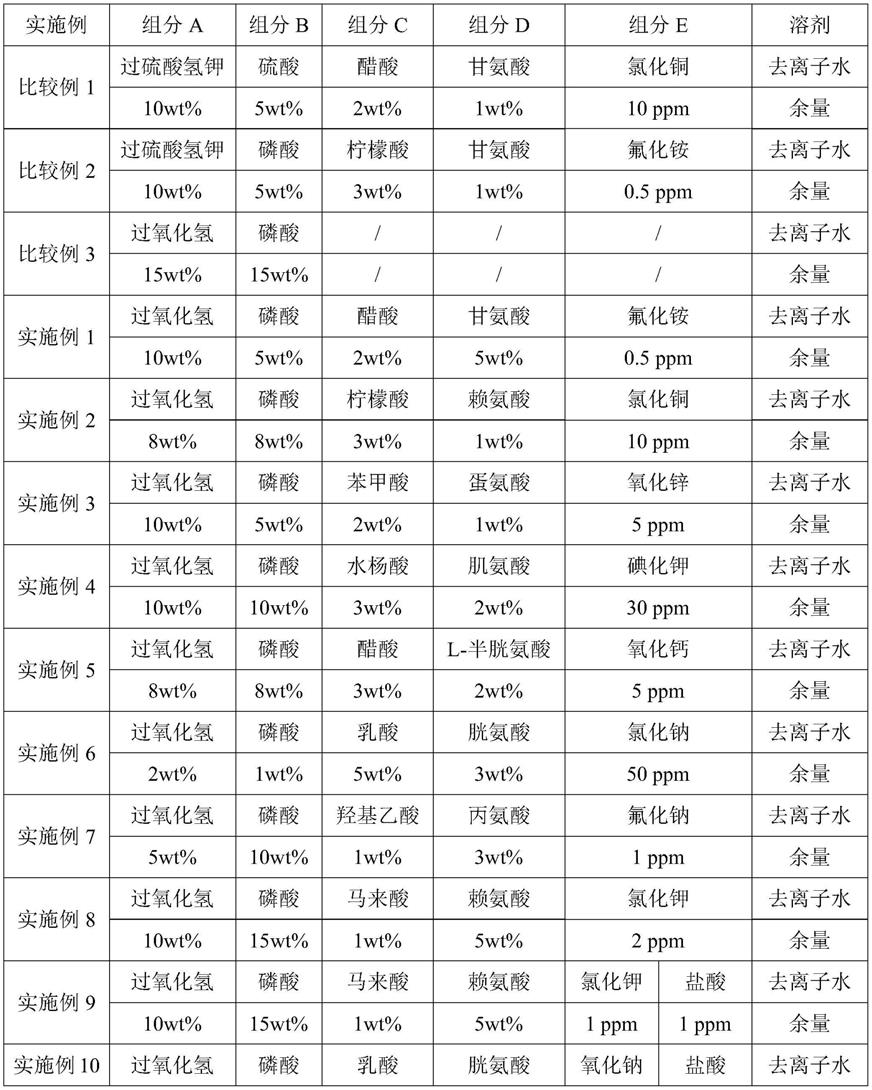
1.本发明涉及芯片加工技术领域,尤其涉及一种蚀刻组合物及其应用。
背景技术:2.在集成电路制造过程中,常常需要在晶圆上定义出极细微的图案(pattern),这些图案主要的形成方式,乃是借由蚀刻(etching)技术,将微影(micro-lithography)后产生的光阻图案转印到光阻下的材质上,以形成集体电路的复杂架构。在芯片制作完成后,将会有专门的封装厂为晶圆制作焊点或者称为凸点(bump),目的是为单颗芯片的下一步互联构建互联介质。我们称这个过程为先进封装工艺。同样的,封装厂也会通过图形化的过程为芯片的互联重新排布线路或者制作凸点。其中在晶圆制作完成后,首先要做的是,使用磁控溅射机台,在晶圆整面溅射一层钛和一层铜,业内称其为种子层。溅射钛层的目的是为了更好地与晶圆结合,溅射铜层的目的是为下一步电镀铜做连接。在电镀铜之前,需要用光阻进行图形化,让电镀铜可以落在开孔的地方。此时即可看出,整面溅射金属钛和铜的目的是为了在电镀时为导通电流提供介质,以便保证整面的开口区域都能电镀上金属。在一张晶圆上,一般少则几十个芯片,多则成千上万个芯片,因为铜层和钛层的存在,芯片上所有的互联位置是相互导通的,也就是处于短路状态。所以,在初期溅射的钛和铜需要采用蚀刻的方式将其去除,以保证芯片在制作完成互联凸点(bump)的同时具有特定的电性能。因此,蚀刻技术在半导体制造与先进封装过程中占有重要的地位。广义而言,所谓的蚀刻技术,包含了将材质整面均匀移除及图案选择性部分去除的技术。而其中大致可以分为湿式蚀刻(wet etching)和干式蚀刻(dry etching)两种技术。目前,湿式蚀刻因其具有低成本、高可靠性、高产能以及优越的蚀刻选择比等优点而被广泛使用于芯片的凸点(bump)制造过程中。
3.虽然湿式蚀刻因其具有的特殊优点而被大量应用先进封装工艺中,但是业内的铜蚀刻组合物仍存在以下缺点:
4.1、凸点因为等向性蚀刻的原因极易发生侧蚀的问题;
5.2、种子层极易发生底切(undercut);
6.3、铝电极损伤问题;
7.4、蚀刻化学反应过程中形成气泡造成的不完全及不均匀的蚀刻。
8.同时,湿式蚀刻除了要考虑上述几点问题外,还需要考虑蚀刻的反应速率;蚀刻组合物对于遮罩物(即前文中所述凸点)的侵蚀等问题。
9.在芯片凸点制造过程的制程相对成熟,但随着集成电路中的元件尺寸越做越小,要求凸点的尺寸进一步减小。由于化学反应没有方向性,因而湿法蚀刻是等向性(isotropic)的,此时,当蚀刻溶液做纵向蚀刻时,侧向的蚀刻将同时发生,进而造成底切(undercut)现象,导致图案线宽失真。上述问题将在很大程度上影响芯片的可靠性。
10.蚀刻组合物由于凸点上包含多层不同金属,且种子层的金属与凸点上的金属层不一样,因为多层金属的蚀刻速率存在差异而造成蚀刻效果难以控制,且不可避免的会存在凸点会发生侧蚀刻(critical dimensionloss,简称为cd loss)过大的问题,以及蚀刻后铜
