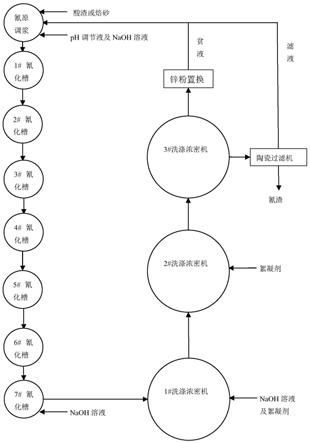
[0001]
本发明涉及一种黄铁矿烧渣氰化矿浆沉降方法,适于矿冶行业应用。
背景技术:[0002]
金银等贵金属常与黄铁矿共生,经浮选后形成以黄铁矿为主要成分的金精矿产品,这类矿石在直接氰化浸出时,大部分金粒被载体矿物所包裹,氰化物不能渗入固体内部与被包裹的金粒作用,因而氰化浸出率较低,为此需要在浸出前进行氧化脱硫预处理,以便嵌布于黄铁矿中的金银充分暴露,从而有利于后续浸出提取。焙烧氧化法是脱硫最为常见的预处理工艺,其处理量大、操作简单、投资成本低,且能产出硫酸副产品。焙烧后形成的烧渣细度与焙烧前的金精矿相当,-0.074mm比例可达90%以上,烧渣制成矿浆后常采用石灰或碳酸钠调节矿浆体系ph至9-11范围,再添加nacn浸出其中的金银,其反应原理为:
[0003]
4au+8nacn+2h2o+o2==4na[au(cn)2]+4naoh(银的浸出反应原理与此原理类似)
[0004]
此反应可将固体形式存在的金银浸出形成含金络合物进入溶液,从而实现金银的提取。为了进一步富集金银,对浸出后的矿浆进行有效沉降是必不可少的步骤,用以实现初步的固液分离,有效的沉降对确保金银回收率有重要作用。如果不能有效沉降分离,不仅影响金银络合物溶液后续正常置换,还将导致氰化矿浆浓密机“跑浑”。由于黄铁矿烧渣产物含有一定量的fe2(so4)3,fe2(so4)3在氰化工序碱性溶液条件环境下,其中的fe
3+
容易与oh-生成红棕色的fe(oh)3溶胶,溶胶将导致正常可以沉降的矿粉难以沉降。一般情况下,添加絮凝剂基本能够使这些少量的溶胶聚集为fe(oh)3沉淀,沉降效果一般可以满足生产需要,但是沉降不够彻底,特别是焙烧来料发生变化或粒级过细时,fe(oh)3溶胶生成过多,单纯采用絮凝剂无法使fe(oh)3溶胶全部沉降,然而导致浓密机“跑浑”。“跑浑”既影响氰化后液的循环使用,又会导致氰化工序的停机停产。为了实现较高的沉降效率,除了加大沉降水用量和延长沉降时间外,目前普遍采用添加聚丙烯酰胺为主要成分的絮凝剂来提升矿浆的沉降效率,但是依然起不到较好的沉降效果,特别是焙烧系统来料发生变化或焙烧进料原矿粒度变细时,经常导致浓密机“跑浑”,添加常规絮凝剂也起不到较理想的沉降作用,进而导致沉降工序停产停机并累及到其它工序无法正常运转。
[0005]
为此寻求一种黄铁矿烧渣氰化矿浆沉降方法就显得尤为迫切。
技术实现要素:[0006]
本发明的任务是为了克服现有工艺的不足,提供一种黄铁矿烧渣氰化矿浆沉降方法。
[0007]
本发明的任务是通过以下技术方案来完成的:
[0008]
本发明的一种黄铁矿烧渣氰化矿浆沉降方法,它包括调浆、氰化、沉降、过滤,它还包括采用naoh溶液+常规絮凝剂作为加速沉降的添加剂,能减少氰化矿浆跑浑。
[0009]
与现有技术相比,本发明具有以下优点和效果:
[0010]
(1)基于冶金物理化学原理,采用naoh溶液+絮凝剂作为加速沉降的添加剂,比单
纯使用絮凝剂有更好更快的沉降效果。
[0011]
(2)选择添加naoh,是基于其带负电的电解质溶液(oh-的负电效应),可以使过多的带正电的fe(oh)3溶胶聚结,颗粒变大转变为沉淀,从而加速沉降,同时矿粉也随之快速沉降,能解决洗涤浓密机“跑浑”现象,保证沉降工序正常进行,具有推广应用价值。
附图说明
[0012]
图1是根据本发明提出的一种黄铁矿烧渣氰化矿浆沉降方法氰化及沉降工序流程示意图。
[0013]
以下结合附图对说明作进一步详细地描述。
具体实施方式
[0014]
