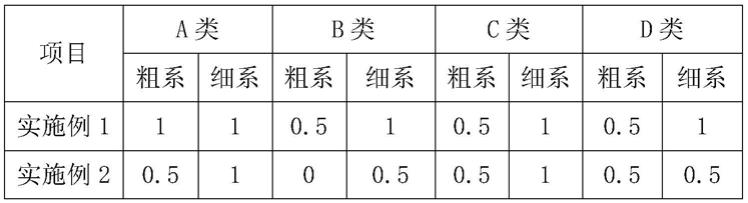
1.本申请涉及钢铁冶炼的技术领域,尤其是涉及一种高纯净度钢及生产工艺。
背景技术:2.铬钼钢广泛应用于机械零件中重要构件的制造,如机车牵引用大齿轮、曲轴、连杆、发动机汽缸、1200至2000米石油深井钻杆接头与打捞工具等。近年来,随着国内外安全监察部门对石油化工、煤化工行业设备安全性和可靠性的日益提高,相关设计单位和制造厂对中高温承压的铬钼钢的化学成分、内部质量和表面质量的要求越来越严格,其中钢质纯净度是衡量产品质量优劣的一项关键指标。
3.针对铬钼钢转炉冶炼而言,出钢过氧化情况比较普遍。出钢过程若采用单一加锰系合金和铝粒预脱氧方式,不仅因过氧化条件下铝系强脱氧剂的过早加入会增加铝条的消耗,还会面临大量氧化铝夹杂难以去除等难题,最终对钢水质量造成不利影响。因此,通过改善炼钢工艺来提高铬钼钢水的纯净度尤为重要。
技术实现要素:4.为了降低钢水中的杂质含量,提高钢水的纯净度,本申请提供一种高纯净度钢及生产工艺。
5.第一方面,本申请提供的一种高纯净度钢的生产工艺采用如下的技术方案:一种高纯净度钢的生产工艺,包括转炉初炼、lf精炼、vd真空处理和连铸工序,lf精炼工序包括:(21)进站时在线底吹氩,氩流量为120~140l/min,ar压力为0.35~0.4mpa;(22)然后加入造渣剂和脱氧剂进行第一次通电造渣,采用6级电压,电流28000~30000a,通氩流量为280~300l/min,通氩压力0.35~0.4mpa,送电加热造渣8
‑
12min后取样,添加合金调整成分;造渣剂包括方解石4.5
‑
7.2kg/t钢、萤石0.7
‑
1.1kg/t钢和铝矾土0.3
‑
0.5kg/t钢;(23)调整成分后进行第二次通电,采用4级电压,电流32000~34000a,氩气流量70~90l/min,ar压力0.3~0.35mpa,当钢水温度≥1670℃时,喂入硅钙线。
6.通过采用上述技术方案,在lf炉精炼过程中,全程通入氩气,能够对钢水起到保护作用,在保证钢水正常脱氧的同时,能够降低钢水被再次氧化的情况,从而有助于提高钢水的纯度。
7.造渣剂采用方解石、萤石和铝矾土三种物质协同作用,使得形成的造渣剂吸附夹杂物的能力提升,且加入效率高,与脱氧剂协同配合,能够快速脱氧造白渣,达到优化钢水质量的效果。方解石在高温作用下分解生成cao和co2气体,co2气体产生的气泡破裂后产生冲击波,从而使得造渣剂分散均匀,避免造渣剂结块,增加造渣剂与钢水的反应速度,避免钢水中残留造渣剂中的杂质,从而提高钢水的精度;另一方面,方解石产生的co2气体可以作为发泡剂,在炉渣中迅速开裂为弥散的小气泡,对炉渣起到发泡作用,并且与脱氧剂配
合,能够保持持续发泡,从而快速形成流动性好、发泡效果好的精炼渣。
8.第一次通电造渣过程中采用小电流加热,避免电流过大影响造渣过程,第二次通电增大电流,有助于提高加热速度,从而降低精炼时间。
9.喂入硅钙线使之与钢水中的al2o3反应,生成低熔点的12cao
·
7al2o3利于夹杂的上浮,从而降低钢水中杂质的含量,提高钢水的洁净度。另外,硅钙线与al2o3反应能够降低浇注过程中堵塞中间包水口的情况,较少水口结瘤等生产事故。
10.优选的,所述步骤(22)中方解石、萤石和铝矾土的重量比为(50
