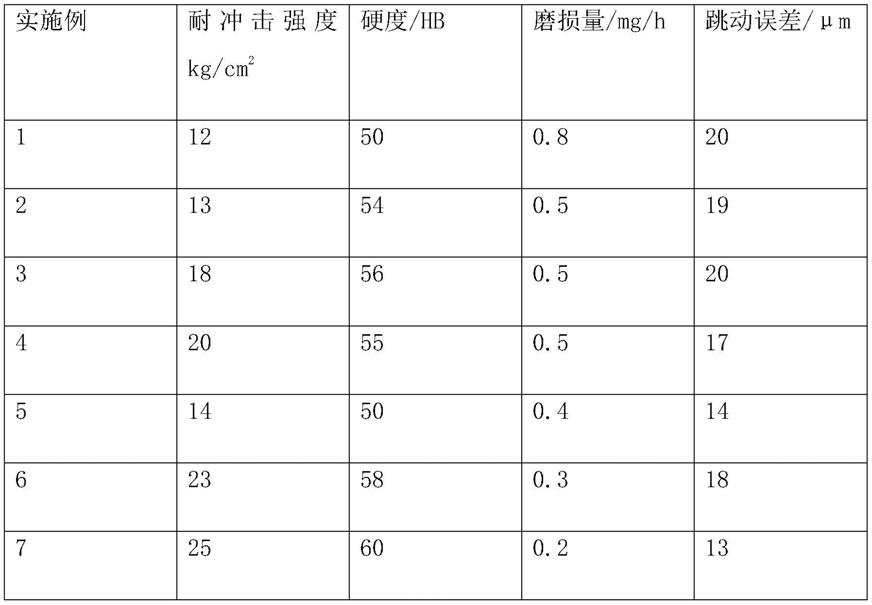
一种平行面cvd金刚石滚轮的制备方法
技术领域
1.本发明涉及磨削设备技术领域,具体涉及一种平行面cvd金刚石滚轮的制备方法。
背景技术:2.金刚石滚轮是新一代砂轮修整工具,具有高精度,高成型的特点。数控成形磨削技术是近年来国内外迅速发展的一种新型的加工技术,其高效精密的加工方式在机械工程上有着极其广泛的应用。金刚石滚轮的工作原理是:通过安装在磨床的修整装置上,金刚石滚轮修整普通陶瓷砂轮或cbn砂轮,砂轮成型后再磨削零件,从而将金刚石滚轮的外形轮廓及精度、尺寸通过砂轮复制到被加工的零件表面。其特点是机床操作简单,对操作工人的技术要求不高,加工的产品精度一致性好,质量稳定,能显著提高生产效率和产品质量,降低制造成本,容易实现磨削加工自动化。
3.如今的工厂发展是朝着追求产能和品质,高精度,省人力,降低对操作工人技术门槛,去掉中间繁琐操作的方向发展,对于双边对称弧形砂轮修整就不能使用以前的工艺单点金刚石修整器了,因为修整的一致性差,要反复调整修整的角度,由于金刚石通常只有一颗,所以磨损快,一致性差,满足不了特殊要求的高精度,而且还更换频繁,费事费力,次品率高;同时,现有技术中的双面修整金刚石滚轮由于金刚石条与基体之间是通过烧结作用固定为一体的,金刚石条的排列较为随机,这将导致双边对称弧形砂轮修整过程中砂轮的两个面被修整的精度不对称,影响工件的加工精度。
技术实现要素:4.针对上述存在的技术问题,本发明提供了一种能够同时对砂轮进行双面精确修整的平行面cvd金刚石滚轮的制备方法。
5.本发明的技术方案为:一种平行面cvd金刚石滚轮的制备方法,包括:
6.s1、根据使用工况,制备刚基体;
7.s2、在石墨模具内腔壁均匀涂抹粘合剂,并手工排列0.8
×
0.8
×
1.8mm的人造金刚石cvd条,人造金刚石cvd条与石墨模具内腔壁之间夹角为15
‑
90
°
,且呈菱形排列;
8.s3、将步骤s1刚基体置入石墨模具中心位置,并在刚基体表面和金刚石cvd条层均匀涂抹钎焊剂;
9.s4、分别称取w80、cu20和过渡层金属粉末,并将w80和cu20金属粉末混合均匀,其中w80和cu20金属粉末的体积比为1:1,过渡层金属粉末的体积占比为w80和cu20混合金属粉末的2
‑
9%;w80、cu20和过渡层金属粉末总体积由体积公式π(r12
‑
r22)
×
h可得,其中r1为石墨模具半径,r2为刚基体半径,h为刚基体高度;
10.s5、将步骤s4所得混合金属粉末总体积的40
‑
70%铺入石墨模具和刚基体之间缝隙,并利用压力机在100
‑
200mpa的压力下压实,然后平铺过渡层金属粉末,最后覆盖剩余混合金属粉末,利用压力机在100
‑
200mpa的压力再次压实混合金属粉末;
11.s6、将步骤s5所得石墨模具后放入真空钎焊炉内,抽真空至0.2
×
10
‑5‑
1.2
×
10
‑
5
pa,并在5
‑
10min内缓慢升温至780
‑
890℃,保温0.5
‑
1.2h,最后取出烧结体并去除模具,自然冷却至室温后,根据图纸加工精度要求以金刚石为基准进行精加工,得到成品金刚石滚轮;
12.s7、对步骤s6所得成品金刚石滚轮做动平衡、清洗、并涂抹防锈油,然后进行包装即可。
