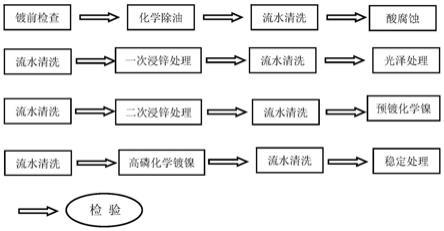
1.本发明属于新型复合材料化学镀镍工艺技术领域,具体涉及一种铝基碳化硅复合材料超厚高磷化学镀镍及稳定处理工艺。
背景技术:2.铝基碳化硅复合材料具有较高的比强度、比弹性模量、低重量及优良的综合性能,广泛应用在航天反射镜、微波集成电路、功率模块、高铁等尖端领域。铝基碳化硅复合材料就是以硬铝合金为基,以一定形式、比例和分布状态,用碳化硅颗粒(金刚砂)作增强体,构成有明显界面的多相复合材料,兼具单一金属不具备的综合优越性能。由于碳化硅颗粒为半导体材料,具有优良的抗化学腐蚀性和抗氧化性,因此在进行化学处理时,铝基优先被腐蚀,而碳化硅颗粒不参加化学反应,会析出粘附在零件表面,形成表面腐蚀不均匀,表面黑灰,严重影响化学镀镍层的表面质量。因此铝基碳化硅复合材料化学镀镍的前处理技术,是保证镀层结合力和基体表面质量的一项关键技术。其次,目前常用的化学镀镍层厚度一般为(5~8)μm;航空发动机上叶轮的化学镀镍层厚度一般为(25~75)μm;汽车工业上的散热器、喷油嘴化学镀镍层的厚度一般为(10~25)μm,而反射镜要求化学镀镍层厚度为(100~150)μm,是普通化学镀镍层厚度的30倍。从化学镀镍沉积机理上分析,是通过催化反应逐步在金属表面沉积镍磷合金,因此催化反应是否能够持续、稳定的进行,是化学镀镍层厚度能否持续增厚的关键因素,也是本发明必须要解决的技术难点之一。
技术实现要素:3.本发明解决的技术问题:提供一种铝基碳化硅复合材料超厚高磷化学镀镍及稳定处理工艺,本发明是针对高强度、低重量的铝基碳化硅复合材料,通过采用适宜的前处理腐蚀和和预镀化学镍工艺,既能去除材料表面的氧化物,又不会产生过腐蚀,提高了镀层的结合力;再通过采用一次浸锌
‑
光泽处理
‑
二次浸锌
‑
预镀化学镍
‑
高磷化学镀镍等工艺,通过温度阶梯升温、主盐浓度的管控等过程控制方法,维持催化反应的正常进行,持续的增厚,以提高化学镀镍层厚度,化学镀镍层表面均匀、平整、光滑;并采取独特的真空稳定处理方法,消除镀层应力,解决了铝基碳化硅复合材料化学镀镍层结合力差,化学镀镍反应停滞,化学镀镍层无法持续增厚的难题。
4.本发明采用的技术方案:铝基碳化硅复合材料超厚高磷化学镀镍及稳定处理工艺,包括以下步骤:
5.步骤1):化学除油:先将氧化镁粉用适量的水调成糊状,对铝基碳化硅复合材料进行镀前检测,然后用糊状的氧化镁粉擦拭铝基碳化硅复合材料零件待镀面,之后用流动水冲洗铝基碳化硅复合材料零件至零件表面水膜均匀30s不断裂;
6.步骤2):酸腐蚀:将化学除油后的铝基碳化硅复合材料零件放入酸腐蚀溶液中,溶液工艺参数:温度:75~85℃,时间:1~3min,酸腐蚀后用流水清洗;
7.步骤3):第一次浸锌处理:将零件放入浸锌溶液中,轻轻晃动,第一次浸锌后零件
表面呈稍暗的灰色,并用流水清洗;浸锌溶液参数:温度:15~30℃,第一次浸锌时间:60~120s;
8.步骤4):光泽处理:将第一次浸锌处理后的零件放入光泽处理溶液中,至浸锌层完全溶解呈基体本色,并用流水清洗;光泽处理工艺参数:温度:10~40℃,时间:5~10s;
9.步骤5):第二次浸锌处理:将光泽处理后的零件放入浸锌溶液中进行第二次浸锌处理,第二次浸锌处理后的零件表面呈米黄色,并用流水清洗;其中,温度:15~30℃,第二次浸锌时间:30~60s;
10.步骤6):预镀化学镍:将清洗后的零件放入预镀化学镍槽液中,其中,时间:8~12min,槽液温度:32~38℃,ph值:9.0~9.5,并用流水清洗;
