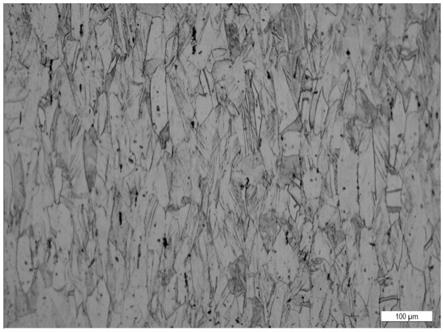
高强高弹ni
‑
cr
‑
co
‑
w基合金丝材及其制备方法
技术领域
1.本发明涉及合金丝材技术领域,尤其是涉及一种高强高弹ni
‑
cr
‑
co
‑
w基合金丝材及其制备方法。
背景技术:2.航空发动机的高温丝材弹簧一般选用gh4169(in718)、gh145(x
‑
750)、gh90(nimonic90)和gh738(waspaloy)等高温合金。但对一些特殊的弹性构件,如滑油系统中的丝材弹簧,上述高温合金因强度或弹性模量不足,无法满足此类弹性构件的使用要求,故而需要选用同时具有更高强度和高弹性模量的高温合金。针对航空发动机特殊弹性构件的材料需求,现已开发出一种高强高弹性模量的镍
‑
铬
‑
钴基高温合金。该合金采取多种强化措施相结合:高含量的w固溶强化、高含量的al、ti弥散强化和时效前冷变形强化。另一方面,冷变形也进一步促进了时效过程中γ
′
相的析出强化。这使该合金具有比其它同类高温合金更高的室温抗拉强度和弹性模量。同时,该合金还具有优异的应力松弛抗力、疲劳强度和在多种腐蚀介质中的耐腐蚀性能,是制造高强度、高弹性构件的理想材料。国内外对多型号航空发动机特殊弹性构件用该合金丝材具有迫切需求。
3.然而该合金的冶金工艺和性能独特,高的合金化程度使该合金的冷、热加工成形非常困难,工艺参数对性能影响非常敏感,具体如下:1)该合金的合金化程度高,脆性大,热加工窗口窄;2)冷加工硬化指数大,中间退火开裂倾向严重;3)丝材冷拔沿径向变形极不均匀,从而导致组织分布异常,即内部正常再结晶组织被浅表层变形量过大而形成的项链状细晶组织包覆;4)丝材供应态的冷变形量与时效工艺对后续弹簧的加工成型和弹力影响非常复杂。目前对该合金丝材加工尚缺乏深入研究,无法顺利制备出满足技术指标要求的丝材以及合格的丝材弹簧,成材率极低。
4.高强度、高弹性构件对航空发动机的安全服役起重要作用,属于使用型号多、用量少、规格品种多、性能要求高而不可替代的关键构件。因此,研究出兼具高强韧性的合金丝材的制备方法对保障关键装备制造具有十分重要的意义,也是本领域亟待解决的问题。
5.有鉴于此,特提出本发明。
技术实现要素:6.本发明的第一目的在于提供高强高弹ni
‑
cr
‑
co
‑
w基合金丝材的制备方法,以解决现有技术中存在的ni
‑
cr
‑
co
‑
w基合金丝材无法兼具高强韧性的技术问题。
7.本发明的第二目的在于提供采用上述制备方法制备得到的高强高弹ni
‑
cr
‑
co
‑
w基合金丝材。
8.为了实现本发明的上述目的,特采用以下技术方案:
9.高强高弹ni
‑
cr
‑
co
‑
w基合金丝材的制备方法,包括如下步骤:
10.(a)按ni
‑
cr
‑
co
‑
w基合金成分配料,进行精炼后浇注得到重熔电极棒;将所述重熔电极棒经真空自耗得到合金锭;其中,所述配料中,包括按质量百分比计的zr 0.05%~
0.1%;
11.(b)将所述合金锭均匀化处理后,于1140~1160℃保温处理后锻造,得到60~80mm方形锭坯,然后加热到1140~1160℃保温1~2h后,热轧成直径为8~12mm的盘条;
12.(c)将所述盘条于1050~1140℃保温处理20~80min后,炉冷至≤600℃后,空冷;然后进行归圆、剥皮和覆膜处理;
13.(d)将步骤(c)处理后的盘条依次进行多火次拉拔和退火直至得到预设直径的合金丝材;其中,每火次变形量范围为20%~60%,退火温度为1050~1120℃;所述多火次拉拔中,末火次变形量为20%~40%。
