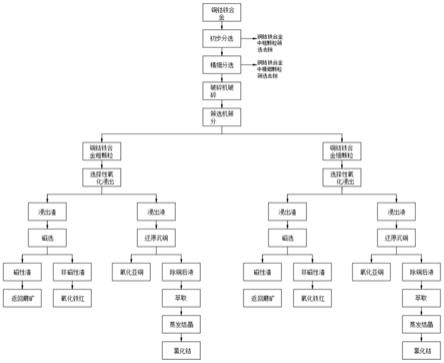
[0001]
本发明涉及有价金属回收技术领域,特别涉及一种铜钴铁合金综合回收有价金属的生产工艺。
背景技术:[0002]
随着世界经济的快速发展,特别是电池功能材料、超细粉体材料和超硬材料的迅猛发展,导致相关有色金属材料的消费量也在快速增长,特别是中国十分缺乏并且全球消费势头迅猛的钴资源,特别是现在民主刚果和赞比亚等国家严格限制钴矿的出口,改为出口初级钴产品,铜钴合金就是其中重要的一种,这一政策严重影响到国内厂家钴原料的来源,故就铜钴合金分离技术进行研究开发显得尤为重要,铜钴铁合金(俗称白合金)是目前刚果(金)钴铜矿石粗加工产品的主要形式之一,也是我国今后从非洲进口的主要钴原料之一,主要成份为铜、钴、铁、硅等元素,含量为铜(cu)10~45%、钴(co)8~35%、铁(fe)20~55%、硅(si)3~25%,其来源主要有两种:一种是铜冶炼过程中,转炉吹炼时得到的转炉渣,再经电炉还原熔炼水淬得到,另一种是熔炼氧化钴矿和钴精矿的富铜产品,铜钴铁合金自2003年来到中国后,因其硬度大、延展性好、耐腐蚀性强、难浸出的特点一直是困扰业界的难题;目前,在铜钴铁合金破碎前,未对铜钴铁合金进行预先筛选,铜钴铁合金中含有一些杂物,铜钴铁合金中的有价金属在回收过程中反应效率低,等待时间长,并且铜钴铁合金破碎后铜钴铁合金粗细颗粒与铜钴铁合金细颗粒混合,使得反应不够彻底的问题,进而使得产出的有价金属总量降低。
技术实现要素:[0003]
本发明的主要目的在于提供一种铜钴铁合金综合回收有价金属的生产工艺,可以有效解决背景技术中在铜钴铁合金破碎前,未对铜钴铁合金进行预先筛选,铜钴铁合金中含有一些杂物,铜钴铁合金中的有价金属在回收过程中反应效率低,等待时间长,并且铜钴铁合金破碎后铜钴铁合金粗细颗粒与铜钴铁合金细颗粒混合,使得反应不够彻底的问题,进而使得产出的有价金属总量降低的问题。
[0004]
为实现上述目的,本发明采取的技术方案为:
[0005]
一种铜钴铁合金综合回收有价金属的生产工艺,包括以下步骤:
[0006]
s1、初步筛选,首先,来到筛选机设备的前方,打开筛选机的装料斗,然后选择筛选网的孔径,从控制面板处开启筛选机,去除铜钴铁合金中大块的矿土或包装物等粗颗粒杂物;
[0007]
s2、精细分选,在步骤s1完成后,然后,来到筛选机设备的下料口处,使用装料筒进行装料,再次打开筛选机的装料斗,然后选择筛选网的孔径,从控制面板处开启筛选机,筛选去除铜钴铁合金中的粉尘等细颗粒杂物;
[0008]
s3、破碎并筛选分级,在步骤s2完成后,使用破碎机进行破碎工作,打开破碎机的进料斗门,然后把铜钴铁合金置入破碎机的进料斗中,从控制面板处开启破碎机进行破碎
工作,破碎后,对铜钴铁合金颗粒进行筛选分级,分为铜钴铁合金粗颗粒和铜钴铁合金细颗粒;
[0009]
