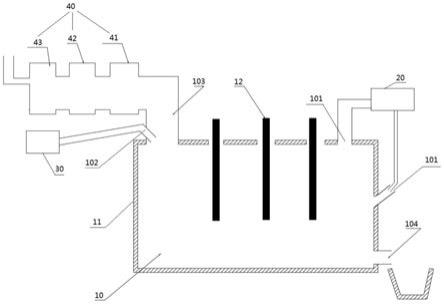
1.本发明涉及铅还原渣后处理领域,具体而言,涉及一种铅还原渣的处理方法及装置。
背景技术:2.目前,国内超过90%的铅冶炼厂采用底吹炼铅工艺,熔炼炉产出渣还原产出还原渣和粗铅,粗铅送去火法精炼,液态铅还原渣进入烟化炉处理回收其中锌铅等金属。
3.工业实践中,铅还原渣中锌含量为10%~20%、铅含量为1%~5%,现有烟化炉处理铅还原渣工艺由于其技术及装置条件的局限,处理后的渣含锌一般为1.5%~2.5%,渣含铅一般为0.3%~0.5%,尾渣中锌铅含量高,造成资源浪费。与此同时,烟化炉处理铅还原渣时由煤粉提供热源,煤粉喷吹造成大量气体进入,产生较多烟尘,使得锌烟尘品位降低。
4.cr(comprehensive recovery)技术是中国恩菲提出的火法处理技术,对应的处理装置为cr炉,目前已经应用于铜渣的处理中。cn108165755b提供了一种铜熔炼渣综合回收方法,采用cr炉处理铜渣,实现铜渣中有价金属的综合回收;cn208008863u提供了一种铜熔炼渣综合回收装置,其中处理炉采用cr炉。然而,尚未发现有关于cr炉处理铅还原渣的报道。
技术实现要素:5.本发明的主要目的在于提供一种铅还原渣的处理方法及装置,以解决现有技术中采用烟化炉处理铅还原渣时存在的尾渣中锌铅含量高、造成资源浪费的问题。
6.为了实现上述目的,根据本发明的一个方面,提供了一种铅还原渣的处理方法,其包括以下步骤:将铅还原渣和还原剂在cr炉中进行电热还原反应,得到含铅锌烟气;其中cr炉包括壳体和电极,壳体内部具有腔体,电极穿过壳体延伸至腔体中以进行供热,且电极延伸至腔体中的部分的体积占腔体总容积的1.5~5.5%;腔体为电热还原反应提供场所;回收含铅锌烟气中的铅锌,得到含铅锌烟尘。
7.进一步地,壳体顶部设置有铅还原渣进口,铅还原渣以液态热渣的形式通过铅还原渣进口进入腔体;优选地,壳体顶部设置有还原剂入口,处理方法还包括:通过还原剂入口向腔体中通入颗粒状的还原剂;和/或,壳体顶部和/或侧部设置有喂线孔,处理方法还包括:通过喂线孔向腔体中喂入碳粉线作为还原剂;和/或,壳体的顶部和/或侧部设置有第一喷枪,处理方法还包括:通过第一喷枪向腔体中喷吹粉末状的还原剂和/或喷吹还原性气体作为还原剂。
8.进一步地,颗粒状的还原剂包括粒径为0.5~5cm的第一碳质还原剂,其加入量为铅还原渣重量的1~15%;粉末状的还原剂为粒度高于200目粉末占比≥50wt%的第二碳质还原剂,且第二碳质还原剂中碳含量大于50wt%,灰分含量<25wt%,第二碳质还原剂的喷入量为铅还原渣重量的1~10%;优选地,第一碳质还原剂和第二碳质还原剂分别独立地选
自无烟煤、烟煤、褐煤、焦炭、石墨、木头中的一种或多种;优选地,还原性气体为天然气和/或液化石油气;优选地,在喷吹粉末状的还原剂和/或喷吹还原性气体的过程中,以氮气作为载体,并向电热还原反应的熔池中进行喷吹。
9.进一步地,壳体的顶部和/或侧部设置有2~15个第一喷枪,且第一喷枪的喷口位于熔池中;优选地,将第一喷枪的喷口距壳体内部底壁的高度记为s,将熔池表面距壳体内部底壁高度记为s,s/s=1/4~3/4;优选地,在喷吹粉末状的还原剂的过程中,粉剂浓度比为1~40kg/m3,更优选为20~30kg/m3。