13.进一步地,步骤s2中,粘合剂为酚醛树脂粘合剂,通过酚醛树脂粘合剂将人造金刚石cvd条与石墨模具内腔臂进行粘接,不仅能够提高人造金刚石cvd与金属粉末钎焊过程中的排列稳定性,同时也有利于烧结体顺利脱模。
14.进一步地,步骤s2中,人造金刚石cvd条由改性石墨粉、触媒合金粉末和溶剂组分按照体积比2:1:1混合而成,其中,触媒合金粉末为铁粉、硅粉和钴粉按照体积比4:2:1组成的混合物,溶剂组分按重量份计,包括环氧树脂约15
‑
25份、正丁醇5
‑
17份、硬化蓖麻油2
‑
16份、甲基琥珀酸1
‑
9份、脂肪酸酰胺10
‑
20份;人造金刚石cvd条的制备方法为:将改性石墨粉、触媒合金粉末和溶剂组分按比例均匀混合,然后在温度为960
‑
1200℃,压力为450
‑
706mpa条件下,持续下压0.5
‑
2min,并包压处理1
‑
5min,冷却后及得人造金刚石cvd条,通过上述方法制备的人造金刚石cvd条具有良好的晶形,同时具有完整度高、粒度均已的优势。
15.进一步地,步骤s3中,钎焊剂按重量份计,包括苯乙烯
‑
马来酸树脂15
‑
30份、十七烷酸7
‑
16份、丙二醇15
‑
35份、纳米银微粒5
‑
10份、二氟化铜粉末4
‑
9份、抗坏血酸12
‑
19份,钎焊剂的制备方法为:将苯乙烯
‑
马来酸树脂、十七烷酸、丙二醇和抗坏血酸分别置于分散容器中,加热搅拌使其完全溶解,然后将纳米银微粒和二氟化铜粉末分别加入上述混合溶解中,并不断搅拌至膏状即可。通过上述方法所制备的钎焊剂,具有较好的高温流动性和湿润性,大大提高了钎焊剂在人造金刚石cvd条与金属粉末烧结体之间焊缝的铺展面积和深度,进而提高焊缝的牢固程度。
16.进一步地,步骤s6中,对金刚石滚轮进行精加工过程中,利用磨削方式反复进行3
‑
5次,使修整后的金刚石滚轮表面的圆跳动误差降至20μm以下,通过对金刚石滚轮进行磨削精加工,大大减小了金刚石滚轮使用过程中产生的摆动,提高了使用安全性,同时也使得本发明的金刚石滚轮能够适用于更高转速的修整设备。
17.进一步地,步骤s4中,过渡层金属粉末为铜镍合金粉末,通过添加过渡层金属粉末层,使得w80和cu20金属粉末在烧结钎焊过程中金属颗粒排列更加均匀,避免金属粉末钎焊过程中产生孔洞,减少属粉末在烧结钎焊缺陷。
18.进一步地,步骤s6中完成后,对成品金刚石滚轮进行高频淬火处理,具体操作为:将成品金刚石滚轮置入高频电流感应器中,在15
‑
25s内迅速升温至650
‑
950℃,然后在8
‑
12s内迅速降温至室温即可,通过对成品金刚石滚轮进行高频淬火处理,使得成品金刚石滚轮的硬度得到很大改善,延长其使用寿命。
19.与现有技术相比,本发明的有益效果是:本发明的金刚石滚轮与传统的单点金刚石笔修整相比,生产效率大幅度提高,且加工出的零件表面质量和精度更高,特别适合高精度、大批量生产中;利用本发明的金刚石滚轮能够在很短时间内完成砂轮的整形和修锐,且修整时修整力小、修具本身磨损小、修整精度高;金刚石滚轮砂轮修整器具有修整效率高、寿命长、便于冷却、结构简单、体积小、安装方便的优势,本发明通过将人造金刚石cvd条与石墨模具内腔壁之间呈45
°
,且菱形排列粘贴,能够大大提高成品金刚石滚轮的硬度,减小
