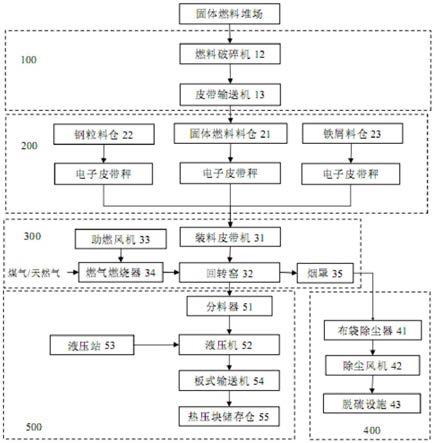
[0001]
本实用新型属于炼钢原料准备技术领域,具体涉及一种热压废钢增碳使用的装置。
背景技术:[0002]
废钢是炼钢生产的原料之一,为了达到高效利用废钢的效果,要求废钢必须有一定的块度、比重,并且铁含量高、杂质少。在废钢原料中,有一些钢渣中磁选出的钢粒、炼铁火渣中磁选出的铁粒,以及钢铁产品深加工过程中产生的铁屑等,因其粒度小无法直接入炉冶炼,目前的方法多为采用热压造块设备将粒子钢热压块成型再进行炼钢。如:中国实用新型专利申请《一种废钢破碎料热压块机以及采用该热压块机的热压工艺》(cn201810802666.7)公开了一种热压方法:
①
加热废铁破碎料,控制加热温度为800-1100℃,将废铁破碎料的温度保持在900-1000℃10分钟至15分钟;
②
将加热后的废铁破碎料注入至下模的型腔;
③
当废铁破碎料堆满型腔一定高度后,压料油缸压缩(工作压力为 20mpa-30mpa);制成的饼块的密度为5.9-6.1kg/dm。
[0003]
该种方法将加热和液压压缩分开,可以防止因为装置的过热而影响使用寿命,但是仍存在以下问题:废钢热压块工艺需要将废钢的温度提升到800℃以上 (保温温度为900-1000℃),这个温度下的部分废钢会产生氧化,从而降低热压块中的金属铁含量,进而影响铁的回收率,导致热压块的金属铁占全铁的比例只有90%左右。而使用这种工艺做成的热压块,在后续转炉炼钢生产过程中,会大量吸收热量,致使吨钢铁耗升高,影响转炉产量和节奏。实践证明,每增加1吨的现有工艺制备的钢粒压块,会使废钢总体加入量降低2.5吨到3吨。
[0004]
如何减小热压块对炼钢的热损耗,提高铁的收得率、保证炼钢生产节奏,成为目前废钢热压块技术的研究课题。
技术实现要素:[0005]
本实用新型的技术任务是针对以上现有技术的不足,提供一种热压废钢增碳方法及其装置,使用该装置将合适的固体燃料磨制到合适的粒度后,按合适的比例精准地配加到钢粒中,然后使用回转窑混匀、梯度加热,最后压制成含有一定固定碳的废钢压块。
[0006]
本实用新型解决其技术问题的技术方案是:一种热压废钢增碳使用的装置,其特征在于,包括固体燃料破碎系统、配料系统、回转窑混合加热系统、烟气除尘脱硫系统、热压块系统;所述的固体燃料破碎系统,包括燃料破碎机和皮带输送机;所述的配料系统,包括固体燃料料仓、钢料料仓;所述的回转窑混合加热系统,包括装料皮带机、回转窑、助燃风机、燃气燃烧器;所述的回转窑头部设置有助燃风机和燃气燃烧器,所述的回转窑尾部设置有装料皮带机和烟罩;所述的除尘脱硫系统,包括通过烟道顺序连接的布袋除尘器、除尘风机和脱硫设施;所述的布袋除尘器通过烟道连接回转窑尾部的烟罩;所述的热压块系统,包括分料器、液压机、板式输送机和热压块储存仓。
[0007]
上述的燃料破碎机优化为四辊破碎机。
[0008]
上述的钢料料仓包括钢粒料仓、铁屑料仓。
[0009]
上述的电子皮带秤采用plc自动配料系统。
[0010]
与现有技术相比较,本实用新型具有以下突出的有益效果:
[0011]
1、使用本装置生产可以将热压块中的碳含量提升到3~8%,避免了在转炉使用热压块时出现降温大而影响炼钢产量的问题,且碳含量大于5%时还能起到提供热源、降低吨钢铁耗的效果;
[0012]
2、使用本装置生产,防止废钢在加热过程中的氧化,可提高1%以上的金属铁含量,即增加1%以上的金属收得率,降低钢铁料消耗,是一个能够有效提升效率的循环经济技术。
附图说明
[0013]
图1是本实用新型的结构流程图。
具体实施方式
[0014]
下面结合说明书附图和具体实施方式对本实用新型进一步说明。
[0015]
