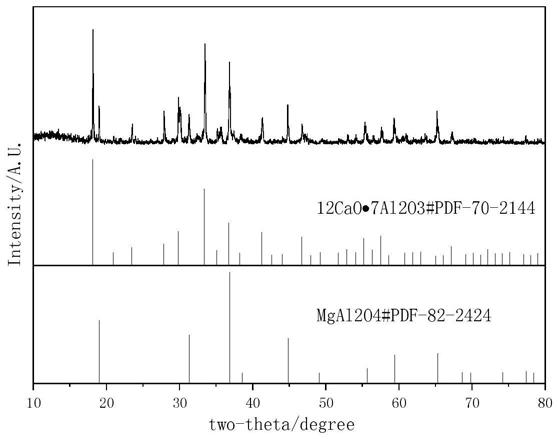
1.本发明涉及一种铝酸钙炼钢脱硫剂的制备方法,特别涉及一种利用高镁铝灰渣为原料,通过惰性化除杂结合高温固相反应制备铝酸钙炼钢脱硫剂的方法,属于再生金属领域和固体废弃物综合利用领域。
背景技术:2.铝灰渣是金属铝及铝合金生产加工以及回收利用过程中形成的含铝废渣,由于其中含有大量的金属铝,通常采用炒灰等方法进行回收;在炒灰过程中需要加入大量氯化钾、氯化钠为主的熔盐,降低体系熔点及表面张力,提高分离效率。经过炒灰之后的灰渣,铝主要为氧化铝、氮化铝、碳化铝及少量单质铝,此外还含有大量的氯盐、氟化物、氮化物等毒害物质。2019年生态环境部发布的《国家危险废物名录(修订稿)》已经明确将铝生产加工过程产生的各类铝灰纳入危险废物。每生产一吨原生铝或者再生铝,会形成10~20%的铝灰渣;目前国内铝工业年产能为3000~4000万吨,据不完全统计,每年产生的铝灰渣高达500万吨以上。
3.传统的铝灰渣综合利用工艺,多以回收金属铝或者惰性氧化铝为目标,采用水浸分离可溶盐的同时,将部分氮化物、碳化物水解惰化转化为氧化铝,最后将惰化渣作为高氧化铝原料用于制备陶瓷、耐火材料、或者氧化铝的生产原料等。
4.随着再生铝行业发展,废旧铝制品的综合回收成为未来铝工业发展的趋势。在变形铝合金和铸造铝合金中,除了主要金属铝组分之外,合金相中还有大量的镁、硅等其他合金组分,在熔铸再生过程中,合金中的硅、镁合金组分同时会发生氧化进入铝灰渣中,甚至在高温条件下与氧化铝反应生产铝镁尖晶石等高熔点物质,给后续的加工处置带来困难。
技术实现要素:5.针对现有铝灰渣综合处置工艺复杂、综合经济价值低等缺陷,本发明的目的是在于提供一种以高镁铝灰渣为原料通过湿法惰化/活化结合高温固相反应获得铝酸钙炼钢脱硫剂的方法,该方法通过湿法惰化/活化实现铝灰渣中有害物质分解脱除和可溶盐的分离,有用铝成分惰化为高活性、大比表面积的氢氧化铝,再结合高温焙烧实现尖晶石高效分解以及铝酸钙系物质的生成,该方法操作简单,合成温度低,原料转化率高,生产成本低,环境友好,满足工业化生产要求。
6.为了实现上述技术目的,本发明提供了一种高镁铝灰渣熔制铝酸钙炼钢脱硫剂的方法,该方法是将高镁铝灰渣在碱性条件下进行湿式球磨,所得湿式球磨物料经过固液分离,所得固体产物与钢渣及消石灰进行干式球磨,所得干式球磨物料进行焙烧处理,即得铝酸钙产品。
7.本发明技术方案以高镁铝灰渣为原料,为实现其中有害组分的无害化处理和有价组分铝的综合利用增值加工,采用湿式球磨惰化和除杂、原料组分调控以及高温固相反应强化转化的协同处理过程,湿式球磨过程实现其中氮、碳、可溶盐的脱除和有用铝成分的转
化和活化,配料添加的钢渣和消石灰等活性物质可促进合成铝酸钙过程固相反应顺利进行,最终降低了合成温度,提高尖晶石的分解率及铝酸钙的生成率。高温固相反应中生成的硅钙镁铝氧化物体系具备较低的熔点,这些低熔点物质的形成可促进液相润湿、扩散作用,从而强化尖晶石的分解;同时部分氧化铝游离出来,进一步与氧化钙结合形成铝酸钙。
