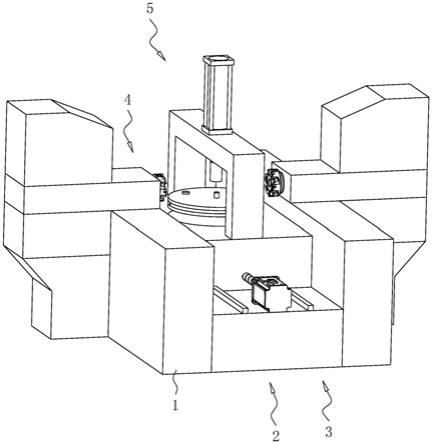
1.本申请涉及材料加工技术的领域,尤其是涉及一种铝合金靶材的制备方法。
背景技术:2.液晶板和有机场致发光板是平板电视、笔记本电脑和监视器中重要组成部分,液晶板和有机场致发光板的薄膜一般采用磁控溅射的方法来沉积制造构成。在磁控溅射过程中,一般采用矩形或圆形的平面靶,通常这种靶材要求较高的加工精度、特定的织构及较高纯度密度,铝合金靶材就是这样的靶材。
3.现有技术中通过将铝锭和稀土金属锭熔炼后铸锭,所得铝合金锭为立方体,铸锭结束后高温退火处理,所得铝合金锭通过双面铣床铣削扒皮后加工为指定尺寸靶材样品。
4.公开号为cn111687456a的中国发明专利申请公开了一种带有旋转工作台的数控双侧铣床,包括床体,床体的上表面两侧均设置有支座,支座朝向另一支座一侧安装有铣刀,两个铣刀同轴设置且处于同一水平面,床体上竖直滑动连接有升降座,升降座上表面转动连接有用于放置工件的旋转盘。
5.对立方体靶材样品进行加工时,将靶材样品放置于旋转盘上,升降座升降从而调整靶材样品高度,铣刀靠近靶材样品然后对靶材样品进行铣削,铣削完成后转动靶材样品对未铣削面进行铣削,重复操作直至完成立方体六个面的铣削。
6.针对上述中的相关技术,发明人认为形成的铝合金内部孔洞数量,从而导致铝合金密度偏低。
技术实现要素:7.为了降低铝合金内部孔洞数量,提高铝合金密度,本申请提供一种铝合金靶材的制备方法。
8.本申请提供的一种铝合金靶材的制备方法采用如下的技术方案:一种铝合金靶材的制备方法,包括以下步骤:s1、将铝锭和稀土金属锭均切割成100mm
×
10mm
×
10mm细条,稀土金属为钕,铝锭和稀土金属锭重量份数之比为95:5,然后表面超声波清洗,烘干,称量装炉,将炉体抽真空至0.01pa级,氧化铝坩埚升温至800~1000℃,真空中频感应熔炼,停电、铜质水冷模浇铸铸锭,随炉冷,破真空取锭,制得尺寸为300mm
×
300mm
×
300mm的铝合金锭;s2、对铝合金锭进行退火处理,退火温度为200~400℃,保温2~5小时,然后使用双面铣床对铝合金锭表面铣削扒皮、切头部缩孔;s3、加热至350~460℃,热锻打至厚度15~30mm,温度低于350℃时需再度加热;s4、加热至350~420℃,热轧处理,道次变形率为40~50%,温度低于350℃时需再度加热;s5、进行去应力退火,退火温度为200~400℃,保温时间为2~5小时,然后机加工获得指定尺寸的铝合金靶材产品;
本申请中铣削扒皮为通过双面铣床将铝合金锭表面氧化层去除;本申请中切头部缩孔为:浇注到模具的过程中会产生气泡,气泡如果在铝合金锭中排不出去,会造成气孔,模具会在头部设计一个冒口,有益于气孔的排出及浇注方便,此冒口中有大量气孔,无法使用,故需要切去此冒口。
9.通过采用上述技术方案,铝锭和金属钕锭浇铸铣削完毕后,经过热锻打和热轧减少铝合金内部孔洞,提高铝合金密度,有效提高靶材性能。
10.可选的,所述双面铣床包括床体,所述床体上水平滑动连接有支撑机构,所述支撑机构滑移方向与铣刀轴向垂直,所述支撑机构内竖直滑动连接有升降机构,所述升降机构上转动连接有转动机构,所述支撑机构上表面设置有用于从上方压紧靶材样品的顶压机构。