层发生底切(undercut)等状况。目前,现有技术已经公开的蚀刻组合物体系主要的氧化剂为过氧化物,比较典型的为过硫酸盐和双氧水,但是,过硫酸盐作为氧化剂的蚀刻组合物对于对结构层中的镍层有严重损伤,而现有技术中已经公开的双氧水作为氧化剂的蚀刻组合物体系存在蚀刻后晶圆上的电路或焊点形貌不佳,影响芯片使用可靠性的问题。
11.在上述的双氧水蚀刻组合物中需要酸环境进行铜的溶解。在常见的无机酸中硫酸会对结构中的镍有严重腐蚀,硝酸对锡或锡合金、镍均有严重腐蚀,盐酸和氟酸具有很强的渗透性,将对芯片的下层金属铝有严重腐蚀。这些腐蚀对芯片的可靠性将产生致命打击。
技术实现要素:12.为了解决现有技术中存在的问题,本发明提供了一种蚀刻组合物,如上文所述的,在制作凸点的过程需要将铜层和钛层蚀刻掉,在提供芯片互联能力的同时,也保证其电性能,本发明的铜蚀刻组合物即为湿式蚀刻所用的药水,以腐蚀此工艺过程的铜层。所述蚀刻组合物通过添加剂的筛选和研究,在低金属损伤的情况下,能够很好地控制腐蚀的电路或焊点形貌,提高了芯片在封装互联中的可靠性。
13.本发明提供了一种蚀刻组合物,所述蚀刻组合物包含:组分a:氧化剂1~30wt%、组分b:无机酸0.5~20wt%、组分c:有机酸0~15wt%、组分d:螯合剂0.01~15wt%、组分e:离子化合物和/或除组分b所述无机酸外的其他无机酸0~0.1wt%,以及去离子水。
14.作为一种优选的技术方案,所述组分a:氧化物选自过氧化氢、过硫酸氢钾、过硫酸氢钠中的至少一种。
15.作为一种优选的技术方案,所述组分b:无机酸选自硝酸、硫酸、磷酸中的一种或多种的混合。
16.作为一种优选的技术方案,所述组分c:有机酸选自柠檬酸、醋酸、酒石酸、苹果酸、甲酸、丙酸、丁酸、异丁酸、戊酸、异戊酸、丙二酸、丁二酸、戊二酸、已二酸、羟基乙酸、丙烯酸、甲基丙烯酸、乳酸、葡萄糖酸、马来酸、苯甲酸、水杨酸中的一种或多种的混合。
17.作为一种优选的技术方案,所述有机酸的种类为一到五种。
18.作为一种优选的技术方案,所述组分d:螯合剂选自葡萄糖酸钠、柠檬酸钠、氨基酸中的一种或多种的混合。
19.作为一种优选的技术方案,所述氨基酸选自乙二胺四乙酸、二乙三胺五乙酸、丙氨酸、甘氨酸、天冬氨酸、谷氨酸、肌氨酸、l-半胱氨酸、赖氨酸、半胱氨酸、蛋氨酸中的一种或多种的混合。
20.作为一种优选的技术方案,所述组分e中可选的离子化合物为氧化物和/或无机盐。
21.作为一种优选的技术方案,所述组分e中所述无机酸选自盐酸、氢溴酸、氢碘酸、氢氟酸中的一种或多种的混合。
22.本发明还提供了一种如上所述的蚀刻组合物在制作芯片中的应用,所述芯片包含凸点及凸点下方的种子层;所述凸点包含锡或锡合金构成的上层、镍或镍铜合金构成的下层。
23.本发明提供了一种蚀刻组合物,相比于现有技术具有以下有益效果:
24.1.侧蚀刻(cd loss)小;
25.2.铜层底切undercut小;
26.3.对基板无损伤或损伤很小,不影响芯片的使用可靠性;
27.4.蚀刻均匀性好,且无蚀刻残渣;
28.5.蚀刻后晶圆上的电路或焊点形貌良好;
29.6.蚀刻组合物性能稳定。
附图说明