高成品金刚石滚轮的磨损量,同时本发明的人造金刚石cvd条,具有良好的晶形,同时具有完整度高、粒度均一的优势,进而使成品金刚石滚轮具有良好的硬度以及耐冲击强度,减小了成品金刚石滚轮的磨损量;本发明的钎焊剂,大大提高了钎焊剂在人造金刚石cvd条与金属粉末烧结体之间焊缝的铺展面积和深度,提高了成品金刚石滚轮的耐冲击强度,通过对成品金刚石滚轮进行了磨削修整,使得金刚石滚轮表面的圆跳动误差得到改善,对成品金刚石滚轮进行高频淬火处理,使其硬度得到提升,进而减小了磨损量。
具体实施方式
20.实施例1:一种平行面cvd金刚石滚轮的制备方法,包括:
21.s1、根据使用工况,制备刚基体;
22.s2、在石墨模具内腔壁均匀涂抹粘合剂,并手工排列0.8
×
0.8
×
1.8mm的人造金刚石cvd条,人造金刚石cvd条与石墨模具内腔壁之间夹角为15
°
,且呈菱形排列;粘合剂为酚醛树脂粘合剂,通过酚醛树脂粘合剂将人造金刚石cvd条与石墨模具内腔臂进行粘接,不仅能够提高人造金刚石cvd与金属粉末钎焊过程中的排列稳定性,同时也有利于烧结体顺利脱模;人造金刚石cvd条为市售产品;
23.s3、将步骤s1刚基体置入石墨模具中心位置,并在刚基体表面和金刚石cvd条层均匀涂抹钎焊剂,钎焊剂为市售产品;
24.s4、分别称取w80、cu20和过渡层金属粉末,并将w80和cu20金属粉末混合均匀,其中w80和cu20金属粉末的体积比为1:1,过渡层金属粉末的体积占比为w80和cu20混合金属粉末的2%;w80、cu20和过渡层金属粉末总体积由体积公式π(r12‑
r22)
×
h可得,其中r1为石墨模具半径,r2为刚基体半径,h为刚基体高度;过渡层金属粉末为铜镍合金粉末,通过添加过渡层金属粉末层,使得w80和cu20金属粉末在烧结钎焊过程中金属颗粒排列更加均匀,避免金属粉末钎焊过程中产生孔洞,减少属粉末在烧结钎焊缺陷;
25.s5、将步骤s4所得混合金属粉末总体积的40%铺入石墨模具和刚基体之间缝隙,并利用小型20t压力机在100mpa的压力下压实,然后平铺过渡层金属粉末,最后覆盖剩余混合金属粉末,利用压力机在150mpa的压力再次压实混合金属粉末;
26.s6、将步骤s5所得石墨模具后放入真空钎焊炉内,抽真空至0.2
×
10
‑5pa,并在5min内缓慢升温至780
‑
℃,保温0.5h,最后取出烧结体并去除模具,自然冷却至室温后,根据图纸加工精度要求以金刚石为基准进行精加工,得到成品金刚石滚轮;
27.s7、对步骤s6所得成品金刚石滚轮做动平衡、清洗、并涂抹防锈油,然后进行包装即可。
28.实施例2:本实施例与实施例基本相同,不同之处在于:步骤s2中,人造金刚石cvd条与石墨模具内腔壁之间夹角为45
°
,且呈菱形排列。
29.实施例3:本实施例与实施例2基本相同,不同之处在于:
30.步骤s2中,人造金刚石cvd条由改性石墨粉、触媒合金粉末和溶剂组分按照体积比2:1:1混合而成,其中,触媒合金粉末为铁粉、硅粉和钴粉按照体积比4:2:1组成的混合物,溶剂组分按重量份计,包括环氧树脂约15份、正丁醇5份、硬化蓖麻油2份、甲基琥珀酸1份、脂肪酸酰胺10份;人造金刚石cvd条的制备方法为:将改性石墨粉、触媒合金粉末和溶剂组分按比例均匀混合,然后在温度为960℃,压力为450mpa条件下,持续下压0.5min,并包压处