11.通过采用上述技术方案,将靶材样品放置于转动机构上,升降机构调整靶材样品在竖直方向上的高度,顶压机构将靶材样品上表面压紧后,铣刀靠近靶材样品,铣刀对靶材样品朝向铣刀的竖直面进行铣削,铣削完毕后铣刀向远离靶材样品方向滑移,转动机构带动靶材样品转过90
°
后,铣刀将未铣削竖直面进行铣削,顶压机构有效增加靶材样品加工过程中的稳定性,从而提高加工精度。
12.可选的,所述竖直固定连接于升降机构上表面的支撑柱,所述支撑柱上同轴转动连接有转动杆,所述转动杆为空心杆,所述转动杆内壁抵接于支撑柱侧壁,所述转动杆背离升降机构一端同轴固定连接有旋转盘,所述旋转盘背离转动杆一侧固定连接有下夹具,所述升降机构上设置有用于驱动旋转盘转动的第二驱动电机。
13.通过采用上述技术方案,将靶材样品放置于下夹具上,第二驱动电机驱动转动盘转动从而带动靶材样品转动,从而使靶材样品转过90
°
,方便对靶材样品未铣削竖直面进行铣削。
14.可选的,所述转动杆侧壁同轴固定连接有蜗轮,所述第二驱动电机主轴上同轴固定连接有蜗杆,所述蜗杆与蜗轮啮合。
15.通过采用上述技术方案,第二驱动电机启动后带动蜗杆转动,蜗杆转动转动驱动蜗轮转动,从而带动转动杆转动,转动杆带动转动盘转动,操作简单方便。
16.可选的,所述升降机构上表面固定连接有支撑环,所述支撑环轴线与旋转盘轴线同轴设置,所述旋转盘朝向升降机构一侧同轴开设有环槽,所述支撑环背离升降机构一端转动连接于环槽内。
17.通过采用上述技术方案,支撑环可以有效减少进入旋转盘与升降机构间隙内的碎屑,从而有效防止碎屑对第二驱动电机以及蜗杆和蜗轮的损伤。
18.可选的,所述顶压机构包括固定连接于升降机构上表面的龙门架,所述龙门架上固定连接有顶压液压缸,所述顶压液压缸轴线竖直设置,所述顶压液压缸活塞杆朝向旋转盘伸缩,所述顶压液压缸活塞杆上同轴转动连接有圆柱形上夹具,所述上夹具轴线与下夹具转动轴线共线设置。
19.通过采用上述技术方案,当旋转盘发生转动时,靶材样品带动上夹具转动,从而使靶材样品转动过程中上夹具始终将靶材样品抵紧,有效提高靶材样品加工过程中的稳定性,提高靶材样品加工精度。
20.可选的,所述上夹具朝向顶压液压缸一端同轴固定连接有第一连接环,所述顶压
液压缸活塞杆朝向上夹具一端同轴固定连接有圆柱形连接块,所述连接块侧壁抵接于第一连接环内壁,所述连接块直径大于顶压液压缸活塞杆直径,所述第一连接环内壁同轴固定连接有第二连接环,所述第二连接环抵接于连接块朝向顶压液压缸一侧。
21.通过采用上述技术方案,上夹具通过连接块、第一连接环和第二连接环连接于顶压液压缸活塞杆上,顶压液压缸活塞杆伸缩带动上夹具上下滑移,从而实现将靶材样品的抵紧和松开,操作简单方便。
22.可选的,所述旋转盘背离转动杆一侧沿与旋转盘轴线垂直方向水平滑动连接有第一支撑盘,所述第一支撑盘背离旋转盘一侧水平滑动连接有第二支撑盘,所述第二支撑盘滑移方向与第一支撑盘滑移方向垂直,所述下夹具固定连接于第二支撑盘背离第一支撑盘一侧,所述第一支撑盘、第二支撑盘和旋转盘均为圆板,当第一支撑盘滑移方向在旋转盘上表面的投影、第二支撑盘在旋转盘上表面的投影以及旋转盘转动轴线两两垂直时,所述第一支撑盘、第二支撑盘和旋转盘同轴设置。