s4、浸出,对铜钴铁合金粗颗粒和铜钴铁合金细颗粒进行分级筛选后,对铜钴铁合金粗颗粒和铜钴铁合金细颗粒分别置入两个浸出槽进行浸出工作,分别向铜钴铁合金粗颗粒和铜钴铁合金细颗粒中加水搅拌,然后分别向铜钴铁合金粗颗粒和铜钴铁合金细颗粒中加入所需理论量的氟离子,再分别向铜钴铁合金粗颗粒和铜钴铁合金细颗粒中加入无机酸,反应2小时后,再分别向铜钴铁合金粗颗粒和铜钴铁合金细颗粒中缓慢加入氧化剂溶液,最后向铜钴铁合金粗颗粒和铜钴铁合金细颗粒中加入氧化剂溶液后,继续保持温度大于100℃搅拌2小时后,对铜钴铁合金粗颗粒和铜钴铁合金细颗粒中的两个浸出槽中混合溶液进行固液分离;
[0010]
s5、萃取和蒸发结晶,对浸出渣和浸出液分别进行处理,浸出渣采用磁选的方式,磁性渣会返回磨矿,非磁性渣生成氯化铁红,而浸出液采用反应还原沉铜的方式,在第s4所得的滤液中,加还原剂,还原剂量用量为理论量的1.15倍,常温下搅拌,反应2小时后,过滤后得到氯化亚铜和萃前液,最后,将萃前液经过萃取后蒸发结晶,得到氯化钴。
[0011]
优先的,所述步骤s3中破碎机为重锤式破碎机。
[0012]
优先的,所述步骤s4的氟离子是指氢氟酸、氟化铵或氟化氢氨中的一种或几种。
[0013]
优先的,所述步骤s4中无机酸为浓硫酸、硫酸或工业盐酸,所述氧化剂为氯酸钠溶液。
[0014]
优先的,所述s4中浸出槽是由一个反应槽槽体,一个反应槽槽盖,反应槽槽体侧面外壁上的连接法兰构成,其中,反应槽槽盖上设有浸出后液输出连接法兰,并分别连接前液或前浆液管,蒸汽管,酸或碱管,所述步骤s5中还原剂为亚硫酸钠。
[0015]
与现有技术相比,本发明具有如下有益效果:在铜钴铁合金破碎前,对铜钴铁合金进行多次筛选,能够去除大块的矿土或包装物等粗颗粒杂物和去除铜钴铁合金中的粉尘等细颗粒杂物,杂物的去除能够提高反应效率,减少反应等待的时间,同时也提高了有价金属回收产品的质量,在铜钴铁合金破碎后,对铜钴铁合金粗颗粒和铜钴铁合金细颗粒进行分级筛选,之后对铜钴铁合金粗颗粒和铜钴铁合金细颗粒分别浸出处理,对铜钴铁合金粗颗粒和铜钴铁合金细颗粒分别处理,既能够节省整体回收处理的时间,也能够降低铜钴铁合金粗颗粒和铜钴铁合金细颗粒混合处理导致反应不够彻底的问题,进而使得产出的有价金属总量降低。
附图说明
[0016]
图1为本发明一种铜钴铁合金综合回收有价金属的生产工艺的工艺流程示意图。
具体实施方式
[0017]
为使本发明实现的技术手段、创作特征、达成目的与功效易于明白了解,下面结合具体实施方式,进一步阐述本发明。
[0018]
实施例1
[0019]
如图1所示的一种铜钴铁合金综合回收有价金属的生产工艺,包括以下步骤:
[0020]
s1、初步筛选,首先,来到筛选机设备的前方,打开筛选机的装料斗,然后选择筛选
网的孔径,从控制面板处开启筛选机,去除铜钴铁合金中大块的矿土或包装物等粗颗粒杂物;
[0021]
s2、精细分选,在步骤s1完成后,然后,来到筛选机设备的下料口处,使用装料筒进行装料,再次打开筛选机的装料斗,然后选择筛选网的孔径,从控制面板处开启筛选机,筛选去除铜钴铁合金中的粉尘等细颗粒杂物;
[0022]
s3、破碎并筛选分级,在步骤s2完成后,使用破碎机进行破碎工作,打开破碎机的进料斗门,然后把铜钴铁合金置入破碎机的进料斗中,从控制面板处开启破碎机进行破碎工作,破碎后,对铜钴铁合金颗粒进行筛选分级,分为铜钴铁合金粗颗粒和铜钴铁合金细颗粒;