14.本发明将原料按质量百分比配料后进行真空感应+真空自耗双联冶炼并浇注成合金锭,考虑到合金脆性大,热加工窗口窄,真空冶炼时配入微量元素zr,以提高晶界强度;通过均匀化后锻造成合金锭坯,再进行探伤和精整后热轧为直径φ8~φ12mm的盘条;对盘条进行固溶处理,并进行归圆、剥皮和覆膜;依次进行拉拔和退火,分多次将盘条拉至所要求的合金丝直径,得到该合金丝材成品。
15.本发明对盘条进行特定的固溶处理,降低水淬引起的残余应力,γ
′
析出相粗化增加合金冷拔塑性。
16.在本发明的具体实施方式中,所述真空自耗的同时采用氦气冷却。以增加高温晶界强度,降低元素偏析,提高真空自耗得到的合金锭的热开坯塑性。
17.在本发明的具体实施方式中,所述末火次的变形量为30%~40%,优选为38%~40%。
18.本发明通过控制丝材的终冷变形量在上述范围内,终冷变形量过大,强度高而塑韧性差导致丝材无法绕簧,而终冷变形量过小会导致丝材强度低弹簧成型后弹力不足,因此控制合理的终冷变形量是保证丝材良好综合性能的关键所在。
19.在本发明的具体实施方式中,所述配料中包括按质量百分比计的如下组分:cr 18%~20%、zr 0.05%~0.1%、w 9%~10.5%、al 1.3%~1.8%、ti 2.7%~3.2%、co 5.5%~6.7%、c≤0.05%、mn≤0.4%、ce≤0.05%、b≤0.006%和余量ni及不可避免的杂质。
20.在本发明的具体实施方式中,所述配料中包括按质量百分比计的如下组分:cr 18%~20%、zr 0.05%~0.1%、w 9%~10.5%、al 1.3%~1.8%、ti 2.7%~3.2%、co 5.5%~6.7%、c≤0.05%、si≤0.4%、mn≤0.4%、s≤0.01%、p≤0.015%、fe≤1%、cu≤0.07%、ce≤0.05%、b≤0.006%和余量ni及不可避免的杂质。
21.在本发明的具体实施方式中,所述均匀化处理的温度为1180~1200℃,所述均匀化处理的时间为48~72h。
22.在本发明的具体实施方式中,所述锻造的终锻温度≥1050℃。
23.在本发明的具体实施方式中,所述热轧的终轧温度≥950℃。
24.在本发明的具体实施方式中,所述热轧的温度为950~1140℃。
25.在本发明的具体实施方式中,所述精炼的温度为1490~1550℃。进一步的,所述精炼包括:在0.1~5pa的真空度条件下精炼20~40min,然后于≤0.1pa的真空度条件下精炼10~20min。具体的,还包括:炉料熔清后,在100~200kw条件下搅拌1~3min。
26.在本发明的具体实施方式中,步骤(b)中,于1140~1160℃保温处理0.5~1h后锻
造。
27.在实际操作中,将所述方形锭坯进行探伤、精整处理后,再进行热轧处理。
28.在本发明的具体实施方式中,步骤(d)中,所述退火的保温时间按丝材直径确定,具体为(3.5~4.5)min/mm
×
φmm,其中,φ为待退火处理的丝材的直径。
29.本发明还提供了采用上述任意一种所述的高强高弹ni
‑
cr
‑
co
‑
w基合金丝材的制备方法制得的高强高弹ni
‑
cr
‑
co
‑
w基合金丝材。
30.在本发明的具体实施方式中,所述高强高弹ni
‑
cr
‑
co
‑
w基合金丝材的直径为0.5~1.0mm,优选为0.75~0.85mm,如为0.8mm。
31.在本发明的具体实施方式中,所述高强高弹ni
‑
cr
‑
co
‑