‑
60):(8
‑
9):(3
‑
4)。
11.通过采用上述技术方案,方解石粉末含量低,块度均匀,不会对除尘及煤气回收系统的浊环水造成污染,大大降低除尘及煤气回收系统堵塞率。另外,方解石中的碳酸钙含量在98%以上,其中非金属夹杂p、s、si等含量极低,符合现在洁净度钢的需求,对钢水污染低。
12.萤石能够使方解石生产的cao和阻碍cao溶解的2cao.sio2外壳的熔点显著降低,生成3cao.caf2.2sio2,从而有助于加速cao的溶解,迅速改善炉渣流动性。但过多使用萤石会形成严重的泡沫渣,导致喷溅,同时也加剧对炉衬的侵蚀,并污染环境。
13.铝矾土用于调整炉渣成分,使其熔点降低,且铝矾土能够代替部分萤石,降低萤石的用量,在保证钢水质量的情况下,能够降低萤石对对环境造成的污染。
14.因此,经试验发现,方解石、萤石和铝矾土的重量比为(50
‑
60):(8
‑
9):(3
‑
4)时,形成的炉渣流动性较好,且钢水中的杂质含量较低。
15.优选的,所述步骤(22)中脱氧剂包括铝粒0.2
‑
0.21kg/t钢、碳化硅0.3
‑
0.45kg/t钢和电石0.3
‑
0.45kg/t钢。
16.通过采用上述技术方案,铝粒、碳化硅和电石的脱氧强度从强到弱为,铝粒>碳化硅>电石,在精炼初期,炉渣的氧化性较高,加入强的脱氧剂铝粒,在精炼后期炉渣的氧化性弱,但需要保持还原气氛则加入弱脱氧剂碳化硅和电石,因此,脱氧剂的加入顺序为铝粒、碳化硅和电石。另外,al减少钢水中含氧量的同时,和钢中的n能形成细小难溶的aln颗粒,细化钢的晶粒,固定钢中的氮和氧,减轻钢对缺口的敏感性,减小刚到时效性,提高钢的韧性。
17.优选的,所述步骤(23)中的硅钙线喂入量为245
‑
255m,喂线速度为2.5
‑
4.5m/s。
18.优选的,所述转炉初炼工艺采用顶吹氧气和底吹氩气搅拌的复合吹炼法冶炼,顶吹氧气压力为0.8
‑
1.0mpa,底吹前2
‑
4min吹氮气,后切换为底吹氩气,过程加入白灰和白云石全程化渣,吹炼结束时,钢水中c≥0.08%;p≤0.015%;出钢温度:1600
‑
1630℃。
19.优选的,所述加入白灰35kg/t钢和白云石8kg/t钢。
20.通过采用上述技术方案,采用复合吹炼控制转炉内钢水较低的含碳量,出钢时再加入碳提高钢水含碳量,使钢水中含碳量符合后续工艺,从而能够实现钢水中的s、p与氧气在高温下充分反应从钢水中去除,提高钢水的洁净度;加入白灰和白云石便于造渣,从而更加有效去除钢中的有害元素s、p,同时,炉渣能够覆盖在钢水表面,保护钢水不过度氧化,不吸收有害气体,减少有益元素烧坏,在降低钢水中夹杂的同时,保证钢水的质量。
21.优选的,所述转炉初炼工序,转炉出钢过程中不下渣,期间依次加入人造石墨3.3
‑
3.8kg/t、铝条0.7
‑
1.0kg/t、硅锰合金、硅铁合金、高碳铬铁、钼铁;其中,锰元素的收得率为
85%,硅元素的收得率为75%,铬元素的收得率为95%,钼元素的收得率为95%,结束后钢水成分为:c 0.36
‑
0.40%、si 0.15
‑
0.20%、mn 0.55
‑
0.60%、cr 0.95
‑
1.00%、mo 0.15
‑
0.17%、p≤0.015%,余量为fe。