23.通过采用上述技术方案,当上夹具轴线与下夹具转动轴线因安装误差而无法同轴时,旋转盘转动带动靶材样品转动,因上夹具将靶材样品上表面抵紧,第一支撑盘和第二支撑盘在扭矩作用下发生滑移,从而使上夹具与下夹具保持相对静止,减少靶材样品转动过程中因扭矩而偏移的距离,提高靶材样品转动后的精准度,提高加工精度。
24.可选的,所述第二支撑盘上沿与第二支撑盘轴向平行方向开设有通孔,所述通孔在第二支撑盘上偏心设置,当第一支撑盘、第二支撑盘和旋转盘同轴设置时,所述通孔贯穿第一支撑盘、第二支撑盘和旋转盘,所述通孔内竖直滑动连接有辅助杆。
25.通过采用上述技术方案,需要将第一支撑盘和第二支撑盘复位时,滑动第一支撑盘和第二支撑盘,当辅助杆将第一支撑盘、第二支撑盘和旋转盘贯穿时,第一支撑盘、第二支撑盘和旋转盘同轴,操作简单方便。
26.综上所述,本申请包括以下至少一种有益技术效果:1.浇铸铣削后的铝钕合金锭经热锻打和热轧后,有效提高铝钕合金内部密度,减少内部孔洞数量,从而提高靶材样品的质量,有效提高磁控溅射质量;2.靶材试样随旋转盘转动时,因上夹具将靶材样品抵紧,从而减少靶材试样在转动过程中的偏移,且减少加工过程中因铣刀碰触导致靶材样品发生滑移的情况,提高加工精度;3.当上夹具轴线与下夹具轴线不同轴时,靶材样品随旋转盘转动的过程中,靶材样品因扭矩而发生偏移,导致靶材样品无法随旋转盘转过90
°
,铣刀铣削完毕后相邻竖直面无法垂直,从而影响磁控溅射质量,将下夹具变为可随扭矩作用滑移调整位置,使下夹具与上夹具保持相对静止,从而减少靶材样品因扭矩而发生的偏移,提高加工精度和磁控溅射质量。
附图说明
27.图1是本申请实施例4整体结构示意图;图2是本申请实施例4部分结构剖视示意图,主要用于展示支撑机构和升降机构;图3是本申请实施例4部分结构爆炸视图,主要用于展示旋转机构;图4是本申请实施例4部分结构爆炸视图,主要用于展示旋转机构;
图5是图2中a部分的局部放大示意图,主要用于展示上夹具与顶压液压缸连接关系;图6是本申请实施例5整体结构示意图;图7是本申请实施例5部分结构爆炸视图,主要用于展示第一支撑盘、第二支撑盘与旋转盘连接关系;图8是本申请实施例5部分结构爆炸视图,主要用于展示第一支撑盘、第二支撑盘与旋转盘连接关系。
28.附图标记说明:1、床体;11、第一滑槽;2、支撑机构;21、支撑架;211、第二滑槽;22、导轨;24、第一驱动电机;25、驱动丝杠;26、支撑杆;3、升降机构;31、支撑座;32、升降液压缸;4、转动机构;41、支撑柱;42、转动杆;43、旋转盘;431、环槽;432、第三滑槽;44、下夹具;45、蜗轮;46、蜗杆;47、第二驱动电机;48、支撑环;5、顶压机构;51、龙门架;52、顶压液压缸;53、上夹具;54、第一连接环;55、连接块;56、第二连接环;6、第一支撑盘;61、第四滑槽;62、第一滑块;7、第二支撑盘;71、第二滑块;8、通孔;9、辅助杆。
具体实施方式
29.本申请中铝锭采购自北京浩克科技有限公司,纯度为99.99%;金属钕锭采购自北京兴荣源科技有限公司,纯度为99.5%。
