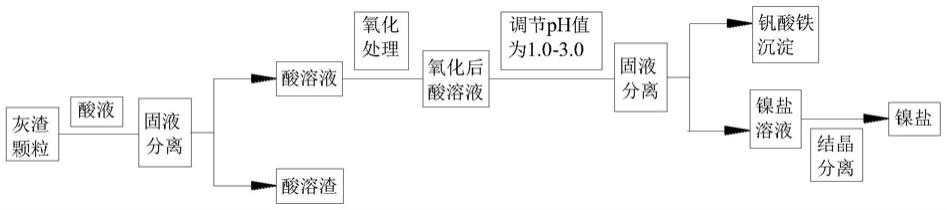
1.本申请涉及石油焦气化灰渣的处理技术领域,具体而言,涉及一种石油焦气化灰渣的处理方法。
背景技术:2.针对煤气化灰渣或其他性质相近的灰渣,目前主要处理方式是稳定化后进行二次利用。煤气化灰渣的主要成分包括碳、氧化硅、氧化铝、氧化钙等,其中不含有重金属钒和镍;石油焦制氢虽与煤制氢工艺过程一致,但由于原料的差异,石油焦制氢灰渣的主要成分包括碳、氧化硅、氧化铝、氧化钙、氧化钒、氧化镍、氧化铁、氧化钠等化合物,其中含有重金属钒和镍。如果直接进行稳定化处理,不能够对重金属进行回收,造成资源浪费,且直接稳定化处置能耗较大、危害大。
技术实现要素:3.本申请的目的在于提供一种石油焦气化灰渣的处理方法,能够对重金属钒和镍分别进行回收,使灰渣的资源化利用率更高。
4.第一方面,本申请提供一种石油焦气化灰渣的处理方法,包括:对石油焦气化灰渣进行酸处理:将灰渣与酸液混合进行酸溶处理,使灰渣中的镍、钒、铁溶出,然后固液分离分别得到酸溶渣和酸溶液。对酸溶液进行氧化处理:向酸溶液中添加氧化剂得到氧化后的酸溶液,使酸溶液中的钒离子被氧化成5价态,铁离子被氧化成3价态。调节氧化后酸溶液的ph值:调节氧化后酸溶液的ph值为1.0
‑
3.0。
5.酸溶处理可以使灰渣中的镍、钒、铁溶出,酸溶渣中的重金属含量减少,可以作为建材原料进行使用;酸溶液中含有钒离子、镍离子和铁离子;由于石油焦气化灰渣是在还原氛围中产生的,酸溶液中的钒离子和铁离子均处于还原态,向酸溶液中加入氧化剂,可以使酸溶液中的低价态钒离子被氧化成5价态,低价态铁离子被氧化成3价态。将氧化后酸溶液的ph值调节为1.0
‑
3.0,可以使部分钒离子和铁离子共同沉淀成钒酸铁,部分钒离子水解成水合五氧化二钒沉淀,部分铁离子水解成氢氧化铁沉淀,以对钒进行回收;沉淀以后,酸溶液中主要含有的是镍盐,以对镍进行回收。可以分别对灰渣中的硅铝酸盐(酸溶渣)、钒和镍进行回收,使灰渣的资源化利用率更高。
6.第二方面,本申请提供一种石油焦气化灰渣的处理方法,包括:对石油焦气化灰渣进行烧炭处理得到烧炭灰渣。对烧炭灰渣进行酸处理:将烧炭灰渣与酸液混合进行酸溶处理,使灰渣中的镍、钒、铁溶出,然后固液分离分别得到酸溶渣和酸溶液。调节酸溶液的ph值为1.0
‑
3.0。
7.由于石油焦气化灰渣是在还原氛围中产生的,酸溶液中的钒离子和铁离子均处于还原态,进行烧炭处理以后,钒离子和铁离子均被氧化成了高价态的金属离子(氧化钒中的钒为5价态,氧化铁中的铁为3价态)。酸溶处理可以使灰渣中的镍、钒、铁溶出,且由于经过烧炭处理,使钒和铁的溶出率更高,酸溶渣中的重金属含量减少,可以作为建材原料进行使
用。酸溶液中含有5价态的钒离子和3价态的铁离子;将酸溶液的ph值调节为1.0
‑
3.0,可以使部分钒离子和铁离子共同沉淀成钒酸铁,部分钒离子水解成水合五氧化二钒沉淀,部分铁离子水解成氢氧化铁沉淀,以对钒进行回收;沉淀以后,酸溶液中主要含有的是镍盐,以对镍进行回收。可以分别对灰渣中的硅铝酸盐(酸溶渣)、钒和镍进行回收,使灰渣的资源化利用率更高。
8.在一种可能的实施方式中,酸溶处理的条件是:酸液是质量浓度为20
‑
60%的强酸,处理温度为100
‑
200℃,处理时间为0.5
‑
3h。铝的溶出率<2%,而镍的溶出率≥60%,钒的溶出率≥50%,铁的溶出率≥30%,不会影响灰渣的玻璃体结构,且能够使镍和钒具有较多的溶出。
9.可选地,酸液是质量浓度30
‑
50%的硫酸;或酸液是质量浓度为40
‑
60%的硝酸。
10.在一种可能的实施方式中,调节酸溶液的ph值为1.0