10.进一步地,碳粉线包括芯层和壳层,壳层为0.1~0.5mm厚的铝皮或铁皮,芯层为碳质粉末;优选地,碳质粉末为烟煤、无烟煤、褐煤、石墨、焦炭粉末中的一种或多种;优选地,碳质粉末中碳含量为50~99wt%。
11.进一步地,喂入碳粉线作为还原剂的过程中,将喂入的碳粉线中的碳粉重量记为a,将铅还原渣中铅氧化物和锌氧化物被还原所需的理论配碳重量记为b,其中a/b=0.8~2.0;优选地,壳体顶部和/或侧部设置有喂线孔3~15个孔径为20~80mm的喂线孔,且喂入碳粉线的过程中,将碳粉线的线端置于在电热还原反应的熔池中;优选地,将壳体内部底壁距熔池表面的高度记为h,将碳粉线的线端距壳体内部底壁的高度记为h,h/h=1/10~1/2。
12.进一步地,电热还原反应过程,腔体中的温度为1200~1500℃,腔体中的功率密度为100kw/m2~250kw/m2;优选地,腔体中的温度为1350~1450℃,腔体中的功率密度为150kw/m2~200kw/m2。
13.进一步地,回收含铅锌烟气中的铅锌的步骤包括:将含铅锌烟气进行余热回,得到冷却烟气;对冷却烟气进行收尘,得到含铅锌烟尘和除尘烟气。
14.进一步地,铅还原渣中的锌含量为10~20wt%,铅含量为1~5wt%。
15.根据本发明的另一方面,还提供了一种铅还原渣的处理装置,其包括:cr炉,包括壳体和电极,壳体内部具有腔体,电极穿过壳体延伸至腔体中以进行供热,且电极延伸至腔体中的部分的体积占腔体总容积的1.5~5.5%;壳体还具有还原剂入口、铅还原渣入口和含铅锌烟气出口;cr炉用于使铅还原渣和还原剂进行电热还原反应以得到含铅锌烟气;还原剂供应装置,与还原剂入口相连;铅还原渣输送装置,与铅还原渣入口相连;以及含铅锌烟气处理装置,与含铅锌烟气出口相连,用于回收含铅锌烟气中的铅锌以得到含铅锌烟尘。
16.进一步地,铅还原渣输送装置为流槽或渣包。
17.进一步地,壳体的顶部设置有还原剂入口,用于向腔体中通入颗粒状的还原剂;和/或,壳体的顶部和/或侧部设置有喂线孔作为还原剂入口,用于向腔体中喂入碳粉线作为还原剂;和/或,壳体的顶部和/或侧部设置有第一喷孔,处理装置还包括第一喷枪,第一喷枪用于通过第一喷孔向腔体中喷吹粉末状的还原剂和/或喷吹还原性气体作为还原剂。
18.进一步地,处理装置包括2~15个第一喷枪,第一喷枪与第一喷孔一一对应设置,且第一喷枪的喷口延伸至腔体的熔池中。
19.进一步地,将第一喷枪的喷口距壳体内部底壁的高度记为s,将熔池表面距壳体内部底壁高度记为s,s/s=1/4~3/4。
20.进一步地,壳体的顶部和/或侧部设置有3~15个孔径为20~80mm的喂线孔。
21.进一步地,含铅锌烟气处理装置包括:余热回收单元,具有含铅锌烟气进口和冷却烟气出口,含铅锌烟气进口与含铅锌烟气出口相连;收尘装置单元,具有冷却烟气进口、含
铅锌烟尘出口和除尘烟气出口,冷却烟气进口与冷却烟气出口相连。
22.进一步地,含铅锌烟气处理装置还包括除尘烟气处理单元,除尘烟气处理单元与除尘烟气出口相连,除尘烟气处理单元用于对除尘烟气出口排出的除尘烟气进行脱硫处理。
23.进一步地,壳体的底部还设置有放渣口,用于排放电热还原反应中产出的尾渣。
