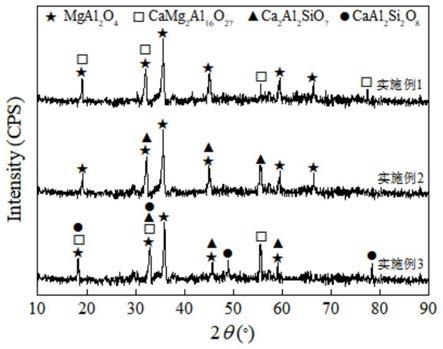
[0001]
本发明属于冶金技术领域,特别涉及一种转炉渣与镍渣和/或铜渣的熔融耦合改质提铁方法。
技术背景
[0002]
随着我国有色冶金工业的快速发展,每年都有大量有色冶金渣产生,其中,镍渣和铜渣中的全铁量约为30-45%,均高于我国铁矿石可采品位,提取并回收镍渣和铜渣中的铁资源有助于拓展我国铁矿资源渠道,促进钢铁与有色冶金行业的协同发展。镍渣中的铁主要以铁橄榄石(2feo
·
sio2)形式存在,铜渣中的含铁相也主要以铁橄榄石和磁铁矿形式存在。由于铁橄榄石属硅酸盐矿物,为si-o构成的稳定致密网状结构,进而导致镍渣和铜渣中的铁资源难以直接回收。因此,无论是采用高温氧化法抑或是还原法提取镍渣和铜渣中的铁资源时,通常都需要加入cao等碱性调质剂,以促使铁橄榄石解离并释放出简单铁氧化物(氧化亚铁feo),从而促进铁资源的深度提取与回收。
[0003]
转炉渣是转炉炼钢的副产品,具有产生量大、碱度高(二元碱度cao/sio2约为3.0-4.0)、含铁等特性。转炉渣中的全铁含量可达15-25%,含铁相主要以铁酸钙(2cao
·
fe2o3)、ro相(feo、mgo、mno形成的固熔体)等复杂含铁矿物存在;转炉渣中的含钙矿物主要包括游离氧化钙(f-cao)、硅酸三钙(3cao
·
sio2)、硅酸二钙(2cao
·
sio2)等;转炉渣中的含磷矿物相则主要以硅酸二钙(2cao
·
sio2)与磷酸三钙(ca3p2o8)形成的固溶体形式存在。而目前,转炉渣的综合利用率不足30%,其在大宗资源化利用方面所需要解决的主要问题包括:游离氧化钙水化易引起体积安定性不良、含铁导致可磨性差、含磷限制了在钢铁流程内部的循环利用。为解决上述问题,业内通常向转炉渣中添加硅质改质剂(硅石或硅灰、粉煤灰等)以实现惰化游离氧化钙的目的;同时,硅质改质剂还能促进转炉渣中铁酸钙(2cao
·
fe2o3)解离为简单的氧化铁(fe2o3),有利于转炉渣中铁资源的提取回收,从而使得含铁可磨性差的转炉渣转化为无铁易磨的安定化炉渣,实现转炉渣的高效循环利用。
[0004]
因此,借助转炉渣中的游离氧化钙、硅酸三钙、硅酸二钙、铁酸钙等钙质矿物,与镍渣和/或铜渣中的铁橄榄石进行交互反应,可在无需额外改质剂条件下,实现转炉渣与镍渣和/或铜渣之间的耦合改质,达到转炉渣中铁酸钙和镍渣和/或铜渣中铁橄榄石同时解离为简单铁氧化物的目的,进而促进转炉渣及镍渣和/或铜渣中铁资源的共同提取与回收。
[0005]
在转炉渣与镍渣和/或铜渣之间进行交互反应时,含钙矿物与铁橄榄石的交互反应如式(1)-(6)所示,即,转炉渣中的游离氧化钙、硅酸三钙、硅酸二钙、铁酸钙等含钙矿物,与镍渣和/或铜渣中的铁橄榄石进行耦合改质反应,实现转炉渣中的铁酸钙和镍渣和/或铜渣中的橄榄石同时解离,并生成简单铁氧化物fe2o3和feo。
[0006]
cao+2feo
·
sio2=cao
·
sio2+2feo
ꢀꢀꢀꢀꢀꢀꢀꢀꢀꢀꢀꢀꢀꢀꢀꢀꢀꢀꢀ
(1)
[0007]
2cao+2feo
·
sio2=2cao
·
sio2+2feo
ꢀꢀꢀꢀꢀꢀꢀꢀꢀꢀꢀꢀꢀꢀꢀꢀꢀ
(2)
[0008]
1/2(3cao
·
sio2)+2feo
·
sio2=3/2(cao
·
sio2)+2feo
ꢀꢀꢀ
(3)
[0009]
2(3cao
·
sio2)+2feo
·