w基合金丝材的冷拔态室温力学性能为:抗拉强度为1500~2100mpa;断后伸长率为3.5%~9.5%。
32.本发明制得的合金丝材具有均匀细晶组织,平均晶粒度细于5级。冷拔及时效后力学性能和工艺性能满足技术指标要求,5倍放大镜目视未发现超标缺陷,能有效保证最终时效后弹簧构件的性能,满足航空发动机等用丝材弹簧的技术指标要求。
33.与现有技术相比,本发明的有益效果为:
34.(1)本发明的ni
‑
cr
‑
co
‑
w基高温合金丝材的制备方法,通过采用适宜的成分,配合特定的拉拔变形量,使丝材兼具强度、弹力、塑韧性,能够在φ1.0mm的芯棒上顺利绕制弹簧,成材率高;
35.(2)采用本发明的制备方法制得的ni
‑
cr
‑
co
‑
w基高温合金丝材尺寸精度高、表面质量好、成分和组织均匀、力学性能和工艺性能优良,兼具高强韧性,可广泛用于航空发动机特殊弹性构件用高温合金丝材加工领域。
附图说明
36.为了更清楚地说明本发明具体实施方式或现有技术中的技术方案,下面将对具体实施方式或现有技术描述中所需要使用的附图作简单地介绍,显而易见地,下面描述中的附图是本发明的一些实施方式,对于本领域普通技术人员来讲,在不付出创造性劳动的前提下,还可以根据这些附图获得其他的附图。
37.图1是实施例1的成品丝材图;
38.图2是实施例1的丝材冷拉态晶粒组织图。
具体实施方式
39.下面将结合附图和具体实施方式对本发明的技术方案进行清楚、完整地描述,但是本领域技术人员将会理解,下列所描述的实施例是本发明一部分实施例,而不是全部的实施例,仅用于说明本发明,而不应视为限制本发明的范围。基于本发明中的实施例,本领域普通技术人员在没有做出创造性劳动前提下所获得的所有其他实施例,都属于本发明保护的范围。实施例中未注明具体条件者,按照常规条件或制造商建议的条件进行。所用试剂或仪器未注明生产厂商者,均为可以通过市售购买获得的常规产品。
40.高强高弹ni
‑
cr
‑
co
‑
w基合金丝材的制备方法,包括如下步骤:
41.(a)按ni
‑
cr
‑
co
‑
w基合金成分配料,进行精炼后浇注得到重熔电极棒;将所述重熔电极棒经真空自耗得到合金锭;其中,所述配料中,包括按质量百分比计的zr 0.05%~
0.1%;
42.(b)将所述合金锭均匀化处理后,于1140~1160℃保温处理后锻造,得到60~80mm方形锭坯,然后加热到1140~1160℃保温1~2h后,热轧成直径为8~12mm的盘条;
43.(c)将所述盘条于1050~1140℃保温处理20~80min后,炉冷至≤600℃后,空冷;然后进行归圆、剥皮和覆膜处理;
44.(d)将步骤(c)处理后的盘条依次进行多火次拉拔和退火直至得到预设直径的合金丝材;其中,每火次变形量范围为20%~60%,退火温度为1050~1120℃;所述多火次拉拔中,末火次变形量为20%~40%。
45.其中,多次拉拔和退火包括:每火次拉拔和每火次拉拔后的退火以及末火次拉拔。即,除末火次拉拔外,其余每火次拉拔后均进行退火,在末火次拉拔后不再进行退火处理,冷拔态交付使用。
46.本发明通过大量研究发现,针对ni
‑
cr
‑
co
‑
w基合金,当终冷变形量过小时,丝材时效后强度不足,弹簧弹力不够;而当终冷变形量过大时,丝材强度高但塑韧性低,无法在φ1.0mm的芯棒上顺利绕制弹簧,成材率极低。
47.本发明通过在真空冶炼时配入一定量的微量元素zr,以提高晶界强度;并配合特定的固溶处理以及多火车拉拔变形量,使制得的合金丝材具有高强韧性,满足特殊弹性构件的使用要求。