30.为了进一步解释说明本发明中提供的一种蚀刻组合物及其应用的有益效果,提供了相应的附图,需要指出的是本发明中提供的附图只是所有附图中选出来的个别示例,目的也不是作为对权利要求的限定,所有通过本技术中提供的附图获得的其他相应图谱均应该认为在本技术保护的范围之内。
31.图1为芯片凸点蚀刻前的结构示意图。
32.图2为芯片凸点蚀刻后的结构示意图。
具体实施方式
33.结合以下本发明的优选实施方法的详述以及包括的实施例可进一步地理解本发明的内容。除非另有说明,本技术中使用的所有技术及科学术语均具有与本技术所属领域普通技术人员的通常理解相同的含义。如果现有技术中披露的具体术语的定义与本技术中提供的任何定义不一致,则以本技术中提供的术语定义为准。
34.在本技术中使用的,除非上下文中明确地另有指示,否则没有限定单复数形式的特征也意在包括复数形式的特征。还应理解的是,如本技术所用术语“由
…
制备”与“包含”同义,“包括”、“包括有”、“具有”、“包含”和/或“包含有”,当在本说明书中使用时表示所陈述的组合物、步骤、方法、制品或装置,但不排除存在或添加一个或多个其它组合物、步骤、方法、制品或装置。此外,当描述本技术的实施方式时,使用“优选的”、“优选地”、“更优选的”等是指,在某些情况下可提供某些有益效果的本发明实施方案。然而,在相同的情况下或其他情况下,其他实施方案也可能是优选的。除此之外,对一个或多个优选实施方案的表述并不暗示其他实施方案不可用,也并非旨在将其他实施方案排除在本发明的范围之外。
35.为了解决现有技术中存在的问题,本发明提供了一种蚀刻组合物,所述蚀刻组合物包含:组分a:氧化剂1~30wt%、组分b:无机酸0.5~20wt%、组分c:有机酸0~15wt%、组分d:螯合剂0.01~15wt%、组分e:离子化合物和/或除组分b所述无机酸外的其他无机酸0~0.1wt%,余量为去离子水。
36.作为一种示例,所述组分a:氧化剂在蚀刻组合物中的重量百分比可以为1%、3%、5%、8%、10%、12%、15%、20%、22%、25%、30%等;作为一种示例,所述组分b:无机酸在蚀刻组合物中的重量百分比可以为0.5%、1%、2%、3%、5%、8%、10%、12%、15%、18%、20%等;作为一种示例,所述组分c:有机酸在蚀刻组合物中的重量百分比可以为0.1%、0.5%、1%、2%、3%、5%、8%、10%、12%、15%等;作为一种示例,所述组分d:螯合剂在蚀刻组合物中的重量百分比可以为0.1%、0.5%、0.8%、1%、1.2%、1.5%、1.8%、2%、2.2%、2.5%、2.8%、3%、3.2%、3.5%、3.8%、4%、4.2%、4.5%、4.8%、5%、8%、10%、12%、15%等;作为一种示例,所述组分e:离子化合物和/或除组分b所述无机酸外的其他无
机酸在蚀刻组合物中的重量占比可以为0.5ppm、1ppm、1.2ppm、1.5ppm、1.8ppm、2ppm、2.5ppm、2.8ppm、3ppm、3.2ppm、3.5ppm、3.8ppm、4ppm、4.2ppm、4.5ppm、4.8ppm、5ppm、5.2ppm、5.5ppm、5.8ppm、6ppm、6.5ppm、7ppm、7.5ppm、8ppm、8.5ppm、9ppm、9.5ppm、10ppm、15ppm、20ppm、25ppm、30ppm、35ppm、40ppm、45ppm、50ppm、60ppm、65ppm、68ppm、70ppm、75ppm、80ppm、82ppm、85ppm、90ppm、95ppm、100ppm等。