‑
3.0的方法包括:将碱液添加进80
‑
105℃的酸溶液中以使酸溶液的ph值为1.0
‑
3.0并沉淀1
‑
12h。此条件下,钒和铁的沉淀率较高,可以达到80%以上,以便将钒和镍分离,分别进行回收。
11.可选地,碱液为强碱溶液。
12.进一步地,强碱溶液为氢氧化钠溶液或/和氢氧化钾溶液。
13.在一种可能的实施方式中,氧化剂包括氯酸钠、过氧化氢、次氯酸钠和亚氯酸钠中的一种或多种。此氧化剂不引入重金属离子,氯酸钠、次氯酸钠和亚氯酸钠的用量更少,过氧化氢的用量稍大,但都能够将低价态的钒离子氧化成5价态,低价态的铁离子氧化成3价态。
14.在一种可能的实施方式中,灰渣在酸处理之前,还包括将灰渣粉碎成粒径小于110μm的步骤。以便后续酸处理的效率更高,钒离子和镍离子更加容易溶出,溶出率也更高。
15.在一种可能的实施方式中,灰渣在烧炭处理之前,还包括将灰渣粉碎成粒径小于110μm的步骤,以便后续对灰渣进行处理。
附图说明
16.为了更清楚地说明本申请实施例的技术方案,下面将对实施例中所需要使用的附图作简单地介绍,应当理解,以下附图仅示出了本申请的某些实施例,因此不应被看作是对范围的限定,对于本领域普通技术人员来讲,在不付出创造性劳动的前提下,还可以根据这些附图获得其他相关的附图也属于本申请的保护范围。
17.图1为本申请提供的石油焦气化灰渣的处理方法的第一工艺流程图;
18.图2为本申请提供的石油焦气化灰渣的处理方法的第二工艺流程图。
具体实施方式
19.为使本申请实施例的目的、技术方案和优点更加清楚,下面将结合本申请实施例中的附图,对本申请实施例中的技术方案进行描述。
20.石油焦气化灰渣的主要成分是碳、氧化硅、氧化铝、氧化钙、氧化钒、氧化镍、硫化镍、氧化铁等化合物,灰渣中碳占主要部分且含有镍和钒,灰渣属于危废固体废弃物,需要对其进行处理,去除重金属钒和镍,实现灰渣的无害化处理。灰渣在生成过程中的特殊工艺(1400℃的高温下熔浆进入水冷系统),导致灰渣具有玻璃体结构,石油焦气化灰渣的比表
面积<5m2/g。由于灰渣是从还原氛围中产生的,玻璃体结构中主体是硅铝陶瓷结构,硅铝被固定且和碳交叉包裹,金属在灰渣中有还原态,例如:硫化镍、四价氧化钒,三价氧化钒,二价铁氧化物等,镍存在玻璃体结构的表面,铁和钒等金属主要嵌入在玻璃体结构中。所以,将灰渣中的重金属镍和钒去除,并对灰渣进行资源化利用的难度较高。
21.图1为本申请提供的石油焦气化灰渣的处理方法的第一工艺流程图。请参阅图1,石油焦气化灰渣的处理方法包括如下步骤:
22.s10,将灰渣粉碎成粒径小于110μm的灰渣颗粒,有利于后续重金属镍和钒的溶出。其中,可采用湿磨、干磨等手段进行处理。
23.s20,对灰渣进行酸处理:将灰渣与酸液混合进行酸溶处理,使灰渣中的镍、钒、铁溶出,然后固液分离分别得到酸溶渣和酸溶液。
24.酸处理可以使灰渣中的镍、钒、铁溶出(硫化镍和氧化镍转化成镍盐;氧化钒转化成钒盐;氧化铁转化成铁盐),酸溶渣中的重金属含量减少,可以作为建材原料进行使用。需要说明的是:酸溶渣中,镍和钒虽然可能没有能够完全溶出,但是,由于酸溶渣中镍和钒的量减少,可以使其达到合格的标准,能够进行其他资源化的利用。
25.可选地,酸溶处理的条件是:酸液是质量浓度为20
‑
60%的强酸,处理温度为100
‑
200℃,处理时间为0.5
‑
3h。此条件下,铝的溶出率<2%,而镍的溶出率≥60%,钒的溶出率≥50%,铁的溶出率≥30%。
26.例如:酸溶处理的处理温度为100℃、120℃、140℃、160℃、180℃或200℃;处理时间为0.5h、1h、1.5h、2h、2.5h或3h。