11.步骤7):高磷化学镀镍:将预镀化学镍后的零件放入高磷化学镀镍溶液中进行化学镀镍处理,并用流水清洗;其中,高磷化学镀镍工艺参数:初始温度:80~84℃,时间:3~4h,温度:85~88℃,时间:镀层至规定厚度,ph值:4.6~5.0,沉积速度:8~12μm/h;
12.步骤8):稳定处理:将高磷化学镀镍后的零件放入真空干燥箱进行稳定处理;稳定处理工艺参数:温度:180~200℃,时间:3~4h,真空度:100~200pa
‑1;
13.步骤9):检验:检验零件镀层外观、镀层厚度、镀层结合力、镀层含磷量是否符合。
14.上述步骤1)中,采用洁净的软毛刷蘸取糊状的氧化镁粉擦拭铝基碳化硅复合材料零件待镀面2~3遍。
15.上述步骤2)中,所述酸腐蚀溶液配方:硫酸h2so4:ρ=1.84g/cm3,130~150ml/l。
16.上述步骤3)和步骤5)中,所述浸锌溶液配方:铝上沉锌剂w
‑
2000:500~550ml/l;纯水b类h2o:余量。
17.上述步骤4)中,所述光泽处理溶液配方:40%的硝酸hno3:ρ=1.42g/cm3;氢氟酸hf:ρ=1.12g/cm3,20ml/l。
18.上述步骤6)中,所述预镀化学镍溶液配方:镍离子ni
2+
以碱式碳酸镍形式加入:5.6~6.4g/l;次亚磷酸钠nah2po2·
3h2o:21~27g/l。
19.上述步骤7)中,所述高磷化学镀镍溶液配方:镍离子ni
2+
以硫酸镍形式加入:5.0~6.2g/l,次亚磷酸钠nah2po2·
3h2o:26~33g/l;其中,所述高磷化学镀镍溶液ph值的测试采用经校准的酸度计,测试液需冷却至室温后测量,硫酸镍应根据装载量在镀覆过程中随时分析补加,有规律的补充镀液而保持ph值相对稳定;采用过滤精度不低于5μm的化学镀镍过滤机对高磷化学镀镍溶液进行循环过滤,循环过滤频率为7~10次/h,确保槽液洁净;所述高磷化学镀镍溶液加热方式采用聚四氟乙烯包覆的不锈钢电加热管,并配备pt100温控感应探头,温控精度
±
0.5℃,确保加热可靠、温度均匀。
20.本发明与现有技术相比的优点:
21.本方案是针对高强度、低重量的铝基碳化硅复合材料,通过采用适宜的前处理腐蚀和预镀化学镍工艺,既能去除材料表面的氧化物,又不会产生过腐蚀,提高了镀层的结合力;再通过采用一次浸锌
‑
光泽处理
‑
二次浸锌
‑
预镀化学镍
‑
高磷化学镀镍等工艺,通过温度阶梯升温、主盐浓度的管控等过程控制方法,维持催化反应的正常进行,持续的增厚,以提高化学镀镍层厚度,可将化学镀镍层厚度达到0.15mm,含磷量达到13%,化学镀镍层表面均匀、平整、光滑,结合力良好;并采取独特的真空稳定处理方法,消除镀层应力,解决了铝基碳化硅复合材料化学镀镍层结合力差,化学镀镍反应停滞,化学镀镍层无法持续增厚的
技术难题;可应用在航空航天光学镜片、轴承轴颈、起落架零件;汽车散热器、化工涡轮机叶轮等行业,具有较强的实用性和推广性。
附图说明
22.图1为本发明的工艺流程图;
23.图2为本发明实施例2中的某反射镜超厚高磷化学镀镍处理后的实物图。
具体实施方式
24.以下对本发明实施例作进一步详细描述:
25.实施例1:
26.铝基碳化硅复合材料超厚高磷化学镀镍及稳定处理工艺,如图1所示,包括以下步骤:
