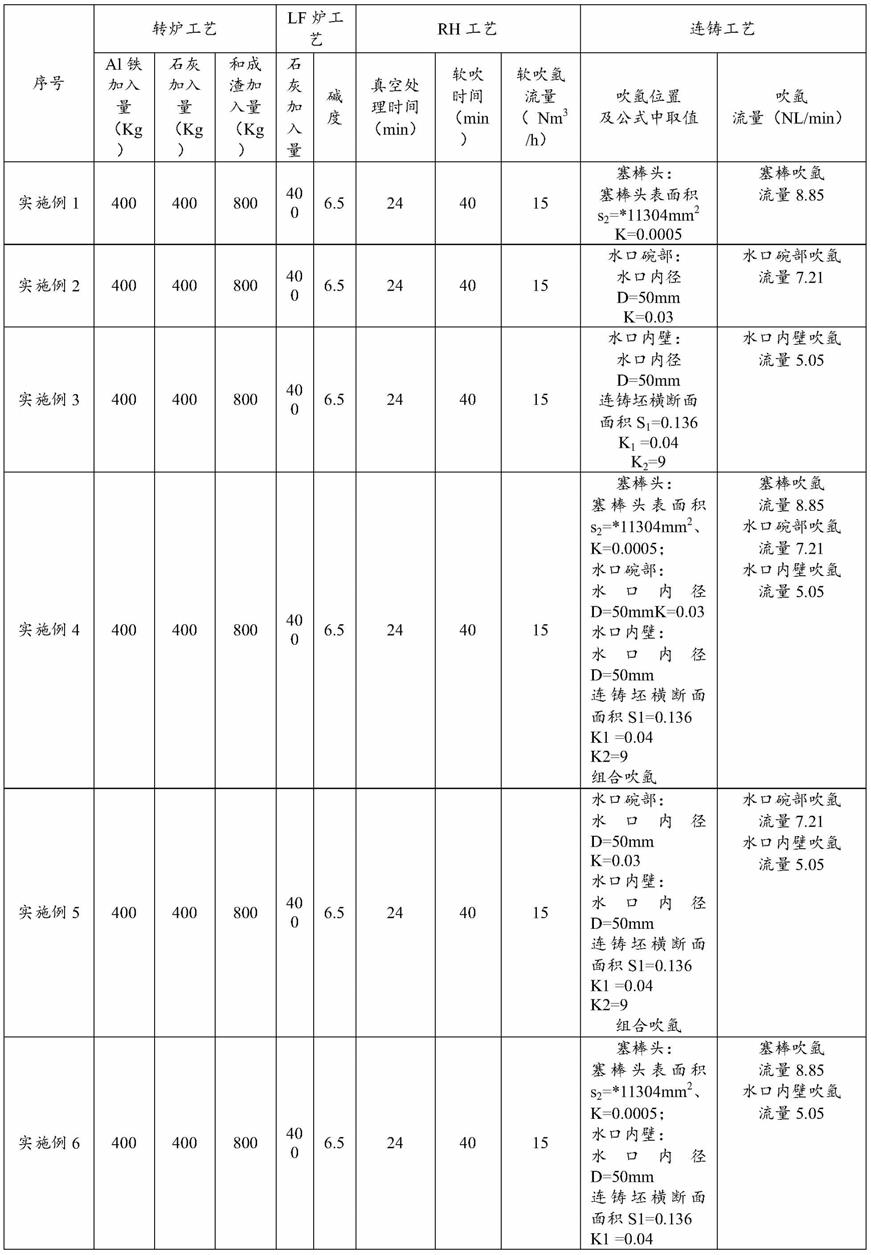
[0001]
本申请涉及钢铁冶炼领域,具体而言,涉及一种减少轴承钢中夹杂物的方法以及连铸吹氩控制方法。
背景技术:[0002]
高碳铬轴承钢生产过程,由于转炉冶炼过程脱碳,导致钢水中产生大量游离氧。为了降低钢中的游离氧,需要对钢水进行脱氧,脱氧过程会产生大量夹杂物,降低轴承的疲劳寿命。
[0003]
目前常规的减少轴承钢夹杂物的方法主要在转炉出钢过程,通过加入al铁沉淀脱氧。同时加入cao等渣料进行造渣,同时在lf钢包精炼工序造“白渣”,进行扩散脱氧、去除夹杂物。但是由于渣系的成分设计不能有效吸附夹杂物,导致钢材钢材中出现大尺寸的夹杂物。
技术实现要素:[0004]
本申请实施例的目的在于提供一种减少轴承钢中夹杂物的方法以及连铸吹氩控制方法。
[0005]
第一方面,本申请提供一种减少轴承钢中夹杂物的连铸吹氩控制方法,包括:
[0006]
连铸结晶器浸入式水口采用整体式水口,对水口碗部、水口内壁以及塞棒头部单独或同时吹入氩气;
[0007]
其中,对水口碗部吹入的氩气流量根据结晶器浸入式水口内径进行调整;
[0008]
对水口内壁吹入的氩气流量根据结晶器浸入式水口内径、连铸坯横断面面积进行调整;
[0009]
对塞棒头部吹入的氩气流量根据塞棒头表面积进行调整。
[0010]
第二方面,本申请提供一种减少轴承钢中夹杂物的方法,在轴承钢冶炼过程中,对冶炼工序进行控制;冶炼工序包括:
[0011]
转炉出钢工序;
[0012]
精炼工序;
[0013]
rh真空脱气处理工序;以及
[0014]
连铸工序,在连铸工序采用前述的减少轴承钢中夹杂物的连铸吹氩控制方法进行吹氩。
[0015]
本申请实施例提供的减少轴承钢中夹杂物的方法以及连铸吹氩控制方法的有益效果包括:
[0016]
本申请水口碗部吹氩流量依据结晶器浸入式水口内径进行调整,能很好的控制轴承钢连铸过程中夹杂物在水口碗部产生聚集剥落,通过水口碗部吹氩流量公式,将吹氩流量与结晶器浸入式水口内径通过公式定量表征,定量控制和调整水口碗部吹氩流量;水口内壁吹氩流量依据结晶器浸入式水口内径、连铸坯横断面面积进行调整,能很好的控制轴
承钢连铸过程中夹杂物在水口内壁产生聚集剥落,通过水口内壁吹氩流量公式,将吹氩流量与结晶器浸入式水口内径、连铸坯横断面面积关系通过公式定量表征,定量控制和调整水口内壁吹氩流量;塞棒吹氩流量依据塞棒头表面积进行调整,能很好的控制轴承钢连铸过程中夹杂物在塞棒头部产生聚集剥落,通过塞棒吹氩流量公式,将吹氩流量与塞棒头表面积通过公式定量表征,定量控制和调整塞棒吹氩流量;从而避免了人工经验范围调整导致轴承钢夹杂物控制失败,为吹氩流量精确控制提供了可操作易于实现的控制依据,减少了水口碗部、水口内壁以及塞棒头部夹杂物的聚集剥落,进一步减少了轴承钢内夹杂物的数量及尺寸,使轴承钢夹杂物控制到目标范围。
具体实施方式
[0017]
为使本申请实施例的目的、技术方案和优点更加清楚,下面将对本申请实施例中的技术方案进行清楚、完整地描述,显然,所描述的实施例是本申请一部分实施例,而不是全部的实施例。
[0018]
