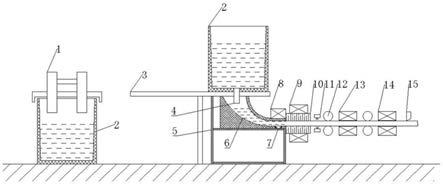
1.本发明涉及泡沫钢生产技术领域,尤其涉及一种泡沫钢的水平连铸系统及泡沫钢制备工艺。
背景技术:2.金属泡沫材料是一类密度极低的材料,其具备的相对质量小、比表面积高、比力学性能好、阻尼性能优良等特点,使其成为了一种新型的结构—功能一体化材料。由于泡沫金属同时兼备优异的物理、化学性能和功能与结构的双重属性,使其被广泛的应用于电化学、建筑、机械、冶金、环保、医学、原子能、交通运输、航空航天和石油化工等领域,同时也在涉及吸振、消声、过滤、分离、隔热阻火、热交换、电磁屏蔽、生物工程和催化剂反应工程等诸多领域有着较好的应用前景。
3.自1948年美国科学家sosnik通过气化熔融铝中添加汞制备出泡沫铝以来,材料研究者们对泡沫金属的制备工艺、结构性能及开发应用等方面做了一系列的研究工作。国外研究者们对泡沫金属的研究远早于国内,但主要围绕着泡沫铝的制备工艺进行研究。制备方法主要有粉末冶金法、电沉积法、金属沉积法以及熔体发泡法等。国内研究者们大约从20世纪80年代后期开始泡沫金属的研发,经过20多年的不懈努力,已经初步掌握部分泡沫金属的制备工艺。实验室开发成熟的泡沫金属主要有铝、镍、钛、锌等,但是泡沫金属的工业化和稳定生产仍是难点,尤其是钢质泡沫金属,尚处于实验室开发阶段。
4.公开号为cn101381822b的中国发明专利公开了一种“熔体发泡制备多孔泡沫钢的方法及其装置”。先将发泡剂平铺于坩埚底部,将不锈钢钢网罩在上面,以防止发泡剂上浮;然后将坩埚放入加热炉内加热至发泡剂开始分解温度以下50~100℃,将熔化后的钢水倒入坩埚内,利用保温加热装置将坩埚内钢水温度调节在发泡剂开始分解温度以上250~350℃范围之内,保温搅拌1~2min后,取出坩埚空冷至室温,得到多孔泡沫钢材料。该方法仅限于实验室开发,制得泡沫钢样品的尺寸较小,不利于推广到工业化生产。
5.公开号为cn101205576的中国专利申请公开了“一种通孔泡沫钢的制备方法”,采用熔点低于钢的不同直径的铜金属球烧结为前驱体,以钢为渗流体,通过压力渗流的方法渗入到前驱体中,冷却得到复合体,加热复合体使前驱体金属铜从复合体中熔除,得到通孔泡沫钢。该方法中熔除前驱体增加了工艺难度且无法判断铜前驱体是否还有残留,影响泡沫钢力学性能,且不利于工业化生产。
6.另外,由于气体在钢水中容易聚集上浮,在常规钢种冶炼中气体为钢中缺陷,因此目前还没有通过连铸制备泡沫钢的工艺。
技术实现要素:7.本发明提供了一种泡沫钢的水平连铸系统及泡沫钢制备工艺,能够实现孔隙率1%~90%泡沫钢制备,其工艺流程短,成材率高,生产效率高,可实现方坯和圆坯连铸;通过连铸生产的泡沫钢,金属框架强度高,可以满足后续深加工的要求。
8.为了达到上述目的,本发明采用以下技术方案实现:
9.一种泡沫钢的水平连铸系统,包括钢包、电极加热装置、水平连铸装置及电磁搅拌系统;所述水平连铸装置由钢包回转台、连铸中包、结晶器、二次冷却装置及牵引机构组成,钢包回转台设于连铸中包入口端的上方,用于放置钢包并带动钢包水平转动,浇铸前的钢包内设电极加热装置,钢包回转台上的钢包通过长水口与连铸中包相连;连铸中包置于基座上,其出口端的底部设供气元件,出口端与结晶器相连,沿连铸方向,结晶器的下游依次设二次冷却装置及牵引机构;所述电磁搅拌系统包括中包电磁搅拌装置、结晶器电磁搅拌装置、二冷区电磁搅拌装置及凝固末端电磁搅拌装置;所述中包电磁搅拌装置设于连铸中包出口端的顶部,所述结晶器电磁搅拌装置设于结晶器的外侧,所述二冷区电磁搅拌装置设于二次冷却装置下游的连铸坯移动路径外侧,所述凝固末端电磁搅拌装置设于牵引机构下游的连铸坯移动路径外侧;所述电磁搅拌系统设有水冷装置。
