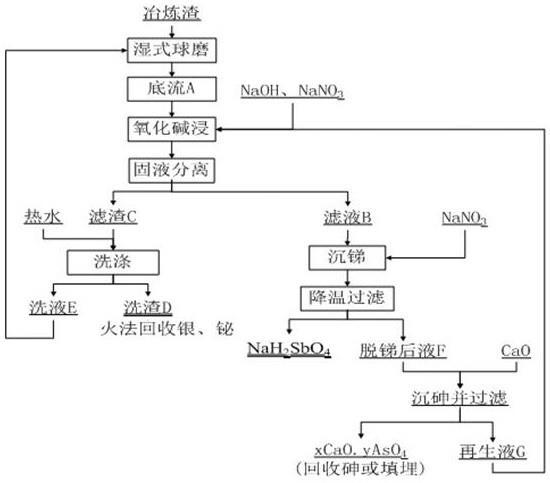
[0001]
本发明属于有色金属冶炼综合回收技术领域,涉及一种脱除有害元素的方法,具体涉及一种脱除高含量铋银冶炼渣中有害元素砷、锑的方法。
背景技术:[0002]
铜冶炼生产中会产生含铅60%、铋20%、银3~5%左右的铅铋合金,常采用阳极炉熔炼成铅阳极,在硅氟酸-硅氟酸铅介质中进行电解,得到99.5%左右的阴极铅和高含量铋银冶炼渣。
[0003]
高含量铋银冶炼渣通常由50~60%铋(bi)、8~15%银(ag)、3~8%铅(pb)、2~4%砷(as)、8~14%锑(sb)和少量的铜(cu)等组成,是一种有价金属含量高、附加高而有害元素砷、锑含量大的危险固体废物。
[0004]
随着有色金属富矿的日益匮乏,从类似高含量铋银冶炼渣等二次资源中综合回收各种有价金属元素越来越受到重视。但是由于其中含有很多的危险元素砷、锑,给回收工作带来很大困难,现有技术中并没有很安全、成熟的回收工艺,容易在某个环节出现严重安全事故。
[0005]
目前对这种含铋高的物料,主要采用以下三种方式进行回收处理。
[0006]
1、火法处理:对于砷、锑等危险元素含量低的物料,通过火法熔炼加硫除铜—除砷、锑—加锌除银—氯化除铅、锌—碱性精炼—铋锭加以回收;火法处理工艺对渣中砷、锑含量要求高,一般要求锑含量不高于5%。
[0007]
2、硝酸湿法处理:含铋物料经过球磨,采用高浓度硝酸溶液进行浸出,浸出液加硫酸进行沉铅反应,过滤完硫酸铅渣后向滤液中加饱和食盐水沉银,沉银后液用纯碱溶液调节ph值到3-4,得到碱式硝酸铋白色沉淀,过滤所得铋渣采用火法还原处理得到金属铋;银渣用氨水络合为银氨溶液,用水合肼还原得到银粉;硝酸处理的生产过程中,难以保证不生产剧毒化学气体ash3,存在很高的人身安全隐患。
[0008]
3、氯盐法:利用物料自身容易被氧化的特点,先将其中的砷、锑、铋等杂质通过自然堆放氧化或烘烤氧化转变成相应的氧化物,然后在含有氯离(cl-)的酸性溶液如h2so4+nacl或hcl+nacl体系中浸出。通过控制溶液中cl-浓度,在阻止ag溶解的情况下提高锑、铅、铜、铋等金属的浸出率,浸出液采取逐步水解工艺回收其中的锑、铋、铜等金属,浸出渣经氧化+氨浸+肼或甲醛还原回收银;氯盐法处理存在设备腐蚀快、生产环境糟、水解作业条件苛刻等弊端,难以大范围推广应用。
技术实现要素:[0009]
本发明的目的为提供一种脱除高含量铋银冶炼渣中有害元素砷、锑的方法,包括以下步骤:步骤(1)球磨,洗涤液按溶液(l):渣(
㎏
)=(3-4):1的比例对高含量铋银冶炼渣进行冲矿和湿式球磨,磨碎时间30min,磨矿粒度100%达到-60目;静置后的上清液用清液泵泵回高
位槽作为磨碎冲水,底流a作为步骤(2)浸出的原料;步骤(2)浸出,用矿浆泵将步骤(1)的底流a泵入密闭浸出槽中,加入再生溶液g并控制浸出液固比为溶液量(l):渣量(
㎏
)=(6-8):1,加入适量的反应试剂(反应试剂为先加入试剂级固体氢氧化钠至溶液浓度150~170g/l,搅拌均匀后再加入试剂级固体硝酸钠至溶液浓度30~40g/l);升温并维持反应温度至95℃以上,搅拌反应180-240分钟,过滤,得到碱性浸出液b和浸出渣c;步骤(3)浸出渣洗涤,将步骤(2)所得浸出渣c用水进行常温浆化两段逆流洗涤,洗涤液固比为水量(l):浸出渣量(
㎏
