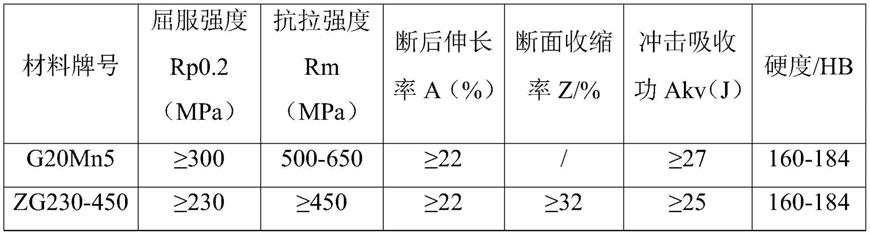
1.本发明涉及铸造技术领域,具体涉及一种消失模陶瓷质空腔壳型铸件及其铸造方法。
背景技术:2.铸造已经有几千年的历史,随着现代技术的发展,对铸件的外观及内在还有尺寸精度,都更加严格。现有的铸造方法包括:砂型铸造、失蜡铸造、消失模铸造、压力铸造等,而这些铸造工艺方法又各有其优缺点。
3.砂型铸造的工艺过程包括:模具
‑
填砂
‑
紧实
‑
起模
‑
刷涂料
‑
下芯子(有芯子)
‑
合箱
‑
浇注
‑
开箱
‑
去除毛刺及浇冒口
‑
热处理
‑
抛丸
‑
打磨修整等。优点:尺寸精度达到ct10
‑
13级,铁砂比为1:4,表面粗糙度一般。缺点:有飞边毛刺,夹砂夹渣多,容易生产气孔等,所带来的严重后果是,铸造的后期,打磨工作量大;而且因为铁砂比大,所以固化物和有害气体的排除总量会很大。该方法适合于批量小且重量大的铸件生产。
4.失蜡铸造的工艺过程包括:模具
‑
涂料
‑
烘干
‑
2次预料
‑
涂料后撒砂
‑
烘干
‑
3次涂料
‑
2次撒砂
‑
烘干
‑
4次涂料
‑
3次撒砂
‑
烘干(总计6
‑
7次涂料,视铸件不同而定)
‑
高温蒸汽脱蜡900
°
~930
°
对壳子烘干
‑
浇注
‑
切割浇冒口(该工艺没有飞边毛刺)
‑
抛丸
‑
焊接
‑
打磨修整等。优点:尺寸精度达到ct6
‑
8级,铁砂比为1:1.6
‑
1.8,表面粗糙度高;该工艺最大优点是不增c(碳)。缺点:工人劳动强度大,固化物排放一般。该方法适合于批量大且重量小的铸件生产。
5.消失模铸造工艺的工艺过程包括:模具
‑
白模
‑
1次涂料
‑
烘干
‑
2次涂料
‑
烘干
‑
3次涂料
‑
烘干
‑
4次涂料
‑
烘干(总计4
‑
5次涂料,视铸件不同而定)
‑
装箱浇注
‑
切割浇冒口(该工艺没有飞边毛刺)
‑
抛丸
‑
焊接
‑
打磨修整等。优点:尺寸精度达到ct6
‑
8级,铁砂比为1:0.4
‑
0.6,表面粗糙度高。缺点:最大缺点是增c(碳)严重,特别是低碳钢和低合金钢铸件;最大可以增c0.6,形成夹渣和气孔的概率大,固化物排放一般;工人劳动强度一般。该方法适合于批量大且重量一般的铸件生产;只适合于铸铁和高碳钢铸件,而低碳钢铸件,因为其增碳的问题,几乎不能采用。
6.空壳浇注工艺采用消失模的模具,失蜡铸造的涂料(制壳),将白模(消失模用的白模)烧掉,再浇注钢水的工艺方法。工艺过程包括:模具
‑
白模
‑
1次涂料
‑
烘干
‑
2次涂料
‑
烘干
‑
3次涂料
‑
烘干
‑
4次涂料
‑
烘干(总计4
‑
5次涂料,视铸件不同而定)
‑
对型壳烘干
‑
焙烧型壳
‑
装箱浇注
‑
切割浇冒口(该工艺没有飞边毛刺)
‑
喷丸
‑
焊接
‑
打磨修整等。优点:尺寸精度达到ct6
‑
8级,铁砂比为1:0.3
‑
0.4,表面粗糙度高;该工艺最大优点是不增c(碳),工人劳动强度小,固化物排放非常低;该工艺具有了失蜡铸造和消失模铸造的优点,也避免了他们的缺点。缺点:成本偏高。该方法适合于批量大,质量要求高,且重量一般的铸件生产。
7.综合分析上述几种铸造工艺:(1)砂型铸造分为无机粘结剂和有机粘结剂二种;无机粘结剂对于低碳铸钢来讲不会增碳,但是落砂,清理,困难,因为工艺问题所产生的披缝会极大增加后道工序的打磨量;而所产生的夹砂/气孔/夹渣又会增加简介修补和打磨量;
有机粘结剂解决了落砂问题,但是却带来了表面增碳和气孔的危害,同时固化物和有害气体排放高。(2)失蜡铸造为无机粘结剂,生产过程工艺稳定,后道清理劳动强度也比较小,但其固化物排放仍然比较大,只能做很小的铸件。(3)消失模铸造已经在铸铁和高碳钢生产中得到大力推广,但是因为增碳的原因,在低碳铸钢件的生产中遇到了非常大的困难,甚至举步维艰。如何将失蜡铸造和消失模铸造的优点结合起来,开发一种新型的铸造工艺,将影响铸件增碳的白模气化,并将残余在壳子表面的c(碳)预先去除,而且保证型壳不开裂和破损,从而达到生产高端铸钢件的目的,是需要解决的问题。
