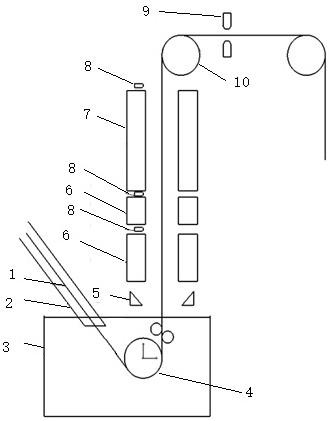
[0001]
本发明涉及一种生产高表面质量锌铝镁镀层钢的系统和方法,属于带钢涂镀技术领域。
背景技术:[0002]
锌铝镁镀层钢因较好的耐腐蚀性能而被越来越广泛的使用。锌铝镁镀层钢由钢基体及附着其上的镀层组成,该镀层组织的典型结构为纯锌相、mg-zn二元共晶相、zn-al-mg三元共晶三种相组成。镀层组织的变化会造成产品表面质量的变化。比如,镀层表面会出现黑点、流纹、结晶不良等缺陷。因此,精确控制镀层组织,是获得高表面质量锌铝镁镀层产品的关键。
[0003]
为了获得准确的目标镀层组织,需要对带钢表面镀层组织的凝固结晶过程进行精确控制。而镀层凝固结晶过程受到产线速度、锌液温度、带钢温度、带钢厚度、锌层重量、气刀压力、气刀间距、镀后风机结构、功率等众多参数的影响。这些参数作用相互耦合制约,导致镀层凝固过程控制十分复杂,目前大多数企业是依靠人工经验根据带钢表面质量对镀后冷却过程进行手动控制,效率低且表面控制水平差。从而导致锌铝镁产品开发一般需要两到三年时间的工艺摸索,才能获得稳定且良好的表面质量。
技术实现要素:[0004]
本发明目的是提供一种生产高表面质量锌铝镁镀层钢的系统和方法,通过视觉识别技术,实现对锌铝镁产品主要表面缺陷种类和严重等级的自动识别,并通过神经网络自学习控制系统对镀后各组风箱冷却曲线精确控制,实现了镀层组织凝固过程与镀后冷却过程精确闭环控制,解决了人工调整步骤繁琐复杂、高度依赖经验,调整不及时等问题,大大解放了人工劳动力,提高了锌铝镁产品表面质量控制水平,降低了产品缺陷发生率;同时,结合卷积神经算法,极大的提高了带钢表面缺陷识别的准确率;同时设计的人机交互系统,可以实现全自动/半自动之间切换,系统自由度高,兼容性强,鲁棒性高,有效地解决了背景技术中存在的上述问题。
[0005]
本发明的技术方案是:一种生产高表面质量锌铝镁镀层钢的系统,包含带钢、炉鼻子、锌锅、下传送辊、气刀、镀后冷却系统、塔顶辊、视觉系统和冷却控制系统,所述镀后冷却系统包含移动风箱组和固定风箱组,从下至上设置;视觉系统包括图像采集单元、图像处理与识别服务器和图像存储系统;冷却控制系统包括服务器和人机交互界面,二者互相连接;带钢通过炉鼻子进入锌锅;气刀和镀后冷却系统从下至上设置在锌锅与塔顶辊之间,分布在带钢的两侧;视觉系统设置在穿过塔顶辊后的带钢两侧;冷却控制系统的输入端与视觉系统连接,输出端与镀后冷却系统连接。
[0006]
所述移动风箱组和固定风箱组后安装有带钢温度检测装置;移动风箱组包括两段式冷却风箱,风箱采用变频风机供风;固定风箱组包括四段风箱组,风箱采用变频风机或定频风机中的一种供风。
[0007]
所述移动风箱组和固定风箱组的出口安装有空气颗粒物探测装置。
[0008]
所述视觉系统中图像采集单元的最小分辨率为0.2
×
0.2mm。
[0009]
所述锌锅内溶液温度设定值为目标成分熔点+40-60℃。
[0010]
所述气刀的喷吹介质为氮气,喷吹压力100-500mbar。
[0011]
所述炉鼻子设有排渣结构,排渣量≥0.15m3/h;;一种生产高表面质量锌铝镁镀层钢的方法,包含以下步骤:a. 采集机组数据与图像:采集机组信息process_paras以及当前参数下图像采集单元采集的带钢表面图像origin_picture;b. 图像标签化:对步骤a中采集的图像origin_picture进行人工标签化,即由人工判断出缺陷种类和等级;c.图像识别模型训练;将步骤b中得到的标签化的图像,输入到图像处理与识别服务器,对图像缺陷识别模型进行训练,最终缺陷识别模型准确率大于95%;d. 冷却模型训练:建立基于深度神经网络的冷却模型cooling_model,使用数据库中cooling_model_db的数据进行训练,预测结果为各组冷却风机功率序列或风门开度序列,冷却模型准确率大于95%;e. 实时图像采集与识别:将实时采集到的带钢表面图像输入图像处理与识别服务器中,得到实时的带钢表面预设缺陷的等级标签;f. 指令下达:当步骤d中实时采集图像的预设缺陷等级标签超出人机交互界面中设定的上限阈值时,则将人机交互界面中预设的目标缺陷等级以及当前机组信息提交给冷却模型cooling_model,冷却模型cooling_model计算出镀后冷却系统各组冷却风箱功率序列或风门开度序列,并向镀后冷却系统的控制箱发送动作指令;g. 冷却系统执行:镀后冷却系统的各组风箱风机控制箱接收到上位机下发的新功率或风门开度指令后,调整到新的功率或风门开度进行冷却。