)=(1.5-2):1,经过液固分离后,得到洗涤渣d和洗涤液e;步骤(4)浸出液脱锑、脱砷,将步骤(2)所得浸出液b泵入间接加热反应釜,加热到80℃
±
10℃,加入硝酸钠使其浓度初始浓度3-5g/l,反应30~40min,将溶液中的nasbo2氧化;氧化反应结束后,通入冷却水,将溶液温度降温至25
±
5℃,使溶液中的锑以不定型nah2sbo4沉淀析出,液固分离后得到脱锑后液f;步骤(5)脱锑后液脱砷及回用,在反应槽中向步骤(4)所得的脱锑后液f加入氧化钙,加入量为溶液中cao浓度3~3.5g/l,搅拌温度50℃
±
10℃,反应时间60min,砷以砷酸钙形式沉淀。
[0010]
进一步地,步骤(2)中反应试剂为氢氧化钠和硝酸钠,其中氢氧化钠初始浓度150-170g/l,硝酸钠初始浓度30-40g/l。
[0011]
进一步地,步骤(3)中得到的洗涤液e进入步骤(1)中作为洗涤液。
[0012]
进一步地,步骤(5)中砷沉淀后液固分离后得到再生溶液g,回用于步骤(2)高含量铋银冶炼渣的碱性浸出。
[0013]
高含量铋银冶炼渣中有害元素砷、锑均主要以三价氧化物形态存在,少量以单质态和cu3as金属间化合物形态形态存在,其中的砷在naoh-nano3碱性氧化体系中以na3aso4的产物形式溶解进入浸出液;在控制nano3使用量的氧化体系下,锑可以可溶性产物偏亚锑酸盐(nasbo2)形态选择性溶出,从而实现砷、锑危害元素的脱除,而铋的反应产物(bi2o3)和银则不溶于上述溶液,实现了主体金属与危害元素的有效分离;而在含砷、锑的浸出液处理回用时,主要利用偏亚锑酸盐(nasbo2)被nano3氧化成锑酸盐(na3sbo4),锑酸盐在低温条件下转变成溶解度很小的无定型锑酸二氢盐(nah2sbo4)析出,释放出氢氧化钠碱试剂,同时溶液中金属离子浓度降低,浸出试剂得到一定程度的再生。
[0014]
步骤(2)中得到洗涤渣c为脱除砷、锑等危害元素的合格中间产品,采用火法还原熔炼和阳极铸锭,用电解工艺产出符合国标质量的电解铋,阳极泥用来回收贵金属银。
[0015]
步骤(4)中不定型nah2sbo4沉淀可以回用于铜冶炼生产企业铜电解液中砷、锑、铋等有害杂质的脱除剂。
[0016]
步骤(5)中,液固分离得到的砷酸钙沉淀,可以作为提供给有资质生产单质砷的生产企业,也可以委托危废处理厂进行填埋处理。
[0017]
本发明主要反应方程式如下:球磨及浸出过程:
浸出除砷、锑及再生过程:与现有技术相比,本发明的有益效果如下:(1)本发明有效保留了高含量铋银冶炼渣中的有价元素铋和银,有害元素砷、锑以副产品形式得到回收,实现了变废为利的目标;(2)本发明的生产过程中不产生危险毒害气体ash3,处理介质为碱性介质,设备腐蚀小,生产环境友好;(3)经过碱性氧化浸出,产出原渣重量约70%的浸出渣,渣中主要成分仍为铋和银,但其品位均有不同度的提高,其中铋提高近20个百分点,为76%左右,银提高了近5个百分点,为18%左右;浸出渣经过逆流洗涤后,砷、锑等危害元素含量很低,不对铋、银的回收产生危害。洗涤渣采用火法还原熔炼和阳极铸锭,用电解工艺可产出符合国标质量的电解铋,铋阳极泥用来回收贵金属银;(4)浸出液中的碱试剂可以实现再生,可以实现液体的闭路运行和循环利用,无废水排放。
附图说明
[0018]
图1为本发明的工艺流程图。
具体实施方式
[0019]
实施例1一种脱除高含量铋银冶炼渣中有害元素砷、锑的方法,包括以下步骤:步骤(1)球磨,洗涤液按溶液(l):渣(
㎏
