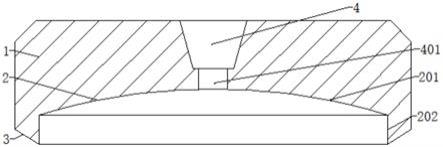
[0001]
本实用新型涉及镜片打抛模具领域,具体涉及一种曲率半径为356.7mm 的抛光模具。
背景技术:[0002]
镜片生产过程中,需要经过精磨抛光工序,此工序通常使用高速抛光机来实现加工,利用高速抛光机抛光时,根据需要生产的光学镜片产品图纸,设计制作抛光工装夹具(凸面和凹面各一套),由于需要抛光模具必须完全和镜片曲率一致并贴合,才能达到把镜片抛光的效果,但是目前在对曲率半径为356.7mm的镜片进行抛光时,由于没有设置专用的抛光模具来符合使用需要,造成了对曲率半径为356.7mm的镜片抛光加工的精度一般,良品率较低。
技术实现要素:[0003]
本实用新型的目的就在于为了解决上述问题而提供一种曲率半径为 356.7mm的抛光模具,在模具本体的底面向内凹陷开设有曲率半径为 356.7mm的打抛凹面,继而利用抛光机匀速运转,上摆驱动模具本体的方式将固定在球座上曲率半径为356.7mm的光学镜片进行精确的抛光,确保能够使曲率半径为356.7mm的光学镜片打磨完成后符合加工的精度要求,详见下文阐述。
[0004]
为实现上述目的,本实用新型提供了以下技术方案:
[0005]
本实用新型提供的一种曲率半径为356.7mm的抛光模具,包括模具本体,所述模具本体为凹模,所述模具本体为圆柱体结构,所述模具本体的底面向内凹陷的开设有用以打磨抛光镜片的打抛凹面,且所述打抛凹面的曲率半径为356.7mm。
[0006]
作为优选,所述模具本体的顶面中部竖直向下开设有用以与抛光机主轴连接的连接孔,且所述连接孔为盲孔,所述连接孔的底端竖直同轴开设有缓冲孔,且所述缓冲孔为通孔。
[0007]
作为优选,所述连接孔为倒置的圆台孔,所述缓冲孔的孔径小于所述连接孔的底端直径。
[0008]
作为优选,所述打抛凹面由顶部向内凹陷的凹面部和下部竖直的直筒部组成,且所述凹面部的底端最大直径和所述直筒部的直径均为79mm。
[0009]
作为优选,所述打抛凹面通过去除材料的方式获得,且所述打抛凹面的表面粗糙度为6.3。
[0010]
作为优选,所述凹面部的曲率半径误差范围为0.02mm,所述直筒部的深度为2.19mm。
[0011]
作为优选,所述模具本体的顶部和底部边缘均开设有倒角,且所述倒角的规格为5
×
45
°
。
[0012]
采用上述一种曲率半径为356.7mm的抛光模具,所述模具本体在加工时,先在所述
连接部的顶面中部自上而下的开设所述连接孔,后在所述连接孔的底端竖直开设所述缓冲孔并直至打穿出所述模具本体底面,之后在所述模具本体的底面通过用去除材料的方法加工出所述打抛凹面,所述打抛凹面在制作时应先加工所述直筒部,后在所述直筒部的顶端面加工出曲率半径为356.7的所述凹面部,最后可所述模具本体的顶部和底部边缘开设倒角来去毛刺,提升美观,则在使用时,将所述模具本体通过所述连接孔与外界抛光机主轴连接,后由外界抛光机主轴匀速运转而上摆驱动所述模具本体,继而通过所述打抛凹面的所述凹面部与固定在球座上曲率半径为356.7mm的光学镜片贴合接触并匀速转动的方式来对光学镜片表面进行打磨,打磨过程中,通过所述直筒部的设置能够确保在打磨过程中完全罩住镜片来进行打磨,确保了所述打抛凹面打磨时边缘处不会划伤镜片表面且防止了打磨产生的颗粒物飞溅,这样便实现了通过上摆驱动所述模具本体的方式将固定在球座上曲率半径为356.7mm的光学镜片进行精确的抛光,确保能够使曲率半径为356.7mm的光学镜片打磨完成后符合加工的精度要求,填补了对曲率半径为356.7mm的光学镜片打磨时专用模具的空缺,有利于提升良品率。
[0013]
有益效果在于:1、本实用新型在模具本体的底面向内凹陷开设有曲率半径为356.7mm的打抛凹面,继而利用抛光机匀速运转,上摆驱动模具本体的方式将固定在球座上曲率半径为356.7mm的光学镜片进行精确的抛光,确保能够使曲率半径为356.7mm的光学镜片打磨完成后符合加工的精度要求,填补了对曲率半径为356.7mm的光学镜片打磨时专用模具的空缺,有利于提升良品率;
[0014]
2、在打抛凹面的底部竖直开设有直筒部,以此通过直筒部的设置来确保在打磨过程中完全罩住镜片来进行打磨,确保了打抛凹面打磨时边缘处不会划伤镜片表面且防止了打磨产生的颗粒物飞溅。
附图说明
[0015]