sio2=3(cao
·
sio2)+2feo
ꢀꢀꢀꢀꢀꢀꢀꢀ
(4)
[0010]
2cao
·
sio2+2feo
·
sio2=2(cao
·
sio2)+2feo
ꢀꢀꢀꢀꢀꢀꢀꢀꢀ
(5)
[0011]
1/2(3cao
·
fe2o3)+2feo
·
sio2=cao
·
sio2+2feo+1/2fe2o3ꢀꢀꢀꢀꢀ
(6)
[0012]
由此可见,将还原剂添加到转炉渣与镍渣和/或铜渣所形成的耦合改质渣中,可对耦合改质反应生成的feo、fe2o3等简单铁氧化物进行还原,可最终实现耦合改质渣中铁资源的共同提取与回收。
[0013]
由于,炼钢厂的转炉渣的排渣温度通常在1450℃以上,吨渣显热相当于60kg标准煤,是优质的高温余热资源。如果利用熔融转炉渣所携带的物理显热把掺入的镍渣和/或铜渣加热至熔融态,则可实现转炉渣与镍渣和/或铜渣的熔融耦合改质,进而提高改质效率。
[0014]
但是,由于熔融转炉渣所携带的物理显热有限,如果仅利用熔融转炉渣物理显热来加热镍渣和/或铜渣至熔融态,则熔融转炉渣能够混熔的镍渣和/或铜渣量是有限的,从而导致耦合改质渣无法达到目标碱度,会造成转炉渣和镍渣和/或铜渣中存在的复杂铁氧化物不能完全解离,最终影响改质渣中铁资源的深度提取与回收。因此,为了获得目标碱度的改质渣,除了可直接利用熔融转炉渣的物理显热,还需要补充热量对更多的镍渣和/或铜渣进行加热熔化。
[0015]
因此,一种无需补充热量的转炉渣与镍渣和/或铜渣的熔融耦合改质及共同提铁方法亟待开发。
技术实现要素:[0016]
针对转炉渣、镍渣、铜渣中铁资源的提取技术现状,本发明提供了一种转炉渣与镍渣和/或铜渣的熔融耦合改质提铁方法,实现了在无需额外补充热量的条件下,转炉渣和镍渣和/或铜渣中复杂铁矿物同时解离为简单铁氧化物,进而促进多源冶金渣中铁资源的共同提取与回收。
[0017]
为实现上述目的,本发明提供的技术方案如下:
[0018]
一种转炉渣与镍渣和/或铜渣的熔融耦合改质提铁方法,包括:
[0019]
将渣温≥1450℃的熔融转炉渣排入到渣罐中,并在熔融转炉渣处于搅拌状态下,向渣罐中加入镍渣和/或铜渣和铝灰,获得熔混渣;
[0020]
对熔混渣进行持续搅拌,使镍渣和/或铜渣和铝灰与渣罐中的熔融转炉渣在充分混合的状态下,完成耦合改质和还原反应,获得含有大量金属铁滴的最终熔渣;
[0021]
停止搅拌,使渣罐中的最终熔渣自然冷却至室温后,取出沉降于渣罐底部的金属铁坨,同时通过磁选回收尾渣中的金属铁。
[0022]
进一步的,在将渣温≥1450℃的熔融转炉渣排入到渣罐中,并在熔融转炉渣处于搅拌状态下,向渣罐中加入镍渣和/或铜渣和铝灰时,包括:
[0023]
将渣温≥1450℃的熔融转炉渣排放到渣罐内后,通过分批次将镍渣和/或铜渣和铝灰掺入到熔融转炉渣中,使渣罐中熔混渣的温度保持在1400-1700℃。
[0024]
进一步的,在通过分批次将镍渣和/或铜渣和铝灰掺入到熔融转炉渣中时,包括:
[0025]
通过机械搅拌方式对渣罐进行搅拌,以使每一批次的镍渣和/或铜渣和铝灰与熔融转炉渣混合均匀,且在相邻两批次的镍渣和/或铜渣和铝灰掺入时间间隔为10-40min。
[0026]
进一步的,将两个批次镍渣和/或铜渣和铝灰掺入到熔融转炉渣中时,包括:
[0027]
在熔融转炉渣排放到渣罐内后,立即向渣罐内加入第一批次的镍渣和/或铜渣和