8.作为一个优选的方案,所述高镁铝灰中氧化镁质量百分比含量为6~12%,铝元素质量百分比含量不低于50%。高镁铝灰渣中的铝是主要有价组分,其物相组成为金属铝、氧化铝、氮化铝和碳化铝等,制备铝酸钙的前提是将这些物相中的铝转化为氧化铝;高镁铝灰中的镁主要来源于铝合金熔融再生过程中铝、镁的氧化,高温过程中,大量金属相的镁氧化为氧化镁,进而大部分与氧化铝反应生产镁铝尖晶石;尖晶石和氧化镁结构稳定,且熔点高于2000℃,直接进入炼钢脱硫渣系对其粘度及脱硫性能起不利作用,另外,常规条件下尖晶石难以分解或者与其他物质发生反应,因此氧化镁含量过高不利于合成铝酸钙。
9.作为一个优选的方案,所述湿式球磨控制ph值为12~13.5,球磨液固比为2~1.2ml:1g,球磨转速为5~100r/min,球磨时间为3~5h。优选的球磨转速为10~50r/min。优选在碱性条件下进行湿法球磨,可以在机械力作用下促进金属铝、氮化铝、碳化铝的协同转化,强化金属铝氧化、氮化铝和碳化铝分解,生成高活性的氢氧化铝,同时氮化铝、碳化铝中的有害元素氮和碳转化为气体;碱性条件下,有助于碱性气体氨气和甲烷等的溢散,从而实现含铝物质的惰化和无害化处理;球磨过程起到搅拌、混匀和机械活化作用,可显著提高惰化产物中氢氧化铝和镁铝尖晶石的活性,促进后续焙烧过程中铝氧化物、尖晶石与添加剂的固相反应,强化尖晶石的分解。与此同时,在湿式球磨过程中可溶盐随溶液被洗涤和分离,实现杂质的有效脱除。湿式球磨的球磨介质为水。
10.作为一个优选的方案,固体产物与钢渣及消石灰的配料满足:摩尔比mg:si=1:1.2~1.5,且al:(ca+mg)=1:1.18~1.26。由于高镁铝灰中的氧化镁及镁铝尖晶石的熔点高,为降低体系熔点,促进尖晶石分解及铝酸钙的生成,本发明通过添加适量的含硅熔剂,一般的天然硅石矿物中的二氧化硅结构致密、反应性差,不利于固相反应进行。而钢渣中的主要组成为硅酸钙系物质,体系物料熔点相对低,反应活性强,可以实现在较低的反应温度下实现铝镁尖晶石的转化,转化产物为硅钙镁铝复合氧化物,熔点低于1300℃;另外氧化铝与氧化钙结合形成七铝十二钙为主的低熔点化合物。消石灰有助于物料的聚集,在后续高温固相反应过程中有助于铝镁尖晶石的转化和铝酸钙生成。
11.作为一个优选的方案,所述焙烧处理的条件为:在空气气氛下,于1350~1400℃温度下,焙烧90~120min。混合物料中活化后的氢氧化铝、镁铝尖晶石、钢渣、消石灰均具备优良的反应性,可在低于样品熔点的条件下发生固相反应,形成前驱体物质,最终焙烧产物为镁铝黄长石和铝酸钙系列物质的混合物、此外还含有少量的液相物质。合成产品熔点低于1450℃,铝酸钙含量高于60%,是优良的预熔型炼钢脱硫剂。
12.本发明的干式球磨为常规的球磨过程,起到将物料粉化和混合均匀的作用。
13.相对现有技术,本发明的技术方案带来的有益效果:
14.1)本发明以工业固废铝灰渣为原料,在无害化综合处置的同时实现增值加工,制备出可以作为炼钢脱硫剂的铝酸钙系列产品,获得较高的经济价值;
15.2)本发明通过湿法惰化/活化,实现铝灰渣中有害物质分解脱除和可溶盐的分离,惰化后的产物为高活性、大比表面积的氢氧化铝,为后续烧结合成铝酸钙及尖晶石高效分
解创造了条件;