因此,以下本申请的实施例的详细描述并非旨在限制要求保护的本申请的范围,而是仅仅表示本申请的选定实施例。基于本申请中的实施例,本领域普通技术人员在没有作出创造性劳动前提下所获得的所有其他实施例,都属于本申请保护的范围。
[0019]
以下“%”均指质量百分比。
[0020]
本申请实施方式提供一种减少轴承钢中夹杂物的方法,在轴承钢冶炼过程中,对冶炼工序进行控制。从而减少轴承钢中的夹杂物,使得夹杂物尺寸更小。
[0021]
在本申请一些实施方式中,对高碳铬轴承钢冶炼工序进行控制。
[0022]
该高碳铬轴承钢的成分包括:
[0023]
c:0.95~1.05%,si:0.15~0.35%,mn:0.25~0.45%,p≤0.020%,s≤0.005%,cu≤0.25%,ni≤0.10%,cr:1.35~1.65%,ti≤0.0025%,o≤0.0007%,余量为fe及不可避免的杂质。
[0024]
进一步地,冶炼工序包括:转炉出钢工序、精炼工序、rh真空脱气处理工序以及连铸工序。
[0025]
s1、转炉出钢工序。
[0026]
进一步地,在转炉出钢工序:根据终点碳含量,每炉钢水中加入300~500kg铝铁进行脱氧,然后进行合金化。最后每炉钢水中:加入300~500kg石灰、40~100kg萤石球、600~900kg炼钢合成渣造渣。每炉钢水重量为120~140吨。
[0027]
在该工序进行脱氧合金化,并快速造好炉渣,能够有效吸附脱氧过程产生的氧化物夹杂。
[0028]
进一步可选地,在转炉出钢工序:根据终点碳含量,每炉钢水中加入310~490kg铝铁进行脱氧,然后进行合金化。最后每炉钢水中:加入310~490kg石灰、45~95kg萤石球、610~980kg炼钢合成渣造渣。
[0029]
示例性地,在转炉出钢工序:根据终点碳含量,每炉钢水中加入320kg、340kg、360kg、380kg、400kg、420kg、450kg、470kg或者480kg铝铁进行脱氧,然后进行合金化。最后每炉钢水中:加入320kg、340kg、360kg、380kg、400kg、420kg、450kg、470kg或者480kg石灰;加入48kg、50kg、55kg、60kg、65kg、70kg、75kg、80kg、85kg、90kg或者95kg萤石球;加入
650kg、700kg、750kg、800kg、850kg、900kg或者950kg炼钢合成渣造渣。
[0030]
进一步可选地,上述进行合金化的步骤包括:加入碳粉、si铁、mn铁、cr铁等进行合金化。
[0031]
s2、精炼工序。
[0032]
进一步地,精炼炉座位后,一次性加入300~500kg石灰,根据成渣情况,加入20~80kg萤石球进行化渣。进一步可选地,前述石灰加入量为310~490kg;萤石球加入量25~75kg。示例性地,前述石灰加入量为350kg、380kg、400kg、450kg或者490kg;萤石球加入量为30kg、40kg、50kg、60kg或者70kg。
[0033]