如图1所示,本实用新型包括固体燃料破碎系统100、配料系统200、回转窑混合加热系统300、烟气除尘脱硫系统400、热压块系统500。
[0016]
所述的固体燃料破碎系统100,包括燃料破碎机12和皮带输送机13。所述的燃料破碎机12优化为四辊破碎机。使用四辊破碎机对固体燃料进行破碎,要求固体燃料的粒度3mm以下达到90%,最大粒度不超过5mm,且固体燃料固定碳含量不低于80%、灰分不高于15%。加工好的固体燃料用皮带输送机13输送到所述的配料系统200的固体燃料料仓21。
[0017]
所述的配料系统200,包括固体燃料料仓21、钢料料仓。所述的各个料仓通过电子皮带秤与装料皮带机连接。具体的钢料料仓包括钢粒料仓22、铁屑料仓23。所述的电子皮带秤采用plc自动配料系统,将固体燃料、钢粒、铁屑等按一定的比例和配料量搭配好,供给所述的回转窑混合加热系统300的装料皮带机31。
[0018]
所述的回转窑混合加热系统300,包括装料皮带机31、回转窑32、助燃风机33、燃气燃烧器34。所述的回转窑32头部设置有助燃风机33和燃气燃烧器 34,所述的回转窑32尾部设置有装料皮带机31和烟罩35。所产生的二氧化硫、二氧化碳、水蒸气随着烟气向回转窑32尾部流动,并被安装在回转窑尾部的烟罩收集,进入除尘脱硫系统400的布袋除尘器41。
[0019]
所述的除尘脱硫系统400,包括通过烟道顺序连接的布袋除尘器41、除尘风机42和脱硫设施43。所述的布袋除尘器41通过烟道连接回转窑32尾部的烟罩,使用除尘风机42将烟气先抽到布袋除尘器41收集粉尘,然后进入脱硫设施43脱除二氧化硫,最后将达标的烟气排放到大气中。
[0020]
所述的热压块系统500,包括分料器51、液压机52、板式输送机54和热压块储存仓55。所述的回转窑32头部排出的高温废钢,经分料器51后,装入连接有液压站53的液压机52缸内,然后运行液压站53将高温废钢压制成块,比例达到5.5t/m3以上,最后由板式输送机54将热压块输送到热压块储存仓55。
[0021]
本实用新型的生产工序包括固体燃料破碎工序、配料工序、回转窑混合加热工序、
烟气除尘脱硫工序、热压工序。
[0022]
(1)固体燃料破碎工序
[0023]
使用破碎机对固体燃料进行破碎(具体可以为四辊破碎机),要求固体燃料的最大粒度不超过5mm,90%以上固体燃料的粒度达到3mm以下。其中,固体燃料可以为兰炭粉、焦粉等,要求固体燃料固定碳含量不低于80%、灰分不高于15%。加工好的固体燃料用皮带输送机输送到所述的配料工序。
[0024]
(2)配料工序
[0025]
将工序(1)所述的固体燃料与钢粒、铁屑按一定的比例和配料量搭配好,供给所述的混合加热工序。具体为使用电子皮带秤采用plc自动配料系统。
[0026]
(3)回转窑混合加热工序
[0027]
将工序(2)配好的物料用装料皮带机装入回转窑尾部,在回转窑头部燃烧煤气或天然气,将窑内的物料加热到900℃左右,随着烟气向回转窑尾部流动,温度逐步下降,直到200℃以内,具体燃烧温度和煤气流量可结合废钢特性、固体燃料配加比例、窑头温度来调整(详见实施例)。随着回转窑的转动,废钢在窑内从尾部向头部运动,温度也随之逐步升高,当温度达到232℃以上时,固体燃料中的硫开始氧化,变成二氧化硫:
[0028]
s+o2=so2[0029]
当温度继续升高到830℃时,固体燃料产生挥发分,同时物料内部的碳与附近的少量氧气反应产生一氧化碳,防止了废钢被氧化,产生的挥发分和一氧化碳从物料内部逸出后,与更多的氧气接触充分燃烧,产生二氧化碳和水蒸气。
[0030]
2c+o2=2co
[0031]
2co+o2=2co2[0032]
ch4+2o2=co2+2h2o
[0033]
所产生的二氧化硫、二氧化碳、水蒸气随着烟气向回转窑尾部流动,并被安装在回转窑尾部的烟罩收集,进入除尘脱硫工序。