理1min,冷却后及得人造金刚石cvd条,通过上述方法制备的人造金刚石cvd条具有良好的晶形,同时具有完整度高、粒度均一的优势。
31.实施例4:本实施例与实施例2基本相同,不同之处在于:
32.步骤s3中,钎焊剂按重量份计,包括苯乙烯
‑
马来酸树脂15份、十七烷酸7份、丙二醇15份、纳米银微粒5份、二氟化铜粉末4份、抗坏血酸12份,钎焊剂的制备方法为:将苯乙烯
‑
马来酸树脂、十七烷酸、丙二醇和抗坏血酸分别置于分散容器中,加热搅拌使其完全溶解,然后将纳米银微粒和二氟化铜粉末分别加入上述混合溶解中,并不断搅拌至膏状即可;通过上述方法所制备的钎焊剂,具有较好的高温流动性和湿润性,大大提高了钎焊剂在人造金刚石cvd条与金属粉末烧结体之间焊缝的铺展面积和深度,进而提高焊缝的牢固程度。
33.实施例5:本实施例与实施例2基本相同,不同之处在于:
34.步骤s6中,对金刚石滚轮进行精加工过程中,利用磨削方式反复进行3次,使修整后的金刚石滚轮表面的圆跳动误差为15μm,通过对金刚石滚轮进行磨削精加工,大大减小了金刚石滚轮使用过程中产生的摆动,提高了使用安全性,同时也使得本发明的金刚石滚轮能够适用于更高转速的修整设备。
35.实施例6:本实施例与实施例2基本相同,不同之处在于:
36.步骤s6中完成后,对成品金刚石滚轮进行进行高频淬火处理,具体操作为:将成品金刚石滚轮置入高频电流感应器中,在15s内迅速升温至650℃,然后在8s内迅速降温至室温即可,通过对成品金刚石滚轮进行高频淬火处理,使得成品金刚石滚轮的硬度得到很大改善,延长其使用寿命。
37.实施例7:一种平行面cvd金刚石滚轮的制备方法,包括:
38.s1、根据使用工况,制备刚基体;
39.s2、在石墨模具内腔壁均匀涂抹粘合剂,并手工排列0.8
×
0.8
×
1.8mm的人造金刚石cvd条,人造金刚石cvd条与石墨模具内腔壁之间夹角为45
°
,且呈菱形排列;粘合剂为酚醛树脂粘合剂,通过酚醛树脂粘合剂将人造金刚石cvd条与石墨模具内腔臂进行粘接,不仅能够提高人造金刚石cvd与金属粉末钎焊过程中的排列稳定性,同时也有利于烧结体顺利脱模;人造金刚石cvd条由改性石墨粉、触媒合金粉末和溶剂组分按照体积比2:1:1混合而成,其中,触媒合金粉末为铁粉、硅粉和钴粉按照体积比4:2:1组成的混合物,溶剂组分按重量份计,包括环氧树脂约25份、正丁醇17份、硬化蓖麻油16份、甲基琥珀酸9份、脂肪酸酰胺20份;人造金刚石cvd条的制备方法为:将改性石墨粉、触媒合金粉末和溶剂组分按比例均匀混合,然后在温度为1200℃,压力为706mpa条件下,持续下压2min,并包压处理5min,冷却后及得人造金刚石cvd条,通过上述方法制备的人造金刚石cvd条具有良好的晶形,同时具有完整度高、粒度均已的优势;
40.s3、将步骤s1刚基体置入石墨模具中心位置,并在刚基体表面和金刚石cvd条层均匀涂抹钎焊剂;钎焊剂按重量份计,包括苯乙烯
‑
马来酸树脂30份、十七烷酸16份、丙二醇35份、纳米银微粒10份、二氟化铜粉末9份、抗坏血酸19份,钎焊剂的制备方法为:将苯乙烯
‑