10.所述连铸中包由弧形段和水平段组成;其中靠近入口端为弧形段,靠近出口端为水平段;弧形段的入口在上并与钢包通过长水口相连,弧形段的出口在下并与水平段的入口相连,水平段的出口连接结晶器;供气元件设于水平段的底部;弧形段的入口截面积大于出口截面积。
11.一种泡沫钢的水平连铸系统,还包括切割装置,所述切割装置设于铸坯凝固末端电磁搅拌装置下游的连铸坯移动路径上。
12.一种基于所述系统的泡沫钢制备工艺,包括如下步骤:
13.步骤1:钢包、长水口、连铸中包、结晶器在投入使用前分别进行烘烤;将母材锭装入钢包中,吊至加热工位,采用电极加热装置升温至熔点温度以上,使母材锭完全融化至液态,添加覆盖剂防止氧化;
14.步骤2:将装有钢液的钢包吊至连铸工位,置于钢包回转台上;引入长水口开浇,钢液进入连铸中包;开浇过程采取保护浇注,添加中间包覆盖剂,氩气保护长水口;根据钢种的不同,钢液的过热度保持在15~55℃;
15.步骤3:开启电磁搅拌系统的水冷装置;
16.步骤4:开浇后,连铸达到稳态时,通过供气元件向连铸中包的水平段通入氩气,吹出直径为0.1~6mm的气泡;开启结晶器电磁搅拌装置,对连铸坯的气液混合区域进行电磁搅拌,促进气液混合并打碎体积较大的气泡;
17.步骤5:随着连铸坯的气液混合区域进入二冷区直至凝固末端,依次开启二冷区电磁搅拌装置及凝固末端电磁搅拌装置,促进气液混合及打碎体积较大的气泡;
18.连铸过程中,根据铸坯尺寸,设定拉速为10~200mm/min;铸坯下线后通过热处理、轧制及机械加工制成泡沫钢半成品及成品。
19.所述步骤1中,烘烤时间不少于3小时,烘烤温度大于800℃。
20.所述步骤4中,通入氩气的量为单位通钢量体积分数的1%~90%;氩气最大流量为400l/min,最大压力为0.35mpa。
21.所述步骤4中,结晶器电磁搅拌装置的最大电流为800a,最大频率为50hz且连续可调。
22.所述步骤5中,二冷区电磁搅拌装置及凝固末端电磁搅拌装置的最大电流均为800a,最大频率均为50hz且连续可调。
23.所述铸坯的断面尺寸为:方坯100
×
100mm以下,圆坯直径
24.所述母材为钢、生铁、铁合金、铸铁或其他铁基金属材料。
25.与现有技术相比,本发明的有益效果是:
26.1)实现了泡沫钢的连续生产,对于推进泡沫钢的工业化量产具有重大意义。
27.2)设计了适用泡沫钢生产的连铸中包,连铸中包由弧形段和水平段组成,弧形段的设计有利于钢液流动;水平段设置供气元件和中包电磁搅拌装置,由供气元件向钢液中提供弥散化气泡,气泡尺寸在0.1~6mm,氩气供气量占单位通钢量体积分数的1%~90%,使泡沫钢产品的孔隙率控制在1%~90%。
28.3)本发明为了实现气泡在钢中的弥散分布,在连铸中包、结晶器、二冷区及凝固末端位置分别添加多套电磁搅拌装置,电磁搅拌的优势是搅拌力直接作用于钢液内部,可保证供气元件产生的气泡与钢液充分混合,同时将大气泡打散或打碎,气泡在液芯处均匀分布,直至钢液凝固。
附图说明
29.图1是本发明所述一种制备泡沫钢的水平连铸系统的结构示意图。
30.图2是本发明所述连铸中包的结构示意图。
31.图中:1.电极加热装置 2.钢包 3.钢包回转台 4.长水口 5.基座 6.连铸中包 6.1弧形段 6.2水平段 7.供气元件 8.中包电磁搅拌装置 9.结晶器电磁搅拌装置 10.结晶器 11.二次冷却装置 12.牵引机构 13.二冷区电磁搅拌装置 14.凝固末端电磁搅拌装置 15.切割装置