27.进一步地,酸液是质量浓度为30
‑
50%的硫酸,处理温度为140
‑
180℃,可以使铝的溶出率<2%,而镍的溶出率≥70%,钒的溶出率≥50%,铁的溶出率≥30%,镍的溶出率更高。例如:硫酸的质量浓度为30%、40%、50%或60%,处理温度为140℃、150℃、160℃、170℃或180℃。
28.在其他实施例中,酸液是还可以是盐酸,或酸液是质量浓度为40
‑
60%的硝酸。
29.该实施例中,灰渣在酸处理之前,不进行烧炭处理。一方面,可以使镍的溶出率大大增加;另一方面,碳在酸溶渣中,酸溶渣在作为水泥或砖等建材材料的原料的时候,碳可以作为燃料进行使用,灰渣的资源化利用率更高。
30.s30,对酸溶液进行氧化处理:向酸溶液中添加氧化剂得到氧化后的酸溶液,使酸溶液中的钒离子被氧化成5价态,铁离子被氧化成3价态,以便后续铁离子和钒离子沉淀。
31.可选地,氧化剂包括氯酸钠、过氧化氢、次氯酸钠和亚氯酸钠中的一种或多种。此氧化剂不引入重金属离子,氯酸钠、次氯酸钠和亚氯酸钠的用量更少,过氧化氢的用量稍大,但都能够将低价态的钒离子氧化成5价态,低价态的铁离子氧化成3价态。
32.s40,调节氧化后酸溶液的ph值:调节氧化后酸溶液的ph值为1.0
‑
3.0,使酸溶液中的铁离子和钒离子沉淀。
33.酸溶液中含有钒离子(5价态)、镍离子和铁离子(3价态);将酸溶液的ph值调节为1.0
‑
3.0,可以使钒离子和铁离子共同沉淀成钒酸铁,钒离子水解成水合五氧化二钒沉淀,以对钒进行回收,铁离子沉淀成氢氧化铁沉淀。
34.对沉淀后的酸溶液进行固液分离,钒酸铁、水合五氧化二钒以及氢氧化铁作为铁钒滤渣,可以进行资源化利用,用于制备钒铁合金。滤液中主要含有的是镍盐(镍盐溶液),
将镍盐溶液进行结晶分离,得到工业镍(达到工业镍的国标),以对镍进行回收利用。
35.如果使用硫酸作为酸溶处理的酸液,得到的硫酸镍产品中,硫酸镍的含量可以达到59%及其以上,用于制备镍合金,也可用做电解的原料。
36.可选地,调节酸溶液的ph值为1.0
‑
3.0的方法包括:将碱液添加进80
‑
105℃的酸溶液中以使酸溶液的ph值为1.0
‑
3.0并沉淀1
‑
12h。此条件下,钒和铁的沉淀率较高,可以达到80%以上,以便将钒和镍分离,分别进行回收。例如:调节酸溶液中的ph值可以为1.0、1.5、2.0、2.5或3.0;的温度可以是80℃、90℃、100℃或110℃;沉淀的时间可以是1h、3h、5h、7h、9h或12h。
37.可选地,碱液是强碱溶液或/和强碱弱酸盐溶液。进一步地,强碱溶液为氢氧化钠溶液或/和氢氧化钾溶液;强碱弱酸盐溶液为碳酸钠溶液或/和碳酸钾溶液。
38.图2为本申请提供的石油焦气化灰渣的处理方法的第二工艺流程图。请参阅图2,该实施例中,灰渣在粉碎以后、酸处理之前,进行烧炭处理。进行烧炭处理以后,硫化镍转化成氧化镍,在后续酸处理过程中,镍的溶出率下降,钒元素和铁元素均被氧化成了高价态的金属离子(氧化钒中的钒为5价态,氧化铁中的铁为3价态),以便后续钒和铁的溶出,有利于钒的回收,且后续对酸溶液不需要进行氧化处理,就能够使ph值为1.0
‑
3.0酸溶液中的钒离子和铁离子更加容易水解得到钒酸铁沉淀、水合五氧化二钒沉淀以及氢氧化铁沉淀。
39.为使本申请实施例的目的、技术方案和优点更加清楚,下面将对本申请实施例中的技术方案进行清楚、完整地描述。实施例中未注明具体条件者,按照常规条件或制造商建议的条件进行。所用试剂或仪器未注明生产厂商者,均为可以通过市售购买获得的常规产品。