)=4:1的比例对高含量铋银冶炼渣进行冲矿和湿式球磨,磨碎时间30min,磨矿粒度100%达到-60目;静置后的上清液用清液泵泵回高位槽作为磨碎冲水,底流a作为步骤(2)浸出的原料;步骤(2)浸出,用矿浆泵将步骤(1)的底流a泵入密闭浸出槽中,加入再生溶液g并控制浸出液固比为溶液量(l):渣量(
㎏
)=6:1,先加入试剂级固体氢氧化钠,搅拌均匀后再加入试剂级固体硝酸钠;升温并维持反应温度至95℃以上,搅拌反应180分钟,过滤,得到碱性浸出液b和浸出渣c;步骤(2)中反应试剂为氢氧化钠和硝酸钠,其中氢氧化钠初始浓度160g/l,硝酸钠初始浓度30g/l;步骤(3)浸出渣洗涤,将步骤(2)所得浸出渣c用水进行常温浆化两段逆流洗涤,洗涤液
固比为水量(l):浸出渣量(
㎏
)=2:1,经过液固分离后,得到洗涤渣d和洗涤液e;步骤(3)中得到的洗涤液e进入步骤(1)中作为洗涤液;步骤(4)浸出液脱锑、脱砷,将步骤(2)所得浸出液b泵入间接加热反应釜,加热到80℃,加入硝酸钠使其浓度初始浓度3.5g/l,反应30min,将溶液中的nasbo2氧化;氧化反应结束后,通入冷却水,将溶液温度降温至20℃,使溶液中的锑以不定型nah2sbo4沉淀析出,液固分离后得到脱锑后液f;步骤(5)脱锑后液脱砷及回用,在反应槽中向步骤(4)所得的脱锑后液f加入氧化钙,加入量为溶液中cao浓度3.5g/l,搅拌温度50℃,反应时间60min,砷以砷酸钙形式沉淀;步骤(5)中砷沉淀后液固分离后得到再生溶液g,回用于步骤(2)高含量铋银冶炼渣的碱性浸出。
[0020]
经过分析,浸出液(含浆洗液)中砷浓度为3.02g/l,锑为12.86g/l;浸出渣产率为72.4%,含铋77.91%,银18.68%,砷0.41%,锑0.84%;浸出液(含浆洗液)经过沉锑、钙后,溶液中残钙、锑的浓度分别为83.68mg/l和65.38mg/l;全流程锑、砷脱除率为94.16%和96.29%,铋、银总收率为99.85%和99.93%。
[0021]
实施例2一种脱除高含量铋银冶炼渣中有害元素砷、锑的方法,包括以下步骤:步骤(1)球磨,洗涤液按溶液(l):渣(
㎏
)=3:1的比例对高含量铋银冶炼渣进行冲矿和湿式球磨,磨碎时间30min,磨矿粒度100%达到-60目;静置后的上清液用清液泵泵回高位槽作为磨碎冲水,底流a作为步骤(2)浸出的原料;步骤(2)浸出,用矿浆泵将步骤(1)的底流a泵入密闭浸出槽中,加入再生溶液g并控制浸出液固比为溶液量(l):渣量(
㎏
)=6:1,先加入试剂级固体氢氧化钠,搅拌均匀后再加入试剂级固体硝酸钠;升温并维持反应温度至95℃以上,搅拌反应150分钟,过滤,得到碱性浸出液b和浸出渣c;步骤(2)中反应试剂为氢氧化钠和硝酸钠,其中氢氧化钠初始浓度160g/l,硝酸钠初始浓度40g/l;步骤(3)浸出渣洗涤,将步骤(2)所得浸出渣c用水进行常温浆化两段逆流洗涤,洗涤液固比为水量(l):浸出渣量(
㎏
)=2:1,经过液固分离后,得到洗涤渣d和洗涤液e;步骤(3)中得到的洗涤液e进入步骤(1)中作为洗涤液;步骤(4)浸出液脱锑、脱砷,将步骤(2)所得浸出液b泵入间接加热反应釜,加热到80℃,加入硝酸钠使其浓度初始浓度4g/l,反应30min,将溶液中的nasbo2氧化;氧化反应结束后,通入冷却水,将溶液温度降温至20℃,使溶液中的锑以不定型nah2sbo4沉淀析出,液固分离后得到脱锑后液f;步骤(5)脱锑后液脱砷及回用,在反应槽中向步骤(4)所得的脱锑后液f加入氧化钙,加入量为溶液中cao浓度3.5g/l,搅拌温度50℃,反应时间60min,砷以砷酸钙形式沉淀;步骤(5)中砷沉淀后液固分离后得到再生溶液g,回用于步骤(2)高含量铋银冶炼渣的碱性浸出。
