的二水合乙酸锌置于烧杯中,加入100ml乙二醇甲醚。使用磁力搅拌器进行搅拌,可观察到形成浑浊液。之后加入与二水合乙酸锌同摩尔量的乙醇胺,可观察到浑浊液变澄清。继续搅拌6-12h。在室温下陈化24h以上,得到稳定的0.1-1mol/l的乙酸锌溶胶。
[0013]
在步骤1中,使用二水合乙酸锌和四水合乙酸镁的混合物制备溶胶时,金属离子总浓度为0.1-1.0mol/l,锌离子与镁离子的摩尔比为zn:mg=(1-x):x,x为0.05-0.50。即称取1.317g-20.853g二水合乙酸锌和0.1072g-0.8578g四水合乙酸镁置于烧杯中,加入100ml乙二醇甲醚。使用磁力搅拌器进行搅拌,可观察到形成浑浊液。之后加入与二水合乙酸锌同摩尔量的乙醇胺,可观察到浑浊液变澄清。继续搅拌6-12h。在室温下陈化24h以上,得到金属离子总浓度为0.1-1.0mol/l、mg掺杂浓度为5%-50%的乙酸锌溶胶。其中锌离子与镁离子的浓度比为zn:mg=(1-x):x,x为0.05-0.50,mg
x
zn
1-x
o(x为0.05-0.50)。
[0014]
步骤2,使用步骤1得到的溶胶在基底上进行涂膜,以得到涂膜试样;
[0015]
在步骤2中,采用304不锈钢作为基底,使用不同型号的砂纸依次进行打磨,打磨后
抛光,用去离子水清洗后在酒精中超声5-30min,优选10-20min,吹干后备用。
[0016]
在步骤2中,采用静态旋涂法进行涂膜,转速控制在1000-3000r/min,旋涂完毕后,放入80-160℃的烘箱中烘干5-20min,每涂一层重复上述操作,共旋涂6-16层。
[0017]
在步骤2中,采用静态旋涂法进行涂膜,转速控制在1000-2000r/min,旋涂完毕后,放入100-150℃的烘箱中烘干10-20min,每涂一层重复上述操作,共旋涂8-16层。
[0018]
步骤3,将步骤2得到的涂膜试样置于惰性保护气氛中进行退火处理,自室温20—25摄氏度升温至退火温度,经退火后随炉冷却到室温,即可获得阻变型zno耐蚀薄膜;其中升温速度为1-5℃/min,退火温度为350-600℃,退火时间0.5-1.5h。
[0019]
在步骤3中,惰性保护气氛为氮气、氦气或者氩气。
[0020]
在步骤3中,退火温度为400-600℃,退火时间1-1.5h。
[0021]
本发明采用溶胶-凝胶法在制备出zno薄膜以及mg掺杂的zno阻变薄膜(mg
x
zn
1-x
o),利用阻变薄膜吸附和结合氧气的能力,大大减慢氧气向金属表面的扩散速度,从而减缓氧化的发生。而且还可通过改变mg的掺杂浓度控制薄膜(mg
x
zn
1-x
o)的氧空位含量获得具有不同电阻值的耐蚀薄膜。本发明制备出的zno薄膜均匀致密、晶粒尺寸在10nm以下,可以有效的阻挡溶液以及腐蚀性离子向304不锈钢基底的扩散,此外,制备出的zno薄膜含有大量氧空位,利用阻变薄膜中氧空位可以结合吸附氧的特点,可以阻碍环境中氧向基底的扩散,大大降低了基底的腐蚀速率。
[0022]
(1)良好的耐蚀性能将制备好的样品使用环氧树脂进行密封,只留制备有zno薄膜的一面,并将四周密封,只留薄膜一面中心1cm2的面积,使用封样后面积为1cm2的未处理304不锈钢作为空白对照组。使用ag/agcl电极和铂片作为参比电极和对电极,利用autolab302电化学工作站测定了样品在3.5%nacl溶液中浸泡1h后的电化学阻抗谱和极化曲线,如图1和图2所示。从图1可以看出,制备有zno薄膜的阻抗弧半径明显增大。经拟合计算可以得出zno薄膜的保护效率达到了99.51%。从图2可以看出,制备有zno薄膜和未处理的304不锈钢相比,腐蚀电位正移十分明显,腐蚀电流密度也下降了将近两个数量级,经拟合计算可以得到薄膜的保护效率达到了99.27%,即zno阻变薄膜对在氯离子环境中工作的304不锈钢具有良好的保护效果。