技术实现要素:8.针对现有技术中的缺陷,本发明目的在于提供一种消失模陶瓷质空腔壳型铸件的铸造方法,将影响铸件增碳的白模气化,并将残余在壳子表面的c(碳)预先去除,且保证型壳不开裂和破损;基本无汚染排放,降低劳动强度,大幅降低成本。
9.为实现上述目的,本发明提供的技术方案为:
10.本发明提供了一种消失模陶瓷质空腔壳型铸件的铸造方法,包括步骤:步骤一:将需铸造的铸件进行仿真模拟,根据模拟结果制造白模模具;步骤二:以发泡聚苯乙烯(eps)为原料,利用白模模具制作聚苯乙烯泡沫白模;步骤三:在聚苯乙烯泡沫白模表面涂覆涂料并干燥处理,得到黄模;其中,涂料的原料组分包括三氧化二铝、二氧化硅和木纤维;步骤四:将黄模进行热处理,之后将内腔清理干净,得到空腔壳型;其中,热处理包括升温、液化和烧炭脱碳的步骤;步骤五:将空腔壳型装箱并进行负压浇注金属液,冷却凝固后进行打磨,得到消失模陶瓷质空腔壳型铸件。
11.从砂型铸件模拟结果看,模拟有缺陷时,实际铸造结果肯定会有;但是模拟没有缺陷的时候,结果却不一定没有;对于采用失蜡铸造和消失模铸造两种工艺的结合,在模拟软件中却没有现成的可靠数据,这样就会给模拟造成更大的偏差;本发明采用铸造仿真数值模拟系统对于模拟所需要的数据进行了大量修正和试验,取得预设结果后将模拟结果数据化带入白模模具制造中,可以大大缩小开发周期,提高铸件工艺出品率,减少开发费用。
12.本发明步骤二采用发泡聚苯乙烯(eps)为原料,型号优选为h
‑
s。利用白模模具制作聚苯乙烯泡沫白模,具体包括步骤:(1)预热:打开汽水分配器下排污阀将水排净并关闭;打开上下模型排污阀,供蒸汽加热,当下排污没有水后,关闭上下排污阀;当压力表指示压力达到0.06
‑
0.12mpa后,关闭蒸汽进气阀,打开上下模型排污阀,直到没有蒸汽溢出;开模、吹净消失模模型表面水分;(2)加料:模具处于闭合状态下进料,用射料枪向型腔内加料;(3)融合、加压:打开上下模型排污阀,给汽并见水出净后,把上模降下与下模重合,关闭上下排污阀,压力表压力达到规定压力0.4
‑
0.5mpa时,关闭给气阀,打开上下模型排污阀;(4)冷却、出模:打开给水阀大流量给水(室温水),当模具温度降到手温后,关闭给水阀,开模并通压缩空气起模,冷却时间120
‑
180s。
13.作为优选方案,本发明步骤三中,涂料的原料组分按重量份计,包括:三氧化二铝65
‑
70重量份、二氧化硅18
‑
22重量份、木纤维6.2
‑
6.8重量份;其中,木纤维的长度为0.8
‑
1.5mm;涂料的原料组分优选还包括防腐剂,防腐剂的用量可以根据实际需要进行添加。本发明采用的涂料,可以在失蜡铸造合金钢用涂料(按质量百分比,包括al2o360
‑
65%+sio235%
‑
40%)的基础上添加木纤维和高铝粉(al2o3含量达到80%),并且按需添加防腐
剂,其中失蜡铸造合金钢用涂料、木纤维和高铝粉的重量比为100:0.6:60
‑
70。
14.作为优选方案,本发明步骤四中,热处理具体包括步骤:将黄模在温度小于90℃以下时以小于2℃/min的加热速率缓慢升温,在温度超过90℃后随炉升温至280
‑
320℃,之后保温20
‑
30min,去除液化后的聚苯乙烯液体;继续升温至650℃,使渗入涂层内的聚苯乙烯液体和其它挥发物分解气化完全;之后加热至730℃,保温30min使碳残留全部燃烧干净。本发明采用电阻热处理炉加热,增加喷淋+uv光催化氧化装置,实现去除烟尘、vocs(以非甲烷总烃计),达到达标排放。本发明的热处理包括缓慢升温、液化和烧炭脱碳三个步骤,其中液化阶段,黄模全部液化后将电阻热处理炉车拉出,然后将液化后流出的eps液体收集去出来;其一是重复利用,其二是减少有害气体排放;烧碳、脱碳阶段,当炉内温度到达650℃时,黄模已经全部气化,但是型壳内及内壁上仍然有碳残留;为了去除碳残留,继续加热到730℃并保温30min,将碳残留全部燃烧干净,保证得到的空腔壳型为无机状态。