37.在一些优选的实施方式中,所述蚀刻组合物包含:组分a:氧化剂1~25wt%、组分b:无机酸0.5~15wt%、组分c:有机酸0~10wt%、组分d:螯合剂0.01~10wt%、组分e:离子化合物和/或除组分b所述无机酸外的其他无机酸0.1~100ppm,余量为去离子水;进一步优选的,所述蚀刻组合物包含:组分a:氧化剂1~20wt%、组分b:无机酸0.5~15wt%、组分c:有机酸0~5wt%、组分d:螯合剂0.1~10wt%、组分e:离子化合物和/或除组分b所述无机酸外的其他无机酸0.1~60ppm,以及去离子水。
38.在一些优选的实施方式中,所述组分a:氧化物选自过氧化氢、过硫酸氢钾、过硫酸氢钠中的至少一种;从蚀刻制程可控以及改善蚀刻过度的角度考虑,进一步优选的,所述氧化物为过氧化氢。
39.在一些优选的实施方式中,所述过氧化氢在蚀刻组合物中的占比为1~15wt%;进一步优选的,所述过氧化氢在蚀刻组合物中的占比为1~10wt%;更进一步的,所述过氧化氢在蚀刻组合物中的占比为2~10wt%。
40.在一些优选的实施方式中,所述组分b:无机酸不包含卤酸。
41.在一些优选的实施方式中,所述组分b:无机酸选自硝酸、硫酸、磷酸中的一种或多种的混合;从调节蚀刻反应速率的角度考虑,进一步优选的,所述组分b:无机酸为磷酸。发明人在研究中发现,无机酸可以溶解铜,对蚀刻反应速率有正向作用,但无机酸的用量超过20wt%时会造成物料过剩,增加成本负担。
42.在一些实施方式中,所述组分c:有机酸选自柠檬酸、醋酸、酒石酸、苹果酸、甲酸、丙酸、丁酸、异丁酸、戊酸、异戊酸、丙二酸、丁二酸、戊二酸、已二酸、羟基乙酸、丙烯酸、甲基丙烯酸、乳酸、葡萄糖酸、马来酸、苯甲酸、水杨酸中的一种或多种的混合;优选的,所述组分c:有机酸选自柠檬酸、醋酸、酒石酸、苹果酸、丁酸、草酸、丙二酸、丁二酸、羟基乙酸、丙烯酸、乳酸、马来酸、苯甲酸、水杨酸中的一种或多种的混合;进一步优选的,所述组分c:有机酸选自醋酸、柠檬酸、酒石酸、酒石酸、苹果酸、草酸、甲酸、丙烯酸、乳酸、马来酸、苯甲酸、水杨酸中的一种或多种的混合;更进一步的,所述组分c:有机酸选自醋酸、柠檬酸、酒石酸、苹果酸、草酸、甲酸、丙烯酸、乳酸、马来酸、苯甲酸、水杨酸中的一种或多种的混合。
43.在一些实施方式中,所述有机酸的种类为一到五种;优选的,所述有机酸的种类为至少两种、或至少三种、或至少四种;进一步优选的,所述有机酸的种类为一种、或两种、或三种、或四种。发明人在研究中发现,当有机酸的种类超过五种之后,蚀刻液对于金属蚀刻的速率以及蚀刻均一性存在影响。
44.为了保证蚀刻过程的安全性以及解决铜残留的问题,在实际制程中会在一般工艺余量的基础上将蚀刻时间增加15%,一些情况下甚至会增加至100%,这就导致蚀刻的铜金属会存在蚀刻金属蚀刻不均一的问题,所蚀刻金属的均匀度一般在15%以下。为了保证蚀刻的均一性,同时保证蚀刻过程的安全性并解决蚀刻金属残留的问题,本技术的发明人通过大量实验发现,添加占所述蚀刻组合物重量百分比为不超过15%的有机酸能够有效改善