16.3)本发明通过原料组分调控以及高温焙烧条件控制,实现固相/液相反应同步进行,中间液相的生成可协同调控硅钙镁铝复合氧化物的生成及转化,强化铝酸钙系列物质的生成,降低体系反应温度,提高转化率。
附图说明
17.图1为对比例1制备的铝酸钙脱硫剂产品xrd图;
18.图2为实施例1制备的铝酸钙脱硫剂产品xrd图。
具体实施方式
19.以下实施例旨在进一步说明本发明内容,而不是限制本发明权利要求的保护范围。
20.对比例1:
21.以某再生铝厂铝灰(铝含量58.2%、氧化镁含量6.0%)为原料,将铝灰与添加剂进行配料,包括钢渣(氧化钙含量45.0%、硅含量15.3%)、消石灰(氧化钙理论含量72.8%)两种,其配料量控制在混合物料mg:si摩尔比1:1.2,al:(ca+mg)=1:1.26;将干燥后的物料混匀后置于干式球磨机中混匀充分,最后将活化后的物料置于空气气氛进行焙烧,焙烧温度1350℃,焙烧时间120min,对烧制产品进行检测。检测产品铝酸钙理论含量30.5%,镁铝尖晶石转化率40.6%,产品熔点为1685℃。无湿式球磨活化过程,铝酸钙转化率低、尖晶石难分解,产品熔点高,无法制备成炼钢脱硫剂。如附图1所示,产品中含有大量尖晶石衍射峰。
22.对比例2
23.以某再生铝厂铝灰(铝含量58.2%、氧化镁含量6.0%)为原料,将高镁铝灰渣首先在碱性条件下进行湿式球磨惰化,湿式球磨碱性条件ph值为12.0,球磨液固比为2:1,球磨转速为10r/min,球磨时间为3h,球磨结束后进行液固分离和洗涤;将分离获得的固体产物与添加剂进行配料,添加剂为消石灰(氧化钙理论含量72.8%),al:ca=1:1.26;将干燥后的物料混匀后置于干式球磨机中混匀充分,最后将活化后的物料置于空气气氛进行焙烧,焙烧温度1350℃,焙烧时间120min,检测产品铝酸钙理论含量48.7%,镁铝尖晶石转化率15.0%,产品熔点为1760℃。在无合适添加剂条件下,铝酸钙转化率低、镁铝尖晶石几乎不分解,产品熔点高,无法作为炼钢脱硫剂使用。
24.对比例3
25.以某再生铝厂铝灰(铝含量58.2%、氧化镁含量6.0%)为原料,将铝灰与添加剂进行配料,包括硅石矿(氧化硅含量91.2%、氧化铝含量2.1%)、消石灰(氧化钙理论含量72.8%)两种,其配料量控制在混合物料mg:si摩尔比1:1.2,al:(ca+mg)=1:1.26;将干燥后的物料混匀后置于干式球磨机中混匀充分,最后将活化后的物料置于空气气氛进行焙烧,焙烧温度1350℃,焙烧时间120min,对烧制产品进行检测。检测产品铝酸钙理论含量13.5%,镁铝尖晶石转化率54.3%,产品熔点为1613℃。硅石矿难以矿化且无湿式球磨活化过程,铝酸钙转化率低、尖晶石难分解,产品熔点高,无法制备成炼钢脱硫剂。
26.实施例1:
27.以某再生铝厂铝灰(铝含量58.2%、氧化镁含量6.0%)为原料,将高镁铝灰渣首先