15.作为优选方案,本发明步骤三中,在聚苯乙烯泡沫白模表面涂覆涂料并干燥处理具体包括步骤:在聚苯乙烯泡沫白模表面涂覆一层涂料,涂料厚度为0.6
‑
0.9mm,之后在湿度≤16%的条件下45℃烘干5
‑
6h;依次重复涂料和烘干4
‑
6次。本发明涂料的总厚度优选维持在3
‑
5mm。本发明在涂料过程中是将聚苯乙烯泡沫白模放置在黄模架(q235钢材料制作)上,每涂料1次,进烘干室烘干一次(烘干室预设温度最高47℃,最低43℃,控制烘干温度45℃,湿度≤16%,烘干时间5
‑
6h,记录起始烘干和终止时间(起始烘干时间从最后一辆烘干小车推入开始计时),每次用游标卡尺测量烘干后浇注系统立面涂料厚度,每一次浸刷涂料,其涂料厚度为0.6
‑
0.9mm,涂料的总厚度优选维持在3
‑
5mm。
16.作为优选方案,本发明步骤二中,还包括将发泡聚苯乙烯进行预发熟化的步骤,其中预发蒸汽压力为0.3
‑
0.4mpa,压缩空气气压≥0.3mpa;预设温度为100℃,预发时间为11
‑
20s,保温时间11s,出料时间6
‑
7s,使所发发泡聚苯乙烯颗粒的密度为30
‑
32g/l,再自然熟化不低于6h。
17.作为优选方案,本发明步骤三中,在聚苯乙烯泡沫白模表面涂覆涂料并干燥处理之前,还包括将在聚苯乙烯泡沫白模上加装浇口和冒口的步骤。
18.作为优选方案,本发明步骤五中,负压浇注过程中保持砂箱中的负压度为
‑
0.03
‑‑
0.045mpa,浇注完成后保压时间≥500s。
19.作为优选方案,本发明步骤五中,装箱过程中,加底砂高100
‑
300mm,放入空腔壳型后内外均匀填砂,塞紧不易紧实的部位,填砂高出空腔壳型45
‑
55mm,刮平、振实;之后覆盖塑料薄膜密封。
20.作为优选方案,本发明步骤五中,打磨步骤包括:清理铸件表面及内腔的飞边、毛刺、浇冒口残留,非加工面要求平整,加工表面控制不超过2mm;削铸件的飞边、毛刺和浇冒口残根,要求平整,没有明显缺肉、凸起。
21.本发明还保护根据上述方法铸造得到的消失模陶瓷质空腔壳型铸件。
22.本发明提供的技术方案具有如下的有益效果:
23.(1)本发明提供的铸造方法非常适合生产内部有超声波或射线探伤要求、表面有磁粉或着色探伤要求、近表面有特殊要求的高端铸件;特别是生产超低碳合金钢(如:c≤0.03%双相不锈钢)铸件不增碳,生产球铁铸件球化率高、夹渣(宏观和微观)等缺陷少。
24.(2)本发明提供的工艺铸造浇注工艺设计灵活,冒口补贴配合冷铁以及激冷砂水
风局部速冷负压振动浇注快速卸压易割保温冒口等等工艺措施,便于消除缩孔缩松缺陷或细化晶粒,很容易保证铸件内部探伤和试压要求(压力试验),可做高端铸件。
25.(3)本发明提供的工艺壳型是高温不粉化不分层的高强硬、高耐火度、高透气性的陶瓷质的数毫米厚的涂层,确保铸件表面和近表面无砂眼、气孔、夹渣等缺陷,铸件后续焊修、打磨工作量大为减少,特别是不锈钢等高合金钢铸件焊补和打磨工作量可降低90%左右,既降低劳动强度、确保铸件外型美观又大幅降低成本,对环境也大为改善。
26.(4)本发明提供的工艺在制作型壳过程中95%以上的泡沫状固态聚苯乙烯塑料变成液态聚苯乙烯塑料,从壳型中流出并回收利用,固态到液态的转变是物理变化过程,既不对环境造成汚染还能废物利用。极少量的分解产物在加热炉中集中收集进入除烟机分解成co2和h2o排放。
27.(5)本发明提供的工艺铸件清理后的少量片状涂层废料,粉磨后可掺于背层涂料利用;消失模铸造的粉状涂料废料混入干砂中,易产生粉尘汚染。因此,本工艺基本无汚染排放,是各种铸造工艺方法中最环保的工艺,是真正意义的绿色铸造。