铜蚀刻的均一性以及金属残留的问题,同时保证蚀刻过程的安全性,但是发明人同时也发现当有机酸的含量超过10%时将会明显抑制铜的蚀刻速率,因此,本发明所述的蚀刻组合物中所述有机酸的含量优选不超过10wt%,为了保证蚀刻速率满足要求,同时保证蚀刻的均一性,解决蚀刻中金属残留的问题以及保证蚀刻的安全性,所述有机酸占所述蚀刻的重量百分比优选为0~10%,进一步优选为0.1~5%。
45.在一些优选的实施方式中,所述组分d:螯合剂选自葡萄糖酸钠、柠檬酸钠、氨基酸中的一种或多种的混合;进一步优选的,所述组分d:螯合剂为氨基酸。
46.在一些优选的实施方式中,所述氨基酸选自乙二胺四乙酸、二乙三胺五乙酸、丙氨酸、甘氨酸、天冬氨酸、谷氨酸、肌氨酸、l-半胱氨酸、赖氨酸、半胱氨酸、蛋氨酸中的一种或多种的混合;进一步优选的,所述氨基酸选自丙氨酸、甘氨酸、赖氨酸、半胱氨酸、蛋氨酸中的一种或多种的混合;更进一步的,所述氨基酸选自赖氨酸、半胱氨酸、蛋氨酸中的一种或多种的混合。发明人在研发过程中发现,本发明所述氨基酸加入蚀刻组合物中,可以起到降低凸点和种子层的侧向腐蚀量cd的作用。发明人在大量的实践中还发现,当螯合剂在体系中的重量百分比在0.1~8%的范围内时,随着螯合剂含量的增加,所蚀刻铜凸点的侧向蚀刻量减少,而螯合剂占所述蚀刻组合物的重量百分比超过8%时,将会大大降低铜是蚀刻均匀度,并大幅增加铜残留的发生。发明人在仔细求证中发现所述螯合剂的含量趋近2wt%时,螯合剂的正向作用趋于平稳,即对于侧蚀量cd的改善达到最佳值。
47.在一些优选的实施方式中,当组分e为离子化合物时,所述离子化合物为氧化物和/或无机盐。
48.在一些优选的实施方式中,所述氧化物为碱性氧化物和/或两性氧化物;进一步优选的,所述碱性氧化物选自氧化钠、氧化钙、氧化镁中的一种或多种的混合,所述两性氧化物为氧化锌和/或氧化锰。
49.在一些优选的实施方式中,所述无机盐优选为卤化盐,所述卤化盐选自氯化铜、氯化铁、氯化钠、氯化铵、氯化钾、氯化钙、溴化铜、溴化铁、溴化钠、溴化铵、碘化铜、碘化铁、碘化钠、碘化铵、氟化铜、氟化铁、氟化钠、氟化铵中的一种或多种的混合;进一步优选的,所述卤化盐选自氯化铜、氯化铁、氯化钠、氯化铵、氯化钾、氯化钙、氟化铜、氟化铁、氟化钠、氟化铵中的一种或多种的混合。
50.在一些优选的实施方式中,当组分e为无机酸时,所述无机酸优选为除组分b所述无机酸外的其他无机酸,进一步优选为卤酸,所述卤酸选自盐酸、氢溴酸、氢碘酸、氢氟酸中的一种或多种的混合;进一步优选的,所述卤酸为盐酸和/或氢氟酸;更进一步的,所述卤酸为盐酸。
51.在一些优选的实施方式中,所述无机盐在蚀刻组合物中的重量占比为0.1~100ppm,所述组分e为卤酸时,其在蚀刻组合物中的重量占比为0.01~5ppm。发明人在研究过程中发现,组分e可有效改善铜的底切问题,在100ppm以下,底切量随着组分e的浓度增加而提升。