[0022]
经过分析,浸出液(含浆洗液)中砷浓度为3.24g/l,锑为13.15g/l;浸出渣产率为71.7%,含铋77.98%,银18.74%,砷0.40%,锑0.81%;浸出液(含浆洗液)经过沉锑、钙后,溶液中残钙、锑的浓度分别为91.75mg/l和59.42mg/l;全流程锑、砷脱除率为94.36%和96.98%,铋、银总收率为99.87%和99.95%。
[0023]
实施例3一种脱除高含量铋银冶炼渣中有害元素砷、锑的方法,包括以下步骤:
步骤(1)球磨,洗涤液按溶液(l):渣(
㎏
)=4:1的比例对高含量铋银冶炼渣进行冲矿和湿式球磨,磨碎时间30min,磨矿粒度100%达到-60目;静置后的上清液用清液泵泵回高位槽作为磨碎冲水,底流a作为步骤(2)浸出的原料;步骤(2)浸出,用矿浆泵将步骤(1)的底流a泵入密闭浸出槽中,加入再生溶液g并控制浸出液固比为溶液量(l):渣量(
㎏
)=8:1,先加入试剂级固体氢氧化钠,搅拌均匀后再加入试剂级固体硝酸钠;升温并维持反应温度至95℃以上,搅拌反应150分钟,过滤,得到碱性浸出液b和浸出渣c;步骤(2)中反应试剂为氢氧化钠和硝酸钠,其中氢氧化钠初始浓度180g/l,硝酸钠初始浓度40g/l;步骤(3)浸出渣洗涤,将步骤(2)所得浸出渣c用水进行常温浆化两段逆流洗涤,洗涤液固比为水量(l):浸出渣量(
㎏
)=2:1,经过液固分离后,得到洗涤渣d和洗涤液e;步骤(3)中得到的洗涤液e进入步骤(1)中作为洗涤液;步骤(4)浸出液脱锑、脱砷,将步骤(2)所得浸出液b泵入间接加热反应釜,加热到80℃,加入硝酸钠使其浓度初始浓度5g/l,反应30min,将溶液中的nasbo2氧化;氧化反应结束后,通入冷却水,将溶液温度降温至25℃,使溶液中的锑以不定型nah2sbo4沉淀析出,液固分离后得到脱锑后液f;步骤(5)脱锑后液脱砷及回用,在反应槽中向步骤(4)所得的脱锑后液f加入氧化钙,加入量为溶液中cao浓度4g/l,搅拌温度50℃,反应时间60min,砷以砷酸钙形式沉淀;步骤(5)中砷沉淀后液固分离后得到再生溶液g,回用于步骤(2)高含量铋银冶炼渣的碱性浸出。
[0024]
经过分析,浸出液(含浆洗液)中砷浓度为3.18g/l,锑为12.95g/l;浸出渣产率为70.55%,含铋78.36%,银18.92%,砷0.34%,锑0.76%;浸出液(含浆洗液)经过沉锑、钙后,溶液中残钙、锑的浓度分别为83.37mg/l和54.86mg/l;全流程锑、砷脱除率为96.25%和97.32%,铋、银总收率为99.36%和99.96%。
[0025]
实施例4一种脱除高含量铋银冶炼渣中有害元素砷、锑的方法,包括以下步骤:步骤(1)球磨,洗涤液按溶液(l):渣(
㎏
)=3:1的比例对高含量铋银冶炼渣进行冲矿和湿式球磨,磨碎时间30min,磨矿粒度100%达到-60目;静置后的上清液用清液泵泵回高位槽作为磨碎冲水,底流a作为步骤(2)浸出的原料;步骤(2)浸出,用矿浆泵将步骤(1)的底流a泵入密闭浸出槽中,加入再生溶液g并控制浸出液固比为溶液量(l):渣量(
㎏