28.总之,本发明提供的技术方案是结合消失模铸造方法、金属凝固理论、材料科学、铸造工艺学等而研发的高端铸件新工艺,是消失模铸造方法的改进和提升,在eps白模外形上涂覆特殊涂料,制成高强度、高耐火度、高透气性、内壁光滑、尺寸精确的陶瓷质的空腔薄壁壳型,在负压浇注条件下铸造高质量铸件。本工艺与消失模铸造的根本区别在于:消失模铸造是往涂覆涂料的泡沫塑料模型上浇注金属液,本工艺是往清洁的陶瓷质空腔壳型内浇注金属液;因此,两者的应用方式、工艺措施以及铸件质量品次有本质的区别。本工艺可生产各类合金材质的、内在和外观质量高的、几十公斤到数吨重的高端精密铸件,可大幅提高各类铸钢件、球铁件、灰铁件、有色合金件的质量档次,便于在消失模铸造、蜡模精密铸造、各类砂型铸造方面推广运用。
29.本发明的附加方面和优点将在下面的描述中部分给出,部分将从下面的描述中变得明显,或通过本发明的实践了解到。
具体实施方式
30.下面将结合本发明实施例对本发明的技术方案进行清楚、完整地描述。以下实施例仅用于更加清楚地说明本发明的技术方案,因此只是作为示例,而不能以此来限制本发明的保护范围。
31.下述实施例中的实验方法,如无特殊说明,均为常规方法。下述实施例中所用的试验材料,如无特殊说明,均为自常规试剂商店购买得到的。以下实施例中的定量试验,均设置三次重复实验,数据为三次重复实验的平均值或平均值
±
标准差。
32.本发明提供一种消失模陶瓷质空腔壳型铸件的铸造方法,包括如下的步骤。
33.1、铸件仿真模拟:将需铸造的铸件进行仿真模拟,根据模拟结果制造白模模具;本发明对于模拟所需要的数据进行了大量修正和试验,最后获得理想参数,从而大大缩小开发周期,提高铸件工艺出品率,减少开发费用。
34.2、预发熟化:1)预发蒸汽压力达到0.3
‑
0.4mpa,压缩空气气压≥0.3mpa;2)eps材料采用型号h
‑
s;3)开机预热:预设温度100℃;4)发泡时预设置:保证所发eps颗粒的密度达到30
‑
32g/l,预发时间11
‑
20s,保温时间11s,出料时间6
‑
7s;5)每次预发后,使用电子秤称
量,所发颗粒的密度,保证在控制范围内;6)通过管道输送到熟化仓中,自然熟化不低于6h。
35.3、白模成型:1)预热:打开汽水分配器下排污阀将水排净,并关闭;打开上下模型排污阀,供蒸汽加热当下排污没有水后,关闭上下排污阀;当压力表压力达到0.06
‑
0.12mpa后,关闭蒸汽进气阀,打开上下模型排污阀,截止到没有蒸汽溢出;开模、吹净消失模模型表面水分;2)加料:模具处于闭合状态下进料,用射料枪向型腔内加料;3)融合、加压:打开上下模型排污阀,给汽并见水出净后,把上模降下与下模重合,关闭上下排污阀,压力表压力达到规定压力0.4
‑
0.5mpa时,关闭给气阀,打开上下模型排污阀;4)冷却、出模:打开给水阀大流量给水(室温水),当模具温度降到手温后,关闭给水阀,开模并通压缩空气起模,冷却时间120
‑
180s。
36.4、加装浇口和冒口:根据模拟所得数据,在白模上加装浇口和冒口。
37.5、涂料:浸刷涂料5次,形成黄模,放置在黄模架(q235钢材料制作)上,每涂料1次,进烘干室烘干一次(烘干室预设温度最高47℃,最低43℃),控制烘干温度45℃,湿度≤16%,烘干时间5
‑
6h,记录起始烘干和终止时间(起始烘干时间从最后一辆烘干小车推入开始计时),每班次用游标卡尺测量烘干后浇注系统立面涂料厚度,每一次浸刷涂料,其涂料厚度为0.6
‑
0.9mm,浸刷涂料5次计总涂料厚度在3
‑
5mm。传动端压圈和传动端压圈铸件上22个椭圆孔内,在消失模浸刷3道涂料后采用水玻璃砂填实。该步骤中采用的每100kg涂料中,al2o3加入量65
‑
70kg,sio2加入量18
‑
22kg、木纤维加入量6.2
‑
6.8kg(木纤维长度保持在0.8
‑
1.5mm),余量为防腐剂。
38.6、型壳烘干:利用电阻热处理炉加热,增加喷淋+uv光催化氧化装置,实现去除烟尘、vocs(以非甲烷总烃计),达到达标排放。分为缓慢加温、液化、烧炭脱碳3个阶段:缓慢加温阶段(热处理炉温度小于90℃)阶段,加热速度小于2℃/min;液化阶段,温度处于280