22.通过采用上述技术方案,出钢过程中不下渣,在钢水中含有一定量的炉渣,在进行精炼工作时,由于刚开始温度较低,钢水中会含有大量的磷,此时炉渣能够起到脱磷的作用,从而将转炉中产生的炉渣充分利用,减少了造渣剂的消耗,降低渣量。
23.首先加入人造石墨,人造石墨其会与钢水中的氧反应生成co进行脱氧;而铝条的加入进一步增加钢水中的脱氧效果;然后加入硅锰合金,在钢水中掺有充足人造石墨的环境下,硅锰合金可快速不断地将钢水中feo中的氧脱除,降低钢水中的氧含量。
24.优选的,所述vd真空处理工序,保持吹ar压力0.3~0.4mpa,保证钢水不裸露,软吹10
‑
20min。
25.通过采用上述技术方案,vd炉真空处理,能够保证ar能够从炉底吹入炉内,从而对vd炉内的钢水起到保护作用,避免钢水中的金属再一次被氧化。
26.优选的,所述连铸工序中,连铸开浇前,对中间包进行吹氩处理。
27.通过采用上述技术方案,排除中间包内的空气,减少钢水解除空气的机会,进一步降低钢水中的金属再一次被氧化的情况,提高钢水的洁净度。
28.第二方面,本申请提供一种高纯净度钢,采用如下的技术方案:一种高纯净度钢,所述高纯度钢的化学成分按质量百分比计,c 0.4
‑
0.44%、si 0.2
‑
0.28%、mn 0.6
‑
0.68%、p≤0.02%、s≤0.02%、cr 1.00
‑
1.10%、mo 0.15
‑
0.18%、al 0.005
‑
0.025%,余量为fe。
29.综上所述,本申请包括以下至少一种有益技术效果:1.lf炉精炼过程中全程吹氩,对钢水起到保护作用,保证钢水正常脱氧;同时,造渣剂采用方解石、萤石和铝矾土并限定配比,使得三者协同配合,共同作用,使得形成的造渣剂吸附夹杂物的能力提升,且加入效率高,与脱氧剂协同配合,能够快速脱氧造白渣,达到优化钢水质量的效果;2.喂入硅钙线,使之与钢水中的al2o3反应,生成低熔点的12cao
·
7al2o3利于夹杂的上浮,从而降低钢水中杂质的含量,提高钢水的洁净度。另外,硅钙线与al2o3反应能够降低浇注过程中堵塞中间包水口的情况,较少水口结瘤等生产事故;3.采用复合吹炼控制转炉内钢水较低的含碳量,出钢时再加入碳提高钢水含碳量,使钢水中含碳量符合后续工艺,从而能够实现钢水中的s、p与氧气在高温下充分反应从钢水中去除,提高钢水的洁净度。
具体实施方式
30.以下结合实施例和对比例对本申请作进一步详细说明。实施例
31.实施例1一种采用以下工艺制备的高纯净度钢,包括以下步骤:(一)转炉初炼(11)先向转炉中加入铁水,入炉铁水温度控制在≥1250℃,按质量百分含量计,铁
水中p≤0.120%、含渣量≤0.5%;然后,向铁水中加入废钢,铁水和废钢总加入量为110t,其中废钢为32t;之后,采用顶吹氧气和底吹氩气搅拌复合吹炼12
‑
min,顶吹氧气压力为1.0mpa,底吹前2min吹氮气,后切换为底吹氩气;吹炼过程加入白灰32kg/t钢和白云石9kg/t钢进行造渣,全程化渣,控制炉渣碱度在3.8;吹炼结束时,钢水中c≥0.08%;p≤0.015%;出钢温度:1600℃。
