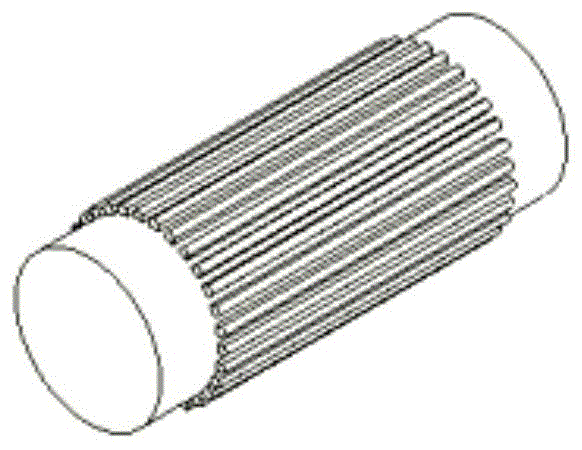
本发明涉及一种增强vw75镁合金热障涂层与基体结合强度的前处理方法,属于金属材料领域。
背景技术:
:镁合金是目前最轻的金属结构材料,具有较高的比强度、比刚度及阻尼减震性能。同时,经过添加稀土的镁合金,也具有较好的耐热特性,因此是目前航空航天、武器装备等领域重要的备选材料。通常情况下,vw75稀土镁合金的稳定使用温度不会超过其固有的时效温度,一般会在200~250℃范围内。但是随着高端装备的发展,特别是现代化武器发展的需求,提高稀土镁合金的耐热特性已经成为目前国内外所重点研究的方向。为了进一步提高镁合金的耐热温度,在既有镁合金表面增加可靠的耐热涂层,是一类重要的有效手段。目前根据涂层的种类及制备方法,可以将镁合金的涂层分为以下几类:典型的包括微弧氧化陶瓷层、化学转化涂层以及等离子喷涂耐热涂层。相比于微弧氧化陶瓷层以及化学转化涂层而言,等离子喷涂涂层在厚度以及耐热温度方面具有更高的优势,主要原因在于等离子喷涂涂层由粘接层和陶瓷层共同组成,其组份本身就具有较好的耐热特性。因此,等离子喷涂是最具优势的热障涂层。由等离子涂层的形成方式可知,粘接层与基体的结合度是影响热障涂层有效性的关键所在。因此,如何能够提高热障涂层与基体的结合强度就转化为如何提高涂层中粘接层与基体的结合强度这个关键问题。通常情况下,基体的表面处理是经过吹沙处理,从本质上来说对于一些常规材料是可行的,但是对于镁合金,特别是稀土镁合金而言,塑性相对较差,简单喷砂后基体极易剥落。技术实现要素:基于以上现有技术,本发明的目的在于提供一种增强vw75镁合金热障涂层与基体结合强度的前处理方法,希望通过特殊方法构造vw75稀土镁合金基体特殊的表面形态,进而提高热障涂层与机体的结合强度,实现热障涂层寿命的延长。为实现上述目的,本发明采用以下技术方案:一种增强vw75镁合金热障涂层与基体结合强度的前处理方法,该方法包括以下步骤:(1)对vw75镁合金板材需要进行等离子喷涂的一侧施加压应力,所采用的方式为以下方式中的一种:1)采用表面辊轧的方式,轧辊表面具有齿或凸点,相邻两齿或凸点的间距为1~3mm,齿或凸点的高度为2~3mm;单道次轧制之后采用交叉轧制1次,压下量在0.3%~0.5%;2)采用喷丸的方式,对vw75镁合金表面进行处理,所用的喷丸粒径在1-8mm范围内,喷丸处理后表面粗糙度达到3.2~3.5;3)对vw75镁合金淬火处理,对板材进行高温加热后,对板材表面进行喷淋处理,喷淋处理过程中,选择热介质与冷介质交替喷淋到板材表面,在板材表面构成交替的应力差,上述介质均采用相同的流速为0.5~1m/s;(2)对已经施加压应力的vw75镁合金表面采用具有金属钨制成的尖端的装置从心部向边部沿螺旋状进行滑动形成螺旋线沟槽,所述尖端直径为1mm,形成的螺旋线沟槽深度在0.1~0.5mm之间,螺旋线沟槽间距为3~5mm,最终覆盖整个表面。其中,所述齿的顶端为半弧形状。其中,在所述步骤(2)中,喷丸中小于3mm颗粒所占比例为30%,3~5mm的颗粒占比50%,5~8mm颗粒占比15%,8mm尺寸的颗粒为正六面体,占比5%。其中,所述冷介质为液氮或冰水,所述热介质为温水或热水。本发明的优点在于:本发明利用特定方式对vw75镁合金表面进行处理,制备特定形状的沟槽,进而增加了粘接层与基体的结合效果,同时,对进一步降低vw75镁合金在等离子喷涂过程中表面过时效造成性能下降的影响,通过强化合金的表面,对合金的耐蚀性能也将有一定的提高效果。另外,在压应力的作用下,样品表面即使受到高温影响,也会抵消部分因体积膨胀而引起的过大拉应力,对进一步提高热障涂层的尺寸稳定性也有非常积极的作用。附图说明图1为实施例1中所用轧辊的结构示意图。图2为实施例2中所用轧辊的结构示意图。图3为实施例3中喷淋淬火处理所用装置的结构示意图。图4为实施例中形成螺旋线沟槽时装置的结构示意图。具体实施方式下面通过具体实施例对本发明做进一步说明,但并不意味着对本发明保护范围的限制。作为本发明的具体实施方式,所选择的vw75镁合金板材的厚度在15~50mm之间。首先,通过特殊方法在需要进行等离子喷涂的一侧施加压应力;如果是正反两面同时进行等离子喷涂,则需要在基体表面的正反两面施加压应力。在本发明中,在vw75镁合金表面施加压应力的具体方法包括:1)采用表面辊轧的方式。轧辊的形貌如图1、2所示,轧辊表面具有齿痕或凸点。