30.以下结合附图1
‑
8、实施例1
‑
5和对比例1
‑
3对本申请作进一步详细说明。
31.实施例1本申请实施例公开一种铝合金靶材的制备方法,包括以下步骤,s1、将铝锭和稀土金属锭均切割成100mm
×
10mm
×
10mm细条,稀土金属为钕,铝锭和稀土金属锭重量份数之比为95:5,然后表面超声波清洗,烘干,称量装炉,将炉体抽真空至0.01pa级,氧化铝坩埚升温至800℃,真空中频感应熔炼,停电、铜质水冷模浇铸铸锭,随炉冷,破真空取锭,制得尺寸为300mm
×
300mm
×
300mm的铝合金锭;s2、对铝合金锭进行退火处理,退火温度为200℃,保温2小时,然后使用双面铣床对铝合金锭表面铣削扒皮、切头部缩孔;s3、加热至350℃,热锻打至厚度15mm,温度低于350℃时需再度加热;s4、加热至350℃,热轧处理,道次变形率为40%,温度低于350℃时需再度加热;s5、进行去应力退火,退火温度为200℃,保温时间为2小时,然后机加工获得尺寸为300mm
×
100mm
×
10mm的铝合金靶材产品。
32.实施例2s1、将铝锭和稀土金属锭均切割成100mm
×
10mm
×
10mm细条,稀土金属为钕,铝锭和稀土金属锭重量份数之比为95:5,然后表面超声波清洗,烘干,称量装炉,将炉体抽真空至0.01pa级,氧化铝坩埚升温至900℃,真空中频感应熔炼,停电、铜质水冷模浇铸铸锭,随炉冷,破真空取锭,制得尺寸为300mm
×
300mm
×
300mm的铝合金锭;s2、对铝合金锭进行退火处理,退火温度为300℃,保温3.5小时,然后使用双面铣床对铝合金锭表面铣削扒皮、切头部缩孔;s3、加热至405℃,热锻打至厚度23mm,温度低于350℃时需再度加热;s4、加热至385℃,热轧处理,道次变形率为45%,温度低于350℃时需再度加热;
s5、进行去应力退火,退火温度为300℃,保温时间为3.5小时,然后机加工获得尺寸为300mm
×
100mm
×
10mm的铝合金靶材产品。
33.实施例3s1、将铝锭和稀土金属锭均切割成100mm
×
10mm
×
10mm细条,稀土金属为钕,铝锭和稀土金属锭重量份数之比为95:5,然后表面超声波清洗,烘干,称量装炉,将炉体抽真空至0.01pa级,氧化铝坩埚升温至1000℃,真空中频感应熔炼,停电、铜质水冷模浇铸铸锭,随炉冷,破真空取锭,制得尺寸为300mm
×
300mm
×
300mm的铝合金锭;s2、对铝合金锭进行退火处理,退火温度为400℃,保温5小时,然后使用双面铣床对铝合金锭表面铣削扒皮、切头部缩孔;s3、加热至460℃,热锻打至厚度30mm,温度低于350℃时需再度加热;s4、加热至420℃,热轧处理,道次变形率为50%,温度低于350℃时需再度加热;s5、进行去应力退火,退火温度为400℃,保温时间为5小时,然后机加工获得尺寸为300mm
×
100mm
×
10mm的铝合金靶材产品。
34.对比例1与实施例2不同之处在于,无s3热锻打工序,无s4热轧处理工序,s5中无去应力退火操作。
35.对比例2与实施例2不同之处在于,无s4热轧处理工序。