32.(12)出钢,出钢前取样分析,出钢过程中不下渣,出钢过程中当钢水深度为钢包高度1/4时,根据分析结果开始按顺序加入3.8kg/t人造石墨、0.7kg/t的铝条、硅锰合金、硅铁合金、高碳铬铁、钼铁进行调整,其中,锰元素的收得率为85%,硅元素的收得率为75%,铬元素的收得率为95%,钼元素的收得率为95%;钢水深度为钢包高度3/4时,加入400kg白灰,结束后钢水成分为:c 0.36%、si 0.20%、mn 0.55%、cr 1.00%、mo 0.15%、p≤0.015%,余量为fe。
33.(二)lf炉精炼(21)控制进站温度为1510℃,且进站过程中在线底吹氩,氩流量为120l/min,ar压力为0.4mpa;然后加入造渣剂和脱氧剂后进行第一次通电造渣,采用6级电压,电流28000a,通氩流量为300l/min,通氩压力0.35mpa,送电加热造渣12min后测温、取样,按目标成分加入硅铁、硅锰、高碳格铁、钼铁、钛铁、人造石墨等合金进行调整;其中,造渣剂包括方解石4.5kg/t钢、萤石1.1kg/t钢和铝矾土0.3kg/t钢;脱氧剂包括铝粒0.21kg/t钢、碳化硅0.3kg/t钢和电石0.45kg/t钢。
34.(22)调整成分后进行第二次通电,采用4级电压,电流32000a,氩气流量90l/min,ar压力0.3mpa,并在此过程中分2
‑
3批加入白灰,白灰加入总量≥600kg,再视炉渣的流动性补加萤石,调整炉渣流动性;根据炉渣渣量,进行调整碱度,使总渣量保持在12
㎏
/t钢,碱度控制在3.0,并使白渣保持10min,feo<0.5%。
35.(23)当钢水温度≥1570℃,炉渣变白后加入钛铁100kg,钛铁含ti质量百分比为28%
‑
30%,回收率60~70%,出站前成分、温度达到工艺要求后,喂入硅钙线255m,喂线速度2.5m/s,将钢包调出。
36.(三)vd真空处理:(31)将钢包直接放入vd坑,保持吹ar压力0.3mpa,保证钢水不裸露,然后测温、取样;之后开始抽真空处理,抽真空5min后,真空度达到0.5乇以下保持15min,抽真空过程中氩气压力为0.4mpa,真空度达到0.5乇以下后氩气压力为0.3mpa。
37.(32)破空处理:破真空过程中必须关闭氩气,破空结束后吹氩弱搅拌10min后吊包,加碳化稻壳覆盖全渣面,吊包温度为1555℃。
38.(四)连铸工序(41)开浇前对烘烤后的中间包进行吹氩处理,排出中间包内空气,减少钢水接触空气的机会,同时,检查长水口、塞棒、侵入式水口等关键设备氩气密封情况,避免钢水二次氧化,增加夹杂物的含量;(42)然后,将钢水转移到中间包并通过连铸机注铸坯,当中间包钢水液面高度≥300mm开浇,待中间包钢水到2/3高度时加入中包覆盖剂,之后再分两次加入中包覆盖剂,待钢水达到最高后,加入碳化稻壳,使钢水不露红为止,同时整个过程控制连铸中间包钢温度
为1510℃,并利用结晶器保护高碳保护渣,停浇时中间包液面高度≥250mm。浇注后带钢成分为c 0.40%、si 0.28%、mn 0.60%、p≤0.02%、s≤0.02%、cr 1.10%、mo 0.15%、al 0.025%,余量为fe。
39.实施例2一种采用以下工艺制备的高纯净度钢,包括以下步骤:(一)转炉初炼(11)先向转炉中加入铁水,入炉铁水温度控制在≥1250℃,按质量百分含量计,铁水中p≤0.120%、含渣量≤0.5%;然后,向铁水中加入废钢,铁水和废钢总加入量为112t,其中废钢为30t;之后,采用顶吹氧气和底吹氩气搅拌复合吹炼13min,顶吹氧气压力为0.9mpa,底吹前3min吹氮气,后切换为底吹氩气;吹炼过程加入白灰35kg/t钢和白云石8kg/t钢进行造渣,全程化渣,控制炉渣碱度在3.5;吹炼结束时,钢水中c≥0.08%;p≤0.015%;出钢温度:1615℃。