铝灰;并在第一批次的镍渣和/或铜渣和铝灰与熔融转炉渣持续搅拌30-40min后,向渣罐内加入第二批次的镍渣和/或铜渣和铝灰。
[0028]
进一步的,镍渣和/或铜渣在第一批次和第二批次的掺入量,按质量比分别为镍渣和/或铜渣总掺入量的50-70%和30-50%;铝灰在第一批次和第二批次的掺入量,按质量比分别为铝灰总加入量的50-70%和30-50%。
[0029]
进一步的,在通过磁选回收尾渣中的金属铁时,包括:
[0030]
将尾渣破碎至10-400μm后,通过磁选回收尾渣中的金属铁。
[0031]
进一步的,镍渣和/或铜渣的总掺入量为熔融转炉渣质量的60%-120%,铝灰的总掺入量为熔融转炉渣和镍渣和/或铜渣的总质量的30%-40%。
[0032]
进一步的,所述镍渣和/或铜渣的粒径≤5mm;铝灰以铝灰球形式加入到渣罐中,且铝灰球的直径≤10mm。
[0033]
本发明提供的一种转炉渣与镍渣和/或铜渣的熔融耦合改质提铁方法与现有冶金渣中铁资源的还原提取技术相比,具有以下优点:
[0034]
1)无需添加额外改质剂,实现了转炉渣与镍渣和/或铜渣的熔融耦合改质提铁及铁资源的共同回收;
[0035]
2)可在转炉排渣工序利用渣罐进行耦合改质和还原提铁操作,不需要额外处置设备。
[0036]
3)通过同时利用熔融转炉渣物理热及铝热还原反应化学热,满足了熔融耦合改质和还原提铁的热量需求,无需额外补充热量;
[0037]
4)铁的回收率高,可达到93%以上;
[0038]
5)提铁后的尾渣的碱度cao/sio2为0.75-1.5,可用作水泥原料,实现了最大程度的资源利用。
[0039]
本发明的其它特征和优点将在随后的说明书中阐述,并且,部分地从说明书中变得显而易见,或者通过实施本发明而了解。本发明的目的和其他优点可通过在所写的说明书、权利要求书、以及附图中所特别指出的结构来实现和获得。
[0040]
下面通过附图和实施例,对本发明的技术方案做进一步的详细描述。
附图说明
[0041]
图1为本发明示例性实施例1至3的原始镍渣的xrd图谱
[0042]
图2为本发明示例性实施例1至3的原始转炉渣的xrd图谱;
[0043]
图3为本发明示例性实施例1至3的最终获得的尾渣的xrd图谱。
具体实施方式
[0044]
为使本发明的目的、技术方案和优点更加清楚,下面将结合本发明实施例,对本发明的技术方案进行清楚、完整地描述。显然,所描述的实施例是本发明的一部分实施例,而不是全部的实施例。基于本发明中的实施例,本领域普通技术人员在没有做出创造性劳动的前提下所获得的所有其他实施例,都属于本发明保护的范围。
[0045]
本发明提供的一种转炉渣与镍渣和/或铜渣的熔融耦合改质提铁方法,包括如下步骤:
[0046]
(1)将渣温≥1450℃的熔融转炉渣排入到渣罐中,并在熔融转炉渣处于搅拌状态下,再向渣罐中加入总掺入量为熔融转炉渣质量的60%-120%的镍渣和/或铜渣、以及总掺入量为熔融转炉渣和镍渣和/或铜渣的总质量的30%-40%的铝灰,获得熔混渣;
[0047]
(2)对熔混渣进行持续搅拌,使镍渣和/或铜渣和铝灰与渣罐中的熔融转炉渣在充分混合的状态下,完成熔融耦合改质和还原反应,获得含有大量金属铁滴的最终熔渣;
[0048]
(3)停止搅拌,使渣罐中的最终熔渣自然冷却至室温后,取出沉降于渣罐底部的金属铁坨,同时将尾渣破碎至10-400μm后,并通过磁选回收尾渣中的金属铁,完成对转炉渣与镍渣和/或铜渣的共同提铁。
[0049]