进一步地,炉渣化开后,保持“白渣”时间20~40分钟。进一步可选地,为了保持“白渣”状态,可以加入40~100kg碳化硅。进一步可选地,碳化硅应小批量,多批次加入。碳化硅的加入量应该参考炉渣的流动性,如果流动性较差,可以加入80~100kg;如果流动性较好,可以加入40~60kg。
[0034]
进一步地,最终炉渣成分组成如下:cao:50~55%、sio2:7~9%、al2o3:25~35%;mgo:3~6%,其余成分为mno、tio2及fe。
[0035]
进一步地,最终炉渣的碱度6~8。进一步可选地,最终炉渣的碱度6.5~7.5。
[0036]
s3、rh真空脱气处理工序。
[0037]
进一步地,在rh真空脱气处理工序,真空处理时间为24~30分钟;复压后,对钢水进行底吹氩气操作,吹氩流量5~50nm3/h,吹氩时间30~45分钟。
[0038]
进一步可选地,在rh真空脱气处理工序,真空处理时间为25~29分钟;复压后,对钢水进行底吹氩气操作,吹氩流量6~45nm3/h,吹氩时间31~44分钟。进一步可选地,在rh真空脱气处理工序,真空处理时间为26~28分钟;复压后,对钢水进行底吹氩气操作,吹氩流量10~40nm3/h,吹氩时间32~43分钟。
[0039]
示例性地,在rh真空脱气处理工序,真空处理时间为26、27或者28分钟;复压后,对钢水进行底吹氩气操作,吹氩流量7nm3/h、10nm3/h、12nm3/h、15nm3/h、20nm3/h、25nm3/h、30nm3/h或者35nm3/h;吹氩时间32、35、38、40、42或者44分钟。
[0040]
通过对工序s1~s3进行控制,能够造还原性较好的炉渣,有效吸附去除钢水中夹杂物,从而能够从源头上改善轴承钢的纯净度。
[0041]
s4、连铸工序。
[0042]
进一步地,连铸工序,全程保护浇注。通过在连铸工序,全程保护浇注,能够有效地防止钢水二次氧化,产生新的夹杂物。
[0043]
进一步地,连铸结晶器浸入式水口采用整体式水口,对水口碗部、水口内壁以及塞棒头部单独或同时吹入氩气。
[0044]
发明人发现,夹杂物在连铸塞棒、水口处容易聚集,严重时产生剥落进入到最终产品,会导致最终钢产品中夹杂物过多、尺寸较大,不符合要求。本申请实施方式,通过使连铸结晶器浸入式水口采用整体式水口,对水口碗部、水口内壁以及塞棒头部单独或同时吹入氩气,能够有效地避免夹杂物在塞棒头部、水口内壁聚集、剥落,导致大尺寸夹杂物进入到最终的钢水的现象发生。
[0045]
本申请实施方式提供一种减少轴承钢中夹杂物的连铸吹氩控制方法,包括:连铸结晶器浸入式水口采用整体式水口,对水口碗部、水口内壁以及塞棒头部单独或同时吹入
氩气;
[0046]
其中,对水口碗部吹入的氩气流量根据结晶器浸入式水口内径进行调整;
[0047]
对水口内壁吹入的氩气流量根据结晶器浸入式水口内径、连铸坯横断面面积进行调整;
[0048]
对塞棒头部吹入的氩气流量根据塞棒头表面积进行调整。
[0049]
进一步地,在本申请一些实施方式中,水口碗部吹入的氩气流量与结晶器浸入式水口内径呈线性关系;
[0050]
塞棒头部吹入的氩气流量与塞棒头表面积呈线性关系;
[0051]
水口内壁吹入的氩气流量与结晶器浸入式水口内径和连铸坯横断面面积之间呈线性关系。