40.(12)出钢,出钢前取样分析,出钢过程中不下渣,出钢过程中当钢水深度为钢包高度1/4时,根据分析结果开始按顺序加入3.5kg/t人造石墨、0.8kg/t的铝条、硅锰合金、硅铁合金、高碳铬铁、钼铁进行调整,其中,锰元素的收得率为85%,硅元素的收得率为75%,铬元素的收得率为95%,钼元素的收得率为95%;钢水深度为钢包高度3/4时,加入400kg白灰,结束后钢水成分为:c 0.38%、si 0.17%、mn 0.58%、cr 0.98%、mo 0.16%、p≤0.015%,余量为fe。
41.(二)lf炉精炼(21)控制进站温度为1520℃,且进站过程中在线底吹氩,氩流量为130l/min,ar压力为0.38mpa;然后加入造渣剂和脱氧剂后进行第一次通电造渣,采用6级电压,电流29000a,通氩流量为290l/min,通氩压力0.38mpa,送电加热造渣10min后测温、取样,按目标成分加入硅铁、硅锰、高碳格铁、钼铁、钛铁、人造石墨等合金进行调整;其中,造渣剂包括方解石6kg/t钢、萤石0.9kg/t钢和铝矾土0.4kg/t钢;脱氧剂包括铝粒0.2kg/t钢、碳化硅0.4kg/t钢和电石0.4kg/t钢。
42.(22)调整成分后进行第二次通电,采用4级电压,电流33000a,氩气流量80l/min,ar压力0.32mpa,并在此过程中分2
‑
3批加入白灰,白灰加入总量≥600kg,再视炉渣的流动性补加萤石,调整炉渣流动性;根据炉渣渣量,进行调整碱度,使总渣量保持在10
㎏
/t钢,碱度控制在3.5,并使白渣保持10min,feo<0.5%。
43.(23)当钢水温度≥1570℃,炉渣变白后加入钛铁110kg,钛铁含ti质量百分比为28%
‑
30%,回收率60~70%,出站前成分、温度达到工艺要求后,喂入硅钙线250m,喂线速度3.5m/s,将钢包调出。
44.(三)vd真空处理:(31)将钢包直接放入vd坑,保持吹ar压力0.35mpa,保证钢水不裸露,然后测温、取样;之后开始抽真空处理,抽真空5min后,真空度达到0.5乇以下保持15min,抽真空过程中氩气压力为0.4mpa,真空度达到0.5乇以下后氩气压力为0.25mpa。
45.(32)破空处理:破真空过程中必须关闭氩气,破空结束后吹氩弱搅拌10min后吊包,加碳化稻壳覆盖全渣面,吊包温度为1560℃。
46.(四)连铸工序(41)开浇前对烘烤后的中间包进行吹氩处理,排出中间包内空气,减少钢水接触空气的机会,同时,检查长水口、塞棒、侵入式水口等关键设备氩气密封情况,避免钢水二次氧化,增加夹杂物的含量;(42)然后,将钢水转移到中间包并通过连铸机注铸坯,当中间包钢水液面高度≥300mm开浇,待中间包钢水到2/3高度时加入中包覆盖剂,之后再分两次加入中包覆盖剂,待钢水达到最高后,加入碳化稻壳,使钢水不露红为止,同时整个过程控制连铸中间包钢温度为1520℃,并利用结晶器保护高碳保护渣,停浇时中间包液面高度≥250mm。浇注后带钢成分为,此时钢水成分为:c 0.42%、si 0.24%、mn 0.64%、cr 1.05%、mo 0.16%、p≤0.015%,余量为fe。
