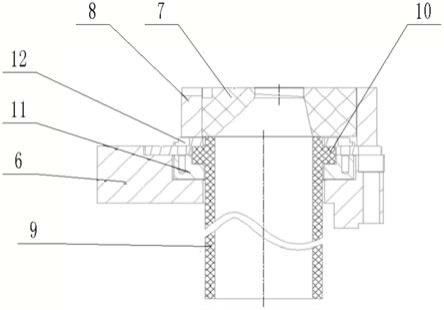
[0001]
本实用新型涉及差压铸造技术领域,特别是涉及一种差压一模多腔升液管。
背景技术:[0002]
当前差压一模多腔(6腔,8腔)铝合金生产工艺,正在普遍应用于铝合金铸造行业,当前差压一模多腔受制设备安装面积,模具布局紧凑,同时坩埚保温炉内径空间有限,使用升液管直径(内径φ60,外径φ80),工艺范围狭窄,传统升液管(硅酸铝)使用寿命一般5-7 天,使用成本高等问题,制约差压铸造行业发展。因此,需设计一种差压一模多腔升液管以解决现有技术存在的问题。
技术实现要素:[0003]
本实用新型的目的是提供一种差压一模多腔升液管,以解决上述现有技术存在的问题,本实用新型可以拓宽铸件的铸造工艺范围,大大降低使用成本。
[0004]
为实现上述目的,本实用新型提供了如下方案:本实用新型提供一种差压一模多腔升液管,包括管体,所述管体一端外侧固接有凸台,所述管体靠近所述凸台的一端相接有中间管,所述中间管外部套接有中间管保护套,所述中间管一端为小口径,所述中间管另一端为大口径,所述中间管大口径的一端与所述管体相接,所述管体的内径与所述中间管大口径尺寸相同,所述中间管小口径的中心线与所述中间管大口径的中心线不重合,所述凸台上下两侧分别设置有上法兰、下法兰,所述上法兰与所述下法兰通过螺栓固定连接,所述下法兰嵌装有炉盖,所述管体贯通所述炉盖,所述中间管嵌装有设备上台板,所述设备上台板上贯通有若干个浇口。
[0005]
优选的,所述中间管内腔一侧设置有r角。
[0006]
优选的,所述管体与所述中间管之间、所述中间管与所述浇口之间均固接有密封层。
[0007]
优选的,所述炉盖下部设置有坩埚炉,所述管体伸入到所述坩埚炉内,所述管体外壁到所述坩埚炉璧之间存在间隔。
[0008]
优选的,所述中间管嵌装有所述设备上台板,所述中间管的长度等于所述设备上台板的厚度。
[0009]
优选的,所述中间管小口径端面到所述坩埚炉底面内璧的距离大于所述管体的长度。
[0010]
本实用新型公开了以下技术效果:
[0011]
本实用新型将通过将管体的直径调整变大,使浇注过程中管体铝液体积增加,管体内铝液总热量增加,浇口温度下降速度放缓,有利于实现铸件自上而下的凝固顺序;通过设置中间管一端为小口径,中间管小口径与浇口内径尺寸相同,中间管另一端为大口径,管体的内径与中间管大口径尺寸相同,中间管小口径的中心线与中间管大口径的中心线不重合,可以将不同心的管体与模具浇口直接连接,保证管体与模具浇口顺畅连接,同时保证模
具浇口位置维持原尺寸不做调整,满足差压模具布局相对紧凑,避免因产品浇口位置较大调整而影响模具整体工艺的缺陷,有利于浇注工艺的稳定进行。
附图说明
[0012]
为了更清楚地说明本实用新型实施例或现有技术中的技术方案,下面将对实施例中所需要使用的附图作简单地介绍,显而易见地,下面描述中的附图仅仅是本实用新型的一些实施例,对于本领域普通技术人员来讲,在不付出创造性劳动性的前提下,还可以根据这些附图获得其他的附图。
[0013]
图1为本实用新型结构示意图;
[0014]
图2为管体、中间管、上法兰、下法兰以及炉盖结构示意图;
[0015]
图3为中间管结构示意图;
[0016]
图4为管体结构示意图;
[0017]
图5为炉盖、管体、法兰结构示意图。
[0018]
其中,1为设备上台板,2为浇口,3为设备下台板,4为坩埚炉, 5为凸肩,6为炉盖,7为中间管,8为中间管保护套,9为管体,10 为凸台,11为下法兰,12为上法兰,13为r角。
具体实施方式
[0019]
下面将结合本实用新型实施例中的附图,对本实用新型实施例中的技术方案进行清楚、完整地描述,显然,所描述的实施例仅仅是本实用新型一部分实施例,而不是全部的实施例。基于本实用新型中的实施例,本领域普通技术人员在没有做出创造性劳动前提下所获得的所有其他实施例,都属于本实用新型保护的范围。
[0020]
为使本实用新型的上述目的、特征和优点能够更加明显易懂,下面结合附图和具体实施方式对本实用新型作进一步详细的说明。
[0021]