)=7:1,先加入试剂级固体氢氧化钠,搅拌均匀后再加入试剂级固体硝酸钠;升温并维持反应温度至95℃以上,搅拌反应240分钟,过滤,得到碱性浸出液b和浸出渣c;步骤(2)中反应试剂为氢氧化钠和硝酸钠,其中氢氧化钠初始浓度160g/l,硝酸钠初始浓度35g/l;步骤(3)浸出渣洗涤,将步骤(2)所得浸出渣c用水进行常温浆化两段逆流洗涤,洗涤液固比为水量(l):浸出渣量(
㎏
)=2:1,经过液固分离后,得到洗涤渣d和洗涤液e;步骤(3)中得到的洗涤液e进入步骤(1)中作为洗涤液;步骤(4)浸出液脱锑、脱砷,将步骤(2)所得浸出液b泵入间接加热反应釜,加热到80℃,加入硝酸钠使其浓度初始浓度5g/l,反应40min,将溶液中的nasbo2氧化;氧化反应结束后,通入冷却水,将溶液温度降温至20℃,使溶液中的锑以不定型nah2sbo4沉淀析出,液固分离后得到脱锑后液f;
步骤(5)脱锑后液脱砷及回用,在反应槽中向步骤(4)所得的脱锑后液f加入氧化钙,加入量为溶液中cao浓度4g/l,搅拌温度50℃,反应时间60min,砷以砷酸钙形式沉淀;步骤(5)中砷沉淀后液固分离后得到再生溶液g,回用于步骤(2)高含量铋银冶炼渣的碱性浸出。
[0026]
经过分析,浸出液(含浆洗液)中砷浓度为2.96g/l,锑为10.72g/l;浸出渣产率为75.84%,含铋75.68%,银16.46%,砷0.31%,锑0.97%;浸出液(含浆洗液)经过沉锑、钙后,溶液中残钙、锑的浓度分别为79.63mg/l和42.65mg/l;全流程锑、砷脱除率为89.38%和98.18%,铋、银总收率为99.61%和99.95%。
[0027]
实施例5一种脱除高含量铋银冶炼渣中有害元素砷、锑的方法,包括以下步骤:步骤(1)球磨,洗涤液按溶液(l):渣(
㎏
)=3:1的比例对高含量铋银冶炼渣进行冲矿和湿式球磨,磨碎时间30min,磨矿粒度100%达到-60目;静置后的上清液用清液泵泵回高位槽作为磨碎冲水,底流a作为步骤(2)浸出的原料;步骤(2)浸出,用矿浆泵将步骤(1)的底流a泵入密闭浸出槽中,加入再生溶液g并控制浸出液固比为溶液量(l):渣量(
㎏
)=8:1,先加入试剂级固体氢氧化钠,搅拌均匀后再加入试剂级固体硝酸钠;升温并维持反应温度至95℃以上,搅拌反应240分钟,过滤,得到碱性浸出液b和浸出渣c;步骤(2)中反应试剂为氢氧化钠和硝酸钠,其中氢氧化钠初始浓度160g/l,硝酸钠初始浓度40g/l;步骤(3)浸出渣洗涤,将步骤(2)所得浸出渣c用水进行常温浆化两段逆流洗涤,洗涤液固比为水量(l):浸出渣量(
㎏
)=2:1,经过液固分离后,得到洗涤渣d和洗涤液e;步骤(3)中得到的洗涤液e进入步骤(1)中作为洗涤液;步骤(4)浸出液脱锑、脱砷,将步骤(2)所得浸出液b泵入间接加热反应釜,加热到80℃,加入硝酸钠使其浓度初始浓度5g/l,反应40min,将溶液中的nasbo2氧化;氧化反应结束后,通入冷却水,将溶液温度降温至30℃,使溶液中的锑以不定型nah2sbo4沉淀析出,液固分离后得到脱锑后液f;步骤(5)脱锑后液脱砷及回用,在反应槽中向步骤(4)所得的脱锑后液f加入氧化钙,加入量为溶液中cao浓度4g/l,搅拌温度50℃,反应时间60min,砷以砷酸钙形式沉淀;步骤(5)中砷沉淀后液固分离后得到再生溶液g,回用于步骤(2)高含量铋银冶炼渣的碱性浸出。
[0028]