‑
320℃时,白模液化,等保温20
‑
30min,白模全部液化后将电阻热处理炉车拉出,然后将液化后流出的eps液体收集去出来;烧碳脱碳阶段,当炉内温度到达650℃时,白模已经全部气化。但是型壳内及内壁上仍然有碳残留,为了去除碳残留,继续加热到730℃并保温30min,将碳残留全部燃烧干净,保证型壳是无机状态。
39.7、内腔清理:型壳随黄模架(不锈钢材料制作)从热处理炉拉出,冷却到室温,出炉后将黄模内腔清理干净,即可等待装箱浇注。
40.8、装箱、抽真空、浇注:1)检查黄模是否完整,有无露白。如发现露白面积≤2mm2的部分用醇基涂料补好;2)准备好锯条、刮砂板、0
‑
600mm卡尺和醇基涂料、合箱胶、连接砂套等;3)推入砂箱、夹紧、顶升;加底砂高约100
‑
300mm,刮平、振实;4)放入黄模,内外均匀填砂,用手塞紧不易紧实的部位,填砂高出黄模50mm左右,刮平、振实;5)覆盖塑料薄膜,加装过滤网,浇口杯;6)填砂、振实台复位,松开夹紧,出箱;7)抽真空,用负压胶管将砂箱和真空分配器连接好;调节真空分配器上的阀门手柄,使之真空压力维持在
‑
0.035~
‑
0.045mpa;8)用热电偶测温枪测量温度、光谱仪分析化学成分,合格后浇注;9)冷却凝固:浇注后保持稳压时间,具体根据铸件情况确定,一般需要保压时间≥500s。
41.9、打磨:浇注后8
‑
10h,出箱进入打磨清理程序:1)设定抛丸机铸件抛丸时间(一般设定为6
‑
8min),备足cw1.5钢丸(规格:φ1.5mm);2)用猫头吊钩牢稳的吊起铸件,按动输送器启动按钮输送铸件到清理室,将抛丸室大门关闭;3)按下自动启动按钮,抛丸机开始工作,丸料闸门开启,顺序处理开始,完成抛丸工作,丸料闸门关闭,将抛丸室大门打开,按动
输送器启动按钮输出铸件到抛丸室外;4)用锤子和錾子等工具清理铸件表面及内腔的飞边、毛刺、浇冒口残留,非加工面要求平整,加工表面控制不超过2mm;5)用砂轮磨削机磨削铸件的飞边、毛刺和浇冒口残根,要求平整,没有明显的缺肉、凸起;6)检验员要对清理后的铸件进行检查,并按产品类别进行分类。
42.下面结合具体实施例对本发明提供的消失模陶瓷质空腔壳型铸件的铸造方法作进一步说明。
43.本实施例提供一种消失模陶瓷质空腔壳型铸件的铸造方法,包括如下的步骤。
44.1、铸件仿真模拟:将需铸造的铸件进行仿真模拟,根据模拟结果制造白模模具。
45.2、预发熟化:1)预发蒸汽压力达到0.35mpa,压缩空气气压0.3mpa;2)eps材料采用型号h
‑
s;3)开机预热:预设温度100℃;4)发泡时预设置:保证所发eps颗粒的密度达到31g/l左右,预发时间15s,保温时间11s,出料时间6s;5)每次预发后,使用电子秤称量,所发颗粒的密度保证在控制范围内;6)通过管道输送到熟化仓中,自然熟化时间不小于6h。
46.3、白模成型:1)预热:打开汽水分配器下排污阀将水排净,并关闭;打开上下模型排污阀,供蒸汽加热当下排污没有水后,关闭上下排污阀;当压力表压力达到0.1mpa后,关闭蒸汽进气阀,打开上下模型排污阀,截止到没有蒸汽溢出;开模、吹净消失模模型表面水分;2)加料:模具处于闭合状态下进料,用射料枪向型腔内加料;3)融合、加压:打开上下模型排污阀,给汽并见水出净后,把上模降下与下模重合,关闭上下排污阀,压力表压力达到规定压力0.4mpa时,关闭给气阀,打开上下模型排污阀;4)冷却、出模:打开给水阀大流量给水(室温水),当模具温度降到手温后,关闭给水阀,开模并通压缩空气起模,冷却时间150s。
47.4、加装浇口和冒口:根据模拟所得数据,在白模上加装浇口和冒口。
