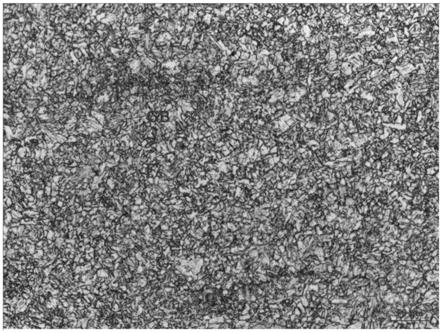
一种低温压力容器用07mnnimodr钢及其织构控制方法
技术领域
1.本发明涉及冶金领域一种钢板的生产工艺,具体涉及一种全厚度方向低温性能均匀的容器钢及其生产方法。
背景技术:2.低温压力容器用钢,涉及到液化石油气、液态石油、液氨、液氮等的开采与运输。随着石化工业的发展,新工艺、新设备不断出现,气体的液化、分离、贮运及应用在各国已普遍,这些低温技术和设备的开发促进了低温压力容器用钢的发展。随着工业发展需要,材料心部的低温韧性也逐渐变得重要。
3.07mnnimodr钢是gb19189-2011标准中的一种低温容器钢,具有良好的低温冲击韧性、强度和延伸率等性能指标,钢种采用低碳、低合金成分设计,一般采用调质热处理方式交货,生产成本低,但对韧性值的要求较高,-50℃冲击韧性值(kv2)要求80j以上,材料低温韧性的提高能使其在低温下仍然保持较高的韧性。
4.专利cn 103343298a 公开了一种低温容器用钢07mnnimodr的生产方法,按照其方法可以生产32mm厚度的钢板,但是该方法调质淬火温度900-920℃℃,且未公开相关性能数据,主要目的是生产出性能稳定、符合标准要求可供认证用的钢板,以杜绝皮下裂纹发生等。
5.专利cn 105543679a 公开了一种反应堆压力壳用调质板07mnnimodr厚板及其生产方法,其成分设计中含cr为0.3%,其生产钢板的厚度为60~80mm规格,未关注1/2厚度冲击韧性的提高。
6.专利cn109487041a 公开了一种高强调质压力容器07mnnimodr钢板及其生产方法,其生产钢板的厚度≤100mm,采用了常规“淬火+回火”热处理工艺,钢板强度和延伸率良好,但其钢板厚度1/2与钢板厚度1/4的冲击功相差略大。
7.专利cn107267857a公开了一种07mnnimodr钢板及其在线淬火生产方法,生产钢板厚度≤50mm,当厚度≤30mm时,板厚低温冲击韧性及均匀性较好,但其厚度在30~50mm之间的钢板厚度1/2与钢板厚度1/4的冲击功相差略大;同时,其成分设计增加了0.1~0.2%cr,且对在线淬火工艺和设备有较高的要求。
技术实现要素:8.现有的低温压力容器用07mnnimodr钢板,多采用“淬火+回火”工艺,但其1/2厚处冲击韧性较低,韧性均匀性比较差,钢板内部织构取向较为单一,其冲击断口形貌表现其断裂形式为准解理断裂。
9.本发明通过成分设计,采用控制轧制技术,选用较为合适的“亚温淬火+回火”工艺,在钢板强度不降低的条件下,得到内部织构取向较为随机化的钢板,在保证钢板强度、延伸率的情况下,提高了40~50mm厚07mnnimodr钢板的心部冲击韧性,钢板1/4厚处冲击韧性达到249.83j/cm2,1/2厚处冲击韧性达到231.66j/cm2。
10.本发明具体采用以下技术方案:一种低温压力容器用07mnnimodr钢板,其特征在于,钢板厚度40~50mm,钢板的化学成分按重量百分比计为:c ≤0.09,si 0.15~0.40,mn 1.20-1.60,p≤0.015,s≤0.005,ni 0.30~0.60,alt ≥0.02,mo 0.10~0.30,nb 0.025~0.030%,v 0.045~0.050%,ti 0.0025~0.0030%,ca 0.0015~0.0020%,其余为fe和残留元素。
11.上述低温压力容器用07mnnimodr钢板的织构控制方法,其特征在于采用320mm大断面铸坯、控轧轧制工艺、亚温淬火和回火工艺,具体包括如下步骤:(1)、炼钢工序:铁水预处理脱s、转炉深脱p、lf深脱s,超低as、sb、sn、pb、bi、b残余元素控制;采用动态轻压下、电磁搅拌技术,获得中心偏析c0.5、c1.0级的07mnnimodr钢铸坯;(2)、加热工序:铸坯入加热炉加热,加热系数≥10.0min/cm,加热温度1180~1220℃,保证铸坯加热均匀性;(3)、轧制工序:采用320mm大断面连铸坯,采用2阶段控轧工艺,第一阶段轧制温度在980~1150℃之间,第二阶段的开轧温度≤840℃;(4)、冷却工序:轧制后的钢板自然空冷,然后进行堆垛缓冷,堆垛时间72小时及以上;(5)、热处理工序:堆冷后的钢板进行准亚温淬火和回火处理,淬火加热温度ac3以下5~10℃,淬火加热和保温时间为1.8~2.3min/mm;回火加热温度550~650℃,回火加热和保温时间为2.5~3.5min/mm。
12.采用上述技术方案所产生的有益效果在于:本发明采用低合金成本设计,较少的锰、镍、钼成分,原料成本低。
13.采用320mm大断面铸坯,以较大的压缩比来提高钢板心部的致密性,从而提高钢板心部的低温冲击韧性。