[0052]
进一步地,在本申请一些实施方式中,对水口碗部吹入的氩气流量按照公式(1)进行调整;
[0053]
l=2.5+k*πd
ꢀꢀꢀ
(1)
[0054]
式(1)中,l为氩气流量;d为结晶器浸入式水口内径,d的单位为mm;k为系数,k的取值范围在0.020~0.040,k的单位为l/min*mm。
[0055]
以往水口碗部吹氩流量控制大多采用经验方式控制在一定范围内,但是由于结晶器浸入式水口内径不同等因素,仅给出水口碗部吹氩流量控制范围,在轴承钢连铸过程中,人工调整会导致水口碗部处夹杂物的聚集无法杜绝,导致轴承钢大尺寸夹杂物控制的失败,或者吹氩流量太大,导致结晶器液位不稳定,带入外来夹杂物。后者经研究发现,水口碗部吹氩流量依据结晶器浸入式水口内径进行调整,能很好的控制轴承钢连铸过程中水口碗部夹杂物的聚集剥落,通过水口碗部吹氩流量公式,将吹氩流量与结晶器浸入式水口内径通过公式定量表征,定量控制和调整水口碗部吹氩流量,避免了人工经验范围调整导致轴承钢夹杂物控制失败,为吹氩流量精确控制提供了可操作易于实现的控制依据,减少了水口碗部夹杂物的聚集剥落,进一步减少了轴承钢内夹杂物的数量及尺寸,使轴承钢夹杂物控制到目标范围。
[0056]
进一步地,在本申请一些实施方式中,对水口内壁吹入的氩气流量按照公式(2)进行调整;
[0057]
l=1.8+k1*d+k2*s1ꢀꢀꢀ
(2)
[0058]
式(2)中,l为氩气流量;d为结晶器浸入式水口内径,d的单位为mm;s1为连铸坯横断面面积,s1的单位为m2;k1和k2为系数;k1的取值范围在:0.03~0.06,k1的单位为l/min*mm;k2的取值范围在:6~12,k2的单位为l/min*m2。
[0059]
以往水口内壁吹氩流量控制大多采用经验方式控制在一定范围内,但是由于结晶器浸入式水口内径不同、连铸坯横断面面积不同等因素,仅给出水口内壁吹氩流量控制范围,在轴承钢连铸过程中,人工调整会导致水口内壁处仍然产生夹杂物的聚集剥落,或者结晶器液位波动较大带入外来夹杂物,导致轴承钢夹杂物控制的失败。经研究发现,水口内壁吹氩流量依据结晶器浸入式水口内径、连铸坯横断面面积进行调整,能很好的控制轴承钢连铸过程中水口内壁处夹杂物的聚集剥落,通过水口内壁吹氩流量公式,将吹氩流量与结晶器浸入式水口内径、连铸坯横断面面积关系通过公式定量表征,定量控制和调整水口内壁吹氩流量,避免了人工经验范围调整导致轴承钢夹杂物控制失败,为吹氩流量精确控制
提供了可操作易于实现的控制依据,减少了水口内壁处产生的夹杂物聚集剥落,进一步减少了轴承钢内夹杂物的数量及尺寸,使轴承钢夹杂物控制到目标范围。
[0060]
进一步地,在本申请一些实施方式中,对塞棒头部吹入的氩气流量按照公式(3)进行调整;
[0061]
l=3.2+k*s2ꢀꢀꢀ
(3)
[0062]
式(3)中,l为氩气流量;s2为塞棒头表面积,s2的单位为mm2;k为系数,k的取值范围在0.0003~0.0008,k的单位为l/min*mm2。
[0063]