金属铝不仅是强还原剂,且铝热还原反应伴随大量热量产生,1kg金属铝还原铁氧化物所释放的热量约为17500kj。因此,在采用金属铝作为还原剂对耦合改质中释放出的简单铁氧化物进行还原时,可充分利用铝热反应放热对耦合改质及共同提铁过程提供热量补偿。又由于铝灰是铝电解及熔铸过程所产生的冶金固废,铝灰中金属铝含量约为10-40wt%,因此,采用铝灰替代金属铝作为还原剂,不仅可降低还原剂成本,更重要的是借助铝灰中金属铝还原铁氧化物的化学热对耦合改质和还原过程进行热补偿,进而可实现基于熔融转炉渣物理显热和铝热反应化学热的双利用,满足熔融改质、以及熔融还原提铁的热量需求,进而保证耦合改质及还原提铁过程顺利进行。
[0050]
因此,通过熔融转炉渣中的游离氧化钙(f-cao)、硅酸三钙3cao
·
sio2、硅酸二钙2cao
·
sio2、铁酸钙2cao
·
fe2o3等含钙矿物,与镍渣和/或铜渣中的铁橄榄石2feo
·
sio2,在熔融转炉渣的排渣温度和铝热还原反应化学热所提供的热量下,使熔融转炉渣、镍渣和/或铜渣进行交互反应,进而实现熔融转炉渣中的铁酸钙及镍渣和/或铜渣中的铁橄榄石同时解离,并释放出fe2o3和feo,同时通过铝灰与fe2o3和feo的反应,完成对铁氧化物的还原。
[0051]
作为一优选实施方式,在将渣温≥1450℃的熔融转炉渣排入到渣罐中,并在熔融转炉渣处于搅拌状态下,向渣罐中加入镍渣和/或铜渣和铝灰时,包括:
[0052]
将渣温≥1450℃的熔融转炉渣排放到渣罐内后,通过分批次将镍渣和/或铜渣和铝灰掺入到熔融转炉渣中,使渣罐中熔混渣的温度保持在1400-1700℃。
[0053]
由于,铝灰作为还原剂对耦合改质中释放出的简单铁氧化物进行还原时,会产生大量的热量,而熔融转炉渣与镍渣和/或铜渣的熔融耦合改质提铁需要在1400-1700℃下进行,因此,通过分批次将镍渣和/或铜渣和铝灰掺入到熔融转炉渣中,可保证转炉渣与镍渣和/或铜渣的熔融耦合改质和还原提铁过程中的熔混渣温度控制在1400-1700℃之间,进而无需外界对渣罐的补热。
[0054]
作为优选的,在每一批次的镍渣和/或铜渣和铝灰掺入到熔融转炉渣中,均对渣罐进行机械搅拌,以促进熔融转炉渣中镍渣和/或铜渣和铝灰的均匀分布,进而促进耦合改质和还原反应的充分进行。同时,通过控制对渣罐进行机械搅拌的转速,还可以控制耦合改质和还原反应的速率,进而控制铝热反应速率,以便将熔混渣温度控制在1400-1700℃之间。
[0055]
具体的,在通过分批次将镍渣和/或铜渣和铝灰掺入到熔融转炉渣中时,包括:
[0056]
通过机械搅拌方式对渣罐进行搅拌,以使每一批次的镍渣和/或铜渣和铝灰与熔融转炉渣混合均匀,且在相邻两批次的镍渣和/或铜渣和铝灰掺入时间间隔为10-40min。
[0057]
其中,在一批次的镍渣和/或铜渣和铝灰掺入到熔融转炉渣中后,对渣罐持续进行机械搅拌,使熔融转炉渣与此批次的镍渣和/或铜渣和铝灰反应10-40min后,再将另一批次
的镍渣和/或铜渣和铝灰掺入到熔融转炉渣中,以控制渣罐中的温度保持在1400-1700℃。
[0058]
进一步的,当两个批次将镍渣和/或铜渣和铝灰掺入到熔融转炉渣中时,包括:
[0059]
在熔融转炉渣排放到渣罐内后,立即向渣罐内加入第一批次的镍渣和/或铜渣和铝灰;并在第一批次的镍渣和/或铜渣和铝灰与熔融转炉渣持续搅拌30-40min后,向渣罐内加入第二批次的镍渣和/或铜渣和铝灰。