47.实施例3一种采用以下工艺制备的高纯净度钢,包括以下步骤:(一)转炉初炼(11)先向转炉中加入铁水,入炉铁水温度控制在≥1250℃,按质量百分含量计,铁水中p≤0.120%、含渣量≤0.5%;然后,向铁水中加入废钢,铁水和废钢总加入量为115t,其中废钢为25t;之后,采用顶吹氧气和底吹氩气搅拌复合吹炼15min,顶吹氧气压力为0.8mpa,底吹前4min吹氮气,后切换为底吹氩气;吹炼过程加入白灰37kg/t钢和白云石7kg/t钢进行造渣,全程化渣,控制炉渣碱度在3;吹炼结束时,钢水中c≥0.08%;p≤0.015%;出钢温度:1630℃。
48.(12)出钢,出钢前取样分析,出钢过程中不下渣,出钢过程中当钢水深度为钢包高度1/4时,根据分析结果开始按顺序加入3.3kg/t人造石墨、1.0kg/t的铝条、硅锰合金、硅铁合金、高碳铬铁、钼铁进行调整,其中,锰元素的收得率为85%,硅元素的收得率为75%,铬元素的收得率为95%,钼元素的收得率为95%;钢水深度为钢包高度3/4时,加入400kg白灰,结束后钢水成分为:c 0.40%、si 0.15%、mn 0.60%、cr 0.95%、mo 0.17%、p≤0.015%,余量为fe。
49.(二)lf炉精炼(21)控制进站温度为1530℃,且进站过程中在线底吹氩,氩流量为140l/min,ar压力为0.35mpa;然后加入造渣剂和脱氧剂后进行第一次通电造渣,采用6级电压,电流30000a,通氩流量为280l/min,通氩压力0.4mpa,送电加热造渣10min后测温、取样,按目标成分加入硅铁、硅锰、高碳格铁、钼铁、钛铁、人造石墨等合金进行调整;其中,造渣剂包括方解石7.2kg/t钢、萤石0.7kg/t钢和铝矾土0.5kg/t钢;脱氧剂包括铝粒0.21kg/t钢、碳化硅0.45kg/t钢和电石0.3kg/t钢。
50.(22)调整成分后进行第二次通电,采用4级电压,电流34000a,氩气流量70l/min,ar压力0.35mpa,并在此过程中分2
‑
3批加入白灰,白灰加入总量≥600kg,再视炉渣的流动性补加萤石,调整炉渣流动性;根据炉渣渣量,进行调整碱度,使总渣量保持在8
㎏
/t钢,碱度控制在4.5,并使白渣保持10min,feo<0.5%。
51.(23)当钢水温度≥1570℃,炉渣变白后加入钛铁120kg,钛铁含ti质量百分比为28%
‑
30%,回收率60~70%,出站前成分、温度达到工艺要求后,喂入硅钙线245m,喂线速度4.5m/s,将钢包调出。
52.(三)vd真空处理:(31)将钢包直接放入vd坑,保持吹ar压力0.4mpa,保证钢水不裸露,然后测温、取样;之后开始抽真空处理,抽真空3min后,真空度达到0.5乇以下保持15min,抽真空过程中氩气压力为0.5mpa,真空度达到0.5乇以下后氩气压力为0.2mpa。
53.(32)破空处理:破真空过程中必须关闭氩气,破空结束后吹氩弱搅拌10min后吊包,加碳化稻壳覆盖全渣面,吊包温度为1565℃。