[0023]
(2)良好的阻变性能分别将退火温度为350℃、400℃、450℃、500℃制备出的zno薄膜样品封样处理,使用ag/agcl电极和铂片作为参比电极和对电极,利用autolab 302电化学工作站测定了样品在3.5%nacl溶液中浸泡1h后的电化学阻抗谱和极化曲线,如图3所示。从图中可以看出,不同退火温度制备出的zno薄膜样品的阻抗弧半径是不同的,这说明它们的电阻值也是不同的,随退火温度升高,阻抗弧半径先增大后减小,在400℃达到最大,即电阻值达到最大。由此可见制备出的zno薄膜实现了电阻值可控的阻变性能。
[0024]
(3)良好的耐蚀性能将制备好的样品使用环氧树脂进行密封,只留制备有mg
x
zn
1-x
o薄膜的一面,并将四周密封,只留薄膜一面中心1cm2的面积,使用封样后面积为1cm2的未处理304不锈钢作为空白对照组。使用ag/agcl电极和铂片作为参比电极和对电极,利用autolab302电化学工作站测定了样品在3.5%nacl溶液中的电化学阻抗谱和极化曲线,如图4和图5所示。从图4可以看出,制备有mg
x
zn
1-x
o薄膜的阻抗弧半径均明显增大。不同掺杂浓度制备出的mg
x
zn
1-x
o薄膜样品的阻抗弧半径是不同的,这说明它们的电阻值也是不同的,掺杂浓度为0.10时,阻抗弧半径达到最大,即电阻值达到最大,经拟合计算可以得出
mg
0.1
zn
0.9
o薄膜的保护效率最高可达到93.06%,由此可见制备出的mg
x
zn
1-x
o薄膜实现了电阻值可控的阻变性能。从图5可以看出,制备有mg
x
zn
1-x
o薄膜和未处理的304不锈钢相比,腐蚀电位正移均十分明显,腐蚀电流密度也下降了将近两个数量级,即mg
x
zn
1-x
o阻变薄膜对在氯离子环境中工作的304不锈钢具有良好的保护效果。
附图说明
[0025]
图1是本发明制备的zno薄膜在3.5%nacl溶液中浸泡1小时后的电化学阻抗谱测试结果谱线图。
[0026]
图2是本发明制备的zno薄膜在3.5%nacl溶液中浸泡1小时后的极化曲线测试结果谱线图。
[0027]
图3是本发明制备的不同退火温度下zno薄膜在3.5%nacl溶液中浸泡1小时后的极化曲线测试结果谱线图。
[0028]
图4是本发明制备的不同mg掺杂浓度mg
x
zn
1-x
o薄膜在3.5%nacl溶液中的电化学阻抗谱测试结果谱线图。
[0029]
图5是本发明制备的不同mg掺杂浓度mg
x
zn
1-x
o薄膜在3.5%nacl溶液中的极化曲线测试结果谱线图。
具体实施方式
[0030]
下面结合附图和实施例对本发明做进一步的说明,但本发明不限于这些具体的实施例。
[0031]
实施例1
[0032]
(1)称取2.195g的二水合乙酸锌置于烧杯中,加入100ml乙二醇甲醚。使用磁力搅拌器进行搅拌,可观察到形成浑浊液;之后加入与二水合乙酸锌同摩尔量的乙醇胺,可观察到浑浊液变澄清。继续搅拌12h。在室温下陈化24h以上,得到稳定0.1mol/l的乙酸锌溶胶。
[0033]