48.在研究过程中,当ni
‑
cr
‑
co
‑
w基合金成分配料中不添加zr时,合金热塑性差,无法进行热加工。
49.在实际操作中,当盘条直径≥10mm时,剥皮厚度1~1.5mm,盘条直径<10mm时,剥皮厚度≤0.5mm。
50.在本发明的具体实施方式中,所述真空自耗的同时采用氦气冷却。以增加高温晶界强度,降低元素偏析,提高真空自耗得到的合金锭的热开坯塑性。
51.在本发明的具体实施方式中,所述末火次的变形量为30%~40%,优选为38%~40%。
52.如在不同实施方式中,所述多火次拉拔的次数可以为6~8次。
53.本发明通过控制丝材的终冷变形量在上述范围内,终冷变形量过大,强度高而塑韧性差导致丝材无法绕簧,而终冷变形量过小会导致丝材强度低弹簧成型后弹力不足,因此控制合理的终冷变形量是保证丝材良好综合性能的关键所在。
54.在本发明的具体实施方式中,所述每火次变形量范围为25%~60%。
55.在本发明的具体实施方式中,所述配料中包括按质量百分比计的如下组分:cr 18%~20%、zr 0.05%~0.1%、w 9%~10.5%、al 1.3%~1.8%、ti 2.7%~3.2%、co 5.5%~6.7%、c≤0.05%、mn≤0.4%、ce≤0.05%、b≤0.006%和余量ni及不可避免的杂质。
56.在本发明的具体实施方式中,所述配料中包括按质量百分比计的如下组分:cr 18%~20%、zr 0.05%~0.1%、w 9%~10.5%、al 1.3%~1.8%、ti 2.7%~3.2%、co 5.5%~6.7%、c≤0.05%、si≤0.4%、mn≤0.4%、s≤0.01%、p≤0.015%、fe≤1%、cu≤0.07%、ce≤0.05%、b≤0.006%和余量ni及不可避免的杂质。
57.在本发明的具体实施方式中,所述均匀化处理的温度为1180~1200℃,所述均匀
化处理的时间为48~72h。
58.在本发明的具体实施方式中,所述锻造的终锻温度≥1050℃。
59.在本发明的具体实施方式中,所述热轧的终轧温度≥950℃。
60.在本发明的具体实施方式中,所述热轧的温度为950~1140℃。
61.在本发明的具体实施方式中,所述精炼的温度为1490~1550℃。进一步的,所述精炼包括:在0.1~5pa的真空度条件下精炼20~40min,然后于≤0.1pa的真空度条件下精炼10~20min。具体的,还包括:炉料熔清后,在100~200kw条件下搅拌1~3min。
62.在本发明的具体实施方式中,步骤(b)中,于1140~1160℃保温处理0.5~1h后锻造。
63.在实际操作中,将所述方形锭坯进行探伤、精整处理后,再进行热轧处理。
64.在本发明的具体实施方式中,步骤(d)中,所述退火的保温时间按丝材直径确定,具体为(3.5~4.5)min/mm
×
φmm,其中,φ为待退火处理的丝材的直径。退火的保温时间随着每次拉拔得到的丝材的直径的变化而变化。
65.本发明还提供了采用上述任意一种所述的高强高弹ni
‑
cr
‑
co
‑
w基合金丝材的制备方法制得的高强高弹ni
‑
cr
‑
co
‑
w基合金丝材。
66.在本发明的具体实施方式中,所述高强高弹ni
‑
cr
‑
co
‑
w基合金丝材的直径为0.5~1.0mm,优选为0.75~0.85mm,如为0.8mm。
67.在本发明的具体实施方式中,所述高强高弹ni
‑
cr
‑
co
‑
w基合金丝材的冷拔态室温力学性能为:抗拉强度为1500~2100mpa;断后伸长率为3.5%~9.5%。