[0012]
所述锌铝镁镀层钢包括钢基体和镀层,镀层化学成分包括zn、al和mg,以及其他微量元素,al含量为1.0-60.0%,mg含量为0.5-3.5%,以及其他微量元素合小于1%,剩余为zn。
[0013]
所述步骤a中,采集机组信息process_paras,包括气刀高度、气刀间距、锌层重量、生产线速度、带钢入锌锅温度、锌锅溶液温度、各冷却风箱出口温度、各组风箱风机功率或风门开度和各组风箱颗粒物浓度pm10检测仪数据。
[0014]
所述步骤b中,缺陷标签按照统一格式进行编码,包含了“缺陷类型+缺陷等级”信息;其中缺陷类型格式和顺序固定,缺陷等级分为5级,其中0级代表最好,5级代表最差。
[0015]
所述步骤c中,包括必要的图像预处理步骤,视觉识别模型是基于卷积神经网络模型实现的。
[0016]
所述步骤d中,冷却模型基于深度神经网络的方法实现,具体为神经网络计算模型中,输入特征为数据库cooling_model_db中的气刀高度、气刀间距、锌层重量、生产线速度、带钢入锌锅温度、锌锅溶液温度、各组风箱出口温度和各组风箱颗粒物浓度pm10;输出特征为:沿气刀运行方向由下而上各组风箱风机功率或风门开度序列;神经网络模型训练参数设置如下:第一隐含层网络神经元个数64个,激活函数为relu,第二隐含层神经元个数64个,激活函数为relu,模型损失函数使用均方误差,迭代周期500次,训练优化器为加速小批量梯度下降法。
[0017]
本发明的有益效果是:通过视觉识别技术,实现对锌铝镁产品主要表面缺陷种类和严重等级的自动识别,并通过神经网络自学习控制系统对镀后各组风箱冷却曲线精确控制,实现了镀层组织凝固过程与镀后冷却过程精确闭环控制,解决了人工调整步骤繁琐复杂、高度依赖经验,调整不及时等问题,大大解放了人工劳动力,提高了锌铝镁产品表面质量控制水平,降低了产品缺陷发生率;同时,结合卷积神经算法,极大的提高了带钢表面缺陷识别的准确率;同时设计的人机交互系统,可以实现全自动/半自动之间切换,系统自由度高,兼容性强,鲁棒性高。
附图说明
[0018]
图1为本发明的系统结构示意图;图2为本发明使用图像采集单元对带钢表面进行图像采集得到的原始图像;图中:带钢1、炉鼻子2、锌锅3、下传送辊4、气刀5、移动风箱组6、固定风箱组7、带钢温度检测装置8、图像采集单元9、塔顶辊10。
具体实施方式
[0019]
为了使发明实施案例的目的、技术方案和优点更加清楚,下面将结合实施案例中的附图,对本发明实施案例中的技术方案进行清晰的、完整的描述,显然,所表述的实施案例是本发明一小部分实施案例,而不是全部的实施案例,基于本发明中的实施案例,本领域普通技术人员在没有做出创造性劳动前提下所获得的所有其他实施案例,都属于本发明保护范围。
[0020]
一种生产高表面质量锌铝镁镀层钢的系统,包含带钢1、炉鼻子2、锌锅3、下传送辊4、气刀5、镀后冷却系统、塔顶辊10、视觉系统和冷却控制系统,所述镀后冷却系统包含移动风箱组6和固定风箱组7,从下至上设置;视觉系统包括图像采集单元9、图像处理与识别服务器和图像存储系统;冷却控制系统包括服务器和人机交互界面,二者互相连接;带钢1通过炉鼻子2进入锌锅3内,下传送辊4设置在锌锅3内部,塔顶辊10设置在锌锅3上方,带钢1绕过下传送辊4与塔顶辊10;气刀5和镀后冷却系统从下至上设置在锌锅3与塔顶辊10之间,分布在带钢1的两侧;视觉系统设置在穿过塔顶辊10后的带钢1两侧;冷却控制系统的输入端与视觉系统连接,输出端与镀后冷却系统连接。