为了更清楚地说明本实用新型实施例或现有技术中的技术方案,下面将对实施例或现有技术描述中所需要使用的附图作简单地介绍,显而易见地,下面描述中的附图仅仅是本实用新型的一些实施例,对于本领域普通技术人员来讲,在不付出创造性劳动的前提下,还可以根据这些附图获得其他的附图。
[0016]
图1是本实用新型的整体剖视图。
[0017]
附图标记说明如下:
[0018]
1、模具本体;2、打抛凹面;201、凹面部;202、直筒部;3、倒角; 4、连接孔;401、缓冲孔。
具体实施方式
[0019]
为使本实用新型的目的、技术方案和优点更加清楚,下面将对本实用新型的技术方案进行详细的描述。显然,所描述的实施例仅仅是本实用新型一部分实施例,而不是全部的实施例。基于本实用新型中的实施例,本领域普通技术人员在没有做出创造性劳动的前提下所得到的所有其它实施方式,都属于本实用新型所保护的范围。
[0020]
参见图1所示,本实用新型提供了一种曲率半径为356.7mm的抛光模具,包括模具本体1,所述模具本体1为凹模,所述模具本体1为圆柱体结构,所述模具本体1的底面向内凹
陷的开设有用以打磨抛光镜片的打抛凹面2,且所述打抛凹面2的曲率半径为356.7mm。
[0021]
作为本案优选的方案,所述模具本体1的顶面中部竖直向下开设有用以与抛光机主轴连接的连接孔4,且所述连接孔4为盲孔,以便通过连接孔4使模具本体1与抛光机主轴稳固连接所述连接孔4的底端竖直同轴开设有缓冲孔401,且所述缓冲孔401为通孔,如此设置,便于通过缓冲孔 401的设置来确保在打磨镜片的过程中,磨削取出的镜片材料能够通过进入到所述缓冲孔401的方式进行缓冲,避免镜片材料向打抛凹面2的最高位置汇聚时停留在打抛凹面2最高位置而干扰到镜片打磨,所述连接孔4 为倒置的圆台孔,所述缓冲孔401的孔径小于所述连接孔4的底端直径,如此设置,便于连接孔4和缓冲孔401能够被准确快速的加工出来。
[0022]
所述打抛凹面2由顶部向内凹陷的凹面部201和下部竖直的直筒部 202组成,且所述凹面部201的底端最大直径和所述直筒部202的直径均为79mm,如此设置,便于通过直筒部202的设置来确保在打磨过程中完全罩住镜片来进行打磨,确保了打抛凹面2打磨时边缘处不会划伤镜片表面且防止了打磨产生的颗粒物飞溅,所述打抛凹面2通过去除材料的方式获得,且所述打抛凹面2的表面粗糙度为6.3,优选通过铣削的方式加工获得,以便打抛凹面2在打磨抛光使用时能够打磨出符合精度的光学镜片。
[0023]
所述凹面部201的曲率半径误差范围为0.02mm,以便凹面部201对光学镜片打磨时具有准确的精度,所述直筒部202的深度为2.19mm,如此设置,便于直筒部202具有一定深度的范围来实现罩住镜片并防止打磨产生的颗粒物飞溅,所述模具本体1的顶部和底部边缘均开设有倒角3,且所述倒角3的规格为5
×
45
°
,以便去除模具本体1外缘的毛刺并提升美观,同时方式模具本体1外缘过于锐利。
[0024]
采用上述结构,所述模具本体1在加工时,先在所述连接部的顶面中部自上而下的开设所述连接孔4,后在所述连接孔4的底端竖直开设所述缓冲孔401并直至打穿出所述模具本体1底面,之后在所述模具本体1的底面通过用去除材料的方法加工出所述打抛凹面2,所述打抛凹面2在制作时应先加工所述直筒部202,后在所述直筒部202的顶端面加工出曲率半径为356.7的所述凹面部201,最后可所述模具本体1的顶部和底部边缘开设倒角3来去毛刺,提升美观,则在使用时,将所述模具本体1通过所述连接孔4与外界抛光机主轴连接,后由外界抛光机主轴匀速运转而上摆驱动所述模具本体1,继而通过所述打抛凹面2的所述凹面部201与固定在球座上曲率半径为356.7mm的光学镜片贴合接触并匀速转动的方式来对光学镜片表面进行打磨,打磨过程中,通过所述直筒部202的设置能够确保在打磨过程中完全罩住镜片来进行打磨,确保了所述打抛凹面2打磨时边缘处不会划伤镜片表面且防止了打磨产生的颗粒物飞溅,这样便实现了通过上摆驱动所述模具本体1的方式将固定在球座上曲率半径为 356.7mm的光学镜片进行精确的抛光,确保能够使曲率半径为356.7mm的光学镜片打磨完成后符合加工的精度要求,填补了对曲率半径为356.7mm 的光学镜片打磨时专用模具的空缺,有利于提升良品率。
[0025]
以上所述,仅为本实用新型的具体实施方式,但本实用新型的保护范围并不局限于此,任何熟悉本技术领域的技术人员在本实用新型揭露的技术范围内,可轻易想到变化或替换,都应涵盖在本实用新型的保护范围之内。因此,本实用新型的保护范围应以所述权利要求的保护范围为准。