36.对比例3与实施例2不同之处在于,无s3热锻打工序。
37.实施例1~3和对比例1~3各工序参数见下表
表1实施例1~3和对比例1~3各工序参数表对铝合金靶材进行孔洞数量、晶粒粒径、密度和纯度进行检测。
38.通过c扫描对靶材样品孔洞数量进行检测,具体检测项目为每平方米大于2mm孔数量;通过icp电感耦合等离子光谱发生仪检测靶材样品纯度;通过金相显微镜观测靶材样品晶粒粒径;通过电子比重计检测靶材样品密度。具体检测数据见下表,表2检测数据表根据实施例2、对比例1和对比例2并结合表2可以看出,靶材样品经热锻打处理后,孔洞数量减少,密度增加,且晶粒破碎后粒径减小,有效提高靶材性能。
39.根据实施例2、对比例1和对比例3并结合表2可以看出,靶材样品经热轧处理后,晶粒破碎从而使粒径减小,因孔洞数量较少,从而提高靶材密度,有效提高靶材性能。
40.实施例4本申请实施例4提供一种双面铣床,用于本申请中铝合金锭铣削扒皮。
41.参照图1,一种双面铣床,包括床体1,床体1上设置有支撑机构2,支撑机构2内设置有升降机构3,升降机构3上表面设置有用于放置靶材样品的转动机构4,支撑机构2上表面设置有用于从上方压紧靶材样品的顶压机构5。
42.将靶材样品放置于转动机构4上,顶压机构5将靶材样品抵紧于转动机构4上,加工完相背离的两个竖直侧面后,转动机构4转动带动靶材样品转动,从而使靶材样品水平转过90
°
,顶压机构5减少靶材样品加工过程中的滑移距离,从而提高加工精度。
43.参照图1和图2,床体1内水平开设有第一滑槽11,第一滑槽11长度方向与铣刀轴向垂直。支撑机构2包括滑动连接于第一滑槽11内的支撑架21,支撑架21位于两个铣刀之间,第一滑槽11底壁沿第一滑槽11长度方向固定连接有导轨22,支撑架21滑动连接于导轨22上。第一滑槽11底壁转动连接有驱动丝杠25,驱动丝杠25轴向与导轨22长度方向平行,驱动丝杠25与支撑架21螺纹连接。第一滑槽11底壁固定连接有第一驱动电机24,第一驱动电机24主轴与驱动丝杠25一端同轴固定连接。驱动丝杠25两端均同轴固定连接有轴承,轴承外周侧壁固定连接有支撑杆26,支撑杆26固定连接于第一滑槽11底壁。
44.第一驱动电机24启动后带动驱动丝杠25转动,驱动丝杠25驱动支撑架21滑移,支撑架21滑移带动靶材样品进行滑移,从而使铣刀对靶材样品进行铣削。
45.参照图2,支撑架21内竖直开设有圆柱形第二滑槽211,升降机构3包括竖直滑动连接于第二滑槽211内的支撑座31,支撑座31为轴线竖直设置的圆板,支撑座31侧壁抵接于第二滑槽211侧壁,第二滑槽211内同轴固定连接有升降液压缸32,升降液压缸32缸体固定连接余第二滑槽211底壁,升降液压缸32活塞杆固定连接于支撑座31下表面,升降液压缸32活塞杆伸出推动支撑座31上升。
46.升降液压缸32活塞杆伸出推动支撑座31上升,支撑座31推动转动机构4上升,从而推动靶材样品上升,方便铣刀对靶材样品进行铣削。
