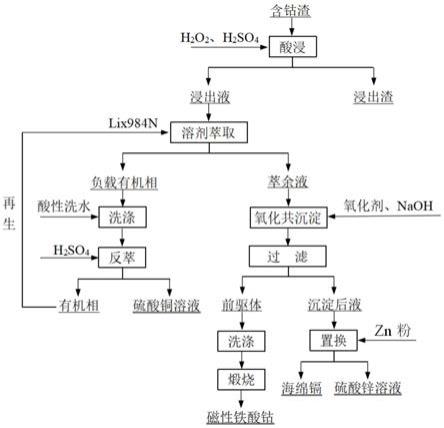
[0001]
本发明属于湿法冶金废渣综合回收领域,特别涉及一种从含钴渣中制备铁酸钴的方法。
背景技术:[0002]
钴是一种极其重要的战略资源,被广泛应用于电池生产、电子器件、化学化工、航空航天、机械制造等行业领域。2018年全球探明钴矿资源储量约为687.5万吨,这些钴矿资源多伴生于铜、镍、锌等矿床中,独立钴矿物极少,因此钴的获取主要来源于铜、镍、强、锌等主金属的冶炼系统和含钴的资源废料。2018年我国探明钴矿资源储量仅为8万吨,资源较为匮乏,且具有品位低、矿床规模小、贫矿和伴生矿多、开采难度较大的特点。我国是世界上最大的钴消费国家,且随着通信技术的不断革新和国家对新能源产业的大力扶持,对钴的需求也会日益增大。由于钴矿资源极为稀缺,所以我国钴矿石主要从刚果、赞比亚和澳大利亚等产钴国家进口,依赖程度高,不利于我国钴产业的持续发展,所以开展含钴二次资源的清洁回收技术迫在眉睫。
[0003]
在湿法炼锌工艺中,过多的铁存在会增加锌电解电能消耗、降低电流效率,过多的钴存在会导致锌电解“烧板”,所以硫酸锌溶液进入电解系统前需要进行净化沉铁、沉钴处理,得到成分复杂的净化渣,可作为回收铁、钴的重要二次资源。针对含钴渣,常先用硫酸浸出处理,获得包含铜、钴、铁、镉和锌的硫酸浸出溶液,通常溶液预先除铜和除铁,再通过溶剂萃取、沉淀剂选择性沉淀等方法回收钴,得到的富钴溶液或沉淀需要再进一步净化处理,再制作钴盐或钴的氧化物。
[0004]
例如张恩玉等人公开专利“一种锌钴分离方法”(cn106119560a),对浸出液加锌粉、氧化剂、氢氧化钠一步实现置换除铜、氧化沉铁,净化液采用氢氧化钠调节溶液在特别高的ph值,使锌以锌酸根形式留在溶液中,而钴以氢氧化钴形式沉淀,但溶液耗碱量特别大,导致生产成本过高,且沉淀后溶液中硫酸钠含量过高,影响后续锌的回收。
[0005]
许斌等人公开专利“一种锌冶炼钴渣制备氧化钴的方法”(cn106119560a),针对钴渣的浸出液先加入碳酸钠中和沉淀除铁,再加入选择性沉钴剂选择性沉钴得到一次沉钴渣,一次沉钴渣再经还原浸出、氢氧化钠沉钴得到二次沉钴渣,二次沉钴渣经洗涤和煅烧后制备出氧化钴产品。但在选择性沉钴剂一次沉钴过程中钴沉淀不完全,且在二段沉钴过程中不可避免地有部分锌沉淀下来,加大了分离难度。
[0006]
综上,现有的含铁的钴渣回收方法手段复杂,铁、钴的回收需要分开,得到的富钴物需要进一步净化工艺才能制备纯净钴产品,且金属回收率有待进一步提升。
技术实现要素:[0007]
基于此,本发明的目的在于,提供一种从含钴渣中制备铁酸钴的方法,特别适用于处理从锌冶炼过程得到的含铁的钴渣,与现有的回收方法比较,本发明将铁、钴以铁酸钴的形式同步从锌冶炼系统中开路,并实现其他金属的综合回收。
[0008]
一种从含钴渣中制备铁酸钴的方法,包括如下步骤:
[0009]
步骤1、酸浸:将含钴渣采用酸性浸出,过滤得到含铁、钴的浸出液和浸出渣;
[0010]
步骤2、溶剂萃取:步骤1的浸出液先采用肟羟基萃取剂萃取,分离后得到负载有机相和萃余液;负载有机相采用酸性水洗,分离后得到洗涤后液和洗涤后有机相;洗涤后有机相采用硫酸反萃,得到反萃后有机相和硫酸铜溶液;
[0011]
步骤3、氧化共沉淀:步骤2的萃余液加入氧化剂将铁、钴完全氧化成fe
3+
和co
3+
,反应结束后在室温下静置和老化,过滤后得到成分为含镉、锌的沉淀后液和含fe(oh)3、co(oh)3的前驱体;
[0012]