马来酸树脂、十七烷酸、丙二醇和抗坏血酸分别置于分散容器中,加热搅拌使其完全溶解,然后将纳米银微粒和二氟化铜粉末分别加入上述混合溶解中,并不断搅拌至膏状即可。通过上述方法所制备的钎焊剂,具有较好的高温流动性和湿润性,大大提高了钎焊剂在人造金刚石cvd条与金属粉末烧结体之间焊缝的铺展面积和深度,进而提高焊缝的牢固程度;
41.s4、分别称取w80、cu20和过渡层金属粉末,并将w80和cu20金属粉末混合均匀,其中w80和cu20金属粉末的体积比为1:1,过渡层金属粉末的体积占比为w80和cu20混合金属粉末的5%;w80、cu20和过渡层金属粉末总体积由体积公式π(r12
‑
r22)
×
h可得,其中r1为石墨模具半径,r2为刚基体半径,h为刚基体高度;过渡层金属粉末为铜镍合金粉末,通过添加过渡层金属粉末层,使得w80和cu20金属粉末在烧结钎焊过程中金属颗粒排列更加均匀,避免金属粉末钎焊过程中产生孔洞,减少属粉末在烧结钎焊缺陷;
42.s5、将步骤s4所得混合金属粉末总体积的50%铺入石墨模具和刚基体之间缝隙,并利用压力机在200mpa的压力下压实,然后平铺过渡层金属粉末,最后覆盖剩余混合金属粉末,利用压力机在200mpa的压力再次压实混合金属粉末;
43.s6、将步骤s5所得石墨模具后放入真空钎焊炉内,抽真空至0.5
×
10
‑5pa,并在7min内缓慢升温至850℃,保温0.9h,最后取出烧结体并去除模具,自然冷却至室温后,根据图纸加工精度要求以金刚石为基准进行精加工,得到成品金刚石滚轮;对金刚石滚轮进行精加工过程中,利用磨削方式反复进行3
‑
5次,使修整后的金刚石滚轮表面的圆跳动误差为15μm,通过对金刚石滚轮进行磨削精加工,大大减小了金刚石滚轮使用过程中产生的摆动,提高了使用安全性,同时也使得本发明的金刚石滚轮能够适用于更高转速的修整设备;对成品金刚石滚轮进行高频淬火处理,具体操作为:将成品金刚石滚轮置入高频电流感应器中,在25s内迅速升温至950℃,然后在12s内迅速降温至室温即可,通过对成品金刚石滚轮进行高频淬火处理,使得成品金刚石滚轮的硬度得到很大改善,延长其使用寿命;
44.s7、对步骤s6所得成品金刚石滚轮做动平衡、清洗、并涂抹防锈油,然后进行包装即可。
45.实验例:分别对实施例1
‑
7所制备的成品金刚石滚轮进行力学性能检测,检测结果如表1所示;
46.表1:实施例1
‑
7所制备的成品金刚石滚轮力学性能检测结果;
[0047][0048]
由表1可知,通过实施例2与实施例对比可知,通过将人造金刚石cvd条与石墨模具内腔壁之间呈45
°
,且菱形排列粘贴,能够大大提高成品金刚石滚轮的硬度,减小高成品金刚石滚轮的磨损量;通过实施3与实施例2相比,采用本发明所制备的人造金刚石cvd条,具有良好的晶形,同时具有完整度高、粒度均一的优势,进而使成品金刚石滚轮具有良好的硬度以及耐冲击强度,减小了成品金刚石滚轮的磨损量;通过实施例4与实施例2相比,由于采用了本发明所制备的钎焊剂,大大提高了钎焊剂在人造金刚石cvd条与金属粉末烧结体之间焊缝的铺展面积和深度,提高了成品金刚石滚轮的耐冲击强度;通过实施例5与实施例2相比,由于对成品金刚石滚轮进行了磨削修整,使得金刚石滚轮表面的圆跳动误差得到改善;通过实施例6与实施例2相比,由于对成品金刚石滚轮进行了高频淬火处理,使其硬度得到提升,进而减小了磨损量。