若采用带齿痕的轧辊,如图1所示,轧辊表面两个齿痕的间距在1~3mm之间,齿顶端为半弧形,齿高为2~3mm;若采用带凸点的轧辊,如图2所示,凸点之间距离为2~3mm。单道次轧制之后采用交叉轧制1次,压下量为0.3%~0.5%。2)采用喷丸的方式,对vw75镁合金表面进行处理。所用的喷丸粒径在1-8mm范围内,其中小于3mm颗粒所占比例为30%,3~5mm的颗粒占比50%,5~8mm颗粒占比15%,8mm尺寸的颗粒为正六面体,占比5%。喷丸处理过程不以表面光亮为最终选择目标,表面粗糙度达到3.2~3.5即可。3)对vw75镁合金淬火处理。对板材进行高温加热然后通过采用如图3所示的装置,对材料表面进行喷淋处理。喷淋处理过程中,需要分别加入液氮以及热水,或者进行温水及冰水的处理,在材料表面构成交替的应力差,上述介质均采用相同的流速,为0.5~1m/s。对已经施加压应力的vw75镁合金表面采用如图4所示的装置进行圆周滑动,该装置的尖端直径约为1mm,采用金属钨作为头部,所形成的螺旋线沟槽的深度在0.1~0.5mm之间,螺旋线沟槽的间距为3~5mm,且可以从心部向边部沿螺旋状进行滑动,最终覆盖整个表面。实施例1选择厚度为20mm的vw75镁合金板材,利用表面为条状齿轮的轧辊(如图1)进行轧制,轧辊表面两个齿痕的间距为3mm,齿顶端为半弧形齿,齿高为3mm。单道次轧制之后采用交叉轧制1次,压下量为0.3%。对交叉轧制后的vw75镁合金表面采用如图4所示的装置进行圆周滑动。该装置的尖端直径为1mm,采用金属钨作为头部,螺旋线沟槽深度为0.1mm,螺旋线沟槽间距为3mm,从心部向边部沿螺旋状进行滑动,最终覆盖整个表面。实施例2选择厚度为30mm的vw75镁合金板材,利用表面为点状凸起的轧辊(如图2)进行轧制,轧辊表面任意两个凸点的间距为2mm,凸点顶端为半球形,凸点高为2mm,单道次轧制之后采用交叉轧制1次,压下量为0.5%。对轧制后的vw75镁合金表面采用如图4所示的装置进行圆周滑动。该装置的尖端直径为1mm,采用金属钨作为头部,螺旋线沟槽深度为0.3mm,螺旋线沟槽间距为5mm,从心部向边部沿螺旋状进行滑动,最终覆盖整个表面。实施例3选择厚度为30mm的vw75镁合金板材,利用喷丸处理的方式进行表面加工,所用的喷丸粒径在1-8mm范围内,其中小于3mm颗粒所占比例为30%,5mm的颗粒占比50%,6mm颗粒占比10%,8mm尺寸的颗粒为正六面体,占比5%。喷丸处理过程不以表面光亮为最终选择目标,表面粗糙度达到3.2即可。对喷丸处理后的vw75镁合金表面采用如图4所示的装置进行圆周滑动。该装置的尖端直径为1mm,采用金属钨作为头部,螺旋线沟槽深度为0.4mm,螺旋线沟槽间距为4mm,从心部向边部沿螺旋状进行滑动,最终覆盖整个表面。实施例4选择厚度为50mm的vw75镁合金板材进行高温加热然后通过采用如图3所示的装置,对材料表面进行喷淋淬火处理。喷淋处理过程中,需要分别在1号阀门通入液氮,2号阀门通入热水,3号阀门通入液氮,上述介质均采用相同的流速,为0.8m/s,在材料表面构成交替的应力差以产生表面压应力。对淬火处理后的vw75镁合金表面采用如图4所示的装置进行圆周滑动。该装置的尖端直径为1mm,采用金属钨作为头部,螺旋线沟槽深度为0.45mm,螺旋线沟槽间距为3mm,从心部向边部沿螺旋状进行滑动,最终覆盖整个表面。实施效果:结合强度测试方法:涂层的结合强度按照gb/t8642-2002,采用轴向拉伸法对热障涂层进行结合强度测试。结合强度试样尺寸为采用美国3m公司生产的fm1000薄膜胶作为粘结剂。拉伸试验机型号为cmt5205。将制备好的拉伸对偶件装卡在万能材料试验机上,采用1mm/min的速度加载,采集断裂时的最大结合强度,取平均值进行分析。将改性后样品的结合强度减去原始样品的结合强度,所得差值再除以原始样品的涂层结合强度,即为提升值。热振测试方法:实验在箱式高温电炉中进行,设备型号为rjx-4-13。并通过程序设定控制加热温度。加热温度300℃,保温时间5分钟(到温计时),随后冷风吹至室温,一次加热、保温和冷却记为一次,并循环进行,将施加本发明的方法后样品的热振次数减去原始方式所获样品的热振次数,所得到的差值再除以原始样品热振次数,即为提升值。原始方式是指按照普通喷砂工艺完成的表面前处理。结合强度较原始提升%热振次数提升%实施例123%18%实施例222%16%实施例322.5%17.5%实施例418%18.5%当前第1页12