48.5、涂料:浸刷涂料5次,形成黄模,放置在黄模架(q235钢材料制作)上,每涂料1次,进烘干室烘干一次(烘干室预设温度45℃,实际运行过程中可能会上下浮动2℃),控制烘干温度45℃,湿度16%,烘干5.5h,记录起始烘干和终止时间,每一次浸刷涂料厚度约为0.8mm,浸刷涂料5次计总涂料厚度4mm。传动端压圈和传动端压圈铸件上22个椭圆孔内,在消失模浸刷3道涂料后采用水玻璃砂填实。该步骤中采用的每100kg涂料中,al2o3加入量68kg,sio2加入量20kg、木纤维加入量6.5kg(木纤维长度保持在1mm左右),余量为防腐剂。
49.6、型壳烘干:利用电阻热处理炉加热,增加喷淋+uv光催化氧化装置,实现去除烟尘、去除vocs(以非甲烷总烃计),达到达标排放。分为缓慢加温、液化、烧炭脱碳3个阶段:缓慢加温阶段(温度小于90℃)阶段,加热速度小于2℃/min;液化阶段,温度达到300℃时,白模液化,保温25min,白模全部液化后将热处理炉车拉出,然后将液化后流出的eps液体收集去出来;烧碳脱碳阶段,当炉内温度到达650℃时,白模已经全部气化。但是型壳内及内壁上仍然有碳残留,为了去除碳残留,继续加热到730℃并保温30min,将碳残留全部燃烧干净,保证型壳是无机状态。
50.7、内腔清理:型壳随黄模架(不锈钢材料制作)从热处理炉拉出,冷却到室温,出炉后将黄模内腔清理干净,即可等待装箱浇注。
51.8、装箱、抽真空、浇注:1)检查黄模是否完整无露白;2)准备好锯条、刮砂板、0
‑
600mm卡尺和醇基涂料、合箱胶、连接砂套等;3)推入砂箱、夹紧、顶升;加底砂高约200mm,刮平、振实;4)放入黄模,内外均匀填砂,用手塞紧不易紧实的部位,填砂高出黄模50mm左右,刮平、振实;5)覆盖塑料薄膜,加装过滤网,浇口杯;6)填砂、振实台复位,松开夹紧,出箱;7)
抽真空,用负压胶管将砂箱和真空分配器连接好;调节真空分配器上的阀门手柄,使之真空压力维持在
‑
0.04mpa;8)用热电偶测温枪测量温度、光谱仪分析化学成分,合格后浇注;9)冷却凝固:浇注后保持稳压时间600s。
52.9、打磨:浇注后9h,出箱进入打磨清理程序:1)设定抛丸机铸件抛丸时间7min,备足cw1.5钢丸(规格:φ1.5mm);2)用猫头吊钩牢稳的吊起铸件,按动输送器启动按钮输送铸件到清理室,将抛丸室大门关闭;3)按下自动启动按钮,抛丸机开始工作,丸料闸门开启,顺序处理开始,完成抛丸工作,丸料闸门关闭,将抛丸室大门打开,按动输送器启动按钮输出铸件到抛丸室外;4)用锤子和錾子等工具清理铸件表面及内腔的飞边、毛刺、浇冒口残留,非加工面要求平整,加工表面控制不超过2mm;5)用砂轮磨削机磨削铸件的飞边、毛刺和浇冒口残根,要求平整,没有明显的缺肉、凸起。
53.本实施例制备得到的铸件能够完全满足地铁永磁电机非传动端压圈和传动端压圈两种压圈铸钢件的要求。中车集团株洲电力机车研究所有限公司用于深圳地铁10号线永磁电机,比传统的异步交流电机节能30%,使用环境按照低温(零下40℃)设计,其中非传动端压圈和传动端压圈两种压圈为铸钢件。
54.材料牌号:g20mn5,执行标准为:《q/xd116
‑
2019牵引电机铸钢件采购规范》,其中化学成分要求如下表1:其中c(%):0.17~0.23,s(%)≤0.020,p(%)≤0.020。
55.表1化学成分要求
56.牌号c(%)si(%)mn(%)cr(%)mo(9%)g20mn50.17
‑
0.23≤0.61.00
‑
1.60≤0.30≤0.12zg230
‑
4500.20
‑
0.300.20
‑
0.500.50
‑
0.90≤0.35≤0.20牌号ni(%)cu(%)p(%)s(%)
‑
g20mn5≤0.80≤0.30≤0.020≤0.020
‑
zg230
‑
450≤0.30≤0.30≤0.040≤0.040
‑
57.力学性能要求如下表2所示:其中低温(零下40℃)冲击吸收功akv(j)≥27j。
58.表2力学性能要求
[0059][0060]
内部质量要求:铸件内部质量检查采用x
‑
射线探伤法。除另有规定外,b类产品不需要进行射线探伤。
[0061]