经过分析,浸出液(含浆洗液)中砷浓度为2.98g/l,锑为11.56g/l;浸出渣产率为72.45%,含铋77.52%,银18.14%,砷0.30%,锑0.68%;浸出液(含浆洗液)经过沉锑、钙后,溶液中残钙、锑的浓度分别为85.28mg/l和52.48mg/l;全流程锑、砷脱除率为96.88%和98.48%,铋、银总收率为99.63%和99.95%。
[0029]
实施例6一种脱除高含量铋银冶炼渣中有害元素砷、锑的方法,包括以下步骤:步骤(1)球磨,洗涤液按溶液(l):渣(
㎏
)=4:1的比例对高含量铋银冶炼渣进行冲矿和湿式球磨,磨碎时间30min,磨矿粒度100%达到-60目;静置后的上清液用清液泵泵回高位槽作为磨碎冲水,底流a作为步骤(2)浸出的原料;步骤(2)浸出,用矿浆泵将步骤(1)的底流a泵入密闭浸出槽中,加入再生溶液g并控制浸出液固比为溶液量(l):渣量(
㎏
)=7:1,先加入试剂级固体氢氧化钠,搅拌均匀后再加入试剂级固体硝酸钠;升温并维持反应温度至95℃以上,搅拌反应210分钟,过滤,得到碱性浸
出液b和浸出渣c;步骤(2)中反应试剂为氢氧化钠和硝酸钠,其中氢氧化钠初始浓度170g/l,硝酸钠初始浓度30g/l;步骤(3)浸出渣洗涤,将步骤(2)所得浸出渣c用水进行常温浆化两段逆流洗涤,洗涤液固比为水量(l):浸出渣量(
㎏
)=2:1,经过液固分离后,得到洗涤渣d和洗涤液e;步骤(3)中得到的洗涤液e进入步骤(1)中作为洗涤液;步骤(4)浸出液脱锑、脱砷,将步骤(2)所得浸出液b泵入间接加热反应釜,加热到80℃,加入硝酸钠使其浓度初始浓度4g/l,反应40min,将溶液中的nasbo2氧化;氧化反应结束后,通入冷却水,将溶液温度降温至20℃,使溶液中的锑以不定型nah2sbo4沉淀析出,液固分离后得到脱锑后液f;步骤(5)脱锑后液脱砷及回用,在反应槽中向步骤(4)所得的脱锑后液f加入氧化钙,加入量为溶液中cao浓度4g/l,搅拌温度50℃,反应时间60min,砷以砷酸钙形式沉淀;步骤(5)中砷沉淀后液固分离后得到再生溶液g,回用于步骤(2)高含量铋银冶炼渣的碱性浸出。
[0030]
经过分析,浸出液(含浆洗液)中砷浓度为2.99g/l,锑为12.36g/l;浸出渣产率为71.54%,含铋78.18%,银18.73%,砷0.39%,锑0.83%;浸出液(含浆洗液)经过沉锑、钙后,溶液中残钙、锑的浓度分别为81.34mg/l和55.26mg/l;全流程锑、砷脱除率为95.41%和96. 84%,铋、银总收率为99.58%和99.96%。
[0031]
实施例1:将高含量铋银冶炼渣磨矿至100%-60目,在液固比溶液(l):渣(
㎏
)=6:1的条件下,加入氢氧化钠至浓度160/l,加入硝酸钠至浓度30/l;升温并维持反应温度至95℃以上,搅拌反应180分钟,液固分离后并按液固比溶液(l):渣(
㎏
)=2:1浆洗浸出渣,浆洗液合并浸出液后化验分析;混合溶液加热到80℃,加入硝酸钠至其浓度为3.5g/l,反应30min;氧化反应结束后,将溶液温度降至20℃,静置60min,固液分离,得到锑渣和除锑后液;除锑后液加入氧化钙至cao浓度3.5g/l,温度50℃,反应时间60min。经过分析,浸出液(含浆洗液)中砷浓度为3.02g/l,锑为12.86g/l;浸出渣产率为72.4%,含铋77.91%,银18.68%,砷0.41%,锑0.84%;浸出液(含浆洗液)经过沉锑、钙后,溶液中残钙、锑的浓度分别为83.68mg/l和65.38mg/l;全流程锑、砷脱除率为94.16%和96.29%,铋、银总收率为99.85%和99.93%。