具体实施方式
32.下面结合附图对本发明的具体实施方式作进一步说明:
33.如图1所示,本发明所述一种泡沫钢的水平连铸系统,包括钢包2、电极加热装置1、水平连铸装置及电磁搅拌系统;所述水平连铸装置由钢包回转台3、连铸中包6、结晶器10、二次冷却装置11及牵引机构12组成,钢包回转台3设于连铸中包6入口端的上方,用于放置钢包2并带动钢包2水平转动,浇铸前的钢包2内设电极加热装置1,钢包回转台3上的钢包2通过长水口4与连铸中包6相连;连铸中包6置于基座5上,其出口端的底部设供气元件7,出口端与结晶器10相连,沿连铸方向,结晶器10的下游依次设二次冷却装置11及牵引机构12;所述电磁搅拌系统包括中包电磁搅拌装置8、结晶器电磁搅拌装置9、二冷区电磁搅拌装置13及凝固末端电磁搅拌装置14;所述中包电磁搅拌装置8设于连铸中包6出口端的顶部,所述结晶器电磁搅拌装置9设于结晶器10的外侧,所述二冷区电磁搅拌装置13设于二次冷却装置11下游的连铸坯移动路径外侧,所述凝固末端电磁搅拌装置14设于牵引机构12下游的连铸坯移动路径外侧;所述电磁搅拌系统设有水冷装置。
34.所述连铸中包6由弧形段61和水平段62组成;其中靠近入口端为弧形段61,靠近出口端为水平段62;弧形段61的入口在上并与钢包2通过长水口4相连,弧形段61的出口在下并与水平段62的入口相连,水平段62的出口连接结晶器10;供气元件7设于水平段62的底部;弧形段61的入口截面积大于出口截面积。
35.一种泡沫钢的水平连铸系统,还包括切割装置15,所述切割装置15设于铸坯凝固
末端电磁搅拌装置14下游的连铸坯移动路径上。
36.一种基于所述系统的泡沫钢制备工艺,包括如下步骤:
37.步骤1:钢包2、长水口4、连铸中包6、结晶器10在投入使用前分别进行烘烤;将母材锭装入钢包2中,吊至加热工位,采用电极加热装置1升温至熔点温度以上,使母材锭完全融化至液态,添加覆盖剂防止氧化;
38.步骤2:将装有钢液的钢包2吊至连铸工位,置于钢包回转台3上;引入长水口4开浇,钢液进入连铸中包6;开浇过程采取保护浇注,添加中间包覆盖剂,氩气保护长水口4;根据钢种的不同,钢液的过热度保持在15~55℃;
39.步骤3:开启电磁搅拌系统的水冷装置;
40.步骤4:开浇后,连铸达到稳态时,通过供气元件7向连铸中包6的水平段62通入氩气,吹出直径为0.1~6mm的气泡;开启结晶器电磁搅拌装置9,对连铸坯的气液混合区域进行电磁搅拌,促进气液混合并打碎体积较大的气泡;
41.步骤5:随着连铸坯的气液混合区域进入二冷区直至凝固末端,依次开启二冷区电磁搅拌装置13及凝固末端电磁搅拌装置14,促进气液混合及打碎体积较大的气泡;
42.连铸过程中,根据铸坯尺寸,设定拉速为10~200mm/min;铸坯下线后通过热处理、轧制及机械加工制成泡沫钢半成品及成品。
43.所述步骤1中,烘烤时间不少于3小时,烘烤温度大于800℃。
44.所述步骤4中,通入氩气的量为单位通钢量体积分数的1%~90%;氩气最大流量为400l/min,最大压力为0.35mpa。
45.所述步骤4中,结晶器电磁搅拌装置9的最大电流为800a,最大频率为50hz且连续可调。
46.所述步骤5中,二冷区电磁搅拌装置13及凝固末端电磁搅拌装置14的最大电流均为800a,最大频率均为50hz且连续可调。
47.所述铸坯的断面尺寸为:方坯100
×
100mm以下,圆坯直径
48.所述母材为钢、生铁、铁合金、铸铁或其他铁基金属材料。