52.在一些优选的实施方式中,所述组分e为至少一种卤化盐和至少一种卤酸的混合,其中所述卤化盐选自氯化铜、氯化铁、氯化钠、氯化铵、氯化钾、氯化钙、氟化铜、氟化铁、氟化钠、氟化铵中的一种或多种的混合,所述卤酸为盐酸和/或氢氟酸。
53.在一些优选的实施方式中,所述组分e在蚀刻组合物中的重量占比为0.1~80ppm,
为卤化盐和卤酸的混合,其中所述卤化盐在蚀刻组合物中的重量占比为0.1~50ppm,所述卤酸在蚀刻组合物中的重量占比为0.1~30ppm。作为一种示例,所述卤化盐在蚀刻组合物中的重量占比可以为0.1ppm、0.3ppm、0.5ppm、0.8ppm、1ppm、1.2ppm、1.5ppm、2ppm、2.5ppm、3ppm、3.5ppm、4ppm、4.5ppm、5ppm、6ppm、7ppm、8ppm、9ppm、10ppm、15ppm、20ppm、25ppm、30ppm、35ppm、40ppm、50ppm等;作为一种示例,所述卤酸在蚀刻组合物中的重量占比可以为0.1ppm、0.3ppm、0.5ppm、0.8ppm、1ppm、1.2ppm、1.5ppm、2ppm、2.5ppm、3ppm、3.5ppm、4ppm、4.5ppm、5ppm、6ppm、7ppm、8ppm、9ppm、10ppm、15ppm、20ppm、25ppm、30ppm等。
54.本发明中组分a:氧化物和组分b:无机酸是控制金属蚀刻速率的主要成分,其中两者的重量比在1:2~2:1时利用率最高,否则其中量较大的物质将会过剩,虽然无明显负面作用,但可视为无效添加,造成成本负担。优选的浓度是根据凸点制作工艺时间来定义的,金属蚀刻速率过高或者过低都将对工艺控制造成困难。这里所述的金属蚀刻速率,经验上在为最优。组分c:有机酸的加入能够保证蚀刻的均一性、安全性,解决铜残留的问题,而组分d:螯合剂能够调节体系中的离子浓度,降低凸点和种子层的侧向腐蚀量。发明人在实践中还意料不到地发现,当组分e中同时含有卤化盐及卤酸时,所述蚀刻组合物不仅能够有效改善底切问题,还可以有效改善蚀刻后金属的形貌,有效改善金属的蚀刻均一性,并且有效改善蚀刻组合物的稳定性。
55.本发明中蚀刻组合物的制备方法可为本领域技术人员熟知的任何一种,例如物理共混。
56.本发明还提供了上述蚀刻组合物的应用,其用于制造显示器件;进一步的,所述蚀刻组合物用于制作芯片上的凸点。
57.本发明所述芯片包含凸点及凸点下方的种子层;所述凸点包含锡或锡合金构成的上层、镍或镍铜合金构成的下层。本技术中所述锡合金的种类不作特殊限定,通常是指锡与铜、银、铅等金属构成的合金。在一些实施方式中,所述凸点和种子层之间还包含电镀层。
58.如图1所示,为芯片凸点的示意图,其中芯片包含凸点及凸点下方的种子层;所述凸点包含锡银合金构成的上层、镍构成的下层;所述种子层由上至下包含铜种子层、钛种子层;所述凸点和种子层之间包含电镀铜层。
59.这里所述的包含锡或锡合金构成的上层、镍构成的下层或镍和铜构成的下层的结构是先进分装过程惯用的金属凸点制作材料,其优点是性能稳定、成本低廉,其中镍是电镀铜或者铜种子层的连接阻隔层,在导电的同时对铜与锡金属件的相互迁移起到阻隔作用,防止影响凸点的可靠性。在不同种类的芯片上根据设计需要可考虑电镀铜的必要性。锡合金与锡是在芯片进一步封装时的互联材料,根据设计的电性能需求进行选择。
