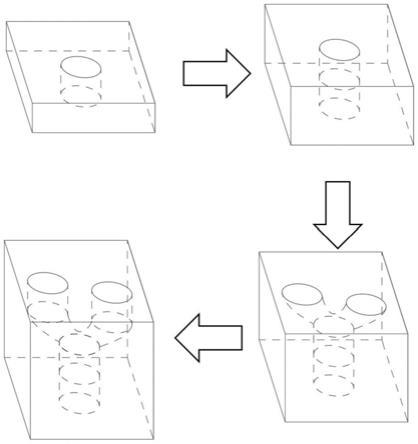
1.本发明属于金属熔丝增减材制造内流道成形领域,具体涉及一种基于金属熔丝增减材的内流道无支撑成形方法。
背景技术:2.增材制造可以快速得到结构较为复杂的结构,然而其几何尺寸以及表面形貌并不符合实际的生产需求,特别是在航空领域中。减材制造应用较早且其加工机制较为成熟,可以将精度控制在微米级别,因此集增材制造和减材制造优点于一身的增减材制造应运而生。将增材制造与传统的加工工艺结合起来,既可以加工结构较为复杂的零件,又可以保持其精度。然而对于复杂内流道的零件,当其性能需求不高的时候,往往采用铸造工艺。然而铸造工艺需要制作模具,制造工期较长,且其表面精度往往并不是特别高,容易存在夹杂等缺陷,只适合于大批量生产。已有的内流道增减材制造方法大多采用了支撑,然后此类工艺存在一个问题,那就是支撑制作周期太长,表面精度不高,且后期完全去除支撑的难度较大。
3.目前对于无支撑的内流道加工工艺的专利较少,专利《一种基于选区激光熔化与电解加工的孔道构件制造方法》(申请号:202010319193.2)公开了一种利用激光选区熔化技术与电解加工相结合的方法,此种方法只适合于简单的小构件,对于大型构件以及复杂的内流道而言就有很大的困难,并且难以成为一个一体化的设备。
技术实现要素:4.本发明的目的在于克服上述不足,提供一种基于金属熔丝增减材的内流道无支撑成形方法,可以快速成型含有复杂内流道的零件,主要适合于单件小批量生产或者精度要求较高的大型复杂内流道的零件。
5.为了达到上述目的,本发明包括以下步骤:
6.步骤一,将具有内流道的零件模型进行分层;
7.步骤二,根据分层数据进行前n层的打印;
8.步骤三,根据分层数据进行第n+1层的打印;
9.步骤四,根据精度要求完成第n+1的加工;
10.步骤五,重复步骤三和步骤四,将具有内流道的零件打印成型;
11.步骤六,对前n层的内流道完成精加工,完成整体成形。
12.具有内流道的零件模型的内流道的拐角角度小于等于45度。
13.当第n层的内流道和第n+1层的内流道完全相同时,将第n+1层打印完之后一起进行后续操作。
14.步骤四的加工采用传统工艺。
15.传统工艺包括但不限于铣削和磨削。
16.第n层与第n+1层为流道弯折处。
17.与现有技术相比,本发明首先将具有内流道的零件模型进行分层,然后打印具有内流道的零件打印,最后再通过传统工艺对内流道完成精加工,本发明不需要支撑,且内流道表面都是经过经加工处理的,满足工艺生产的尺寸精度和表面精度要求。本发明能够快速成型含有复杂内流道的零件,主要适合于单件小批量生产或者精度要求较高的大型复杂内流道的零件。
附图说明
18.图1为本发明的流程图。
具体实施方式
19.下面结合附图对本发明做进一步说明。
20.参见图1,本发明包括以下步骤:
21.步骤一,将具有内流道的零件模型进行分层;
22.步骤二,根据分层数据进行前n层的打印;
23.步骤三,根据分层数据进行第n+1层的打印;
24.步骤四,采用传统工艺根据精度要求完成第n+1的加工;传统工艺包括但不限于铣削和磨削;
25.步骤五,重复步骤三和步骤四,将具有内流道的零件打印成型;
26.步骤六,采用传统工艺对前n层的内流道完成精加工,完成整体成形。
27.具有内流道的零件模型的内流道的拐角角度小于等于45度。当第n层的内流道和第n+1层的内流道完全相同时,将第n+1层打印完之后一起进行后续操作。第n层与第n+1层为流道弯折处。
28.实施例:
29.一种基于金属熔丝增减材的内流道无支撑成形方法包括如下步骤:
30.第一步:模型分层:通过绘图软件制作零件的模型,然后导入到适配的分层软件里,获得整体构件的分层数据;
31.第二步:按照分层数据进行前五层的打印;
32.第三步:打印第六层,如图1所示;
33.第四步:因第七层和第六层的内流道完全相同,因此直接打印第七层,如图1;
34.第五步:根据精度要求对第六层和第七层进行铣削加工,保证其尺寸要求以及表面精度要求;
35.第六步:重复第三步至第五步,如图1,直至加工完成;然后进行前五层内流道的加工,从而获得符合要求的零件。