在碱性条件下进行湿式球磨惰化,湿式球磨碱性条件ph值为12.0,球磨液固比为2:1,球磨转速为10r/min,球磨时间为3h,球磨结束后进行液固分离和洗涤;将分离获得的固体产物与添加剂进行配料,添加剂包括钢渣(氧化钙含量45.0%、硅含量15.3%)、消石灰(氧化钙理论含量72.8%)两种,其配料量控制在混合物料mg:si摩尔比1:1.2,al:(ca+mg)=1:1.26;将干燥后的物料混匀后置于干式球磨机中混匀充分,最后将活化后的物料置于空气气氛进行焙烧,焙烧温度1350℃,焙烧时间120min,烧制的产品即为可用于炼钢脱硫的铝酸钙产品。检测产品铝酸钙理论含量68.7%,镁铝尖晶石转化率99.6%,产品熔点为1385℃。如图2所示,产品中仅存在铝酸钙衍射峰(七铝十二钙)。
28.实施例2
29.以某再生铝厂铝灰(铝含量58.2%、氧化镁含量6.0%)为原料,将高镁铝灰渣首先在碱性条件下进行湿式球磨惰化,湿式球磨碱性条件ph值为13.5,球磨液固比为1.2:1,球磨转速为20r/min,球磨时间为5h,球磨结束后进行液固分离和洗涤;将分离获得的固体产物与添加剂进行配料,添加剂包括钢渣(氧化钙含量45.0%、硅含量15.3%)、消石灰(氧化钙理论含量72.8%)两种,其配料量控制在混合物料mg:si摩尔比1:1.5,al:(ca+mg)=1:1.18;将干燥后的物料混匀后置于干式球磨机中混匀充分,最后将活化后的物料置于空气气氛进行焙烧,焙烧温度1380℃,焙烧时间90min,烧制的产品即为可用于炼钢脱硫的铝酸钙产品。检测产品铝酸钙理论含量69.3%,镁铝尖晶石转化率99.8%,产品熔点为1389℃。
30.实施例3
31.以某再生铝厂铝灰(铝含量63.6%、氧化镁含量12.0%)为原料,将高镁铝灰渣首先在碱性条件下进行湿式球磨惰化,湿式球磨碱性条件ph值为13.0,球磨液固比为1.5:1,球磨转速为30r/min,球磨时间为4h,球磨结束后进行液固分离和洗涤;将分离获得的固体产物与添加剂进行配料,添加剂包括钢渣(氧化钙含量40.0%、硅含量18.2%)、消石灰(氧化钙理论含量73.3%)两种,其配料量控制在混合物料mg:si摩尔比1:1.3,al:(ca+mg)=1:1.20;将干燥后的物料混匀后置于干式球磨机中混匀充分,最后将活化后的物料置于空气气氛进行焙烧,焙烧温度1400℃,焙烧时间100min,烧制的产品即为可用于炼钢脱硫的铝酸钙产品。检测产品铝酸钙理论含量70.5%,镁铝尖晶石转化率99.9%,产品熔点为1396℃。
32.实施例4:
33.以某再生铝厂铝灰(铝含量63.6%、氧化镁含量12.0%)为原料,将高镁铝灰渣首先在碱性条件下进行湿式球磨惰化,湿式球磨碱性条件ph值为12.5,球磨液固比为2.0:1,球磨转速为40r/min,球磨时间为3.5h,球磨结束后进行液固分离和洗涤;将分离获得的固体产物与添加剂进行配料,添加剂包括钢渣(氧化钙含量40.0%、硅含量18.2%)、消石灰(氧化钙理论含量73.3%)两种,其配料量控制在混合物料mg:si摩尔比1:1.5,al:(ca+mg)=1:1.26;将干燥后的物料混匀后置于干式球磨机中混匀充分,最后将活化后的物料置于空气气氛进行焙烧,焙烧温度1400℃,焙烧时间90min,烧制的产品即为可用于炼钢脱硫的铝酸钙产品。检测产品铝酸钙理论含量72.1%,镁铝尖晶石转化率99.9%,产品熔点为1398℃。