24.本发明提供了一种铅还原渣的处理方法,其是利用cr炉处理铅还原渣,使其在还原剂和电极供热的作用下进行电热还原反应。使用该cr炉具有较高的功率密度,从而能够有效提高铅还原渣电热还原反应的深度,使其中的铅锌氧化物和其他有价金属氧化物尽可能被还原,铅锌升华进入烟气,经回收后形成含铅锌烟尘。采用本发明cr炉处理铅还原渣,能够明显提高铅锌的回收率,尾渣中的锌含量降至0.3%以下,铅含量降至0.1%以下,远低于现有工艺产出的弃渣中锌含量1.5%~2.5%,渣含铅0.3%~0.5%。与此同时,采用cr炉处理铅还原渣,烟气量、烟尘量均远小于传统的烟化炉工艺,产出的铅锌烟尘中锌品位较高,锌含量可达65%以上,甚至可达70%以上,远高于传统烟化炉工艺中的45~55%。
25.总之,通过上述处理方法,采用cr炉处理铅还原渣,能够实现铅还原渣中铅锌的全面深度回收,获得品位较高的锌铅烟尘,尾渣中的铅锌残留明显降低。
附图说明
26.构成本申请的一部分的说明书附图用来提供对本发明的进一步理解,本发明的示意性实施例及其说明用于解释本发明,并不构成对本发明的不当限定。在附图中:
27.图1示出了根据本发明一种实施例的铅还原渣的处理装置的结构示意图。
28.其中,上述附图包括以下附图标记:
29.10、cr炉;20、还原剂供应装置;30、铅还原渣输送装置;40、含铅锌烟气处理装置;11、壳体;12、电极;41、余热回收单元;42、收尘装置单元;43、除尘烟气处理单元;101、还原剂入口;102、铅还原渣入口;103、含铅锌烟气出口;104、放渣口。
具体实施方式
30.需要说明的是,在不冲突的情况下,本申请中的实施例及实施例中的特征可以相互组合。下面将参考附图并结合实施例来详细说明本发明。
31.正如背景技术部分所描述的,现有技术中采用烟化炉处理铅还原渣时存在尾渣中锌铅含量高、造成资源浪费的问题。
32.为了解决上述问题,本发明提供了一种铅还原渣的处理方法,其包括以下步骤:将铅还原渣和还原剂在cr炉中进行电热还原反应,得到含铅锌烟气;其中cr炉包括壳体和电极,壳体内部具有腔体,电极穿过壳体延伸至腔体中以进行供热,且电极延伸至腔体中的部分的体积占腔体总容积的1.5~5.5%;腔体为电热还原反应提供场所;回收含铅锌烟气中的铅锌,得到含铅锌烟尘。
33.本发明提供的铅还原渣的处理方法是利用cr炉处理铅还原渣,使其在还原剂和电极供热的作用下进行电热还原反应。使用该cr炉具有较高的功率密度,从而能够有效提高铅还原渣电热还原反应的深度,使其中的铅锌氧化物和其他有价金属氧化物尽可能被还原,铅锌升华进入烟气,经回收后形成含铅锌烟尘。采用本发明cr炉处理铅还原渣,能够明
显提高铅锌的回收率,尾渣中的锌含量降至0.3%以下,铅含量降至0.1%以下,远低于现有工艺产出的弃渣中锌含量1.5%~2.5%,渣含铅0.3%~0.5%。与此同时,采用cr炉处理铅还原渣,利用电极补热,烟气量、烟尘量均远小于传统的烟化炉工艺,产出的铅锌烟尘中锌品位较高,锌含量可达65%以上,甚至可达70%以上,远高于传统烟化炉工艺中的45~55%。
34.总之,通过上述处理方法,采用cr炉处理铅还原渣,能够实现铅还原渣中铅锌的全面深度回收,获得品位较高的锌铅烟尘,尾渣中的铅锌残留明显降低。此外,采用上述处理方法,除了可实现铅还原渣中锌铅等有价金属深度回收,投资小、占地面积小,烟气量小、烟气带走热损失少,因此在节约能源、保证生产率、降低投资和生产成本等方面也具有较大优势。