步骤4、前驱体洗涤煅烧:采用硫酸多次洗涤前驱体,洗涤后将前驱体风干,然后高温煅烧得到高纯铁酸钴。
[0013]
本发明所述的一种从含钴渣中制备铁酸钴的方法。通过硫酸浸出含钴渣使铜、铁、钴、镉和锌进入浸出液,利用萃取过程中金属在两相中配比的不同和金属氢氧化物溶度积常数的不同,继而浸出液经过溶剂萃取提取铜,氧化共沉淀分离出铁、钴,得到的前驱体经过洗涤煅烧后最终制得磁性纳米铁酸钴产品。实现了从含钴渣中提取钴和制备铁酸钴的目的。与现有方法比较,本发明有以下有点:不需要分布除去铁、钴,能使二者共同沉淀且碱消耗量小,并以含铁的钴渣作为铁源和钴源直接制备出磁性纳米铁酸钴;铁、钴的回收率高,均达到98%以上;得到的前驱体经洗涤即可煅烧制备产品铁酸钴;工艺及设备简单、流程短、环境友好。
[0014]
进一步地,步骤1所述酸浸时采用的酸为硫酸,控制反应ph值为0.5~1.5,反应温度为60℃~80℃。
[0015]
进一步地,步骤2中肟羟基萃取剂采用浓度为20%~30%的lix984n,萃取条件为:温度25℃,ph值为1.8~2.4,萃取时间为4~8min,萃取相比o/a为1/2~2/1。步骤2中负载有机相采用ph值为3~4的硫酸溶液进行洗涤;洗涤后有机相采用浓度为1.0~2.5mol/l的硫酸以1:1的相比反萃。
[0016]
进一步地,步骤3中萃余液在加氧化剂之前,先补入一定量硫酸亚铁或硫酸钴,完全溶解后使溶液中离子摩尔比fe:co=2:1,其中溶液中的铁离子可能存在形式为fe
2+
、fe
3+
中的一种或两种,溶液中的钴离子可能存在形式为co
2+
、co
3+
中的一种或两种。
[0017]
进一步地,步骤3中所述氧化剂为过硫酸钠或双氧水,且氧化剂的加入量为理论量的2~5倍,可将铁、钴完全氧化成fe
3+
和co
3+
;氧化共沉淀的反应条件为:氧气通入的流速为10~50ml/min,温度为65℃~85℃,时间50~80min,沉淀终点ph值为3.5~4.5。
[0018]
进一步地,步骤4中采用ph为3.5~4.5的硫酸溶液洗涤前驱体,洗涤液中加入双氧水来维持氧化氛围。前驱体在空气或惰性气体氛围下,温度为400℃~1000℃进行高温煅烧,煅烧时间20~60min。
[0019]
进一步地,步骤3中含镉、锌的沉淀后液可制备海绵镉、硫酸锌产品;步骤4中所述高纯铁酸钴是一种具有磁性的纳米颗粒。
[0020]
进一步地,步骤2中所述洗涤后液可补酸后在步骤1中作为浆化剂;步骤2中所述反萃后有机相可再生在步骤2中重新作为萃取剂;步骤2中所述硫酸铜溶液可补酸,作为负载有机相的反萃剂,多次循环后得到高含量硫酸铜溶液,再采用电解沉积制备电铜。
[0021]
本发明的有益效果为:
[0022]
1、本发明中,针对锌冶炼过程产出的含铁的钴渣,本发明创新性地提出以渣中铁、钴作为原料,协同除去溶液中铁、钴的同时得到前驱体,并进一步制备出磁性纳米铁酸钴;本发明方法,可实现铁、钴与锌的高选择性和高回收率的分离,研究发现,铁钴的同步回收率可达到95%以上,而铜的回收率可达96%以上。
[0023]
2、本发明工艺简单,环境污染小,对含铁的钴渣进行有效的综合回收,尤其是渣中的钴、铁,制备出具有磁性的纳米材料,避免了湿法炼锌工艺中铁渣和钴渣难回收的问题,减轻了废渣堆存对环境的压力,达到清洁生产的要求。
[0024]
3、资源循环利用率高。本发明最终得到产品纯净硫酸铜溶液、磁性纳米铁酸钴、镉和锌的硫酸混合溶液,其中纯净硫酸铜溶液可补酸,作为负载有机相的反萃剂,多次循环后得到高含量硫酸铜溶液采用电解沉积制备电铜;磁性纳米铁酸钴可作为一种软磁材料,有广泛的工业应用;镉和锌的硫酸混合溶液可以通过“锌粉置换-深度除杂-蒸发结晶”工艺制备出海绵镉、一水硫酸锌或十二水硫酸锌产品,因此整个工艺有很好的工业化应用前景。