49.本发明中,所述电极加热装置用于融化铁基母材,加热温度为1500℃~1800℃;钢包用于存储熔化后的金属液,水平连铸装置用于铸坯的铸造成型。
50.二次冷却区可采用喷淋水雾化冷却、空冷及其它冷却方式。
51.本发明所述一种泡沫钢的水平连铸系统还包括气体保护装置,气体保护装置在各个设备的连接处施加气体保护,防止空气进入造成铸坯氧化。
52.以下实施例在以本发明技术方案为前提下进行实施,给出了详细的实施方式和具体的操作过程,但本发明的保护范围不限于下述的实施例。下述实施例中所用方法如无特别说明均为常规方法。
53.【实施例1】
54.本实施例中,采用的母材为45号钢(碳含量0.42%~0.50%,硅含量0.17%~0.37%,锰含量0.50%~0.80%,铬含量≤0.25%,镍含量≤0.30%),连铸生产80mm
×
80mm的泡沫钢方坯。具体过程如下:
55.将母材放入预热好的钢包内,吊至加热工位,电极加热装置升温至1650℃熔化钢包内的母材;将钢包吊至钢包回转台,接入长水口,开浇稳定后,供气元件开始供气,通气量
为单位通钢量体积分数的50%,氩气流量200l/min,压力0.2mpa,钢液过热度控制在15~20℃。依次打开中间包电磁搅拌装置、结晶器电磁搅拌装置、二冷区电磁搅拌装置、凝固末端电磁搅拌装置,各电磁搅拌装置的电流为500a,频率30hz连续可调,拉坯速度100mm/min。
56.本实施例所制备的泡沫钢方坯规格为80mm
×
80mm,孔隙率为48%,密度为4.08g/cm3。
57.【实施例2】
58.本实施例中,采用的母材为304不锈钢(碳含量≤0.08%,锰含量≤2.00%,硅含量≤1.00%,磷含量≤0.045%,硫含量≤0.030%,铬含量18.00%~20.00%,铌含量8.00%~11.00%),连铸生产100mm
×
100mm的泡沫钢方坯。具体过程如下:
59.将母材放入预热好的钢包内,吊至加热工位,电极加热装置升温至1620℃熔化钢包内的母材;将钢包吊至钢包回转台,接入长水口,开浇稳定后,供气元件开始供气,通气量为单位通钢量体积分数的60%,氩气流量230l/min,压力0.25mpa,钢液过热度控制在10~15℃。依次打开中间包电磁搅拌装置、结晶器电磁搅拌装置、二冷区电磁搅拌装置、凝固末端电磁搅拌装置,各电磁搅拌装置的电流为550a,频率40hz连续可调,拉坯速度80mm/min。
60.本实施例所制备的泡沫钢方坯规格为100mm
×
100mm,孔隙率为55%,密度为3.57g/cm3。
61.【实施例3】
62.本实施例中,采用的母材为超低碳钢(碳含量≤0.07%),连铸生产直径的泡沫钢圆坯。具体过程如下:
63.将母材放入预热好的钢包内,吊至加热工位,电极加热装置升温至1680℃熔化钢包内的母材;将钢包吊至钢包回转台,接入长水口,开浇稳定后,供气元件开始供气,通气量为单位通钢量体积分数的75%,氩气流量350l/min,压力0.3mpa,钢液过热度控制在15~20℃,依次打开中间包电磁搅拌装置、结晶器电磁搅拌装置、二冷区电磁搅拌装置、凝固末端电磁搅拌装置,各电磁搅拌装置的电流为500a,频率40hz连续可调,拉坯速度50mm/min。
64.本实施例所制备的泡沫钢圆坯规格为孔隙率为68%,密度为2.51g/cm3。
65.以上所述,仅为本发明较佳的具体实施方式,但本发明的保护范围并不局限于此,任何熟悉本技术领域的技术人员在本发明揭露的技术范围内,根据本发明的技术方案及其发明构思加以等同替换或改变,都应涵盖在本发明的保护范围之内。