(2)采用304不锈钢作为基底。使用不同型号的砂纸依次进行打磨,打磨后抛光,用去离子水清洗后在酒精中超声15min,吹干后备用。
[0034]
(3)采用静态旋涂法进行涂膜,转速控制在1000r/min,旋涂完毕后,放入150℃的烘箱中烘干15min。每涂一层重复上述操作。共旋涂12层。
[0035]
(4)涂膜完毕后,将试样置于方舟中放入到管式炉中,先通氮气排净装置中的空气,再抽真空,重复两次,最后通入氮气后密封。升温速度为5℃/min,退火温度为400℃,退火时间0.5h,退火后随炉冷却到室温后取出。
[0036]
实施例2
[0037]
(1)称取6.585g的二水合乙酸锌置于烧杯中,加入100ml乙二醇甲醚。使用磁力搅拌器进行搅拌,可观察到形成浑浊液;之后加入与二水合乙酸锌同摩尔量的乙醇胺,可观察到浑浊液变澄清。继续搅拌12h。在室温下陈化24h以上,得到稳定的0.3mol/l的乙酸锌溶胶。
[0038]
(2)采用304不锈钢作为基底。使用不同型号的砂纸依次进行打磨,打磨后抛光,用去离子水清洗后在酒精中超声18min,吹干后备用。
[0039]
(3)采用静态旋涂法进行涂膜,转速控制在1500r/min,旋涂完毕后,放入130℃的
烘箱中烘干15min。每涂一层重复上述操作。共旋涂12层。
[0040]
(4)涂膜完毕后,将试样置于方舟中放入到管式炉中,先通氮气排净装置中的空气,再抽真空,重复两次,最后通入氮气后密封。升温速度为4℃/min,退火温度为450℃,退火时间1.5h,退火后随炉冷却到室温后取出。
[0041]
实施例3
[0042]
(1)称取10.975g的二水合乙酸锌置于烧杯中,加入100ml乙二醇甲醚。使用磁力搅拌器进行搅拌,可观察到形成浑浊液;之后加入与二水合乙酸锌同摩尔量的乙醇胺,可观察到浑浊液变澄清。继续搅拌12h。在室温下陈化24h以上,得到稳定的0.5mol/l的乙酸锌溶胶。
[0043]
(2)采用304不锈钢作为基底。使用不同型号的砂纸依次进行打磨,打磨后抛光,用去离子水清洗后在酒精中超声17min,吹干后备用。
[0044]
(3)采用静态旋涂法进行涂膜,转速控制在2000r/min,旋涂完毕后,放入100℃的烘箱中烘干11min。每涂一层重复上述操作。共旋涂12层。
[0045]
(4)涂膜完毕后,将试样置于方舟中放入到管式炉中,先通氮气排净装置中的空气,再抽真空,重复两次,最后通入氮气后密封。升温速度为3℃/min,退火温度为560℃,退火时间0.8h,退火后随炉冷却到室温后取出。
[0046]
实施例4
[0047]
(1)称取15.365g的二水合乙酸锌置于烧杯中,加入100ml乙二醇甲醚。使用磁力搅拌器进行搅拌,可观察到形成浑浊液;之后加入与二水合乙酸锌同摩尔量的乙醇胺,可观察到浑浊液变澄清。继续搅拌12h。在室温下陈化24h以上,得到稳定的0.7mol/l的乙酸锌溶胶。
[0048]
(2)采用304不锈钢作为基底。使用不同型号的砂纸依次进行打磨,打磨后抛光,用去离子水清洗后在酒精中超声10min,吹干后备用。
[0049]
(3)采用静态旋涂法进行涂膜,转速控制在1200r/min,旋涂完毕后,放入140℃的烘箱中烘干15min。每涂一层重复上述操作。共旋涂12层。
[0050]
(4)涂膜完毕后,将试样置于方舟中放入到管式炉中,先通氮气排净装置中的空气,再抽真空,重复两次,最后通入氮气后密封。升温速度为2℃/min,退火温度为500℃,退火时间1h,退火后随炉冷却到室温后取出。