[0025]
为了更好地理解和实施,下面结合附图详细说明本发明。
附图说明
[0026]
图1为本发明的工艺流程图;
[0027]
图2为实施例1产品xrd表征图,表征铁酸钴(cofe2o4)一种物相;
[0028]
图3为实施例1产品ft-ir表征图,表征和两种振动吸收峰;
[0029]
图4为实施例1产品sem-eds表征,表征类球形纳米颗粒;
[0030]
图5为实施例1和实施例8产品vsm表征图,表征铁酸钴的磁性滞回曲线。
具体实施方式
[0031]
本说明书中公开的所有特征,或公开的所有方法或过程中的步骤,除了互相排斥的特征和或步骤以外,均可以以任何方式组合。
[0032]
本说明书包括任何附加权利要求和摘要中公开的任一特征,除非特别叙述,均可被其他等效或具有类似目的的替代特征加以替换。即,除非特别叙述,每个特征只是一系列等效或类似特征中的一个例子而已。
[0033]
以下案例,以某冶炼厂湿法炼锌工艺中的两种含钴渣为原料,其主要金属成分如表1所示。其中,铜含量0.3%~7%,铁含量0.3%~4%,钴含量0.5%~3%,镉含量1%~12%,锌含量10%~30%。
[0034]
表1两种含钴渣原料主要金属成分及含量/%
[0035][0036]
实施例1
[0037]
一种从含钴渣中制备铁酸钴的方法,以1号含钴渣作为原料,按质量百分比计:渣
中含铜0.96%、铁0.50%、钴2.83%、镉2.57%、锌24.66%,所述方法包括如下步骤。
[0038]
步骤1,酸浸工序:将含钴渣用水浆化,加入双氧水作为氧化剂,然后缓慢加入浓硫酸,为此反应温度80℃,并控制反应ph值0.5,反应完过滤后,得到富含铜、铁、钴、镉和锌的浸出液和微量残渣;
[0039]
步骤2,溶剂萃取工序:浸出液先采用浓度为25%的肟羟基萃取剂(lix984n)萃取,萃取温度为25℃,水相ph值为2.0,萃取时间为6min,萃取相比o/a为1/1.5,分离后得到萃余液和负载有机相;负载有机相采用ph值为3的硫酸溶液进行洗涤,分离后得到洗涤后液和洗涤后有机相;洗涤后有机相采用浓度为2.0mol/l的硫酸以1:1的相比反萃,得到反萃后有机相和纯净硫酸铜溶液;
[0040]
步骤3,氧化共沉淀工序:步骤2得到的萃余液静置后通过活性炭吸附除去表层的残余油,然后补入一定量的硫酸亚铁,完全溶解后溶液中离子摩尔比fe:co=2:1,然后加入氧化剂过硫酸钠,且氧化剂的加入量为理论量的4倍,氧气通入的流速控制为20ml/min,在温度为75℃的条件下反应时间60min,沉淀终点ph值为4,反应结束后在室温下静置和老化24h;过滤后得到成分为含镉、锌的沉淀后液和含fe(oh)3、co(oh)3的前驱体;
[0041]
步骤4,前驱体洗涤煅烧:采用ph为4的硫酸溶液多次洗涤前驱体,洗涤液中加入2ml双氧水来维持氧化氛围,洗涤后将前驱体在室温下风干,然后放入高温管式炉,在空气氛围升温至800℃,煅烧30min后得到高纯度铁酸钴。
[0042]
试验结果为:铜、铁和钴的回收率分别为98.61%、99.94%和99.72%。最终得到平均粒径为78nm、饱和磁化强度为62.20emu/g、矫顽力为736.19oe的磁性纳米铁酸钴。产品铁酸钴成分如表2所示,xrd表征如图2所示,ft-ir表征如图3所示,sem-eds表征如图4所示,vsm磁性表征如图5所示。
[0043]
此时的工艺条件作为最优选条件。