[0034]
(4)烟气除尘脱硫工序
[0035]
通过烟道安装在回转窑尾部的烟罩,使用除尘风机将烟气先抽到布袋除尘器收集粉尘,然后进入脱硫设施脱除二氧化硫,最后将达标的烟气排放到大气中。
[0036]
(5)热压工序
[0037]
所述的回转窑头部排出的高温废钢,经分料器后,装入液压机缸内,然后运行液压站将高温废钢压制成块,比例达到5.5t/m3以上,最后由板式输送机将热压块输送到热压块储存仓。
[0038]
本实用新型通过回转窑将设定规格的固体含碳燃料颗粒与钢粒铁屑动态混合,温度梯度下硫和碳分阶段氧化,溢出气体扰动增加挥发分与氧的接触,解决了现有技术900~1000℃保温温度下的部分废钢产生氧化的技术问题,从而减少热压块中的金属铁含量的流失,增加金属收得率,降低钢铁料消耗。
[0039]
与此同时,本工艺还可以增加热压块中的碳含量。现有技术中,全废钢加热过程中,碳含量较低,碳氧反应较弱,造成金属大量氧化,钢铁料氧化程度高,会造成热压块中feo含量过高,降低金属收得率。并且熔池渗碳效果差,废钢难熔。而单纯的混料配碳,如中国实用新型专利申请《一种复合含碳球团的制备方法》(申请号200510134295.2)将含碳材
料,氧化铁皮,粘结剂等放入混料机中进行搅拌混合,之后压制成球,待球团干燥即为成品,但该方法在略微增加碳量的情况下,没有充分考虑冶炼过程中球团中的金属氧化物与碳素进行还原反应产生会产生球团爆裂的现象,会使得球团碎片化,上浮至渣表面,使得增碳效果不稳定。而本工艺回转窑温度梯度下混合加热,溢出气体扰动,增碳效果均匀肯定。可以将碳含量提升到3~8%,避免了在转炉使用热压块时出现降温大而影响炼钢产量的问题,且碳含量大于5%时还能起到提供热源、降低吨钢铁耗的效果。
[0040]
为了更好的进行验证,在河北某废钢热压生产线上进行了对比实验。
[0041]
其中,对照组,工艺步骤如下:
[0042]
(1)固体燃料破碎工序:同实施例组。
[0043]
(2)配料工序:同实施例组。
[0044]
(3)加热工序:配好的混料采用加热炉加热,控制加热温度为900-920℃, 10分钟至15分钟。
[0045]
(4)热压工序:高温废钢装入液压机缸内,然后运行液压机将高温废钢压制成块,比重达到6.0t/m3以上。
[0046]
实施例组,采用本实用新型技术方案,参数和结果数据如下。
[0047][0048]
以上组别生产出来的热压块,按每吨钢50kg应用于转炉炼钢生产,对比实验结果如下
[0049][0050]
注:热压块对应的铁收得率是根据消耗数据计算而来,其它原料的含铁量和收得率给定一个经验值,分别为:钢坯铁含量为99%,铁水含铁量按94%、铁收得率按98%计算,其它废钢含铁量按98%、铁收得率按98%计算。
[0051]
由以上结果可以看出:应用本实用新型技术,与现有的增碳热压技术相比,由于采用梯度加热,使得固体燃料与钢粒、铁屑能够充分结合,首先可以将热压块中的含量碳量提升到3~8%,有效化解配加冷压块后引起的吨钢铁耗大幅度升高的问题,当配碳量达到较高数量时,还能继续降低吨钢铁耗,从而提高钢产量;其次,本技术较现有技术具有更好的还原效果,压块中的金属铁所占全铁的比例提升了3%以上,从而炼钢过程的金属收得率也随之升高3%以上,更有利于提高回收废钢资源效率,降低炼钢原料成本;再次,本技术采用
的兰碳粉属于清洁能源,且价格低廉,通过热压应用于炼钢生产中,替代部分价格高昂的增碳剂,对降低炼钢成本也非常有利。
[0052]
需要说明的是,本实用新型的特定实施方案已经对本实用新型进行了详细描述,对于本领域的技术人员来说,在不背离本实用新型的精神和范围的情况下对它进行的各种显而易见的改变都在本实用新型的保护范围之内。