如图1所示,依据本发明提出的一种黄铁矿烧渣氰化矿浆沉降方法,它包括调浆、氰化、沉降、过滤,它还包括采用naoh溶液+絮凝剂作为加速沉降的添加剂,能减少氰化矿浆跑浑。
[0015]
本发明的工艺可以进一步是:
[0016]
在调浆步骤依然添加石灰或碳酸钠调节氰原的ph值,同时按0.1~0.5kg/m3用量加入naoh溶液,调节矿浆ph值至9~11,依次进行七道氰化。
[0017]
或者在第七道氰化完成后按0.1~0.5kg/m3添加naoh溶液,准备沉降。
[0018]
或者在氰化完成后进入三道沉降的第一道或第二道洗涤浓密机内按0.1~0.5kg/m3添加naoh溶液,同时按正常量添加絮凝剂。
[0019]
经三道沉降的底流入陶瓷过滤机过滤,得氰渣和滤液。
[0020]
经三道沉降的上清液经常规锌粉置换,得贫液。
[0021]
将滤液和贫液返回调浆循环使用。
[0022]
本申请文件中涉及的氰原为氰化前的矿浆,沉降的洗涤浓密机为矿浆沉降提供充足的空间,
[0023]
下面结合具体实施例对本发明具体实施方式进一步说明。
[0024]
实施例1
[0025]
某厂以焙烧-酸浸-氰化工艺提取金银,其中原料是以黄铁矿为主的混合矿源,原矿经焙烧-酸浸-固液分离工序后进入氰化调浆工序,按碳酸钠与烧碱的质量比例为1:0.1-0.2的溶质用量以及氰化后液以及一定量的清水为溶液配置ph值调节液,充分搅拌溶解后加入到氰化矿浆中调节ph值至9-11,后续再添加nacn溶液和鼓入压缩空气进行氰化浸出,氰化完成后在洗涤浓密机上方添加适量的絮凝剂,经过三道浓密机沉降,其底流浓度均达到60%-65%,上清液清澈透明,固含量少于0.1%,达到了较好的沉降分离效果,将底流过滤、上清液锌粉置换后的贫液和滤液返回调浆循环使用。
[0026]
使用该例的方案,浓密机无“跑浑”现象,可避免停机停产事故。
[0027]
实施例2
[0028]
某厂以焙烧-氰化工艺提取金银,其中原料以黄铁矿为主的单一矿源,原矿焙烧渣经过球磨机细末后,-0.074mm比例达90%以上,后续进入氰化调浆工序,ph值调节液为石灰溶液,调节ph值至9-11后进行氰化浸出,在最后一个氰化槽内添加0.1~0.5kg/m3的烧碱溶
液,同时在后续洗涤浓密机上方添加正常用量的絮凝剂,经过三道浓密机沉降,浓密机底流浓度60%-65%,浓密机上清液清澈透明,固含量少于0.2%,达到了较好的沉降分离效果,将底流过滤、上清液锌粉置换后的贫液和滤液返回调浆循环使用。
[0029]
使用该例的方案,浓密机无“跑浑”现象。
[0030]
实施例3
[0031]
某厂采用浮选铜精矿所得的硫铁精矿生产铁精粉和硫酸,硫铁精矿主要成分为黄铁矿,其中含有一定量的铜以及金银,铜采用烧渣酸浸-酸浸液萃取电积工艺回收,而金银采用酸浸渣氰化工艺进行回收。氰化前,氰原采用石灰溶液调节ph,因硫铁精矿-0.074mm比例达95%以上,氰化沉降工序采用常规絮凝剂沉降,浓密机经常“跑浑”,沉降效果不理想。在第一个浓密机上方按0.1~0.5kg/m3添加烧碱溶液,同时添加适当的絮凝剂进行沉降,浓密机上清液清澈透明,固含量少于0.2%,达到了较好的沉降分离效果,将底流过滤、上清液锌粉置换后的贫液和滤液返回调浆循环使用。
[0032]
使用该例的方案,尽管是矿粉较细的矿浆,浓密机仍无“跑浑”现象,达到了有效快速沉降的效果。
[0033]
上述实施例仅为本发明最佳的实施方式,但本发明的实施方式并不受上述实施例的限制,其他未背离本发明的精神实质与原理下所做的改变、修饰、替换、组合、简化,均应为等效的置换方式,都包含在本发明的保护范围内。