[0044]
表2实施例1产品铁酸钴元素成分/%
[0045]
元素fecocucdzno含量48.8524.370.000.000.0026.78
[0046]
实施例2
[0047]
实施例2与实施例1大致相同,不同之处在于步骤2中:
[0048]
浸出液先采用浓度为20%的肟羟基萃取剂(lix984n)萃取,萃取温度为25℃,水相ph值为1.8,萃取时间为4min,萃取相比o/a为1/2,分离后得到萃余液和负载有机相;负载有机相采用ph值为3的硫酸溶液进行洗涤,分离后得到洗涤后液和洗涤后有机相;洗涤后有机相采用浓度为1.0mol/l的硫酸以1:1的相比反萃。
[0049]
试验结果为:铜、铁和钴的回收率分别为96.31%、99.87%和99.75%。最终得到平均粒径为75nm、饱和磁化强度为63.41emu/g、矫顽力为742.74oe的磁性纳米铁酸钴,产品铁酸钴成分如表3所示。
[0050]
此时,在步骤2中有少量的铜在萃取时未能完全分离,从而在步骤3氧化共沉淀过程中随之沉降,使产品中出现杂质cu。
[0051]
表3实施例2产品铁酸钴元素成分/%
[0052]
元素fecocucdzno含量48.6424.220.200.000.0026.94
[0053]
实施例3
[0054]
实施例3与实施例1大致相同,不同之处在于步骤2中:
[0055]
浸出液先采用浓度为30%的肟羟基萃取剂(lix984n)萃取,在温度为25℃,水相ph值为2.4,萃取时间为8min,萃取相比o/a为2/1的条件下萃取,分离后得到萃余液和负载有机相;负载有机相采用ph值为4的硫酸溶液进行洗涤,分离后得到洗涤后液和洗涤后有机相;洗涤后有机相采用浓度为2.5mol/l的硫酸以1:1的相比反萃,得到反萃后有机相和纯净硫酸铜溶液。
[0056]
试验结果为:铜、铁和钴的回收率分别为99.66%、99.83%和99.69%。最终得到平均粒径为74nm、饱和磁化强度为62.58emu/g、矫顽力为730.12oe的磁性纳米铁酸钴,产品铁酸钴成分为fe:48.61%、co:24.25%和o:27.14%。
[0057]
此时,步骤2中铜回收效果最佳,但萃取剂成分大、萃取时间长、萃取相比大、反萃剂硫酸浓度高,而导致能量及经济损耗更大,且得到的纯净硫酸铜溶液相比浸出液浓度更低。
[0058]
实施例4
[0059]
实施例4与实施例1大致相同,不同之处在于步骤3中:
[0060]
萃余液静置后通过活性炭吸附除去表层的残余油,然后补入一定量的硫酸亚铁,完全溶解后使溶液中离子摩尔比fe:co=2:1,然后加入氧化剂过双氧水,且氧化剂的加入量为理论量的2倍,控制在氧气通入的流速为10ml/min,温度65℃,时间50min,沉淀终点ph值3.5的条件下进行反应,反应结束后在室温下静置和老化24h。
[0061]
试验结果为:铜、铁和钴的回收率分别为98.46%、98.04%和95.20%。最终得到平均粒径为70nm、饱和磁化强度为63.13emu/g、矫顽力为728.20oe的磁性纳米铁酸钴,产品铁酸钴成分为fe:49.85%、co:23.23%和o:26.92%。
[0062]
此时,步骤3中铁、钴的沉淀率未达到最高,部分铁、钴未氧化完全,从而未能够沉淀下来。
[0063]
实施例5
[0064]
实施5与实施例1大致相同,不同之处在于步骤3中:
[0065]
萃余液静置后通过活性炭吸附除去表层的残余油,然后补入一定量的硫酸亚铁,完全溶解后使溶液中离子摩尔比fe:co=2:1,然后加入氧化剂过双氧水,且氧化剂的加入量为理论量的5倍,控制在氧气通入的流速为50ml/min,温度85℃,时间80min,沉淀终点ph值4.5的条件下进行反应,反应结束后在室温下静置和老化24h。