35.在一种优选的实施方式中,铅还原渣以液态热渣的形式通过铅还原渣进口进入腔体。铅冶炼过程中由还原炉产出的为液态热渣,具体操作过程中,可利用流槽或渣包将液态热渣转送至cr炉中,在cr炉内完成综合铅、锌等金属的深度回收。液态热渣携带的热量能够直接利用,使其更快速地进入反应程序。
36.上述还原剂的加入形式众多,优选地,可以通过以下方式中的一种或多种加入还原剂,具体如下:
37.(1)壳体顶部设置有还原剂入口,处理方法还包括:通过还原剂入口向腔体中通入颗粒状的还原剂。具体操作时,可以直接通过皮带机在壳体顶部还原剂入口加入颗粒状还原剂,操作简单。
38.(2)壳体顶部和/或侧部设置有喂线孔,处理方法还包括:通过喂线孔向腔体中喂入碳粉线作为还原剂。采用喂线方式加入还原剂,可以直接将碳粉线喂入壳体内部的反应熔池中,与熔池直接接触,发挥还原剂的功能,从而在较高的贫化动力学条件下铅还原渣中的铅锌氧化物还原为铅锌单质,使其升华进入烟气。相比于壳体顶部加入颗粒状还原剂的形式,采用喂线的形式能够进一步提高反应效率。
39.(3)壳体的顶部和/或侧部设置有第一喷枪,处理方法还包括:通过第一喷枪向腔体中喷吹粉末状的还原剂和/或喷吹还原性气体作为还原剂。利用这种喷吹形式喷入粉末状还原剂或还原性气体,也能够增大还原剂与熔渣的接触面积,促进反应的进行。
40.为了进一步提高反应效率,进而提高铅锌回收率,同时提高烟尘中的铅锌品位,在一种优选的实施方式中,颗粒状的还原剂包括粒径为0.5~5cm的第一碳质还原剂,其加入量为铅还原渣重量的1~15%;粉末状的还原剂为粒度高于200目粉末占比≥50wt%的第二碳质还原剂,且第二碳质还原剂中碳含量大于50wt%,灰分含量<25wt%,第二碳质还原剂的喷入量为铅还原渣重量的1~10%。优选地,第一碳质还原剂和第二碳质还原剂分别独立地选自无烟煤、烟煤、褐煤、焦炭、石墨、木头中的一种或多种;优选地,还原性气体为天然气和/或液化石油气。
41.优选地,在喷吹粉末状的还原剂和/或喷吹还原性气体的过程中,以氮气作为载体,并向电热还原反应的熔池中进行喷吹。以氮气作为载体,除了进一步增加粉末状还原剂和还原性气体与熔渣的接触面积,另还起到了搅拌熔池的作用,有利于提高反应动力学条件,促进铅锌等物质的挥发,并提高反应效率。
42.在一种优选的实施方式中,壳体的顶部和/或侧部设置有2~15个第一喷枪,且第
一喷枪的喷口位于熔池中;优选地,将第一喷枪的喷口距壳体内部底壁的高度记为s,将熔池表面距壳体内部底壁高度记为s,s/s=1/4~3/4。将喷口位置控制在上述位置,有利于进一步提高反应效率,相应提高铅锌的回收率。以喷吹形式加入还原剂时,喷吹方式优选采用浓相输送,在喷吹粉末状的还原剂的过程中,粉剂浓度比为1~40kg/m3,更优选为20~30kg/m3(喷粉时,每立方米载气携带的粉重量)。粉末状碳质还原剂进入熔池后与锌铅等氧化物反应,生成co、co2气体,将以铅锌等氧化物还原成金属挥发;惰性气体和生成的co、co2气体由熔体逸出过程中,对熔体进行搅拌,优选促进还原反应的进行,铅还原渣在炉中还原及保温沉降时间0.5h~4h。
43.在一种优选的实施方式中,碳粉线包括芯层和壳层,壳层为0.1~0.5mm厚的铝皮或铁皮,芯层为碳质粉末。碳粉线进入熔池后,铝皮或铁皮高温熔化或与其他金属氧化物反应氧化后溶于渣中,碳质粉末进入熔池后与铅锌氧化物反应,生成co、co2气体,将以氧化物状态存在的铅锌等金属被还原成金属态,其中铅锌挥发至烟尘中;气体由熔池逸出过程中,对熔池进行搅拌,促进铅锌的挥发,促进还原反应的进行。优选地,碳质粉末为烟煤、无烟煤、褐煤、石墨、焦炭粉末中的一种或多种;优选地,碳质粉末中碳含量为50~99wt%。