以往塞棒吹氩流量控制大多采用经验方式控制在一定范围内,但是由于塞棒头表面积不同等因素,仅给出塞棒吹氩流量控制范围,在轴承钢连铸过程中,会导致塞棒头处夹杂物聚集剥落,导致轴承钢夹杂物控制的失败,经研究发现,塞棒吹氩流量依据塞棒头表面积进行调整,能很好的控制轴承钢连铸过程中塞棒头部夹杂物产生聚集剥落,通过塞棒吹氩流量公式,将吹氩流量与塞棒头表面积通过公式定量表征,定量控制和调整塞棒吹氩流量,避免了人工经验范围调整导致轴承钢夹杂物控制失败,为吹氩流量精确控制提供了可操作易于实现的控制依据,减少了塞棒头处产生的夹杂物聚集剥落,进一步减少了轴承钢内夹杂物的数量及尺寸,使轴承钢夹杂物控制到目标范围。
[0064]
在本申请一些实施方式中,对水口碗部、水口内壁以及塞棒头部同时吹入氩气。示例性地:对水口碗部吹入的氩气流量按照前述的公式(1)进行调整;对水口内壁吹入的氩气流量按照前述的公式(2)进行调整;对塞棒头部吹入的氩气流量按照前述的公式(3)进行调整。
[0065]
在本申请一些实施方式中,对水口碗部、水口内壁以及塞棒头部中的任意两个吹入氩气。示例性地:对水口碗部吹入的氩气流量按照前述的公式(1)进行调整;同时,对水口内壁吹入的氩气流量按照前述的公式(2)进行调整。或者,对水口碗部吹入的氩气流量按照前述的公式(1)进行调整;同时,对塞棒头部吹入的氩气流量按照前述的公式(3)进行调整。或者,对水口内壁吹入的氩气流量按照前述的公式(2)进行调整。同时,对塞棒头部吹入的氩气流量按照前述的公式(3)进行调整。
[0066]
在本申请一些实施方式中,对水口碗部、水口内壁以及塞棒头部中的任意一个吹入氩气。示例性地:仅仅对水口碗部吹入的氩气流量按照前述的公式(1)进行调整;或者,仅仅对水口内壁吹入的氩气流量按照前述的公式(2)进行调整;或者,仅仅对塞棒头部吹入的氩气流量按照前述的公式(3)进行调整。
[0067]
进一步地,在水口碗部、水口内壁以及塞棒头部均开设透气孔。
[0068]
通过在水口碗部、水口内壁以及塞棒头部均开设透气孔,能够从该透气孔通入氩气。
[0069]
进一步地,透气孔的直径均在0.8~1.2mm范围内。
[0070]
进一步可选地,透气孔的直径均在0.9~1.1mm范围内。
[0071]
示例性地,透气孔的直径为0.95mm、1.0mm或者1.05mm。
[0072]
以下结合实施例对本申请的特征和性能作进一步的详细描述:
[0073]
实施例1
[0074]
提供一种轴承钢,钢的成分见表1。
[0075]
对冶炼工序进行控制:
[0076]
s1、转炉出钢,根据终点碳含量,加入al铁进行脱氧,随后加入碳粉、si铁、mn铁、cr铁等进行合金化。最后加入石灰、炼钢合成渣造渣。al铁、石灰、炼钢合成渣的加入量见表2。
[0077]
s2、lf炉精炼,一次性加入石灰。石灰的加入量、最终炉渣碱度见表2。
[0078]
s3、rh真空脱气处理,真空处理一段时间,复压后,对钢水进行底吹氩气操作。真空处理时间、吹氩时间、吹氩流量见表2。
[0079]
s4、连铸工序,全程保护浇注,连铸结晶器浸入式水口采用整体式水口,在塞棒头部开设1mm的透气孔,进行吹氩操作,吹氩流量见表2。
[0080]
s5、铸坯加热、轧制后生产出轴承圆钢产品。