40.实验例1酸处理的条件研究
41.将灰渣粉碎成粒径为50
‑
70μm的灰渣颗粒,将灰渣颗粒与质量浓度为30%的硫酸溶液混合,在140℃的条件下进行酸溶处理3h,固液分离以后得到酸溶渣。检测酸处理前后灰渣中的主要成分的溶出率如表1。其中,灰渣中各成分的量的检测方法是:先分别对酸处理前后的灰渣进行微波消解,然后通过电感耦合等离子发射光谱仪检测灰渣中离子含量,再计算出溶出率。
42.表1酸处理前后灰渣中的主要成分的溶出率
[0043] al2o3fe2o3niov2o5原料20.3310.841.074.27处理后19.444.320.082.06溶出率1.79%60.32%91.77%55.68%
[0044]
其中,硫化镍和氧化镍均以氧化镍计。
[0045]
从表1可以看出,经过了酸处理以后,灰渣中的铝溶出率小于2%,镍溶出率大于90%,钒溶出率大于50%,铁溶出率大于60%,可以使得到的酸溶渣中的重金属镍和钒的含量大大减少,可以作为水泥或砖等建材原料进行使用。
[0046]
检测酸处理前后灰渣的比表面积(通过micromerritics asap 2460比表面分析仪检测灰渣的内孔比表面积)如表2。
[0047]
表2酸处理前后灰渣中的比表面积
[0048]
酸溶前m2/g2305
酸溶后m2/g3162
[0049]
从表2中可以看出,酸溶前和酸溶后,灰渣的内孔比表面积基本没有发生变化,说明酸溶处理没有对灰渣的玻璃体结构造成破坏,仅将灰渣中的部分金属溶出。
[0050]
将灰渣粉碎成粒径为70
‑
90μm的灰渣颗粒,将灰渣颗粒与质量浓度为30%的硫酸溶液混合,在不同温度的条件下进行酸溶处理3h,固液分离以后得到酸溶渣。检测酸处理前后灰渣中的主要成分的溶出率如表3。
[0051]
表3酸处理前后灰渣中的主要成分的溶出率
[0052]
处理温度100℃120℃140℃160℃180℃镍溶出率55%64%73%91%92%铁溶出率22%36%54%61%63%钒溶出率52%58%54%56%63%
[0053]
从表3可以看出,如果酸液是硫酸溶液,酸处理的温度为140
‑
180℃,镍、铁和钒的溶出率较高。
[0054]
将灰渣粉碎成粒径为70
‑
90μm的灰渣颗粒,将灰渣颗粒与不同质量浓度的硫酸溶液混合,在140℃的条件下进行酸溶处理3h,固液分离以后得到酸溶渣。检测酸处理前后灰渣中的主要成分的溶出率如表4。
[0055]
表4酸处理前后灰渣中的主要成分的溶出率
[0056]
硫酸质量浓度10%20%30%40%50%60%镍溶出率50%63%72%88%92%60%铁溶出率20%32%41%55%63%33%钒溶出率43%51%53%56%63%28%
[0057]
从表4可以看出,如果酸液是硫酸溶液,硫酸的质量浓度为30%
‑
50%,镍、铁和钒的溶出率较高。硫酸溶液的浓度为60%时,金属溶出率反而下降,发明人研究认为,其原因可能是:硫酸浓度过高,浆液流动性差而影响传质效果,导致金属溶出率下降。
[0058]
将灰渣粉碎成粒径为90
‑
110μm的灰渣颗粒,将灰渣颗粒与质量浓度为45%的硫酸溶液混合,在140℃的条件下进行不同时间的酸溶处理,固液分离以后得到酸溶渣。检测酸处理前后灰渣中的主要成分的溶出率如表5。
[0059]
表5酸处理前后灰渣中的主要成分的溶出率
[0060]
处理时间1h2h3h4h5h镍溶出率89%88%91%87%86%铁溶出率56%53%57%53%54%钒溶出率58%54%47%51%48%
[0061]
从表5可以看出,不同处理时间,金属溶出率的值差别不大,只要能够达到基本的时间即可。