44.为了进一步提高渣中铅锌的还原效率,在一种优选的实施方式中,喂入碳粉线作为还原剂的过程中,将喂入的碳粉线中的碳粉重量记为a,将铅还原渣中铜氧化物、铅氧化物和锌氧化物被还原所需的理论配碳重量记为b,其中a/b=0.8~2.0。此处“铜氧化物、铅氧化物和锌氧化物被还原所需的理论配碳重量”是指将这些氧化物还原为金属单质所需的理论碳量。优选地,壳体顶部和/或侧部设置有喂线孔3~15个孔径为20~80mm的喂线孔,且喂入碳粉线的过程中,将碳粉线的线端置于在电热还原反应的熔池中;优选地,将壳体内部底壁距熔池表面的高度记为h,将碳粉线的线端距壳体内部底壁的高度记为h,h/h=1/10~1/2。这样,一方面碳粉线与熔池的接触更为充分,反应条件更佳,另一方面熔池中部的除铅锌以外的金属氧化物完成还原反应之后,可以通过沉降作用进入熔池底部,形成较为稳定的锍层,方便排出。实际操作过程中,上述电热还原反应及保温沉降时间为1~3h。
45.在一种优选的实施方式中,电热还原反应过程,腔体中的温度为1200~1500℃,腔体中的功率密度为100kw/m2~250kw/m2;优选地,腔体中的温度为1350~1450℃,腔体中的功率密度为150kw/m2~200kw/m2。该功率密度和操作温度下,铅还原渣中的铅锌氧化物能够更充分地被还原,从而有利于进一步提高铅锌的回收率。
46.在得到含铅锌烟气后,优选回收含铅锌烟气中的铅锌的步骤包括:将含铅锌烟气进行余热回收(以使其中的铅锌凝固),得到冷却烟气;对冷却烟气进行收尘,得到含铅锌烟尘和除尘烟气。反应过程中产出的尾渣由cr炉排出(可先用接受单元将尾渣接受,冷却),为一般固废。
47.利用本发明提供的上述处理方法处理铅还原渣,能够实现渣含锌降至0.3%以下,渣含铅降至0.1%,锌挥发率超过95%,铅回收率超过90%,得到高品位锌烟尘。优选地,铅还原渣中的锌含量为10~20wt%,铅含量为1~5wt%。
48.根据本发明的另一方面,还提供了一种铅还原渣的处理装置,如图1所示,该装置包括cr炉10、还原剂供应装置20、铅还原渣输送装置30和含铅锌烟气处理装置40;cr炉10包括壳体11和电极12,壳体11内部具有腔体,电极12穿过壳体11延伸至腔体中以进行供热,且电极12延伸至腔体中的部分的体积占腔体总容积的1.5~5.5%;壳体11还具有还原剂入口
101、铅还原渣入口102和含铅锌烟气出口103;cr炉10用于使铅还原渣和还原剂进行电热还原反应以得到含铅锌烟气;还原剂供应装置20与还原剂入口101相连;铅还原渣输送装置30与铅还原渣入口102相连;含铅锌烟气处理装置40与含铅锌烟气出口103相连,用于回收含铅锌烟气中的铅锌以得到含铅锌烟尘。
49.采用上述装置处理铅还原渣,使其在cr炉中和还原剂和电极供热的作用下进行电热还原反应。使用该cr炉具有较高的功率密度,从而能够有效提高铅还原渣电热还原反应的深度,使其中的铅锌氧化物和其他有价金属氧化物尽可能被还原,铅锌升华进入烟气,经回收后形成含铅锌烟尘。采用本发明cr炉处理铅还原渣,能够明显提高铅锌的回收率,尾渣中的锌含量降至0.3%以下,铅含量降至0.1%以下,远低于现有工艺产出的弃渣中锌含量1.5%~2%,渣含铅0.3%~0.5%。与此同时,采用cr炉处理铅还原渣,利用电极补热,烟气量、烟尘量均远小于传统的烟化炉工艺,产出的铅锌烟尘中锌品位较高,锌含量可达65%以上,甚至可达70%以上,远高于传统烟化炉工艺中的45~55%。