54.(四)连铸工序(41)开浇前对烘烤后的中间包进行吹氩处理,排出中间包内空气,减少钢水接触空气的机会,同时,检查长水口、塞棒、侵入式水口等关键设备氩气密封情况,避免钢水二次氧化,增加夹杂物的含量;(42)然后,将钢水转移到中间包并通过连铸机注铸坯,当中间包钢水液面高度≥300mm开浇,待中间包钢水到2/3高度时加入中包覆盖剂,之后再分两次加入中包覆盖剂,待钢水达到最高后,加入碳化稻壳,使钢水不露红为止,同时整个过程控制连铸中间包钢温度为1525℃,并利用结晶器保护高碳保护渣,停浇时中间包液面高度≥250mm。浇注后带钢成分为,此时钢水成分为:c 0.44%、si 0.20%、mn 0.68%、cr 1.00%、mo 0.18%、p≤0.015%,余量为fe。
55.实施例4一种采用以下工艺制备的高纯净度钢,包括以下步骤:与实施例2的区别在于,造渣剂包括方解石5.0kg/t钢、萤石0.9kg/t钢、铝矾土0.3kg/t钢。
56.实施例5一种采用以下工艺制备的高纯净度钢,包括以下步骤:与实施例2的区别在于,造渣剂包括方解石6.0kg/t钢、萤石0.8kg/t钢、铝矾土0.4kg/t钢。
57.对比例1一种采用以下工艺制备的高纯净度钢,包括以下步骤,与实施例2的区别在于,造渣剂中取等量的石灰替换方解石。
58.对比例2一种采用以下工艺制备的高纯净度钢,包括以下步骤,与实施例2的区别在于,造渣剂中取等量的方解石替换萤石。
59.对比例3一种采用以下工艺制备的高纯净度钢,包括以下步骤,与实施例2的区别在于,造渣剂中取等量的萤石替换铝矾土。
60.对比例4一种采用以下工艺制备的高纯净度钢,包括以下步骤,与实施例2的区别在于,脱氧剂中取等量的碳化硅替换铝粒。
61.性能测试(1)对实施例1
‑
5和对比例1
‑
4制得的钢进行性能测试,参照《gbt10516
‑
2005钢中非金属夹杂物含量的测定方法》,对夹杂物评级如表1所示。
62.表1钢夹杂评级表
结合实施例1
‑
5和表1可以看出,实施例1
‑
5中制得的钢的夹杂物a、b、c、d类细系夹杂物均≤1.0,a类粗系夹杂物≤1.0,b、c、d类粗系夹杂物≤0.5;再结合对比例1
‑
4可知,实施例1
‑
5中的各类夹杂物均小于对比例1
‑
4中的各类夹杂物;说明采用本申请的生产工艺制得的钢的纯净度较高,能够有效提高钢的纯净度。
63.(2)根据《gb/t228
‑
2002金属材料室温拉伸试验方法》测定实施例1
‑
5和对比例1
‑
4中的屈服强度(r
m
)和抗拉强度(r
el
),根据astm a370
‑
2016测定冲击试验,结果列于表2。
64.表2钢力学性能测试结果项目rm/mparel/mpa冲击性能/j实施例11181108576实施例21201109880实施例31192108977实施例41210110581实施例51213110983对比例11085101563对比例21090102064对比例31091102165对比例41089101964结合实施例1
‑
5和对比例1
‑
4,并结合表2可以看出,实施例1
‑
5中钢的屈服强度、抗拉强度和冲击性能均优于对比例1
‑
4,说明采用本申请的制备工艺制得的钢具有较好的屈服性能、抗拉性能和抗冲击性能,对钢的力学性能有所改善。
65.以上均为本申请的较佳实施例,并非依此限制本申请的保护范围,故:凡依本申请的结构、形状、原理所做的等效变化,均应涵盖于本申请的保护范围之内。