铸件内部不允许存在裂纹缺陷,其他缺陷应符合以下规定:1)图纸中标明的重要区域的内部质量应符合din1690
‑
v2的质量等级要求;2)其他非重要区域的内部质量应符合din1690
‑
v3的质量等级要求。
[0062]
国内原设计的铸造工艺为水玻璃铸造工艺,存在的问题是铸件表面质量差,22个椭圆孔内几乎无法铸成;采用树脂砂铸造工艺,存在的问题是铸件表面增碳,铸造废品率
高;采用消失模铸造工艺,存在的主要问题是碳缺陷和消失模未全部烧净及残余消失模颗粒形成的残渣,废品率依然很高。
[0063]
砂型铸造,失蜡铸造,消失模铸造三种铸造工艺,很难满足铸件内部质量检查采用x
‑
射线探伤要求,即使通过了探伤检查,但成品率非常低,无法满足客户要求。
[0064]
本发明通过采用消失模空壳铸造工艺,即把消失模白模采用5道涂料浸涂、烘干、涂层厚度、强度、透气性等技术指标达到要求后的黄模,放入热处理炉,按照确定的热处理工艺加热到规定温度、保温后,将黄模中的eps材料烧净,出炉后再清理干净黄模内腔;铸件上22个椭圆孔内,在消失模上就采用水玻璃砂填实,后续工序随黄模,放入热处理炉进行;再按照正常消失模工艺装箱、真空负压浇注;控制电炉熔化铁水质量,包括铁水温度、铁水化学成分;控制铁水出炉温度、浇注温度、浇注时间、浇注速度,即采取减流措施,缓慢浇注,确保平稳浇注。通过以上工艺设计创新,生产的300件压圈订单,全部通过了检验机构的探伤检查。
[0065]
本发明提供的铸造方法不仅彻底克服了消失模铸造铸件的各种特有缺陷,还大幅提高了消失模铸造各类铸钢件、球铁件、灰铁件、有色合金件的质量档次。(1)因白模密度可以更高,铸件尺寸更精确;白模表面泡沫珠粒更致密且微缝隙可被修饰、涂层强度高不被金属液高温粉化冲坏,铸件表面更光洁,近表面(表面以里0
‑
5mm内、或超声波探伤的盲区)亦无夹渣、气孔、夹砂、砂眼等缺陷,打磨和机加工更方便,外观质量更好。(2)非常适合内部有超声波或射线探伤要求、表面有磁粉或着色探伤要求、近表面有特殊要求的高端铸件。特别是,生产超低碳合金钢(如:c≤0.03%双相不锈钢)铸件不增碳,生产球铁铸件球化率高、夹渣(宏观和微观)等缺陷少。(3)因涂层在高温强风快速烘干不开裂变形,生产效率比消失模铸造不仅不降低反而提高,一般从涂覆涂料开始2天内即可浇注。(4)白模和涂层易校正和加强,有利于防止铸件变形。(5)涂层不易潮解软化,型壳损坏率可小与1%,铸件成品率高达98%以上。(6)由于泡沫塑料白模95%以上液化并回收,少量挥发气体易集中除烟处理,更加环保节能。(7)本工艺的缺点是比消失模铸造多一道制壳工序,铸件成型成本也有提高。
[0066]
本发明提供的铸造方法与熔模(蜡模)精密铸造相比两者质量接近,本工艺铸造成本较低、可做中大件、铸造工艺措施灵活:(1)可以铸造单重几十公斤到数吨重的精密铸件。(2)生产效率高,一般从开始上涂料到浇注2天即可。(3)生产成本降低(特别是高合金钢件最明显)。(4)本工艺仅蘸涂料不需撒砂,型壳不宜变形、裂壳、分层和剥落;做复杂大件更具优势;制壳节能。(5)不需红热态浇注,工作条件改善,可实施冷铁等工艺措施、消除铸件缩孔缩松缺陷。(6)型壳薄而轻便,仅为蜡模精铸型壳的1/2
‑
1/3,便于操作,节省材料。(7)制壳过程无酸、碱和气味排放,更环保。(8)涂料对蜡模涂挂性优异、制壳无排放、生产效率高,原精铸模具也可部分利用,增加负压浇注设施便可推广于蜡模精铸做较大铸件。
[0067]
本发明提供的铸造方法与各类砂型铸造相比两者成本接近,而内外质量提高数个级别,本工艺的主要优势:(1)铸件尺寸精度从ct12
‑
14提高为ct5
‑
8;表面粗糙度从ra50
‑
100μm提高为ra12.5
‑
25μm。(2)生产效率比水玻璃砂和各种树脂砂铸造提高1
‑
2倍。(3)不须砂芯、拔模斜度可忽略,铸件壁厚均匀,没有分型面无飞边批缝,铸件尺寸精度高、切割打磨工作量少。(4)做结构复杂铸件上述优势更为突出。(5)铸造浇注工艺设计灵活,冒口补贴配合冷铁以及激冷砂水风局部速冷负压振动浇注快速卸压易割保温冒口等等工艺措施,便于