68.本发明制得的合金丝材具有均匀细晶组织,平均晶粒度细于5级。冷拔及时效后力学性能和工艺性能满足技术指标要求,5倍放大镜目视未发现超标缺陷,能有效保证最终时效后弹簧构件的性能,满足航空发动机等用丝材弹簧的技术指标要求。
69.实施例1
70.本实施例提供了高强高弹ni
‑
cr
‑
co
‑
w基合金丝材的制备方法,包括如下步骤:
71.(1)按合金成分要求配料,化学成分按质量百分比为:cr 18.5%、al 1.4%、ti 2.80%、w 9.5%、co 6.0%、mn 0.1%、c 0.02%、ce 0.05%、b 0.003%、zr 0.05%,余量为ni。
72.(2)将步骤(1)所配物料于真空炉中进行精炼,在1490~1550℃下,真空度为1pa精炼20min,然后在真空度为0.1pa精炼10min;炉料熔清后采用100kw功率电磁搅拌2min,在温度1490℃下,浇注,获得重熔电极棒。
73.(3)将步骤(2)制得的重熔电极棒经真空自耗得到合金锭;
74.(4)将步骤(3)得到的合金锭进行1190℃条件下保温48h的均匀化处理后,将合金锭在1150℃保温1h后立即开锻,控制终锻温度≥1050℃,经锻造得到80mm
×
80mm
×
l的方坯,经探伤和精整,将方坯加热到1150℃,保温80min,出炉后立即热轧成直径为12mm的盘条,终轧温度≥950℃。
75.(5)将步骤(4)得到的盘条进行固溶处理,具体的,加热温度1050℃,到温将盘条入炉,保温30min后,炉冷至600℃后出炉空冷;
76.(6)将步骤(5)经固溶处理后的盘条进行归圆、剥皮和覆膜,剥皮厚度1~1.5mm;
77.(7)将步骤(6)处理后的盘条依次进行拉拔和退火;具体的中间退火温度和末火次
退火(此处的末火次退火是指在末火次拉拔前的退火)温度均为1050℃,每火次退火的保温时间按丝材直径确定,退火的保温时间为4min/mm,如丝材直径为7mm,则退火的保温时间为28min;具体的拉拔过程为:φ10mm
→
φ7.0mm
→
φ5.2mm
→
φ3.5mm
→
φ2.5mm
→
φ1.6mm
→
φ1.2mm
→
φ1.02mm
→
φ0.8mm,各火次变形量依次为51%、44.8%、54.7%、48.9%、59%、43.8%、27.8%、38.4%。每火次拉拔后对丝材进行上述退火和精整处理,末火次冷变形量为38.4%,末火次拉拔后不再进行退火,冷拔态交付使用。
78.(8)用5倍放大镜对步骤(7)得到的丝材成品的表面进行目视检测。
79.本实施例制得的高强高弹ni
‑
cr
‑
co基合金丝材表面质量好,无裂纹、拉痕等超标缺陷。直径为0.8mm,尺寸精度为
±
0.001mm,椭圆度小于等于0.01mm。
80.实施例2
81.本实施例提供了高强高弹ni
‑
cr
‑
co
‑
w基合金丝材的制备方法,包括如下步骤:
82.(1)按合金成分要求配料,化学成分按质量百分比为:cr 19.5%、al 1.8%、ti 3.20%、w 10.0%、co 6.5%、mn 0.2%、c 0.04%、ce 0.05%、b 0.003%、zr 0.1%,余量为ni。
83.(2)将步骤(1)所配物料于真空炉中进行精炼,在1490~1550℃下,真空度为2pa精炼40min,然后在真空度为0.008pa精炼20min;炉料熔清后采用200kw功率电磁搅拌3min,在温度1550℃下,浇注,获得重熔电极棒。
84.(3)将步骤(2)制得的重熔电极棒经真空自耗得到合金锭;