[0066]
试验结果为:铜、铁和钴的回收率分别为98.71%、99.98%和99.93%。最终得到平均粒径为75nm、饱和磁化强度为63.30emu/g、矫顽力为734.28oe的磁性纳米铁酸钴,产品铁酸钴成分为fe:48.87%、co:24.34%和o:26.82%。
[0067]
此时,步骤3中铁、钴沉淀效果最佳,但氧化剂加入量大、氧气消耗多、反应温度高、反应时间长,而导致能量及经济损耗更大。
[0068]
实施例6
[0069]
实施例6采用2号含钴渣为原料,方法步骤与实施例1大致相同,不同之处在于:
[0070]
步骤3中:补入一定量的硫酸钴,完全溶解后使溶液中离子摩尔比fe:co=2:1;
[0071]
步骤4中:采用ph为3.5的硫酸溶液多次洗涤前驱体,洗涤液中加入2ml双氧水来维
持氧化氛围,洗涤后将前驱体在室温下风干,然后放入高温管式炉,在空气氛围升温至400℃,煅烧20min后得到高纯度铁酸钴。
[0072]
试验结果为:铜、铁和钴的回收率分别为98.65%、99.92%和99.86%。最终得到平均粒径为176nm、饱和磁化强度为58.43emu/g、矫顽力为424.70oe的磁性纳米铁酸钴,产品铁酸钴成分为fe:48.83%、co:24.37%和o:26.80%。
[0073]
此时,步骤4中产品铁酸钴颗粒大,饱和磁化强度和矫顽力均更小,磁性能更小。
[0074]
实施例7
[0075]
实施例7采用2号含钴渣为原料,方法步骤与实施例6大致相同,不同之处在于:
[0076]
步骤4中:采用ph为4.5的硫酸溶液多次洗涤前驱体,洗涤液中加入2ml双氧水来维持氧化氛围,洗涤后将前驱体在室温下风干,然后放入高温管式炉,在空气氛围升温至1000℃,煅烧60min后得到高纯度铁酸钴。
[0077]
试验结果为:铜、铁和钴的回收率分别为98.57%、99.89%和99.74%。最终得到平均粒径为52nm、饱和磁化强度为78.48emu/g、矫顽力为872.91oe的磁性纳米铁酸钴,产品铁酸钴成分为fe:48.83%、co:24.37%和o:26.80%。
[0078]
此时,步骤4中产品铁酸钴颗粒更小,饱和磁化强度和矫顽力更大,更偏离软磁铁,且煅烧温度更高、煅烧时间更长导致能耗更大。
[0079]
实施例8
[0080]
实施例8采用2号含钴渣为原料,方法步骤与实施例6大致相同,不同之处在于:
[0081]
步骤4中:煅烧氛围为氩气。
[0082]
试验结果为:铜、铁和钴的回收率分别为98.57%、99.94%和99.83%。最终得到平均粒径为84nm、饱和磁化强度为69.17emu/g、矫顽力为785.72oe的磁性纳米铁酸钴,产品铁酸钴成分为fe:50.25%、co:26.67%和o:23.08%,vsm磁性表征如图5所示
[0083]
此时,步骤4中产品铁酸钴颗粒更大,饱和磁化强度和矫顽力更大,铁、钴含量更高、氧含量更低。
[0084]
对比实施例1和实施例8发现,煅烧氛围对产品性能和成分有影响:相比在氩气氛围,空气氛围下制备的铁酸钴氧含量更高,但磁饱和强度和矫顽力更小。
[0085]
以上所述实施例仅表达了本发明的几种实施方式,其描述较为具体和详细,但并不能因此而理解为对发明/专利范围的限制。应当指出的是,对于本领域的普通技术人员来说,在不脱离本发明构思的前提下,还可以做出若干变形和改进,这些都属于本发明的保护范围。