消除缩孔缩松缺陷或细化晶粒,很容易保证铸件内部探伤和试压要求,可做高端铸件。(6)各类砂型铸造、消失模铸造、v法铸造等,所用涂料均易在浇注金属液时高温粉化被冲刷损坏。本工艺壳型是高温不粉化不分层的高强硬、高耐火度、高透气性的陶瓷质的数毫米厚的涂层,确保铸件表面和近表面无砂眼、气孔、夹渣等缺陷,铸件后续焊修、打磨工作量大为减少,特别是不锈钢等高合金钢铸件焊补和打磨工作量可降低90%左右,既降低劳动强度、确保铸件外型美观又大幅降低成本,对环境也大为改善。(7)对表面有磁粉探伤要求的高端铸件更易保证质量。(8)经涂层加固措施可做数吨重的大件。(9)增加负压浇注设施和泡沫塑料模型便可推广于砂型铸造生产。本工艺不适合推广于自动流水线生产铸铁中小件、有色合金压铸等生产。
[0068]
本发明提供的铸造方法方便耐磨件冒口去除:耐磨合金钢、高锰钢、高铬铸铁等耐磨铸件,均要求较大冒口补缩,由于其硬度高,冒口冷去除非常困难,火焰热割易使铸件断裂,因此,利用其铸态较脆的特性,本工艺配合保温冒口可实现易敲冒口,降低劳动强度、减少成本。
[0069]
本发明提供的铸造方法节能环保,实现真正意义的绿色铸造消失模铸造被公认为“21世纪绿色铸造”,本工艺生产过程比消失模铸造更环保:(1)烟气排放除了两者共同的砂子循环使用不排放外,消失模铸造中聚苯乙烯泡沫塑料白模在浇注过程中被金属液加热100%燃烧或气化,一部分烟气直接排入大气一部分通过真空泵系统简单处理排入大气,对环境有一定汚染。本工艺在制作型壳过程中95%以上的泡沫状固态聚苯乙烯塑料变成液态聚苯乙烯塑料,从壳型中流出并回收利用,固态到液态的转变是物理变化过程,既不对环境造成汚染还能废物利用。极少量的分解产物在加热炉中集中收集进入除烟机分解成co2和h2o排放。(2)本工艺铸件清理后的少量片状涂层废料,粉磨后可掺于背层涂料利用。消失模铸造的粉状涂料废料混入干砂中,易产生粉尘汚染。因此,本工艺基本无汚染排放,是各种铸造工艺方法中最环保的工艺,是真正意义的绿色铸造。
[0070]
本发明提供的铸造方法快速制作铸件样件或单件小批量生产有独特优势:(1)采用3d雕刻泡沫塑料块状白模或3d增材打印空心塑料模+表面修饰+制做涂层壳型+负压浇注,即可在一周内做出样件,样件质量与模具打制白模相近,工期、质量、成本均优于3d打印样件。(2)单件或小批量定单生产,因数量少工期短不宜开模具,可采取手工+多维雕刻机利用泡沫塑料板材制作白模进行生产。(3)利用本工艺的独特优势可以实现智能化和柔性化生产,与互联网结合实施定制化生产和服务。
[0071]
需要注意的是,除非另有说明,本申请使用的技术术语或者科学术语应当为本发明所属领域技术人员所理解的通常意义。除非另外具体说明,否则在这些实施例中阐述的部件和步骤的相对步骤、数字表达式和数值并不限制本发明的范围。在这里示出和描述的所有示例中,除非另有规定,任何具体值应被解释为仅仅是示例性的,而不是作为限制,因此,示例性实施例的其他示例可以具有不同的值。
[0072]
在本发明的描述中,需要理解的是,术语“第一”、“第二”仅用于描述目的,而不能理解为指示或暗示相对重要性或者隐含指明所指示的技术特征的数量。由此,限定有“第一”、“第二”的特征可以明示或者隐含地包括一个或者更多个该特征。在本发明的描述中,“多个”的含义是两个以上,除非另有明确具体的限定。
[0073]
最后应说明的是:以上各实施例仅用以说明本发明的技术方案,而非对其限制;尽
管参照前述各实施例对本发明进行了详细的说明,本领域的普通技术人员应当理解:其依然可以对前述各实施例所记载的技术方案进行修改,或者对其中部分或者全部技术特征进行等同替换;而这些修改或者替换,并不使相应技术方案的本质脱离本发明各实施例技术方案的范围,其均应涵盖在本发明的保护范围当中。