50.总之,通过上述处理装置,采用cr炉处理铅还原渣,能够实现铅还原渣中铅锌的全面深度回收,获得品位较高的锌铅烟尘,尾渣中的铅锌残留明显降低。此外,采用上述处理方法,除了可实现铅还原渣中锌铅等有价金属深度回收,投资小、占地面积小,烟气量小、烟气带走热损失少,因此在节约能源、保证生产率、降低投资和生产成本等方面也具有较大优势。
51.在一种优选的实施方式中,铅还原渣输送装置30为流槽或渣包。铅冶炼过程中由还原炉产出的为液态热渣,具体操作过程中,可利用流槽或渣包将液态热渣转送至cr炉中,在cr炉内完成综合铅、锌等金属的深度回收。液态热渣携带的热量能够直接利用,使其更快速地进入反应程序。
52.上述还原剂的加入形式众多,优选地,可以通过以下方式中的一种或多种加入还原剂,具体如下:
53.(1)壳体11的顶部设置有还原剂入口101,用于向腔体中通入颗粒状的还原剂;具体操作时,可以直接通过皮带机在壳体顶部还原剂入口加入颗粒状还原剂,操作简单。
54.(2)壳体11的顶部和/或侧部设置有喂线孔作为还原剂入口101,用于向腔体中喂入碳粉线作为还原剂。采用喂线方式加入还原剂,可以直接将碳粉线喂入壳体内部的反应熔池中,与熔池直接接触,发挥还原剂的功能,从而在较高的贫化动力学条件下铅还原渣中的铅锌氧化物还原为铅锌单质,使其升华进入烟气。相比于壳体顶部加入颗粒状还原剂的形式,采用喂线的形式能够进一步提高反应效率。
55.(3)壳体11的顶部和/或侧部设置有第一喷孔,处理装置还包括第一喷枪,第一喷枪用于通过第一喷孔向腔体中喷吹粉末状的还原剂和/或喷吹还原性气体作为还原剂。利用这种喷吹形式喷入粉末状还原剂或还原性气体,也能够增大还原剂与熔渣的接触面积,促进反应的进行。
56.优选地,处理装置包括2~15个第一喷枪,第一喷枪与第一喷孔一一对应设置,且第一喷枪的喷口延伸至腔体的熔池中。更优选地,将第一喷枪的喷口距壳体内部底壁的高度记为s,将熔池表面距壳体内部底壁高度记为s,s/s=1/4~3/4。将喷口位置控制在上述位置,有利于进一步提高反应效率,相应提高铅锌的回收率。在一种优选的实施方式中,壳体11的顶部和/或侧部设置有3~15个孔径为20~80mm的喂线孔。
57.在一种优选的实施方式中,如图1所示,含铅锌烟气处理装置40包括:余热回收单元41,具有含铅锌烟气进口和冷却烟气出口,含铅锌烟气进口与含铅锌烟气出口103相连;收尘装置单元42,具有冷却烟气进口、含铅锌烟尘出口和除尘烟气出口,冷却烟气进口与冷却烟气出口相连。这样,可以先将含铅锌烟气进行余热回收,以使其中的铅锌凝固,得到冷却烟气;对冷却烟气进行收尘,得到含铅锌烟尘和除尘烟气。反应过程中产出的尾渣有cr炉排出,该熔炼渣为一般固废。
58.优选地,含铅锌烟气处理装置40还包括除尘烟气处理单元43,除尘烟气处理单元43与除尘烟气出口相连,除尘烟气处理单元43用于对除尘烟气出口排出的除尘烟气进行脱硫处理。经脱硫处理后,净化烟气排空即可。
59.优选地,壳体11的底部还设置有放渣口104,用于排放电热还原反应中产出的尾渣。