[0062]
实施例2是否烧炭对酸处理效果的影响
[0063]
将灰渣粉碎成粒径为50
‑
70μm的灰渣颗粒,将灰渣颗粒与质量浓度为30%的硫酸溶液混合,在140℃的条件下进行酸溶处理3h,固液分离以后得到酸溶渣。检测酸处理前后灰渣中的主要成分的溶出率如表6。其中,灰渣颗粒与硫酸溶液混合之前,一部分进行烧炭
处理,一部分不进行烧炭处理。
[0064]
表6酸处理前后灰渣中的主要成分的溶出率
[0065] 镍溶出率钒溶出率铁溶出率铝溶出率未烧92%56%61%1.8%烧后83%63%66%1.5%
[0066]
从表6可以看出,如果灰渣未经过烧炭处理,镍溶出率较高,钒溶出率和铁溶出率较低;如果灰渣经过烧炭处理,镍溶出率下降,钒溶出率和铁溶出率较高。其原因在于:经过烧炭处理以后,硫化镍转化成氧化镍,其溶出的难度加大,而钒离子转化成5价态,铁离子转化成3价态,其溶出的难度减小。
[0067]
实施例3调节酸溶液的ph值的条件研究
[0068]
将灰渣粉碎成粒径为50
‑
70μm的灰渣颗粒,将灰渣颗粒与质量浓度为30%的硫酸溶液混合,在140℃的条件下进行酸溶处理3h,固液分离以后得到酸溶液。向酸溶液中加入氯酸钠溶液得到氧化后的酸溶液,然后在95℃下,继续加入氢氧化钠溶液,调节氧化后的酸溶液的ph值为2.5,并沉淀不同时间,固液分离后得到滤饼和滤液。检测酸溶液中钒离子和铁离子的沉淀率如表7。其中,酸溶液中钒离子和铁离子的沉淀率的检测方法是:通过检测沉淀前后溶液中的离子浓度,根据离子浓度差计算出沉淀率。
[0069]
表7酸溶液中钒离子和铁离子的沉淀率
[0070]
沉淀时间1h2h4h6h沉淀率75.7%84.1%96.7%96.5%
[0071]
从表7可以看出,沉淀达到4h以后,沉淀率基本不再发生变化,可以说明最佳沉淀时间为4h左右(3
‑
5h)。
[0072]
将灰渣粉碎成粒径为50
‑
70μm的灰渣颗粒,将灰渣颗粒与质量浓度为30%的硫酸溶液混合,在140℃的条件下进行酸溶处理3h,固液分离以后得到酸溶液。向酸溶液中加入氯酸钠溶液得到氧化后的酸溶液,然后在不同温度下,继续加入氢氧化钠溶液,调节氧化后的酸溶液的ph值为2.5,并沉淀3h,固液分离后得到滤饼和滤液。检测并计算酸溶液中钒离子和铁离子的沉淀率如表8。
[0073]
表8酸溶液中钒离子和铁离子的沉淀率
[0074]
沉淀温度60℃70℃80℃95℃沉淀率65.7%84.1%90.7%96.5%
[0075]
从表8可以看出,沉淀温度为80
‑
95℃时,沉淀率的值更高。
[0076]
将灰渣粉碎成粒径为50
‑
70μm的灰渣颗粒,将灰渣颗粒与质量浓度为30%的硫酸溶液混合,在140℃的条件下进行酸溶处理3h,固液分离以后得到酸溶液。向酸溶液中加入氯酸钠溶液得到氧化后的酸溶液,然后在80℃下,继续加入氢氧化钠溶液,调节氧化后的酸溶液为不同的ph值,并沉淀3h,固液分离后得到滤饼和滤液。检测并计算酸溶液中钒离子和铁离子的沉淀率如表9。
[0077]
表9酸溶液中钒离子和铁离子的沉淀率
[0078]
ph0.71.52.03.0沉淀率10.7%55.6%86.7%98.5%
[0079]
从表9可以看出,沉淀的ph值为2
‑
3时,沉淀率的值更高。
[0080]
以上所描述的实施例是本申请一部分实施例,而不是全部的实施例。本申请的实施例的详细描述并非旨在限制要求保护的本申请的范围,而是仅仅表示本申请的选定实施例。基于本申请中的实施例,本领域普通技术人员在没有作出创造性劳动前提下所获得的所有其他实施例,都属于本申请保护的范围。