47.参照图3和图4,转动机构4包括同轴固定连接于支撑座31上表面的支撑柱41,支撑柱41上同轴套设有空心转动杆42,转动杆42背离支撑座31一端同轴固定连接有旋转盘43,旋转盘43为圆板,旋转盘43轴线为旋转盘43转动轴线,旋转盘43上表面固定连接有下夹具44。转动杆42侧壁同轴固定连接有蜗轮45,支撑座31上表面固定连接有第二驱动电机47,第二驱动电机47主轴上同轴固定连接有蜗杆46,蜗杆46轴线水平设置,蜗杆46与蜗轮45啮合。蜗杆46远离第二驱动电机47一端同轴固定连接有轴承,轴承外周侧壁固定连接有支撑杆26,支撑杆26固定连接于支撑座31上表面。支撑座31上表面同轴固定连接有支撑环48,转动盘朝向支撑环48一侧同轴开设有环槽431,支撑环48背离支撑座31一端转动连接于环槽431内且抵接于环槽431底壁。
48.第二驱动电机47启动带动蜗杆46转动,蜗杆46驱动蜗轮45转动从而带动转动杆42转动,转动杆42带动旋转盘43转动,从而带动靶材样品转动,靶材样品转过90
°
后,铣刀对另外两竖直侧面进行铣削,操作简单方便。
49.参照图2,顶压机构5包括固定连接于支撑架21上表面的龙门架51,龙门架51上竖直固定连接有顶压液压缸52,顶压液压缸52缸体固定连接于龙门架51上,在竖直方向上,顶压液压缸52活塞杆朝向旋转盘43伸缩,顶压液压缸52活塞杆上通过连接组件同轴转动连接有圆柱形上夹具53,上夹具53轴线与旋转盘43转动轴线同轴设置。
50.顶压液压缸52活塞杆伸出推动上夹具53抵接于靶材样品,当旋转盘43发生转动
时,上夹具53始终将靶材样品抵紧,从而减少靶材样品转动过程中的滑移距离,提高加工精度。
51.参照图5,上夹具53朝向顶压液压缸52一端同轴固定连接有第一连接环54,顶压液压缸52活塞杆朝向上夹具53一端同轴固定连接有圆柱形连接块55,连接块55侧壁抵接于第一连接环54内壁,连接块55直径大于顶压液压缸52活塞杆直径,第一连接环54内壁同轴固定连接有第二连接环56,第二连接环56抵接于连接块55朝向顶压液压缸52一侧。
52.当旋转盘43带动靶材样品发生转动时,靶材样品带动上夹具53相对于顶压液压缸52活塞杆发生转动,从而使靶材样品水平转过90
°
。
53.本申请实施例4一种双面铣床的实施原理为:将靶材样品放置于下夹具44上,顶压液压缸52活塞杆伸出使上夹具53将靶材样品上表面抵紧,靶材样品其中两竖直侧面与铣刀轴线垂直,升降液压缸32活塞杆升降从而调整靶材样品在竖直方向上的高度,第一驱动电机24通过驱动丝杠25驱动支撑架21滑移,从而带动靶材样品水平滑移,方便铣刀对靶材样品进行铣削,铣刀将靶材样品的两个竖直侧面铣削完毕后,铣刀离开靶材样品表面。
54.第二驱动电机47启动带动蜗杆46转动,蜗杆46驱动蜗轮45带动转动杆42转动,转动杆42带动旋转盘43转动从而使靶材样品转过90
°
,方便铣刀对另外两竖直侧面进行铣削。
55.靶材样品竖直侧面铣削完毕后,顶压液压缸52活塞杆收回缸体内,带动上夹具53上升,翻转靶材样品后,顶压液压缸52活塞杆伸出使上夹具53将靶材样品抵紧,从而方便铣刀对剩余待铣削面进行铣削。
56.实施例5在实际生产过程中,因存在安装误差,旋转盘43轴线与上夹具53轴线不同轴,从而导致旋转盘43转动时,靶材样品与旋转盘43之间发生相对滑移,转动盘转过90
°
后,靶材样品并未转过90
°