[0060]
其中,镍渣和/或铜渣在第一批次和第二批次的掺入量,按质量比分别为镍渣和/或铜渣总掺入量的50-70%和30-50%;铝灰在第一批次和第二批次的掺入量,按质量比分别为铝灰总加入量的50-70%和30-50%。
[0061]
作为一优选实施方式,镍渣和/或铜渣的粒径≤5mm;铝灰以铝灰球形式加入到渣罐中,且铝灰球的直径≤10mm。
[0062]
以下是本发明的实施例,表1-3分别给出了实施例用熔融转炉渣、镍渣、铝灰的化学成分。
[0063]
表1实施例用熔融转炉渣的化学成分
[0064][0065]
表2实施例用镍渣的化学成分
[0066][0067]
表3实施例用铝灰的化学成分
[0068][0069]
实施例1
[0070]
一种转炉渣与镍渣的熔融耦合改质提铁方法,包括如下步骤:
[0071]
(1)将25吨的渣温为1600℃的熔融转炉渣排入到渣罐中,再向渣罐中加入第一批次的粒径≤5mm的镍渣和直径为10mm铝灰球,获得初期熔混渣;其中,镍渣的加入量为19.6吨、铝灰球的加入量为14.7吨,并在第一次加料后采用机械搅拌持续搅拌熔混渣40分钟;
[0072]
(2)在初期熔混渣处于搅拌状态下,向渣罐内加入第二批次的粒径≤5mm的镍渣和直径为10mm铝灰球,获得中期熔混渣;其中,镍渣的加入量为8.4吨、铝灰球的加入量为6.3吨;
[0073]
(3)并在第二次加料后,持续搅拌中期熔混渣20分钟,使镍渣和铝灰在与熔融转炉渣充分混合状态下,完成耦合改质和还原反应,整个熔融耦合改质和还原过程中,渣罐内熔混渣的温度控制在1403-1692℃,并获得含有大量金属铁滴的最终熔渣;
[0074]
(4)停止搅拌,使渣罐中的最终熔渣自然冷却至室温后,然后倾翻渣罐,取出沉降于渣罐底部的金属铁坨,将尾渣破碎至50-100μm后,并通过磁选回收尾渣中的金属铁。
[0075]
通过实施例1提取的金属铁化学成分检测结果如表4所示,其按质量百分比含fe 99.21%,同时,相对于原始转炉渣和镍渣,本实施例的铁回收率分别为95.9%和98.0%。
[0076]
通过实施例1获得的尾渣的化学成分检测结果如表5所示,尾渣碱度cao/sio2约为
1.00,尾渣主要物相为camg2al
16
o
27
、mgal2o4,由此可见,本实施例获得的尾渣可用作水泥原料。
[0077]
实施例2
[0078]
一种转炉渣与镍渣的熔融耦合改质提铁方法,包括如下步骤:
[0079]
(1)将25吨的渣温为1500℃的熔融转炉渣排入到渣罐中,再向渣罐中加入第一批次的粒径≤4mm的镍渣和直径为9mm铝灰球,获得初期熔混渣;其中,镍渣的加入量为11吨、铝灰球的加入量为8.8吨,并在第一次加料后采用机械搅拌持续搅拌初期熔混渣35分钟;
[0080]
(2)在初期熔混渣处于搅拌状态下,向渣罐内加入第二批次的粒径≤4mm的镍渣和直径为9mm铝灰球,获得中期熔混渣;其中,镍渣的加入量为5吨、铝灰球的加入量为7.2吨;
[0081]
(3)并在第二次加料后,持续搅拌中期熔混渣25分钟,使镍渣和铝灰在与熔融转炉渣充分混合状态下,完成耦合改质和还原反应整个熔融耦合改质和还原过程中,渣罐内熔混渣的温度控制在1411-1685℃,并获得含有大量金属铁滴的最终熔渣;
[0082]
(4)停止搅拌,使渣罐中的最终熔渣自然冷却至室温后,然后倾翻渣罐,取出沉降于渣罐底部的金属铁坨,将尾渣破碎至50-100μm后,并通过磁选回收尾渣中的金属铁。