[0081]
实施例2~6
[0082]
提供一种轴承钢,与实施例1基本相同,所不同之处在于钢的成分以及工艺参数,具体的见表1和表2。
[0083]
对比例1~6
[0084]
提供一种轴承钢,与实施例1基本相同,所不同之处在于钢的成分以及工艺参数,具体的见表1和表2。
[0085]
表1 钢的主要化学成分/%
[0086]
成分csimnpscunicrtio实施例11.000.250.350.0120.0010.020.041.480.00130.0004实施例21.000.250.350.0100.0020.020.021.490.00120.0005实施例31.010.240.350.0080.0020.020.051.480.00120.0004实施例40.980.250.350.0120.0010.020.011.480.00130.0004实施例51.000.250.350.0150.0020.020.011.490.00120.0006实施例60.970.240.340.0170.0020.020.011.480.00120.0004对比例10.980.240.370.0150.0020.020.041.470.00160.0006对比例20.990.240.360.010.0020.020.061.480.00140.0007对比例31.010.250.360.0110.0020.020.011.50.00160.0006对比例40.990.240.360.0120.0020.020.011.480.00150.0007对比例51.000.230.350.0180.0020.010.011.480.00190.0006对比例60.970.210.340.0090.0010.030.041.490.00170.0006
[0087]
表2 轴承钢冶炼工艺参数
[0088]
[0089][0090]
对实施例1~6以及对比例1~6提供的轴承钢的性能进行检测。
[0091]
对实施例1~6以及对比例1~6提供的轴承圆钢产品取样检测夹杂物控制情况。其中微观夹杂物采用gb/t 10561检测评级,要求a粗≤1.0、a细≤2.0;b粗≤0.5、b细≤1.0;c粗、c细:0;d粗≤0.5、d细≤1.0;ds≤0.5。宏观夹杂采用sep 1927第四等级进行检测,要求宏观夹杂物信号指示长度≤5mm。
[0092]
检测结果见表3。
[0093]
表3 夹杂物检测结果
[0094]
[0095][0096]
从上述表格可以看出,本申请实施例1~6提供的轴承钢的微观夹杂物较少,且没有宏观夹杂物。由此说明采用本申请实施例的方法能够有效减少轴承钢内夹杂物的数量及尺寸,使轴承钢夹杂物控制到目标范围。而对比例1~6提供的轴承钢,其微观夹杂物、宏观夹杂物均明显多于本申请实施例,无法使轴承钢夹杂物控制到目标范围。
[0097]
以上所述仅为本申请的优选实施例而已,并不用于限制本申请,对于本领域的技术人员来说,本申请可以有各种更改和变化。凡在本申请的精神和原则之内,所作的任何修改、等同替换、改进等,均应包含在本申请的保护范围之内。