,从而使靶材样品两相邻侧面不垂直,影响加工精度,从而使后续磁控溅射后的薄膜质量不佳。
57.本实施例与实施例4区别之处在于:参照图6和图7,旋转盘43背离转动杆42一侧沿与旋转盘43轴线垂直方向水平滑动连接有第一支撑盘6,第一支撑盘6背离旋转盘43一侧水平滑动连接有第二支撑盘7,第二支撑盘7滑移方向与第一支撑盘6滑移方向垂直,下夹具44固定连接于第二支撑盘7背离第一支撑盘6一侧。第一支撑盘6、第二支撑盘7和旋转盘43均为圆板且直径相等。
58.当旋转盘43发生转动时,靶材样品发生转动,因上夹具53仅以自身轴线为转动轴线转动,第一支撑盘6和第二支撑盘7在扭矩作用下滑移,从而使下夹具44与上夹具53保持相对静止,减少靶材样品在转动过程中的偏移,从而提高加工精度。
59.参照图7和图8,旋转盘43背离转动杆42一侧沿与旋转盘43轴线垂直方向水平开设有第三滑槽432,第三滑槽432穿过旋转盘43轴线,第一支撑盘6朝向旋转盘43一侧固定连接有第一滑块62,第一滑块62滑动连接于第三滑槽432内。第一支撑盘6朝向第二支撑盘7一侧水平开设有第四滑槽61,第四滑槽61长度方向与第三滑槽432长度方向垂直,第二支撑盘7朝向第一支撑盘6一侧固定连接有第二滑块71,第二滑块71滑动连接于第四滑槽61内。
60.参照图7和图8,第一支撑盘6滑移方向在旋转盘43上表面的投影和第二支撑盘7在旋转盘43上表面的投影垂直,二者相交点为原点。第二支撑盘7上竖直开设有通孔8,通孔8偏心设置,当旋转盘43轴线穿过原点时,第一支撑盘6、第二支撑盘7和旋转盘43同轴设置,
通孔8贯穿第一支撑盘6、第二支撑盘7和旋转盘43,通孔8内竖直滑动连接有辅助杆9。加工完毕后滑动第一支撑盘6和第二支撑盘7均与旋转盘43同轴,辅助杆9将三者固定,从而有效减少靶材样品在放置过程中第一支撑盘6和第二支撑盘7滑移距离,从而方便放置靶材样品。
61.本申请实施例5一种双面铣床的实施原理为:将靶材样品放置于下夹具44上,顶压液压缸52活塞杆伸出使上夹具53将靶材样品上表面抵紧,靶材样品其中两竖直侧面与铣刀轴线垂直,升降液压缸32活塞杆升降从而调整靶材样品在竖直方向上的高度,第一驱动电机24通过驱动丝杠25驱动支撑架21滑移,从而带动靶材样品水平滑移,方便铣刀对靶材样品进行铣削,铣刀将靶材样品的两个竖直侧面铣削完毕后,铣刀离开靶材样品表面。
62.第二驱动电机47启动带动蜗杆46转动,蜗杆46驱动蜗轮45带动转动杆42转动,转动杆42带动旋转盘43转动从而使靶材样品转过90
°
,方便铣刀对另外两竖直侧面进行铣削。旋转过程中,在扭矩作用下,第一支撑盘6和第二支撑盘7滑移,从而使上夹具53和下夹具44保持相对静止,减少靶材样品在转动过程中的相对滑移,提高转动角度精准度,从而提高加工精度。
63.靶材样品竖直侧面铣削完毕后,顶压液压缸52活塞杆收回缸体内,带动上夹具53上升,翻转靶材样品后,顶压液压缸52活塞杆伸出使上夹具53将靶材样品抵紧,从而方便铣刀对剩余待铣削面进行铣削。
64.以上均为本申请的较佳实施例,并非依此限制本申请的保护范围,故:凡依本申请的结构、形状、原理所做的等效变化,均应涵盖于本申请的保护范围之内。