[0051]
实施例5
[0052]
(1)称取21.95g的二水合乙酸锌置于烧杯中,加入100ml乙二醇甲醚。使用磁力搅拌器进行搅拌,可观察到形成浑浊液;之后加入与二水合乙酸锌同摩尔量的乙醇胺,可观察到浑浊液变澄清。继续搅拌12h。在室温下陈化24h以上,得到稳定的1.0mol/l的乙酸锌溶胶。
[0053]
(2)采用304不锈钢作为基底。使用不同型号的砂纸依次进行打磨,打磨后抛光,用去离子水清洗后在酒精中超声20min,吹干后备用。
[0054]
(3)采用静态旋涂法进行涂膜,转速控制在1000r/min,旋涂完毕后,放入120℃的烘箱中烘干20min。每涂一层重复上述操作。共旋涂12层。
[0055]
(4)涂膜完毕后,将试样置于方舟中放入到管式炉中,先通氮气排净装置中的空气,再抽真空,重复两次,最后通入氮气后密封。升温速度为1℃/min,退火温度为350℃,退
火时间1.2h,退火后随炉冷却到室温后取出。
[0056]
实施例6
[0057]
(1)称取1.537g的二水合乙酸锌和0.642g四水合乙酸镁置于烧杯中,加入100ml乙二醇甲醚。使用磁力搅拌器进行搅拌,可观察到形成浑浊液;之后加入与金属离子同摩尔量的乙醇胺,可观察到浑浊液变澄清。继续搅拌12h。在室温下陈化24h以上,得到金属离子总浓度为0.1mol/l、mg掺杂浓度为30%的乙酸锌溶胶。
[0058]
(2)采用304不锈钢作为基底。使用不同型号的砂纸依次进行打磨,打磨后抛光,用去离子水清洗后在酒精中超声15min,吹干后备用。
[0059]
(3)采用静态旋涂法进行涂膜,转速控制在1000r/min,旋涂完毕后,放入150℃的烘箱中烘干15min。每涂一层重复上述操作。共旋涂12层。
[0060]
(4)涂膜完毕后,将试样置于方舟中放入到管式炉中,先通氮气排净装置中的空气,再抽真空,重复2次,最后通入氮气后密封。升温速度为5℃/min,退火温度为400℃,退火时间0.5h,退火后随炉冷却到室温后取出,获得阻变型mg
0.3
zn
0.7
o耐蚀薄膜。
[0061]
实施例7
[0062]
(1)称取3.951g的二水合乙酸锌和2.574g四水合乙酸镁置于烧杯中,加入100ml乙二醇甲醚。使用磁力搅拌器进行搅拌,可观察到形成浑浊液;之后加入与金属离子同摩尔量的乙醇胺,可观察到浑浊液变澄清。继续搅拌8h。在室温下陈化24h以上,得到稳定的金属离子总浓度为0.3mol/l、mg掺杂浓度为40%的乙酸锌溶胶。
[0063]
(2)采用304不锈钢作为基底。使用不同型号的砂纸依次进行打磨,打磨后抛光,用去离子水清洗后在酒精中超声18min,吹干后备用。
[0064]
(3)采用静态旋涂法进行涂膜,转速控制在1500r/min,旋涂完毕后,放入130℃的烘箱中烘干15min。每涂一层重复上述操作。共旋涂10层。
[0065]
(4)涂膜完毕后,将试样置于方舟中放入到管式炉中,先通氮气排净装置中的空气,再抽真空,重复3次,最后通入氮气后密封。升温速度为4℃/min,退火温度为450℃,退火时间1.5h,退火后随炉冷却到室温后取出,获得阻变型mg
0.4
zn
0.6
o耐蚀薄膜。。
[0066]
实施例8
[0067]