60.实施例
61.以下通过实施例对本发明技术方案进行详细说明,但是本发明的保护范围不局限于所述实施例。如无特殊说明,本发明中的原料均为市售。
62.本发明所述蚀刻组合物的性能参数测试指标:
63.1.侧蚀刻量cd loss,如图1~2所示,将电镀铜在铜蚀刻前后水平方向的收缩量称为侧蚀刻量(cd loss),单位μm,腐蚀后电镀铜与铜种子层需尽可能与ni或sn/ag层平齐,没有收缩,因此低cd为性能优值,一般应用要求小于1μm。
64.2.底切量undercut,如图1~2所示,在凸点的单侧,将蚀刻后铜种子层相对电镀铜
或者镍层(在没有电镀层的情况下)在水平方向的收缩量称为底切量(undercut),单位μm,腐蚀后电镀铜与铜种子层需尽可能与ni或sn/ag层平齐,没有收缩,因此低undercut为性能优值,一般应用要求小于1μm。
65.3.均匀度,单位为%,在晶圆上采集一定数量的点(本发明使用8寸晶圆,均匀采集24点的方法),进行铜蚀刻厚度x的测定。均匀度=(x
max-x
min
)/(2x
avg
),其中x
max
、x
min
、x
avg
分别代表蚀刻厚度的最大值、最小值与平均值,小均匀度为性能优值,一般应用要求小于5%。
66.4.金属腐蚀速率,以锡或锡合金、镍、铝损伤速率为依据,单位小腐蚀速率为性能优值,一般应用要求镍损伤小于锡或锡合金损伤小于铝损伤小于
67.实施例1~12、比较例1~3均提供了一种蚀刻组合物,各例中的成分如表1所示。所述蚀刻组合物的制备方法为物理共混。
68.表1
[0069][0070][0071]
性能测试结果
[0072]
对实施例1~12、比较例1~3得到的蚀刻组合物进行性能测试,测试内容包括侧蚀刻量cd loss、底切量undercut、均匀度、金属腐蚀速率,测试结果见表2。
[0073]
为保证实施方案与对比方案的平行实施,实验过程使用如图1所示结构的晶圆(实验晶圆cu种子层厚度为)进行药水的浸泡实验。实验温度恒定控制在25℃。
[0074]
此外,在保证实验同一种实验方法的前提下,需要指出cd和undercut的数值的影响因素是配方成分与过刻量,此处按照配方在使用时的惯例,过刻量均为100%,作为实验的背景条件。本技术中所述过刻量为实验的背景条件,单位%,过刻量=(t-t0)/t0,其中铜面完全腐蚀干净的时间为t0,实际腐蚀的时间为t。
[0075][0076][0077]
通过对比比较例和实施例的数据可以看出,本发明所述的蚀刻组合物在侧蚀量、底切量以及均匀度上均有大幅改进,同时还具有低的金属腐蚀速率,应用于基板蚀刻时,对基板基本无损伤大大提高了芯片的使用可靠性。
[0078]
前述的实例仅是说明性的,用于解释本发明所述方法的一些特征。所附的权利要求旨在要求可以设想的尽可能广的范围,且本文所呈现的实施例仅是根据所有可能的实施例的组合的选择的实施方式的说明。因此,申请人的用意是所附的权利要求不被说明本发明的特征的示例的选择限制。在权利要求中所用的一些数值范围也包括了在其之内的子范围,这些范围中的变化也应在可能的情况下解释为被所附的权利要求覆盖。