60.以下结合具体实施例对本申请作进一步详细描述,这些实施例不能理解为限制本申请所要求保护的范围。
61.实施例1
62.采用图1所示处理装置,cr炉包括壳体和电极,壳体内部具有腔体,电极穿过壳体延伸至腔体中以进行供热,且电极延伸至腔体中的部分的体积占腔体总容积的5.5%。还原剂加入方式采用壳体顶部还原剂入口直接加入的方式,通过皮带机向腔体中通入颗粒状的还原剂。壳体侧部熔池上方设置有漏风口。
63.采用流槽将铅还原渣以的液态热渣的形式加入cr炉内,5~30mm的褐煤颗粒通过皮带机输送至腔体中,加入量为铅还原渣的6%,提升炉内渣的温度至1460℃,腔体中的功率密度为210kw/m2,进行电热还原反应,形成含铅锌烟气。
64.含铅锌烟气经余热回收后,铅锌凝固,形成冷却烟气。冷却烟气经收尘后,得到含铅锌烟尘和除尘烟气。除尘烟气经脱硫后排放,cr炉中的尾渣排放。
65.处理结果:年处理37万吨铅精矿,精矿含铅35%,含锌11%;经过熔炼、还原产出铅还原渣25万吨,含锌21%,含铅2.3%;铅还原渣经cr炉处理后,渣含锌0.15%,渣含铅0.1%,产出的锌烟尘中锌含量约69%、铅含量约9%。cr炉处理装置锌回收率约99.7%,铅回收率约95.8%。
66.实施例2
67.采用图1所示处理装置,cr炉包括壳体和电极,壳体内部具有腔体,电极穿过壳体延伸至腔体中以进行供热,且电极延伸至腔体中的部分的体积占腔体总容积的5.5%。还原剂加入方式采用喂线方式,壳体顶部和侧部设置有15个孔径为20mm的喂线孔,碳粉线为0.1mm厚的铝皮包裹的焦炭粉末,碳含量为99wt%。壳体侧部熔池上方设置有漏风口。
68.采用流槽将铅还原渣以的液态热渣的形式加入cr炉内,碳粉线喂入腔体,提升炉内渣的温度至1470℃,腔体中的功率密度为220kw/m2,进行电热还原反应,形成含铅锌烟气;喂入碳粉线,其中碳粉线中焦炭粉末的加入重量记为a,将铅还原渣中铜氧化物、铅氧化物和锌氧化物被还原所需的理论配碳重量记为b,其中a/b=1.2。将壳体内部底壁距熔池表面的高度记为h,将碳粉线的线端距壳体内部底壁的高度记为h,h/h=1/10。
69.含铅锌烟气经余热回收后,铅锌凝固,形成冷却烟气。冷却烟气经收尘后,得到含铅锌烟尘和除尘烟气。除尘烟气经脱硫后排放,cr炉中的尾渣排放。
70.处理结果:年处理50万吨铅精矿,精矿含铅40%,含锌8%;经过熔炼、还原产出铅还原渣35万吨,含锌18%,含铅1.9%;铅还原渣经cr炉处理后,渣含锌0.12%,渣含铅0.08%,产出的锌烟尘中锌含量约68%、铅含量约10%。cr炉处理装置锌回收率约99.1%,铅回收率约96.8%。
71.实施例3
72.采用图1所示处理装置,cr炉包括壳体和电极,壳体内部具有腔体,电极穿过壳体延伸至腔体中以进行供热,且电极延伸至腔体中的部分的体积占腔体总容积的5.5%。还原剂加入方式采用壳体顶部和侧部喷枪的喷入形式,顶部设置一根喷枪,侧部两根喷枪,用于以氮气为载体喷入粉末状还原剂。壳体侧部熔池上方设置有空气喷枪,用于向熔池上方喷入空气。
73.采用流槽将铅还原渣以的液态热渣的形式加入cr炉内,粉末状的还原剂为粒度高于200目粉末占比≥50wt%的焦粉,加入量为铅还原渣的5%,喷入的粉剂浓度为25kg/m3。提升炉内渣的温度至1480℃,腔体中的功率密度为240kw/m2,进行电热还原反应,形成含铅锌烟气。