(1)称取8.780g的二水合乙酸锌和2.145g四水合乙酸镁置于烧杯中,加入100ml乙二醇甲醚。使用磁力搅拌器进行搅拌,可观察到形成浑浊液;之后加入与金属离子同摩尔量的乙醇胺,可观察到浑浊液变澄清。继续搅拌6h。在室温下陈化24h以上,得到稳定的金属离子总浓度为0.5mol/l、mg掺杂浓度为20%的乙酸锌溶胶。
[0068]
(2)采用304不锈钢作为基底。使用不同型号的砂纸依次进行打磨,打磨后抛光,用去离子水清洗后在酒精中超声25min,吹干后备用。
[0069]
(3)采用静态旋涂法进行涂膜,转速控制在3000r/min,旋涂完毕后,放入100℃的烘箱中烘干20min。每涂一层重复上述操作。共旋涂14层。
[0070]
(4)涂膜完毕后,将试样置于方舟中放入到管式炉中,先通氮气排净装置中的空气,再抽真空,重复2次,最后通入氮气后密封。升温速度为3℃/min,退火温度为500℃,退火时间0.8h,退火后随炉冷却到室温后取出,获得阻变型mg
0.2
zn
0.8
o耐蚀薄膜。。
[0071]
实施例9
[0072]
(1)称取13.828g的二水合乙酸锌和1.502g四水合乙酸镁置于烧杯中,加入100ml
乙二醇甲醚。使用磁力搅拌器进行搅拌,可观察到形成浑浊液;之后加入与金属离子同摩尔量的乙醇胺,可观察到浑浊液变澄清。继续搅拌12h。在室温下陈化24h以上,得到稳定的金属离子总浓度为0.7mol/l、mg掺杂浓度为50%的乙酸锌溶胶。
[0073]
(2)采用304不锈钢作为基底。使用不同型号的砂纸依次进行打磨,打磨后抛光,用去离子水清洗后在酒精中超声10min,吹干后备用。
[0074]
(3)采用静态旋涂法进行涂膜,转速控制在2000r/min,旋涂完毕后,放入140℃的烘箱中烘干15min。每涂一层重复上述操作。共旋涂12层。
[0075]
(4)涂膜完毕后,将试样置于方舟中放入到管式炉中,先通氮气排净装置中的空气,再抽真空,重复4次,最后通入氮气后密封。升温速度为2℃/min,退火温度为450℃,退火时间1h,退火后随炉冷却到室温后取出,获得阻变型mg
0.5
zn
0.5
o耐蚀薄膜。。
[0076]
实施例10
[0077]
(1)称取16.4625g的二水合乙酸锌和5.362g四水合乙酸镁置于烧杯中,加入100ml乙二醇甲醚。使用磁力搅拌器进行搅拌,可观察到形成浑浊液;之后加入与金属离子同摩尔量的乙醇胺,可观察到浑浊液变澄清。继续搅拌10h。在室温下陈化24h以上,得到稳定的金属离子总浓度为1.0mol/l、mg掺杂浓度为5%的乙酸锌溶胶。
[0078]
(2)采用304不锈钢作为基底。使用不同型号的砂纸依次进行打磨,打磨后抛光,用去离子水清洗后在酒精中超声5min,吹干后备用。
[0079]
(3)采用静态旋涂法进行涂膜,转速控制在2500r/min,旋涂完毕后,放入120℃的烘箱中烘干20min。每涂一层重复上述操作。共旋涂8层。
[0080]
(4)涂膜完毕后,将试样置于方舟中放入到管式炉中,先通氮气排净装置中的空气,再抽真空,重复3次,最后通入氮气后密封。升温速度为1℃/min,退火温度为350℃,退火时间1.2h,退火后随炉冷却到室温后取出,获得阻变型mg
0.05
zn
0.95
o耐蚀薄膜。
[0081]
根据本发明内容进行工艺参数的调整,均可实现阻变型zno耐蚀薄膜的制备,经测试表现出与本发明基本一致的性能。以上对本发明做了示例性的描述,应该说明的是,在不脱离本发明的核心的情况下,任何简单的变形、修改或者其他本领域技术人员能够不花费创造性劳动的等同替换均落入本发明的保护范围。