27.步骤1):化学除油:先将氧化镁粉用适量的水调成糊状,对铝基碳化硅复合材料进行镀前检测,然后用糊状的氧化镁粉擦拭铝基碳化硅复合材料零件待镀面,之后用流动水冲洗铝基碳化硅复合材料零件至零件表面水膜均匀30s不断裂。其中,采用洁净的软毛刷蘸取糊状的氧化镁粉擦拭铝基碳化硅复合材料零件待镀面2~3遍。
28.步骤2):酸腐蚀:将化学除油后的铝基碳化硅复合材料零件放入酸腐蚀溶液中。所述酸腐蚀溶液配方:硫酸h2so4:ρ=1.84g/cm3,130~150ml/l。溶液工艺参数:温度:75~85℃,时间:1~3min,酸腐蚀后用流水清洗。
29.步骤3):第一次浸锌处理:将零件放入浸锌溶液中,轻轻晃动,第一次浸锌后零件表面呈稍暗的灰色,并用流水清洗;浸锌溶液参数:温度:15~30℃,第一次浸锌时间:60~120s;
30.步骤4):光泽处理:将第一次浸锌处理后的零件放入光泽处理溶液中,至浸锌层完全溶解呈基体本色,并用流水清洗。所述光泽处理溶液配方:40%的硝酸hno3:ρ=1.42g/cm3;氢氟酸hf:ρ=1.12g/cm3,20ml/l。光泽处理工艺参数:温度:10~40℃,时间:5~10s
31.步骤5):第二次浸锌处理:将光泽处理后的零件放入浸锌溶液中进行第二次浸锌处理,第二次浸锌处理后的零件表面呈米黄色,并用流水清洗;其中,温度:15~30℃,第二次浸锌时间:30~60s;
32.步骤3)和步骤5)中,所述浸锌溶液配方:铝上沉锌剂w
‑
2000:500~550ml/l;纯水b类h2o:余量。
33.步骤6):预镀化学镍:将清洗后的零件放入预镀化学镍槽液中,其中,时间:8~12min,槽液温度:32~38℃,ph值:9.0~9.5,并用流水清洗。所述预镀化学镍溶液配方:镍离子ni
2+
以碱式碳酸镍形式加入:5.6~6.4g/l;次亚磷酸钠nah2po2·
3h2o:21~27g/l。
34.步骤7):高磷化学镀镍:将预镀化学镍后的零件放入高磷化学镀镍溶液中进行化学镀镍处理,并用流水清洗。其中,高磷化学镀镍工艺参数:初始温度:80~84℃,时间:3~4h,温度:85~88℃,时间:镀层至规定厚度,ph值:4.6~5.0,沉积速度:8~12μm/h。所述高磷化学镀镍溶液配方:镍离子ni
2+
以硫酸镍形式加入:5.0~6.2g/l,次亚磷酸钠nah2po2·
3h2o:26~33g/l。
35.以下为超厚的高磷化学镀镍过程控制技术:
36.a)高磷化学镀镍液成分的控制
37.硫酸镍是化学镀镍溶液中的主盐,是镀层中镍离子的来源,超厚化学镀镍过程中,镍离子浓度的稳定是确保镀层持续增厚的关键点,应根据装载量在镀覆过程中随时分析补加。高磷化学镀镍液镍盐浓度补充表见表1。
38.表1化学镀镍液镍盐浓度补充表
[0039][0040]
b)高磷化学镀镍液中还原剂的控制
[0041]
还原剂的作用是通过催化脱氢,提供活拨的新生态氢原子,把镍离子还原为金属镍。还原剂的含量对沉积速度的影响较大,随着还原剂浓度的增加,沉积速度加快,但还原剂不能过高,否则镀液易发生自分解,破坏了镀液的稳定性,同时沉积速度也将达到一个极限值。
[0042]
c)高磷化学镀镍槽液ph值的控制
[0043]
高磷化学镀镍槽液ph值偏低,镀层外观颜色发暗,镀层的延展性和结合力将会下降。ph值偏高,镀层中的磷含量降低,甚至会引发镀液自发分解而导致的溶液失效。所以,高磷化学镀镍槽液的ph值的测试采用经校准的酸度计,测试液需冷却至室温后测量,有规律的补充镀液可以保持ph值相对稳定,每班次至少检测一次。
[0044]
d)槽液温度的控制
[0045]