14.采用控制轧制+轧后空冷堆垛技术,尽可能的提高轧态钢板的性能,同时保证钢板厚度方向的均匀性。
15.最终得到的钢板组织为“粒状贝氏体+少量块状铁素体”,粒状贝氏体保证了钢板的强度,块状铁素体则能提高钢板的韧性。经检测,钢板内部织构随机性较强,钢板1/4厚处冲击韧性达到249.83j/cm2,1/2厚处冲击韧性达到231.66j/cm2。冲击断口表现为韧窝和准解理断裂的复合形貌。07mnnimodr钢板市场需求量较大,经济效益好,预计吨钢毛利1300元/吨以上。
附图说明
16.图1为实施例1中48mm厚钢板的显微组织图(板厚1/2处);图2为实施例1中48mm厚钢板的ebsd取向分布图(板厚1/2处);图3为实施例2中48mm厚钢板的显微组织图(板厚1/2处);图4为实施例2中48mm厚钢板的ebsd取向分布图(板厚1/2处)。
具体实施方式
17.实施例1:
此07mnnimodr钢板厚度为48mm,采用下述成分配比以及生产方法。成分含量(wt)为:c:0.067%,si:0.211%,mn:1.508%,p:0.007%,s:0.0009%,ni:0.392%,al:0.036%,mo:0.270%,nb:0.029%,v:0.046%,ti:0.0029%,ca:0.0019%,其余为fe和残留元素。
18.本钢板的生产方法如下:(1)、炼钢工序:铁水预处理后s≤0.005%、转炉深脱p≤0.010%、lf深脱硫后s≤0.002%,超低as、sb、sn、pb、bi、b残余元素控制,冶炼采用成分合格铁水作为原材料,钢水冶炼过程添加合金避免残余元素增加。rh结束后钢液温度1515℃,至连铸中间包,钢液过热度控制在10~15℃,连铸采用动态轻压下、电磁搅拌技术,320mm厚铸坯中心偏析c0.5级。
19.(2)、加热工序:铸坯入加热炉加热,加热系数为10.2min/cm,加热温度1198℃,均热段保温61min;(3)、轧制工序:采用2阶段控轧工艺,第一阶段轧制终了温度1005℃,此阶段最后2道次压下量为32、29mm;第二阶段开轧温度为833℃,终轧温度为821℃。
20.(4)、冷却工序:轧制后的钢板自然空冷,堆垛温度530℃,堆垛时间74小时。
21.(5)、热处理工序:淬火加热温度860℃,淬火加热和保温时间为90min;回火加热温度620℃,回火加热和保温时间为125min。
22.本07mnnimodr钢坯轧成48mm钢板,其厚度1/2处显微组织如图1所示,1/2处ebsd取向分布图如图2所示。钢板组织均匀细小,组织类型为:粒状贝氏体+块状铁素体。1/2处织构随机性较强。力学性能为:屈服强度580mpa,抗拉强度650mpa,断后伸长22%,-50℃沿厚度方向各位置冲击韧性(1/4t、1/2t,t表示厚度):249.83j/cm2、231.66j/cm2。
23.实施例2:此07mnnimodr钢板厚度为48mm,采用下述成分配比以及生产方法。成分含量(wt)为:c:0.068%,si:0.212%,mn:1.509%,p:0.0076%,s:0.001%,ni:0.393%,al:0.037%,mo:0.271%,nb:0.030%,v:0.047%,ti:0.0029%,ca:0.002%,其余为fe和残留元素。
24.本钢板的生产方法如下:(1)、炼钢工序:铁水预处理后s≤0.005%、转炉深脱p≤0.010%、lf深脱硫后s≤0.002%,超低as、sb、sn、pb、bi、b残余元素控制,冶炼采用成分合格铁水作为原材料,钢水冶炼过程添加合金避免残余元素增加。rh结束后钢液温度1518℃,至连铸中间包,钢液过热度控制在10~13℃,连铸采用动态轻压下、电磁搅拌技术,320mm厚铸坯中心偏析c0.5级。
25.(2)、加热工序:铸坯入加热炉加热,加热系数10min/cm,加热温度1186℃,均热段保温65min;(3)、轧制工序:采用2阶段控轧工艺,第一阶段轧制终了温度1003℃,此阶段最后2道次压下量为32、29mm;第二阶段开轧温度为830℃,终轧温度为818℃。
26.(4)、冷却工序:轧制后的钢板自然空冷,堆垛温度528℃,堆垛时间72小时。
27.(5)、热处理工序:淬火加热温度860℃,淬火加热和保温时间为92min;回火加热温度610℃,回火加热和保温时间为121min。
28.本07mnnimodr钢坯轧成48mm钢板,其厚度1/2处显微组织如图3所示,1/2处ebsd取向分布图如图4所示。钢板组织均匀细小,组织类型为:粒状贝氏体+块状铁素体。1/2处织构随机性较强。力学性能为:屈服强度585mpa,抗拉强度663mpa,断后伸长22%,-50℃沿厚度方向各位置冲击韧性(1/4t、1/2t,t表示厚度):251.92j/cm2、240.37j/cm2。