[0021]
所述移动风箱组6和固定风箱组7后安装有带钢温度检测装置8;移动风箱组6包括两段式冷却风箱,风箱采用变频风机供风;固定风箱组7包括四段风箱组,风箱采用变频风机或定频风机中的一种供风。
[0022]
所述移动风箱组6和固定风箱组7的出口安装有空气颗粒物探测装置。
[0023]
所述视觉系统中图像采集单元9的最小分辨率为0.2
×
0.2mm。
[0024]
所述锌锅3内溶液温度设定值为目标成分熔点+40-60℃。
[0025]
所述气刀5的喷吹介质为氮气,喷吹压力100-500mbar。
[0026]
所述炉鼻子2设有排渣结构,排渣量≥0.15m3/h;;一种生产高表面质量锌铝镁镀层钢的方法,包含以下步骤:a. 采集机组数据与图像:采集机组信息process_paras以及当前参数下图像采集单元采集的带钢表面图像origin_picture;
b. 图像标签化:对步骤a中采集的图像origin_picture进行人工标签化,即由人工判断出缺陷种类和等级;c.图像识别模型训练;将步骤b中得到的标签化的图像,输入到图像处理与识别服务器,对图像缺陷识别模型进行训练,最终缺陷识别模型准确率大于95%;d. 冷却模型训练:建立基于深度神经网络的冷却模型cooling_model,使用数据库中cooling_model_db的数据进行训练,预测结果为各组冷却风机功率序列或风门开度序列,冷却模型准确率大于95%;e. 实时图像采集与识别:将实时采集到的带钢表面图像输入图像处理与识别服务器中,得到实时的带钢表面预设缺陷的等级标签;f. 指令下达:当步骤d中实时采集图像的预设缺陷等级标签超出人机交互界面中设定的上限阈值时,则将人机交互界面中预设的目标缺陷等级以及当前机组信息提交给冷却模型cooling_model,冷却模型cooling_model计算出镀后冷却系统各组冷却风箱功率序列或风门开度序列,并向镀后冷却系统的控制箱发送动作指令;g. 冷却系统执行:镀后冷却系统的各组风箱风机控制箱接收到上位机下发的新功率或风门开度指令后,调整到新的功率进行冷却。
[0027]
所述锌铝镁镀层钢包括钢基体和镀层,镀层化学成分包括zn、al和mg,以及其他微量元素,al含量为1.0-60.0%,mg含量为0.5-3.5%,以及其他微量元素合小于1%,剩余为zn。
[0028]
所述步骤a中,采集机组信息process_paras,包括气刀高度、气刀间距、锌层重量、生产线速度、带钢入锌锅温度、锌锅溶液温度、各冷却风箱出口温度、各组风箱风机功率或风门开度和各组风箱颗粒物浓度pm10检测仪数据。
[0029]
所述步骤b中,缺陷标签按照统一格式进行编码,包含了“缺陷类型+缺陷等级”信息;其中缺陷类型格式和顺序固定,缺陷等级分为5级,其中0级代表最好,5级代表最差。
[0030]
所述步骤c中,包括必要的图像预处理步骤,视觉识别模型是基于卷积神经网络模型实现的。
[0031]
所述步骤d中,冷却模型基于深度神经网络的方法实现,具体为神经网络计算模型中,输入特征为数据库cooling_model_db中的气刀高度、气刀间距、锌层重量、生产线速度、带钢入锌锅温度、锌锅溶液温度、各组风箱出口温度和各组风箱颗粒物浓度pm10;输出特征为:沿气刀运行方向由下而上各组风箱风机功率或风门开度序列;神经网络模型训练参数设置如下:第一隐含层网络神经元个数64个,激活函数为relu,第二隐含层神经元个数64个,激活函数为relu,模型损失函数使用均方误差,迭代周期500次,训练优化器为加速小批量梯度下降法。
[0032]
实施例:如图1,一种生产高表面质量锌铝镁镀层钢的系统:包括带钢1,炉鼻子2,锌锅3,气刀5,镀后冷却系统,视觉系统和冷却控制系统,其中:镀后冷却系统包括移动风箱组6和固定风箱组7;视觉系统包括图像采集单元9、图像处理与识别服务器和图像存储系统;控制系统包括服务器,以及与服务器连接的人机交互界面;本实施例中,移动风箱组6和固定风箱组7后安装有带钢温度检测装置8。移动风箱组6包括两段式冷却风箱,风箱采用变频风机供风。固定风箱组7包括四段风箱组,风箱采用定频风机供风。移动风箱和固定风箱组出口安装有空气颗粒物探测装置,能够检测pm10数值。