74.含铅锌烟气经余热回收后,铅锌凝固,形成冷却烟气。冷却烟气经收尘后,得到含铅锌烟尘和除尘烟气。除尘烟气经脱硫后排放,cr炉中的尾渣排放。
75.处理结果:年处理50万吨铅精矿,精矿含铅38%,含锌9.5%;经过熔炼、还原产出铅还原渣34.5万吨,含锌20%,含铅2.3%;铅还原渣经cr炉处理后,渣含锌0.10%,渣含铅0.06%,产出的锌烟尘中锌含量约67%、铅含量约9%。
76.实施例4
77.采用图1所示处理装置,cr炉包括壳体和电极,壳体内部具有腔体,电极穿过壳体延伸至腔体中以进行供热,且电极延伸至腔体中的部分的体积占腔体总容积的5.5%。还原剂加入方式采用喂线方式,壳体顶部和侧部设置有10个孔径为20mm的喂线孔,碳粉线为0.1mm厚的铝皮包裹的焦炭粉末,碳含量为85wt%。壳体侧部熔池上方设置有漏风口。
78.采用流槽将铅还原渣以的液态热渣的形式加入cr炉内,碳粉线喂入腔体,提升炉内渣的温度至1350℃,腔体中的功率密度为180kw/m2,进行电热还原反应,形成含铅锌烟气;喂入碳粉线,其中碳粉线中焦炭粉末的加入重量记为a,将铅还原渣中铜氧化物、铅氧化物和锌氧化物被还原所需的理论配碳重量记为b,其中a/b=1.2。将壳体内部底壁距熔池表面的高度记为h,将碳粉线的线端距壳体内部底壁的高度记为h,h/h=1/5。
79.含铅锌烟气经余热回收后,铅锌凝固,形成冷却烟气。冷却烟气经收尘后,得到含铅锌烟尘和除尘烟气。除尘烟气经脱硫后排放,cr炉中的尾渣排放。
80.处理结果:年处理30万吨铅精矿,精矿含铅42%,含锌9%;经过熔炼、还原产出铅还原渣20.7万吨,含锌16%,含铅1.5%;铅还原渣经cr炉处理后,渣含锌0.26%,渣含铅0.12%,产出的锌烟尘中锌含量约67%、铅含量约9%。cr炉处理装置锌回收率约98.2%,铅回收率约95.3%。
81.实施例5
82.采用图1所示处理装置,cr炉包括壳体和电极,壳体内部具有腔体,电极穿过壳体延伸至腔体中以进行供热,且电极延伸至腔体中的部分的体积占腔体总容积的5.2%。还原剂加入方式采用壳体顶部和侧部喷枪的喷入形式,顶部设置一根喷枪,侧部两根喷枪,用于
以氮气为载体喷入粉末状还原剂。壳体侧部熔池上方设置有空气喷枪,用于向熔池上方喷入空气。
83.采用流槽将铅还原渣以的液态热渣的形式加入cr炉内,粉末状的还原剂为粒度高于200目粉末占比≥50wt%的焦粉,加入量为铅还原渣的4.5%,喷入的粉剂浓度为18kg/m3。提升炉内渣的温度至1380℃,腔体中的功率密度为190kw/m2,进行电热还原反应,形成含铅锌烟气。
84.含铅锌烟气经余热回收后,铅锌凝固,形成冷却烟气。冷却烟气经收尘后,得到含铅锌烟尘和除尘烟气。除尘烟气经脱硫后排放,cr炉中的尾渣排放。
85.处理结果:年处理40万吨铅精矿,精矿含铅38%,含锌9.5%;经过熔炼、还原产出铅还原渣27.6万吨,含锌21%,含铅1.8%;铅还原渣经cr炉处理后,渣含锌0.29%,渣含铅0.16%,产出的锌烟尘中锌含量约64%、铅含量约8%。
86.以上所述仅为本发明的优选实施例而已,并不用于限制本发明,对于本领域的技术人员来说,本发明可以有各种更改和变化。凡在本发明的精神和原则之内,所作的任何修改、等同替换、改进等,均应包含在本发明的保护范围之内。