高磷化学镀镍液工作温度范围在(80~88)℃,由于是超厚化学镀镍,初始温度过高,还原反应迅速且剧烈,气体析出强烈,容易在零件表面产生气流痕缺陷;其次会加速镍离子的沉积,表面会产生微观粗糙、针孔,在后续的增厚过程中,会出现凸起、凹坑等缺陷。因此需要严格控制初始温度,确保底层化学镀镍层均匀、致密,为后续持续增厚奠定良好的基础。
[0046]
e)槽液杂质的控制
[0047]
高磷化学镀镍液被硝酸根污染将导致沉积速度变慢,镀层中磷含量低于正常值。此类污染经常发生在硝酸清洗槽体后没有用足够的清水冲洗干净所致。高磷化学镀镍液中的悬浮杂质和固体镍盐颗粒,将会导致镀层表面粗糙,甚至会造成槽液使用寿命的降低。因此使用非金属滤泵,过滤精度不低于5μm的化学镀镍过滤机,对镀液进行循环过滤,循环过滤频率为(7~10)次/h,确保槽液洁净。
[0048]
f)电加热及温控装置要求
[0049]
高磷化学镀镍液的加热方式需采用聚四氟乙烯包覆的不锈钢电加热管,并配备pt100温控感应探头,温控精度
±
0.5℃,确保加热可靠、温度均匀。在每班次生产后,需要将电加热棒取出,并清洁加热棒表面沉积的镍层。
[0050]
步骤8):稳定处理:将高磷化学镀镍后的零件放入真空干燥箱进行稳定处理;稳定处理工艺参数:温度:180~200℃,时间:3~4h,真空度:100~200pa
‑1。
[0051]
步骤9):检验:检验零件镀层外观、镀层厚度、镀层结合力、镀层含磷量是否符合。具体检验方法见表2。
[0052]
表2超厚高磷化学镀镍层质量检验要求
[0053][0054]
实施例2:
[0055]
对于某光学反射镜零件,材料为铝基碳化硅,牌号为sic45/al yb i级,材料标准:q/hitcl001
‑
2010,要求高磷化学镀镍,镀层厚度为(0.12~0.15)mm、含磷量(10.5~13)%,反射镜外表面要求镀层平整,不允许有气孔、疏松、颗粒、划伤、流痕等缺陷,镀层结合力良好。
[0056]
采用本发明工艺流程及工艺方法处理后,反射镜化学镀镍层的外观、镀层厚度、结合力、磷含量四项技术指标,按照《hb/z 5071
‑
2004化学镀镍工艺及质量检验》标准,镀层外观呈半光泽的银白色,镀层无脱落、起皮、起泡;镀层厚度达到(120~140)μm;镀层中磷含量为13%,合格率达到100%。后续进行研抛处理,达到金属镜面的效果,满足用户使用要求,如图2所示。其所使用的表面处理方法、稳定处理工艺及实施结果具有行业先进性和唯一性。
[0057]
本发明是针对高强度、低重量的铝基碳化硅复合材料,通过采用适宜的前处理腐
蚀和预镀化学镍工艺,既能去除材料表面的氧化物,又不会产生过腐蚀,提高了镀层的结合力;再通过采用一次浸锌
‑
光泽处理
‑
二次浸锌
‑
预镀化学镍
‑
高磷化学镀镍等工艺,通过温度阶梯升温、主盐浓度的管控等过程控制方法,维持催化反应的正常进行,持续的增厚,以提高化学镀镍层厚度,可将化学镀镍层厚度达到0.15mm,含磷量达到13%,化学镀镍层表面均匀、平整、光滑,结合力良好;并采取独特的真空稳定处理方法,消除镀层应力;解决了铝基碳化硅复合材料化学镀镍层结合力差,化学镀镍反应停滞,化学镀镍层无法持续增厚的技术难题;可应用在航空航天光学镜片、轴承轴颈、起落架零件,汽车散热器、化工涡轮机叶轮等行业,具有较强的实用性和推广性。
[0058]
上述实施例,只是本发明的较佳实施例,并非用来限制本发明实施范围,故凡以本发明权利要求所述内容所做的等效变化,均应包括在本发明权利要求范围之内。