[0023]
s4、浸出,对铜钴铁合金粗颗粒和铜钴铁合金细颗粒进行分级筛选后,对铜钴铁合金粗颗粒和铜钴铁合金细颗粒分别置入两个浸出槽进行浸出工作,分别向铜钴铁合金粗颗粒和铜钴铁合金细颗粒中加水搅拌,然后分别向铜钴铁合金粗颗粒和铜钴铁合金细颗粒中加入所需理论量的氟离子,再分别向铜钴铁合金粗颗粒和铜钴铁合金细颗粒中加入无机酸,反应2小时后,再分别向铜钴铁合金粗颗粒和铜钴铁合金细颗粒中缓慢加入氧化剂溶液,最后向铜钴铁合金粗颗粒和铜钴铁合金细颗粒中加入氧化剂溶液后,继续保持温度大于100℃搅拌2小时后,对铜钴铁合金粗颗粒和铜钴铁合金细颗粒中的两个浸出槽中混合溶液进行固液分离;
[0024]
s5、萃取和蒸发结晶,对浸出渣和浸出液分别进行处理,浸出渣采用磁选的方式,磁性渣会返回磨矿,非磁性渣生成氯化铁红,而浸出液采用反应还原沉铜的方式,在第s4所得的滤液中,加还原剂,还原剂量用量为理论量的1.15倍,常温下搅拌,反应2小时后,过滤后得到氯化亚铜和萃前液,最后,将萃前液经过萃取后蒸发结晶,得到氯化钴。
[0025]
其中,步骤s3中破碎机为重锤式破碎机;步骤s4的氟离子是指氢氟酸、氟化铵或氟化氢氨中的一种或几种;步骤s4中无机酸为浓硫酸、硫酸或工业盐酸,所述氧化剂为氯酸钠溶液;s4中浸出槽是由一个反应槽槽体,一个反应槽槽盖,反应槽槽体侧面外壁上的连接法兰构成,其中,反应槽槽盖上设有浸出后液输出连接法兰,并分别连接前液或前浆液管,蒸汽管,酸或碱管,所述步骤s5中还原剂为亚硫酸钠。
[0026]
需要说明的是,本发明为一种铜钴铁合金综合回收有价金属的生产工艺,在铜钴铁合金破碎前,需要对铜钴铁合金进行多次筛选,首先去除大块的矿土或包装物等粗颗粒杂物,再次精细的筛选,去除铜钴铁合金中的粉尘等细颗粒杂物,杂物的去除能够提高反应效率,减少反应等待的时间,同时也提高了有价金属回收产品的质量,在铜钴铁合金破碎后,对铜钴铁合金粗颗粒和铜钴铁合金细颗粒进行分级筛选,之后对铜钴铁合金粗颗粒和铜钴铁合金细颗粒分别置入浸出槽进行浸出处理,浸出槽是由一个反应槽槽体,一个反应槽槽盖,反应槽槽体侧面外壁上的连接法兰构成,其中,反应槽槽盖上设有浸出后液输出连接法兰,并分别连接前液或前浆液管,蒸汽管和酸或碱管,对铜钴铁合金粗颗粒和铜钴铁合金细颗粒分别处理,既能够节省整体回收处理的时间,也能够降低铜钴铁合金粗颗粒和铜钴铁合金细颗粒混合处理导致反应不够彻底的问题,进而使得产出的有价金属总量降低,浸出后会出现固液分离,对浸出渣和浸出液分别进行处理,浸出渣采用磁选的方式,磁性渣会返回磨矿,非磁性渣生成氯化铁红,而浸出液采用反应还原沉铜的方式,还原沉铜会产生氧化亚铜和除铜后的液体,对除铜后的液体进行萃取,萃取后进行蒸发结晶,之后会生成氯
化钴。
[0027]
显然,上述实施例仅仅是为清楚地说明所作的举例,而并非对实施方式的限定。对于所属领域的普通技术人员来说,在上述说明的基础上还可以做出其它不同形式的变化或变动。这里无需也无法对所有的实施方式予以穷举。而由此所引伸出的显而易见的变化或变动仍处于本发明创造的保护范围之中。