参照图1-5,本实用新型提供一种差压一模多腔升液管,包括包括管体9,所述管体9一端外侧固接有凸台10,所述管体9靠近所述凸台10的一端相接有中间管7,所述中间管7外部套接有中间管保护套8,所述中间管7一端为小口径,所述中间管7另一端为大口径,所述中间管7大口径的一端与所述管体9相接,所述管体9的内径与所述中间管7大口径尺寸相同,所述中间管7小口径的中心线与所述中间管7大口径的中心线不重合,所述凸台10上下两侧分别设置有上法兰12、下法兰11,所述上法兰12与所述下法兰11通过螺栓固定连接,所述下法兰11嵌装有炉盖6,所述管体9贯通所述炉盖6。炉盖6上部布设有设备上台板1,设备上台板1下部固接有设备下台板3,设备下台板3中心开设有通孔,通孔内固接有凸肩5,炉盖6 搭接在凸肩5上,设备上台板1上贯通开设有若干个浇口2,中间管 7小口径一端与浇口2相接,中间管7小口径尺寸与浇口2内径相同。
[0022]
进一步优选方案,中间管7内腔一侧设置有r角,若干个管体9 呈圆形阵列排列,管体9的材质优选为氮化硅、碳化硅或钛酸氯。
[0023]
进一步优选方案,管体9与中间管7之间以及浇口2与中间管7 之间均固接有密封层,密封层优选为石棉板或石墨板,中间管7的材质优选为陶瓷。
[0024]
进一步优选方案,管体9外壁到坩埚炉4之间存在间隔,保证管体9与坩埚炉4壁安全距离。
[0025]
进一步优选方案,炉盖6与凸肩5之间通过螺栓固定连接,此处螺栓采用m20-h30。
[0026]
进一步优选方案,浇口2到坩埚炉4底面内璧的距离大于管体9 的长度。
[0027]
本实施例中管体9的数量优选为6个,管体9的尺寸设计为内径φ100mm,外径φ120mm,即适用于差压一模六腔设备,其中保温炉盖6板尺寸φ860mm,均匀分布6根管体9(传统管体9的内径φ60mm,外径φ80mm);铝液坩埚炉4保温炉内壁与管体9边沿尺寸30mm;调整保温炉盖6板管体9法兰尺寸,保证新结构管体9(内径φ100mm,外径φ120mm)满足装配需求;差压模具布局相对紧凑,产品浇口2 位置较大调整将影响模具整体工艺,不利于浇注工艺稳定;模具浇口 2位置维持原尺寸不做调整;调整后保温炉盖6板法兰及管体9中心与模具浇口2不同心;制作中间管7,保证管体9与模具浇口2顺畅连接;管体9口及中间管7口,中间管7与模具浇口2连接部位蜜蜂层优选为石棉垫圈;准备就绪按照铸造工艺参数进行生产。
[0028]
参照图2,安装步骤:使用管体9上、下法兰11将管体9锁紧组装,安装至炉盖6上法兰12安装孔,使用螺栓紧固,将陶瓷中间管7和中间管保护套组装完成放置管体9口上方,管体9连接位置使用石棉板或石墨板进行密封;组装完成炉盖6与差压设备下台板3连接完成;
[0029]
陶瓷中间管7口与差压模具浇口2对正,满足装配需求。
[0030]
参照图3,管体9直径调整由60mm改为100mm,中心移动。管体 9中心位置移动,模具的浇口2位置未调整,浇口2中心与管体9中心不同心;通过使用变径的陶瓷中间管7,将不同心的管体9与模具浇口2直接连接;变径的陶瓷中间管7采用陶瓷保温材质,陶瓷中间管7使用专用法兰盘进行固定。
[0031]
参照图4,管体9直径由φ60mm调整为φ100mm,浇注过程中管体 9铝液体积增加64%,管体9内铝液总热量增加,浇口2温度下降速度放缓,有利于实现铸件自上而下的凝固顺序;管体9尺寸φ100mm 型号较φ60mm型号更为普遍,更利于获得;且φ100mm型管体9,广泛应用于低压铝合金的低压铸造领域;新材质(氮化硅、碳化硅、钛酸氯)管体9(使用寿命1年)可以循环使用,大大降低生产成本。
[0032]
参照图5,管体9直径增加(外径由80mm增加至120mm),炉盖 6管体9法兰安装孔尺寸调整能够满足管体9安装;管体9边沿与坩埚炉4壁间隔减小或碰撞,要调整此距离,需要将管体9中心向内部移动,保证管体9与坩埚炉4壁安全距离。
[0033]
本实施例使用大直径(内径φ100mm,外径φ120mm)管体9,差压一模多腔生产产品保压时间降低10-20%,提高生产效率;生产过程能耗降低,铝合金液保温温度由715-725℃,降低至695-705℃;新型管体与老管体使用寿命直接采购成本降低;同时减少频繁更换损坏管体9造成的设备停机及模具热模造成的生产成本浪费。
[0034]
在本实用新型的描述中,需要理解的是,术语“纵向”、“横向”、“上”、“下”、“前”、“后”、“左”、“右”、“竖直”、“水平”、“顶”、“底”、“内”、“外”等指示的方位或位置关系为基于附图所示的方位或位置关系,仅是为了便于描述本实用新型,而不是指示或暗示所指的装置或元件必须具有特定的方位、以特定的方位构造和操作,因此不能理解为对本实用新型的限制。
[0035]
以上所述的实施例仅是对本实用新型的优选方式进行描述,并非对本实用新型的范围进行限定,在不脱离本实用新型设计精神的前提下,本领域普通技术人员对本实用新型的技术方案做出的各种变形和改进,均应落入本实用新型权利要求书确定的保护范围内。