视觉系统中图像采集单元9最小分辨率为0.2
×
0.2mm。锌锅3内溶液成分为2%al-2%mg,其余为zn,该成分锌铝镁合金熔点385℃,则锌锅温度设定值435℃。气刀5喷吹介质为氮气,喷吹压力100-500mbar。炉鼻子2具备排渣功能,炉鼻子排渣量≥0.15m3/h。塔顶辊10安装有特氟龙材质耐高温包布。
[0033]
一种生产高表面质量锌铝镁镀层钢的系统和方法,利用了上述的系统,其生产过程如下:a. 采集机组数据与图像:采集机组信息process_paras以及当前参数下图像采集系统采集的带钢表面图像origin_picture。其中机组信息process_paras包含气刀高度、气刀间距、锌层重量、生产线速度、带钢入锌锅温度、锌锅溶液温度,各冷却风箱出口温度,各组风箱风机功率或风门开度,各组风箱颗粒物浓度pm10检测仪数据,部分参数数值如表1所示:表 1b. 图像标签化:本实例中,使用图像采集单元对步骤a中机组在表1所示参数下的带钢表面进行图像采集,得到原始图像origin_picture,如图2所示,对该图像进行人工标签化,即由人工判断出缺陷种类和等级。缺陷标签按照统一格式进行编码,包含了“缺陷类型+缺陷等级”信息。其中缺陷类型格式和顺序固定,缺陷等级分为5级,其中0级代表最好,5级代表最差。本实例中缺陷类型排序为:黑点-锌流纹-结晶不良-厚边。根据编码规则,图2中黑点缺陷明显,其他缺陷不明显,则根据编码规则,图2表面缺陷编码为:3-0-0-0,则表示:{
‘
黑点缺陷
’
:3级,
‘
锌流纹缺陷
’
:0级,
‘
结晶不良缺陷
’
:0级,
‘
厚边缺陷
’
:0级}。
[0034]
c.图像识别模型训练;本实例中,按照步骤b的方法得到一定数量的标签化的图像,然后输入到图像处理与识别服务器,对图像缺陷识别模型进行训练,包括必要的图像预处理步骤,视觉识别模型是基于卷积神经网络模型(cnn模型)实现的。图像识别模型准确率要求95%以上。
[0035]
d.冷却模型训练:本实例中,建立基于深度神经网络的冷却模型cooling_model,使用数据库中cooling_model_db的数据进行训练,预测结果为移动风箱冷却风机功率序列+固定风箱风门开度序列。冷却系统预测模型基于深度神经网络的方法实现的,具体为所述神经网络计算模型中,输入特征为数据库cooling_model_db中的气刀高度、气刀间距、锌层重量、生产线速度、带钢入锌锅温度、锌锅溶液温度,各组风箱出口温度、各组风箱颗粒物浓度pm10,图像缺陷标签。输出特征为:沿气刀运行方向由下而上各组风箱风机功率或风门开度序列。神经网络模型训练参数设置如下:第一隐含层网络神经元个数64个,激活函数为relu,第二隐含层神经元个数64个,激活函数为relu。模型损失函数使用mse(均方误差),迭
代周期500次,训练优化器为加速小批量梯度下降法(rmsprop)。本实例中,在表1参数下,镀后每组风箱风机功率或风门开度参数如表2所示。
[0036]
表格2e. 实时图像采集与识别:将实时采集到的带钢表面图像输入步骤c中已训练好的图像处理与识别服务器中,得到实时的带钢表面缺陷标签。
[0037]
f. 指令下达:当步骤e中实时采集图像的预设缺陷等级标签超出人机交互界面系统中设定的上限阈值时,则将人机交互界面中预设的目标缺陷等级标签以及当前机组信息提交给已训练好的冷却模型cooling_model,冷却模型cooling_model计算出镀后各组冷却风箱功率序列或风门开度序列,并向镀后冷却控制系统的控制箱(plc)发送动作指令;g. 冷却系统执行:镀后各组风箱风机控制箱(plc)接收到上位机下发的新功率或风门开度指令后,调整到新的功率进行冷却。