[0083]
通过实施例2提取的金属铁化学成分检测结果如表4所示,其按质量百分比含fe 99.00%,同时,相对于原始转炉渣和镍渣,本实施例的铁回收率分别为95.6%和97.4%。
[0084]
通过实施例2获得的尾渣的化学成分检测结果如表5所示,尾渣碱度cao/sio2约为1.25,尾渣主要物相为ca2al2sio7、mgal2o4,由此可见,本实施例获得的尾渣可用作水泥原料。
[0085]
实施例3
[0086]
一种转炉渣与镍渣的熔融耦合改质提铁方法,包括如下步骤:
[0087]
(1)将25吨的渣温为1450℃的熔融转炉渣排入到渣罐中,再向渣罐中加入第一批次的粒径≤3mm的镍渣和直径为8mm铝灰球,获得初期熔混渣;其中,镍渣的加入量为7吨、铝灰球的加入量为4.8吨,并在第一次加料后采用机械搅拌持续搅拌初期熔混渣30分钟;
[0088]
(2)在初期熔混渣处于搅拌状态下,向渣罐内加入第二批次的粒径≤3mm的镍渣和直径为8mm铝灰球,获得中期熔混渣;其中,镍渣的加入量为8吨、铝灰球的加入量为7.2吨;
[0089]
(3)并在第二次加料后,持续搅拌中期熔混渣30分钟,使镍渣和铝灰在与熔融转炉渣充分混合状态下,完成耦合改质和还原反应,整个耦合改质和还原过程中,渣罐内熔混渣的温度控制在1422-1679℃,并获得含有大量金属铁滴的最终熔渣;
[0090]
(4)停止搅拌,使渣罐中的最终熔渣自然冷却至室温后,然后倾翻渣罐,取出沉降于渣罐底部的金属铁坨,将尾渣破碎至50-100μm后,并通过磁选回收尾渣中的金属铁。
[0091]
通过实施例3提取的金属铁化学成分检测结果如表4所示,其按质量百分比含fe 98.81%,同时,相对于原始转炉渣和镍渣,本实施例的铁回收率分别为93.3%和96.7%。
[0092]
通过实施例3获得的尾渣的化学成分检测结果如表5所示,尾渣碱度cao/sio2约为1.25,尾渣主要物相为ca2al2sio7、mgal2o4、camg2al
16
o
27
、caal2si2o8,由此可见,本实施例获得的尾渣可用作水泥原料。
[0093]
表4实施例1至3提取的金属铁的成分
[0094][0095]
表5实施例1至3中的尾渣化学成分及铁回收率
[0096][0097]
通过对上述实施例进行分析,本发明提供的一种转炉渣与镍渣和/或铜渣的熔融耦合改质提铁方法与现有冶金渣中铁资源的还原提取技术相比,具有以下优点:
[0098]
1)无需添加额外改质剂,实现了转炉渣与镍渣和/或铜渣的熔融耦合改质提铁及铁资源的共同回收;
[0099]
2)可在转炉排渣工序利用渣罐进行耦合改质和还原提铁操作,不需要额外处置设备。
[0100]
3)通过同时利用熔融转炉渣物理热及铝热还原反应化学热,满足了熔融耦合改质和还原提铁的热量需求,无需外界补热;
[0101]
4)铁的回收率高,可达到93%以上;
[0102]
5)提铁后尾渣碱度cao/sio2为0.75-1.5,可用作水泥原料,实现了最大程度的资源利用。
[0103]
最后应说明的是:以上实施例仅用以说明本发明的技术方案,而非对其限制;尽管参照前述实施例对本发明进行了详细的说明,本领域的普通技术人员应当理解:其依然可以对前述各实施例所记载的技术方案进行修改,或者对其中部分技术特征进行等同替换;而这些修改或者替换,并不使相应技术方案的本质脱离本发明各实施例技术方案的精神和范围。