85.(4)将步骤(3)得到的合金锭进行1190℃条件下保温72h的均匀化处理后,将合金锭在1150℃保温1h后立即开锻,控制终锻温度≥1050℃,经锻造得到60mm
×
60mm
×
l的方坯,经探伤和精整,将方坯加热到1150℃,保温80min,出炉后立即热轧成直径为8mm的盘条,终轧温度≥950℃。
86.(5)将步骤(4)得到的盘条进行固溶处理,具体的,加热温度1120℃,到温将盘条入炉,保温30min后,炉冷至600℃后出炉空冷;
87.(6)将步骤(5)经固溶处理后的盘条进行归圆、剥皮和覆膜,剥皮厚度≤0.5mm;
88.(7)将步骤(6)处理后的盘条依次进行拉拔和退火,具体的中间退火温度和末火次退火(此处的末火次退火是指在末火次拉拔前的退火)温度均为1120℃,退火的保温时间按丝材直径确定,4min/mm;具体的拉拔过程为:φ8mm
→
φ5.5mm
→
φ3.8mm
→
φ2.5mm
→
φ1.6mm
→
φ1.03mm
→
φ0.8mm,各火次变形量依次为52.7%、52.2%、56.7%、59%、58.5%、39.6%。每火次拉拔后对丝材进行上述退火和精整处理,末火次冷变形量为39.6%,末火次拉拔后不再进行退火,冷拔态交付使用。
89.(8)用5倍放大镜对步骤(7)得到的丝材成品的表面进行目视检测。
90.本实施例制得的高强高弹ni
‑
cr
‑
co基合金丝材表面质量好,无裂纹、拉痕等超标缺陷。直径为0.79mm,尺寸精度为
±
0.001mm,椭圆度小于等于0.01mm。
91.比较例1
92.比较例1参考实施例2的制备方法,区别在于:步骤(7)中,具体的拉拔过程为:φ8mm
→
φ5.5mm
→
φ3.8mm
→
φ2.5mm
→
φ1.8mm
→
φ1.3mm
→
φ0.88mm
→
φ0.81mm,各火次变形量依次为52.7%、52.2%、56.7%、48.2%、47.8%、54.2%、15.3%。末火次冷变形量为15.3%。
93.比较例2
94.比较例2参考实施例2的制备方法,区别仅在于:步骤(7)中,具体的拉拔过程为:φ8mm
→
φ5.5mm
→
φ3.8mm
→
φ2.5mm
→
φ1.6mm
→
φ1.12mm
→
φ0.82mm,各火次变形量依次为52.7%、52.2%、56.7%、59%、51.0%、46.4%。末火次冷变形量为46.4%。
95.实验例1
96.对本发明实施例1、实施例2和比较例1、比较例2制得的合金丝材冷拔态及按时效制度(800
±
10℃
×
1小时,700
±
10℃
×
2h,空冷),进行的时效态合金丝材进行力学性能检测,测试结果见表1。
97.表1不同合金丝材的室温力学性能测试结果
[0098][0099]
备注:表1中实施例1~2和比较例1~2的力学性能测试结果分别有两组,是指对同一丝材重复取样两次的测试结果;指标要求中的实测是指无具体指标要求,根据实测结果比较。
[0100]
实施例1的丝材成品按标准进行时效处理后,晶粒度为6.5级。图1是实施例1的成品丝材图,图2是实施例1的丝材冷拉态晶粒组织图。实施例2的丝材成品按标准进行时效处理后,晶粒度为5.0级。
[0101]
最后应说明的是:以上各实施例仅用以说明本发明的技术方案,而非对其限制;尽管参照前述各实施例对本发明进行了详细的说明,本领域的普通技术人员应当理解:其依然可以对前述各实施例所记载的技术方案进行修改,或者对其中部分或者全部技术特征进行等同替换;而这些修改或者替换,并不使相应技术方案的本质脱离本发明各实施例技术方案的范围。